Древесно-полимерный композит (ДПК): состав, преимущества материала
Что такое древесно-полимерный композит (ДПК), и в чем его преимущества?
Древесно-полимерный композит (ДПК) – современный материал, который активно используется в строительных и отделочных работах. Материал ДПК – это оптимальная альтернатива дереву и пластику ПВХ, так как совмещает преимущества дерева и полимера, а именно – экологичность, тактильные ощущения, натуральный вид с одной стороны, с другой – прочность и устойчивость к агрессивным воздействиям внешней среды. Срок эксплуатации доски из ДПК достигает 25 лет.
В чем разница ДПК от ДВП, ДСП или МДФ
Материалы ДПК, ДСП, ДВП, МДФ – комбинации дерева и полимера, только древесно-полимерный композит по составу и технологии производства отличается от остальных. Для изготовления ДПК дерево измельчают в порошок. Процентное содержание древесной муки составляет 30-80% от общей массы. Остальные компоненты ДПК – это малогорючий и безопасный полимер (полистирол, полиэтилен, полипропилен или поливинилхлорид), а также химические добавки, которые улучшают технологические свойства материала (цвет, прочность).
Главные преимущества древесно-полимерного композита
- Первая особенность (и главное преимущество) древесно-полимерного композита — возможность производства методом экструзии, доставшаяся «в наследство» от пластиковой составляющей. Что это значит? А это значит, что, во-первых, материал в разогретом состоянии очень пластичен и позволяет получать изделия практически любой формы и конфигурации. Во-вторых, большая часть отходов, образовавшихся при обработке таких изделий, пригодна для вторичной переработки.
- Вторая особенность ДПК — это то, что благодаря древесной составляющей изделия из него могут не только выглядеть, как натуральное дерево, но и иметь запах древесины, интенсивность которого зависит от породы, использованной для приготовления муки, и процентного соотношения в составе материала. Иными словами, при практически одинаковой стоимости доска или плитка, изготовленная из древесно-полимерного композита, может с одинаковым успехом имитировать как запах дуба или сосны, так и аромат мербау или кумару.
- Третья особенность — то, что при всём визуальном, тактильном и ароматическом сходстве с деревом ДПК совершенно не подвержен обычным для него поражениям (гнили, плесени, жучкам, выцветанию и т.п.). А значит — не нуждается в дополнительной обработке.
Изделия из древесно-полимерного композита
- Террасные покрытия из ДПК – оптимальное решение для дачных террас, веранд, для ресторанов и различных заведений на открытом воздухе. По качеству материал успешно конкурирует с покрытиями из лиственницы, «бразильского ореха» и других пород, при этом стоимость террасных систем из ДПК на 30-70% дешевле натуральных аналогов, а срок службы – свыше 20 лет. Широкий ассортимент террасных систем от «Террадек» позволяет реализовать любые дизайнерские решения.
- Ограждения и заборы из ДПК отлично вписываются в ландшафтный дизайн. Такие изделия красивы, прочны и долговечны, что особенно важно для конструкций, установленных на открытом воздухе. Они даже более устойчивы к атмосферным воздействиям, нежели их аналоги из дерева или металла. Срок эксплуатации таких изделий из древесно-полимерного композита составляет 25 лет и более.
- Вентилируемые фасады из древесно-полимерного композита позволяют не только защитить внешние стены от воздействия окружающей среды и придать облику здания более эстетичный вид, но и обладают отличной звукоизоляцией и теплосберегательными свойствами. Используются такие фасады для интерьерной отделки нижних этажей любых сооружений, малоэтажных офисных зданий, частных домов.
Преимущества декинга ДПК
Ищете террасное покрытие на долгие годы? Выбирайте террасу из древесно-полимерного композита (ДПК). ДПК надежен и практичен, прослужит долгие годы, не требуя особого ухода, покраски и антисептика. Доска ДПК подходит к любому дизайну, так как обладает приятной текстурой натурального дерева и богатой цветовой палитрой.
Не скользит
Отвечает экологическим нормам
Долговечен
Прост в уходе
Не нуждается в пропитке
Не гниет, не плесневеет
Не портится насекомыми
Пожароустойчив
Влагоустойчив
Выдерживает вес
до 2000 кг/м
Не выцветает
Заноза исключена
Террасная доска: преимущества и недостатки
×
Советы по отделке дома
Какие материалы вам подойдут?
Как рассчитать количество?
Как установить и не допустить ошибок?
×
Подтвердите ваш электронный адрес!
Перейдите в свой почтовый сервис прямо сейчас, нажав по иконке
и Вы получите уникальную подборку советов по внешней отделке дома от производителя с 18-летним — опытом!
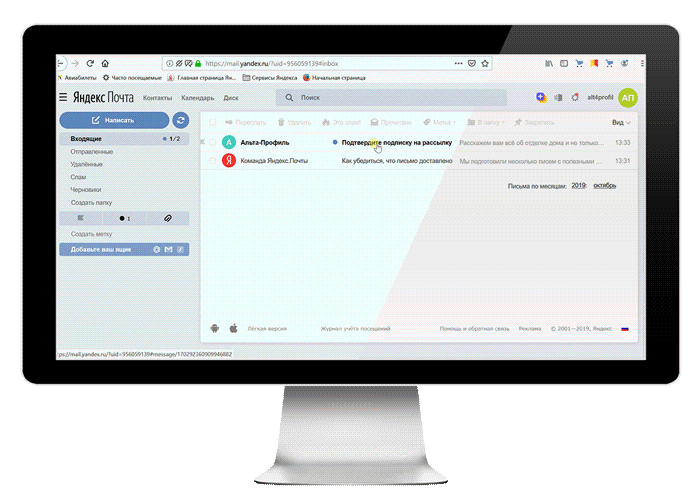
Важно! Если письмо не пришло, обязательно проверьте папку «спам» и переместите письмо во «входящие», если оно туда попало.
К материалам для покрытия пола на террасе, веранде или пирсе предъявляют повышенные требования. С одной стороны, они должны быть влаго- и морозостойкими, устойчивыми к истиранию и механическим повреждениям. С другой — красивыми, безопасными и приятными на ощупь. Но даже у тех материалов, которые соответствуют этим требованиям, есть свои недостатки.
Так, камень стоит дорого, он холодный и тяжелый. Дерево недолговечно и требует регулярного и тщательного ухода. Наливные полы под воздействием ультрафиолета желтеют. А что можно сказать о плюсах и минусах террасной доски ДПК? Давайте разберемся!
Что такое дёкинг ДПК?
Террасная доска (дёкинг) ДПК производится из древесно-полимерного композита. В ней объединены лучшие свойства натуральной древесины и полимерных материалов. Благодаря последним доска долговечна, практична, устойчива к влаге и морозам и не требует специального ухода. Наличие в составе ДПК древесной муки (до 70%) придает красивый вид деревянного покрытия, приятное ощущение тепла и экологичности.
Дёкинг используется на террасах и верандах, дорожках и крыльце, пирсе и плоской крыше — везде, где необходимо обустроить пол на открытом воздухе.
Преимущества террасной доски ДПК:
- 1. Влагостойкость
Благодаря содержанию полимеров дёкинг не впитывает влагу. Его не нужно укрывать в период затяжных дождей, а также на зиму. В отличие от натурального дерева, террасная доска не нуждается в специальной водоотталкивающей обработке. Дёкинг ДПК используется на пирсах и возле бассейнов — он устойчив к солям морской и хлорсодержащей воды.
- 2. Устойчивость к колебаниям влажности и температур
При значительных колебаниях влажности и температуры натуральная древесина высыхает и трескается. Террасная доска из ДПК лишена этого недостатка. Она не впитывает влагу, поэтому даже при резких перепадах температур не теряет первоначальный вид.
- 3. Морозостойкость
Дёкинг ДПК устойчив к низким температурам и может использоваться даже в северных регионах страны.
- 4. Высокая механическая прочность
На террасе играют дети, стоит и передвигается тяжелая мебель, девушки ходят на каблуках. Все это никак не отразится на внешнем виде напольного покрытия.
- 5. Устойчивость к плесени, грибкам и вредителям
Благодаря полимерной составляющей террасная доска не подвержена заражению плесенью и грибками, а также не привлекает вредителей.
- 6. Устойчивость к агрессивной среде
Повышенное содержание в воздухе солей (в приморских регионах) или агрессивных веществ (если неподалеку расположены крупные производства), сильные ветра и другие факторы окружающей среды не влияют на характеристики и срок службы террасной доски ДПК.
- 7. Нескользкая поверхность
Благодаря рифленой поверхности «антислип» дёкинг остается нескользким даже после дождя или мытья. Кроме того, древесно-полимерный композит не впитывает влагу, поэтому зимой в периоды оттепели и заморозков на нем не появляется наледь.
- 8. Безопасная поверхность
По террасной доске очень приятно ходить босиком. Рифленая поверхность создает легкий массажный эффект. К тому же на ее поверхности не образуются сколы и зацепы. Поэтому такое покрытие совершенно безопасно, в том числе для игр маленьких детей.
- 9. Устойчивый цвет
Качественная террасная доска ДПК (например, «Альта-Степ» от «Альта-Профиль») не выгорает на солнце и сохраняет насыщенный цвет в течение многих лет.
- 10. Простой уход
Мыть террасную доску ДПК можно при помощи бытовых моющих средств (некислотных) или проточной водой. Дёкинг не нуждается в защитном покрытии, в отличие от изделий из древесины.
- 11. Обеспечение дренажа
Доска устанавливается с небольшими зазорами для отвода воды и обеспечения качественного дренажа. А значит, на террасе не будет луж.
- 12. Долговечность
При правильной установке и эксплуатации срок службы террасной доски из ДПК — до 50 лет и более.
- 13. Привлекательный внешний вид
По цвету и фактуре дёкинг из ДПК практически неотличим от натуральной древесины. Такое покрытие выглядит респектабельно в течение всего срока службы.
Недостатки террасной доски ДПК
Террасная доска из древесно-композитного полимера не лишена нескольких недостатков.
- 1. Наличие в составе ненатуральных компонентов
В зависимости от производителя в составе террасной доски ДПК от 50 до 80% полимеров. Они вводятся для улучшения эксплуатационных характеристик покрытия. Однако любители натуральных материалов нередко предпочитают доску из дерева (например, лиственницы). При этом они готовы ежегодно тратить время и деньги на уход и защиту настила, а также обновлять его вдвое чаще. Как аргумент в защиту ДПК можно сказать, что дёкинг проходит все необходимые тестирования и имеет сертификат экологической безопасности. На нем без опасения могут играть маленькие дети.
- 2. Стоимость
На первый взгляд может показаться, что наличие в составе полимеров должно удешевлять продукцию. Но это не совсем так. Качественное сырье и аддитивы стоят дорого. Например, при отсутствии специальных добавок дёкинг будет выгорать на солнце. Поэтому его первоначальная стоимость сопоставима с террасной доской из натуральной древесины. Но все-таки дёкинг ДПК экономичнее — потому что не требует затрат на защитные лаки и покрытия, а прослужит, в среднем, вдвое дольше.
Террасная доска «Альта-Профиль»
Описанные выше плюсы и минусы террасной доски ДПК — усредненные данные. Характеристики покрытия могут отличаться в зависимости от выбранного материала и производителей. Мы рекомендуем террасную доску «Альта-Профиль». Она:
- устойчива к воздействию УФ-излучения;
- имеет привлекательный вид натуральной древесины;
- легко монтируется;
- имеет специальное нескользящее покрытие.
В ассортименте компании — 2 коллекции террасной доски:
- Carpinus: двусторонняя доска с рифленой поверхностью.
- Fagus: повторяет структуру натурального дерева. В коллекцию входит 4 цвета.
Посмотреть предложение «Альта-Профиль» и выбрать подходящий вариант для вашей террасы, беседки или крыльца можно в нашем каталоге.
Читайте также
что это такое, расшифровка аббревиатуры, разновидности изделий из древесно-полимерного композита с фото, технология их производства

Он сочетает в себе лучшие черты обоих материалов, однако не лишен недостатков.
Главное преимущество ДПК в том, что этот материал можно изготавливать из древесных отходов, непригодных для переработки, то есть:
- горбыля;
- скрученной древесины;
- сучков;
- тонких веток;
- коротких обрезков.
Что такое ДПК?
Древесно-полимерный композит сочетает в себе цвет древесины с пластичностью современных полимеров, поэтому из него делают самую различную продукцию.
Наиболее популярным изделием из ДПК является декинг (на фото слева) – то есть отделочная доска, применяемая для обшивки полов, стен и различных поверхностей.
Из-за довольно высоких производственных расходов декинг из ДПК не может конкурировать с профилированной доской из дешевых пород древесины (сосна или ель), зато он успешно заменяет более дорогие доски из твердых экзотических пород.
Современная технология работы с древесно-полимерным композитом позволяет придавать изделиям из него любой цвет, а также наносить на поверхность даже довольно сложные узоры.
При правильном подборе пропорций древесины/полимера внешний вид, цвет, а нередко и запах декинга из ДПК ничем не отличается от досок из соответствующих древесных пород.
Поэтому разницу можно заметить лишь на ощупь, ведь термопластичные полимеры создают поверхность, не похожую на древесину.
Одним из основных преимуществ ДПК является водостойкость, ведь небольшое количество влаги впитывает очень тонкий наружный слой, где частицы древесины не покрыты полимерной пленкой.
Поэтому под дождем возникает эффект намокания, то есть цвет поверхности изменяется из-за небольшого количества влаги, впитанного древесным наполнителем, но это никак не влияет на размеры или форму изделия.
Благодаря этому изделия из ДПК не увеличиваются в результате набухания, а также не усыхают от потери влаги, поэтому в такой отделке никогда не появляется щелей.
Помимо декинга, из древесно-полимерного композита производят и другие изделия.
Например:
- несущие лаги для укладки настила;
- несущие элементы для легких конструкций;
- сайдинг и другие виды обшивки;
- мебель;
- кровельные материалы;
- окна и двери.
Более подробно о свойствах и сферах применения ДПК — здесь.
Производство
Для получения качественного изделия из ДПК необходимо четкое соблюдение технологии, а также пропорций всех компонентов композита.
Следует заметить, что этого можно добиться только полной автоматизацией производства данного материала.
При этом соблюдают следующий порядок действий:
- Измельчают полимер и древесный наполнитель, используя сначала шредеры, затем мельницы. Это позволяет применять не только первичный, но и вторичный полимер, собранный на мусорных полигонах или на пунктах приема вторсырья.
- Снижают уровень влажности измельченного древесного сырья, ведь вода при подъеме температуры закипает, образуя пузырьки, которые смешиваются с расплавленным полимером, снижая прочность изделия после застывания. Эту операцию проводят с помощью вакуумных установок, ведь чем ниже давление, тем выше температура кипения, поэтому при сильном разряжении жидкость переходит в пар при комнатной температуре.
- Перемешивают оба компонента в необходимых пропорциях и добавляют к ним вещества, улучшающие свойства готового изделия. Для этого все компоненты подают в одно или двухшнековые установки, которые работают подобно шнеку мясорубки.
- Плавят этот состав в специальных установках, используя для нагрева электрические или масляные нагреватели.
- Расплавленную массу подают в шнековый транспортер, который не только поставляет готовую массу к фильере и создает достаточное для формовки детали давление, но дополнительно перемешивает расплав.
- С помощью фильеры (отверстия особой формы, инверсионно повторяющей контуры будущей детали) формируют готовую деталь.
- Охлаждают ее в водяной ванне, затем наносят на поверхность необходимый рисунок с помощью различных станков.
- Нарезают циркулярными пилами на куски необходимой длины.
На каждом этапе важно выполнить работу не только с высоким качеством, но и за определенное время, чтобы не случалось простоев линии из-за нехватки материала или невозможности переработать его избыток.
Чтобы обеспечить нужную дозировку остальных компонентов, их, в зависимости от технологии, либо загружают в смеситель партиями необходимого объема/веса, либо подают через калиброванные отверстия.
Некоторые предприятия не только производят товары из ДПК, но также продают гранулы из расплавленной и отвердевшей смеси, которые применяют в качестве материала на тех линиях, где нет измельчителей древесины и полимеров.
Кроме того, такой подход позволяет создать запас гранул на случай поломки измельчителей или быстро запустить несколько экструзионных линий. Более подробную информацию об оборудовании и технологиях производства изделий из ДПК вы найдете в статье Производство ДПК.
Самостоятельное изготовление изделий из ДПК
Несмотря на то, что термопластичные полимеры, которые используют при промышленном производстве изделий из ДПК, невозможно применять в домашних условиях, существует целый ряд других полимерных компонентов, которые после застывания превращаются в твердое вещество.
Наиболее популярными среди таких веществ являются:
- ПВА;
- акриловый клей;
- эпоксидная смола;
- полиэфирная смолы;
- жидкости на основе нитроцеллюлозы;
- самодельные растворы на основе толуола или ацетона.
В качестве наполнителя можно использовать не только мелкие древесные отходы, то есть:
но и обрезки веток. Большой выбор древесного наполнителя и полимеров позволяет создавать из них уникальные изделия, которые не выпускают промышленным способом.
Кроме того, для работы с основными компонентами, за исключением полиэфирной смолы, а также жидкостей на основе ацетона или толуола, не требуется каких-то особых условий, достаточно небольшой комнаты с вентиляцией и хорошим освещением.
Для работы с опасными жидкостями необходимо помещение с принудительной вентиляцией, ведь они выделяют ядовитые и взрывоопасные газы.
Если вас заинтересовало изготовление изделий из древесного композита в домашних условиях, то рекомендуем внимательно прочитать соответствующую статью ДПК своими руками.
Вывод
Изготовление изделий из древесно-полимерного композита позволяет снизить выброс вредных веществ, ведь для их производства используют те материалы, которые обычно выкидывают на свалку или сжигают.
Теперь вы знаете:
- расшифровку аббревиатуры ДПК, и что это такое;
- как и из чего производят ДПК;
- что делают из этого материала;
- можно ли в домашних условиях работать с древесно-полимерным композитом.
Состав и основные свойства древесно-полимерных композитов
Древесно-полимерные композиционные материалы (ДПК), предназначенные для переработки методом экструзии состоят из трех основных компонентов:
- частиц измельченной древесина
- синтетических или органических термопластичных полимеров или их смеси,
- комплекса специальных химических добавок ( модификаторов) , улучшающих технологические и другие свойства композиции и получаемой продукции, часто называемых также аддитивами.
От традиционных древесно-наполненных пластмасс (ДНП) композитные материалы отличаются высоким ( более 50 процентов) содержанием древесины по массе в составе общей композиции и соответствующим ее влиянием на свойства готового продукта. В ДНП древесного наполнителя не много и свойства такой пластмассы определяются, в основном, свойствами полимера. А когда древесины становится больше, то свойства композита определяются уже:
- свойствами матрицы,
- свойствами частиц древесины,
- характером связей между древесными частицами и матрицей,
- структурой полученного композита.
На рисунках ниже показаны три схематических структуры наполненного материала :
Cлабо-наполненный пластик, средне-наполненный композит и высоко-наполненный композит.
Содержание древесины в составе древесно-полимерного композита на основе термопластичных смол может меняться в широких пределах. Большинство американских производителей работают пока с составами, содержащими 50 — 70 % древесины. Европейские разработчики технологий экструзии ДПКТ стремятся получать композиции, содержащие более высокое наполнение древесиной — до 80% и более.
Древесина подвергается измельчению на специальных мельничных установках различного типа и превращается в древесную муку или в древесное волокно . В настоящее время наиболее широко для изготовления ДПК используется древесная мука. Производство древесной муки давно освоено отечественной промышленностью. Она используется как наполнитель пластмасс, сырье для взрывчатых веществ, для микробиопрома и т.д.). Наряду со специально измельченной древесиной в состав ДПКТ могут входить некрупные опилки и шлифовальная пыль.
Перспективным является использование в ДПКТ и древесных волокон по типу применяемых в производстве ДВП, МДФ и бумаги. Древесные волокна получают методом дефибрации, т.е. расщепления древесины на волокна. В некоторых случаях используют готовое волокно из картонных и бумажных отходов (макулатуры). Например, у китайской компании имеется опыт промышленной утилилизации в производстве ДПКТ бумажных молочных пакетов, содержащих одновременно полиэтилен, бумагу и даже алюминиевую фольгу.
Финскими специалистами проверена возможность использования в качестве сырья для изготовления компаунда стандартных древесных топливных гранул ( на экструдере типа Conex).
Гранулы проще перевозить и хранить, чем муку
Внешний вид топливных гранул, см. рис 1.
Древесная мука ( англ. wood flour, wood meal, нем holzmehl ) — изготавливается преимущественно из мягких, не смолистых, пород древесины, например сосны. Вовсе не исключается и применение твердых лиственных пород, только их несколько сложнее измельчать. В нашей стране мука выпускается по ГОСТ 16361-87 «Мука древесная. Технические условия».
За рубежом с успехом изготавливается древесная мука для использования в термопластичных ДПК из оболочек зерен растений (рисовой шелухи, ореховой скорлупы). Американское предприятия Heartland BioComposites LLC недавно освоило применение в качестве сырья пшеничной соломы.
В большинстве случаев размер древесных частиц в композите находится в пределах от 500 до 50 мкм. Частицы древесной муки могут принимать самые разнообразные формы. Отношение длин частиц муки к их ширинам находится в пределах от 1:1 до 4:1.
В мельничных установках в ходе размола выделение нужной фракции муки осуществляется при помощи системы сит или центробежными методами. За рубежом принято обозначать фракцию муки при помощи числа Mesh. По российскому стандарту подразделение древесной муки осуществляется по нескольким маркам.
У древесного волокна ( wood fiber ) длина зависит от породы древесины : у лиственных пород 1 — 1, 5 мм, у хвойных 3 — 3, 5 мм. Отношение длины к толщине древесного волокна составляет от 1 : 10 до 1 : 20.
Древесина традиционно используется в механической обработке металлов в качестве шлифующего и полирующего материала, так как обладает заметными абразивными свойствами. Эти свойства сохраняются и у древесной муки. Однако, абразивность древесины ниже, чем у стекловолокна и некоторых др. минеральных наполнителей, используемых в производстве наполненных пластмасс и композитов. Поэтому она считается относительно «мягким» наполнителем.
Скорость абразивного износа оборудования пропорциональна давлению в цилиндре экструдера (и фильере), температуре и скорости движения рабочей смеси относительно поверхности рабочих органов и естественно зависит от состава рабочей смеси ( соотношения количества муки и смолы, вида смолы, видов и количества смазочных материалов и др. факторов). В зависимости от стойкости рабочие цилиндры и шнеки экструдеров могут эксплуатироваться 1-2 года до замены или ремонта.
Насыпная плотность древесной муки и волокна может колебаться в пределах 100 — 300 кг/ м3. Влажность муки в поставке желательно иметь не более 8 %. В готовом композите влажность древесных частиц должна быть, как правило, менее 1 %. Чем меньше влаги в структуре материала, тем более он устойчив ко внешним воздействиям.
Существуют различные и иногда противоречивые мнения, относительно применения различных пород древесины и размеров частиц.
Отметим очевидные вещи:
- в исследованиях изучено влияние размеров частиц на механические свойства композитов, однако оно не очень велико;
- слищком мелкие (пыль) и слишком крупные частицы ухудшают прочность композита, однако это не всегда критично для готового изделия;
- крупные частицы снижают производительность подготовительного оборудования в силу их малой насыпной плотности;
- при плотности композита, приближающейся к 1,4 г/ куб.см, т.е. к истинной плотности древесины, порода древесины уже не имеет принципиального значения.
Композит, изготовленный из крупных частиц будет иметь более зернистую поверхность, подобную поверхности древесно-стружечной плиты и это может требовать шлифования, применения утолщенной облицовки и (или) отделки поверхности изделий. Например, из опыта мебельной промышленности, зернистость профилей, изготовленных фрезерованием из древесно-стружечной плиты не всегда удается скрыть при облицовывании дорогими декоративными пленками на основе пропитанных смолами бумаг общей массой до 130 г на 1 кв метр. А для облицовывания профилей из МДФ, обладающей мелкой равномерной структурой, могут успешно применяться более дешевые декоративные пленки массой менее 80 г на 1 кв.м. Кроме того, крупные частицы древесины, особенно находящиеся вблизи поверхности изделия более подвержены воздействию влаги и повреждению под воздействием неблагоприятных факторов внешней среды.
Очень мелкие пылевидные частицы (менее 50 мкм) имеют большую удельную поверхность и в силу этого требуют использования большего количества смолы для образования полноценной полимерной матрицы.
Примечание. В настоящее время проводятся исследования по использованию в композитных материалов микроцеллюлозы. Но это скорее будет уже друглй класс материалов, т.н. нанокомпозиты.
Окончательное превращение рабочей смеси в композитный материал происходит постепенно по зонам экструдера и в фильере. Полимер должен охватить всю поверхность частицы древесной частицы, внедриться в ее поры и тем самым обеспечить плотное молекулярное взаимодействие между древесиной и полимером. Это существенно отличает процесс экструзии ДПК от процесса экструзии обычных пластмасс, т.к. древесина плохо смачивается расплавом полимера. Интенсифицировать процесс смачивания за счет повышения температуры в экструдере сложно вследствие опасности тепловой деструкции древесины, полимера и возгорания смеси (при температуре более 200 град. С).
Поэтому, с точки зрения качества получаемой продукции и производительности процесса — очень важен технологический уровень применяемого оборудования и состав рецептуры смеси (качество базовой смолы, вид и количество вводимых в рецептуру добавок — модификаторов).
Примечания:
1. Технологическими и физико-механическими свойствами близкими к древесно-полимерным композитам являются композиционные материалы, получаемые на основе и других растительных волокон, например : пенька (Hemp), лен (Flax), сизаль (Sisal), кенаф (Kenaf) и др. волокнистых растений.
Растительные волокна могут вводиться в состав ДПК и одновременно с древесными волокнами. Применение недревесных волокон растительного происхождения особенно активно разрабатывается сейчас в странах Юго-Восточной Азии, в частности в Китае. Подробнее о волокнах см. специальное приложение и библиотеку Биокомпозиты.
2. При внешней простоте идеи производства ДПК , сама конструкция вещества древесно-полимерного композита имеет очень сложную структуру. Не менее сложны для описания и химические, физические и механические процессы технологии производства экструзионных ДПК. Эти сложности определяются сложностью и неоднородностью самой древесины.
С большим или меньшим успехом, в производстве ДПК могут использоваться любые термопластичные полимеры, однако на практике сейчас используются, в основном, четыре вида термопластичных смол: полиэтилен (PE ), полипропилен (PP), поливинилхлорид (PVC) и, в меньшем количестве, полистирол (PS). На диаграмме ( рис.4.2. ) отражены существующие соотношения применения различных смол и наполнителей и прогноз на ближайшие годы.
Рис.2. Состояние и прогноз применяемости базовых смол и наполнителей в производстве композитов
Таким образом, на первом месте по применяемости находится полиэтилен (высокой и низкой плотностей) , затем следует ПВХ и полипропилен. Однако, в Европе наболее перспективным считают полипропилен. В частности, немецкая фирма Advanced Extruder Technologies AG ( изготовитель оборудования для экструзии ДПК) указывает на следующие оптимальные соотношения наполнение композита древесиной для различных типов базовых смол:
- на основе ПВХ — 60 %
- на основе полиэтилена — 70 %
- на основе полипропилен — 80 % и более.
Существенный рост предполагается по всем видам композитов, но начиная с 2003 особенно быстро увеличивается применение, в качестве основы композита, и других ( не древесных ) растительных волокон.
Наряду со смолами заводского изготовления, поставляемых в виде суспензии или гранул, ряд американских компаний используют в производстве ДПК пластиковых промышленных и бытовых отходов ( упаковочной пленки, бутылок и т.п. ), подвергаемых мытью, сушке и измельчению.
Проводятся эксперименты и по использованию в термопластичных ДПК других промышленных термопластов — АБС-пластика, полиамидов (капрона, нейлона), поликарбонатов, полиэтилентерфталата и др. в первичных формах и отходов.
Ориентировочные соотношения мировых цен на сырье ( в английских фунтах за тонну , март 2003 г ), используемое в производстве ДПК приведено в табл. 4.1
Полиэтилен высокого и низкого давления | 500 |
Поливинилхлорид | 350 |
Полипропилен | 580 |
Отходы полиэтилена | 140-170 |
Опилки | 100 |
Древесная мука | 200 |
Готовый к экструзии ДПК компаунд | 700-1200 |
Данная таблица хорошо иллюстрирует экономическое существо интереса к проблемам производства древесно-полимерных композитов и объективных тенденций в развитии и совершенствовании их технологии производства. Следует иметь ввиду, что текущие цены на базовые смолы на мировом рынке сильно зависят от цен на нефть и подвержены значительным колебаниям.
В производстве древесно-полимерных композитов применяются следующие виды добавок — модификаторов: связующие агенты, смазочные материалы, антимикробные добавки, антиокислители, вспенивающие агенты, пигменты, огнезащитные аенты, противоударные модификаторы, светостабилизаторы, температурные стабилизаторы и др.
Эти добавки используются при экструзии и литье обычных наполненных и ненаполненных пластмассовых профилей и примерно с теми же целями, но соотношение их в сочетаннии с древесиной несколько меняется. В первую очередь это относится к связующим агентам, смазочным материалам, и, при необходимости, — к противоударным модификаторам. Добавки поставляются по отдельности, или в виде комплексов (как поливитамины, — все в одной грануле).
Древесина, в отличие от минеральных наполнителей для пластмасс, обладает не очень высокой адгезией к базовым смолам, особенно — к полиолефиновым. Это можно обьяснить очень сложной формой поверхностей ее частиц, затрудняющей процесс смачивания ее расплавленным полимером, а так же ее химическим составом. Это обстоятельство предъявляет к подбору добавок и к конструкции экструдера повышенные требования. На фотографиях ниже показаны 2 образца древесно-полимрной смеси (электронный микроскоп, 200-кратное увеличение, соотношение 60% полипропилена, 40% древесной муки).
На левой фотографии отчетливо видны многочисленные незаполненные полимером пустоты. На правом образце структура материала цельная. Именно это делает материал — композитом, в котором работает и полимерная матрица и древесина. Улучшение структуры обеспечено включением в состав материала специального связующего агента, обеспечивающего хорошую связь между частицами древесины и смолы.
Схематически характерные дефекты структуры композита показаны на двух рисунках ниже
На левой схеме синим цветом выделены незаполненный смолой отдельные пустоты. На правой схеме показано образование агломератов, составляющихся из нескольких не склееных друг с другом древесных частиц. Наличие таких дефектов, особенно на поверхности изделий, приводит к снижению прочности и долговечности материала.
Конкретные рецептуры древесно-полимерных композитов разрабатываются применительно к заданным продуктам, применяемым базовым смолам и технологическим процессам. Они часто являются производственным секретом фирмы-изготовителя конкретных изделий или предметом лицензии поставщика технологии или оборудования.
Важным направлением в области разработок современных рецептур экструзионных ДПК, являются поиски в области использования в их составе природных, т.е. биологических полимеров. Успешным достижением в этой сфере стало использование крахмалистых веществ, например — кукурузной муки (материалы типа Fasal — Fasalex). Активно проводятся исследования по применению лигнина (отходы целлюлозного производства), отходов кожевенной и мясомолочной промышленности и т.д. Есть сведения об исследованиях российских специалистов о возможности применения хвойной смолы — живицы в качестве одного из компонентов экструзионных ДПК.
Внешний вид древесно-полимерных композитов.
В естественном виде ДПК с высоким содержанием древесины более всего напоминает МДФ и или твердую ДВП, см рис.3. Он может окрашиваться в массе или подвергаться лакокрасочной отделке обычными красками и эмалями, или облицовываться синтетическими пленками или натуральным шпоном. На ощупь композит теплый, иногда слегка маслянистый.
Рис.3. Срезы ДПК профилейСуществует технология покрытия ДПК тонким облицовочным слоем пластмассы, или даже нескольких пластмасс непосредственно в процессе его выдавливания в экструдере. Эта технология, широко распространенная в пластиковой индустрии называется со-экструзия или ко-экструзия.
Однако, если при изготовлении компаунда использовались древесные частицы крупных фракций, то поверхность изделия будет ближе по внешнему виду к поверхности древесностружечной плиты. Такие профили выпускаются, например, голландской компанией Tech-Wood.
Термопластичные ДПК имеют слабый запах древесины (опилок).
Физические и механические свойства композитов
Плотность экструзионных композитов может находится в пределах 1000 — 1400 кг/м3. Плотность изделий может быть снижена при использовании специальных вспенивающих агентов до 700-900 кг/м3, но вспенить можно только полимерную матрицу.
Примечания:
- Плотность композита зависит от плотности используемой базовой смолы и применяемых аддитивов и их количества и плотности частичек древесины. В ходе компаундирования и экструзии под воздействием высокого давления и темературы частички древесины уплотняются, — вплоть до значения 1400 кг/м3, т.е. достижения истинной плотности древесины, свободной от пор и др. пустот.
- Истинная плотность древесины практически не зависит от ее породы.
- Изучаются вопросы применения в ДПК полых микронаполнителей (пластиковых и стеклянных микросфер).
Прочностные свойства ДПК в значительной степени зависят от вида базовой смолы, см. табл. 2.
Нагрузка | Размерность | Полиэтилен | ПВХ | Полипропилен |
---|---|---|---|---|
Предел прочности ( временное сопротивление ) | мПа | 5 -16 | 20 — 30 | 17 — 40 |
Модуль упругости при растяжении | гПа | 2 — 5 | 5 — 7 | 4-8 |
Предел прочности при изгибе | мПа | 10 — 26 | 40 — 47 | 30-52 |
Предел прочности при сжатии | мПа | 12 — 27 | 60 | — |
Однако, управлением составом композита и технологическим процессом можно в значительной степени улучшить его прочностные и др. свойства.
Рассмотрим свойства ДПК на примере трех конкретных модификаций выпускаемых под маркой «Fasal» разработанных с применением в качестве базовой смолы полипропилена австрийской фирмой » Austel research and development» Gmbh и продаваемых фирмой «Fasalex «, Австрия, см. табл. 3.
Свойства | Размерность | Fasal F134 | Fasal F 386 | Fasal F 465 |
---|---|---|---|---|
Плотность | кг/дм 3 | 1,4 | 1,35 | 1,2 |
Предел прочности (временное сопротивление ) | МПа | 25 | 17 | 23 |
Модуль упругости при растяжении ( мод. Юнга) | ГПа | 8 | 4 | 5,1 |
Сопротивление изгибу | МПа | 41 | 30 | 52 |
Модуль упругости при изгибе | ГПа | 5,8 | 3,8 | 5 |
Относительное удлиннение при растяжении | % | 0,5 | 0,6 | 1 |
Ударная вязкость по Шарпи | КДж/м2 | 3,2 | 3,3 | 4 |
Срок биологического разложения | недели | месяцы | неразлагаемый | |
Снижение сопротивления изгибу в воде при 23 град.C : | ||||
— после 30 мин. выдержки | % | 65 | 14 | 0 |
— после 120 мин. выдержки | % | 90 | 35 | 0 |
В композиции , предлагаемой фирмой Strandex , США, в качестве базовой смола используется полиэтилен и его отходы. Твердые и мягкие породы древесины считаются приемлемыми, а так же другие целлюлозные волокна, такие как солома, лен, рисовая шелуха , арахисовая шелуха, бамбук, кенаф и пр. Размер частиц 425 микрон ( 40 mesh ) и менее. Допускается большое содержание более мелких частиц (200 mesh и мельче ), включая шлифовальную пыль. Плотность композита составляет 0,98 — 1, 2 кг/дм3. Композит и технология запатентованы и продаются по лицензии вместе с фильерами. Стоимость одной фильеры более 20 000 долларов США, стоимость лицензии ( по некоторым данным) более 1 млн. долларов.
Однако в использовании отходов ДСТП и МДФ существует серьезная проблема. Она связана с возгонкой паров формальдегида из фенольных смол, которые содержатся в этих плитах.
Примечание. Хотя прочность термопластичных ДПК при испытаниях находится на уровне природных древесных материалов, их реальная эксплуатационная прочность во многих случаях существенно выше, т.к. изделия, изготовленне из ДПК, не имеют естественных пороков, присущих древесине (сучков, трещин, свилеватостьи и т.п.), не изменяют своей прочности при увеличении влажности и не поражаются грибками и бактериями.
В начале освоения производства ДПК технологи старались обеспечить максимальную биостойкость изделий. И эта задача была решена.В частности, ряд фирм-изготовителей ДПК предоставляют гарантии на 10, 25 и 50 лет эксплуатации готовых изделий на улице, т.е. самой высокой устойчивости к воздействию влаги, света, грибков и насекомых без специальной защиты. Большинство производимых ДПК могут принимать в себя небольшое количество ( 0,1 — 4 % ) влаги не теряя при этом формы и прочности и восстанавливать прежние свойства при высыхании.
Новым направлением в производстве ДПК, является создание рецептур легко утилизируемых биоразлагаемых ДПК с пониженной биостойкостью. Они предлагаются, например, фирмой Fasalex, — как экологически безопасные по всему жизненному циклу ( указанные выше композиции Fasal F 134 и F 386 ) .
Необходимо отметить, что не смотря на уже солидный производственный опыт и многочисленные уже проведенные исследования, в сфере древесно-полимерных композиций существует еще огромное количество неисследованых направлений. С одной стороны это связано с бесконечными возможностями химии полимеров, а с другой обьясняется молодостью самой этой новой отрасли промышленности.
Способность к обработке
Изделия из ДПК обрабатываются теми же инструментами, что и древесина. ДПК легко пилятся, строгаются, сверлятся, шлифуются и т.п. Очень хорошо удерживает гвозди, скобы, шурупы, см. рис. 4.
Многие рецептуры композитов поддаются склеиванию. Некоторые рецептуры можно сваривать, подобно пластмассе. Уже освоена практика гнутья изделий профильных изделий после нагрева, подобно пластмассовым профилям и т.п.
Рис.4.Обработка древесно-полимерных композитов
ДПК не очень легко воспламенимы, особенно, — если они выполнены на основе поливинилхлоридной смолы.
Интересным направлением в использовании экструзионных ДПК является совместное применения ДПК профиля и металлического проката. В этом случае в полость профиля вставляется стальная труба, полоса и т.п. Металл принимает на себя полностью или частично силовую нагрузку, а профиль выполняет декоративные, защитные и другие функции.
Пока не существует принятой стандартизированной классификации термопластичных ДПК.
Автор статьи: Абушенко Александр Викторович
Добавить в закладки:
Террасная доска из древесно-полимерного композита (дпк), монтаж.
В России, обладающей богатейшими лесными массивами, дерево один из самых востребованных материалов, применяющихся для строительства и отделки. Это обусловлено экологичностью деревянных изделий, уникальностью свойств и универсальностью в обработке. Но древесина подвержена гниению и восприимчивостью к неблагоприятным внешним воздействиям. В стремлении сохранения всех достоинств дерева с минимизацией имеющихся недостатков производителями создан инновационный материал, это ДПК (древесно-полимерный композит).
Немного истории
Впервые ДПК начала производить Швеция в 1977-ом году. Но на этом этапе производство оказалось нерентабельным из-за отсутствия достаточного спроса и высокого износа оборудования. Изготовление практически прекратилось до 90-х годов, когда разработки технологии были продолжены в ряде развитых стран (Германии, Финляндии, Голландии, Италии, Японии, Канаде и США). В настоящее время примерно 70-ть % всего мирового производства ДПК находит применение в США.
В нашей стране промышленное производство материала началось с 2007-го года. Далее рассмотрим, ДПК что это?
Состав изделий и основы технологии производства
Основные слагающие компоненты в процентах:
- древесина, измельчённая до состояния муки — от 30-ти до 80-ти;
- термопластичные полимеры (поливинилхлорид, полипропилен, полистирол, полиэтилен) — 5-ть…50-т;
- модификаторы, улучшающие характеристики конечной продукции — до 10-ти.
Конкретная рецептура подбирается в зависимости от вида изделий, их назначения и условий эксплуатации, а также имеющегося технологического оборудования.
В основном из данных материалов изготавливаются дегинг, не уступающие по свойствам обычным деревянным и керамическим плиткам.
Террасная доска из древесно полимерного композита с наличием в составе ПВХ обладает большей износоустойчивостью, при этом не скользит, устойчива к воздействию ультрафиолета и характеризуется более высоким классом по пожарной безопасности.
Для изготовления профилей, такое название получили изделия, используется метод экструзии. Схема производства:
- измельчение древесины до частиц 0,7…1,5мм при помощи ножевых и молотковых дробилок;
- просев и разделение по фракциям. Крупные — для получения технических профилей, среднего помола — предназначенные для отделки шпоном или плёнками, самые мелкие — без дальнейшей отделки поверхности;
- сушка при влажности сырья ≥ 15-ти %;
- дозировка со смешиванием компонентов;
- прессование и формовка для приобретения древесно полимерным композитом окончательного товарного вида.
Окрашивание декинга происходит сразу в заводских условиях, добавлением в смесь красителей или нанесением на готовые поверхности.
К используемым древесным породам предъявляются следующие требования:
- обязательная стойкость к загниванию;
- твёрдость волокон;
- не поражаемость различными микроорганизмами и насекомыми.
Древесно полимерные террасные доски могут изготавливаться из следующих экзотических древесных пород:
- кумару — бразильского тика;
- бирманского тика;
- ипе;
- пуинкадо;
- банкирая;
- балау и других.
Эти породы, произрастающие в странах с тропическим климатом, обладают красивыми текстурами, великолепными цветами с насыщенными оттенками, но отличаются высокой ценой.
В России террасная доска из ДПК изготавливается, в основном, из лиственницы, которая в достаточных количествах распространена в наших лесах. Высокие водостойкие показатели лиственницы позволяли в старину изготовлять из неё корабельные суда, её, в отличие от перечисленных экзотических пород, легко тонировать в различные оттенки. Стоимость такого декинга гораздо ниже материалов, изготовленных из экзотичных древесных пород.
Достоинства и недостатки
Перед обычной древесиной ДПК имеют следующие преимущества:
- Террасная доска ДПК не деформируется и не растрескивается.
- Обладает повышенной механической прочностью, позволяющей установку на поверхности любых тяжёлых предметов.
- Гарантированное не поражение плесенью и грибками, для чего нет необходимости в обработке антисептиками или специальными пропитками.
- Не поддержка процессов горения.
- Рифлёная ровная поверхность не скользит и не приводит к получению заноз.
- Сохранение цветовых оттенков даже при длительных воздействиях ультрафиолетового излучения.
- Высокая атмосферно-, водо- и химическая стойкость.
- Эксплуатация при температурах от минус 50-ти до плюс 80-ти градусов.
- Отсутствие сучков и шероховатостей.
- Долговечность ≥ 50-ти лет.
- Лёгкое изгибание при нагреве, что позволяет изготовление уникальных по оригинальности изделий.
- Разнообразие цветовой гаммы, которую невозможно получить при использовании натурального дерева.
К плюсам декинга из ДПК можно отнести и следующее:
- возможность строгать, пилить, клеить, вбивать гвозди и завинчивать саморезы, болты и шурупы;
- экологичность, отсутствие неприятных запахов и не выделение вредных летучих веществ в атмосферу;
- хорошее удержание крепёжных элементов без их дальнейшего ржавления;
- сохранение теплопроводности и аромата, присущего натуральному дереву;
- антистатичность;
- простая обработка и монтаж;
- безопасная и комфортная эксплуатация с отсутствием необходимости в тщательном уходе;
- совмещение практичности пластиков с достоинствами натуральной древесины;
- малый вес.
Единственный недостаток — высокая цена материала. Небольшим минусом является незначительное удлинение линейных размеров при нагреве солнечными лучами, что необходимо учитывать при устройстве напольных покрытий на открытом воздухе.
Области применения
Благодаря своим достоинствам древесно полимерные композиты широко применяются в следующих строительных областях, быту и промышленной сфере:
- в качестве сайдинга для отделки фасадов;
- мощения различных площадок, открытых террас из ДПК, садовых дорожек, подходов к бассейнам и сходов в воду;
- заборы и ограждения;
- обустройства в городских парках и на приусадебных участках цветочных клумб и композиций;
- основания для уличного патио;
- возведения садовых беседочных комплексов;
- полы в ванных комнатах, саунах и банях, на лоджиях и балконах;
- изготовление оконных и дверных профилей, элементов кровли, интерьерной и садовой мебели;
- оборудование детских и спортплощадок;
- лаги, ступени, перила лестниц, всевозможная тара и поддоны;
- элементы для железнодорожного строительства, звукозащитные барьеры и переборки;
- морские и речные пирсы, мостики, сваи, палубы кораблей;
- в автомобилестроении — короба, спинки сидений, прокладки для дверей и крыш, подъёмные полки, внутренние панели и полы грузового транспорта.
Более 50-ти % изделий используются в качестве декинга.
Основные размеры:
- длина — 2…6 м;
- ширина — 95…141 мм;
- толщина — 26…45 мм.
Вес погонного метра — от 2-х до 3-х кг, кв. м — от 17-ти до 20-ти кг.
Монтаж террасной доски из ДПК, инструкция
Укладка выполняется 2-мя следующими способами:
- Открытым или клёпаным. Декинг крепится к лагам в предварительно просверленные отверстия саморезами насквозь. Название обусловлено тем, что головки саморезов остаются открытыми (они видны). Саморезы применяются только с антикоррозионной защитой.
- Скрытым, при котором крепление на лаги выполняется при помощи невидимых после монтажа специальных металлических крепёжных элементов с антикоррозионным покрытием или пластиковых кляймеров.
Укладка террасной доски из ДПК может выполняться бесшовным (швы до 1 мм) методом и со швами шириной от 2-х до 10 мм. Бесшовное покрытие устраивается на небольших площадях соединением металлическими пластинами и креплением к лагам по торцам. Для обеспечения вентиляции под покрытием обязательно устраиваются вентзазоры. Для водоотвода устраивается уклон в 2 ÷ 3 градуса. Такой метод применяется для закрытых веранд и помещений.
Покрытие со швами, в основном, применяется для облицовки больших площадей. Монтаж выполняется просто и на высокой скорости, с креплением досок к лагам кляймерами. Вода отводится через оставленные щели, через них происходит и вентиляция. Но в зазоры часто попадает мелкий мусор, могут прорастать сорняки или провалиться тонкий женский каблук.
Инструкция по хранению материала и его монтажу:
- Монтаж выполняется строго по инструкции производителя с участием не менее 2-х человек. Работы производятся только при плюсовых температурах.
- Составление схемы с определением оптимальных линейных размеров, лаг и досок, расчёта их потребного количества.
- Доски должны пройти адаптацию к условием среды, в которой будут укладываться, поэтому их раскладывают на ровной поверхности на поперечные прокладки, уложенные с шагом 40-к см, и оставляют на 2-ва дня. Изделия не должны соприкасаться с землёй и строительным мусором.
- Каждая доска должна быть тщательно осмотрена, после установки заменить её, даже при наличии гарантии, невозможно.
-
Лаги должны быть только из ДПК или алюминия, просто дерево недопустимо. К установке лаг предъявляются следующие требования:
- рекомендуемая длина элементов — 3-и м;
- шаг расположения — ≤ 40-ка см;
- по торцам 2-х см зазор от любых неподвижных деталей и отрезков лаг;
- не допустимо вмуровывание деталей в бетон, нахождение их в воде, склеивание между собой и жёсткое крепление к основанию. Для прижима применяются скобы из алюминия или нержавеющей стали;
- укладка лаг производится вниз рифлёной стороной и канавкой, выполненной посередине, вверх. Это позволяет установку шурупов с клипсами по центру монтажных лаг.
Горизонтальность лаг проверяется лазерным уровнем, допустимые отклонения ≤ 5-ти мм.
- Монтаж террасных досок. Доски монтируются в разбежку со смещением стыков на треть длины доски. В местах стыков укладываются две опорные лаги, чтобы торцы каждой доски опирались на разные лаги. При креплении шурупами в досках просверливаются отверстия равные ¾ их диаметров. Плотность и равномерная фиксация обеспечивается при помощи резиновой киянки. Если края последних рядов нельзя зафиксировать клипсами, то выполняется крепление саморезами или гвоздями, расположенными на 3-и мм от краёв.
- Окантовка покрытия по периметру торцевыми планками с креплением саморезами.
Чтобы настил получился качественным, при выборе материала необходима тщательная проверка на отсутствие видимых дефектов. На торцевых срезах хорошо заметны волнообразности и вздутия, свидетельствующие о технологических нарушениях при изготовлении. От таких приобретений лучше отказаться.
Древесно-полимерный композит (ДПК): состав, преимущества материала
Что такое древесно-полимерный композит (ДПК), и в чем его преимущества?
Древесно-полимерный композит (ДПК) – современный материал, который активно используется в строительных и отделочных работах. Материал ДПК – это оптимальная альтернатива дереву и пластику ПВХ, так как совмещает преимущества дерева и полимера, а именно – экологичность, тактильные ощущения, натуральный вид с одной стороны, с другой – прочность и устойчивость к агрессивным воздействиям внешней среды. Срок эксплуатации доски из ДПК достигает 25 лет.
В чем разница ДПК от ДВП, ДСП или МДФ
Материалы ДПК, ДСП, ДВП, МДФ – комбинации дерева и полимера, только древесно-полимерный композит по составу и технологии производства отличается от остальных. Для изготовления ДПК дерево измельчают в порошок. Процентное содержание древесной муки составляет 30-80% от общей массы. Остальные компоненты ДПК – это малогорючий и безопасный полимер (полистирол, полиэтилен, полипропилен или поливинилхлорид), а также химические добавки, которые улучшают технологические свойства материала (цвет, прочность).
Главные преимущества древесно-полимерного композита
- Первая особенность (и главное преимущество) древесно-полимерного композита — возможность производства методом экструзии, доставшаяся «в наследство» от пластиковой составляющей. Что это значит? А это значит, что, во-первых, материал в разогретом состоянии очень пластичен и позволяет получать изделия практически любой формы и конфигурации. Во-вторых, большая часть отходов, образовавшихся при обработке таких изделий, пригодна для вторичной переработки.
- Вторая особенность ДПК — это то, что благодаря древесной составляющей изделия из него могут не только выглядеть, как натуральное дерево, но и иметь запах древесины, интенсивность которого зависит от породы, использованной для приготовления муки, и процентного соотношения в составе материала. Иными словами, при практически одинаковой стоимости доска или плитка, изготовленная из древесно-полимерного композита, может с одинаковым успехом имитировать как запах дуба или сосны, так и аромат мербау или кумару.
- Третья особенность — то, что при всём визуальном, тактильном и ароматическом сходстве с деревом ДПК совершенно не подвержен обычным для него поражениям (гнили, плесени, жучкам, выцветанию и т.п.). А значит — не нуждается в дополнительной обработке.
Изделия из древесно-полимерного композита
- Террасные покрытия из ДПК – оптимальное решение для дачных террас, веранд, для ресторанов и различных заведений на открытом воздухе. По качеству материал успешно конкурирует с покрытиями из лиственницы, «бразильского ореха» и других пород, при этом стоимость террасных систем из ДПК на 30-70% дешевле натуральных аналогов, а срок службы – свыше 20 лет. Широкий ассортимент террасных систем от «Террадек» позволяет реализовать любые дизайнерские решения.
- Ограждения и заборы из ДПК отлично вписываются в ландшафтный дизайн. Такие изделия красивы, прочны и долговечны, что особенно важно для конструкций, установленных на открытом воздухе. Они даже более устойчивы к атмосферным воздействиям, нежели их аналоги из дерева или металла. Срок эксплуатации таких изделий из древесно-полимерного композита составляет 25 лет и более.
- Вентилируемые фасады из древесно-полимерного композита позволяют не только защитить внешние стены от воздействия окружающей среды и придать облику здания более эстетичный вид, но и обладают отличной звукоизоляцией и теплосберегательными свойствами. Используются такие фасады для интерьерной отделки нижних этажей любых сооружений, малоэтажных офисных зданий, частных домов.
Преимущества декинга ДПК
Ищете террасное покрытие на долгие годы? Выбирайте террасу из древесно-полимерного композита (ДПК). ДПК надежен и практичен, прослужит долгие годы, не требуя особого ухода, покраски и антисептика. Доска ДПК подходит к любому дизайну, так как обладает приятной текстурой натурального дерева и богатой цветовой палитрой.
Не скользит
Отвечает экологическим нормам
Долговечен
Прост в уходе
Не нуждается в пропитке
Не гниет, не плесневеет
Не портится насекомыми
Пожароустойчив
Влагоустойчив
Выдерживает вес до 2000 кг/м2
Не выцветает
Заноза исключена
«Жидкое дерево» или всё о древесно-полимерном композите — ВикиСтрой
Последние 40 лет развития промышленности смело можно назвать «эрой комбинированных материалов». Современное оборудование и технологии позволяют соединить, казалось бы, несовместимое: дерево, бетон, пластик, бумага, металл. Все они смешиваются, диффузируются, сплавляются с одной целью — получить новый продукт, сочетающий в себе наилучшие свойства нескольких исходных материалов. Так, среди прочих новинок мы увидели «жидкое дерево».
Что такое «жидкое дерево»
Говоря техническим языком, это экструдированный древесно-полимерный композит (ДПК). Это значит, что древесная составляющая законсервирована с помощью пластика. В такой комбинации материал принимает наилучшие свойства:
Технологический процесс прост для понимания, но довольно сложен для исполнения. Полимер (пластик) смешивают в определённой пропорции с древесной мукой и нагревают так, чтобы он расплавился. Затем формуют в экструдере, на вальцах или в пресс-формах и охлаждают. На разных этапах в массу подмешивают около 10 разных присадок — пластификаторы, катализаторы, упрочнители и другие. Все подробности изготовления — сорт древесины и марка пластика, пропорции смеси, присадки, температурные режимы, как правило, составляют производственную тайну. Известно, что все ингредиенты можно приобрести в свободной продаже, а для древесной муки преимущественно выбирают бамбук, лиственницу и другие прочные породы средней ценовой категории.
Для изготовления ДПК создаются специальные многоступенчатые производственные линии. Они состоят из множества устройств и контроллеров. Собрать такой станок своими руками в гараже, к сожалению, не получится. Но можно приобрести готовую производственную линию.
Видео — как делают «жидкое дерево»
Продукция из ДПК
В настоящее время ассортимент продукции неполон, т. к. материал относительно новый и свойства его до конца не изучены. Однако несколько наиболее востребованных позиций можно упомянуть уже сейчас.
Террасная доска или декинг
Составляет до 70% всей востребованной продукции из ДПК на сегодняшний день. Большая часть поставляемых производственных линий ориентирована на выпуск именно такой доски, т. к. это единственная на данный момент альтернатива дереву. Доска состоит из рамки периметра, рёбер жёсткости внутри и имеет пазогребневую систему крепления. Предлагаются различные цвета.
Преимущества перед традиционным материалом: от дерева доску ДПК выгодно отличает сплошной прокрас и лучшие физические показатели (прочность, гибкость, точность обработки). Многие виды доски ДПК выпускают двусторонними — с рельефами массива дерева и ребристой нарезкой.
Террасная доска ДПК на видео
Облицовочные фасадные панели или планкен
По большому счёту, их можно соотнести с виниловым сайдингом — принцип монтажа и структура панели у них очень похожи. Но панель ДПК значительно толще и жёстче, соответственно, имеет больший вес и лучшие физические свойства.
Преимущества перед традиционным материалом: более прочный и долговечный фасад, пазухи в панелях и толстые стенки лучше удерживают тепло и поглощают шумы.
Заборы, ограды, перилла, балюстрады
Формы малой архитектуры из «жидкого дерева» для декоративной отделки экстерьера и ландшафта. Имеют хорошую несущую способность и пригодны для интенсивной эксплуатации (в людных местах).
Такие изделия принято было выполнять из дерева (недолговечного и требующего ухода) или бетона (тяжёлого, холодного и не всегда надёжного). Древесно-композитные формы делают сборными, причём все детали проектируют заранее. На месте остаётся только собрать их при помощи болгарки и шуруповёрта. Такой забор не требует мощного фундамента, постоянной окраски. В случае повреждения участка или элемента конструкции, его можно легко заменить, изготовив дополнительно нужное количество деталей.
Общее преимущество — абсолютная нечувствительность к атмосферному износу (влага, мороз, перегрев на солнце), насекомым, грибкам и истиранию.
Общий недостаток — относительно большие колебания при нагреве и охлаждении. Расширение террасной доски ДПК может составлять до 6 мм на 1 м (при постепенном нагреве до +40 °С).
Цены на фасадные панели из «жидкого дерева»
Наименование | Производитель | Характеристики | Цена 1 м2, у. е. |
Duo Fuse FPS-22 | Бельгия | 2800х220х22 мм, ПВХ | 35 |
«МультиПласт» | Россия | 3000х166х18 мм, ПЭ | 20 |
RINDEK | Россия | 3400х190х28 мм, ПВХ | 22 |
CM Cladding | Швеция | 2200х150х11 мм, ПВХ | 28 |
ITP («Интехпласт») | Россия | 3000х250х22 мм, ПВХ | 26 |
DORTMAX | Россия | 4000х142х16 мм, ПЭ | 18 |
Как выбрать террасную доску из ДПК
Любой вид «жидкого дерева» производится из древесной муки, состав которой не столь важен. Но состав полимера, который добавляется к ней, может иметь решающее значение:
По типу профиля террасные доски делятся на два типа:
По типу соединения доски ДПК делятся на:
По типу противоскользящего покрытия или обработки:
На что обратить внимание вне зависимости от выбранного типа доски:
Видео — как выбрать террасную доску ДПК
Совершенно справедливо можно принимать данные советы по отношению к фасадным панелям и другим изделиям из ДПК для облицовки плоскостей.
Индустрия обеспечивает обывателя возможностью сделать свой выбор — использовать новый натуральный материал, на который идут природные ресурсы (дерево, камень) или применить продукцию переработки вторсырья. Сегодня люди научились превращать отходы обработки натуральных материалов в продукцию, опережающую эти материалы по свойствам. Однако выбор остаётся за человеком — либо утилизировать мусор, приобретая ДПК, либо создавать его всё больше, отдавая предпочтение природным материалам.
рмнт.ру