Изготовление современных сверл — Мекка инструмента
Сверло — это, в первую очередь, режущий инструмент для создания отверстий в каком либо материале, а также для увеличения диаметра существующих отверстий.
Принцип сверления заключается в двух движениях, происходящих одновременно: вращении и поступательном движении вдоль своей оси. В основном применяются следующие типы сверл: спиральные, пушечные, перовые, ружейные, центровочные, специальные, а также для кольцевого сверления. В настоящее время при изготовлении сверл применяют такие виды обработки металла как секторно-поперечная, продольная и винтовая прокатка. А для изготовления заготовок применяется прокатка на вальцах и холодная калибровка. Сверла выполняются из специальной режущей стали разных марок.
Основным типом сверл являются спиральные, они наиболее распространены в разных отраслях промышленности для сверления и рассверливания отверстий не более 80 мм диаметром. Такие сверла состоят из режущей и направляющей частей, хвостовика и обычной соединительной части.
Конструкция строения режущей части определяет его конкретное значение и условия работы. Направляющая часть предназначена для создания определённого направления при работе, имеет две винтообразные ленточки, которые в ходе сверления сцепляются с рабочей поверхностью обрабатываемого отверстия. Большинство современных спиральных сверл изготавливаются из твердого сплава. Сверление такими твердосплавными сверлами происходит на высоких режимах и с увеличенным объемом стружки, которая по стружечным канавкам охлаждающей жидкостью вымывается из отверстия. Жидкость подаётся по каналам под высоким давлением.
Направляющая часть включает в себя дополнительные режущие кромки в виде ленточек, которые участвуют в калибровании поверхности обрабатываемого отверстия. Помимо этого направляющая часть предназначена для дальнейшей переточки инструмента. Также она обеспечивает выведение стружки из рабочей зоны. Хвостовик предназначен для фиксации сверла в зажиме станка, при помощи цилиндрической шейки, которая соединяется с рабочей частью. Чаще всего она делается из быстрорежущей, а хвостовик из обычной стали, а затем рабочая часть и хвостовик соединены путём сварки. В технической промышленности также довольно часто применяются специальные твердосплавные материалы. Такие сверла оснащены вставками из твердых сплавов либо твердосплавными коронками.
Технология изготовления сверла по металлу
Технология изготовления сверл
Пайка – процесс соединения пластинок из быстрорежущей стали и державок инструмента, который осуществляется с помощью специальных сварочных порошков с высокой температурой плавления. Для пайки пластинок применяют сварочный порошок из ферромарганца и буры (натриевая соль тетраборной кислоты). Чтобы понизить температуру плавления сварочного порошка, в него добавляют медь.
Чтобы уменьшить расход дорогостоящей инструментальной стали, улучшить качество изделий и снизить трудоемкость их изготовления, при изготовлении заготовок взамен обработки резанием используют методы обработки давлением. При этом удается в некоторых случаях после применения методов обработки давлением получить форму и размеры изделия (или отдельных его элементов) с достаточно высокой точностью, что исключает необходимость дальнейшей механической обработки.
В настоящее время в инструментальной промышленности при изготовлении режущего инструмента применяют следующие виды обработки металлов давлением: секторную, поперечную и продольно-винтовую прокатки для изготовления заготовок сверл; ковку на молотах, прокатку на вальцах, холодную калибровку для изготовления заготовок напильников; безоблойную штамповку насадного режущего инструмента для изготовления других инструментов.
Рассмотрим некоторые особенности технологических процессов изготовления названных выше инструментов.
Развитие и применение пластической деформации при изготовлении заготовок сверл обусловлено тем, что все применяющиеся для них методы пластической деформации заготовок соответствуют основному современному технологическому требованию – приблизить профиль заготовки к профилю готового изделия. Это позволяет при изготовлении сверл сэкономить до 40 % дорогостоящей быстрорежущей стали, снизить трудоемкость изготовления изделий за счет исключения трудоемких операций фрезерования канавок.
Секторной прокаткой изготовляют в настоящее время заготовки сверл диаметром 15…50 мм. Этот метод широко распространен на инструментальных заводах страны и охватывает около 80 % общего выпуска сверл в указанном диапазоне диаметров. Причем выпуск сверл из заготовок, полученных секторной прокаткой, из года в год увеличивается.
При секторной прокатке цилиндрические механически обработанные заготовки из быстрорежущей стали нагревают в соляных ваннах до температуры прокатки (1100… 1200 °С). 3атем их прокатывают на специальных завивочных станках, после чего производят последующую термическую и механическую обработку.
Секторная прокатка положена в основу технологического процесса изготовления сверл и с прокатанными отверстиями для охлаждения. Сверла этого типа предназначены для высокопроизводительного сверления сталей, сплавов и других труднообрабатываемых материалов в тяжелых условиях, при которых затруднено охлаждение в зоне резания и не обеспечен надежный отвод стружки при сверлении. Технологический процесс изготовления сверл с отверстиями для охлаждения обладает всеми преимуществами, присущими методу сектор ной прокатки, а также позволяет исключить трудоемкую операцию сверления глубоких отверстий. Профиль сверла, а также профили отверстий для охлаждения, расположенных по всей длине рабочей части, получают пластической деформацией нагретых до температуры прокатки специальных заготовок.
Дальнейшее усовершенствование секторной прокатки заготовок сверл идет главным образом в направлении повышения точности по профилю и по шагу винтовой стружечной канавки, а также в направлении улучшения внешнего вида сверл.
Виды сверл: типы, назначение, особенности
Виды сверл в зависимости от формы рабочей поверхности
Винтовое или спиральное. Самое востребованное сверло, используется для сверления самых различных материалов. Длина спирального сверла может достигать 28 см, диаметр – 80 мм.
Плоское или перьевое. Используется для сверления преимущественно глубоких, больших по диаметру отверстий. Рабочая часть имеет форму лопатки, в центре которой расположено выступающее острие для центровки. Лопатка может быть выполнена заодно с хвостовиком или быть сменной и крепиться к стержню с помощью державки или борштанги.
Сверло для глубокого сверления. Предназначено для выполнения отверстий, глубина которых, по меньшей мере, в 5 раз больше, чем диаметр. Сверло глубокого сверления имеет два винтовых канала, по которым в зону реза подается охлаждающая эмульсия. Каналы могут располагаться внутри сверла либо в припаянных трубках.
Сверло одностороннего реза. Применяется для сверления отверстий, к которым предъявляются повышенные требования в отношении точности. Сверла одностороннего резания имеют опорную плоскость и две режущие кромки, расположенные с одной стороны от центра.
Коронка или кольцевое сверло. По виду это полый цилиндр. Резание осуществляется стенкой цилиндра, на которой располагается режущая кромка. Сверление получается в виде кольца, внутри которого находится нетронутый материал (керн). После сверления он обычно остается в коронке, нужно только вытряхнуть его.
Центровочное сверло. С его помощью выполняется засверливание (наметка) центра.
Ступенчатое сверло. Относительно новый вид инструмента. Ими удобно сверлить листовой материал, особенно в тех случаях, когда нужно получить большое по диаметру отверстие – до 3,5 см и более.
По форме получающегося отверстия сверла подразделяются на конические, цилиндрические и ступенчатые.
Типы хвостовиков
В зависимости от формы и способа крепления в патроне или шпинделе хвостовики бывают:
- цилиндрические – наружная поверхность имеет форму цилиндра;
- конические – поверхность выполнена в виде конуса;
- граненые – на наружной поверхности имеются 3, 4 или 6 граней;
- типа SDS – хвостовик для крепления в патроне с особым фиксирующим механизмом.
Крепление самых распространенных в быту цилиндрических сверл производится в обычном патроне. Инструменты с коническим хвостовиком предназначены для использования на станках. Хвостовик типа SDS рассчитан на закрепление в перфораторе.
Технология изготовления сверл
Сверла относительно небольших диаметров (до 8-10 мм) обычно изготавливают из цельного прутка стали или сплава. Чаще всего используется быстрорежущая сталь марок Р9, Р9К15, Р18. Сверла больших диаметров изготавливают с помощью сварки; режущая часть выполняется из быстрорежущей стали, а хвостовик – из обычной углеродистой.
Для сверления твердых материалов – закаленной и легированной стали, камня, бетона – применяют сверла, которые на конце имеют припаянные твердосплавные пластины из победита или другого твердого сплава. Режущие кромки пластин могут иметь различную конфигурацию: винтовую, скошенную или прямую.
Виды покрытия
Сверла покрывают с разной целью: предохранения от коррозии, упрочнения поверхностного слоя, улучшения теплоотдачи, снижения трения. Самая распространенная и недорогая операция – оксидирование. Сверло покрывается оксидной пленкой черного цвета, которая защищает его от ржавчины и перегрева.
Покрытие нитридом титана (TiN) повышает срок службы сверла не менее чем в три раза. Однако такие сверла нельзя затачивать, поскольку при этом снимается упрочненный слой. Использующийся также для покрытия карбонитрид титана (TiCN) по своим свойствам близок к TiN.
Титано-алюминиевый нитрид (TiAlN) делает сверло еще более прочным. При его использовании инструмент может проработать в 5 раз дольше обычного.
Самым прочным покрытием считается алмазное напыление. Это и неудивительно. Алмаз занимает первое место по твердости среди прочих материалов. Сверла с алмазным напылением могут использоваться для сверления практически любых по твердости материалов, в том числе и каменных.
О чем говорит окраска сверла?
По цвету покрытия можно примерно определить характеристики сверла. Сверла обычного качества имеют характерную для стали серую краску.
Черный цвет говорит о том, что сверло подвергалось оксидированию. То есть, оно защищено от коррозии, и имеет улучшенные теплоотводящие свойства.
Легкий золотистый оттенок сообщает о том, что сверло прошла процедуру отпуска, во время которого снимаются внутренние напряжения.
Нитридное титановое покрытие проявляет себя ярким блеском позолоты. Сверла с ним имеют увеличенный срок службы и низкое трение при сверлении. Хотя они и стоят дороже, но с лихвой оправдывают свою цену длительной эксплуатацией.
Алмазное напыление можно узнать по желтому цвету и порошкообразной фактуре.
Сверла для металла
Для сверления металлов (стали, чугуна, цветных сплавов) обычно применяют спиральные сверла. Их продольные канавки хорошо справляются с отведением стружки, образующейся при сверлении.
Обрабатываемые материалы имеют различную твердость. Поэтому для их сверления должны использоваться сверла с разной твердостью рабочей части. Для обработки закаленных, легированных, жаропрочных сталей необходимо применять цельные твердосплавные сверла или те, которые имеют на кончике припаянные пластины из твердого сплава.
Сверла для древесины
Относительно небольшие отверстия до 12 мм в древесине или древесных композитах (ДСП, МДФ) можно сверлить обычным спиральным сверлом для металла. Но отверстия, к которым предъявляются повышенные требования по точности размеров и чистоте поверхности выполняют сверлами, специально предназначенными для древесины. Их изготавливают из инструментальной или углеродистой стали и для металла они не годятся.
Спиральные сверла. Предназначены для сверления малых и средних по диаметру отверстий. Как уже отмечалось, вместо них можно использовать спиральные сверла для металла, но отверстия после них получаются хуже качеством.
Винтовые сверла. Имеют острую режущую кромку и шнекоподобную форму. Благодаря последней из отверстия легко удаляется стружка. Это качественные сверла, которые применяют, если требуется получить глубокое отверстие с гладкой стенкой.
Перьевые сверла. Используются для получения отверстий относительно больших диаметров – от 10 до 25 мм и более. Это самые простые и недорогие сверла, их можно даже изготовить самому из подходящей пластины и круглого стержня. Но качество отверстий после них получается невысоким – шершавые стенки, не очень точные размеры.
Коронка. Термин «коронка» говорит о том, что этот инструмент выполнен в виде полого цилиндра, на кромках которого располагаются зубья. Сверление получается в виде кольца, из которого затем удаляется внутренняя часть. Коронка – незаменимый инструмент, если требуется получить большое отверстие – до 100 мм и более. В магазинах ее предлагают в виде набора, в котором имеется оправка, центровочное сверло с хвостовиком и несколько коронок разных диаметров.
Сверло Форснера. Это инструмент для выполнения точных отверстий в древесине (особенно мягкой), ДСП, ламинате и пр. У него имеется центровочное острие и подрезатель с острой кромкой. Благодаря последнему отверстие получается точным и гладким. Если нужно получить глухое отверстие с гладкими стенками и точными размерами, сверло Форснера справится с этой работой наилучшим образом.
Сверла для каменных материалов
Для сверления кирпича, бетона, натурального или искусственного камня обычные сверла по металлу не годятся. Они мгновенно тупятся. Сверло или бур для каменных материалов должны иметь наконечник из твердых сплавов.
Сама операция сверления бетона, кирпича или камня также имеет особенности. Кроме вращательного движения, сверло или бур, вставленные в перфоратор, осуществляют еще и ударно-поступательное. Т. е. камень, по сути, не режется, а дробится.
Бур или сверло для перфоратора может иметь обычный цилиндрический, или особый стандартизированный хвостовик типа SDS (SDS-top, SDS-max или SDS-plus). Его преимущество состоит в том, что вставка и извлечение бура из патрона осуществляется без ключа и очень быстро, одним движением.
Небольшие и средние по диаметру отверстия в кирпиче и бетоне сверлят буром или сверлом с твердосплавным наконечником. Инструмент имеет форму шнека.
Если требуется просверлить большое отверстие, то применяют коронку с твердосплавными зубьями или алмазным напылением. Бурение может быть влажным (с подачей воды для охлаждения) и сухим. По окончании сверления внутри коронки остается керн – цилиндрический кусок вырезанного материала.
Твердосплавные пластины, припаянные к сверлу или буру, имеют разную твердость. Для сверления гранита применяются буры с пластинами из победита высокой твердости. Для работы с бетоном или кирпичом годятся средние или мягкие по твердости марки победита.
Сверла для керамики и стекла
Керамическую плитку или стекло сверлят коронкой или специальным копьевидным инструментом. Его наконечник изготовлен либо из победита, либо из карбида вольфрама. Если специализированный инструмент для стекла или плитки отсутствует, можно использовать сверло для бетона. Только обязательно острое, и работать им нужно осторожно, поскольку его форма не совсем подходит для такой работы.
Копьевидное сверло для плитки из керамики и коронка с алмазным напылением.
Коронка для стекла и кафеля почти не отличается от коронки для камня. Только на ее режущей кромке вместо зубьев имеется алмазное напыление.
Для сверления в кафеле больших отверстий используют инструмент, называемый балериной. Он напоминает обычный циркуль. Сверление производится с изнаночной стороны плитки. Обороты дрели устанавливают на минимум.
Универсальные сверла
Кроме вышеперечисленных специализированных сверл, есть еще универсальные. Ими можно обрабатывать практически любые материалы – кирпич с бетоном, плитку, дерево, пластик, алюминий, сталь. Универсальные сверла имеют хитроумную заточку, которая способна резать любой материал. Это очень удобно в тех случаях, когда приходится работать одновременно с разными материалами. Например, при ремонте квартиры.
Производство сверл
Содержание
В этой статье мы расскажем все о производстве сверл. Вы узнаете:
по какой технологии изготавливают обычные спиральные сверла;
какие материалы идут на производство;
на каком оборудовании выполняют основные технологические операции по производству сверл по металлу;
какие особенности имеют термическая обработка и сварка.
Фотография №1: изготовление сверла по металлу
Технология изготовления сверл
Технологический процесс изготовления спиральных сверл по металлу с коническими хвостовиками состоит из такой последовательности операций.
Отрезка заготовки для хвостовой части.
Отрезка заготовки для рабочей части.
Зачистка торцов у хвостовой части.
Зачистка торцов у рабочей части.
Очистка заготовки на пескоструйном аппарате.
Обдирка наплыва у сварного шва.
Правка заготовки после сварки.
Подрезка торца со стороны хвостовика.
Сверление и зенкерование центрового отверстия со стороны хвостовика.
Обточка наружного центра со стороны рабочей части.
Обточка рабочей части по диаметру, предварительная и окончательная.
Обточка хвостовика на конус, предварительная и окончательная.
Обточка хвостовика под лапку и подрезка торца.
Фрезерование спиральных канавок.
Фрезерование спинки зуба.
Термообработка и очистка на пескоструйном аппарате.
Полирование спиральных канавок.
Шлифование хвостовика на конус.
Шлифование рабочей части по диаметру с обратным конусом.
Контроль и клеймение.
Материалы для изготовления сверл по металлу
В России для изготовления сверл по металлу используют такие материалы, как быстрорежущие стали и твердые сплавы. Перечислим распространенные марки первых.
Р9 и Р18. Похожие по характеристикам стали. Первая содержит 9 % вольфрама, а вторая — 18. Сверла из этих сталей хорошо сверлят, не перегреваются и служат долго.
Р6М5 (зарубежный аналог — сталь HSS). Сверла по металлу из этой быстрорежущей стали встречаются чаще всего. Она содержит 6 % вольфрама и 5 % молибдена. Инструментами из этого материала обрабатывают:
Р6М5К5 (зарубежный аналог — сталь HSS-Co). Этот сплав содержит не только молибден и вольфрам, но и 5 % кобальта. Сверла из стали Р6М5К5 прочнее аналогов из сплава без добавления кобальта.Такими инструментами обрабатывают:
Твердосплавные сверла отличаются от инструментов, изготовленных из быстрорежущей стали, более высокими прочностью и долговечностью. На производство идут 4 вида сплавов.
безвольфрамовые (на основе TiC, TiCN с никель-молибденовой связкой).
Покрытия, улучшающие характеристики сверл
При производстве сверл по металлу для улучшения их свойств на рабочие части и хвостовики наносят два вида покрытий.
Нитрид титана. Твердость поверхностных слоев таких сверл увеличивается на 2300 HV. Термостойкость повышается до 600°.
Нитрид титана, легированный алюминием. Твердость поверхностных слоев таких сверл увеличивается на 3000 HV. Термостойкость повышается до 900°.
Фотография №2: сверло с покрытием из нитрида титана
Сверлами с такими покрытиями обрабатывают:
детали из твердых и улучшенных сплавов;
заготовки из ковкого и серого чугуна, в котором графитовые включения имеют шаровидную форму.
Если вам важны максимальные надежность и износостойкость, покупайте именно такие инструменты. Подробную информацию о выборе сверл по металлу вы найдете здесь.
Станки для изготовления сверл
Для производства обычных сверл используют следующие основные станки, аппараты и приспособления.
Электросварочные стыковые машины.
Станки для производства сверл
Перечислим технологические операции изготовления сверл и назовем станки, аппараты и приспособления, которые применяют для обработки, к примеру, заготовок для инструментов с диаметрами от 0,1 до 1 мм, имеющих утолщенные хвостовики.
Токарная обработка. Для нее применяют продольно-токарные автоматы 1103.
Термическая обработка. Производится в электродных соляных ваннах.
·Отпуск и промывка. Сверла при их выполнении помещают в специальные сетчатые корзины.
Шлифование хвостовиков. Применяется шлифовальный станок ЗМ-180 или МФ-63.
Доводка рабочих частей сверл. Для этой операции используют специальные доводочные станки типа Штейнель.
Шлифование рабочих частей. Выполняется на бесцентрово-шлифовальном станке МФ-63АП при ручной подаче.
Шлифование стружечных канавок. Для него предназначен специальный шлифовальный станок МФ-202.
Заточка. Проводится на станке 64А с применением бинокулярного микроскопа.
Для производства сверл с диаметрами до 12 мм используют иное оборудование.
Шлифование сверл по цилиндрическим поверхностям. Для обработки заготовок с диаметрами до 2 мм применяют станок ЗМ-180 или МФ-63. Более крупные заготовки шлифуют на станке ЗМ-182.
Вышлифовка стружечных канавок. Заготовки с диаметрами до 2 мм обрабатывают на станке М-202П или М3460. Для шлифования более крупных сверл применяют станки 3А650, 3А682, 3А683, 3657, 3А684 и 3А684К.
Заточка и подточка. Эти операции выполняют на станках 3А681, 3А650 и 3А682.
Консервация и упаковка. Для них предназначены специальные аппараты НО-2012, НО-2712 и НО-1894А.
Особенности изготовления сверл, дополнительные методы улучшения характеристик инструментов
Расскажем об особенностях выполнения самых важных операций, входящих в технологию изготовления сверл, и опишем методы, которые используют для улучшения основных характеристик инструментов.
Термическая обработка
Имеет очень важное значение. От правильности выполнения термической обработки напрямую зависят износостойкость инструмента и качество стали.
Закалку проводят в ваннах с расплавленными солями или в печах (электрических и газовых). В некоторых случаях для изготовления сверл применяют оборудование с вакуумом или восстановительной атмосферой.
Для отпуска используют масла, щелочи, соли и воду. Часто заготовки охлаждают на воздухе.
Обратите внимание! Режимы термообработки имеют особую важность. Поэтому все процессы контролируются автоматически.
Контактная стыковая сварка
Выполняется на специальных электросварочных машинах. Существуют три технологии.
Сварка непрерывным оплавлением без подогрева. Технология отличается высокой производительностью. Недостаток — большой расход металла на оплавление и осадку.
Сварка с подогревом прерывистым оплавлением. Протекает немного дольше. Расход металла значительно уменьшается.
Сварка с подогревом сопротивлением. Металл практически не расходуется, но операция требует высокой квалификации рабочих.
Чаще всего используют второй метод.
Фотография №3: контактно-стыковая сварка
Дополнительные методы улучшения основных характеристик сверл
Перечислим технологии, которые применяют при изготовлении сверл для дополнительного улучшения их свойств.
Цианирование. Поверхности рабочих частей насыщают азотом и углеродом. Цианирование повышает прочность инструментов в 2–3 раза.
Сульфидирование. Поверхностные слои сверл насыщают серой. Сернистые соединения снижают трение и повышают износостойкость инструментов в 1,5–2 раза.
Обработка водяным паром. После нее инструменты помещают в масло. На поверхностях образуются черные пленки окислов. Прочность сверл, прошедших такую обработку, увеличивается вдвое.
Заводы по производству сверл
Производство качественных сверл по металлу налажено на огромном количестве заводов в России и за рубежом. Популярностью пользуется продукция под следующими торговыми марками.
Ruko. Компания специализируется на изготовлении сверл с крестовыми заточками. Типы напыления варьируются. Продукция сочетает в себе высокое качество и приемлемую стоимость.
Haisser. Твердосплавные сверла этого бренда — одни из самых лучших в мире. Изделия стоят дорого.
Bosh. Специализируется на изготовлении сверл с SDS-хвостовиками.
«Зубр». Один из лучших российский производителей.
SEKIRA. Это наша собственная торговая марка. Мы выпускаем сверла различных видов и габаритов. Характеристики всех изделий отвечают требованиям ГОСТов. Нашу продукцию вы можете приобрести по самой низкой цене.
Изучите каталог, выберите нужные вам сверла и оформите заказ. Мы доставим металлорежущие инструменты в установленный срок.
Виды сверл по металлу, их устройство и изготовление
Сверло по металлу: конструкция, геометрия, элементы сверла. Как и из чего делают сверла. Типы хвостовиков и маркировка. Выбор, применение и правила хранения. Лучшие производители и советы по выбору сверл по металлу.
В машиностроении сверло по металлу является вторым по частоте использования инструментом после резца, а в домашнем хозяйстве оно уверенно делит лидерство с ножовкой и отрезным кругом. Конструктивно сверло — это длинный цилиндрический стержень из металла с двумя режущими кромками на торце и спиральными канавками для отвода стружки. Принцип резания металла и формирования отверстия у всех типов этого инструмента практически одинаков, поэтому основная классификация сверл по металлу основывается на конструктивных признаках (тип хвостовика, профиль спирали, вид режущей кромки и т. п.). Определить по внешнему виду все необходимые характеристики сверла достаточно сложно, т. к. маркировка, которая гравируется на металле хвостовика, содержит информацию только о диаметре инструмента, материале изготовления и производителе. Поэтому для того, что выбрать сверло для обработки твердых, хрупких или вязких металлов и сплавов необходимо воспользоваться каталогами производителей. Длительное и краткосрочное хранение сверл должно осуществляться по определенным правилам, т. к. инструментальные и быстрорежущие стали склонны к коррозии, а заточенные кромки легко повреждаются при ударе о металл.
Конструкция и геометрия сверла
Любое сверло вне зависимости от его назначения и конструктивных особенностей состоит из двух основных компонентов: хвостовика и рабочей части. Первый служит для передачи инструменту вращения от привода или фиксации его в неподвижном состоянии (на токарных станках). Рабочая часть состоит из ряда элементов, непосредственно обеспечивающих процесс сверления. Геометрия сверла зависит от особенностей сверления, для которого оно предназначено, а также материала обрабатываемой заготовки (различные металлы, древесина, пластики, композиты, керамика).
В качестве примера взят один из самых распространенных в промышленности видов такого инструмента: спиральное сверло для работ по металлу с коническим хвостовиком (см. чертеж ниже). Все изображенные на рисунке углы сверла соответствуют работам по металлу общего назначения. Слева показан вид сбоку, а справа — со стороны рабочего торца (увеличено).
- Хвостовик. Служит для закрепления инструмента в шпинделе станка или зажимном патроне. При сверлении металла на токарных станках крепится неподвижно в конусе задней бабки.
- Рабочая часть. Формирует цилиндрическое отверстие (или углубление).
Состоит из режущей части, длина которой у таких сверл по металлу обычно составляет половину их диаметра, и направляющей с канавками для отвода стружки.
- Конус Морзе. Для установки в шпиндели и задние бабки станков используют инструмент с коническим хвостовиком, а для зажима в кулачковые и цанговые патроны — с цилиндрическим.
- Лапка. Эти конструктивные элементы присутствуют только на конических хвостовиках и предназначены для выбивания инструмента из шпинделя или оправки.
- Шейка. Обеспечивает удобство подвода и отвода шлифовального инструмента при обработке спиральных канавок. Она не выполняет никаких рабочих функций, поэтому на нее обычно наносится маркировка сверла (чеканится непосредственно на металле).
- Направляющая часть. Также называется калибрующей. Опираясь на стенки просверленного в металле отверстия, направляет инструмент вдоль его оси. Включает в себя спиральные поверхности с ленточками и канавки для отвода стружки.
- Угол наклона спиральной поверхности.
Для обработки металла он составляет 18÷30°.
- Стружкоотводящая канавка. От ее ширины, наклона и качества поверхности зависит скорость отвода стружки.
- Диаметр режущей части. Равен расстоянию между внешними краями режущих кромок.
- Режущая кромка. Это острая грань между передней поверхностью (стружечной канавкой) и задней затачиваемой поверхностью.
Общая компоновка других типов сверл по металлу подобна этой, хотя в зависимости от своего назначения они могут отличаться конструкцией режущей части и стружкоотводящих канавок.
Виды сверл по металлу
Среди специальных сверл самой большой группой является инструмент для глубокого сверления в заготовках из металла. Отдельные подгруппы также составляют изделия для сверления отверстий больших диаметров и ступенчатых цилиндрических профилей. Бывает так, что современный сборный инструмент имеет настолько сложную или инновационную конструкцию, что его относят сразу к нескольким типам.
Спиральная форма
Традиционным широко распространенным видом сверлильного инструмента являются спиральные сверла, у которых формирование цилиндрического отверстия в металле осуществляется двумя симметричными режущими кромками. При этом отвод образующейся стружки проходит по спиральным канавкам, начальная часть которых является передними поверхностями, образующими эти кромки. По своей конструкции эти изделия могут быть монолитными или сборными, с заменяемой головкой или механическим креплением режущих пластин. Для снижения трения и повышения скорости отвода стружки спиральную часть полируют и покрывают износостойкими материалами.
Ступенчатая форма
Корончатые сверла
Шнековые сверла
Перовые сверла
Типы хвостовиков
Маркировка сверл согласно ГОСТ
Правила маркировки сверл регламентированы ГОСТ 2034-80. Согласно этому документу на сверлильный инструмент диаметром менее двух миллиметров маркировка не наносится. Все данные о них должны указываться на упаковочной этикетке. Для сверл толщиной свыше двух и до трех миллиметров маркировка сверла по металлу содержит только значение диаметра и марку стали (таким образом их можно отличить от инструмента до двух миллиметров). Для диаметров свыше трех миллиметров в составе маркировки производитель должен указывать его величину, свой товарный знак, марку металла и класс точности. Марка металла, из которого изготовлен инструмент, может указываться как в виде ГОСТовского обозначения стали (например, Р6М7К6), так и общепринятой для быстрорежущих сталей международной аббревиатурой (HSS) с добавлением обозначения основного легирующего металла (Co, Ni, Ti и пр.) (см. фото ниже). Зарубежные изготовители маркируют свою продукцию аналогичным образом, поэтому отличить российские сверла от импортных можно только по торговой марке.
Цветовое обозначение
Кроме того, каждая группа резания подразделяется на группы применения, которые обозначаются числом в интервале от 1 до 40. Группы с большим индексом имеют более высокую прочность, а с меньшим — большую твердость и стойкость к износу.
Технология изготовления сверл
- Подготовка компонентов. Цилиндрические заготовки для обеих частей нарезают на прутковых автоматах, а затем очищают от заусенцев, поверхностных окислов и загрязнений.
- Сварка. Две части из разного металла сваривают контактной стыковой сваркой. После этого со сварных швов удаляют излишки металла, а заготовки правят для придания им точной цилиндрической формы.
- Обточка. Заготовки центруют и обтачивают до точного размера. На этом же этапе подрезают торцы, точат конус хвостовика, обтачивают конец конуса под лапку (у инструмента с цилиндрическим хвостовиком последние две операции отсутствуют).
- Фрезеровка. Фрезеруют лапку (для конических хвостовиков), спиральные канавки и задние поверхности. После этого заготовка подвергается термической обработке с последующей очисткой на пескоструйной установке.
- Шлифовка. Шлифуют и полируют канавки спиралей. После этого шлифовке подвергают хвостовик и рабочую часть (с доводкой обратного конуса).
- Заточка сверла.
Корпуса сборного сверлильного инструмента, в котором режущая часть выполнена из твердосплавных пластин с напайным или механическим креплением, являются достаточно сложными изделиями, т. к. при их изготовлении необходима сложная фрезерная и токарная обработка. Поэтому их обычно изготавливают на станках с ЧПУ или обрабатывающих центрах.
Таблица размеров сверл по металлу
Государственные стандарты, правила изготовления спиральных и центровочных сверл по металлу, включают в себя таблицы размерных рядов для разных исполнений и направлений вращения спирали. Каждому типоразмеру соответствует уникальное цифровое кодовое обозначение. К примеру, если диаметр сверла с цилиндрическим хвостовиком равен 3.1 мм, оно имеет исполнение N1 и правую спираль, то его общая длина должна составлять 65 мм, длина рабочей части — 36 мм, а кодовое обозначение такого изделия будет 2300-7517. Таблицы размеров для сверл по металлу с коническим хвостовиком включают в себя диапазон диаметров от 5 до 80 мм, а для инструмента с цилиндрическим хвостовиком — от 0. 25 до 20 мм. При этом для тонких сверл диаметром до 1 мм предусмотрено только исполнение N1 c правой спиралью.
Материалы изготовления и покрытия
Для улучшения рабочих характеристик сверл по металлу их поверхности подвергают дополнительной обработке или покрывают твердыми соединениями металлов. Самые распространенные методы обработки, повышающие прочность и износостойкость инструмента, — это цианирование и сульфидирование. А для защитных покрытий обычно используют карбонитрид титана (TiCN), в том числе легированный алюминием (TiAlN).
Как подобрать сверло под обрабатываемый металл
При выборе сверла для работ по металлу в первую очередь необходимо ознакомиться с цветовыми маркировками стандарта ISO 513, которых придерживаются все производители сверлильного инструмента. При этом нужно понимать, что такая маркировка не наносится на само изделие, а присутствует только в его каталожном описании. Можно, конечно, положиться на советы консультанта в магазине инструмента, но такой способ подойдет только в том случае, если требуется подобрать сверло для дрели, предназначенное для работы с обычной конструкционной сталью. Если же предстоит сверлить твердые или вязкие металлы или требуется качественное выполнение работы на заказ, то лучше следовать рекомендациям профессионалов. На рисунке ниже приведен пример использования цветовой маркировки из каталога Mitsubishi.
Необходимо также помнить, что параметры процесса сверления зависят как от характеристик сверла, так и от мощности и скорости вращения привода. Поэтому сверла для шуруповерта лучше не использовать с дрелью, т. к. это, скорее всего, приведет к их повреждению. А скорости вращения шуруповерта явно недостаточно для сверления металла обычными сверлами для дрели.
Сверла, применяемые в станках
На сверлильных станках, у которых посадочное отверстие шпинделя выполнено под конус Морзе, сверла для обработки металла устанавливаются напрямую в шпиндель. А для их фиксации в нем предусмотрен специальный сквозной паз для заклинивания лапки. Такие же сверла применяют и в универсальных станках (сверлильно-фрезерных и пр.), у которых посадочное отверстие шпинделя сделано под метрический конус или под одну из его современных разновидностей. Только в этом случае их вставляют в переходные оправки с соответствующим конусом. В целом сверла по металлу, используемые на станках, не отличаются от тех, что применяют при сверлении ручным инструментом. Единственный вид сверлильного инструмента, предназначенный только для станочного применения, — это сверла со сквозным каналом, предназначенным для подачи СОЖ в зону обработки (см. рис. ниже).
Лучшие производители
Среди российских производителей сверлильного инструмента для работ по металлу хорошее соотношение цены и качества имеет продукция Волжского инструментального завода (ВИЗ), Томского инструментального завода (ТИЗ) и ПО «Туламаш». К этой же категории относится инструмент украинского Запорожского инструментального завода (ЗИЗ). Самыми лучшими по качеству являются сверла всемирно известных производителей режущего инструмента, таких как немецкие Bosch, Hasser и Ruko, шведский Sandvik, японская Mitsubishi, тайваньский Winstar и пр. Но их продукция имеет достаточно высокую цену и предназначена в основном для профессионального применения. Кроме того, на рынке массово представлены сверла по металлу под торговыми марками известных продавцов и производителей электроинструмента. В основном это недорогой инструмент, но при этом многие изделия имеют очень высокое качество. В этой категории пользователи чаще всего отмечают «Зубр», «Интерскол», DeWalt, Hilti, Makita и Metabo.
Правила хранения сверл
На рабочих местах промышленных предприятий хранение сверл осуществляется в инструментальных шкафах и тумбочках из листового металла, установленных в непосредственной близости от станка, а также на стеллажах в специальных инструментальных кладовых. Сверлильный инструмент необходимо укладывать в определенном порядке (по типам и диаметрам) в соответствующие отсеки, пеналы или чехлы. Укладка должна обеспечивать сохранность режущих кромок, а также рабочих и посадочных поверхностей. Перед помещением на хранение сверлильный инструмент очищают от металлической пыли и загрязнений, а в случае неиспользования в течение длительного времени смазывают литолом или техническим вазелином. В целях предотвращения возникновения коррозии запрещается располагать рядом с местами хранения инструмента кислотосодержащие и прочие агрессивные жидкости. В домашних мастерских инструмент должен храниться с соблюдением таких же правил. Только вместо тумбочек и шкафов здесь гораздо удобнее использовать пластиковые пеналы и специальные подставки (см. видео ниже).
При сверлении глубоких отверстий в металле рекомендуется поливать поверхность инструмента небольшим количеством масла. На производстве обычно используют И-20, но не у всех есть возможность приобрести именно эту марку. А какое масло взамен индустриального можно использовать в домашних условиях? Поделитесь, пожалуйста, своими соображениями и рекомендациями по этому вопросу в комментариях.
Изготовление витых сверл из литой быстрорежущей стали Текст научной статьи по специальности «Технологии материалов»
ИЗВЕСТИЯ ТОМСКОГО ОРДЕНА ОКТЯБРЬСКОЙ РЕВОЛЮЦИИ И ОРДЕНА ТРУДОВОГО КРАСНОГО ЗНАМЕНИ ПОЛИТЕХНИЧЕСКОГО ИНСТИТУТА имени С. М. КИРОВА
Том 225 1972
СТАЛИ
И. О. ХАЗАНОВ, Ю. к. КОРЗУНИН, Г. Г. ЗАХАРОВА
{Представлена научным семинаром куста кафедр: металловедения, оборудования и технологии термической обработки металлов, оборудования и технологии сварочного
производства и технологии металлов)
Существующие способы изготовления сверл предусматривают применение пруткового горячекатаного материала в качестве исходной заготовки для сверла.
Прутки разрезаются на длину заготовки под рабочую часть сверла, затем к ним приваривается хвостовая часть из стали 45, сваренные заготовки отжигаются, обтачиваются, шлифуются, после чего следует либо прокатка на стане секторного проката с последующей завивкой, либо из обточенной заготовки изготавливается фрезерованное сверло [1].
Изготовление сверл, да и других видов инструмента из быстрорежущих ‘сталей ¡неизменно связано с образованием значительного количества отходов дефицитной и дорогой быстрорежущей стали. Эти отходы получаются в виде стружки, мелких излишних кусочков рабочей части сверла и просто кусковых отходов, которые уже не могут использоваться в производстве инструмента из-за их некондиционно-малых размеров. Эти отходы, в лучшем случае, переплавляются на резцы, литые сверла, а в большинстве случаев сдаются на переплавку. Завод теряет необходимый ему металл’ и терпит убытки из-за разницы в стоимости отходов по сравнению с кондиционным металлом.
Переплавкой отходов на другие виды инструмента на инструментальных заводах можно значительно увеличить выпуск инструмента, что даст заводам дополнительные прибыли на экономии металла.
Однако литой инструмент, наряду с хорошими качествами, имеет существенный недостаток: он обладает значительной хрупкостью и основным видом его износа является выкрашивание режущих кромок [2].
Наиболее перспективным является выпуск такого массово потребляемого инструмента, как сверла. Наша инструментальная промышленность выпускает ежегодно сотни миллионов сверл и потребность в них ежегодно возрастает.
Авторами настоящей работы была разработана на Томском заводе режущих инструментов новая технология изготовления сверл размером от 20 мм и более из литых заготовок.
Предлагаемая технология предусматривает в качестве исходного .материала для заготовок сверл переплав отходов быстрорежущей стали и стружку, из которых отливаются штанги для нужных размеров сверл..
Отлитые штанги отжигаются, режутся на короткие заготовки, соответствующие рабочей части сверла, а вся дальнейшая технология изготовления сверла совпадает с заводской технологией изготовления сверл * методом секторного проката [1].
Известно, что сталь Р18 является малопластичной и наиболее труднодеформируемой сталью по-сравнению со сталью Р12, Р6МЗ [3,4].
Поэтому в настоящее время на большинстве заводов для изготовления сверл методом секторного проката используется в основном сталь Р12 и Р6МЗ. В литом состоянии быстрорежущая сталь обладает весьма ограниченной пластичностью [5], поэтому на металлургических заводах под непосредственную прокатку используются слитки небольшого веса (от 200 до 500 кг) со строго ограниченным в них содержанием углерода, который и определяет пластичность литой быстрорежущей стали. Сильно развитое строение карбидной эвтектики в крупных слитках (весом от 300 кг и выше) [5] вынуждает производственников осу-, ществлят’ь вначале их ковку, после чего кованые заготовки подаются на
прокатку.
В нашем случае, в качестве заготовки под прокат сверл используются отливки малого объема и веса, в которых из-за большой скорости охлаждения при их кристаллизации сильно измельчается зерно и не получаются крупные эвтектические карбиды, а это повышает пластичность литой быстрорежущей стали.
Переплавка отходов стали производилась в индукционной печи с машинным генератором МГП-102а в кислом тигле емкостью 150 кг. Мелкая шихта засыпалась в тигель, сверху покрывалась слоем битого ? стекла, после расплавления первой пор-
ции шихты в тигель вводилась брике-.■ тированная стружка до 30% от веса
плавки. Подшихтовка угара углерода, молибдена, вольфрама, хрома, ванадия производилась высокоуглеродистым быстрорежущим чугуном состава: углерода — 5—5,5%, хрома — 4 %, вольфрама— 6—12%, ванадия — 2,3«%, молибдена — 3,5)%;. Состав высокоуглеродистого чугуна выбирался в зависимости от состава переплавляемой шихты. При выплавке стали из шихты Р6МЗ высокоуглеродистый чугун выплавляется на базе стали Р6МЗ, для ¡стали Р12 выплавляли чугун из стали Р12. Это облегчает подшихтовку выплавляемого металла, так как в быстрорежущем чугуне можно при помощи дополнительного введения ферросплавов получить любое содержание выго-1 рающих легирующих элементов.
Переплавленная и доведенная до стандартного состава сталь Р6МЗ или Р12 разливалась в металлические из-г ложницы, рис. 1, которые снабжаются
прибыльной частью. Прибыльная часть изложницы изготавливается по способу приготовления оболочковых форм. Кокили на торцах и рабочих Ï поверхностях покрываются противопригарной обмазкой из окиси хрома
или окиси алюминия на минеральном или растительном масле.
Рис. 1. Металлическая изложница для отливки заготовок для сверл
1*27
Перёд первой заливкой кокили подогреваются до 400ч-500°С. Коки-ли быстроразъемные и их количество определялось объемом одного ковша стали. В нашем случае использовалось 10 кокилей с весом одной отливки 2,8—3,0 кг, что составляет 30 кг стали в одном ковше. После разливки первого ковша перед второй разливкой литейщики успевали разобрать и подготовить кокили к следующей разливке. При качественном нанесении противопригарной краски в кокиль можно произвести 7—8 заливок без дополнительного окрашивания, а только с подкрашиванием верхней части кокиля, в месте удара струи жидкого металла. Подкрашивание производилось сразу после разборки горячего кокиля тряпочным тамтшном. Краска очень быстро высыхает, и ко’киль снова готов к заливке. Скорость затвердевания отливки в кокилях для заготовок диаметром 30 мм составляла 14 град/сек. Пока заливались последние кокили, первые уже разбирались, из них извлекались отлитые заготовки, кокили немного подкрашивались и снова собирались под заливку. Операция повторной сборки и извлечения отливок составляла 4—6 минут. Так как форма отливок простая, то стойкость кокилей велика.’ Кокили изготавливали из стали 10, ст. 20. В кокилях предусмотрена свободная усадка отливок, в противном случае в них могут появиться горячие трещины.
Кокили устанавливались в ряд на подкладной плите. При заливке металла в подогретые до 400—550°С кокили отливки получались беспористыми с чистой поверхностью. Вес прибыльной части отливки составлял 0,7—0,8 вееа годной штанги, хотя это требование выполняется в каждом отдельном случае по-разному, в зависимости от размера отливки. Основным контролирующим фактором качества отливки должно являться отсутствие усадочной раковины в подприбыльной части отливок.
При конструировании кокилей их тепловой расчет не производился, а вес кокилей в нашем случае составил 3—4 веса отливки. Кокили имеют хороший вид после получения в них более 100 заливок и не было ни одного случая выхода из строя их из-за разгара.’ При появлении разгара рабочая полость может растачиваться под больший размер отливок, что увеличит срок службы кокилей.
Угар элементов в нашем случае составил: углерода— 10%, хрома— —3—4%, молибдена — 5%, ванадия — 6—7%, вольфрам практически не выгорал. Плавка весом 150 кг продолжалась 1,5 часа. Плавка на высокочастотной установке ЛПЗ-60 весом 50 кг длилась около одного часа. Первые опытные плавки производились на установке ЛПЗ-60 весом по 20 кг, время плавки составляло 20—25 минут
Отливки, полученные в кокиле, имеют очень мелкое зерно и тонкую сетку карбидной эвтектики, рис. 2, 3. Твердость отлитых в кокиль заготовок составляет HRC 56, поэтому их необходимо отжечь, так как они должны подвергаться механической обработке. Отжиг производился в шахтных печах с песочной засыпкой. Для снятия окалины и обезугле-роженного сло’я учитывался технологический припуск на обточку для получения качественной заготовки. Твердость отливок после отжига составляет НВ—260 кг/мм2. Мелкозернистое строение отливок обеспечило возможность получения из них сверл методом непосредственной прокатки.
Полученные литые заготовки прокатывались на стане секторного проката по заводской технологии. 64,5 испытывались на скручивание и изгиб в сравнении со сверлами из катаных заготовок. Работа при скручивании у сверл 26 мм из литых заготовок составила 78 кгм, сверла из катаных заготовок показали работу при скручивании 77 кгм. Усилие при изгибе у сверл из катаных заготовок оказалось выше на 350—400 /сг. Сверла прошли лабораторные испытания резанием
по ГОСТ 2034—64 и не имели следов износа и выкрашивания. По внешнему виду сверла из литых заготовок не отличаются от заводских.
Из результатов испытаний механических и режущих свойств следует, что сверла из литых заготовок соответствуют требованиям ГОСТ 10902—64.
Изготовление сверл по предлагаемой технологии из отходов быстрорежущей стали даст инструментальным заводам значительную экономию.
1. А. М. Бранделис. Новая технология производства спиральных сверл. Машгиз, М., 1953.
2. Н. С. Дегтяренко. Литой режущий инструмент и область его применения. ВНИИ, М., 1959.
3. Н. М. Ф а д ю ш и н а, Е. И. М а л и н к и н а. Станки и инструмент. № 6, М., 1966, стр. 30.
4. Г. А. Ко с с о вич, Ю. А. Геллер. МИТОМ, № 5, М., 1964, стр. 3—9.
5. Ю. М. Чижиков. Процессы обработки давлением легированных сталей и сплавов. Металлургия, М., 1965, стр. 248.
6. Ю. А. Геллер. Инструментальные стали. Металлургиздат. М., 1968, стр. 396.
9, Заказ 4746,
Рис. 2. Микроструктура стали Р6МЗ, отлитой в металлическую изложницу, х640, нормальный отжиг
Рис. 3. Микроструктура стали Р12, отлитой в металлическую изложницу, Х640, нормальный отжиг
ЛИТЕРАТУРА
Сверло по металлу: классификация и маркировки, устройство
Сверло по металлу: конструкция, геометрия, элементы сверла. Как и из чего делают сверла. Типы хвостовиков и маркировка. Выбор, применение и правила хранения. Лучшие производители и советы по выбору сверл по металлу.
В машиностроении сверло по металлу является вторым по частоте использования инструментом после резца, а в домашнем хозяйстве оно уверенно делит лидерство с ножовкой и отрезным кругом. Конструктивно сверло — это длинный цилиндрический стержень из металла с двумя режущими кромками на торце и спиральными канавками для отвода стружки. Принцип резания металла и формирования отверстия у всех типов этого инструмента практически одинаков, поэтому основная классификация сверл по металлу основывается на конструктивных признаках (тип хвостовика, профиль спирали, вид режущей кромки и т. п.). Определить по внешнему виду все необходимые характеристики сверла достаточно сложно, т. к. маркировка, которая гравируется на металле хвостовика, содержит информацию только о диаметре инструмента, материале изготовления и производителе. Поэтому для того, что выбрать сверло для обработки твердых, хрупких или вязких металлов и сплавов необходимо воспользоваться каталогами производителей. Длительное и краткосрочное хранение сверл должно осуществляться по определенным правилам, т. к. инструментальные и быстрорежущие стали склонны к коррозии, а заточенные кромки легко повреждаются при ударе о металл.
Конструкция и геометрия сверла
Любое сверло вне зависимости от его назначения и конструктивных особенностей состоит из двух основных компонентов: хвостовика и рабочей части. Первый служит для передачи инструменту вращения от привода или фиксации его в неподвижном состоянии (на токарных станках). Рабочая часть состоит из ряда элементов, непосредственно обеспечивающих процесс сверления. Геометрия сверла зависит от особенностей сверления, для которого оно предназначено, а также материала обрабатываемой заготовки (различные металлы, древесина, пластики, композиты, керамика).
В качестве примера взят один из самых распространенных в промышленности видов такого инструмента: спиральное сверло для работ по металлу с коническим хвостовиком (см. чертеж ниже). Все изображенные на рисунке углы сверла соответствуют работам по металлу общего назначения. Слева показан вид сбоку, а справа — со стороны рабочего торца (увеличено).
Далее с пояснениями перечислены все основные компоненты и геометрические параметры такого сверла:
- Хвостовик. Служит для закрепления инструмента в шпинделе станка или зажимном патроне. При сверлении металла на токарных станках крепится неподвижно в конусе задней бабки.
- Рабочая часть. Формирует цилиндрическое отверстие (или углубление). Состоит из режущей части, длина которой у таких сверл по металлу обычно составляет половину их диаметра, и направляющей с канавками для отвода стружки.
- Конус Морзе. Для установки в шпиндели и задние бабки станков используют инструмент с коническим хвостовиком, а для зажима в кулачковые и цанговые патроны — с цилиндрическим.
- Лапка. Эти конструктивные элементы присутствуют только на конических хвостовиках и предназначены для выбивания инструмента из шпинделя или оправки.
- Шейка. Обеспечивает удобство подвода и отвода шлифовального инструмента при обработке спиральных канавок. Она не выполняет никаких рабочих функций, поэтому на нее обычно наносится маркировка сверла (чеканится непосредственно на металле).
- Направляющая часть. Также называется калибрующей. Опираясь на стенки просверленного в металле отверстия, направляет инструмент вдоль его оси. Включает в себя спиральные поверхности с ленточками и канавки для отвода стружки.
- Угол наклона спиральной поверхности. Для обработки металла он составляет 18÷30°.
- Стружкоотводящая канавка. От ее ширины, наклона и качества поверхности зависит скорость отвода стружки.
- Диаметр режущей части. Равен расстоянию между внешними краями режущих кромок.
- Режущая кромка. Это острая грань между передней поверхностью (стружечной канавкой) и задней затачиваемой поверхностью.
- Главный угол при вершине. Угол между режущими кромками, оказывает значительное влияние на процесс резания и прочность сверлильного инструмента. Для работ по металлу его стандартное значение равно 116÷118°.
- Задняя поверхность. Для снижения трения в зоне резания задняя поверхность затачивается под углом к режущей кромке. Для сверления металла его значение около ленточки должно составлять 8÷12°.
- Перемычка. Конструктивная часть, общая для обеих задних поверхностей.
- Поперечная режущая кромка. Острая грань на перемычке, разделяющая задние поверхности. При правильной заточке на ее середине находится геометрический центр режущей части, который должен совпадать с осью инструмента.
- Ленточка. Две слегка выступающие над спиральными поверхностями полоски, которые калибруют отверстие и снижают трение о его стенки.
Общая компоновка других типов сверл по металлу подобна этой, хотя в зависимости от своего назначения они могут отличаться конструкцией режущей части и стружкоотводящих канавок.
Виды сверл по металлу
Основная классификация сверлильного инструмента проводится по конструктивному признаку, т. к. он напрямую связан с назначением конкретного вида сверла по металлу.
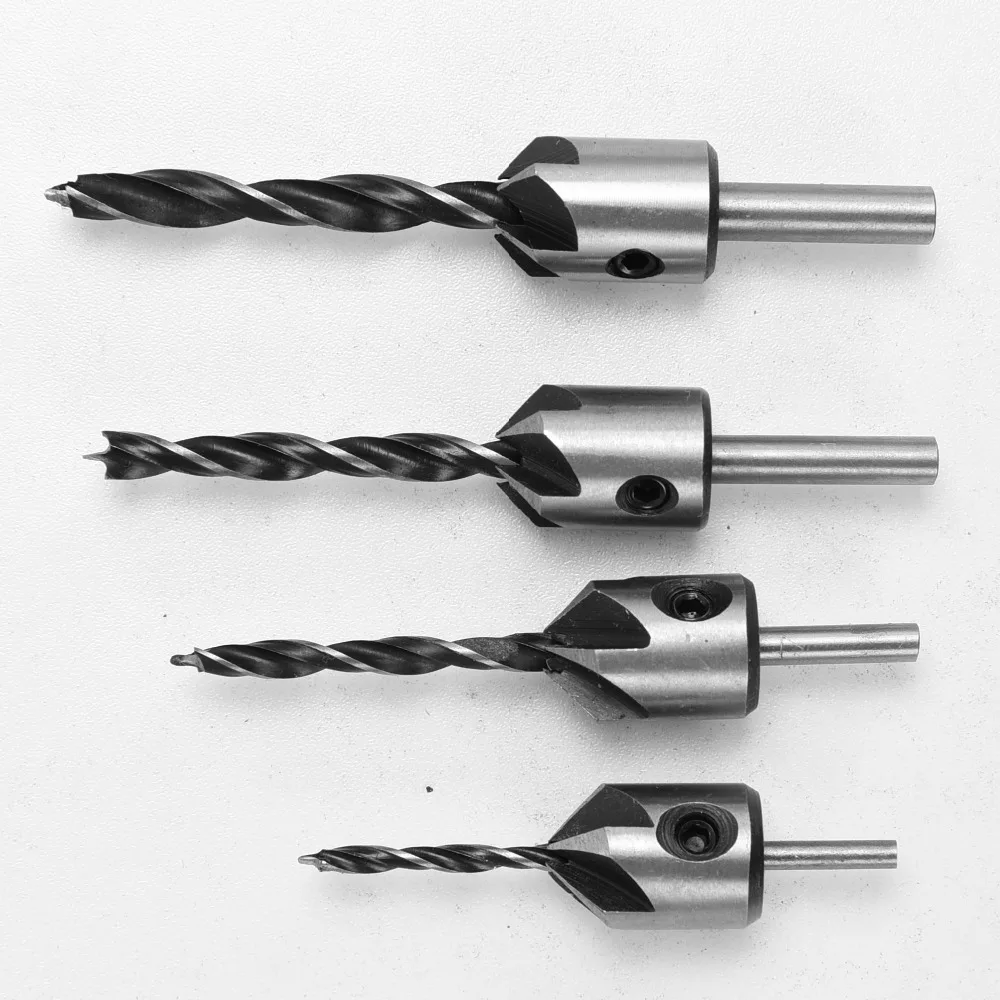
- спиральные;
- перовые;
- центровочные;
- специальные.
Среди специальных сверл самой большой группой является инструмент для глубокого сверления в заготовках из металла. Отдельные подгруппы также составляют изделия для сверления отверстий больших диаметров и ступенчатых цилиндрических профилей. Бывает так, что современный сборный инструмент имеет настолько сложную или инновационную конструкцию, что его относят сразу к нескольким типам.
Спиральная форма
Традиционным широко распространенным видом сверлильного инструмента являются спиральные сверла, у которых формирование цилиндрического отверстия в металле осуществляется двумя симметричными режущими кромками. При этом отвод образующейся стружки проходит по спиральным канавкам, начальная часть которых является передними поверхностями, образующими эти кромки. По своей конструкции эти изделия могут быть монолитными или сборными, с заменяемой головкой или механическим креплением режущих пластин. Для снижения трения и повышения скорости отвода стружки спиральную часть полируют и покрывают износостойкими материалами.
Ступенчатая форма
Ступенчатые сверла используют для получения отверстий небольшой глубины с фиксированной геометрией ступеней. Такой инструмент позволяет за один проход сформировать от двух и более цилиндрических поверхностей и чаще всего используется при автоматизированной обработке. По своей конструкции современные ступенчатые сверла, как правило, представляют монолитный блок, повторяющий конфигурацию будущего отверстия, с рядами режущих пластин и прямыми канавками. Первые сверлят в металле заготовки начальное отверстие, а следующие за ними являются рассверливающими.

Корончатые сверла
Корончатым сверлом называют пустотелый инструмент с кольцевым расположением шести или двенадцати режущих поверхностей и соответствующим им числом стружкоотводящих канавок. Он применяется для сквозного сверления в металле отверстий больших диаметров. В процессе работы режущие кромки прорезают только кольцо вокруг середины будущего отверстия, а центральная часть металла просто выпадает (или выбивается) после прохода насквозь. Этот инструмент относят к сверлильному, скорее, по устоявшейся традиции, т. к. по своему принципу работы он гораздо ближе к фрезам.
Шнековые сверла
При сверлении отверстий в металле на глубины, кратные 30÷40 диаметрам, применяют удлиненные сверла специальной конструкции со спиральной канавкой в виде шнека. Такое решение намного улучшает стружкоудаление и позволяет производить непрерывное сверление металла на полную глубину отверстия без периодического вывода инструмента.
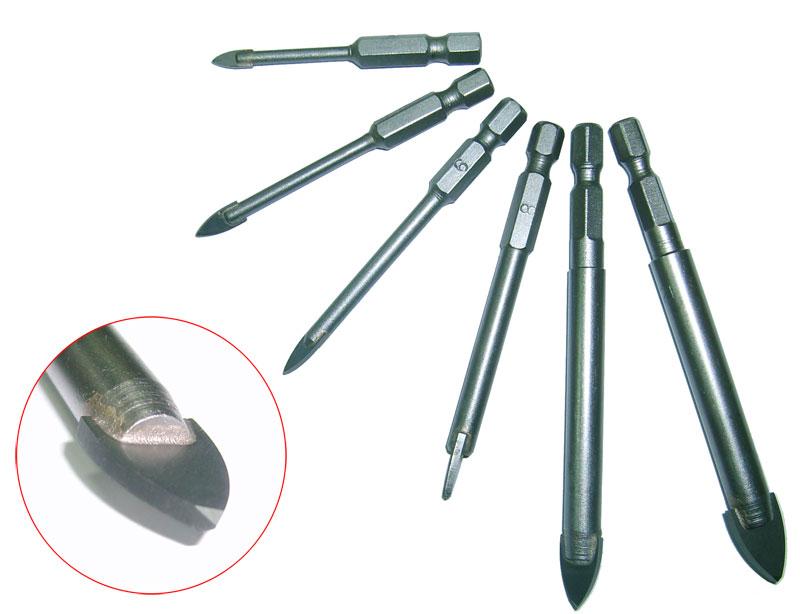
Перовые сверла
Перовые сверла используются для получения отверстий в металле, покрытом литейной коркой и окалиной. Конструктивно это самый простой сверлильный инструмент, т. к. имеет прямые канавки и режущую часть в виде пластины. Его недостатки являются прямым следствием простоты конструкции и невысокой стоимости. В процессе сверления металла у перовых сверл плохо отводится стружка, и они имеют склонность к уходу от оси отверстия. Выступающая вперед пластина снижает прочность всего изделия, что не позволяет работать на больших подачах, а также требует частой переточки. Это узкоспециализированный инструмент повышенной жесткости, который применяют при работе с отливками и поковками.
Типы хвостовиков
В соответствии с ранними советскими ГОСТами, которые действуют до сих пор, для сверлильного инструмента по металлу было предусмотрено два типа хвостовиков: цилиндрический и конический (Морзе).

Маркировка сверл согласно ГОСТ
Правила маркировки сверл регламентированы ГОСТ 2034-80. Согласно этому документу на сверлильный инструмент диаметром менее двух миллиметров маркировка не наносится. Все данные о них должны указываться на упаковочной этикетке. Для сверл толщиной свыше двух и до трех миллиметров маркировка сверла по металлу содержит только значение диаметра и марку стали (таким образом их можно отличить от инструмента до двух миллиметров). Для диаметров свыше трех миллиметров в составе маркировки производитель должен указывать его величину, свой товарный знак, марку металла и класс точности. Марка металла, из которого изготовлен инструмент, может указываться как в виде ГОСТовского обозначения стали (например, Р6М7К6), так и общепринятой для быстрорежущих сталей международной аббревиатурой (HSS) с добавлением обозначения основного легирующего металла (Co, Ni, Ti и пр.) (см. фото ниже). Зарубежные изготовители маркируют свою продукцию аналогичным образом, поэтому отличить российские сверла от импортных можно только по торговой марке.
Цветовое обозначение
В своих каталогах все ведущие производители сверлильного инструмента используют для обозначения продукции цветовую маркировку, предусмотренную международным стандартом ISO 513. В соответствии с этим регламентирующим документом все инструментальные материалы делятся на шесть групп, каждая из которых предназначена для обработки определенных видов металлов, сплавов и полимерных материалов.
Группа | Цвет | Обрабатываемые металлы и пластики |
---|---|---|
P | Голубой | Отдельные виды углеродистых, легированных и инструментальных сталей.![]() |
M | Желтый | Аустенитные коррозионностойкие стали. Отдельные виды немагнитных и износостойких сталей. |
K | Красный | Различные марки чугунов. |
N | Зеленый | Цветные металлы и их сплавы. Термопласты и дуропласты. |
S | Золотистый | Жаростойкие сплавы на основе никеля, кобальта, титана и железа. |
H | Серый | Закаленные стали высокой твердости. |
Кроме того, каждая группа резания подразделяется на группы применения, которые обозначаются числом в интервале от 1 до 40. Группы с большим индексом имеют более высокую прочность, а с меньшим — большую твердость и стойкость к износу.
Технология изготовления сверл
Конструктивно спиральное сверло состоит из двух основных компонентов: рабочей части и хвостовика. Первую изготавливают из быстрорежущей стали или твердых сплавов, а второй — из углеродистой инструментальной стали.

- Подготовка компонентов. Цилиндрические заготовки для обеих частей нарезают на прутковых автоматах, а затем очищают от заусенцев, поверхностных окислов и загрязнений.
- Сварка. Две части из разного металла сваривают контактной стыковой сваркой. После этого со сварных швов удаляют излишки металла, а заготовки правят для придания им точной цилиндрической формы.
- Обточка. Заготовки центруют и обтачивают до точного размера. На этом же этапе подрезают торцы, точат конус хвостовика, обтачивают конец конуса под лапку (у инструмента с цилиндрическим хвостовиком последние две операции отсутствуют).
- Фрезеровка. Фрезеруют лапку (для конических хвостовиков), спиральные канавки и задние поверхности. После этого заготовка подвергается термической обработке с последующей очисткой на пескоструйной установке.
- Шлифовка. Шлифуют и полируют канавки спиралей. После этого шлифовке подвергают хвостовик и рабочую часть (с доводкой обратного конуса).
- Заточка сверла.
Корпуса сборного сверлильного инструмента, в котором режущая часть выполнена из твердосплавных пластин с напайным или механическим креплением, являются достаточно сложными изделиями, т. к. при их изготовлении необходима сложная фрезерная и токарная обработка. Поэтому их обычно изготавливают на станках с ЧПУ или обрабатывающих центрах.
Таблица размеров сверл по металлу
Государственные стандарты, правила изготовления спиральных и центровочных сверл по металлу, включают в себя таблицы размерных рядов для разных исполнений и направлений вращения спирали. Каждому типоразмеру соответствует уникальное цифровое кодовое обозначение. К примеру, если диаметр сверла с цилиндрическим хвостовиком равен 3.1 мм, оно имеет исполнение N1 и правую спираль, то его общая длина должна составлять 65 мм, длина рабочей части — 36 мм, а кодовое обозначение такого изделия будет 2300-7517. Таблицы размеров для сверл по металлу с коническим хвостовиком включают в себя диапазон диаметров от 5 до 80 мм, а для инструмента с цилиндрическим хвостовиком — от 0. 25 до 20 мм. При этом для тонких сверл диаметром до 1 мм предусмотрено только исполнение N1 c правой спиралью.
Материалы изготовления и покрытия
Основные материалы для изготовления рабочих частей монолитного сверлильного инструмента — это быстрорежущие стали и твердые сплавы. В качестве быстрореза чаще всего применяют стали с вольфрамовыми или вольфраммолибденовыми лигатурами. Последние также используют в варианте с добавкой кобальта. Твердые сплавы, которые производятся методами порошковой металлургии, долговечнее, прочнее и термоустойчивее быстрорежущих сталей. В их состав обычно входит несколько тугоплавких металлов, таких как вольфрам, титан, кобальт и тантал. Некоторые изделия, предназначенные для выполнения за одну установку инструмента нескольких технологических операций (например, комбинированное сверло), могут включать в свой состав компоненты, изготовленные из разных инструментальных материалов.
Для улучшения рабочих характеристик сверл по металлу их поверхности подвергают дополнительной обработке или покрывают твердыми соединениями металлов. Самые распространенные методы обработки, повышающие прочность и износостойкость инструмента, — это цианирование и сульфидирование. А для защитных покрытий обычно используют карбонитрид титана (TiCN), в том числе легированный алюминием (TiAlN).
Как подобрать сверло под обрабатываемый металл
При выборе сверла для работ по металлу в первую очередь необходимо ознакомиться с цветовыми маркировками стандарта ISO 513, которых придерживаются все производители сверлильного инструмента. При этом нужно понимать, что такая маркировка не наносится на само изделие, а присутствует только в его каталожном описании. Можно, конечно, положиться на советы консультанта в магазине инструмента, но такой способ подойдет только в том случае, если требуется подобрать сверло для дрели, предназначенное для работы с обычной конструкционной сталью. Если же предстоит сверлить твердые или вязкие металлы или требуется качественное выполнение работы на заказ, то лучше следовать рекомендациям профессионалов. На рисунке ниже приведен пример использования цветовой маркировки из каталога Mitsubishi.
Необходимо также помнить, что параметры процесса сверления зависят как от характеристик сверла, так и от мощности и скорости вращения привода. Поэтому сверла для шуруповерта лучше не использовать с дрелью, т. к. это, скорее всего, приведет к их повреждению. А скорости вращения шуруповерта явно недостаточно для сверления металла обычными сверлами для дрели.
Сверла, применяемые в станках
На сверлильных станках, у которых посадочное отверстие шпинделя выполнено под конус Морзе, сверла для обработки металла устанавливаются напрямую в шпиндель. А для их фиксации в нем предусмотрен специальный сквозной паз для заклинивания лапки. Такие же сверла применяют и в универсальных станках (сверлильно-фрезерных и пр.), у которых посадочное отверстие шпинделя сделано под метрический конус или под одну из его современных разновидностей. Только в этом случае их вставляют в переходные оправки с соответствующим конусом. В целом сверла по металлу, используемые на станках, не отличаются от тех, что применяют при сверлении ручным инструментом. Единственный вид сверлильного инструмента, предназначенный только для станочного применения, — это сверла со сквозным каналом, предназначенным для подачи СОЖ в зону обработки (см. рис. ниже).
Лучшие производители
Среди российских производителей сверлильного инструмента для работ по металлу хорошее соотношение цены и качества имеет продукция Волжского инструментального завода (ВИЗ), Томского инструментального завода (ТИЗ) и ПО «Туламаш». К этой же категории относится инструмент украинского Запорожского инструментального завода (ЗИЗ). Самыми лучшими по качеству являются сверла всемирно известных производителей режущего инструмента, таких как немецкие Bosch, Hasser и Ruko, шведский Sandvik, японская Mitsubishi, тайваньский Winstar и пр. Но их продукция имеет достаточно высокую цену и предназначена в основном для профессионального применения. Кроме того, на рынке массово представлены сверла по металлу под торговыми марками известных продавцов и производителей электроинструмента. В основном это недорогой инструмент, но при этом многие изделия имеют очень высокое качество. В этой категории пользователи чаще всего отмечают «Зубр», «Интерскол», DeWalt, Hilti, Makita и Metabo.
Правила хранения сверл
На рабочих местах промышленных предприятий хранение сверл осуществляется в инструментальных шкафах и тумбочках из листового металла, установленных в непосредственной близости от станка, а также на стеллажах в специальных инструментальных кладовых. Сверлильный инструмент необходимо укладывать в определенном порядке (по типам и диаметрам) в соответствующие отсеки, пеналы или чехлы. Укладка должна обеспечивать сохранность режущих кромок, а также рабочих и посадочных поверхностей. Перед помещением на хранение сверлильный инструмент очищают от металлической пыли и загрязнений, а в случае неиспользования в течение длительного времени смазывают литолом или техническим вазелином. В целях предотвращения возникновения коррозии запрещается располагать рядом с местами хранения инструмента кислотосодержащие и прочие агрессивные жидкости. В домашних мастерских инструмент должен храниться с соблюдением таких же правил. Только вместо тумбочек и шкафов здесь гораздо удобнее использовать пластиковые пеналы и специальные подставки (см. видео ниже).
При сверлении глубоких отверстий в металле рекомендуется поливать поверхность инструмента небольшим количеством масла. На производстве обычно используют И-20, но не у всех есть возможность приобрести именно эту марку. А какое масло взамен индустриального можно использовать в домашних условиях? Поделитесь, пожалуйста, своими соображениями и рекомендациями по этому вопросу в комментариях.
Технология изготовления сверл — Инструментальные материалы
Пайка – процесс соединения пластинок из быстрорежущей стали и державок инструмента, который осуществляется с помощью специальных сварочных порошков с высокой температурой плавления. Для пайки пластинок применяют сварочный порошок из ферромарганца и буры (натриевая соль тетраборной кислоты). Чтобы понизить температуру плавления сварочного порошка, в него добавляют медь.
Чтобы уменьшить расход дорогостоящей инструментальной стали, улучшить качество изделий и снизить трудоемкость их изготовления, при изготовлении заготовок взамен обработки резанием используют методы обработки давлением. При этом удается в некоторых случаях после применения методов обработки давлением получить форму и размеры изделия (или отдельных его элементов) с достаточно высокой точностью, что исключает необходимость дальнейшей механической обработки.
В настоящее время в инструментальной промышленности при изготовлении режущего инструмента применяют следующие виды обработки металлов давлением: секторную, поперечную и продольно-винтовую прокатки для изготовления заготовок сверл; ковку на молотах, прокатку на вальцах, холодную калибровку для изготовления заготовок напильников; безоблойную штамповку насадного режущего инструмента для изготовления других инструментов.
Рассмотрим некоторые особенности технологических процессов изготовления названных выше инструментов.
Развитие и применение пластической деформации при изготовлении заготовок сверл обусловлено тем, что все применяющиеся для них методы пластической деформации заготовок соответствуют основному современному технологическому требованию – приблизить профиль заготовки к профилю готового изделия. Это позволяет при изготовлении сверл сэкономить до 40 % дорогостоящей быстрорежущей стали, снизить трудоемкость изготовления изделий за счет исключения трудоемких операций фрезерования канавок.
Секторной прокаткой изготовляют в настоящее время заготовки сверл диаметром 15…50 мм. Этот метод широко распространен на инструментальных заводах страны и охватывает около 80 % общего выпуска сверл в указанном диапазоне диаметров. Причем выпуск сверл из заготовок, полученных секторной прокаткой, из года в год увеличивается.
При секторной прокатке цилиндрические механически обработанные заготовки из быстрорежущей стали нагревают в соляных ваннах до температуры прокатки (1100… 1200 °С). 3атем их прокатывают на специальных завивочных станках, после чего производят последующую термическую и механическую обработку.
Секторная прокатка положена в основу технологического процесса изготовления сверл и с прокатанными отверстиями для охлаждения. Сверла этого типа предназначены для высокопроизводительного сверления сталей, сплавов и других труднообрабатываемых материалов в тяжелых условиях, при которых затруднено охлаждение в зоне резания и не обеспечен надежный отвод стружки при сверлении. Технологический процесс изготовления сверл с отверстиями для охлаждения обладает всеми преимуществами, присущими методу сектор ной прокатки, а также позволяет исключить трудоемкую операцию сверления глубоких отверстий. Профиль сверла, а также профили отверстий для охлаждения, расположенных по всей длине рабочей части, получают пластической деформацией нагретых до температуры прокатки специальных заготовок.
Дальнейшее усовершенствование секторной прокатки заготовок сверл идет главным образом в направлении повышения точности по профилю и по шагу винтовой стружечной канавки, а также в направлении улучшения внешнего вида сверл.
Как сделать приспособление для заточки сверл своими руками — Изготовление ножа — Как сделать нож — Каталог статей
Как сделать приспособление для заточки сверл своими руками. Как сделать приспособление для заточки сверл. Приспособление для ручной заточки спиральных свёрл. Некоторое время назад случайно наткнулся (имеется ввиду автор статьи, см. источник) в сети на весьма полезные видеоуроки В. Леонтьева по ручной заточке спиральных свёрл:
Но тут же возникла идея, как сделать заточку свёрл ещё более простой и удобной. В результате раздумий и опытов появилось нижеописываемое приспособление. Сначала потребовалось модернизировать — довести до ума имеющееся фабрично-китайское ( типа немецкое) точило. Потому как работать с ним используя приёмы В.Леонтьева было практически невозможно.
Электроточило фабрично-китайского изготовления.
Хлипкий штатный кронштейн подручника.
Непригодная для работы конструкция подручника.
Вопервых кронштейн крепления подручника к кожуху диска слишком хлипкий, сделан из металла 2 мм толщины. При небольшом усилии гнётся. Поэтому, естественно, углы заточки получаются +/- километр! Да и форма подручника абсолютно не позволяет делать нормальный задний угол по методе В.Леонтьева, так как сверло при опускании хвостовика упирается в угол кронштейна. Тем более, что и сам подручник установлен НИЖЕ оси диска. То есть вообще никак не получить нормальный задний угол, если только не использовать торцевую поверхность диска.
Плоскость площадки подручника гораздо ниже оси вращения диска.
Новый кронштейн крепления подручника.
Для нормального кронштейна был использован кусочек металла толщиной 4 мм, большего размера и дополнительные крепёжные винты. Старый кронштейн крепился на двух заклёпках, которые пришлось срезать. Теперь новый кронштейн гораздо жёстче, чем ранее. Также из кусочков уголка и полосы была сварена горизонтальная полка подручника с дополнительными крепёжными отверстиями. Её положение можно регулировать в некоторых пределах.
Сравнение толщины металла в новом и старом подручниках.
Новый кронштейн крепится в 5 точках.
Детали приспособления. Кронштейн. Подручник. Поворотная пластина…
Далее было изготовлено непосредственно само приспособление. Оно представляет из себя поворотную пластину с приваренной втулкой, которая может качаться на оси, закреплённой в проушине, которая в свою очередь крепится к подручнику. Сверху к поворотной пластине крепится направляющая пластина для свёрл, в которой выбран треугольный паз.
Приспособление в сборе. Пластина в горизонтальном положении.
Приспособление в сборе.
Приспособление для заточки.
Сначала вместо этой пластины была опробована направляющая в виде кусочка уголка (как на видео у В.Леонтьева), но этот вариант совсем не годится — сверло трудно нормально зафиксировать (оно пытается убежать вправо при касании с диском), тем более что его требуется ещё и подавать вперёд при формировании заднего угла. В общем уголок (он есть на фото) совершенно не годится.
Приспособление в нижнем положении.
Работа с приспособлением напоминает движения автора видеоуроков, только вместо пальца и глазомера используется ось качания и установленный угол заточки сверла. Значительно удобнее с приспособлением контроль параллельности диску обрабатываемой режущей кромки сверла. Нужно просто повернуть пластину вниз и прижать сверло в пазу таким образом, чтобы линия режущей кромки была параллельна плоскости пластины — оси качания пластины. Этот момент показан на фото.
Установка сверла в направляющий паз пластины.
Установка сверла на подручник к точильному камню.
Сначала формируется сама кромка. При обработке заднего угла необходимо одновременным движением опускать пластину вниз и подавать само сверло вперёд к диску. Нужно стараться не допускать вращения сверла вокруг своей оси при формировании кромки и обработке заднего угла. Симетрию кромок контролирую точно также, как и в видеоуроках. Кстати, вместо качающейся пластины можно установить на подручник кусочек уголка с фиксированными углами — заточки и задним — это для заточки твердосплавных буров. Нужно только по месту определить необходимую длину сторон уголка для получения нужного заднего угла заточки, так как он зависит и от диаметра диска и местоположения подручника относительно оси вращения диска.
Установка сверла в направляющий паз пластины.
Контроль установки сверла. Режущая кромка сверла параллельна поверхности пластины.
Конфигурация направляющего паза.
Приспособление для ручной заточки спиральных свёрл.
Способ изготовления сплошного кольцевого сверла для колонковой сверлильной коронки
Изобретение относится к способу изготовления сплошного кольцевого сверла для колонковой сверлильной коронки согласно ограничительной части пункта 1 формулы изобретения.
В соответствии с уровнем техники алмазные инструменты, обладающие конструкцией колонковых сверлильных коронок, подразделяют на колонковые сверлильные коронки со сплошным кольцевым сверлом и сегментированные колонковые сверлильные коронки с отдельными режущими сегментами. Колонковые сверлильные коронки состоят из рабочей части, цилиндрического хвостовика и зажимной части со вставляемым в нее концом. Колонковую сверлильную коронку закрепляют в зажиме устройства для кольцевого сверления посредством вставляемого в зажим конца и в режиме сверления указанного устройства приводят во вращение вокруг оси вращения.
Сплошные кольцевые сверла изготавливают из порошковой смеси со статистически распределенными в ней алмазными частицами. Порошковую смесь загружают в пресс-форму и прессуют, получая заготовку, которую при последующем воздействии температуры и давления спекают в сплошное кольцевое сверло. В патенте США US 5,316,416 описана конструкция сплошных кольцевых сверл, которые характеризуются оптимальной обрабатывающей способностью по всей высоте. Кольцевые сверла снабжены несколькими верхними и нижними прорезями, распределенными вдоль окружности кольцевых сверл. Высота верхних прорезей соответствует половине высоты кольцевых сверл, причем верхние прорези упираются в обрабатывающую поверхность кольцевого сверла, обращенную в противоположную от хвостовика сторону. Нижние прорези расположены вдоль окружности кольцевых сверл между соответствующими верхними прорезями и упираются в соединительную поверхность кольцевых сверл, обращенную к хвостовику сверла. Верхние и нижние прорези по высоте кольцевых сверл соединяются внахлестку. Благодаря распределению верхних и нижних прорезей по всей высоте кольцевых сверл в течение всего периода эксплуатации кольцевого сверла к месту обработки транспортируется охлаждающая и промывочная жидкость и из зоны сверления удаляется снимаемый материал.
При изготовления режущих сегментов для сегментированных колонковых сверлильных коронок особое признание профессионалов получили методы, согласно которым алмазные частицы размещают в предназначенном для вставки алмазных частиц шаблоне. Выполняют послойное формирование заготовки из порошковых слоев, содержащих порошковую смесь, и алмазных слоев с алмазными частицами, расположенными в заранее выбранном шаблоне для вставки алмазных частиц, после чего заготовку при воздействии температуры и давления спекают в режущий сегмент. Режущие сегменты размещают вдоль окружности цилиндрического хвостовика сверла и сваривают, спаивают или скрепляют с хвостовиком иным образом. Скорость резания, достигаемая при использовании сегментированной колонковой сверлильной коронки, в значительной степени зависит от расположения алмазов в режущем сегменте. В случае послойного формирования расположение алмазных частиц может определяться количеством алмазных слоев, расстоянием между алмазными слоями и размером алмазных частиц.
В основу настоящего изобретения была положена задача, состоящая в том, чтобы использовать технологию вставки алмазов применительно к сплошным кольцевым сверлам и повысить качество обработки, достигаемое при использовании выполненных в соответствии с указанной технологией кольцевых сверл.
Указанная задача применительно к упомянутому в начале описания способу изготовления сплошного кольцевого сверла для колонковой сверлильной коронки согласно изобретению решается благодаря отличительным признакам, приведенным в независимом пункте 1 формулы изобретения. Предпочтительные улучшенные варианты осуществления изобретения представлены в соответствующих зависимых пунктах.
Предлагаемый в изобретении способ изготовления сплошного кольцевого сверла включает следующие стадии:
— посредством последовательного нанесения порошковых слоев порошковой смеси и алмазных слоев с алмазными частицами, размещенными в шаблоне для вставки, между нижней и верхней сторонами в направлении формирования послойно формируют по меньшей мере две заготовки,
— заготовки при воздействии давления преобразуют в кольцевые сегменты и
— выполняют кольцеобразную сборку кольцевых сегментов и при воздействии температуры спекают их в сплошное кольцевое сверло.
Предлагаемый в изобретении способ включает три стадии, предусматривающие использование разных технологий. На первой технологической стадии послойно формируют несколько заготовок из порошковых слоев, которые содержат порошковую смесь и алмазные слои с алмазными частицами. Определение «порошковая смесь» используют для общего обозначения мелкозернистых порошковых смесей и гранулированных порошковых смесей, причем использование гранулированных порошковых смесей является предпосылкой для объемного холодного прессования. В качестве порошковой смеси можно использовать железный, кобальтовый и/или бронзовый порошок, причем примешивание добавок, например, таких как карбид вольфрама, позволяет оказывать влияние на свойства кольцевых сверл (износостойкость, долговечность и режущую способность). Кроме того, состав порошковой смеси влияет на температуру спекания. Определение «алмазные частицы» используют для общего обозначения как индивидуальных алмазных частиц, так и заключенных в оболочку или покрытых алмазных частиц.
Заготовки обладают слоистой структурой и геометрической формой прямой призмы с многоугольным основанием. Заготовки в форме призм на второй технологической стадии при воздействии давления преобразуют в кольцевые сегменты. Обработку заготовок давлением выполняют при температурах ниже температуры плавления порошковой смеси. На третьей технологической стадии выполняют кольцеобразную сборку кольцевых сегментов, которые при воздействии температуры спекают в сплошное кольцевое сверло. При спекании кольцевых сегментов, во-первых, происходит уплотнение отдельных кольцевых сегментов, а, во-вторых, соединение соседних кольцевых сегментов друг с другом.
Подходящими методами формования являются холодное прессование, горячее прессование, а также иные подобные методы. В случае холодного прессования заготовке придают заданную форму при высоком давлении. Несмотря на то, что материал в прессе для холодного прессования нагревается, формование происходит в температурном интервале, в котором рекристаллизация отсутствует, причем материал деформируется без существенного снижения прочности. При термическом прессовании, называемом также объемной штамповкой, заготовке придают окончательную форму при высоком давлении и подводе тепла. При этом изменяется не только форма, но и структура заготовки, которая становится более твердой, а также приобретает более плотную структуру и более однородную поверхность.
Спекание является технологией изготовления материалов, в соответствии с которой порошок или заготовку (прессованный порошок) с целью повышения прочности, достигаемой благодаря соединению отдельных частиц порошка друг с другом, нагревают до температур ниже температуры плавления. Процесс спекания протекает в три стадии, на которых происходит значительное уменьшение пористости и объема заготовок. На первой стадии спекания происходит только уплотнение заготовки, в то время как на второй стадии спекания значительно уменьшается ее открытая пористость. Прочность спеченного материала обусловлена тем, что на третьей стадии спекания частицы порошка оплавляются и вследствие взаимной поверхностной диффузии соединяются друг с другом. Горячее прессование является особым методом спекания, в соответствии с которым помимо воздействия температуры прикладывают также внешнее давление.
В соответствии с предлагаемым в изобретении способом кольцевое сверло формируют не в виде сплошного кольцевого сверла, а собирают из двух или более кольцевых сегментов, которые соединяют друг с другом посредством спекания. При послойном формировании заготовки используют известные технологии изготовления режущих сегментов для сегментированных колонковых сверлильных коронок.
В предпочтительном варианте осуществления способа кольцевое сверло формируют из количества n (n≥1) первых заготовок, которые преобразуют в первые кольцевые сегменты, и n вторых заготовок, которые преобразуют во вторые кольцевые сегменты, причем первые и вторые кольцевые сегмент располагают поочередно один за другим вдоль направления окружности кольцевого сверла. Изготовление кольцевого сверла из первых и вторых заготовок допускает возможность приведения кольцевого сверла в соответствие с разными подлежащими обработке основаниями. При колонковом сверлении бетонных материалов с утопленной в них арматурной сталью, называемых также армированными бетонными материалами, кольцевое сверло наталкивается, например, на разные основания в виде бетона и арматурной стали.
В особенно предпочтительном варианте первые кольцевые сегменты формируют из первой порошковой смеси и первых алмазных частиц, а вторые кольцевые сегменты формируют из второй порошковой смеси и вторых алмазных частиц. Приведение кольцевого сверла в соответствие с подлежащим обработке основанием можно осуществлять посредством выбора порошковой смеси и алмазных частиц. В случае порошковой смеси возможным является варьирование состава материалов, тогда как в случае алмазных частиц можно варьировать их средний диаметр, распределение и количество.
В альтернативном предпочтительном варианте осуществления способа кольцевое сверло формируют из количества 2n (n≥1) одинаковых заготовок, причем n заготовок при воздействии давления преобразуют в первые кольцевые сегменты с выпуклой кривизной и n заготовок при воздействии давления преобразуют во вторые кольцевые сегменты с вогнутой кривизной. Использование одинаковых заготовок позволяет сократить аппаратурные затраты при их послойном формировании, поскольку в этом случае требуется только одна порошковая смесь и алмазные частицы только одного вида.
В особенно предпочтительном варианте в случае первых кольцевых сегментов верхнюю сторону заготовок размещают на наружной стороне, а в случае вторых кольцевых сегментов на внутренней стороне, причем первые и вторые кольцевые сегменты располагают поочередно один за другим вдоль направления окружности кольцевого сверла. Благодаря варьируемой кривизне кольцевых сегментов из одинаковых заготовок могут быть изготовлены два разных кольцевых сегмента. Заготовки на верхней стороне имеют алмазный слой, который в случае первых кольцевых сегментов расположен на наружной боковой поверхности, а в случае вторых кольцевых сегментов на внутренней боковой поверхности.
В особенно предпочтительном варианте количество алмазных слоев и размер алмазных частиц устанавливают таким образом, чтобы средний диаметр алмазных частиц составлял по меньшей мере 45% от отношения ширины кольцевого сверла к количеству алмазных слоев. Благоприятным для обработки армированных бетонных материалов оказывается максимально близкое взаимное расположение круговых дорожек, вдоль которых алмазные частицы проходят путь при обработке основания, и арматурная сталь почти полностью удаляется алмазными частицами. Благодаря чередующемуся расположению кольцевых сегментов количество дорожек на основании, которые алмазные частицы производят при его обработке, может быть удвоено при одном и том же количестве алмазных частиц.
Послойно сформированные заготовки обладают геометрической формой прямой призмы с многоугольным основанием. Подходящими многоугольными основаниями являются прямоугольные, пятиугольные и шестиугольные основания.
В первом варианте формируют заготовки с прямоугольными основаниями. Прямоугольное основание заготовок обладает наиболее простой геометрической формой, подходящей для изготовления кольцевых сверл из нескольких кольцевых сегментов. Кольцевые сегменты по боковым краям соединяют с соседними кольцевыми сегментами.
Во втором варианте формируют заготовки с пятиугольными основаниями, состоящими из прямоугольника и трапеции с двумя прямыми внутренними углами. В зоне наклонной боковой стороны трапеции при спекании с соседним кольцевым сегментом образуется канавка для охлаждающей жидкости (ниже кратко называемая канавкой). В случае подобного пятиугольного основания и кольцевого сверла с 2n (n≥1) кольцевыми сегментами количество образующихся канавок равно n.
В третьем варианте формируют заготовки из порошковых слоев с шестиугольными основаниями, состоящими из прямоугольника и равнобедренной трапеции. В зоне наклона боковых сторон подобной трапеции при спекании с соседними кольцевыми сегментами образуются канавки. В случае подобного шестиугольного основания и кольцевого сверла с n (n≥2) кольцевыми сегментами количество образующихся канавок равно n.
В особенно предпочтительном варианте высоту трапеции устанавливают между 1/3 и 5/6 от общей высоты заготовки. В случае кольцевых сверл, которые сваривают с хвостовиком, зону соответствующего соединения формируют без алмазов, в связи с чем она непригодна для обработки оснований. Для обработки оснований пригодна снабженная алмазными частицами матричная зона, высота которой составляет около 5/6 от общей высоты кольцевого сверла. В особенно предпочтительном варианте высоту трапеции устанавливают таким образом, чтобы она составляла 2/3 от общей высоты заготовки. При высоте трапеции, составляющей 2/3 от общей высоты кольцевого сверла, может быть обеспечена достаточная прочность готового кольцевого сверла. В процессе обработки кольцевым сверлом к месту обработки необходимо транспортировать охлаждающую жидкость, причем выполненные в кольцевом сверле канавки должны обладать максимально возможной длиной.
В предпочтительном улучшенном варианте осуществления изобретения кольцевые сегменты при спекании подвергают воздействию температуры и давления. При использовании технологии спекания, предусматривающей воздействие температуры и давления, например, метода горячего прессования, спекание происходит быстрее и при более низкой температуре по сравнению с технологией спекания, реализуемой без воздействия давления, например, по сравнению со свободным спеканием. Поскольку термические повреждения алмаза появляются уже при 600°С, более низкая температура спекания может обеспечить преимущества в отношении качества.
В особенно предпочтительном варианте посредством воздействия давления при спекании кольцевые сегменты подвергают дополнительному внешнему формованию. Для обработки различных оснований подходящими оказываются особые куполообразные формы. Подобные куполообразные формы можно создавать посредством воздействия давления при спекании.
Примеры осуществления изобретения
Ниже приведены примеры осуществления изобретения со ссылкой на прилагаемые к описанию чертежи. При этом соблюдение истинных масштабов не является обязательным: напротив, чертежи для наглядности выполнены схематически и/или в несколько искаженной форме. В отношении непосредственно обнаруживаемых на чертежах дополнительных технических решений следует сослаться на соответствующий уровень техники. При этом следует учитывать возможность многообразных модификаций и изменений формы и деталей того или иного варианта осуществления изобретения без отклонения от общей идеи изобретения. Указанные в описании, на чертежах и в формуле изобретения отличительные признаки как по отдельности, так и в любых комбинациях друг с другом могут иметь важное значение для усовершенствования изобретения. Кроме того, изобретение предусматривает любые комбинации по меньшей мере двух отличительных признаков, указанных в описании, на чертежах и/или в формуле изобретения. Общая идея изобретения не ограничена точной формой или деталями приведенного ниже предпочтительного варианта осуществления или ограничена объектом, сокращенным по сравнению с заявленным в формуле изобретения объектом. При указанных диапазонах параметров предельными, пригодными для любого использования и способными быть предметом притязания следует считать также находящиеся в указанных пределах значения. Для обозначения идентичных или подобных частей или частей с идентичной или подобной функцией для простоты используют одни и те же позиции.
На прилагаемых к описанию чертежах показано:
на фиг. 1 колонковая сверлильная коронка, состоящая из кольцевого сверла, цилиндрического хвостовика сверла и зажимаемой части,
на фиг. 2А-С первый вариант конструктивного исполнения предлагаемого в изобретении кольцевого сверла, сформированного из четырех кольцевых сегментов, в трехмерной проекции (фиг. 2А), перпендикулярное оси вращения поперечное сечение (фиг. 2В) и фрагмент в увеличенном масштабе (фиг. 2С),
на фиг. 3 второй вариант конструктивного исполнения предлагаемого в изобретении кольцевого сверла, сформированного из четырех кольцевых сегментов с канавками для охлаждающей жидкости,
на фиг. 4A-D изготовление показанного на фиг. 3 кольцевого сверла из четырех одинаковых заготовок с шестиугольным основанием (фиг. 4А), причем две заготовки преобразуют в вогнутые первые кольцевые сегменты и две заготовки преобразуют в выпуклые вторые кольцевые сегменты (фиг. 4В), первые и вторые кольцевые сегмент располагают поочередно один за другим вдоль направления окружности (фиг. 4С) и соединяют друг с другом при воздействии температуры и давления, получая сплошное кольцевое сверло (фиг. 4D),
на фиг. 5А-С заготовки с прямоугольным основанием (фиг. 5А), пятиугольным основанием (фиг. 5В) и шестиугольным основанием (фиг. 5С).
На фиг. 1 показана колонковая сверлильная коронка 10 с кольцевым сверлом 11, цилиндрическим хвостовиком 12 и зажимаемой частью 13 со вставляемым в зажим концом 14. Колонковую сверлильную коронку 10 закрепляют в зажиме устройства для колонкового сверления посредством вставляемого в зажим конца 14 и в режиме сверления указанного устройства приводят во вращение в направлении вращения 15 вокруг оси вращения 16, причем ось вращения 16 совпадает с цилиндрической осью колонковой сверлильной коронки 10.
Кольцевое сверло 11 сварено, спаяно, свинчено с хвостовиком 12 или скреплено ним иным надлежащим способом. Для обеспечения возможности сваривания кольцевого сверла 11 с хвостовиком 12 зона соединения кольцевого сверла 11 с хвостовиком 12 должна быть выполнена из пригодного для сварки материала и не должна включать алмазные частицы, поскольку алмазные частицы непригодны для сварки.
На фиг. 2А-С показан первый вариант конструктивного исполнения предлагаемого в изобретении кольцевого сверла 21, которое состоит из нескольких кольцевых сегментов и может заменить показанное на фиг. 1 кольцевое сверло 11 колонковой сверлильной коронки 10. При этом на фиг. 2А показано кольцевое сверло 21 в трехмерной проекции, на фиг. 2В перпендикулярное оси вращения 16 поперечное сечение кольцевого сверла 21 и на фиг. 2С фрагмент из представленного на фиг. 2В поперечного сечения в месте соединения двух кольцевых сегментов.
Кольцевое сверло 21 состоит из четырех кольцевых сегментов, которые по боковым краям соединены друг с другом и по окружности образуют сплошное кольцо (фиг. 2А). Кольцевые сегменты могут быть подразделены на два первых кольцевых сегмента 22.1, 22.2 и два вторых кольцевых сегмента 23.1, 23.2, которые располагают поочередно один за другим вдоль направления окружности кольцевого сверла 21. Первые кольцевые сегменты 22.1, 22.2 состоят из первой порошковой смеси 24 и первых алмазных частиц 25, а вторые кольцевые сегменты 23.1, 23.2 состоят из второй порошковой смеси 26 и вторых алмазных частиц 27 (фиг. 2В).
На фиг. 2С показан вырыв из представленного на фиг. 2В поперечного сечения в месте соединения первого кольцевого сегмента 22.1 со вторым кольцевым сегментом 23.1. Первый кольцевой сегмент 22.1 сформирован из m1 порошковых слоев первой порошковой смеси 24 и m1 алмазных слоев первых алмазных частиц 25. Второй кольцевой сегмент 23.1 сформирован из m2 порошковых слоев второй порошковой смеси 26 и m2 алмазных слоев вторых алмазных частиц 27. В показанном на фиг. 2С примере конструктивного исполнения первый кольцевой сегмент 22.1 имеет три порошковых слоя 28.1, 29.1, 30.1 (m1=3) и три алмазных слоя 32.1, 33.1, 34.1 (m1=3), второй кольцевой сегмент 23.1 имеет три порошковых слоя 35.1, 36.1, 37.1 (m2=3) и три алмазных слоя 38.1, 39.1, 40.1 (m2=3).
Первые алмазные частицы 25 алмазных слоев 32.1-34.1 расположены на трех круговых первых обрабатывающих дорожках 42.1, 43.1, 44.1 с разными первыми радиусами кривизны R1i (i=1, 2, 3). Вторые алмазные частицы 27 алмазных слоев 38.1-40.1 расположены на трех круговых вторых обрабатывающих дорожках 45.1, 46.1, 47.1 с разными вторыми радиусами кривизны R2i (i=1, 2, 3). Выбор материалов первой и второй порошковых смесей 24, 26, а также выбор распределения и размера первых и вторых алмазных частиц 25, 27 и количества m1, m2 алмазных слоев и обрабатывающих дорожек позволяет приводить кольцевое сверло 21 в соответствие с различными подлежащими обработке основаниями.
Кольцевые сегменты 22.1,22.2, 23.1, 23.2 послойно сформированы из трех порошковых слоев и трех алмазных слоев. В случае послойного формирования кольцевых сегментов порошковую смесь загружают в матрицу и формируют первый порошковый слой. Алмазные частицы в шаблоне для вставки помещают в качестве первого алмазного слоя на первый порошковый слой или, соответственно, в первый порошковый слой. Для уплотнения слоистой структуры после указанного размещения алмазных частиц можно выполнять промежуточное прессование. Затем вновь загружают порошковую смесь в матрицу и формируют второй порошковый слой. Алмазные частицы в шаблоне для вставки помещают в качестве второго алмазного слоя на второй порошковый слой или, соответственно, во второй порошковый слой. Данный процесс повторяют, пока не достигнут необходимой формируемой высоты заготовки. В качестве последнего слоя используют алмазный слой.
На фиг. 3 показан второй вариант конструктивного исполнения предлагаемого в изобретении кольцевого сверла 51, которое состоит из четырех кольцевых сегментов и может заменить кольцевое сверло 11 колонковой сверлильной коронки 10. Между кольцевыми сегментами сформированы четыре канавки 52.1, 52.2, 52.3, 52.4, через которые к месту обработки транспортируется охлаждающая жидкость. Кольцевые сегменты расположены таким образом, чтобы кольцевое сверло 51 на внутренней поверхности 53 и на наружной поверхности 54 попеременно имело заполненный алмазными частицами участок 55 и участок 56 без алмазных частиц.
Высота канавок 52.1-52.4 составляет около 2/3 от общей высоты кольцевого сверла 51. Для обеспечения функциональной способности кольцевого сверла 21 в случае износа канавок 52.1-52.4 два кольцевых сегмента снабжены соответствующими отверстиями 57.1, 57.2, через которые к месту обработки транспортируется охлаждающая жидкость.
На фиг. 4A-D показано изготовление кольцевого сверла 51 из четырех одинаковых заготовок 61 с шестиугольным основанием (фиг. 4А). Две заготовки 61 преобразуют в вогнутые первые кольцевые сегменты 62, а две заготовки 61 в выпуклые вторые кольцевые сегменты 63 (фиг. 4В). Первые и вторые кольцевые сегменты 62, 63 располагают поочередно один за другим вдоль направления окружности кольцевого сверла 51 (фиг. 4С) и при воздействии температуры и давления спекают в сплошное кольцевое сверло (фиг. 4D).
На фиг. 4А показана конструкция заготовки 61, послойно выполненной из порошковых слоев порошковой смеси 64 и слоев алмазных частиц 65. Заготовка 61 состоит из соединительного участка 66, называемого также нижней зоной, и обрабатывающего участка 67, называемого также матричной зоной. Можно осуществлять совместное послойное формирование соединительного участка 66 и обрабатывающего участка 67, причем алмазные частицы 65 в соединительный участок не вставляют. В качестве альтернативы соединительный участок можно изготавливать в виде отдельного участка и при спекании соединять с обрабатывающим участком.
Основание заготовки 61 обладает формой шестиугольника, состоящего из прямоугольника 68 и примыкающей к нему равнобедренной трапеции 69, причем соединительный участок 66 заготовки 61 находится внутри прямоугольника 68. В зоне боковых сторон трапеции при спекании вследствие дополнительного воздействия давления образуются канавки 52.1-52.4, через которые к месту обработки транспортируется охлаждающая жидкость. Высота h трапеции 69 в заготовке определяет высоту канавок 52.1-52.4. В данном примере высота h трапеции 69 соответствует половине общей высоты H заготовки.
На фиг. 4В показан первый кольцевой сегмент 62, который выполнен из представленной на фиг. 4А заготовки 61 при воздействии давления и обладает выпуклой кривизной, а также второй кольцевой сегмент 63, который выполнен из представленной на фиг. 4А заготовки 61 при воздействии давления и обладает вогнутой кривизной. Выполненная в виде алмазного слоя верхняя сторона заготовки 61 расположена на наружной стороне 54 первого кольцевого сегмента 62, а верхняя сторона заготовки 61 расположена на внутренней стороне 53 второго кольцевого сегмента 63.
Первый кольцевой сегмент 62 имеет первый и второй боковые края 71, 72, которые при спекании соединяются с первым и вторым боковыми краями 73, 74 второго кольцевого сегмента 63. При этом первый боковой край 71 первого кольцевого сегмента 62 соединяют со вторым боковым краем 74 второго кольцевого сегмента 63, а второй боковой край 72 первого кольцевого сегмента 62 с первым боковым краем 73 второго кольцевого сегмента 63. В случае кольцевого сверла 51 с двумя первыми и двумя вторыми кольцевыми сегментами 62.1, 62.2, 63.1, 63.2 соединяют друг с другом соответственно первые и вторые боковые края соседних кольцевых сегментов.
На фиг. 4С показаны первые кольцевые сегменты 62.1, 62.2 и вторые кольцевые сегменты 63.1, 63.2, которые располагают поочередно один за другим вдоль направления окружности кольцевого сверла 51. Кольцевые сегменты 62.1, 63.1, 62.2, 63.2, которые образуют сплошное кольцевое сверло и находятся в показанном на фиг. 4С расположении, подвергают дальнейшей переработке в горячем прессе. На фиг. 4D показано сплошное кольцевое сверло после горячего прессования. При горячем прессовании кольцевые сегменты 62.1, 63.1, 62.2, 63.2 подвергают воздействию температуры и давления. Воздействие температуры обеспечивает спекание порошковой смеси в кольцевые сегменты, которые по боковым краям соединяют друг с другом. В результате воздействия давления в осевом направлении, то есть параллельно оси вращения кольцевого сверла, происходит сжатие кольцевых сегментов, которое обусловливает их уплотнение. Горячее прессование выполняют в матрице, придающей кольцевому сверлу окончательную форму.
В соответствии с предлагаемым в изобретении способом кольцевое сверло формируют из нескольких заготовок, которые преобразуют в кольцевые сегменты и спекают в сплошное кольцевое сверло, причем подходящей геометрической формой оснований заготовок является многоугольник. На фиг. 5А-С показаны заготовки 81 с прямоугольным основанием (фиг. 5А), заготовки 82 с пятиугольным основанием (фиг. 5В) и заготовки 83 с шестиугольным основанием (фиг. 5С).
Прямоугольное основание 84 заготовок 81 обладает наиболее простой геометрической формой, подходящей для изготовления кольцевых сверл из нескольких кольцевых сегментов. В показанном на фиг. 5А примере для изготовления сплошного кольцевого сверла используют три одинаковые заготовки 81.1, 81.2, 81.3.
Пятиугольное основание заготовок 82 может быть разделено на прямоугольник 85 и трапецию 86 с двумя прямыми внутренними углами. В зоне наклона боковой стороны трапеции при спекании с соседним кольцевым сегментом образуется канавка 87. В случае подобного пятиугольного основания и кольцевого сверла с 2n (n≥1) кольцевыми сегментами количество образующихся канавок 87 равно n.
Шестиугольное основание заготовок 83 может быть разделено на прямоугольник 88 и равнобедренную трапецию 89. В зоне наклона боковых сторон трапеции при спекании с соседними кольцевыми сегментами образуются канавки 90. В случае подобного шестиугольного основания и кольцевого сверла с n (n≥2) кольцевыми сегментами количество образующихся канавок 90 равно n.
Глава 8: Сверление и сверление | Применение режущего инструмента
Сверление — один из самых сложных процессов обработки. Главной характеристикой, которая отличает его от других операций обработки, является комбинированная резка и выдавливание металла на кромке долота в центре сверла. Большая сила тяги, вызванная движением подачи, сначала выдавливает металл под кромку долота. Затем он имеет тенденцию к срезанию под действием инструмента с отрицательным передним углом.
Номенклатура спирального сверла — Режущее действие вдоль кромки сверла мало чем отличается от других процессов обработки.Однако из-за переменного переднего угла и наклона режущие кромки при разных радиусах режущих кромок отличаются друг от друга. Это осложняется ограничением всего стружки потоком стружки в любой точке вдоль кромки. Тем не менее, удаление металла — это настоящая резка, и проблемы с изменяемой геометрией и ограничениями присутствуют. Тем не менее, поскольку это такая небольшая часть от общей операции бурения, это не является отличительной особенностью процесса.
Настройки станка, используемые при сверлении, раскрывают некоторые важные особенности этой операции создания отверстий.Глубина резания, являющаяся основным параметром в других процессах резания, наиболее точно соответствует радиусу сверла. Ширина недеформированной стружки эквивалентна длине кромки сверла, которая зависит от угла при вершине, а также от размера сверла. Для данной установки ширина недеформированной стружки при сверлении остается постоянной. Размер подачи, указанный для сверления, представляет собой подачу на оборот шпинделя. Более фундаментальная величина — это подача на губу. Для обычного сверла с двумя режущими кромками это половина подачи на оборот.Толщина недеформированной стружки отличается от подачи на кромку в зависимости от угла при вершине.
Скорость шпинделя постоянна для любой одной операции, в то время как скорость резания меняется по всей режущей кромке. Скорость резания обычно рассчитывается для наружного диаметра. В центре режущей кромки зубила скорость резания равна нулю; в любой точке губы он пропорционален радиусу этой точки. Это изменение скорости резания вдоль режущих кромок является важной характеристикой сверления.
Как только сверло входит в контакт с заготовкой, контакт продолжается до тех пор, пока сверло не прорвет дно детали или не выйдет из отверстия. В этом отношении сверление похоже на токарную обработку и не похоже на фрезерование. Непрерывное резание означает, что вскоре после контакта сверла и заготовки можно ожидать постоянных усилий и температуры.
Номенклатура сверл — Наиболее важным типом сверл является спиральное сверло. Важная номенклатура указана ниже и проиллюстрирована на рисунке выше.
Сверло: Сверло — это концевой режущий инструмент для выполнения отверстий. Он имеет одну или несколько режущих кромок и канавки, позволяющие проникать жидкости и выбрасывать стружку. Сверло состоит из хвостовика, корпуса и острия.
Хвостовик: Хвостовик — это часть сверла, которая удерживается и приводится в движение. Он может быть прямым или коническим.
Трубка: Хвостовик — это уплощенная часть на конце хвостовика, которая входит в приводной паз держателя сверла на шпинделе станка.
Корпус: Корпус сверла простирается от хвостовика до острия и содержит канавки. Во время заточки частично стачивается корпус сверла.
Острие: Острие — это режущий конец сверла.
Канавки: Канавки — это канавки, которые прорезаны или сформированы в корпусе сверла, чтобы жидкости доходили до острия, а стружка — до поверхности заготовки. Хотя в некоторых случаях используются прямые канавки, обычно они имеют спиральную форму.
Земля: Земля — это остаток внешней части корпуса сверла после нарезания канавок. Земля немного сокращена от внешнего диаметра сверла, чтобы обеспечить зазор.
Поля: Поля — это небольшая часть земли, не отрезанная для очистки. Он сохраняет полный диаметр сверла.
Веб: Стенка — это центральная часть корпуса сверла, которая соединяет площадки.
Кромка зубила: Кромка, отшлифованная на острие инструмента вдоль стенки, называется кромкой зубила.Соединяет режущие губы.
Кромки: Кромки являются основными режущими кромками сверла. Они простираются от острия долота до периферии сверла.
Ось: Ось сверла является средней линией инструмента. Он проходит через полотно и перпендикулярно диаметру.
Шея: Некоторые сверла изготавливаются с участком разгрузки между корпусом и хвостовиком. Это называется шейкой сверла. В дополнение к этим терминам, которые определяют различные части сверла, существует ряд терминов, которые относятся к размерам сверла, включая важные углы сверления.Среди этих терминов:
Длина: Наряду с внешним диаметром указывается осевая длина сверла, когда указывается размер сверла. Кроме того, часто используются длина стержня, длина канавки и длина шейки.
Зазор по диаметру корпуса: Высота уступа от края до земли называется зазором по диаметру корпуса.
Толщина полотна: Толщина полотна — это наименьший размер полотна. Он измеряется в точке, если не указано иное.Толщина перемычки часто будет увеличиваться по мере продвижения вверх по корпусу от острия, и, возможно, ее придется отшлифовать во время заточки, чтобы уменьшить размер лезвия долота. Этот процесс называется «прореживанием сети».
Угол наклона винтовой линии: Угол, который передний край фаски образует с осью сверла, называется углом наклона спирали. Доступны сверла с различными углами наклона спирали для различных требований эксплуатации.
Угол при вершине: Угол между губками сверла называется углом при вершине.Он варьируется для разных материалов заготовки.
Угол снятия кромки: Угол снятия кромки соответствует обычным углам снятия кромки, используемым на других инструментах. Измеряется по периферии.
Угол кромки долота: Угол кромки долота — это угол между кромкой и кромкой долота, если смотреть с конца сверла.
Классы сверл — Существуют разные классы сверл для разных типов операций. Материалы заготовки также могут влиять на класс используемого сверла, но обычно он определяет геометрию острия, а не общий тип сверла, который лучше всего подходит для работы.Спиральное сверло — самый важный класс. В общем классе спиральных сверл есть несколько типов сверл, предназначенных для различных видов работ.
Сверла с большой спиралью: У этого сверла большой угол наклона спирали, что повышает эффективность резания, но ослабляет корпус сверла. Он используется для резки более мягких металлов и других материалов с низкой прочностью.
Сверла с малой спиралью: Угол наклона спирали ниже нормального иногда бывает полезен для предотвращения «забегания вперед» или «заедания» инструмента при сверлении латуни и подобных материалов.
Сверла для тяжелых условий эксплуатации: Сверла, подверженные большим нагрузкам, можно сделать более прочными с помощью таких методов, как увеличение толщины стенки.
Левосторонние сверла: Стандартные спиральные сверла могут изготавливаться как левосторонние инструменты. Они используются в нескольких сверлильных головках, где конструкция головки упрощена, позволяя шпинделю вращаться в разных направлениях.
Сверла с прямой канавкой: Сверла с прямой канавкой — это крайний случай сверл с малой спиралью. Они используются для сверления латуни и листового металла.
Сверла для коленчатого вала: Сверла, специально разработанные для работы с коленчатым валом, оказались полезными для обработки глубоких отверстий в твердых материалах. У них тяжелая перепонка и угол наклона спирали несколько больше обычного.
Удлинители: Удлинители имеют длинный закаленный хвостовик, позволяющий сверлить на поверхностях, которые обычно недоступны.
Сверла увеличенной длины: Для глубоких отверстий стандартного длинного сверла может оказаться недостаточно, и потребуется сверло с более длинным корпусом.
Ступенчатое сверло: Спиральное сверло может шлифовать два или более диаметра для получения отверстия ступенчатого диаметра.
Сверло для обработки ложа: Сверло для обработки углублений или сверло с несколькими режущими кромками выполняет ту же работу, что и ступенчатое сверло. У него есть отдельные пазы, идущие по всей длине корпуса для каждого диаметра, тогда как ступенчатое сверло использует одну пазу. Подземное сверло выглядит как два сверла, скрученных вместе.
Твердосплавные сверла: Для сверления небольших отверстий в легких сплавах и неметаллических материалах твердосплавные стержни можно отшлифовать до стандартной геометрии сверла.Необходимо выполнять легкие пропилы без ударов, потому что твердый сплав довольно хрупкий.
Сверла с твердосплавными напайками: Сверла с твердосплавными напайками можно использовать в спиральных сверлах для повышения износостойкости кромок на высоких скоростях. Сверла с твердосплавными напайками широко используются для обработки твердых абразивных неметаллических материалов, таких как кладка.
Сверла для масляных отверстий: Небольшие отверстия в пазах или маленькие трубки в пазах, фрезерованных в пазах, можно использовать для нагнетания масла под давлением к острию инструмента. Эти сверла особенно полезны для сверления глубоких отверстий в твердых материалах.
Плоские сверла: Плоские стержни можно шлифовать с помощью обычного сверла на конце. Это дает очень большие пространства для стружки, но без спирали. Их основное применение — бурение железнодорожных путей.
Сверла с тремя и четырьмя канавками: Существуют сверла с тремя или четырьмя канавками, которые напоминают стандартные спиральные сверла, за исключением того, что у них нет резца. Они используются для увеличения отверстий, которые ранее были просверлены или пробиты. Эти сверла используются потому, что они обеспечивают лучшую производительность, точность и качество поверхности, чем стандартное сверло при той же работе.
Сверло и зенковка: Комбинированное сверло и зенкер — полезный инструмент для обработки «центральных отверстий» на стержнях, которые нужно точить или шлифовать между центрами. Конец этого инструмента напоминает стандартное сверло. Зенковка начинается на небольшом расстоянии от корпуса.
Сопутствующие операции бурения — Некоторые операции связаны с бурением. В следующем списке большинство операций следует за сверлением, за исключением центрирования и точечной обработки, которые предшествуют сверлению.Отверстие должно быть сначала просверлено, а затем отверстие модифицируется одной из других операций. Некоторые из этих операций проиллюстрированы ниже.
Развертка: Развертка используется для увеличения ранее просверленного отверстия, обеспечения более высокого допуска и улучшения чистоты поверхности отверстия.
Нарезание резьбы: Метчик используется для нарезания внутренней резьбы на ранее просверленном отверстии.
Зенковка: Зенковка дает больший шаг в отверстии, чтобы головка болта могла располагаться ниже поверхности детали.
Зенковка: Зенковка аналогична зенковке, за исключением того, что ступенька является угловой, что позволяет винтам с плоской головкой располагаться ниже поверхности.
Центрирование: Центровочное сверление используется для точного определения местоположения отверстия, которое будет просверлено впоследствии.
Точечная наплавка: Точечная наплавка используется для получения плоской обработанной поверхности детали.
Условия эксплуатации — Различные условия, в которых используются сверла, затрудняют установление правил для скорости и подачи.Производители сверл и различные справочные тексты предоставляют рекомендации по правильной скорости и подаче для сверления различных материалов.
Скорость сверления: Скорость резания — это скорость, с которой точка на окружности сверла проходит за 1 минуту. Он выражается в поверхностных футах в минуту (SFPM). Скорость резания — один из важнейших факторов, определяющих срок службы сверла. Если скорость резания слишком низкая, сверло может сломаться или сломаться.Слишком высокая скорость резания приводит к быстрому притуплению режущих кромок. Скорость резания зависит от следующих семи переменных:
- Тип просверливаемого материала. (Чем тверже материал, тем ниже скорость резания.)
- Материал и диаметр режущего инструмента. (Чем тверже материал режущего инструмента, тем быстрее он обрабатывает материал. Чем больше сверло, тем медленнее оно должно вращаться.)
- Типы и использование смазочно-охлаждающих жидкостей позволяют увеличить скорость резания.
- Жесткость сверлильного станка.
- Жесткость сверла. (Чем короче сверло, тем лучше.)
- Жесткость рабочей установки.
- Качество просверливаемого отверстия.
Перед сверлением отверстия необходимо учитывать каждую переменную. Каждая переменная важна, но наиболее важными факторами являются рабочий материал и скорость его резания.
Подача при сверлении: После выбора скорости резания для определенного материала и состояния заготовки необходимо установить соответствующую скорость подачи.Скорость подачи сверления выбрана так, чтобы максимизировать производительность при сохранении стружкодробления. Подача при сверлении выражается в дюймах на оборот, или IPR, что представляет собой расстояние, на которое сверло перемещается в дюймах за каждый оборот сверла. Подача также может быть выражена как расстояние, пройденное сверлом за одну минуту, или IPM (дюймы в минуту), которое является произведением числа оборотов в минуту и IPR сверла. Его можно рассчитать следующим образом: IPM = IPR x RPM.
Выбор скорости сверления (SFPM) и подачи сверления (IPR) для различных обрабатываемых материалов часто начинается с рекомендаций в виде таблиц применения от производителей или с помощью справочников.
Износ спирального сверла — Износ сверла начинается, как только начинается резание, и вместо того, чтобы прогрессировать с постоянной скоростью, износ постоянно ускоряется. Износ начинается с острых углов режущих кромок и в то же время распространяется вдоль режущих кромок к кромке долота и вверх по краям сверла. По мере износа зазор уменьшается. В результате трения возникает больше тепла, что, в свою очередь, приводит к более быстрому износу.
Полосы износа за режущими кромками не являются лучшими индикаторами износа, так как они зависят от угла снятия кромки.Износ кромок сверла фактически определяет степень износа и не так очевиден, как износ площадок. Когда углы сверла закруглены, сверло повреждено больше, чем это очевидно. Вполне возможно, что сверло работало нормально даже во время ношения. Края можно было сточить конусом на расстоянии до дюйма от острия.
Чтобы восстановить инструмент до нового состояния, необходимо удалить изношенный участок. Из-за ускоряющегося характера износа количество отверстий на дюйм сверла иногда можно увеличить вдвое, уменьшив на 25 процентов количество отверстий, просверливаемых за одно шлифование.
Шлифование вершины сверла — Было подсчитано, что около 90 процентов проблем при сверлении происходит из-за неправильной заточки вершины сверла. Поэтому важно соблюдать осторожность при переточке сверл. Хорошее острие сверла будет иметь: обе кромки под одинаковым углом к оси сверла; обе губы одинаковой длины; правильный клиренс; и правильная толщина полотна.
Лопаточные сверла — Инструмент обычно состоит из режущего лезвия, закрепленного в держателе с канавками. Лопаточные сверла могут обрабатывать гораздо большие отверстия (до 15 в диаметре), чем спиральные сверла.Сверла диаметром менее 0,75 мм обычно недоступны. Допустимая глубина сверления перфорированных сверл с возможным отношением длины к диаметру более 100: 1 намного превышает таковую у спиральных сверл.
В то же время, из-за их гораздо большей способности подачи, скорость проникновения перфорационных сверл превышает таковую у спиральных сверл на 60–100 процентов. Однако из-за этого обычно страдает чистовая обработка отверстий. По сравнению с спиральными сверлами, перфорационные сверла гораздо более устойчивы к вибрации при тяжелых подачах, когда они полностью входят в зацепление с заготовкой.Прямолинейность отверстия обычно улучшается (при сопоставимых размерах) за счет использования перфоратора. Однако эти преимущества могут быть получены только при использовании сверлильных станков соответствующей мощности и мощности.
Перфоратор также является очень экономичным сверлом из-за его гибкости по диаметру. Один держатель подходит для лезвий разных диаметров. Поэтому, когда требуется изменение диаметра, необходимо покупать только лезвие, что намного дешевле, чем покупка всего сверла.
Твердосплавные сверла со сменными пластинами — Сверло со сменными пластинами стало настолько эффективным и экономичным, что во многих случаях просверлить отверстие дешевле, чем его отлить или ковать.По сути, сверло со сменными пластинами представляет собой инструмент с двумя режущими кромками и центральной режущей кромкой со сменными твердосплавными пластинами. Сверла со сменными пластинами были введены с использованием квадратных пластин. В сверлах со сменными пластинами, использующими более популярную пластину Trigon, используются две пластины; но по мере увеличения размера добавляется больше пластин, до восьми пластин в очень больших инструментах.
Сверла со сменными пластинами имеют проблему нулевой скорости резания в центре, даже если скорость может превышать 1000 SFPM на крайних пластинах. Поскольку скорость обычно до некоторой степени заменяет подачу, осевые силы обычно составляют от 25 до 30 процентов от сил, требуемых для обычных инструментов того же размера.Сверла со сменными пластинами имеют хвостовик, корпус и многогранное острие. Обычно доступны конструкции хвостовиков: прямые, конические и V-образные фланцы № 50.
Корпуса имеют две канавки, которые обычно прямые, но могут иметь спиральную форму. Поскольку для обеспечения опоры подшипника отсутствуют поля, инструменты должны полагаться на присущую им жесткость и баланс сил резания, чтобы поддерживать точный размер отверстия и прямолинейность. Поэтому эти инструменты обычно ограничиваются отношением длины к диаметру примерно 4: 1.
Острие сверла изготовлено из твердосплавных пластин с карманами. Эти вставки обычно специально разработаны. Режущая кромка может быть отрицательной, нейтральной или положительной, в зависимости от держателя и конструкции пластины. Твердосплавные сплавы с покрытием и без покрытия доступны для сверления самых разных рабочих материалов. Иногда сверла комбинируются со сменными или сменными пластинами для выполнения нескольких операций, таких как сверление, зенкование и зенкование.
Монтажный инструмент с пластинами на корпусе может выполнять несколько операций.
Общая геометрия режущих кромок важна для работы сверл со сменными пластинами. Как упоминалось ранее, нет опорных полей для удержания этих инструментов в рабочем состоянии, поэтому силы, необходимые для перемещения режущих кромок через обрабатываемый материал, должны быть сбалансированы, чтобы минимизировать отклонение инструмента, особенно при запуске, и поддерживать размер отверстия.
Хотя они в основном предназначены для сверления, некоторые сверла со сменными пластинами могут выполнять торцевание и растачивание на токарных станках.Насколько хорошо эти инструменты работают в этих приложениях, зависит от их размера, жесткости и конструкции.
При правильном использовании сверла со сменными пластинами работают впечатляюще. Однако для успешного применения необходимо тщательно соблюдать рекомендации производителя.
Трепанирование — При трепанировании режущий инструмент производит отверстие, удаляя дискообразную деталь, также называемую заготовкой или сердечником, обычно из плоских пластин. Отверстие производится без превращения всего удаляемого материала в стружку, как в случае сверления.Процесс трепанирования может использоваться для изготовления дисков диаметром до 6 дюймов из плоского листа или пластины. Инструмент для трепанирования, также называемый Rotabroach.
Трепанирование может выполняться на токарных станках, сверлильных станках и фрезерных станках, а также на других машинах, использующих одноточечные или многоточечные инструменты. Сверла Rotabroach обеспечивают больший срок службы инструмента, поскольку они имеют больше зубьев, чем обычные сверлильные инструменты. Поскольку в заготовке задействовано больше зубьев, материал, вырезанный на одно отверстие, распределяется по большему количеству режущих кромок.Каждая режущая кромка прорезает меньше материала для данного отверстия. Это значительно увеличивает срок службы инструмента.
Операции трепанации — Трепанирование — это черновая операция. Для чистовой обработки требуется вторичная операция с использованием разверток или расточных оправок для получения заданного размера и чистовой обработки. Из многих типов операций по просверливанию отверстий он конкурирует с твердосплавными фрезами со сменными пластинами и лопаточным сверлением.
Для трепана используются инструменты нескольких типов. Самый простой — это фрезы с одним или двумя остриями.Кольцевая пила — еще один инструмент для трепанации отверстий.
Выбор материала для режущего инструмента — Быстрорежущая сталь M2 (HSS) — это стандартный материал для режущего инструмента Rotabroach. M2 имеет широчайший диапазон применения и является наиболее экономичным инструментальным материалом. Его можно использовать для обработки черных и цветных металлов и обычно рекомендуется для резки материалов плотностью до 275 BHN. M2 можно наносить на более твердые материалы, но стойкость инструмента значительно снижается.
Сверла Rotabroach M2 HSS с покрытием TiN предназначены для более высоких скоростей, большей выносливости, более твердых материалов или более свободного резания для снижения энергопотребления.Покрытие TiN снижает трение и работает при более низких температурах, обеспечивая более твердую поверхность режущей кромки. Инструменты с покрытием TiN рекомендуются для обработки материалов до 325 BHN.
Твердосплавные режущие инструменты также доступны в качестве специальной опции для сверл Rotabroach. Карбид имеет определенные преимущества перед быстрорежущей сталью. Возможности применения ограничены, и их необходимо обсуждать с представителем производителя.
Жесткость и допуск на размер отверстия — Сверла Rotabroach изначально были разработаны как инструменты для черновой обработки, чтобы конкурировать с спиральными сверлами и обеспечивать аналогичные допуски отверстий.Многие пользователи успешно применили сверла Rotabroach для получистовой обработки, сократив количество проходов с двух или более до одного. Для изготовления отверстий в соответствии с этими спецификациями требуется жесткий станок и установка. Допуски зависят от области применения, и их невозможно точно определить.
Chip Control — В таких материалах, как алюминий, инструментальная сталь и чугун, правильный выбор подач и скоростей обычно приводит к дроблению стружки и ее вымыванию из резания смазочно-охлаждающей жидкостью.Во многих других материалах, таких как низкоуглеродистые и легированные стали, стружка имеет тенденцию быть длинной и часто наматывается на сверло, образуя «птичье гнездо». В большинстве ручных операций это раздражение перевешивается другими преимуществами метода. Однако в автоматизированных операциях недопустимо скопление стружки вокруг сверла. Помимо очевидных проблем, которые это может вызвать, скопление стружки препятствует потоку дополнительной стружки, пытающейся выйти из канавок. Это, в свою очередь, может привести к уплотнению канавок и поломке сверла.
Есть несколько методов, которые можно использовать для измельчения стружки, если это не может быть достигнуто путем регулировки подачи и скорости. Один из способов — использовать прерванный цикл кормления. Не рекомендуется втягивать сверло, как в цикле «клевки», потому что стружка может застрять под режущими кромками. Вместо этого используйте очень короткую паузу примерно каждые два оборота. Это приведет к образованию стружки, которая обычно бывает достаточно короткой, чтобы не оборачиваться вокруг инструмента. В запрограммированной задержке может не быть необходимости, поскольку между последовательными командами подачи в системе ЧПУ, вероятно, присущи некоторые колебания.
Преимущества инструментов для трепанации — Спиральное сверло имеет центральную точку, которая на самом деле не является точкой. Это пересекающаяся линия, где два угла режущей кромки встречаются на стенке сверла. Это так называемая «мертвая зона» спирального сверла.
Это называется мертвой зоной, потому что поверхностная скорость режущих кромок (коэффициент числа оборотов в минуту и диаметр сверла) приближается к нулю, когда соответствующий диаметр приближается к нулю. Более низкая скорость резания снижает эффективность резки и требует повышенного давления подачи, чтобы режущие кромки врезались в материал.Фактически, центр сверла не режет — оно продвигается сквозь материал. Величина осевого усилия, необходимого для преодоления сопротивления заготовки, часто вызывает деформацию заготовки или углубление вокруг отверстия, а также создает вторую проблему — заусенцы или отслаивание вокруг стороны прорыва отверстия. По мере того, как материал на дне отверстия становится все тоньше и тоньше, если подача не снижается, сверло будет проталкиваться, обычно оставляя прикрепленными два зазубренных остатка материала.
Инструменты для трепанирования производят отверстия быстрее, чем обычные инструменты.На приведенном ниже рисунке показано отверстие диаметром 1 1/2 дюйма, просверленное в стальной пластине 1018 толщиной 2 дюйма с помощью: перфорационного сверла, спирального сверла, твердосплавного сверла со сменными пластинами и перфоратора Rotabroach. При сокращении времени бурения примерно на 50-80% стоимость отверстия может быть значительно ниже.
Джордж Шнайдер-младший является автором Cutting Tool Applications, справочника по материалам, принципам и конструкциям станков. Он является почетным профессором инженерных технологий Технологического университета Лоуренса и бывшим председателем Детройтского отделения Общества инженеров-технологов.
Сверла — режущие инструменты | Начи Америка
Отвечая на спрос на снижение затрат на обработку и сокращение времени выполнения заказа, а также на вашу потребность в обработке разнообразных деталей и снижении воздействия на окружающую среду. Nachi America поддерживает вас в постоянно меняющейся среде, в которой вам необходимо решать технологические задачи повышения эффективности, точности и функциональности.
Твердосплавные сверла
значительно улучшает все функции сверления
Детали | |
Одношаговое сверление с минимальным заусенцем
Подробная информация | |
Одношаговое сверление с минимальным заусенцем
Детали | |
Последовательное высокопроизводительное сверление
Детали | |
Стабильное высокопроизводительное сверление
Детали | |
One Shot Drilling до 40XD
Детали | |
Одноэтапное сверление с минимальным заусенцем
Детали | |
Aqua Coat с высокой надежностью
Детали |
Сверла из быстрорежущей стали
Сокращение времени и процесса
Детали | |
Высокопроизводительное сверло из быстрорежущей стали с быстрой подачей
Детали | |
Сухое сверление алюминия | |
HSS и HSSCO, разработанные Nachi
Детали | |
HSS и HSSCO, разработанные Nachi
Подробности | |
HSS и HSSCO, разработанные Nachi
Детали | |
Сверла Nachi Long Drills из быстрорежущей стали
Детали | |
HSS и HSSCO, разработанные Nachi
Подробности | |
Nachi разработал HSS
Подробности |
Как изготавливается спиральное сверло? — Производство спиральных сверл из быстрорежущей стали
Основной процесс производства спирального сверла включает в себя обработку спиральных канавок, термообработку и заточку по трем аспектам.Поскольку термическая обработка и последующий процесс шлифования в основном одинаковы, основное различие заключается в том, что в процессе формовки используется спиральное сверло. В настоящее время для процесса изготовления спирального сверла в основном используются следующие три метода: метод фрезерования, метод прокатки, метод шлифования.
Процесс изготовления спирального сверла
Метод фрезерования : Фрезерование спиральной канавки требуемой формы с помощью формовочной фрезы на незакаленной заготовке спирального сверла.Метод фрезерования имеет большой диапазон обработки при производстве спиральных сверл, в основном это обработка спиральных сверл от 2,5 до 70 мм.
Недостатком метода фрезерования является высокая стоимость инструмента, длительное время обработки спирального сверла и окончательная обработка окончательной формы перед термообработкой. Во время термообработки могут возникать геометрические ошибки, почти все из которых отражаются на готовом сверле.
Прокатка : сверло прокатывают по нагретой заготовке с четырьмя веерообразными пластинами, чтобы сформировать форму сверла.
По сравнению с методом фрезерования, с использованием пластической деформации сверла , изготовителя сверла с меньшей точностью, кроме того, из-за термической обработки изменится геометрия спирального сверла для прокатки, что сделает невозможным выполнение требований сверления качественные отверстия.
Основным преимуществом этого метода является экономия сырья для изготовления спирального сверла при хорошей экономии.
Шлифование : Новейший способ обработки спиральных сверл.
Когда скорость круга достигает 100 м / с, спиральная канавка спирального сверла шлифуется из всего материала, высокоскоростное шлифование может снизить силу резания, значительно улучшить качество поверхности и уменьшить погрешность формы. По сравнению с методом измельчения, метод измельчения может значительно сократить время обработки одной детали, обеспечить высокое качество и стабильность.
В настоящее время методом изготовления спирального шлифовального сверла можно производить только спиральные сверла диаметром 15 или меньше.
Технический анализ и экономические эффекты трех производственных процессов спирального сверла.
1. Технические показатели
Фрезерование | Прокатка | Фрезерование | |||||||||||||||||||||||||||||||||||||||||||||||||||||||||||||||||||||||||||||||||||||||||||||||||||||||||||||||||||||||||||||||||||||||||||||||||||||||||||||||||||||||||||||||||||||||||||||||||||||||||||||||||||||||||||||||||||||||||||||||||||||||||||||||||||||||||||||||||||||||||||||||||||||||||||||||||||||||||||
Шероховатость Ra (мкм) | Кромочная лента | 4.6 | 6,5 | 8,6 | 12,5 | 3,2 | |||||||||||||||||||||||||||||||||||||||||||||||||||||||||||||||||||||||||||||||||||||||||||||||||||||||||||||||||||||||||||||||||||||||||||||||||||||||||||||||||||||||||||||||||||||||||||||||||||||||||||||||||||||||||||||||||||||||||||||||||||||||||||||||||||||||||||||||||||||||||||||||||||||||||||||||||||||||
Симметрия заслонки лезвия | 0.105 | 0,301 | 0,03 | ||||||||||||||||||||||||||||||||||||||||||||||||||||||||||||||||||||||||||||||||||||||||||||||||||||||||||||||||||||||||||||||||||||||||||||||||||||||||||||||||||||||||||||||||||||||||||||||||||||||||||||||||||||||||||||||||||||||||||||||||||||||||||||||||||||||||||||||||||||||||||||||||||||||||||||||||||||||||||
Радиальное биение | 0,05 | 0,08 | 0,01 | ||||||||||||||||||||||||||||||||||||||||||||||||||||||||||||||||||||||||||||||||||||||||||||||||||||||||||||||||||||||||||||||||||||||||||||||||||||||||||||||||||||||||||||||||||||||||||||||||||||||||||||||||||||||||||||||||||||||||||||||||||||||||||||||||||||||||||||||||||||||||||||||||||||||||||||||||||||||||||
Биение канавки | 0,05 | 0,18 | 0,05 | 0,18 | 0,05 Из-за изготовления спирального сверла в дополнение к обработке спиральной канавки другие процессы обработки в основном такие же, по этой причине для этого сравнения только время обработки спиральной канавки.За один час обработки спиральным сверлом 12 мм с прямой ручкой несколько примеров.
Условия эксперимента: (1) Обрабатываемые материалы: закалка стали 45 #, HB — 190-200 (2) Параметры сверления; V = 30м / дождь, f-0.28 мм / об, глубина отверстия: 36 мм, глухое отверстие. (3) Смазочно-охлаждающая жидкость: эмульгированный раствор масла и воды 4. Экономический эффект Фрезерование: Этот метод обработки имеет низкую производительность. Он подходит только для мелкосерийного производства одной детали, со сложной структурой резца, высокой ценой и множеством процессов, для сверл с разными характеристиками требуется резец с разными характеристиками, поэтому стоимость производства высока. По сравнению с методом измельчения этот метод позволяет легко добавлять стружку. Прокат: (1) Экономия сырья: поскольку прокатка является бесструнной обработкой, она может сэкономить более 30% быстрорежущей стали, коэффициент использования материала может достигать более 90%, в то время как коэффициент использования материала метод резки металла составляет всего 60% -70%. (2) Повышенная эффективность производства: использование процессов прокатки может повысить эффективность производства в 15-20 раз, и, по оценкам, четырехспицевый стан эквивалентен 15-20 автоматическим фрезерным станкам. (3) Повышение внутреннего качества: при резке металла обрабатывается весь пруток путем удаления материала, который полностью разрушает волокнистую ткань металла, в то время как при прокатке волокнистый слой металла не режется. Более того, он деформируется при высоких температурах, которые очищают ткань мозга и улучшают равномерное распределение карбидов, тем самым улучшая их внутреннее качество. (4) Снижение затрат: поскольку это может сэкономить не менее 30% HSS и повысить производительность труда в 15-20 раз, это может значительно сократить производственное оборудование и операторов; он позволяет уменьшить площадь рабочего завода, а также рабочих, измерительных инструментов и материалов. (5) Точность невысокая, так как термообработка проводится после прокатки, и геометрические параметры соответственно изменятся. Шлифование Производительность выше, чем у метода фрезерования; исключает деформацию изгиба и сохраняет процесс правки; высокая точность обработки и стабильное качество. Очень низкий процент брака. Высокая цена оборудования. Небольшой диапазон обработки и сложный сбор стружки. Таким образом, приведенные выше данные показывают, что процессы шлифовального сверла из быстрорежущей стали, прокатки и фрезерования в некоторой степени сравниваются со следующими. 1, Высокая геометрическая точность шлифовальной коронки. В процессе прокатки и фрезерования нарезание канавок сверла должно выполняться перед закалкой, что снижает геометрическую точность сверла из-за искажения процесса закалки. Процесс шлифования заключается в шлифовании канавки после закалки, устранении деформации, вызванной закалкой, так что геометрическая точность сверла может быть улучшена, что может сделать спецификацию размера сверла более тонкой, чтобы соответствовать точная обработка различных размеров, повышение точности диаметра отверстия обрабатываемых деталей, может сэкономить процесс сверления и последующего развертывания. 2. Высокая чистота шлифовальных сверл. Прокатные и фрезерованные сверла имеют чистоту 6 или меньше, а фрезерованные сверла имеют чистоту 8 или более. Улучшение чистовой обработки бурового долота не только улучшает чистовой диаметр отверстия обрабатываемых деталей, устраняя процесс чистовой обработки после сверления, но также обеспечивает плавный отвод стружки из канавки сверла, уменьшая поломку сверла из-за закупорки. 2. Длительный срок службы шлифовального сверла. Доказано, что шлифовальные сверла имеют в 1-2 раза больший срок службы, чем сверла для прокатки и фрезерования.Это связано с хорошей точностью, чистотой обработки, острыми краями и равномерным распределением напряжений шлифовальных сверл. 4. Высокая производительность. Теперь процесс шлифования перешел в стадию интенсивного шлифования, а производительность обработки долот в 2-5 раз выше, чем при фрезеровании. С точки зрения точности / чистоты / производительности / стоимости все три процесса являются инкрементными. Прокатка < Фрезерование < Шлифование Зная описанный выше процесс, я считаю, что вы уже знаете, как выбрать правильное сверло.Чтобы узнать больше о продукте, следите за обновлениями в следующих статьях. TTC PRODUCTION 01-001-028 Сверло Jobbers 7/16 «TTC PRODUCTION 01-001-028 Сверло Jobbers 7/16″ | Инструмент TraversПохоже, в вашем браузере отключен JavaScript. Для наилучшего взаимодействия с нашим сайтом обязательно включите Javascript в своем браузере. Нажмите на изображение, чтобы увеличить
Многие металлообрабатывающие изделия действительно содержат металлы, которые включены в последнее предупреждение Prop 65.Воздействие элементов может быть вредным. Может вызвать рак и нанести вред репродуктивной системе. ПодробностиОбработка поверхности увеличивает стойкость к истиранию, уменьшает количество стружки при сварке и улучшает отвод стружки Области применения
Характеристики
Технические характеристики
Мы нашли другие продукты, которые могут вам понравиться!backgroundLayer 1backgroundLayer 1Copyright © 2021 Travers Tool Co.Все права защищены. Обработка с ЧПУ, Твердосплавные сверла, фрезы и расточные оправки Производственные ресурсыПочему Accuromm?Наше современное оборудование и компьютеризированные процессы контроля помогают обеспечить полную точность .
Производственная обработка
Стандартные размеры инструмента Твердосплавные сверла и твердосплавные паяные сверла со стальным хвостовиком Доступны фрезы и расточные оправки большего размера Отверстия PCD (поликристаллический алмаз) и отверстия для охлаждающей жидкости доступны для инструментов диаметром 5 мм и выше.Также доступны чертежи с двойными размерами
Аккумуляторная дрель — DDL WikiИз DDL Wiki Группа II Область применения Использование аккумуляторной дрели разнообразно и во многом зависит от «бита», помещенного в патрон.Хотя эти долота важны, наше внимание будет по-прежнему сосредоточено на работе самого бурового станка. Потребности и требования У дрели должны быть определенные потребности клиентов: срок службы батареи, портативность, комфорт, долговечность и способность работать в необычных местах. В дополнение к этому, однако, существуют определенные требования, которых следует ожидать от аккумуляторной дрели. Как и в случае с потребностями заказчика, дрель должна иметь долговечный аккумулятор и быть портативной. Он также должен быть безопасным, иметь надежные детали и в целом быть более удобным, чем обычная сетчатая дрель. Системная функция Дрель активируется нажатием спускового крючка на передней части рукоятки. В результате патрон вращается со скоростью, пропорциональной степени нажатия спускового крючка. Чтобы эффективно использовать дрель, пользователю необходимо иметь приличную силу руки и контроль пальцев, чтобы вставить сверло, а также не позволять сверлу вылетать из его руки. Кроме того, правильное использование должно определяться окружающей средой, в которой используется буровая установка, с учетом хорошего освещения, достаточно низкого окружающего шума и отсутствия чрезмерной влажности (например, дождя), попадающей в обсадную колонну. Производство Сверло кажется очень рентабельным, с небольшим количеством деталей, большинство из которых, если не все, массово производятся с использованием таких технологий, как литье под давлением. С точки зрения сборки сверло выглядит хорошо сконструированным. Рама, например, защелкивается, а затем закрепляется винтами. Одна область для улучшения может заключаться в количестве используемых типов винтов. Мы нашли пять различных типов винтов и полагаем, что четыре из этих размеров можно было бы объединить. Анализ видов отказов и последствий Возможные проблемы в работе дрели могут быть связаны с муфтой, патроном, аккумулятором и гильзой.Для сцепления действие очень жесткое и не очень легко меняет направление. Это может привести к перелому из-за того, что пользователь приложит слишком много усилий. Для патрона возможна поломка, а в данном случае может отсутствовать эргономика, что приведет к неудобному захвату. Проблема, которую мы считаем самой важной, заключается в батарее. Мощность кажется очень низкой, и мы рекомендуем найти батарею более высокого качества для замены 9,6 В. При кратком наблюдении становится очевидным, что основная цель сверла — вращать «долото» с достаточно высокими скоростями и крутящим моментом для выполнения задачи.Существует множество различных «бит» для выполнения множества различных задач, наиболее распространенными из которых являются сверла и насадки для отверток. Эти «биты» типа используются в основном в функциях, которые в конечном итоге связаны с тем или иным скреплением двух или более объектов вместе. Другие применения включают взбивание яиц, водяные насосы, дремлинг и т. Д. Несмотря на то, что многие из этих «бит» существуют, наше внимание сосредоточено на самой аккумуляторной дрели, поэтому наше обсуждение не будет напрямую включать использование этих «бит», а роль дрель играет в их вращении и в том, что требуется от дрели. Что касается среднестатистического использования потребителями, мы обнаружили, что пользователи очень нуждаются в аккумуляторных дрелях. Пользователи хотят, чтобы в их аккумуляторной дрели была батарея, которая прослужила долгое время или имела очень быстрое время перезарядки, потому что необходимость останавливать проект только для того, чтобы подзарядить батарею, становится большим неудобством. Для непрерывного использования в течение максимального количества времени, которое позволяет батарея, конструкция дрели должна быть эргономичной, легкой и обеспечивать низкий уровень вибрации / шума, чтобы не вызывать у пользователя дискомфорта, такого как образование пузырей, отек суставов или болезненность руки.Другими средними потребностями клиентов являются максимальная мощность, простота и относительно интуитивное управление, а также возможность использовать дрель в ограниченном пространстве, неудобных углах или в местах с препятствиями. В конечном итоге аккумуляторная дрель должна быть достаточно функциональной, чтобы позволить пользователю выполнить небольшой проект более эффективно, чем с помощью ручных инструментов. Конструкция аккумуляторной дрели требует, чтобы ее использование было явным преимуществом по сравнению с аналогичным ручным инструментом, а также способно работать так, как не может ее аналог со шнуром.Аккумуляторные дрели должны обладать мощностью, необходимой для создания необходимого количества крутящего момента для того, что считается средним использованием функций, быстрее и значительно проще, чем ручной инструмент. Достаточно прочный и надежный, чтобы выдерживать длительное многократное использование без сбоев и вреда для пользователя. Маркировки и ярлыки на инструменте должны быть достаточно адекватными, чтобы неопытный средний человек мог их понять и использовать. Срок службы батареи и время перезарядки должны быть как можно более длинными и короткими (соответственно), по 2 часа для каждого из них, что является разумным стандартом.Аккумуляторные дрели должны обеспечивать достаточную мощность, будучи портативными и легкими, чтобы выполнять функции, требующие использования в областях, где сетевые или пневматические дрели являются неудобными. Эта информация была собрана в ходе исследования, в ходе которого мы беседовали с людьми, знакомыми с использованием аккумуляторных дрелей, наблюдали за тем, как те, кто не знаком с дрелями, пытались ими управлять, а также из нашего личного опыта. Позже мы обсудим специальные сценарии использования, но в целом мы определили, что самые большие группы пользователей используют небольшие аккумуляторные дрели для личных некоммерческих небольших проектов, включая благоустройство дома, хобби и т. Д.Наши потребности пользователей и требования к продукции отражают эту группу пользователей и то, что при проектировании аккумуляторной дрели необходимо сосредоточить внимание на надежности и удобстве для пользователя. В таблице 1-1 приведены пять основных областей, вызывающих озабоченность в связи с потребностями клиентов и требованиями к продукции. Таблица 1-1: Сводка пяти основных потребностей клиентов и требований к продукции
Функция / назначение:Назначение аккумуляторной дрели — вращать «биты».«Биты» — это инструменты, которые входят в конец сверла, и они бывают самых разных форм, чтобы приспособиться к движению, сверлению, смешиванию или резке. Вещи, которые можно закручивать, включают винты с головкой Philips, плоскую или шестигранную головку. Для сверления сверла бывают разных размеров, от мелких долей дюйма до примерно дюйма в диаметре. Материал сверл также варьируется в зависимости от просверливаемой поверхности. Также есть насадки для перемешивания, например, взбиватели для яиц или венчики.Для резки можно даже вставить небольшие отрезные круги, хотя в основном аккумуляторные дрели предназначены для сверления и забивки. Аккумуляторная дрель должна быть портативной и достаточно маленькой, чтобы ее можно было использовать в труднодоступных местах, что делает ее подходящей для дома или автомобиля. Он не имеет вредных выхлопов, поэтому его можно использовать как в помещении, так и на открытом воздухе, но при этом не допускать попадания воды внутрь корпуса. Помимо просверливания отверстий, он также используется для скрепления материалов винтами или может использоваться для сверления более слабых объектов, таких как оторванные винты или сломанные замки.Он часто используется для установки оборудования или снятия крышек или чего-либо, что действительно закреплено на месте винтами. Его даже можно использовать для откручивания полностью снятых винтов, затянув патрон вокруг головки винта и перевернув сверло. Входы / Выходы:Физическим воздействием на сверло является осевое усилие на спусковой крючок, которое обычно прикладывается указательным пальцем, когда стержень сверла находится в ладони. Когда спусковой крючок (022) нажат, потенциометр (часть контроллера сцепления / переключателя, часть 024) измеряет глубину нажатия спускового крючка и позволяет подавать пропорциональное количество напряжения на двигатель (016).Двигатель вращается на очень высоких скоростях с низким крутящим моментом, потому что мощность = крутящий момент * скорость (при условии отсутствия потерь), а производительность сверла зависит от высокого крутящего момента, а не от высокой скорости, существует планетарная зубчатая передача (028), которая снижает скорость и увеличивает крутящий момент сверла. Планетарный редуктор (028), в свою очередь, раскручивает узел патрона (027). Если сцепление установлено вперед, патрон вращается по часовой стрелке, если сцепление находится посередине, спусковой крючок не сможет нажать, а если сцепление установлено на задний ход, патрон будет вращаться против часовой стрелки. ОперацияДля работы дрели необходимо сначала зарядить аккумулятор дрели (001). Для этого нужно сдвинуть аккумулятор с дрели на зарядное устройство 12 В, которое подключается к стене. Примерно через 2 часа аккумулятор будет полностью заряжен, и его можно будет надеть на основание дрели.После того, как батарея вставлена на место, необходимо открыть зубцы патрона (027), чтобы немного могла проскользнуть внутрь. Чтобы открыть зубцы патрона, удерживайте верхнюю часть сверла неподвижно и поверните хомут (026) на конце сверла. дрель против часовой стрелки. Зубы начнут открываться. Когда они откроются достаточно широко для сверла, которое вы хотите использовать, поместите сверло в патрон и поверните кольцо по часовой стрелке, чтобы затянуть зубья. Когда сверло надежно закреплено, выберите крутящий момент отсечки, который вы хотите использовать, повернув воротник с изображениями сверла до желаемой настройки.Включите сцепление в прямом или обратном направлении в зависимости от области применения и поместите биту на желаемую поверхность. Крепко удерживая его, осторожно нажмите спусковой крючок (022), одновременно продвигая его вперед. Продолжайте сжимать, пока сверло не начнет двигаться с желаемой скоростью. Как только задача будет завершена, верните муфту в центральное положение и установите сверло. Испытания пользователейаккумуляторной дрели Внутри, нажатие на спусковой крючок (022) подает напряжение на двигатель (016) с помощью контроллера сцепления / переключателя (024).Эта частота вращения и крутящий момент передаются на планетарный редуктор (028), который значительно снижает скорость и увеличивает крутящий момент. Затем это вращение передается на узел патрона (027), который надежно удерживает сверло и раскручивает его, позволяя сверлу резать. После отпускания спускового крючка тормозной патрон быстро останавливает сверло, чтобы не создавать угрозы для безопасности. Нам не удалось разобрать патрон в сборе (как вы можете видеть на фотографиях ниже), и мы не совсем уверены, как работает тормоз патрона.Онлайн-исследования показывают, что тормозной патрон может иметь электрическое управление, хотя мы скептически относимся к этому (мы не видели проводов, ведущих к узлу сцепления). Разные пользователи / сценарии использованияНекоторые предсказуемые проблемы с конструкцией дрели возникают из-за непреднамеренного использования и ненормальных пользователей. По большей части сверло предназначено для сверления и забивки. Использование его для других целей просто не соответствует первоначальному замыслу. Пользователи могут использовать дрель для расширения отверстий, гравировки объектов и т. Д.но они выходят за рамки первоначального объема товара. Однако использование во влажных помещениях вызывает опасения. Хотя обычная аккумуляторная дрель, скорее всего, никогда не будет использоваться под водой, мы считаем, что ограниченное использование во влажных помещениях может быть полезной потребностью для потребителей, особенно если аварийные ремонтные работы необходимо проводить в ненастную погоду. Это может быть серьезной проблемой для безопасности из-за риска поражения электрическим током и поскользнуться в воде. Такая модификация должна включать в себя электрическую изоляцию, а также дополнительную рукоятку, чтобы предотвратить падение или скольжение пользователя на сверле и причинение вреда пользователю или проекту пользователя. Даже со вспомогательной рукояткой, которую мы обнаружили, аккумуляторная дрель требует приличной силы руки. Ручка позволяет пользователю лучше контролировать выравнивание во время использования. Однако эта ручка смещена от точки первичного силового контакта (у долота), что может вызвать момент, который пользователь должен компенсировать своей основной рукой (на спусковом крючке). К сожалению, это требует от пользователя «приличной силы рук». Мы обнаружили, что эта вспомогательная ручка позволяет «более слабому» пользователю использовать более тяжелую дрель, потому что вес дрели не поддерживается одной рукой, даже если спусковой крючок должен компенсировать момент, вызванный вспомогательной рукой. Другие проблемы исходят от особых потребителей. Эти проблемы могут возникнуть из-за пользователей со слабым захватом или трясущимися руками. Плохое зрение может затруднить использование, а также плохое освещение или невозможность толкать сверло вперед с разумной мощностью. Установка сверла в патрон может оказаться проблемой даже для нормально способных людей, и снятие шурупов — обычное дело. Глухие люди могут не слышать, когда сверло пропускает винт, и приложение слишком большого крутящего момента также может произойти, если материал слишком мягкий и сверло не настроено на правильную настройку крутящего момента (что довольно сбивает с толку на дрель).Вызывает беспокойство даже наличие неправильных битов, равно как и наличие действительно узких участков, не позволяющих сверлу располагаться перпендикулярно объекту. Прежде чем делать что-либо еще, мы проанализировали нашу дрель, чтобы рассмотреть каждую деталь поближе и понять, как дрель работает с технической точки зрения. Аккумуляторная дрель, предварительное рассечение показано выше. Цифры обозначают легко видимые внешние компоненты. Номера соответствуют номерам деталей в таблице ниже. На изображении выше в разобранном виде показана аналогичная дрель с некоторыми внутренними компонентами. Список деталей Нас очень впечатлила компактность сверла, особенно то, насколько хорошо в сверло помещается большое количество компонентов. Мы считаем, что помимо унификации винтов и конструкции для разборки не было никаких очевидных улучшений, которые бы существенно повлияли на стоимость или производительность сверла. Очевидно, что если бы мы провели более обширное исследование, сосредоточенное исключительно на DFMA буровой установки и ее производственных мощностях, мы могли бы найти больше областей для улучшения.Тем не менее, DFMA — одна из сильных сторон вашей дрели. Мы предлагаем оптимизировать другую область, чтобы улучшить аккумуляторную дрель. Производство: Сборка: Разборка: Возможности для улучшения: Из-за значительных ресурсов, необходимых для создания точного и тщательного FMEA, здесь будут представлены только 5 основных видов отказов. Поскольку наш продукт представляет собой относительно безопасное и легкое оборудование, серьезный риск для пользователя невелик.В целом, отказы нашего продукта, скорее всего, связаны с эргономическими проблемами и / или ухудшением со временем, а не с катастрофическим отказом. В нашем анализе мы рассматриваем винты / сверла и винты как отдельные изделия от сверла. Таким образом, наш FMEA не учитывает такие отказы, как отрыв головки винта, отлом головки винта или поломка сверла. Согласно нашему FMEA, наиболее серьезные проблемы с неисправностями связаны с заклиниванием патрона, разрядкой аккумулятора, отказом тормоза патрона, заеданием корпуса руки пользователя и заеданием спускового крючка сцепления.Проблемы безопасности, связанные с этими отказами, не являются серьезными, хотя они существуют. Например, если патрон заклинивает, пользователь может очень сильно дернуть руками (или зажимом), что может привести к травме руки, если он поскользнется. Отказ тормоза зажима может привести к тому, что пользователь попытается остановить зажимной патрон рукой, что было бы небезопасно. В некоторых случаях неисправность приводит к полной непригодности продукта (заклинивание патрона или разряд батареи). Однако в других случаях отказы вызывают только незначительные неудобства для пользователя, например, когда имеешь дело с неудобным захватом или залипающим спусковым крючком муфты.Сбои, которые приводят к невозможности использования дрели, должны быть устранены в первую очередь, чтобы уменьшить случаи полной неработоспособности. Мы рекомендуем, чтобы все 5 основных видов отказов были дополнительно исследованы и улучшены, если это экономически целесообразно. Очевидно, что безопасность является главным приоритетом, и можно увеличить стоимость дрели, чтобы устранить проблему с безопасностью.
Проведя предварительное исследование, мы смогли выделить пять следующих пунктов, которые кажутся наиболее очевидными в качестве основных проблемных областей с точки зрения аккумуляторной дрели и дизайна для окружающей среды: конструкция для разборки, количество деталей, разнообразие / разнообразие деталей, использование батареи, и модульность / возможность модернизации.Подробности о каждом из них изложены здесь:
Наиболее важной особенностью аккумуляторной дрели является время автономной работы, поскольку время, затрачиваемое пользователем на выполнение задачи, ограничивается сроком службы аккумулятора. Если пользователь находится в середине проекта и батарея разряжена, нет возможности добиться большего прогресса, пока батарея не зарядится. Более того, зарядка аккумулятора занимает значительно больше времени, чем разрядка с помощью аккумуляторной дрели.Таким образом, мы обнаруживаем, что пользователи оставляют свои батареи подключенными к зарядным устройствам намного дольше, чем это необходимо для зарядки, просто чтобы быть уверенным, что батарея всегда заряжается. Это создает серьезную проблему DFE из-за чрезмерного расхода энергии. Наши предложения состоят в том, чтобы найти способ либо продлить время зарядки аккумулятора, либо изменить зарядное устройство, чтобы оно отключалось от источника питания, если аккумулятор полностью заряжен. В дополнение к этим рекомендациям мы обнаружили, что буровая установка была успешной в других аспектах DFE, наиболее важными из которых являются: использование перезаряжаемой батареи, оптимальное использование пластика для обсадной колонны, разнообразная доступность «долот» позволяет легко выполнять многозадачную работу, упаковка (со снятым аккумулятором и зарядным устройством) занимает мало места. 2025 © Все права защищены. |