ΠΠΈΡΠΏΠΈΡ ΠΈΠ· ΠΎΠΏΠΈΠ»ΠΎΠΊ ΠΈ ΡΠ΅ΠΌΠ΅Π½ΡΠ° ΡΠ²ΠΎΠΈΠΌΠΈ ΡΡΠΊΠ°ΠΌΠΈ, ΠΏΡΠΈΠΌΠ΅Ρ ΠΌΠ°Π»ΠΎΠ³ΠΎ Π±ΠΈΠ·Π½Π΅ΡΠ°
ΠΠΈΡΠΏΠΈΡ ΠΈΠ· ΠΎΠΏΠΈΠ»ΠΎΠΊ ΠΈ ΡΠ΅ΠΌΠ΅Π½ΡΠ° ΡΠ²ΠΎΠΈΠΌΠΈ ΡΡΠΊΠ°ΠΌΠΈ, ΠΈΠ΄Π΅ΠΈ ΠΌΠ°Π»ΠΎΠ³ΠΎ Π±ΠΈΠ·Π½Π΅ΡΠ° ΠΈ ΡΡΡΠΎΠΈΡΠ΅Π»ΡΡΡΠ²ΠΎ ΡΠΎΠ±ΡΡΠ²Π΅Π½Π½ΡΡ ΠΎΠ±ΡΠ΅ΠΊΡΠΎΠ².
ΠΡΠ±ΠΎΠ»ΠΈΡ ΠΏΠΎΠ»ΡΡΠΈΠ» ΡΠΈΡΠΎΠΊΠΎΠ΅ ΠΏΡΠΈΠΌΠ΅Π½Π΅Π½ΠΈΠ΅ Π² 60 Π³ΠΎΠ΄Π°Ρ ΠΏΡΠΎΡΠ»ΠΎΠ³ΠΎ Π²Π΅ΠΊΠ°, Π½ΠΎ Π² ΡΠ΅ΡΠ΅Π΄ΠΈΠ½Π΅ 90 Π±ΡΠ» Π½Π΅Π·Π°ΡΠ»ΡΠΆΠ΅Π½Π½ΠΎ Π·Π°Π±ΡΡ. ΠΡΠΈΡΠΈΠ½Π° ΡΠ½ΠΈΠΆΠ΅Π½ΠΈΡ ΠΏΠΎΠΏΡΠ»ΡΡΠ½ΠΎΡΡΠΈ ΠΊΡΠΎΠ΅ΡΡΡ Π² ΡΠΎΠΌ, ΡΡΠΎ ΠΏΠΎΡΠ»Π΅ ΡΠ°Π·Π²Π°Π»Π° ΡΠΎΡΠ·Π° ΠΏΠ΅ΡΠ΅ΡΡΠ°Π»ΠΈ ΡΠΎΠ±Π»ΡΠ΄Π°ΡΡ ΠΠΠ‘Π’Ρ ΠΏΡΠΈ ΠΈΠ·Π³ΠΎΡΠΎΠ²Π»Π΅Π½ΠΈΠΈ ΠΈΠ·Π΄Π΅Π»ΠΈΠΉ ΠΈΠ· ΠΎΠΏΠΈΠ»ΠΎΠΊ ΠΈ ΡΠ΅ΠΌΠ΅Π½ΡΠ°.
ΠΠΈΠ·ΠΊΠΎΠ΅ ΠΊΠ°ΡΠ΅ΡΡΠ²ΠΎ ΠΈ ΠΊΡΡΡΠ°ΡΠ½ΠΎΠ΅ ΠΏΡΠΎΠΈΠ·Π²ΠΎΠ΄ΡΡΠ²ΠΎ ΠΏΡΠΈΠ²Π΅Π»ΠΈ ΠΊ ΡΠΎΠΌΡ, ΡΡΠΎ Π½ΠΎΠ²ΡΠ΅ Π΄ΠΎΠΌΠ° ΠΈΠ· Π°ΡΠ±ΠΎΠ»ΠΈΡΠ° ΡΠ΅ΡΠ΅Π· Π½Π΅ΠΊΠΎΡΠΎΡΠΎΠ΅ Π²ΡΠ΅ΠΌΡ ΡΡΠ΅ΡΠΊΠ°Π»ΠΈΡΡ, ΡΡΠΏΠ°Π»ΠΈΡΡ ΠΈΠ»ΠΈ ΠΏΠΎΡΠ°ΠΆΠ°Π»ΠΈΡΡ Π³ΡΠΈΠ±ΠΊΠΎΠΌ.
ΠΠ΄Π½Π°ΠΊΠΎ, Π² Π½Π°ΡΠΈ Π΄Π½ΠΈ ΡΠ΅Ρ Π½ΠΎΠ»ΠΎΠ³ΠΈΡ ΠΏΡΠΎΠΈΠ·Π²ΠΎΠ΄ΡΡΠ²Π° ΠΊΠΈΡΠΏΠΈΡΠ΅ΠΉ ΠΈΠ· ΠΎΠΏΠΈΠ»ΠΎΠΊ ΠΈ ΡΠ΅ΠΌΠ΅Π½ΡΠ° ΠΎΠΏΡΡΡ Π½Π°Π±ΠΈΡΠ°Π΅Ρ ΠΏΠΎΠΏΡΠ»ΡΡΠ½ΠΎΡΡΡ. Π Π²ΡΡ ΠΏΠΎΡΠΎΠΌΡ, ΡΡΠΎ ΠΏΡΠΎΠΈΠ·Π²ΠΎΠ΄ΠΈΡΠ΅Π»ΠΈ Π² Π±ΠΎΡΡΠ±Π΅ Π·Π° ΠΊΠ»ΠΈΠ΅Π½ΡΠΎΠ², ΡΡΠ°Π»ΠΈ ΡΠ΄Π΅Π»ΡΡΡ Π±ΠΎΠ»ΡΡΠΎΠ΅ Π²Π½ΠΈΠΌΠ°Π½ΠΈΠ΅ ΠΊΠ°ΡΠ΅ΡΡΠ²Ρ.
Β
ΠΡΠΎΡΡΠΎ ΡΡΠ°Π»ΠΎ Π½Π΅ Π²ΡΠ³ΠΎΠ΄Π½ΠΎ Π²ΡΠΏΡΡΠΊΠ°ΡΡ ΠΈΠ·Π΄Π΅Π»ΠΈΡ, Π½Π΅ ΡΠΎΠΎΡΠ²Π΅ΡΡΡΠ²ΡΡΡΠΈΠ΅ ΡΡΠ°Π½Π΄Π°ΡΡΠ°ΠΌ, ΡΡΡΠ°Π½ΠΎΠ²Π»Π΅Π½Π½ΡΠΌ Π΅ΡΡ Π² ΡΠΎΠ²Π΅ΡΡΠΊΠΎΠ΅ Π²ΡΠ΅ΠΌΡ.
ΠΡΠ»ΠΈ ΡΠΎΠ±Π»ΡΠ΄Π°ΡΡ Π²ΡΠ΅ ΠΏΡΠ°Π²ΠΈΠ»Π° ΠΈΠ·Π³ΠΎΡΠΎΠ²Π»Π΅Π½ΠΈΡ, ΡΠΎ ΠΌΠΎΠΆΠ½ΠΎ ΠΏΠΎΠ»ΡΡΠΈΡΡ Π½Π΅Π΄ΠΎΡΠΎΠ³ΠΎΠΉ, ΠΏΡΠΎΡΠ½ΡΠΉ, Π΄ΠΎΠ»Π³ΠΎΠ²Π΅ΡΠ½ΡΠΉ, ΡΠ΅ΠΏΠ»ΠΎΠΈΠ·ΠΎΠ»ΡΡΠΈΠΎΠ½Π½ΡΠΉ, ΡΡΡΠΎΠΈΡΠ΅Π»ΡΠ½ΡΠΉ ΠΌΠ°ΡΠ΅ΡΠΈΠ°Π», ΠΈΠΌΠ΅Π½ΡΠ΅ΠΌΡΠΉ Π°ΡΠ±ΠΎΠ»ΠΈΡΠΎΠΌ.
ΠΠΈΡΠΏΠΈΡ ΠΈΠ· ΠΎΠΏΠΈΠ»ΠΎΠΊ ΠΈ ΡΠ΅ΠΌΠ΅Π½ΡΠ°, ΡΠ΅Ρ Π½ΠΎΠ»ΠΎΠ³ΠΈΡ
Π’Π΅Ρ Π½ΠΎΠ»ΠΎΠ³ΠΈΡ ΠΈΠ·Π³ΠΎΡΠΎΠ²Π»Π΅Π½ΠΈΡ Π°ΡΠ±ΠΎΠ»ΠΈΡΠΎΠ²ΡΡ ΠΊΠΈΡΠΏΠΈΡΠ΅ΠΉ ΠΏΡΠ΅Π΄ΡΡΠΌΠ°ΡΡΠΈΠ²Π°Π΅Ρ ΠΈΡΠΏΠΎΠ»ΡΠ·ΠΎΠ²Π°Π½ΠΈΠ΅ Π΄ΡΠ΅Π²Π΅ΡΠ½ΡΡ ΠΎΠΏΠΈΠ»ΠΎΠΊ, ΠΈΠ»ΠΈ ΡΠ΅ΠΏΡ. Π‘ΡΡ Π°Ρ Π΄ΡΠ΅Π²Π΅ΡΠ½Π°Ρ ΡΡΡΡΠΆΠΊΠ° ΠΎΠ±ΡΠ°Π±Π°ΡΡΠ²Π°Π΅ΡΡΡ ΡΠΏΠ΅ΡΠΈΠ°Π»ΡΠ½ΡΠΌ ΡΠ°ΡΡΠ²ΠΎΡΠΎΠΌ ΠΈ Π·Π°Π»ΠΈΠ²Π°Π΅ΡΡΡ ΡΠ΅ΠΌΠ΅Π½ΡΠ½ΠΎΠΉ ΡΠΌΠ΅ΡΡΡ.
ΠΠΎΠ»Ρ Π΄ΡΠ΅Π²Π΅ΡΠΈΠ½Ρ Π² Π³ΠΎΡΠΎΠ²ΠΎΠΌ ΠΊΠΈΡΠΏΠΈΡΠ΅, ΡΠΎΡΡΠ°Π²Π»ΡΠ΅Ρ ΠΏΡΠΈΠΌΠ΅ΡΠ½ΠΎ 80%, Π° ΡΠ΅ΠΌΠ΅Π½ΡΠ° β 20%. Π ΡΠ°ΠΊ ΠΊΠ°ΠΊ ΠΎΠ±Π° ΠΊΠΎΠΌΠΏΠΎΠ½Π΅Π½ΡΠ° ΡΡΠΎΡΡ Π½Π΅Π΄ΠΎΡΠΎΠ³ΠΎ, ΡΠΎ ΠΏΡΠΎΠΈΡΡ ΠΎΠ΄ΠΈΡ Π±ΡΡΡΡΠ°Ρ ΠΎΠΊΡΠΏΠ°Π΅ΠΌΠΎΡΡΡ Π²Π»ΠΎΠΆΠ΅Π½ΠΈΠΉ ΠΏΡΠΈ ΠΎΡΠΊΡΡΡΠΈΠΈ ΡΠ²ΠΎΠ΅Π³ΠΎ Π±ΠΈΠ·Π½Π΅ΡΠ°.
Π‘ΡΡΠ΅ΡΡΠ²ΡΡΡ ΡΡΠΈ ΠΎΡΠ½ΠΎΠ²Π½ΡΡ Π²ΠΈΠ΄Π° ΠΈΠ·Π΄Π΅Π»ΠΈΠΉ ΠΈΠ· Π°ΡΠ±ΠΎΠ»ΠΈΡΠ°:
- Π’Π΅ΠΏΠ»ΠΎΠΈΠ·ΠΎΠ»ΡΡΠΈΠΎΠ½Π½ΡΠΉ Π΄Π»Ρ ΡΡΠ΅ΠΏΠ»Π΅Π½ΠΈΡ ΡΡΡΠΎΠ΅Π½ΠΈΠΉ;
- ΠΠΎΠ½ΡΡΡΡΠΊΡΠΈΠ²Π½ΠΎ-ΡΠ΅ΠΏΠ»ΠΎΠΈΠ·ΠΎΠ»ΡΡΠΈΠΎΠ½Π½ΡΠΉ — Π΄Π»Ρ Π²ΠΎΠ·Π²Π΅Π΄Π΅Π½ΠΈΡ ΡΡΠ΅Π½;
- ΠΡΠ±ΠΎΠΌΠΎΠ½ΠΎΠ»ΠΈΡ β ΡΡΠΎ ΠΊΠΎΠ³Π΄Π° Π³ΠΎΡΠΎΠ²Π°Ρ, Π°ΡΠ±ΠΎΠ»ΠΈΡΠΎΠ²Π°Ρ ΡΠΌΠ΅ΡΡ Π·Π°Π»ΠΈΠ²Π°Π΅ΡΡΡ Π½Π΅ΠΏΠΎΡΡΠ΅Π΄ΡΡΠ²Π΅Π½Π½ΠΎ Π² ΠΎΠΏΠ°Π»ΡΠ±ΠΊΡ, ΠΌΠΈΠ½ΡΡ ΡΡΠ°Π΄ΠΈΡ ΠΈΠ·Π³ΠΎΡΠΎΠ²Π»Π΅Π½ΠΈΡ ΠΊΠΈΡΠΏΠΈΡΠ°. ΠΡΠΈ ΡΡΠΎΠΌ, Π²ΡΡ ΠΊΠΎΠ½ΡΡΡΡΠΊΡΠΈΡ ΠΆΠΈΠ»ΠΎΠ³ΠΎ ΡΡΡΠΎΠ΅Π½ΠΈΡ ΠΏΡΠ΅Π΄ΡΡΠ°Π²Π»ΡΠ΅Ρ ΡΠΎΠ±ΠΎΠΉ Π΅Π΄ΠΈΠ½ΡΡ, ΠΌΠΎΠ½ΠΎΠ»ΠΈΡΠ½ΡΡ ΡΡΡΡΠΊΡΡΡΡ.
ΠΠΈΡΠΏΠΈΡΠΈ ΠΈΠ· ΠΎΠΏΠΈΠ»ΠΎΠΊ ΠΈ ΡΠ΅ΠΌΠ΅Π½ΡΠ° ΠΎΡΠ»ΠΈΡΠ½ΠΎ ΡΠ΄Π΅ΡΠΆΠΈΠ²Π°ΡΡ ΡΠ΅ΠΏΠ»ΠΎ, ΠΎΠ±Π»Π°Π΄Π°ΡΡ Π²ΡΡΠΎΠΊΠΎΠΉ Π·Π²ΡΠΊΠΎΠΈΠ·ΠΎΠ»ΡΡΠΈΠ΅ΠΉ. ΠΠ½ΠΈ ΠΏΠΎΠΆΠ°ΡΠΎΠ±Π΅Π·ΠΎΠΏΠ°ΡΠ½ΡΠ΅. ΠΠΎ ΡΠ°ΠΌΠΎΠ΅ Π²Π°ΠΆΠ½ΠΎΠ΅ ΠΏΡΠ΅ΠΈΠΌΡΡΠ΅ΡΡΠ²ΠΎ, ΠΏΠ΅ΡΠ΅Π΄ Π΄ΡΡΠ³ΠΈΠΌΠΈ ΡΡΡΠΎΠΈΡΠ΅Π»ΡΠ½ΡΠΌΠΈ ΠΌΠ°ΡΠ΅ΡΠΈΠ°Π»Π°ΠΌΠΈ β ΡΠΊΠΎΠ»ΠΎΠ³ΠΈΡΠ΅ΡΠΊΠ°Ρ ΡΠΈΡΡΠΎΡΠ° ΠΈ Π½Π΅Π²ΡΡΠΎΠΊΠ°Ρ ΡΡΠΎΠΈΠΌΠΎΡΡΡ.
ΠΠ½ΠΎΠ³ΠΈΡ ΠΏΡΠΈΠ²Π»Π΅ΠΊΠ°Π΅Ρ ΠΏΡΠΎΡΡΠΎΡΠ° ΠΈΠ·Π³ΠΎΡΠΎΠ²Π»Π΅Π½ΠΈΡ, ΠΈ ΠΎΠ½ΠΈ Π½Π°Π»Π°ΠΆΠΈΠ²Π°ΡΡ ΠΏΡΠΎΠΈΠ·Π²ΠΎΠ΄ΡΡΠ²ΠΎ ΠΊΠΈΡΠΏΠΈΡΠ΅ΠΉ ΠΈΠ· ΠΎΠΏΠΈΠ»ΠΎΠΊ ΠΈ ΡΠ΅ΠΌΠ΅Π½ΡΠ° ΡΠ²ΠΎΠΈΠΌΠΈ ΡΡΠΊΠ°ΠΌΠΈ.
Π‘ΡΠΎΠΈΡ Π·Π°ΠΌΠ΅ΡΠΈΡΡ, ΡΡΠΎ ΡΠ°ΠΊΠΎΠ΅ ΠΏΡΠΎΠΈΠ·Π²ΠΎΠ΄ΡΡΠ²ΠΎ Π²ΠΎΠ·ΠΌΠΎΠΆΠ½ΠΎ ΠΎΡΡΡΠ΅ΡΡΠ²ΠΈΡΡ Π² Π΄ΠΎΠΌΠ°ΡΠ½ΠΈΡ ΡΡΠ»ΠΎΠ²ΠΈΡΡ . ΠΠ΄Π½Π°ΠΊΠΎ ΡΠ»Π΅Π΄ΡΠ΅Ρ ΡΠΎΠ±Π»ΡΠ΄Π°ΡΡ Π½Π΅ΠΊΠΎΡΠΎΡΡΠ΅ ΠΏΡΠ°Π²ΠΈΠ»Π°, ΠΎ ΠΊΠΎΡΠΎΡΡΡ ΠΌΡ ΡΠ°ΡΡΠΊΠ°ΠΆΠ΅ΠΌ Π΄Π°Π»Π΅Π΅, ΡΡΠΎΠ±Ρ Π²Π°ΡΠΈ ΠΈΠ·Π΄Π΅Π»ΠΈΡ ΡΠ»ΡΠΆΠΈΠ»ΠΈ ΠΊΠ°ΠΊ ΠΌΠΎΠΆΠ½ΠΎ Π΄ΠΎΠ»ΡΡΠ΅.
ΠΠΈΡΠΏΠΈΡΠΈ ΠΈΠ· ΠΎΠΏΠΈΠ»ΠΎΠΊ ΠΈ ΡΠ΅ΠΌΠ΅Π½ΡΠ°, Π² Π·Π°Π²ΠΈΡΠΈΠΌΠΎΡΡΠΈ ΠΎΡ ΠΏΡΠ΅Π΄Π½Π°Π·Π½Π°ΡΠ΅Π½ΠΈΡ, ΠΈΠΌΠ΅ΡΡ ΡΠ°Π·Π»ΠΈΡΠ°ΡΡΡΡΡΡ ΠΌΠ°ΡΠΊΠΈΡΠΎΠ²ΠΊΡ.
ΠΡΡΡ ΠΌΠ°ΡΠΎΠΊ ΠΈΠ·Π΄Π΅Π»ΠΈΠΉ:
- M5;
- M10;
- M15;
- M25;
- M35.
Π Π΄Π²ΡΡ ΠΏΠΎΡΠ»Π΅Π΄Π½ΠΈΡ ΠΌΠ°ΡΠΊΠ°Ρ , Π½ΠΎΠΌΠ΅Ρ 4 ΠΈ 5, ΠΏΡΠΎΡΠ΅Π½ΡΠ½ΠΎΠ΅ ΡΠΎΠ΄Π΅ΡΠΆΠ°Π½ΠΈΠ΅ ΠΎΠΏΠΈΠ»ΠΎΠΊ ΠΌΠΈΠ½ΠΈΠΌΠ°Π»ΡΠ½ΠΎΠ΅, ΠΏΠΎ ΡΡΠ°Π²Π½Π΅Π½ΠΈΡ Ρ ΠΏΠ΅ΡΠ²ΡΠΌΠΈ Π½ΠΎΠΌΠ΅ΡΠ°ΠΌΠΈ.
ΠΠΎΡΡΠΎΠΌΡ, ΠΊΠΈΡΠΏΠΈΡΠΈ Π΄Π°Π½Π½ΡΡ ΠΌΠ°ΡΠΎΠΊ Π½Π°ΠΌΠ½ΠΎΠ³ΠΎ ΠΏΡΠΎΡΠ½Π΅Π΅ ΠΈ Π²ΡΠ΄Π΅ΡΠΆΠΈΠ²Π°ΡΡ ΠΏΠΎΠ²ΡΡΠ΅Π½Π½ΡΡ Π½Π°Π³ΡΡΠ·ΠΊΡ. Π’Π°ΠΊΠΈΠ΅ ΠΈΠ·Π΄Π΅Π»ΠΈΡ ΠΏΡΠΈΠΌΠ΅Π½ΡΡΡ ΠΏΡΠΈ ΡΡΡΠΎΠΈΡΠ΅Π»ΡΡΡΠ²Π΅ Π½Π΅ΡΡΡΠΈΡ ΡΡΠ΅Π½ Π΄Π²ΡΡ ΡΡΠ°ΠΆΠ½ΡΡ Π·Π΄Π°Π½ΠΈΠΉ.
ΠΠΈΡΠΏΠΈΡ ΠΈΠ· ΠΎΠΏΠΈΠ»ΠΎΠΊ ΠΈ ΡΠ΅ΠΌΠ΅Π½ΡΠ° ΡΠ²ΠΎΠΈΠΌΠΈ ΡΡΠΊΠ°ΠΌΠΈ
ΠΡΠ»ΠΈ Π²Ρ ΡΠ΅ΡΠΈΠ»ΠΈ ΠΈΠ·Π³ΠΎΡΠΎΠ²Π»ΡΡΡ ΠΊΠΈΡΠΏΠΈΡΠΈ ΠΈΠ· ΠΎΠΏΠΈΠ»ΠΎΠΊ ΠΈ ΡΠ΅ΠΌΠ΅Π½ΡΠ° ΡΠ²ΠΎΠΈΠΌΠΈ ΡΡΠΊΠ°ΠΌΠΈ, ΡΠΎ, Π΄Π»Ρ Π½Π°ΡΠ°Π»Π° ΡΠ»Π΅Π΄ΡΠ΅Ρ ΡΠ·Π½Π°ΡΡ Π½Π΅ΡΠΊΠΎΠ»ΡΠΊΠΎ Π²Π°ΠΆΠ½ΡΡ ΠΏΡΠ°Π²ΠΈΠ» ΠΎΡ ΠΏΡΠΎΡΠ΅ΡΡΠΈΠΎΠ½Π°Π»ΠΎΠ². ΠΡΠΈ ΠΏΡΠ°Π²ΠΈΠ»Π° ΠΏΠΎΠΌΠΎΠ³ΡΡ Π²Π°ΠΌ ΠΏΠΎΠ»ΡΡΠΈΡΡ ΠΊΠ°ΡΠ΅ΡΡΠ²Π΅Π½Π½ΡΠ΅ ΠΈΠ·Π΄Π΅Π»ΠΈΡ, Ρ Π½Π΅Π²ΡΡΠΎΠΊΠΎΠΉ ΡΠ΅Π±Π΅ΡΡΠΎΠΈΠΌΠΎΡΡΡΡ.
ΠΡΠ°Π²ΠΈΠ»Π° ΠΈΠ·Π³ΠΎΡΠΎΠ²Π»Π΅Π½ΠΈΡ Π°ΡΠ±ΠΎΠ»ΠΈΡΠΎΠ²ΡΡ Π±Π»ΠΎΠΊΠΎΠ²:
- ΠΠ΅Π»Π°ΡΠ΅Π»ΡΠ½ΠΎ ΠΏΡΠΈΠΎΠ±ΡΠ΅ΡΠ°ΡΡ ΡΠ΅ΠΌΠ΅Π½Ρ ΡΠΎΠ»ΡΠΊΠΎ ΠΌΠ°ΡΠΊΠΈ ΠΌ500;
- ΠΠ»Ρ ΡΡΡΠΎΠΈΡΠ΅Π»ΡΡΡΠ²Π° ΠΆΠΈΠ»ΡΡ ΠΏΠΎΠΌΠ΅ΡΠ΅Π½ΠΈΠΉ Π»ΡΡΡΠ΅ Π²ΡΠ΅Π³ΠΎ ΠΈΡΠΏΠΎΠ»ΡΠ·ΠΎΠ²Π°ΡΡ Ρ Π²ΠΎΠΉΠ½ΡΠ΅ ΠΎΠΏΠΈΠ»ΠΊΠΈ ΠΈΠ»ΠΈ ΡΡΡΡΠΆΠΊΡ, ΡΠ°ΠΌΠΎΠ΅ Π»ΡΡΡΠ΅Π΅ — ΡΠΎΡΠ½Π°;
- ΠΡΠ³Π°Π½ΠΈΡΠ΅ΡΠΊΠΈΠΉ Π½Π°ΠΏΠΎΠ»Π½ΠΈΡΠ΅Π»Ρ, ΡΠΎ Π΅ΡΡΡ ΠΎΠΏΠΈΠ»ΠΊΠΈ, ΡΡΡΡΠΆΠΊΠ° ΠΈ ΡΠ°ΠΊ Π΄Π°Π»Π΅Π΅, Π΄ΠΎΠ»ΠΆΠ΅Π½ Π±ΡΡΡ Π°Π±ΡΠΎΠ»ΡΡΠ½ΠΎ ΡΡΡ ΠΈΠΌ. ΠΠ΅Π»ΡΠ·Ρ ΠΏΡΠΈΠΌΠ΅Π½ΡΡΡ ΠΎΠΏΠΈΠ»ΠΊΠΈ Π²Π»Π°ΠΆΠ½ΡΠ΅, ΠΏΠΎΠ΄ΠΎΠΏΡΠ΅Π²ΡΠΈΠ΅, Ρ ΡΠ°Π½ΠΈΠ²ΡΠΈΠ΅ΡΡ Π½Π΅Π½Π°Π΄Π»Π΅ΠΆΠ°ΡΠΈΠΌ ΠΎΠ±ΡΠ°Π·ΠΎΠΌ. ΠΡΠΎ ΠΌΠΎΠΆΠ΅Ρ ΠΏΡΠΈΠ²Π΅ΡΡΠΈ ΠΊ ΠΏΠΎΡΠ²Π»Π΅Π½ΠΈΡ ΠΏΠ»Π΅ΡΠ΅Π½ΠΈ, Π³ΡΠΈΠ±ΠΊΠ° Π½Π° Π³ΠΎΡΠΎΠ²ΡΡ ΠΈΠ·Π΄Π΅Π»ΠΈΡΡ . Π Π² ΡΠ΅Π·ΡΠ»ΡΡΠ°ΡΠ΅ Π±ΡΠΎΠΆΠ΅Π½ΠΈΡ ΡΠ΅Π»Π»ΡΠ»ΠΎΠ·Ρ ΠΌΠΎΠ³ΡΡ Π½Π°Π±Π»ΡΠ΄Π°ΡΡΡΡ Π²Π·Π΄ΡΡΠΈΠ΅ ΠΈ ΡΠ°Π·ΡΡΠ² Π±Π»ΠΎΠΊΠΎΠ².
- ΠΠ»Ρ ΡΡΡΡΠ°Π½Π΅Π½ΠΈΡ Π½Π΅Π³Π°ΡΠΈΠ²Π½ΡΡ ΡΠ²Π»Π΅Π½ΠΈΠΉ, ΠΎΠΏΠΈΡΠ°Π½Π½ΡΡ Π² ΠΏΡΠ½ΠΊΡΠ΅ 3, ΡΠ»Π΅Π΄ΡΠ΅Ρ ΠΏΡΠΈΠΌΠ΅Π½ΡΡΡ Ρ ΠΈΠΌΠΈΡΠ΅ΡΠΊΠΈΠΉ Π½Π΅ΠΉΡΡΠ°Π»ΠΈΠ·Π°ΡΠΎΡ. Π’Π°ΠΊΠΎΠΉ ΠΊΠ°ΠΊ ΡΡΠ»ΡΡΠ°Ρ Π°Π»ΡΠΌΠΈΠ½ΠΈΡ ΠΈΠ»ΠΈ Ρ Π»ΠΎΡΠΈΠ΄ ΠΊΠ°Π»ΡΡΠΈΡ. ΠΡΠΎ Π½Π΅Π΄ΠΎΡΠΎΠ³ΠΈΠ΅, Π΄ΠΎΡΡΠ°ΡΠΎΡΠ½ΠΎ ΡΡΡΠ΅ΠΊΡΠΈΠ²Π½ΡΠ΅ ΠΈΠ½Π³ΠΈΠ±ΠΈΡΠΎΡΡ. Π’Π°ΠΊΠΆΠ΅, Π² ΡΠΎΠΎΡΠ²Π΅ΡΡΡΠ²ΠΈΠΈ Ρ ΠΠΠ‘Π’ΠΎΠΌ, ΡΠ°Π·ΡΠ΅ΡΠ°Π΅ΡΡΡ Π΄ΠΎΠ±Π°Π²Π»Π΅Π½ΠΈΠ΅ ΠΆΠΈΠ΄ΠΊΠΎΠ³ΠΎ ΡΡΠ΅ΠΊΠ»Π°, ΡΠ΅ΡΠ½ΠΎΠΊΠΈΡΠ»ΠΎΠ³ΠΎ Π³Π»ΠΈΠ½ΠΎΠ·ΡΠΌΠ°, ΠΈΠ·Π²Π΅ΡΡΠΈ, ΡΠΈΠ»ΠΈΠΊΠ°Ρ-Π³Π»ΡΠ±Ρ.
- ΠΠ»Ρ ΡΠΎΠ³ΠΎ, ΡΡΠΎΠ±Ρ Π³ΠΎΡΠΎΠ²ΠΎΠ΅ ΠΈΠ·Π΄Π΅Π»ΠΈΠ΅ Π±ΡΠ»ΠΎ Π±ΠΎΠ»Π΅Π΅ ΡΠ΅Π»ΠΎΡΡΠ½ΡΠΌ ΠΈ ΠΊΡΠ΅ΠΏΠΊΠΈΠΌ, ΡΠ΅ΠΊΠΎΠΌΠ΅Π½Π΄ΡΠ΅ΡΡΡ ΠΏΡΠΈΠΌΠ΅Π½ΡΡΡ ΠΌΠ΅Π»ΠΊΡΡ ΡΡΡΡΠΆΠΊΡ ΠΈΠ»ΠΈ ΠΎΠΏΠΈΠ»ΠΊΠΈ. ΠΡΠ»ΠΈ Ρ Π²Π°Ρ Π΄ΠΎΡΡΠ°ΡΠΎΡΠ½ΠΎ ΠΊΡΡΠΏΠ½Π°Ρ ΡΠ΅ΠΏΠ°, ΡΠΎ Π΅Ρ ΡΠ»Π΅Π΄ΡΠ΅Ρ ΠΏΡΠ΅Π΄Π²Π°ΡΠΈΡΠ΅Π»ΡΠ½ΠΎ ΡΠ°Π·Π΄ΡΠΎΠ±ΠΈΡΡ Π½Π° Π±ΠΎΠ»Π΅Π΅ ΠΌΠ΅Π»ΠΊΠΈΠ΅ ΡΡΠ°Π³ΠΌΠ΅Π½ΡΡ.
ΠΠ°ΠΊ Π²ΠΈΠ΄ΠΈΠΌ, ΠΏΡΠ°Π²ΠΈΠ»Π° Π΄ΠΎΡΡΠ°ΡΠΎΡΠ½ΠΎ ΠΏΡΠΎΡΡΡΠ΅, Π½Π΅ Π·Π°ΡΡΠ°ΡΠ½ΡΠ΅ ΠΈ Π»Π΅Π³ΠΊΠΎ Π²ΡΠΏΠΎΠ»Π½ΠΈΠΌΡΠ΅.
ΠΠ·Π³ΠΎΡΠΎΠ²Π»Π΅Π½ΠΈΠ΅ ΠΊΠΈΡΠΏΠΈΡΠ΅ΠΉ ΠΈΠ· ΠΎΠΏΠΈΠ»ΠΎΠΊ Π² ΠΏΡΠΎΠΌΡΡΠ»Π΅Π½Π½ΡΡ ΠΌΠ°ΡΡΡΠ°Π±Π°Ρ
Π ΡΠΎΠΌ ΡΠ»ΡΡΠ°Π΅, ΠΊΠΎΠ³Π΄Π° Π²Ρ Ρ ΠΎΡΠΈΡΠ΅ ΠΏΠΎΡΡΠ°Π²ΠΈΡΡ ΠΏΡΠΎΠΈΠ·Π²ΠΎΠ΄ΡΡΠ²ΠΎ ΠΊΠΈΡΠΏΠΈΡΠ° ΠΈΠ· ΠΎΠΏΠΈΠ»ΠΎΠΊ ΠΈ ΡΠ΅ΠΌΠ΅Π½ΡΠ° Π½Π° ΠΏΠΎΡΠΎΠΊ, ΠΎΡΠΊΡΡΡΡ ΡΠ²ΠΎΠΉ Π±ΠΈΠ·Π½Π΅Ρ, ΡΠΎ ΠΏΡΠ΅ΠΆΠ΄Π΅ Π²ΡΠ΅Π³ΠΎ ΡΠ»Π΅Π΄ΡΠ΅Ρ ΡΠΎΡΡΠ°Π²ΠΈΡΡ Π±ΠΈΠ·Π½Π΅Ρ-ΠΏΠ»Π°Π½.
Π ΠΏΠ΅ΡΠ²ΡΡ ΠΎΡΠ΅ΡΠ΅Π΄Ρ ΡΠ°ΡΡΡΠΈΡΠ°ΠΉΡΠ΅ Π·Π°ΡΡΠ°ΡΡ Π½Π° Π·Π°ΠΊΡΠΏΠΊΡ ΠΎΠ±ΠΎΡΡΠ΄ΠΎΠ²Π°Π½ΠΈΡ.
ΠΠ»Ρ ΡΡΠΎΠ³ΠΎ Π²Π°ΠΌ ΠΏΠΎΠ½Π°Π΄ΠΎΠ±ΡΡΡΡ:
- ΠΠ΅ΡΠΎΠ½ΠΎΠΌΠ΅ΡΠ°Π»ΠΊΠ°;
- ΠΡΠΎΠ±ΠΈΠ»ΠΊΠ° Π΄Π»Ρ ΠΈΠ·ΠΌΠ΅Π»ΡΡΠ΅Π½ΠΈΡ ΠΎΠΏΠΈΠ»ΠΎΠΊ ΠΈ Π΄ΡΠ΅Π²Π΅ΡΠ½ΠΎΠΉ ΡΡΡΡΠΆΠΊΠΈ;
- ΠΠ΅ΡΡ Π΄Π»Ρ Π²Π·Π²Π΅ΡΠΈΠ²Π°Π½ΠΈΡ ΠΊΠΎΠΌΠΏΠΎΠ½Π΅Π½ΡΠΎΠ²;
- Π€ΠΎΡΠΌΠΎΠ²ΠΎΡΠ½ΡΠ΅ Π΄ΠΎΠ·Π°ΡΠΎΡΡ;
- ΠΠΈΠ±ΡΠΎΡΡΠΎΠ»;
- Π‘ΡΡΠΈΠ»ΡΠ½Π°Ρ ΠΊΠ°ΠΌΠ΅ΡΠ°;
- Π‘ΠΊΠ»Π°Π΄Ρ Π΄Π»Ρ Ρ ΡΠ°Π½Π΅Π½ΠΈΡ ΡΡΡΡΡ ΠΈ Π³ΠΎΡΠΎΠ²ΡΡ ΠΈΠ·Π΄Π΅Π»ΠΈΠΉ;
- Π‘ΠΏΠ΅ΡΠΈΠ°Π»ΡΠ½ΠΎ ΠΎΠ±ΠΎΡΡΠ΄ΠΎΠ²Π°Π½Π½Π°Ρ, ΠΊΡΡΡΠ°Ρ ΠΏΠ»ΠΎΡΠ°Π΄ΠΊΠ° ΠΈΠ»ΠΈ ΡΠ΅Ρ Π΄Π»Ρ ΠΏΡΠΎΠΈΠ·Π²ΠΎΠ΄ΡΡΠ²Π° ΠΊΠΈΡΠΏΠΈΡΠ΅ΠΉ ΠΈΠ»ΠΈ ΡΡΠ΅ΠΏΠ»ΠΈΡΠ΅Π»ΡΠ½ΡΡ Π±Π»ΠΎΠΊΠΎΠ².
ΠΡΠ»ΠΈ Π²Ρ Π½Π΅ Ρ ΠΎΡΠΈΡΠ΅, ΡΡΠΎΠ±Ρ ΠΏΡΠΎΠΈΠ·Π²ΠΎΠ΄ΡΡΠ²ΠΎ Π·Π°Π²ΠΈΡΠ΅Π»ΠΎ ΠΎΡ ΠΏΠΎΠ³ΠΎΠ΄Π½ΡΡ ΡΡΠ»ΠΎΠ²ΠΈΠΉ, ΡΠΎ Π»ΡΡΡΠ΅ Π²ΡΠ΅Π³ΠΎ ΠΏΠΎΠ΄ΡΠΌΠ°ΡΡ ΠΎ Π±ΠΎΠ»ΡΡΠΎΠΌ, ΠΏΡΠΎΡΡΠΎΡΠ½ΠΎΠΌ, ΠΎΡΠ°ΠΏΠ»ΠΈΠ²Π°Π΅ΠΌΠΎΠΌ ΠΏΠΎΠΌΠ΅ΡΠ΅Π½ΠΈΠΈ. Π ΠΊΠΎΡΠΎΡΠΎΠΌ ΠΌΠΎΠΆΠ½ΠΎ Π±ΡΠ΄Π΅Ρ ΡΠ°Π±ΠΎΡΠ°ΡΡ ΠΊΡΡΠ³Π»ΡΠΉ Π³ΠΎΠ΄.
ΠΡΠΎΡΠΎΠΉ, Π½Π΅ ΠΌΠ΅Π½Π΅Π΅ Π²Π°ΠΆΠ½ΡΠΉ Π°ΡΠΏΠ΅ΠΊΡ β Π·Π°ΡΠ°Π½Π΅Π΅ ΠΏΡΠΎΠ΄ΡΠΌΠ°ΡΡ ΠΊΡΠ΄Π° Π²Ρ ΡΡΠ°Π½Π΅ΡΠ΅ ΡΠ±ΡΠ²Π°ΡΡ Π³ΠΎΡΠΎΠ²ΡΡ ΠΏΡΠΎΠ΄ΡΠΊΡΠΈΡ.
Π Π΅ΠΊΠΎΠΌΠ΅Π½Π΄ΡΠ΅ΡΡΡ Π΅ΡΡ Π΄ΠΎ Π½Π°ΡΠ°Π»Π° ΠΏΡΠΎΠΈΠ·Π²ΠΎΠ΄ΡΡΠ²Π° ΡΠ»Π΅Π΄ΡΠ΅Ρ Π½Π°ΠΉΡΠΈ ΠΏΠ΅ΡΠ΅ΠΊΡΠΏΡΠΈΠΊΠΎΠ², ΠΊΠΎΡΠΎΡΡΠ΅ Π±ΡΠ΄ΡΡ ΡΠ±ΡΠ²Π°ΡΡ Π²Π°ΡΡ ΠΏΡΠΎΠ΄ΡΠΊΡΠΈΡ Π½Π°ΡΠ΅Π»Π΅Π½ΠΈΡ.
Π’Π°ΠΊΠΆΠ΅, ΠΌΠΎΠΆΠ½ΠΎ ΠΏΡΠ΅Π΄Π»ΠΎΠΆΠΈΡΡ ΡΠ²ΠΎΠΈ ΠΈΠ·Π΄Π΅Π»ΠΈΡ ΡΡΡΠΎΠΈΡΠ΅Π»ΡΠ½ΡΠΌ ΡΠΈΡΠΌΠ°ΠΌ, ΠΎΡΠ³Π°Π½ΠΈΠ·Π°ΡΠΈΡΠΌ ΠΈ ΡΠ°ΠΊ Π΄Π°Π»Π΅Π΅.
Π£Π·Π½Π°Π² ΡΡΠ½ΠΎΡΠ½ΡΠ΅ Π·Π°ΠΊΡΠΏΠΎΡΠ½ΡΠ΅ ΡΠ΅Π½Ρ, ΠΈ ΠΏΡΠΈΠ±Π»ΠΈΠ·ΠΈΡΠ΅Π»ΡΠ½ΠΎ ΠΎΠΏΡΠ΅Π΄Π΅Π»ΠΈΠ² ΠΎΠ±ΡΡΠΌ ΠΏΡΠΎΠΈΠ·Π²ΠΎΠ΄ΡΡΠ²Π°, Π²Ρ ΡΠΌΠΎΠΆΠ΅ΡΠ΅ Π²ΡΡΡΠΈΡΠ°ΡΡ ΡΡΠΎΠΊΠΈ, Π·Π° ΠΊΠΎΡΠΎΡΡΠ΅ ΠΎΠΊΡΠΏΡΡΡΡ Π²Π°ΡΠΈ Π²Π»ΠΎΠΆΠ΅Π½ΠΈΡ.
Π’Π°ΠΊ ΠΊΠ°ΠΊ ΠΏΡΠΎΠΈΠ·Π²ΠΎΠ΄ΡΡΠ²ΠΎ ΠΊΠΈΡΠΏΠΈΡΠ΅ΠΉ ΠΈΠ· ΠΎΠΏΠΈΠ»ΠΎΠΊ ΠΈ ΡΠ΅ΠΌΠ΅Π½ΡΠ° Π½Π΅ ΡΡΠ΅Π±ΡΠ΅Ρ ΡΠ»ΠΈΡΠΊΠΎΠΌ Π±ΠΎΠ»ΡΡΠΈΡ Π²Π»ΠΎΠΆΠ΅Π½ΠΈΠΉ. Π’ΠΎ ΠΏΡΠΈ Π½Π°Π»ΠΈΡΠΈΠΈ ΡΡΠ½ΠΊΠ° ΡΠ±ΡΡΠ°, Π²Ρ ΡΠΌΠΎΠΆΠ΅ΡΠ΅ Π²ΡΠΉΡΠΈ Π½Π° ΡΠΈΡΡΡΡ ΠΏΡΠΈΠ±ΡΠ»Ρ, ΠΏΡΠΈΠΌΠ΅ΡΠ½ΠΎ Π·Π° ΡΡΠΈ ΠΌΠ΅ΡΡΡΠ°.
Π Π°Π·ΠΌΠ΅ΡΡ ΠΈΠ·Π΄Π΅Π»ΠΈΠΉ ΠΈΠ· ΠΎΠΏΠΈΠ»ΠΎΠΊ ΠΈ ΡΠ΅ΠΌΠ΅Π½ΡΠ°
ΠΠ°Π²ΠΎΠ΄ΡΠΊΠΈΠ΅ ΡΠ°Π·ΠΌΠ΅ΡΡ ΡΡΠ°Π½Π΄Π°ΡΡΠ½ΡΡ ΠΊΠΈΡΠΏΠΈΡΠ΅ΠΉ ΠΈΠ· ΠΎΠΏΠΈΠ»ΠΎΠΊ ΠΈ ΡΠ΅ΠΌΠ΅Π½ΡΠ° ΡΠ°Π²Π½Ρ ΡΠΎΠΎΡΠ½ΠΎΡΠ΅Π½ΠΈΡ:
- ΠΡΡΠΎΡΠ° β 20 ΠΈΠ»ΠΈ 25 ΡΠ°Π½ΡΠΈΠΌΠ΅ΡΡΠΎΠ²;
- Π¨ΠΈΡΠΈΠ½Π° β 20 ΠΈΠ»ΠΈ 30 ΡΠ°Π½ΡΠΈΠΌΠ΅ΡΡΠΎΠ²;
- ΠΠ»ΠΈΠ½Π° β 40 ΠΈΠ»ΠΈ 50 ΡΠ°Π½ΡΠΈΠΌΠ΅ΡΡΠΎΠ².
ΠΠΎ, Π΄ΠΎΠΏΡΡΠΊΠ°ΡΡΡΡ ΠΈ Π΄ΡΡΠ³ΠΈΠ΅ ΡΠΎΠΎΡΠ½ΠΎΡΠ΅Π½ΠΈΡ, ΠΎΡΠΎΠ±Π΅Π½Π½ΠΎ, Π΅ΡΠ»ΠΈ Π²Ρ ΡΡΡΠΎΠΈΡΠ΅ Π΄Π»Ρ ΡΠ΅Π±Ρ. ΠΡΠΈ ΠΆΠ΅Π»Π°Π½ΠΈΠΈ Π²Ρ ΠΌΠΎΠΆΠ΅ΡΠ΅ ΡΠ΄Π΅Π»Π°ΡΡ Π±Π»ΠΎΠΊΠΈ ΡΠΈΡΠ΅ 30 ΡΠ°Π½ΡΠΈΠΌΠ΅ΡΡΠΎΠ².
ΠΠ»ΠΈ ΠΈΠ·Π³ΠΎΡΠΎΠ²ΠΈΡΡ ΠΊΠΈΡΠΏΠΈΡΠΈ Π²ΡΡΠ΅, ΡΠ΅ΠΌ 20 ΡΠ°Π½ΡΠΈΠΌΠ΅ΡΡΠΎΠ². ΠΡΠΎΡΡΠΎ ΡΠ»Π΅Π΄ΡΠ΅Ρ ΡΡΠΈΡΡΠ²Π°ΡΡ, ΡΡΠΎ Π² ΡΡΠΎΠΌ ΡΠ»ΡΡΠ°Π΅ Π±Π»ΠΎΠΊΠΈ Π±ΡΠ΄ΡΡ ΡΡΠΆΠ΅Π»Π΅Π΅, ΠΈ Π½ΡΠΆΠ½ΠΎ Π·Π°ΡΡΠ°ΡΠΈΠ²Π°ΡΡ Π±ΠΎΠ»ΡΡΠ΅ ΡΠΈΠ» Π½Π° ΠΈΡ ΡΡΠ°Π½ΡΠΏΠΎΡΡΠΈΡΠΎΠ²ΠΊΡ Π΄ΠΎ ΠΎΠ±ΡΠ΅ΠΊΡΠ°.
Π Π°Π·ΠΌΠ΅ΡΡ ΡΡΠ΅ΠΏΠ»ΠΈΡΠ΅Π»ΡΠ½ΡΡ ΠΏΠ°Π½Π΅Π»Π΅ΠΉ, ΡΠ°ΠΊΠΆΠ΅ ΠΌΠΎΠ³ΡΡ Π·Π½Π°ΡΠΈΡΠ΅Π»ΡΠ½ΠΎ Π²Π°ΡΡΠΈΡΠΎΠ²Π°ΡΡΡΡ ΠΏΠΎ ΡΠ²ΠΎΠΈΠΌ ΡΠ°Π·ΠΌΠ΅ΡΠ°ΠΌ. ΠΠ½ΠΎΠ³ΠΈΠ΅ ΠΏΡΠΎΠΈΠ·Π²ΠΎΠ΄ΠΈΡΠ΅Π»ΠΈ ΠΈΠ·Π³ΠΎΡΠ°Π²Π»ΠΈΠ²Π°ΡΡ ΠΏΠ°Π½Π΅Π»ΠΈ ΠΏΠΎ ΡΠ²ΠΎΠΈΠΌ, ΠΏΡΠΎΠ²Π΅ΡΠ΅Π½Π½ΡΠΌ Π²ΡΠ΅ΠΌΠ΅Π½Π΅ΠΌ ΡΠ°Π·ΠΌΠ΅ΡΠ°ΠΌ.
Π ΡΡΠ΅Π΄Π½Π΅ΠΌ ΠΌΠΎΠΆΠ½ΠΎ ΡΠΊΠ°Π·Π°ΡΡ ΡΠ»Π΅Π΄ΡΡΡΠΈΠ΅ ΡΠ°Π·ΠΌΠ΅ΡΡ:
- ΠΠ»Ρ ΡΡΠ΅ΠΏΠ»Π΅Π½ΠΈΡ ΠΏΠΎΠ»Π° β 82 ΡΠΌ Ρ 62 ΡΠΌ Ρ 8 ΡΠΌ;
- ΠΠ»Ρ ΡΡΠ΅ΠΏΠ»Π΅Π½ΠΈΡ ΡΡΠ΅Π½ β 82 ΡΠΌ Ρ 62 ΡΠΌ Ρ 10 ΡΠΌ.
Π ΡΠΎΡΡΠ°Π²Π΅ ΡΡΠ΅ΠΏΠ»ΠΈΡΠ΅Π»ΡΠ½ΡΡ ΠΏΠ»ΠΈΡ: 90% ΡΠΎΡΠ½ΠΎΠ²ΠΎΠΉ ΡΠ΅ΠΏΡ ΠΈ 10% ΡΠ΅ΠΌΠ΅Π½ΡΠ° Π500 + ΠΌΠΈΠ½Π΅ΡΠ°Π»ΠΈΠ·Π°ΡΠΎΡΡ.
ΠΡΠΎΠΈΠ·Π²ΠΎΠ΄ΡΡΠ²ΠΎ
ΠΡΡΡΡΠ΅Π½Π½Π°Ρ Π΄ΡΠ΅Π²Π΅ΡΠΈΠ½Π°, Π»ΡΡΡΠ΅ Π²ΡΠ΅Π³ΠΎ Ρ Π²ΠΎΠΉΠ½ΡΡ ΠΏΠΎΡΠΎΠ΄, ΠΏΡΠΎΠΏΡΡΠΊΠ°Π΅ΡΡΡ ΡΠ΅ΡΠ΅Π· Π΄ΡΠΎΠ±ΠΈΠ»ΠΊΡ ΠΈ Π΄Π°Π»Π΅Π΅ ΠΏΠΎΡΡΡΠΏΠ°Π΅Ρ Π² Π±Π°ΡΠ°Π±Π°Π½ Π±Π΅ΡΠΎΠ½ΠΎΠΌΠ΅ΡΠ°Π»ΠΊΠΈ.
ΠΡΠ΄Π΅Π»ΡΠ½ΠΎ Π·Π°ΠΌΠ΅ΡΠΈΠ²Π°ΡΡΡΡ Π²ΠΎΠ΄Π°, ΡΡΠ»ΡΡΠ°Ρ Π°Π»ΡΠΌΠΈΠ½ΠΈΡ, ΡΠ΅ΠΌΠ΅Π½Ρ. ΠΠ°Π½Π½ΡΠΌ ΡΠ°ΡΡΠ²ΠΎΡΠΎΠΌ Π·Π°Π»ΠΈΠ²Π°ΡΡΡΡ ΡΡΡ ΠΈΠ΅ ΠΎΠΏΠΈΠ»ΠΊΠΈ ΠΈ ΠΏΠ΅ΡΠ΅ΠΌΠ΅ΡΠΈΠ²Π°ΡΡΡΡ Π² ΡΠ΅ΡΠ΅Π½ΠΈΠΈ ΠΏΡΡΠΈ ΠΌΠΈΠ½ΡΡ.
ΠΠ°ΠΆΠ½ΠΎ!
ΠΠΎ ΠΎΠΊΠΎΠ½ΡΠ°Π½ΠΈΡ Π·Π°ΠΌΠ΅ΡΠ° ΡΠΌΠ΅ΡΡ Π΄ΠΎΠ»ΠΆΠ½Π° Π±ΡΡΡ ΡΠ°Π²Π½ΠΎΠΌΠ΅ΡΠ½ΠΎ Π²Π»Π°ΠΆΠ½ΠΎΠΉ, Π½ΠΎ Π½Π΅ ΠΌΠΎΠΊΡΠΎΠΉ! Π’ΠΎ Π΅ΡΡΡ, Π½Π΅ Π΄ΠΎΠ»ΠΆΠ½ΠΎ Π±ΡΡΡ ΠΈΠ·Π»ΠΈΡΠΊΠΎΠ² Π²ΠΎΠ΄Ρ Π² ΡΠΌΠ΅ΡΠΈ. ΠΠ½Π°ΡΠ΅, ΡΡΠ΅ΠΊΠ°Ρ ΠΏΡΠΈ ΡΡΡΠ°ΠΌΠ±ΠΎΠ²ΠΊΠ΅, ΠΎΠ½Π° Π²ΡΠΌΠΎΠ΅Ρ ΡΠ°ΡΡΡ ΡΠ΅ΠΌΠ΅Π½ΡΠ° ΠΈΠ· ΡΠ°ΡΡΠ²ΠΎΡΠ°.
ΠΠΎΡΠ»Π΅ ΡΡΠΎΠ³ΠΎ Π³ΠΎΡΠΎΠ²Π°Ρ ΡΠΌΠ΅ΡΡ ΡΠΊΠ»Π°Π΄ΡΠ²Π°Π΅ΡΡΡ Π² ΡΠΎΡΠΌΡ, ΡΠΌΠ°Π·Π°Π½Π½ΡΠ΅ ΠΎΡΡΠ°Π±ΠΎΡΠ°Π½Π½ΡΠΌ ΠΌΠ°ΡΠΈΠ½Π½ΡΠΌ ΠΌΠ°ΡΠ»ΠΎΠΌ. Π£ΡΡΠ°ΠΌΠ±ΠΎΠ²ΡΠ²Π°Π΅ΡΡΡ ΠΏΡΠΈ ΠΏΠΎΠΌΠΎΡΠΈ Π²ΠΈΠ±ΡΠ°ΡΠΈΠΈ ΠΈ Π²ΠΎΠ·Π΄Π΅ΠΉΡΡΠ²ΠΈΡ ΡΠΈΠ»Ρ. ΠΡΠ΅ΡΡΡΠ΅ΡΡΡ ΠΈ ΠΏΠΎΡΡΡΠΏΠ°Π΅Ρ Π½Π° ΠΏΡΠΎΡΡΡΠΊΡ.
Π‘ΡΡΠΈΡΡΡ Π² ΡΠ΅ΡΠ΅Π½ΠΈΠΈ 12 β 18 ΡΠ°ΡΠΎΠ², Π² ΡΡΡΠΈΠ»ΡΠ½ΠΎΠΉ ΠΊΠ°ΠΌΠ΅ΡΠ΅.
Π§Π΅ΠΌ ΠΌΠ΅Π½ΡΡΠ΅, Π² ΠΏΡΠΎΡΠ΅Π½ΡΠ½ΠΎΠΌ ΡΠΎΠ΄Π΅ΡΠΆΠ°Π½ΠΈΠΈ Π²Ρ ΠΊΠ»Π°Π΄ΡΡΠ΅ ΡΠ΅ΠΌΠ΅Π½ΡΠ°, ΡΠ΅ΠΌ Π±ΠΎΠ»Π΅Π΅ ΠΈΠ·Π΄Π΅Π»ΠΈΠ΅ Π±ΡΠ΄Π΅Ρ ΡΠΎΡ ΡΠ°Π½ΡΡΡ ΡΠ΅ΠΏΠ»ΠΎ. ΠΠ΄Π½Π°ΠΊΠΎ, ΠΏΡΠΈ ΡΡΠΎΠΌ ΡΠΌΠ΅Π½ΡΡΠ°Π΅ΡΡΡ Π΅Π³ΠΎ ΠΏΡΠΎΡΠ½ΠΎΡΡΡ.
Π Π½Π°ΠΎΠ±ΠΎΡΠΎΡ, ΡΠ΅ΠΌ Π±ΠΎΠ»ΡΡΠ΅ ΡΠ΅ΠΌΠ΅Π½ΡΠ°, ΡΠ΅ΠΌ ΠΏΠ»ΠΎΡΠ½Π΅Π΅ ΠΈ ΠΏΡΠΎΡΠ½Π΅Π΅ ΠΈΠ·Π΄Π΅Π»ΠΈΠ΅, Π½ΠΎ, ΠΏΡΠΈ ΡΡΠΎΠΌ ΠΏΠΎΠ²ΡΡΠ°Π΅ΡΡΡ ΡΠ΅ΠΏΠ»ΠΎΠΏΡΠΎΠ²ΠΎΠ΄Π½ΠΎΡΡΡ.
Π Π°ΡΡ ΠΎΠ΄ ΠΌΠ°ΡΠ΅ΡΠΈΠ°Π»Π°, ΠΏΡΠΎΠΏΠΎΡΡΠΈΠΈ
ΠΠΎΠ΄Π±ΠΎΡ ΡΠΎΡΡΠ°Π²Π° Π΄Π»Ρ ΠΈΠ·Π³ΠΎΡΠΎΠ²Π»Π΅Π½ΠΈΡ Π°ΡΠ±ΠΎΠ»ΠΈΡΠ° ΠΏΡΠΎΠΈΠ·Π²ΠΎΠ΄ΠΈΡΡΡ ΡΠ°ΡΡΠ΅ΡΠ½ΠΎ-ΡΠΊΡΠΏΠ΅ΡΠΈΠΌΠ΅Π½ΡΠ°Π»ΡΠ½ΡΠΌ ΠΌΠ΅ΡΠΎΠ΄ΠΎΠΌ. ΠΠ½ΠΎΠ³ΠΎΠ΅ Π·Π°Π²ΠΈΡΠΈΡ ΠΎΡ Π²Π»Π°ΠΆΠ½ΠΎΡΡΠΈ, ΠΊΠ°ΡΠ΅ΡΡΠ²Π° ΠΈΡΡ ΠΎΠ΄Π½ΠΎΠ³ΠΎ ΡΡΡΡΡ ΠΈ ΠΏΠΎΡΠΎΠ΄Ρ Π΄Π΅ΡΠ΅Π²Π°.
Π’Π°ΠΊΠΆΠ΅, ΠΎΡ ΡΠΎΠ³ΠΎ, ΠΈΠ·Π΄Π΅Π»ΠΈΠ΅ ΠΊΠ°ΠΊΠΎΠΉ ΠΌΠ°ΡΠΊΠΈ Π²Ρ Ρ ΠΎΡΠΈΡΠ΅ ΠΏΠΎΠ»ΡΡΠΈΡΡ Π½Π° Π²ΡΡ ΠΎΠ΄Π΅. ΠΠ»Ρ ΠΏΠ΅ΡΠ²ΠΎΠ½Π°ΡΠ°Π»ΡΠ½ΠΎΠ³ΠΎ, ΠΏΡΠΎΠ±Π½ΠΎΠ³ΠΎ Π·Π°ΠΌΠ΅ΡΠ°, ΠΏΠΎ ΠΠΠ‘Π’Ρ ΡΠ΅ΠΊΠΎΠΌΠ΅Π½Π΄ΡΡΡΡΡ ΠΏΡΠΈΠΌΠ΅Π½ΡΡΡ ΠΏΡΠΎΠΏΠΎΡΡΠΈΠΈ, ΡΠΊΠ°Π·Π°Π½Π½ΡΠ΅ Π² ΠΈΠ½ΡΡΡΡΠΊΡΠΈΠΈ ΠΏΠΎ ΠΈΠ·Π³ΠΎΡΠΎΠ²Π»Π΅Π½ΠΈΡ ΠΈΠ·Π΄Π΅Π»ΠΈΠΉ ΠΈΠ· Π°ΡΠ±ΠΎΠ»ΠΈΡΠ° β Π‘Π549-82.
Π ΡΠΏΠ΅ΡΠΈΠ°Π»ΡΠ½ΡΡ ΡΠ°Π±Π»ΠΈΡΠ°Ρ ΠΊΠΎΡΠΎΡΠΎΠΉ ΠΈΠ·Π»ΠΎΠΆΠ΅Π½Ρ ΡΠ΅ΠΊΠΎΠΌΠ΅Π½Π΄ΡΠ΅ΠΌΡΠ΅ ΠΏΡΠΎΠΏΠΎΡΡΠΈΠΈ Π²ΡΠ΅Ρ ΠΊΠΎΠΌΠΏΠΎΠ½Π΅Π½ΡΠΎΠ², Π΄Π»Ρ ΠΏΠ΅ΡΠ²ΠΎΠ³ΠΎ Π·Π°ΠΌΠ΅ΡΠ°.
ΠΠ°Ρ ΠΎΠ΄ΠΈΡΡΡ Π΄Π°Π½Π½Π°Ρ ΠΈΠ½ΡΡΡΡΠΊΡΠΈΡ ΠΏΠΎ Π°Π΄ΡΠ΅ΡΡ: files.stroyinf.ru/Data1/2/2032/
ΠΠΈΠ΄Π΅ΠΎ ΠΏΠΎ ΡΠ΅ΠΌΠ΅ ΠΈΠ·Π³ΠΎΡΠΎΠ²Π»Π΅Π½ΠΈΡ ΠΊΠΈΡΠΏΠΈΡΠ° ΠΈΠ· ΠΎΠΏΠΈΠ»ΠΎΠΊ, ΠΏΡΠΈΠΌΠ΅Ρ ΠΌΠ°Π»ΠΎΠ³ΠΎ Π±ΠΈΠ·Π½Π΅ΡΠ°.
Π‘ΡΠ°ΡΡΠΈ ΠΏΠΎ ΡΠ΅ΠΌΠ΅:
Β
Β
ΠΠΈΡΠΏΠΈΡ ΠΈΠ· ΠΎΠΏΠΈΠ»ΠΎΠΊ ΠΈ ΡΠ΅ΠΌΠ΅Π½ΡΠ° β Π‘Π°ΠΉΡ ΠΎ Π΄Π°ΡΠ΅
ΠΠΏΠΈΠ»ΠΊΠΎΠ±Π΅ΡΠΎΠ½ ΡΠ²ΠΎΠΈΠΌΠΈ ΡΡΠΊΠ°ΠΌΠΈ.
Π ΡΠΎΡΡΠ°Π² ΠΎΠΏΠΈΠ»ΠΊΠΎΠ±Π΅ΡΠΎΠ½Π° Π²Ρ ΠΎΠ΄ΡΡ Π΄ΡΠ΅Π²Π΅ΡΠ½ΡΠ΅ ΠΎΠΏΠΈΠ»ΠΊΠΈ ΠΈ ΡΡΡΡΠΆΠΊΠ°, ΠΏΠ΅ΡΠΎΠΊ, Π²ΡΠΆΡΡΠΈΠ΅ ΠΌΠ°ΡΠ΅ΡΠΈΠ°Π»Ρ β ΡΠ΅ΠΌΠ΅Π½Ρ ΠΈ ΠΈΠ·Π²Π΅ΡΡΡ, Π²ΠΎΠ΄Π°. Π‘Π²ΠΎΠΉΡΡΠ²Π° ΠΎΠΏΠΈΠ»ΠΊΠΎΠ±Π΅ΡΠΎΠ½Π° Π·Π°Π²ΠΈΡΡΡ ΠΎΡ ΡΠΎΠΎΡΠ½ΠΎΡΠ΅Π½ΠΈΡ ΠΏΠ΅ΡΠΊΠ° ΠΈ ΠΎΠΏΠΈΠ»ΠΎΠΊ. Π§Π΅ΠΌ ΠΌΠ΅Π½ΡΡΠ΅Π΅ ΠΊΠΎΠ»ΠΈΡΠ΅ΡΡΠ²ΠΎ ΠΏΠ΅ΡΠΊΠ° ΠΏΠΎΡΠ»ΠΎ Π½Π° ΠΈΠ·Π³ΠΎΡΠΎΠ²Π»Π΅Π½ΠΈΠ΅ ΠΎΠΏΠΈΠ»ΠΊΠΎΠ±Π΅ΡΠΎΠ½Π°, ΡΠ΅ΠΌ ΠΌΠ΅Π½ΡΡΠ΅ Π΅Π³ΠΎ ΠΏΠ»ΠΎΡΠ½ΠΎΡΡΡ ΠΈ ΡΠ΅ΠΌ Π»ΡΡΡΠ΅ ΡΠ΅ΠΏΠ»ΠΎΡΠ΅Ρ Π½ΠΈΡΠ΅ΡΠΊΠΈΠ΅ Ρ Π°ΡΠ°ΠΊΡΠ΅ΡΠΈΡΡΠΈΠΊΠΈ. ΠΠΎ Π² ΡΡΠΎΠΌ ΡΠ»ΡΡΠ°Π΅ ΡΠΌΠ΅Π½ΡΡΠ°Π΅ΡΡΡ ΠΏΡΠΎΡΠ½ΠΎΡΡΡ ΠΌΠ°ΡΠ΅ΡΠΈΠ°Π»Π°. Π‘ ΡΠ²Π΅Π»ΠΈΡΠ΅Π½ΠΈΠ΅ΠΌ ΠΊΠΎΠ»ΠΈΡΠ΅ΡΡΠ²Π° ΠΏΠ΅ΡΠΊΠ° ΠΈ Π²ΡΠΆΡΡΠΈΡ ΠΌΠ°ΡΠ΅ΡΠΈΠ°Π»ΠΎΠ² ΠΏΡΠΎΡΠ½ΠΎΡΡΡ ΠΎΠΏΠΈΠ»ΠΊΠΎΠ±Π΅ΡΠΎΠ½Π° Π²ΠΎΠ·ΡΠ°ΡΡΠ°Π΅Ρ, ΡΠ°ΠΊΠΆΠ΅ ΠΏΠΎΠ²ΡΡΠ°Π΅ΡΡΡ ΠΌΠΎΡΠΎΠ·ΠΎΡΡΠΎΠΉΠΊΠΎΡΡΡ ΠΈ ΡΠΌΠ΅Π½ΡΡΠ°Π΅ΡΡΡ Π²ΠΎΠ΄ΠΎΠ½Π΅ΠΏΡΠΎΠ½ΠΈΡΠ°Π΅ΠΌΠΎΡΡΡ. ΠΠΎΡΡΠΎΠΌΡ, ΠΏΡΠ΅ΠΆΠ΄Π΅ ΡΠ΅ΠΌ ΠΏΡΠΈΡΡΡΠΏΠ°ΡΡ ΠΊ ΠΈΠ·Π³ΠΎΡΠΎΠ²Π»Π΅Π½ΠΈΡ ΠΎΠΏΠΈΠ»ΠΊΠΎΠ±Π΅ΡΠΎΠ½Π° Π½Π΅ΠΎΠ±Ρ ΠΎΠ΄ΠΈΠΌΠΎ ΡΡΠΈΡΡΠ²Π°ΡΡ Π΄Π»Ρ ΠΊΠ°ΠΊΠΎΠΉ ΡΠ΅Π»ΠΈ ΠΎΠ½ ΠΈΡΠΏΠΎΠ»ΡΠ·ΡΠ΅ΡΡΡ.
Π’Π°Π±Π»ΠΈΡΠ° 1. ΠΡΠ½ΠΎΠ²Π½ΡΠ΅ ΡΠ²ΠΎΠΉΡΡΠ²Π° ΠΎΠΏΠΈΠ»ΠΊΠΎΠ±Π΅ΡΠΎΠ½Π°.
Π‘Π²ΠΎΠΉΡΡΠ²Π° ΠΎΠΏΠΈΠ»ΠΊΠΎΠ±Π΅ΡΠΎΠ½Π° | Β |
Π’Π΅ΠΏΠ»ΠΎΠΏΡΠΎΠ²ΠΎΠ΄Π½ΠΎΡΡΡ, ΠΊΠΊΠ°Π»/ΠΌΒ·ΡΒ·Π³ΡΠ°Π΄ | 0,2-0,4 |
ΠΠ±ΡΡΠΌΠ½ΡΠΉ Π²Π΅Ρ, ΠΊΠ³/ΠΌ3 | 950-1250 |
ΠΠΎΠ΄ΠΎΠΏΠΎΠ³Π»ΠΎΡΠ΅Π½ΠΈΠ΅, % | 100 |
ΠΡΠΎΡΠ½ΠΎΡΡΡ, ΠΊΠ³/ΡΠΌ2 | 5-20 |
Π£ΡΠ°Π΄ΠΊΠ°, % | 1,5 |
ΠΠΎΡΠΎΠ·ΠΎΡΡΠΎΠΉΠΊΠΎΡΡΡ, ΡΠΈΠΊΠ»Ρ | 10 |
ΠΠ· ΡΠ°Π±Π»ΠΈΡΡ Π²ΠΈΠ΄Π½ΠΎ, ΡΡΠΎ ΡΠ°ΠΌΡΠΌ Π±ΠΎΠ»ΡΡΠΈΠΌ Π½Π΅Π΄ΠΎΡΡΠ°ΡΠΊΠΎΠΌ ΠΎΠΏΠΈΠ»ΠΊΠΎΠ±Π΅ΡΠΎΠ½Π° ΡΠ²Π»ΡΠ΅ΡΡΡ Π±ΠΎΠ»ΡΡΠΎΠ΅ Π²ΠΎΠ΄ΠΎΠΏΠΎΠ³Π»ΠΎΡΠ΅Π½ΠΈΠ΅, ΠΏΠΎΡΡΠΎΠΌΡ ΡΡΠ΅Π½Ρ ΠΈΠ· ΠΎΠΏΠΈΠ»ΠΊΠΎΠ±Π΅ΡΠΎΠ½Π° Π½ΡΠΆΠ΄Π°ΡΡΡΡ Π² ΠΏΡΠΈΠΌΠ΅Π½Π΅Π½ΠΈΠΈ ΠΏΠ°ΡΠΎΠΈΠ·ΠΎΠ»ΡΡΠΈΠΈ ΠΊΠ°ΠΊ Ρ Π²Π½ΡΡΡΠ΅Π½Π½Π΅ΠΉ, ΡΠ°ΠΊ ΠΈ Π²Π½Π΅ΡΠ½Π΅ΠΉ ΡΡΠΎΡΠΎΠ½Ρ.
ΠΠ»Π°Π³ΠΎΠ΄Π°ΡΡ Π½Π°Π»ΠΈΡΠΈΡ ΠΎΠΏΠΈΠ»ΠΎΠΊ Π² ΠΎΠΏΠΈΠ»ΠΊΠΎΠ±Π΅ΡΠΎΠ½Π΅ Π±Π»ΠΎΠΊΠΈ ΠΈΠ· Π½Π΅Π³ΠΎ ΡΠΎΠΎΡΠ²Π΅ΡΡΡΠ²ΡΡΡ ΠΏΠΎ ΠΌΠ½ΠΎΠ³ΠΈΠΌ ΠΏΠΎΠΊΠ°Π·Π°ΡΠ΅Π»ΡΠΌ Π΄ΡΠ΅Π²Π΅ΡΠΈΠ½Π΅. ΠΠΎ Π² ΠΎΡΠ»ΠΈΡΠΈΠ΅Β ΠΎΡ Π΄ΡΠ΅Π²Π΅ΡΠΈΠ½Ρ ΠΎΠΏΠΈΠ»ΠΊΠΎΠ±Π΅ΡΠΎΠ½ ΠΈΠΌΠ΅Π΅Ρ Π²ΡΡΠΎΠΊΡΡ ΠΎΠ³Π½Π΅ΡΡΠΎΠΉΠΊΠΎΡΡΡ, ΠΊΠΎΡΠΎΡΠ°Ρ Β ΠΎΠ±ΡΡΠ»ΠΎΠ²Π»Π΅Π½Π° ΡΠ΅ΠΌ, ΡΡΠΎ ΠΏΠ΅ΡΡΠ°Π½ΠΎβΡΠ΅ΠΌΠ΅Π½ΡΠ½Π°Ρ ΡΠΌΠ΅ΡΡ ΠΏΠ»ΠΎΡΠ½ΠΎ Π·Π°ΠΏΠΎΠ»Π½ΡΠ΅Ρ ΠΏΡΠΎΡΡΡΠ°Π½ΡΡΠ²ΠΎ ΠΌΠ΅ΠΆΠ΄Ρ ΠΎΠΏΠΈΠ»ΠΊΠ°ΠΌΠΈ. ΠΠΏΠΈΠ»ΠΊΠΎΠ±Π΅ΡΠΎΠ½ ΠΏΠΎ ΠΏΠΎΠΊΠ°Π·Π°ΡΠ΅Π»Ρ ΠΎΠ³Π½Π΅ΡΡΠΎΠΉΠΊΠΎΡΡΠΈ ΠΏΡΠ΅Π²ΠΎΡΡ ΠΎΠ΄ΠΈΡ Π΄Π°ΠΆΠ΅ ΠΏΠ΅Π½ΠΎΠΏΠΎΠ»ΠΈΡΡΠΈΡΠΎΠ»Π±Π΅ΡΠΎΠ½.
ΠΠ»ΡΒ ΠΈΠ·Π³ΠΎΡΠΎΠ²Π»Π΅Π½ΠΈΡ ΠΎΠΏΠΈΠ»ΠΊΠΎΠ±Π΅ΡΠΎΠ½Π° ΠΈΡΠΏΠΎΠ»ΡΠ·ΡΡΡΡΡ ΠΎΠΏΠΈΠ»ΠΊΠΈ ΠΈ Π΄ΡΠ΅Π²Π΅ΡΠ½Π°Ρ ΡΡΡΡΠΆΠΊΠ°. ΠΡΠΎΠΏΠΎΡΡΠΈΠΈ ΠΎΠΏΠΈΠ»ΠΎΠΊ ΠΈ ΡΡΡΡΠΆΠΊΠΈ Π²Π°ΡΡΠΈΡΡΡΡΡΡ ΠΎΡ 1:1 Π΄ΠΎ 1:2, ΡΠΎ Π΅ΡΡΡ Π½Π° ΠΎΠ΄Π½Ρ ΡΠ°ΡΡΡ ΠΎΠΏΠΈΠ»ΠΎΠΊ ΠΌΠΎΠΆΠ½ΠΎ ΠΈΡΠΏΠΎΠ»ΡΠ·ΠΎΠ²Π°ΡΡ ΠΎΠ΄Π½Ρ ΠΈΠ»ΠΈ Π΄Π²Π΅ ΡΠ°ΡΡΠΈ ΡΡΡΡΠΆΠΊΠΈ.
ΠΠ»Ρ Π΄ΠΎΡΡΠΈΠΆΠ΅Π½ΠΈΡ Π½Π΅ΠΎΠ±Ρ ΠΎΠ΄ΠΈΠΌΠΎΠΉ ΠΏΡΠΎΡΠ½ΠΎΡΡΠΈ Π² ΠΎΠΏΠΈΠ»ΠΊΠΎΠ±Π΅ΡΠΎΠ½Π΅ ΠΈΡΠΏΠΎΠ»ΡΠ·ΡΠ΅ΡΡΡ Π² ΠΎΡΠ½ΠΎΠ²Π½ΠΎΠΌ ΡΠ΅ΠΌΠ΅Π½ΡΠ½ΠΎ-ΠΏΠ΅ΡΡΠ°Π½Π°Ρ ΡΠΌΠ΅ΡΡ. Π§Π΅ΠΌ Π±ΠΎΠ»ΡΡΠ΅ ΡΠ΅ΠΌΠ΅Π½ΡΠ° ΠΈ ΠΏΠ΅ΡΠΊΠ° Π² ΠΎΠΏΠΈΠ»ΠΊΠΎΠ±Π΅ΡΠΎΠ½Π½ΠΎΠΉ ΡΠΌΠ΅ΡΠΈ, ΡΠ΅ΠΌ ΠΏΡΠΎΡΠ½Π΅Π΅ ΠΏΠΎΠ»ΡΡΠ°Π΅ΡΡΡ ΠΌΠ°ΡΠ΅ΡΠΈΠ°Π», Π½ΠΎ ΠΏΡΠΈ ΡΡΠΎΠΌ ΠΈ ΡΠ·Ρ ΡΠ΄ΡΠ°ΡΡΡΡ Π΅Π³ΠΎ ΡΠ΅ΠΏΠ»ΠΎΠ·Π°ΡΠΈΡΠ½ΡΠ΅ ΡΠ²ΠΎΠΉΡΡΠ²Π°.
ΠΠ° ΠΏΡΠΎΡΠ½ΠΎΡΡΡ ΠΎΠΏΠΈΠ»ΠΊΠΎΠ±Π΅ΡΠΎΠ½Π° ΠΎΡΡΠΈΡΠ°ΡΠ΅Π»ΡΠ½ΠΎ Π²Π»ΠΈΡΠ΅Ρ Π½Π°Π»ΠΈΡΠΈΠ΅ ΡΠ°Ρ Π°ΡΠΈΡΡΡΡ Π²Π΅ΡΠ΅ΡΡΠ², ΡΠΎΠ΄Π΅ΡΠΆΠ°ΡΠΈΡ ΡΡ Π² ΠΎΡΠ³Π°Π½ΠΈΡΠ΅ΡΠΊΠΎΠΌ Π·Π°ΠΏΠΎΠ»Π½ΠΈΡΠ΅Π»Π΅. Π§Π΅ΠΌ Π±ΠΎΠ»ΡΡΠ΅ ΠΈΠ·ΠΌΠ΅Π»ΡΡΠ΅Π½ Π·Π°ΠΏΠΎΠ»Π½ΠΈΡΠ΅Π»Ρ, ΡΠ΅ΠΌ Π±ΠΎΠ»ΡΡΠ΅ ΠΎΠ½ Π²ΡΠ΄Π΅Π»ΡΠ΅Ρ ΡΠ°Ρ Π°ΡΠΈΡΡΡΠ΅ Π²Π΅ΡΠ΅ΡΡΠ²Π°. Π ΡΠ°Π±Π»ΠΈΡΠ΅ ΠΏΡΠΈΠ²Π΅Π΄Π΅Π½ ΠΏΡΠΎΡΠ΅Π½Ρ ΡΠΎΠ΄Π΅ΡΠΆΠ°Π½ΠΈΡ ΡΠ°Ρ Π°ΡΠΈΡΡΡΡ Π²Π΅ΡΠ΅ΡΡΠ² Π² ΡΠ°Π·Π»ΠΈΡΠ½ΡΡ ΠΏΠΎΡΠΎΠ΄Π°Ρ Π΄Π΅ΡΠ΅Π²ΡΠ΅Π². Π§Π΅ΠΌ Π±ΠΎΠ»ΡΡΠΈΠΉ ΠΏΡΠΎΡΠ΅Π½Ρ ΡΠΎΠ΄Π΅ΡΠΆΠ°Π½ΠΈΡ ΡΠ°Ρ Π°ΡΠΈΡΡΡΡ Π²Π΅ΡΠ΅ΡΡΠ² Π² Π΄ΡΠ΅Π²Π΅ΡΠΈΠ½Π΅, ΡΠ΅ΠΌ ΠΌΠ΅Π½Π΅Π΅ ΠΎΠ½Π° ΠΏΡΠΈΠ³ΠΎΠ΄Π½Π° Π΄Π»Ρ ΠΈΠ·Π³ΠΎΡΠΎΠ²Π»Π΅Π½ΠΈΡ Π°ΡΠ±ΠΎΠ»ΠΈΡΠ° ΠΈΠ»ΠΈ ΠΎΠΏΠΈΠ»ΠΊΠΎΠ±Π΅ΡΠΎΠ½Π°.
ΠΠΎΡΠΎΠ΄Π° Π΄ΡΠ΅Π²Π΅ΡΠΈΠ½Ρ | Π‘ΠΎΠ΄Π΅ΡΠΆΠ°Π½ΠΈΠ΅ ΡΠ°Ρ Π°ΡΠΈΡΡΡΡ Π²Π΅ΡΠ΅ΡΡΠ², % |
ΠΠ»Ρ | 1,12 |
Π’ΠΎΠΏΠΎΠ»Ρ | 1,29 β 1,45 |
ΠΠ΅ΡΡΠ·Π° | 2,67 |
Π‘ΠΎΡΠ½Π° | 3,16 β 6,2 |
ΠΡΠ± | 2,55 β 7,33 |
Π―ΡΠ΅Π½Ρ | 2,24 β 5,81 |
ΠΠΈΡΡΠ²Π΅Π½Π½ΠΈΡΠ° | 10,6 |
ΠΠ»Ρ ΡΠ°Π·ΡΡΡΠ΅Π½ΠΈΡ ΡΡΠΈΡ Π²Π΅ΡΠ΅ΡΡΠ² ΠΎΠΏΠΈΠ»ΠΊΠΈ, ΡΡΡΡΠΆΠΊΡ, Π΄ΡΠ΅Π²Π΅ΡΠ½ΡΡ Π΄ΡΠΎΠ±Π»ΡΠ½ΠΊΡ Π½Π΅ΠΎΠ±Ρ ΠΎΠ΄ΠΈΠΌΠΎ Π²ΡΠ΄Π΅ΡΠΆΠ°ΡΡ Π½Π° ΠΎΡΠΊΡΡΡΠΎΠΌ Π²ΠΎΠ·Π΄ΡΡ Π΅, Π½Π΅ Π΄ΠΎΠΏΡΡΠΊΠ°Ρ ΠΈΡ Π³Π½ΠΈΠ΅Π½ΠΈΡ, ΡΠΎ Π΅ΡΡΡ Π½Π°Π΄ΠΎ ΠΏΠΎΡΡΠΎΡΠ½Π½ΠΎ ΠΈΡ Π²ΠΎΡΠΎΡΠΈΡΡ. ΠΠ»Ρ Ρ Π²ΠΎΠΉΠ½ΡΡ ΠΏΠΎΡΠΎΠ΄ Π΄Π΅ΡΠ΅Π²ΡΠ΅Π² ΡΡΠ΅Π±ΡΠ΅ΡΡΡ Π½Π΅ ΠΌΠ΅Π½Π΅Π΅ 2 ΠΌΠ΅ΡΡΡΠ΅Π², Π΄Π»Ρ Π»ΠΈΡΡΠ²Π΅Π½Π½ΡΡ β Π½Π΅ ΠΌΠ΅Π½Π΅Π΅ 6 ΠΌΠ΅ΡΡΡΠ΅Π².Β ΠΠ»Ρ ΡΡΠΊΠΎΡΠ΅Π½ΠΈΡ ΠΏΡΠΎΡΠ΅ΡΡΠ° Π΄ΡΠ΅Π²Π΅ΡΠ½ΡΡ ΠΌΠ°ΡΡΡ Π½Π΅ΠΎΠ±Ρ ΠΎΠ΄ΠΈΠΌΠΎ ΠΎΠ±ΡΠ°Π±ΠΎΡΠ°ΡΡ ΠΈΠ·Π²Π΅ΡΡΡΡ. ΠΠ»Ρ ΠΎΠ±ΡΠ°Π±ΠΎΡΠΊΠΈ 1 ΠΊΡΠ±. ΠΌ Π·Π°ΠΏΠΎΠ»Π½ΠΈΡΠ΅Π»Ρ Π½Π΅ΠΎΠ±Ρ ΠΎΠ΄ΠΈΠΌΠΎ ΡΠ°Π·Π²Π΅ΡΡΠΈ 2 β 3 ΠΊΠ³ ΠΈΠ·Π²Π΅ΡΡΠΈ Π² 150 β 200 Π» Π²ΠΎΠ΄Ρ ΠΈ ΠΏΠΎΠ»ΠΈΡΡ Π΅Ρ Π΄ΡΠ΅Π²Π΅ΡΠ½ΡΡ ΠΌΠ°ΡΡΡ, Π²ΡΠ΄Π΅ΡΠΆΠ°ΡΡΒ 3 β 4 Π΄Π½Ρ, Π΅ΠΆΠ΅Π΄Π½Π΅Π²Π½ΠΎ ΠΏΠ΅ΡΠ΅ΠΌΠ΅ΡΠΈΠ²Π°Ρ. ΠΠ°ΠΏΠΎΠ»Π½ΠΈΡΠ΅Π»Ρ ΠΌΠΎΠΆΠ½ΠΎ Π·Π°ΠΌΠΎΡΠΈΡΡ Π² ΠΈΠ·Π²Π΅ΡΡΠΊΠΎΠ²ΠΎΠΌ ΡΠ°ΡΡΠ²ΠΎΡΠ΅, Π²ΡΠ΄Π΅ΡΠΆΠ°Π² Π² Π½Π΅ΠΌ 2 β 4 ΡΠ°ΡΠ°.
Π Π·Π°Π²ΠΈΡΠΈΠΌΠΎΡΡΠΈ ΠΎΡ ΡΠΎΡΡΠ°Π²Π° ΠΎΠΏΠΈΠ»ΠΊΠΎΠ±Π΅ΡΠΎΠ½ ΠΏΠΎΠ΄ΡΠ°Π·Π΄Π΅Π»ΡΡΡ Π½Π° ΠΌΠ°ΡΠΊΠΈ. Π ΡΠ°Π±Π»ΠΈΡΠ΅ ΠΏΡΠ΅Π΄ΡΡΠ°Π²Π»Π΅Π½Ρ ΠΌΠ°ΡΠΊΠΈ ΠΎΠΏΠΈΠ»ΠΊΠΎΠ±Π΅ΡΠΎΠ½Π° ΠΈ ΡΠΎΠΎΡΠ²Π΅ΡΡΡΠ²ΡΡΡΠΈΠ΅ ΠΈΠΌ ΠΊΠΎΠ»ΠΈΡΠ΅ΡΡΠ²ΠΎ Π²ΡΠΆΡΡΠΈΡ ΠΌΠ°ΡΠ΅ΡΠΈΠ°Π»ΠΎΠ² ΠΈ ΠΏΠ΅ΡΠΊΠ°.
Π’Π°Π±Π»ΠΈΡΠ°. Π Π΅ΠΊΠΎΠΌΠ΅Π½Π΄ΡΠ΅ΠΌΡΠ΅ ΠΏΡΠΎΠΏΠΎΡΡΠΈΠΈ ΠΎΠΏΠΈΠ»ΠΊΠΎΠ±Π΅ΡΠΎΠ½Π°.
ΠΠ°ΡΠΊΠ° ΠΎΠΏΠΈΠ»ΠΊΠΎ-Π±Π΅ΡΠΎΠ½Π° | ΠΠ°ΡΠΊΠ° ΠΏΠΎΡΡΠ»Π°Π½Π΄-ΡΠ΅ΠΌΠ΅Π½ΡΠ° | Π‘ΠΎΡΡΠ°Π² 1 ΠΌ3 Π±Π΅ΡΠΎΠ½Π° ΠΏΠΎ Π²Π΅ΡΡ,ΠΊΠ³ | ΠΠ±ΡΡΠΌΠ½ΡΠΉ Π²Π΅Ρ,ΠΊΠ³/ΠΌ3Β (ΠΏΡΠΈΠΌΠ΅ΡΠ½ΠΎ) | ΠΠΎΡΡΡΠΈΡΠΈΠ΅Π½Ρ ΡΠ΅ΠΏΠ»ΠΎΠΏΡΠΎΠ²ΠΎ- Π΄Π½ΠΎΡΡΠΈ,ΠΊΠΊΠ°Π»/ΠΌΒ·ΡΒ·Π³ΡΠ°Π΄ (ΠΏΡΠΈΠΌΠ΅ΡΠ½ΡΠΉ) | |||
Π¦Π΅-ΠΌΠ΅Π½Ρ | ΠΠ·Π²Π΅-ΡΡΡ Π³Π°ΡΠ΅-Π½Π°Ρ | ΠΠ΅-ΡΠΎΠΊ | ΠΠΏΠΈΠ»ΠΊΠΈ | ||||
Π10 | Π300 | 150 | 150 | 530 | 210 | 950 β 1050 | 0,21 β 0,24 |
Π400 | 90 | 165 | 530 | 210 | |||
Π500 | 75 | 180 | 530 | 210 | |||
Π15 | Π300 | 210 | Β β | 630 | 210 | 1050 β 1150 | 0,24 β 0,27 |
Π400 | 135 | 105 | 610 | 200 | |||
Π500 | 105 | 120 | 620 | 210 | |||
Π25 | Π300 | 300 | β | 670 | 190 | 1150 β 1250 | 0,27 β 0,37 |
ΠΠΏΠΈΠ»ΠΊΠΎΠ±Π΅ΡΠΎΠ½ ΠΌΠ°ΡΠΊΠΈ Π10 ΠΈΡΠΏΠΎΠ»ΡΠ·ΡΠ΅ΡΡΡ Π΄Π»Ρ ΡΡΡΠΎΠΈΡΠ΅Π»ΡΡΡΠ²Π° ΡΡΠ΅Π½ ΠΎΠ΄Π½ΠΎΡΡΠ°ΠΆΠ½ΡΡ ΠΆΠΈΠ»ΡΡ Π·Π΄Π°Π½ΠΈΠΉ, Π΄Π»Ρ ΡΡΠ΅ΠΏΠ»Π΅Π½ΠΈΡ ΠΏΠΎΠ΄Π²Π°Π»ΠΎΠ² ΠΈ ΡΡΠ΅Π½. ΠΠΏΠΈΠ»ΠΊΠΎΠ±Π΅ΡΠΎΠ½ ΠΌΠ°ΡΠΎΠΊ Π15 ΠΈ Π25 ΠΈΡΠΏΠΎΠ»ΡΠ·ΡΠ΅ΡΡΡ Π΄Π»Ρ ΡΡΡΠΎΠΈΡΠ΅Π»ΡΡΡΠ²Π° ΡΡΠ΅Π½ ΠΎΠ΄Π½ΠΎΡΡΠ°ΠΆΠ½ΡΡ ΠΆΠΈΠ»ΡΡ Π·Π΄Π°Π½ΠΈΠΉ Ρ ΠΌΠ°Π½ΡΠ°ΡΠ΄ΠΎΠΉ.
ΠΠ»ΡΒ ΠΈΠ·Π³ΠΎΡΠΎΠ²Π»Π΅Π½ΠΈΡ ΠΎΠΏΠΈΠ»ΠΊΠΎΠ±Π΅ΡΠΎΠ½Π° ΠΈΡΠΏΠΎΠ»ΡΠ·ΡΡΡΡΡ ΠΎΠΏΠΈΠ»ΠΊΠΈ ΠΈ Π΄ΡΠ΅Π²Π΅ΡΠ½Π°Ρ ΡΡΡΡΠΆΠΊΠ°. ΠΡΠΎΠΏΠΎΡΡΠΈΠΈ ΠΎΠΏΠΈΠ»ΠΎΠΊ ΠΈ ΡΡΡΡΠΆΠΊΠΈ Π²Π°ΡΡΠΈΡΡΡΡΡΡ ΠΎΡ 1:1 Π΄ΠΎ 1:2, ΡΠΎ Π΅ΡΡΡ Π½Π° ΠΎΠ΄Π½Ρ ΡΠ°ΡΡΡ ΠΎΠΏΠΈΠ»ΠΎΠΊ ΠΌΠΎΠΆΠ½ΠΎ ΠΈΡΠΏΠΎΠ»ΡΠ·ΠΎΠ²Π°ΡΡ ΠΎΠ΄Π½Ρ ΠΈΠ»ΠΈ Π΄Π²Π΅ ΡΠ°ΡΡΠΈ ΡΡΡΡΠΆΠΊΠΈ. ΠΠ»Ρ ΠΏΡΠΈΠ³ΠΎΡΠΎΠ²Π»Π΅Π½ΠΈΡ ΠΎΠΏΠΈΠ»ΠΊΠΎΠ±Π΅ΡΠΎΠ½Π° Π»ΡΡΡΠ΅ Π±ΡΠ°ΡΡ ΠΎΠΏΠΈΠ»ΠΊΠΈ ΠΈ ΡΡΡΡΠΆΠΊΡ Ρ Π²ΠΎΠΉΠ½ΡΡ ΠΏΠΎΡΠΎΠ΄, ΠΏΡΠΎΠ»Π΅ΠΆΠ°Π²ΡΠΈΠ΅ Π½Π° ΠΎΡΠΊΡΡΡΠΎΠΌ Π²ΠΎΠ·Π΄ΡΡ Π΅ Π½Π΅ΡΠΊΠΎΠ»ΡΠΊΠΎ ΠΌΠ΅ΡΡΡΠ΅Π². ΠΠ΅ΡΠ΅Π΄ ΠΈΡΠΏΠΎΠ»ΡΠ·ΠΎΠ²Π°Π½ΠΈΠ΅ΠΌ ΠΎΠΏΠΈΠ»ΠΊΠΈ ΠΏΠΎΡΠ»Π΅Π΄ΠΎΠ²Π°ΡΠ΅Π»ΡΠ½ΠΎ ΠΏΡΠΎΡΠ΅Π²Π°ΡΡ ΡΠ΅ΡΠ΅Π· ΡΠΈΡΠ° Ρ ΡΠ°Π·ΠΌΠ΅ΡΠΎΠΌ ΡΡΠ΅ΠΉΠΊΠΈ 20Γ20 ΠΌΠΌ, Π·Π°ΡΠ΅ΠΌ 10Γ10 ΠΌΠΌ ΠΈ 5Γ5 ΠΌΠΌ.Β ΠΠ»Ρ ΡΠ»ΡΡΡΠ΅Π½ΠΈΡ ΠΏΡΠΎΡΠ½ΠΎΡΡΠΈ ΠΊ ΠΏΡΠΎΡΠ΅ΡΠ½Π½ΡΠΌ ΠΎΠΏΠΈΠ»ΠΊΠ°ΠΌ Π΄ΠΎΠ±Π°Π²Π»ΡΠ΅ΡΡΡ Π΄ΡΠ΅Π²Π΅ΡΠ½Π°Ρ ΡΡΡΡΠΆΠΊΠ°, ΠΏΡΠΎΡΠ΅ΡΠ½Π½Π°Ρ ΡΠ΅ΡΠ΅Π· ΡΠΈΡΠΎ Ρ ΡΠ°Π·ΠΌΠ΅ΡΠΎΠΌ ΡΡΠ΅Π΅ΠΊ 10Γ10 ΠΌΠΌ.Β Π’Π°ΠΊΠΈΠ΅ ΡΠ°Π·ΠΌΠ΅ΡΡ Π·Π°ΠΏΠΎΠ»Π½ΠΈΡΠ΅Π»Π΅ΠΉ ΠΎΠΏΠΈΠ»ΠΊΠΎΠ±Π΅ΡΠΎΠ½Π° ΠΎΠ±ΡΡΠ»ΠΎΠ²Π»Π΅Π½Ρ ΡΠΊΠΎΠ½ΠΎΠΌΠΈΡΠ΅ΡΠΊΠΈΠΌΠΈ ΡΠΎΠΎΠ±ΡΠ°ΠΆΠ΅Π½ΠΈΡΠΌΠΈ,Β Π΅ΡΠ»ΠΈ ΡΠ°Π·ΠΌΠ΅Ρ Π΄ΡΠ΅Π²Π΅ΡΠ½ΡΡ ΡΠ°ΡΡΠΈΡ ΠΌΠ΅Π½ΡΡΠ΅, ΡΠΎ ΡΡΠΎΠ±Ρ ΠΈΡ ΡΠΊΠ»Π΅ΠΈΡΡ Π½ΡΠΆΠ½ΠΎ, ΠΈΠ·ΡΠ°ΡΡ ΠΎΠ΄ΠΎΠ²Π°ΡΡ Π±ΠΎΠ»ΡΡΠ΅ Π²ΡΠΆΡΡΠ΅Π³ΠΎ ΠΌΠ°ΡΠ΅ΡΠΈΠ°Π»Π°. Π ΡΠ°ΠΊΠΎΠΌ ΡΠ»ΡΡΠ°Π΅ Π΄Π»Ρ ΠΏΡΠΈΠ³ΠΎΡΠΎΠ²Π»Π΅Π½ΠΈΡ ΠΎΠΏΠΈΠ»ΠΊΠΎΠ±Π΅ΡΠΎΠ½Π° ΡΠ°ΡΡ ΠΎΠ΄ ΡΠ΅ΠΌΠ΅Π½ΡΠ° Π±ΡΠ΄Π΅Ρ Π±ΠΎΠ»ΡΡΠ΅. ΠΡΠΎΠΌΠ΅ ΡΠΎΠ³ΠΎ, ΡΠ²Π΅Π»ΠΈΡΠ΅Π½ΠΈΠ΅ ΠΊΠΎΠ»ΠΈΡΠ΅ΡΡΠ²Π° ΡΠ΅ΠΌΠ΅Π½ΡΠ° ΠΏΡΠΈ ΠΏΡΠΎΠΈΠ·Π²ΠΎΠ΄ΡΡΠ²Π΅ ΠΎΠΏΠΈΠ»ΠΊΠΎΠ±Π΅ΡΠΎΠ½Π° ΡΠ½ΠΈΠΆΠ°Π΅Ρ Π΅Π³ΠΎ ΡΠ΅ΠΏΠ»ΠΎΡΠ΅Ρ Π½ΠΈΡΠ΅ΡΠΊΠΈΠ΅ Ρ Π°ΡΠ°ΠΊΡΠ΅ΡΠΈΡΡΠΈΠΊΠΈ.
ΠΠ°ΠΏΠΎΠ»Π½ΠΈΡΠ΅Π»Ρ Π½ΡΠΆΠ½ΠΎ ΠΏΠΎΠ΄Π²Π΅ΡΠ³Π½ΡΡΡ Ρ ΠΈΠΌΠΈΡΠ΅ΡΠΊΠΎΠΉ ΠΎΠ±ΡΠ°Π±ΠΎΡΠΊΠ΅.Β ΠΠ΅ΠΎΠ±Ρ ΠΎΠ΄ΠΈΠΌΠΎΡΡΡ ΠΎΠ±ΡΠ°Π±ΠΎΡΠΊΠΈ ΠΎΠ±ΡΡΠ»ΠΎΠ²Π»Π΅Π½Π° Π½Π°Π»ΠΈΡΠΈΠ΅ΠΌ Π² Π΄ΡΠ΅Π²Π΅ΡΠΈΠ½Π΅ Π²ΠΎΠ΄ΠΎΡΠ°ΡΡΠ²ΠΎΡΠΈΠΌΡΡ Π²Π΅ΡΠ΅ΡΡΠ² Π³ΡΡΠΏΠΏΡ ΡΠ°Ρ Π°ΡΠΎΠ², ΠΊΠΎΡΠΎΡΡΠ΅ ΠΌΠΎΠ³ΡΡ Π²ΡΠ·Π²Π°ΡΡ ΠΏΡΠΎΡΠ΅ΡΡ Π±ΡΠΎΠΆΠ΅Π½ΠΈΡ Π² Π³ΠΎΡΠΎΠ²ΡΡ Π±Π»ΠΎΠΊΠ°Ρ . ΠΡΠΈ ΡΡΠΎΠΌ ΠΏΠΎΠ²Π΅ΡΡ Π½ΠΎΡΡΡ Π±Π»ΠΎΠΊΠ°Β Π²ΡΠΏΡΡΠΈΠ²Π°Π΅ΡΡΡ,Β ΠΌΠΎΠ³ΡΡ ΠΎΠ±ΡΠ°Π·ΠΎΠ²Π°ΡΡΡΡ ΠΏΡΡΡΠΎΡΡ. ΠΠ΅ΠΉΡΡΠ°Π»ΠΈΠ·Π°ΡΠΈΡ ΡΡΠΈΡ Π²Π΅ΡΠ΅ΡΡΠ² ΠΏΡΠΎΠ²ΠΎΠ΄ΠΈΡΡΡ ΡΠ°ΡΡΠ²ΠΎΡΠΎΠΌ Ρ Π»ΠΎΡΠΈΡΡΠΎΠ³ΠΎ ΠΊΠ°Π»ΡΡΠΈΡ, ΡΠ΅ΡΠ½ΠΎΠΊΠΈΡΠ»ΠΎΠ³ΠΎ Π°Π»ΡΠΌΠΈΠ½ΠΈΡ ΠΈΠ»ΠΈ ΠΆΠΈΠ΄ΠΊΠΎΠ³ΠΎ ΡΡΠ΅ΠΊΠ»Π°.
Π§Π΅ΠΌ Π±ΠΎΠ»ΡΡΠ΅ ΠΈΠ·ΠΌΠ΅Π»ΡΡΠ΅Π½ Π·Π°ΠΏΠΎΠ»Π½ΠΈΡΠ΅Π»Ρ, ΡΠ΅ΠΌ Π±ΠΎΠ»ΡΡΠ΅ ΠΎΠ½ Π²ΡΠ΄Π΅Π»ΡΠ΅Ρ ΡΠ°Ρ Π°ΡΠΈΡΡΡΡ Π²Π΅ΡΠ΅ΡΡΠ². ΠΠ»Ρ ΡΠ°Π·ΡΡΡΠ΅Π½ΠΈΡ ΡΡΠΈΡ Π²Π΅ΡΠ΅ΡΡΠ² ΠΎΠΏΠΈΠ»ΠΊΠΈ, ΡΡΡΡΠΆΠΊΡ, Π½Π΅ΠΎΠ±Ρ ΠΎΠ΄ΠΈΠΌΠΎ Π²ΡΠ΄Π΅ΡΠΆΠ°ΡΡ 3 β 4 ΠΌΠ΅ΡΡΡΠ° Π½Π° ΠΎΡΠΊΡΡΡΠΎΠΌ Π²ΠΎΠ·Π΄ΡΡ Π΅, Π½Π΅ Π΄ΠΎΠΏΡΡΠΊΠ°Ρ ΠΈΡ Π³Π½ΠΈΠ΅Π½ΠΈΡ, ΡΠΎ Π΅ΡΡΡ Π½Π°Π΄ΠΎ ΠΏΠΎΡΡΠΎΡΠ½Π½ΠΎ ΠΈΡ Π²ΠΎΡΠΎΡΠΈΡΡ. ΠΠ»Ρ ΡΡΠΊΠΎΡΠ΅Π½ΠΈΡ ΠΏΡΠΎΡΠ΅ΡΡΠ° Π΄ΡΠ΅Π²Π΅ΡΠ½ΡΡ ΠΌΠ°ΡΡΡ Π½Π΅ΠΎΠ±Ρ ΠΎΠ΄ΠΈΠΌΠΎ ΠΎΠ±ΡΠ°Π±ΠΎΡΠ°ΡΡ ΠΈΠ·Π²Π΅ΡΡΡΡ. ΠΠ»Ρ ΠΎΠ±ΡΠ°Π±ΠΎΡΠΊΠΈ 1 ΠΌΒ³ Β Π·Π°ΠΏΠΎΠ»Π½ΠΈΡΠ΅Π»Ρ Π½Π΅ΠΎΠ±Ρ ΠΎΠ΄ΠΈΠΌΠΎ ΡΠ°Π·Π²Π΅ΡΡΠΈ 2 β 3 ΠΊΠ³ ΠΈΠ·Π²Π΅ΡΡΠΈ Π² 150 β 200 Π» Π²ΠΎΠ΄Ρ ΠΈ ΠΏΠΎΠ»ΠΈΡΡ Π΅Ρ Π΄ΡΠ΅Π²Π΅ΡΠ½ΡΡ ΠΌΠ°ΡΡΡ, Π²ΡΠ΄Π΅ΡΠΆΠ°ΡΡ 3 β 4 Π΄Π½Ρ, Π΅ΠΆΠ΅Π΄Π½Π΅Π²Π½ΠΎ ΠΏΠ΅ΡΠ΅ΠΌΠ΅ΡΠΈΠ²Π°Ρ. ΠΠΎΠ»Π³ΠΎ ΠΏΡΠΎΠ»Π΅ΠΆΠ°Π²ΡΠΈΠ΅ ΠΎΠΏΠΈΠ»ΠΊΠΈ ΠΎΠ±ΡΠ·Π°ΡΠ΅Π»ΡΠ½ΠΎ Π½Π΅ΠΎΠ±Ρ ΠΎΠ΄ΠΈΠΌΠΎ ΠΎΠ±ΡΠ°Π±ΠΎΡΠ°ΡΡ ΠΈΠ·Π²Π΅ΡΡΠΊΠΎΠ²ΡΠΌ ΠΌΠΎΠ»ΠΎΠΊΠΎΠΌ ΠΈΠ»ΠΈ Ρ ΠΏΠΎΠΌΠΎΡΡΡ ΡΠ°ΡΡΠ²ΠΎΡΠ° 10% Ρ Π»ΠΎΡΠΈΠ΄Π° ΠΊΠ°Π»ΡΡΠΈΡ. ΠΠΎΡΠ»Π΅ ΡΡΠΎΠ³ΠΎ ΠΈΡ Π½ΡΠΆΠ½ΠΎ ΡΡΠ°ΡΠ΅Π»ΡΠ½ΠΎ Π²ΡΡΡΡΠΈΡΡ ΠΈ ΠΏΡΠΎΠΈΠ·Π²Π΅ΡΡΠΈ ΠΎΠ±ΡΠ°Π±ΠΎΡΠΊΡ Π±ΠΈΡΡΠΌΠ½ΠΎΠΉ ΡΠΌΡΠ»ΡΡΠΈΠ΅ΠΉ ΠΈΠ»ΠΈ ΡΠ°ΡΡΠ²ΠΎΡΠΎΠΌ ΠΈΠ· ΠΆΠΈΠ΄ΠΊΠΎΠ³ΠΎ ΡΡΠ΅ΠΊΠ»Π° Π² ΠΏΡΠΎΠΏΠΎΡΡΠΈΠΈ 1:7.
ΠΠ»Ρ ΡΠ»ΡΡΡΠ΅Π½ΠΈΡ ΠΊΠ°ΡΠ΅ΡΡΠ²Π° ΠΎΠΏΠΈΠ»ΠΊΠΎΠ±Π΅ΡΠΎΠ½Π°Β Π² ΡΠΌΠ΅ΡΡ Π΄ΠΎΠ±Π°Π²Π»ΡΡΡ Ρ ΠΈΠΌΠΈΡΠ΅ΡΠΊΠΈΠ΅ Π΄ΠΎΠ±Π°Π²ΠΊΠΈΒ Π² ΡΠ°ΡΡΠ΅ΡΠ΅ 2 β 4% ΠΎΡ ΠΌΠ°ΡΡΡ ΡΠ΅ΠΌΠ΅Π½ΡΠ°. Π₯ΠΈΠΌΠΈΡΠ΅ΡΠΊΠΈΠ΅ Π΄ΠΎΠ±Π°Π²ΠΊΠΈ ΠΏΠΎ ΡΠΏΠΎΡΠΎΠ±Ρ Π²ΠΎΠ·Π΄Π΅ΠΉΡΡΠ²ΠΈΡ Π΄Π΅Π»ΡΡΡΡ:
- ΡΡΠΊΠΎΡΠΈΡΠ΅Π»ΠΈ ΡΠ²Π΅ΡΠ΄Π΅Π½ΠΈΡ β Ρ Π»ΠΎΡΠΈΠ΄ ΠΊΠ°Π»ΡΡΠΈΡ, Π½ΠΈΡΡΠ°Ρ ΠΊΠ°Π»ΡΡΠΈΡ, Π½ΠΈΡΡΠΈΡ-Π½ΠΈΡΡΠ°Ρ-Ρ Π»ΠΎΡΠΈΠ΄ ΠΊΠ°Π»ΡΡΠΈΡ, ΡΠ΅ΡΠ½ΠΎΠΊΠΈΡΠ»ΡΠΉ Π³Π»ΠΈΠ½ΠΎΠ·Π΅ΠΌ, ΠΆΠΈΠ΄ΠΊΠΎΠ΅ ΡΡΠ΅ΠΊΠ»ΠΎ+Ρ Π»ΠΎΡΠΈΠ΄ Π°Π»ΡΠΌΠΈΠ½ΠΈΡ , Ρ Π»ΠΎΡΠΈΠ΄ ΠΊΠ°Π»ΡΡΠΈΡ + ΠΎΠΊΡΠΈΠ΄ ΠΊΠ°Π»ΡΡΠΈΡ, Π³ΠΈΠ΄ΡΠΎΠΎΠΊΡΠΈΠ΄ ΠΊΠ°Π»ΡΡΠΈΡ;
- ΠΎΠ±ΡΠ°Π·ΡΡΡΠΈΠ΅ ΠΏΠ»Π΅Π½ΠΊΡ Π½Π° ΠΏΠΎΠ²Π΅ΡΡ Π½ΠΎΡΡΠΈ ΠΎΡΠ³Π°Π½ΠΈΡΠ΅ΡΠΊΠΈΡ ΡΠ°ΡΡΠΈΡ β ΡΡΠ΅ΠΊΠ»ΠΎ Π½Π°ΡΡΠΈΠ΅Π²ΠΎΠ΅ ΠΆΠΈΠ΄ΠΊΠΎΠ΅, ΠΆΠΈΠ΄ΠΊΠΎΠ΅ ΡΡΠ΅ΠΊΠ»ΠΎ+Ρ Π»ΠΎΡΠΈΠ΄ ΠΊΠ°Π»ΡΡΠΈΡ, ΠΆΠΈΠ΄ΠΊΠΎΠ΅ ΡΡΠ΅ΠΊΠ»ΠΎ+ΡΠ΅ΡΠ½ΠΎΠΊΠΈΡΠ»ΡΠΉ Π³Π»ΠΈΠ½ΠΎΠ·Π΅ΠΌ , ΠΆΠΈΠ΄ΠΊΠΎΠ΅ ΡΡΠ΅ΠΊΠ»ΠΎ+ΡΡΡΠΈΠ»ΠΎΠ²ΡΠΉ ΡΠΏΠΈΡΡ ;
- ΠΏΠ΅Π½ΠΎΠΎΠ±ΡΠ°Π·ΡΡΡΠΈΠ΅ β ΠΆΠΈΠ΄ΠΊΠΎΡΡΠ΅ΠΊΠΎΠ»ΡΠ½ΡΠΉ ΠΏΠ΅Π½ΠΎΠΎΠ±ΡΠ°Π·ΠΎΠ²Π°ΡΠ΅Π»Ρ, Π°Π»ΠΊΠΈΠ»ΡΡΠ»ΡΡΠ°Π½Π°Ρ ΠΏΠ°ΡΡΠ° Π‘Π-1, Π²Π΅ΡΠ΅ΡΡΠ²ΠΎ ΠΆΠΈΠ΄ΠΊΠΎΠ΅ ΠΌΠΎΡΡΠ΅Π΅ Π‘Π-3;
- Π²ΠΎΠ·Π΄ΡΡ ΠΎΠ²ΠΎΠ²Π»Π΅ΠΊΠ°ΡΡΠΈΠ΅ β ΡΠΌΠΎΠ»Π° Π΄ΡΠ΅Π²Π΅ΡΠ½Π°Ρ ΠΎΠΌΡΠ»Π΅Π½Π½Π°Ρ , ΡΠΌΠΎΠ»Π° Π½Π΅ΠΉΡΡΠ°Π»ΠΈΠ·ΠΎΠ²Π°Π½Π½Π°Ρ Π²ΠΎΠ·Π΄ΡΡ ΠΎΠ²ΠΎΠ²Π»Π΅ΠΊΠ°ΡΡΠ°Ρ, ΠΎΠΌΡΠ»Π΅Π½Π½ΡΠΉ Π΄ΡΠ΅Π²Π΅ΡΠ½ΡΠΉ ΠΏΠ΅ΠΊ Π¦ΠΠΠΠ‘-1;
- Π³ΠΈΠ΄ΡΠΎΡΠΎΠ±ΠΈΠ·ΠΈΡΡΡΡΠΈΠ΅ (Π²ΠΎΠ΄ΠΎΠΎΡΠ°Π»ΠΊΠΈΠ²Π°ΡΡΠΈΠ΅)Β β ΡΡΠΈΠ»ΡΠΈΠ»ΠΈΠΊΠΎΠ½Π°Ρ Π½Π°ΡΡΠΈΡ ΠΠΠ-10, ΠΌΠ΅ΡΠΈΠ»ΡΠΈΠ»ΠΈΠΊΠΎΠ½Π°Ρ Π½Π°ΡΡΠΈΡ ΠΠΠ-11, ΠΏΠΎΠ»ΠΈΠ³ΠΈΠ΄ΡΠΎΡΠΈΠ»ΠΎΠΊΡΠ°Π½ ΠΠΠ-94.
ΠΠΈΠ΄ΡΠΎΡΠΎΠ±ΠΈΠ·Π°ΡΠΎΡΡ ΠΏΡΠ΅Π΄ΡΡΠ°Π²Π»ΡΡΡ ΡΠΎΠ±ΠΎΠΉ ΡΠ°ΡΡΠ²ΠΎΡΡ ΠΊΡΠ΅ΠΌΠ½ΠΈΠΉΠΎΡΠ³Π°Π½ΠΈΡΠ΅ΡΠΊΠΈΡ (ΡΠΈΠ»ΠΈΠΊΠΎΠ½ΠΎΠ²ΡΡ ) ΡΠΎΠ΅Π΄ΠΈΠ½Π΅Π½ΠΈΠΉ. ΠΠΈΠ΄ΡΠΎΡΠΎΠ±ΠΈΠ·Π°ΡΠΎΡΡ ΠΏΡΠΈ ΠΏΠΎΠΌΠΎΡΠΈ Π½ΠΎΡΠΈΡΠ΅Π»Ρ (Π²ΠΎΠ΄Π° ΠΈΠ»ΠΈ ΡΠ°ΡΡΠ²ΠΎΡΠΈΡΠ΅Π»Ρ) ΠΏΠΎΠΏΠ°Π΄Π°ΡΡ Π²Π½ΡΡΡΡ ΠΎΠ±ΡΠ°Π±Π°ΡΡΠ²Π°Π΅ΠΌΠΎΠ³ΠΎ ΠΌΠ°ΡΠ΅ΡΠΈΠ°Π»Π° ΠΈ Π·Π°ΡΠ΅ΠΌ ΠΏΠΎΠ»ΠΈΠΊΠΎΠ½Π΄Π΅Π½ΡΠΈΡΡΡΡΡΡ, ΡΠΎΠ·Π΄Π°Π²Π°Ρ Π²ΠΎΠ΄ΠΎΠΎΡΡΠ°Π»ΠΊΠΈΠ²Π°ΡΡΠΈΠΉ ΠΏΠ°ΡΠΎΠΏΡΠΎΠ½ΠΈΡΠ°Π΅ΠΌΡΠΉ ΡΠ»ΠΎΠΉ, ΠΊΠΎΡΠΎΡΡΠΉΒ Π·Π°ΡΠΈΡΠ°Π΅Ρ ΠΊΠΎΠ½ΡΡΡΡΠΊΡΠΈΡ ΠΎΡ ΠΏΡΠΎΠ½ΠΈΠΊΠ½ΠΎΠ²Π΅Π½ΠΈΡ Π²Π»Π°Π³ΠΈ.
ΠΡΠΎΠΌΠ΅ ΡΠΎΠ³ΠΎ, Π² ΡΠΌΠ΅ΡΡ Π΄ΠΎΠ±Π°Π²Π»ΡΡΡ ΠΌΠΈΠ½Π΅ΡΠ°Π»ΠΈΠ·Π°ΡΠΎΡΡΒ Π² ΡΠ°ΡΡΠ΅ΡΠ΅ 2 β 4% ΠΎΡ ΠΌΠ°ΡΡΡ ΡΠ΅ΠΌΠ΅Π½ΡΠ°. ΠΡΡΡΠΈΠΌΠΈ ΠΌΠΈΠ½Π΅ΡΠ°Π»ΠΈΠ·Π°ΡΠΎΡΠ°ΠΌΠΈΒ Β ΡΠ²Π»ΡΡΡΡΡ:
- ΡΠ΅ΡΠ½ΠΎΠΊΠΈΡΠ»ΡΠΉ Π°Π»ΡΠΌΠΈΠ½ΠΈΠΉ;
- Ρ Π»ΠΎΡΠΈΡΡΡΠΉ Π°Π»ΡΠΌΠΈΠ½ΠΈΠΉ;
- Ρ Π»ΠΎΡΠΈΡΡΡΠΉ ΠΊΠ°Π»ΡΡΠΈΠΉ;
- ΡΠ΅ΡΠ½ΠΎΠΊΠΈΡΠ»ΡΠΉ Π½Π°ΡΡΠΈΠΉ;
- ΠΆΠΈΠ΄ΠΊΠΎΠ΅ ΡΡΠ΅ΠΊΠ»ΠΎ.
ΠΠΎΠΆΠ½ΠΎ ΡΠ°ΠΊΠΆΠ΅ ΠΈΡΠΏΠΎΠ»ΡΠ·ΠΎΠ²Π°ΡΡ ΠΌΠΈΠ½Π΅ΡΠ°Π»ΡΠ½ΡΠ΅ ΡΠ΄ΠΎΠ±ΡΠ΅Π½ΠΈΡ:
- Ρ Π»ΠΎΡΠΈΡΡΡΠΉ ΠΌΠ°Π³Π½ΠΈΠΉ;
- Ρ Π»ΠΎΡΠΈΡΡΡΠΉ ΠΊΠ°Π»ΠΈΠΉ;
- Π°ΠΌΠΌΠΈΠ°ΡΠ½ΡΡ ΡΠ΅Π»ΠΈΡΡΡ.
ΠΡΠΈ Π΄ΠΎΠ±Π°Π²ΠΊΠΈ ΠΌΠΎΠΆΠ½ΠΎ ΠΏΡΠΈΠΌΠ΅Π½ΡΡΡ ΠΎΡΠ΄Π΅Π»ΡΠ½ΠΎ ΠΈΠ»ΠΈ ΡΠΎΠ²ΠΌΠ΅ΡΡΠ½ΠΎ. Π‘ΠΎΠΎΡΠ½ΠΎΡΠ΅Π½ΠΈΠ΅ ΠΌΠΎΠ΄ΠΈΡΠΈΡΠΈΡΡΡΡΠΈΡ Π΄ΠΎΠ±Π°Π²ΠΎΠΊ ΠΈ ΠΎΠΏΠΈΠ»ΠΎΠΊ Π΄Π»Ρ ΠΏΡΠΎΠΈΠ·Π²ΠΎΠ΄ΡΡΠ²Π° ΠΎΠΏΠΈΠ»ΠΊΠΎΠ±Π΅ΡΠΎΠ½Π° Π΄ΠΎΠ»ΠΆΠ½ΠΎ ΡΠΎΡΡΠ°Π²Π»ΡΡΡ 1 ΡΠ°ΡΡΡ Π΄ΠΎΠ±Π°Π²ΠΎΠΊ ΠΊ 40 ΡΠ°ΡΡΡΠΌ ΠΎΠΏΠΈΠ»ΠΎΠΊ. ΠΠ°ΠΏΡΠΈΠΌΠ΅Ρ, Π½Π° ΠΊΡΠ± Π±Π΅ΡΠΎΠ½Π° Π΄ΠΎΠ±Π°Π²Π»ΡΡΡ 8 β 9 ΠΊΠ³ ΠΆΠΈΠ΄ΠΊΠΎΠ³ΠΎ ΡΡΠ΅ΠΊΠ»Π° ΠΈΠ»ΠΈ Ρ Π»ΠΎΡΠΈΡΡΠΎΠ³ΠΎ ΠΊΠ°Π»ΡΡΠΈΡ.
Π ΡΠ°Π±Π»ΠΈΡΠ΅ Β Β ΠΏΡΠΈΠ²Π΅Π΄Π΅Π½ ΠΌΠ°ΠΊΡΠΈΠΌΠ°Π»ΡΠ½ΡΠΉ ΡΠ°ΡΡ ΠΎΠ΄ Ρ ΠΈΠΌΠΈΡΠ΅ΡΠΊΠΎΠΉ Π΄ΠΎΠ±Π°Π²ΠΊΠΈ Π½Π° 1 ΠΌ3Β ΠΎΠΏΠΈΠ»ΠΊΠΎΠ±Π΅ΡΠΎΠ½Π°.
ΠΠΈΠ΄ Ρ ΠΈΠΌΠΈΡΠ΅ΡΠΊΠΈΡ Π΄ΠΎΠ±Π°Π²ΠΎΠΊ | Π Π°ΡΡ ΠΎΠ΄ Ρ ΠΈΠΌΠΈΡΠ΅ΡΠΊΠΎΠΉ Π΄ΠΎΠ±Π°Π²ΠΊΠΈ, ΠΊΠ³ |
ΠΠ°Π»ΡΡΠΈΠΉ Ρ Π»ΠΎΡΠΈΡΡΡΠΉ ΡΠ΅Ρ Π½ΠΈΡΠ΅ΡΠΊΠΈΠΉ | 8 |
Π‘ΡΠ΅ΠΊΠ»ΠΎ Π½Π°ΡΡΠΈΠ΅Π²ΠΎΠ΅ ΠΆΠΈΠ΄ΠΊΠΎΠ΅ | 8 |
Π‘Π΅ΡΠ½ΠΎΠΊΠΈΡΠ»ΡΠΉ Π³Π»ΠΈΠ½ΠΎΠ·Π΅ΠΌ | 20 |
ΠΠ·Π²Π΅ΡΡΡ-ΠΏΡΡΠΎΠ½ΠΊΠ° | 25 |
ΠΠΎΠ±Π°Π²ΠΊΠΈ ΡΠ½Π°ΡΠ°Π»Π° ΡΠ°ΡΡΠ²ΠΎΡΡΡΡ Π² Π²ΠΎΠ΄Π΅, ΡΠ°ΡΡΠ²ΠΎΡ Π²Π»ΠΈΠ²Π°ΡΡ Π² ΠΎΠΏΠΈΠ»ΠΊΠΎΠ±Π΅ΡΠΎΠ½. ΠΠ»Ρ ΠΈΠ·ΠΌΠ΅ΡΠ΅Π½ΠΈΡ ΠΊΠΎΠ»ΠΈΡΠ΅ΡΡΠ²Π° ΡΠΎΡΡΠ°Π²Π»ΡΡΡΠΈΡ Β ΠΌΠΎΠΆΠ½ΠΎ ΠΏΠΎΠ»ΡΠ·ΠΎΠ²Π°ΡΡΡΡ Π²Π΅Π΄ΡΠΎΠΌ. Π Π²Π΅Π΄ΡΠ΅ ΡΠΌΠΊΠΎΡΡΡΡ 10 Π»ΠΈΡΡΠΎΠ² Π²ΠΌΠ΅ΡΠ°Π΅ΡΡΡ 12 ΠΊΠ³ ΡΡΡ ΠΎΠ³ΠΎ ΡΠ΅ΠΌΠ΅Π½ΡΠ°, 1,4 ΠΊΠ³ ΠΎΠΏΠΈΠ»ΠΎΠΊ, 1, 2 ΠΊΠ³ ΡΡΡΡΠΆΠΊΠΈ.
Π’Π°Π±Π»ΠΈΡΠ°. ΠΡΠΎΠΏΠΎΡΡΠΈΠΈ ΠΎΠΏΠΈΠ»ΠΊΠΎΠ±Π΅ΡΠΎΠ½Π° Π² Π²ΡΠ΄ΡΠ°Ρ (10 Π»ΠΈΡΡΠΎΠ²).
ΠΠ°ΡΠΊΠ° ΠΏΠΎΡΡΠ»Π°Π½Π΄- ΡΠ΅ΠΌΠ΅Π½ΡΠ° | Π‘ΠΎΡΡΠ°Π² 1 ΠΌ3 Π±Π΅ΡΠΎΠ½Π° Π² Π²ΡΠ΄ΡΠ°Ρ (10 Π»ΠΈΡΡΠΎΠ²)Β | |||
Π¦Π΅ΠΌΠ΅Π½Ρ | ΠΠ·Π²Π΅ΡΡΡ Β Π³Π°ΡΠ΅Π½Π°Ρ | ΠΠ΅ΡΠΎΠΊ | ΠΠΏΠΈΠ»ΠΊΠΈ | |
Π300 | 12.5 | 12.5 | 33 | 150 |
Π400 | 7.5 | 13.75 | 33 | 150 |
Π500 | 6.25 | 15 | 33 | 150 |
ΠΡΠΈΠ³ΠΎΡΠΎΠ²Π»Π΅Π½ΠΈΠ΅ ΠΎΠΏΠΈΠ»ΠΊΠΎΠ±Π΅ΡΠΎΠ½Π° Π²ΡΡΡΠ½ΡΡ ΡΠ²Π»ΡΠ΅ΡΡΡ Π΄ΠΎΡΡΠ°ΡΠΎΡΠ½ΠΎ ΡΡΡΠ΄ΠΎΡΠΌΠΊΠΈΠΌ ΠΏΡΠΎΡΠ΅ΡΡΠΎΠΌ, ΠΏΠΎΡΡΠΎΠΌΡ Π»ΡΡΡΠ΅ ΠΈΡΠΏΠΎΠ»ΡΠ·ΠΎΠ²Π°ΡΡ Π±Π΅ΡΠΎΠ½ΠΎΠΌΠ΅ΡΠ°Π»ΠΊΡ ΠΈΠ»ΠΈ ΡΠΌΠ΅ΡΠΈΡΠ΅Π»Ρ Π΄Π»Ρ ΡΠ°ΡΡΠ²ΠΎΡΠ°. ΠΡΡΡΡΠ΅Π½Π½ΡΠ΅ ΠΈ ΠΏΡΠΎΡΠ΅ΡΠ½Π½ΡΠ΅ ΠΎΠΏΠΈΠ»ΠΊΠΈ ΡΠΌΠ΅ΡΠΈΠ²Π°ΡΡ Ρ ΠΏΠ΅ΡΠΊΠΎΠΌ ΠΈ ΡΠ΅ΠΌΠ΅Π½ΡΠΎΠΌ, ΡΡΠ°ΡΠ΅Π»ΡΠ½ΠΎ ΠΏΠ΅ΡΠ΅ΠΌΠ΅ΡΠΈΠ²Π°ΡΡ, Π·Π°ΡΠ΅ΠΌ Π΄ΠΎΠ±Π°Π²Π»ΡΡΡ ΠΈΠ·Π²Π΅ΡΡΠΊΠΎΠ²ΠΎΠ΅ ΡΠ΅ΡΡΠΎ ΠΈ ΠΏΠ΅ΡΠ΅ΠΌΠ΅ΡΠΈΠ²Π°ΡΡ. Π ΡΠΌΠ΅ΡΡ Π½Π΅Π±ΠΎΠ»ΡΡΠΈΠΌΠΈ ΠΏΠΎΡΡΠΈΡΠΌΠΈ Π΄ΠΎΠ±Π°Π²Π»ΡΡΡ Π²ΠΎΠ΄Ρ. ΠΠΎΡΠ»Π΅ ΠΊΠ°ΠΆΠ΄ΠΎΠΉ ΠΏΠΎΡΡΠΈΠΈ Π²ΠΎΠ΄Ρ ΡΠΌΠ΅ΡΡ ΠΏΠ΅ΡΠ΅ΠΌΠ΅ΡΠΈΠ²Π°ΡΡ. ΠΠ»Ρ ΠΏΡΠΎΠ²Π΅ΡΠΊΠΈ ΠΊΠ°ΡΠ΅ΡΡΠ²Π° ΡΠΎΡΡΠ°Π²Π° Π½Π΅Π±ΠΎΠ»ΡΡΡΡ ΠΏΠΎΡΡΠΈΡ ΡΠΌΠ΅ΡΠΈ ΡΠΆΠΈΠΌΠ°ΡΡ Π² ΡΡΠΊΠ΅ ΠΈ ΠΊΠ°ΡΠ°ΡΡ ΠΏΠΎ Π»Π°Π΄ΠΎΠ½ΠΈ. ΠΡΠ»ΠΈ ΠΊΠΎΠΌΠΎΠΊ Π½Π΅ ΡΠ°ΡΡΡΠΏΠ°Π΅ΡΡΡΒ ΠΈ Π½Π° ΠΏΠΎΠ²Π΅ΡΡ Π½ΠΎΡΡΠΈ ΠΎΡΡΡΡΡΡΠ²ΡΡΡ ΠΊΠ°ΠΏΠ΅Π»ΡΠΊΠΈ Π²ΠΎΠ΄Ρ, ΡΠΎ ΡΠΌΠ΅ΡΡ Ρ ΠΎΡΠΎΡΠ°Ρ. ΠΡΠ»ΠΈ ΠΊΠΎΠΌΠΎΠΊ ΡΠ°ΡΡΡΠΏΠ°Π΅ΡΡΡ, ΡΠΎ Π½ΡΠΆΠ½ΠΎ Π΄ΠΎΠ±Π°Π²ΠΈΡΡ Π·Π°ΠΏΠΎΠ»Π½ΠΈΡΠ΅Π»Ρ ΠΈ ΡΠΎΠΎΡΠ²Π΅ΡΡΡΠ²ΡΡΡΠ΅Π³ΠΎ ΠΊΠΎΠ»ΠΈΡΠ΅ΡΡΠ²Π° ΡΠ΅ΠΌΠ΅Π½ΡΠ°. ΠΡΠ»ΠΈ ΠΊΠ°ΡΠ΅ΡΡΠ²ΠΎ ΡΠΌΠ΅ΡΠΈ Ρ ΠΎΡΠΎΡΠ΅Π΅, ΡΠΎ ΠΎΠΏΠΈΠ»ΠΊΠΎΠ±Π΅ΡΠΎΠ½ ΠΌΠΎΠΆΠ½ΠΎ ΠΈΡΠΏΠΎΠ»ΡΠ·ΠΎΠ²Π°ΡΡ. Π‘ΡΡΠΎΠΈΡΡ ΡΡΠ΅Π½Ρ ΠΈΠ· ΠΎΠΏΠΈΠ»ΠΊΠΎΠ±Π΅ΡΠΎΠ½Π° ΠΌΠΎΠΆΠ½ΠΎ Π΄Π²ΡΠΌΡ ΡΠΏΠΎΡΠΎΠ±Π°ΠΌΠΈ:
- ΠΌΠΎΠ½ΠΎΠ»ΠΈΡΠ½ΡΠΌ ΡΠΏΠΎΡΠΎΠ±ΠΎΠΌ;
- Ρ ΠΏΠΎΠΌΠΎΡΡΡ Π±Π»ΠΎΠΊΠΎΠ².
Π‘ΡΡΠΎΠΈΡΠ΅Π»ΡΡΡΠ²ΠΎ ΠΌΠΎΠ½ΠΎΠ»ΠΈΡΠ½ΡΠΌ ΡΠΏΠΎΡΠΎΠ±ΠΎΠΌ ΡΡΠ΅Π±ΡΠ΅Ρ Π²ΠΎΠ·Π²Π΅Π΄Π΅Π½ΠΈΡ ΠΎΠΏΠ°Π»ΡΠ±ΠΊΠΈ, ΠΏΠΎΡΡΠΎΠΌΡ Π»ΡΡΡΠ΅ ΠΈΠ·Π³ΠΎΡΠΎΠ²ΠΈΡΡ ΠΈΠ· ΠΎΠΏΠΈΠ»ΠΊΠΎΠ±Π΅ΡΠΎΠ½Π° Π±Π»ΠΎΠΊΠΈ. Π Π»ΡΠ±ΠΎΠΌ ΡΠ»ΡΡΠ°Π΅ ΠΏΡΠΈΠ³ΠΎΡΠΎΠ²Π»Π΅Π½Π½ΡΠΉ ΠΎΠΏΠΈΠ»ΠΊΠΎΠ±Π΅ΡΠΎΠ½ ΡΠ»Π΅Π΄ΡΠ΅Ρ ΠΈΡΠΏΠΎΠ»ΡΠ·ΠΎΠ²Π°ΡΡ Π² ΡΠ΅ΡΠ΅Π½ΠΈΠ΅ 1,5 β 2 ΡΠ°ΡΠΎΠ², ΡΠ°ΠΊ ΠΊΠ°ΠΊ ΠΏΠΎ ΠΈΡΡΠ΅ΡΠ΅Π½ΠΈΠΈ ΡΡΠΎΠ³ΠΎ Π²ΡΠ΅ΠΌΠ΅Π½ΠΈ ΡΠΌΠ΅ΡΡ Π½Π°ΡΠ½Π΅Ρ ΡΠ²Π΅ΡΠ΄Π΅ΡΡ.Β ΠΠ°ΡΠΈΠ½Π°ΡΡ ΠΈΠ·Π³ΠΎΡΠΎΠ²Π»Π΅Π½ΠΈΠ΅ Π±Π»ΠΎΠΊΠΎΠ² ΠΈΠ· ΠΎΠΏΠΈΠ»ΠΊΠΎΠ±Π΅ΡΠΎΠ½Π° Π½ΡΠΆΠ½ΠΎ ΡΡΠ°Π·Ρ ΠΏΠΎΡΠ»Π΅ ΡΡΡΡΠΎΠΉΡΡΠ²Π° ΡΡΠ½Π΄Π°ΠΌΠ΅Π½ΡΠ°, Π»ΡΡΡΠ΅ Π²ΡΠ΅Π³ΠΎ Π² Π½Π°ΡΠ°Π»Π΅ ΠΈΡΠ½Ρ, ΡΠ°ΠΊ ΠΊΠ°ΠΊ Π΄ΠΎ ΠΏΠΎΠ»Π½ΠΎΠΉ Π³ΠΎΡΠΎΠ²Π½ΠΎΡΡΠΈ Π±Π»ΠΎΠΊΠΎΠ² ΡΠΉΠ΄ΡΡ Π½Π΅ ΠΌΠ΅Π½Π΅Π΅ 1,5 ΠΌΠ΅ΡΡΡΠ°. ΠΡΠ΅ΠΌΡ Π½Π° ΡΡΡΠΊΡ Π±Π»ΠΎΠΊΠΎΠ² Π·Π°Π²ΠΈΡΠΈΡ ΠΎΡ ΡΠ°Π·ΠΌΠ΅ΡΠΎΠ² Π±Π»ΠΎΠΊΠΎΠ²: Π΄Π»Ρ Π±Π»ΠΎΠΊΠΎΠ², ΡΠ°Π·ΠΌΠ΅Ρ ΠΊΠΎΡΠΎΡΡΡ Π½Π΅ ΠΏΡΠ΅Π²ΠΎΡΡ ΠΎΠ΄ΠΈΡ 100Β Γ100ΓΒ 200 ΠΌΠΌ, ΡΡΠ΅Π±ΡΠ΅ΡΡΡ ΠΌΠ΅Π½ΡΡΠ΅Π΅ Π²ΡΠ΅ΠΌΡ, Π½Π° ΡΡΡΠΊΡ Π±ΠΎΠ»ΡΡΠΈΡ Π±Π»ΠΎΠΊΠΎΠ² ΡΡΠ΅Π±ΡΠ΅ΡΡΡ Π±ΠΎΠ»ΡΡΠ΅ Π²ΡΠ΅ΠΌΠ΅Π½ΠΈ.
Π Π°Π·ΠΌΠ΅ΡΡ Π±Π»ΠΎΠΊΠΎΠ² ΡΡΠ°Π½Π΄Π°ΡΡΠ°ΠΌΠΈ Π½Π΅ ΠΎΠ³ΠΎΠ²Π°ΡΠΈΠ²Π°ΡΡΡΡ ΠΈ Π·Π°Π²ΠΈΡΡΡ ΠΎΡ ΡΠΎΠ»ΡΠΈΠ½Ρ Π²ΠΎΠ·Π²ΠΎΠ΄ΠΈΠΌΡΡ ΡΡΠ΅Π½, ΡΠΈΡΠΈΠ½Ρ ΠΏΡΠΎΡΡΠ΅Π½ΠΊΠΎΠ² ΠΈ ΠΏΡΠΎΡΠΌΠΎΠ². Π’ΠΎΠ»ΡΠΈΠ½Π° Π±Π»ΠΎΠΊΠ° ΠΎΠ±ΡΡΠ½ΠΎ ΡΠ°Π²Π½ΡΠ΅ΡΡΡ Π΄Π²ΡΠΌ ΡΠΎΠ»ΡΠΈΠ½Π°ΠΌ ΠΎΠ±ΡΠΊΠ½ΠΎΠ²Π΅Π½Π½ΠΎΠ³ΠΎ ΠΊΡΠ°ΡΠ½ΠΎΠ³ΠΎ ΠΊΠΈΡΠΏΠΈΡΠ° Ρ ΡΡΡΡΠΎΠΌ ΡΠΎΠ»ΡΠΈΠ½Ρ ΡΠ°ΡΡΠ²ΠΎΡΠ° ΠΌΠ΅ΠΆΠ΄Ρ Β ΡΠ»ΠΎΠΆΠ΅Π½Π½ΡΠΌΠΈ Π±Π»ΠΎΠΊΠ°ΠΌΠΈ ΠΈ ΡΠΎΡΡΠ°Π²Π»ΡΠ΅Ρ ΠΏΡΠΈΠΌΠ΅ΡΠ½ΠΎ 140 ΠΌΠΌ. Π’Π°ΠΊΠ°Ρ ΡΠΎΠ»ΡΠΈΠ½Π° Π±Π»ΠΎΠΊΠ° ΠΎΡΠ΅Π½Ρ ΡΠ΄ΠΎΠ±Π½Π°, ΡΠ°ΠΊ ΠΊΠ°ΠΊ ΠΏΡΠΈ ΠΊΠ»Π°Π΄ΠΊΠ΅ ΡΠ°ΡΡΠΎ ΠΈΡΠΏΠΎΠ»ΡΠ·ΡΠ΅ΡΡΡ ΠΎΠ±ΡΠΊΠ½ΠΎΠ²Π΅Π½Π½ΡΠΉ ΠΊΠΈΡΠΏΠΈΡ.
ΠΠΎΠ»ΡΡΠΈΠ΅ Π±Π»ΠΎΠΊΠΈ ΠΈΠ· ΠΎΠΏΠΈΠ»ΠΊΠΎΠ±Π΅ΡΠΎΠ½Π° ΡΠΎΡ Π½ΡΡ Π΄ΠΎΡΡΠ°ΡΠΎΡΠ½ΠΎ Π΄ΠΎΠ»Π³ΠΎ, ΠΏΠΎΡΡΠΎΠΌΡ Π΄Π»Ρ ΡΡΠΊΠΎΡΠ΅Π½ΠΈΡ ΠΏΡΠΎΡΠ΅ΡΡΠ° Π² Π±Π»ΠΎΠΊΠ°Ρ Π΄Π΅Π»Π°ΡΡΡΡ 3 β 4 ΠΎΡΠ²Π΅ΡΡΡΠΈΡ. ΠΡΠΎΠΌΠ΅ ΡΠΎΠ³ΠΎ, ΡΡΠΎ Π±Π»ΠΎΠΊ Π²ΡΡΠΎΡ Π½Π΅Ρ Π±ΡΡΡΡΠ΅Π΅, ΡΠ»ΡΡΡΠ°ΡΡΡΡ Π΅Π³ΠΎ ΡΠ΅ΠΏΠ»ΠΎΡΠ΅Ρ Π½ΠΈΡΠ΅ΡΠΊΠΈΠ΅ Ρ Π°ΡΠ°ΠΊΡΠ΅ΡΠΈΡΡΠΈΠΊΠΈ.
ΠΠΏΠΈΠ»ΠΊΠΎΠ±Π΅ΡΠΎΠ½Β ΠΌΠΎΠΆΠ½ΠΎ ΠΏΠΈΠ»ΠΈΡΡ, ΡΠ²Π΅ΡΠ»ΠΈΡΡ, ΠΊΡΠ΅ΠΏΠΈΡΡ Π³Π²ΠΎΠ·Π΄ΡΠΌΠΈ. ΠΠ΅Π΄ΠΎΡΡΠ°ΡΠΊΠΎΠΌ Π±ΠΎΠ»ΡΡΠΈΡ Π±Π»ΠΎΠΊΠΎΠ² ΠΈΠ· ΠΎΠΏΠΈΠ»ΠΊΠΎΠ±Π΅ΡΠΎΠ½Π° (Π±ΠΎΠ»Π΅Π΅ 200ΠΌΠΌ)Β Β ΡΠ²Π»ΡΠ΅ΡΡΡ ΡΠΎ, ΡΡΠΎ ΠΎΠ½ΠΈ ΠΌΠ΅Π΄Π»Π΅Π½Π½ΠΎ Π½Π°Π±ΠΈΡΠ°ΡΡ ΠΏΡΠΎΡΠ½ΠΎΡΡΡ. ΠΠ°ΡΠΎΡΠ½ΡΠ΅ ΠΏΡΠΎΡΠ½ΠΎΡΡΠ½ΡΠ΅ Ρ Π°ΡΠ°ΠΊΡΠ΅ΡΠΈΡΡΠΈΠΊΠΈ ΠΎΠΏΠΈΠ»ΠΊΠΎΠ±Π΅ΡΠΎΠ½ Π½Π°Π±ΠΈΡΠ°Π΅Ρ ΡΠΎΠ»ΡΠΊΠΎ ΡΠ΅ΡΠ΅Π· ΡΡΠΈ ΠΌΠ΅ΡΡΡΠ° ΠΏΠΎΡΠ»Π΅ ΠΈΠ·Π³ΠΎΡΠΎΠ²Π»Π΅Π½ΠΈΡ. ΠΠΏΠΈΠ»ΠΊΠΎΠ±Π΅ΡΠΎΠ½Π½ΡΠ΅ Π±Π»ΠΎΠΊΠΈ Π² ΡΠ΅ΡΠ΅Π½ΠΈΠ΅ Π΄Π»ΠΈΡΠ΅Π»ΡΠ½ΠΎΠ³ΠΎ Π²ΡΠ΅ΠΌΠ΅Π½ΠΈ Π»Π΅Π³ΠΊΠΎ Π΄Π΅ΡΠΎΡΠΌΠΈΡΡΡΡΡΡ, ΡΡΠΎ ΡΠΎΠΆΠ΅ ΡΠ²Π»ΡΠ΅ΡΡΡ Π½Π΅Π΄ΠΎΡΡΠ°ΡΠΊΠΎΠΌ. ΠΡΠΎΠΌΠ΅ ΡΠΎΠ³ΠΎ, ΠΎΠΏΠΈΠ»ΠΊΠΎΠ±Π΅ΡΠΎΠ½ Π½ΡΠΆΠ΄Π°Π΅ΡΡΡ Π²Β Π½Π°Π΄Π΅ΠΆΠ½ΠΎΠΉ Π²Π»Π°Π³ΠΎΠ·Π°ΡΠΈΡΠ΅ ΠΊΠ°ΠΊΒ Π²Π½ΡΡΡΠΈ, ΡΠ°ΠΊΒ ΠΈ ΡΠ½Π°ΡΡΠΆΠΈ.
Π€ΠΎΡΠΌΡ Π΄Π»Ρ Π±Π»ΠΎΠΊΠΎΠ² ΠΈΠ· ΠΎΠΏΠΈΠ»ΠΊΠΎΠ±Π΅ΡΠΎΠ½Π°
ΠΡΠΈ Π²ΡΡΡΡ
Π°Π½ΠΈΠΈ Π±Π»ΠΎΠΊΠΎΠ² ΠΏΡΠΎΠΈΡΡ
ΠΎΠ΄ΠΈΡ ΠΈΡ
ΡΡΡΡΠΊΠ°, ΠΏΠΎΡΡΠΎΠΌΡ ΡΠΎΡΠΌΡ Π΄Π΅Π»Π°ΡΡΡΡ ΠΏΡΠΈΠΌΠ΅ΡΠ½ΠΎ Π½Π° 10% Π±ΠΎΠ»ΡΡΠ΅ ΡΠ°Π·ΠΌΠ΅ΡΠΎΠ² Π±Π»ΠΎΠΊΠΎΠ². Π€ΠΎΡΠΌΡ ΠΌΠΎΠ³ΡΡ Π±ΡΡΡ ΡΠ°Π·ΡΠ΅ΠΌΠ½ΡΠ΅ (Π΄Π»Ρ ΠΊΡΡΠΏΠ½ΠΎΠ³Π°Π±Π°ΡΠΈΡΠ½ΡΡ
Π±Π»ΠΎΠΊΠΎΠ²) Π»ΠΈΠ±ΠΎ ΡΠΎΡΡΠΎΡΡΡ ΠΈΠ· Π½Π΅ΡΠΊΠΎΠ»ΡΠΊΠΈΡ
ΡΡΠ΅Π΅ΠΊ. ΠΠ»Ρ ΠΈΠ·Π³ΠΎΡΠΎΠ²Π»Π΅Π½ΠΈΡ ΡΠΎΡΠΌ ΠΎΠ±ΡΡΠ½ΠΎ ΠΈΡΠΏΠΎΠ»ΡΠ·ΡΡΡ Π΄ΠΎΡΠΊΠΈ ΡΠΎΠ»ΡΠΈΠ½ΠΎΠΉ 20 ΠΌΠΌ, ΠΏΠΎΠΊΡΡΡΡΠ΅ ΠΈΠ·Π½ΡΡΡΠΈ Π»ΠΈΡΡΠΎΠ²ΠΎΠΉ ΡΡΠ°Π»ΡΡ ΠΈΠ»ΠΈ ΠΏΠ»Π°ΡΡΠΈΠΊΠΎΠΌ. Π§ΡΠΎΠ±Ρ Π΄ΡΠ΅Π²Π΅ΡΠΈΠ½Π° Π½Π΅ Π²ΠΏΠΈΡΡΠ²Π°Π»Π° Π²Π»Π°Π³Ρ ΠΈΠ· ΡΠ°ΡΡΠ²ΠΎΡΠ° ΡΠΎΡΠΌΡ ΠΏΠΎΠΊΡΡΠ²Π°ΡΡ Π²Π½ΡΡΡΠΈ ΠΏΠΎΠΊΡΡΠ²Π°ΡΡ Π»ΠΈΡΡΠΎΠ²ΠΎΠΉ ΡΡΠ°Π»ΡΡ, ΠΏΠ»Π°ΡΡΠΈΠΊΠΎΠΌ ΠΈΠ»ΠΈ ΡΡΠ±Π΅ΡΠΎΠΈΠ΄ΠΎΠΌ. ΠΡΠΎΠΌΠ΅ ΡΠΎΠ³ΠΎ, ΠΈΠ· ΡΠΎΡΠΌΡ Ρ ΡΠ°ΠΊΠΈΠΌ ΠΏΠΎΠΊΡΡΡΠΈΠ΅ΠΌ Π»Π΅Π³ΡΠ΅ ΠΈΠ·Π²Π»Π΅ΠΊΠ°ΡΡ Π±Π»ΠΎΠΊΠΈ.
Π€ΠΎΡΠΌΡ ΡΠ»Π΅Π΄ΡΠ΅Ρ ΡΠ°Π·ΠΌΠ΅ΡΡΠΈΡΡ Π½Π° Β ΠΏΠΎΠ΄Π΄ΠΎΠ½Π°Ρ
, ΠΏΠΎΡΡΠΏΠ°Π½Π½ΡΡ
ΠΎΠΏΠΈΠ»ΠΊΠ°ΠΌΠΈ. Π ΠΊΠ°ΡΠ΅ΡΡΠ²Π΅ ΠΏΠΎΠ΄Π΄ΠΎΠ½Π° ΠΌΠΎΠΆΠ½ΠΎ ΠΈΡΠΏΠΎΠ»ΡΠ·ΠΎΠ²Π°ΡΡ ΠΌΠ΅ΡΠ°Π»Π»ΠΈΡΠ΅ΡΠΊΠΈΠ΅ ΠΈΠ»ΠΈ ΠΏΠ»Π°ΡΡΠΈΠΊΠΎΠ²ΡΠ΅ Π»ΠΈΡΡΡ. ΠΠΎΠ΄Π΄ΠΎΠ½ ΠΌΠΎΠΆΠ½ΠΎ ΡΠ΄Π΅Π»Π°ΡΡ ΠΈΠ· Π΄ΠΎΡΠΎΠΊ, Π½ΠΎ ΠΎΠ±ΡΠ·Π°ΡΠ΅Π»ΡΠ½ΠΎ ΠΎΠ±Π±ΠΈΡΡ Β ΡΡΠ±Π΅ΡΠΎΠΈΠ΄ΠΎΠΌ.Β ΠΡΠ»ΠΈ Π² Β Π±Π»ΠΎΠΊΠ΅ Π½Π΅ΠΎΠ±Ρ
ΠΎΠ΄ΠΈΠΌΠΎ ΡΠ΄Π΅Π»Π°ΡΡ ΠΎΡΠ²Π΅ΡΡΡΠΈΡ, ΡΠΎ Π² ΡΠΎΡΠΌΡ ΠΏΠΎΠΌΠ΅ΡΠ°ΡΡ Π΄Π΅ΡΠ΅Π²ΡΠ½Π½ΡΡ ΠΏΡΠΎΠ±ΠΊΡ, ΠΎΠ±Π΅ΡΠ½ΡΡΡΡ ΡΡΠ±Π΅ΡΠΎΠΈΠ΄ΠΎΠΌ, ΠΈΠ»ΠΈ ΠΏΠ»Π°ΡΡΠΈΠΊΠΎΠ²ΡΠ΅ Π±ΡΡΡΠ»ΠΊΠΈ Π½ΡΠΆΠ½ΠΎΠ³ΠΎ ΡΠ°Π·ΠΌΠ΅ΡΠ°.
ΠΠ»Ρ Π±ΠΎΠ»ΡΡΠΈΡ
Π±Π»ΠΎΠΊΠΎΠ² ΠΈΠ·Π³ΠΎΡΠ°Π²Π»ΠΈΠ²Π°ΡΡΡΡ ΡΠ°Π·Π±ΠΎΡΠ½ΡΠ΅ ΠΎΠ΄ΠΈΠ½Π°ΡΠ½ΡΠ΅ ΠΈΠ»ΠΈ Π΄Π²ΠΎΠΉΠ½ΡΠ΅ ΡΠΎΡΠΌΡ. ΠΠ½ΠΈ Π²ΡΠΏΠΎΠ»Π½ΡΡΡΡΡ Π² Π²ΠΈΠ΄Π΅ ΡΠ±ΠΈΡΡΡ
ΠΈΠ· Π΄ΠΎΡΠΎΠΊ ΡΡΠΈΠΊΠΎΠ². Π€ΠΎΡΠΌΡ Π»ΡΡΡΠ΅ Π΄Π΅Π»Π°ΡΡ ΡΠ°Π·ΡΠ΅ΠΌΠ½ΡΠΌΠΈ, ΡΡΠΎ ΠΏΠΎΠ·Π²ΠΎΠ»ΡΠ΅Ρ ΠΎΡΠ΅Π½Ρ Π±ΡΡΡΡΠΎ ΠΈΡ
ΡΠ°Π·Π±ΠΈΡΠ°ΡΡ ΠΈ ΡΠΎΠ±ΠΈΡΠ°ΡΡ. ΠΠ΅Π»Π°ΡΡΡΡ ΠΎΠ½ΠΈ ΠΈΠ· Π΄ΠΎΡΠΎΠΊ, ΡΠΎΠ»ΡΠΈΠ½Π° ΠΊΠΎΡΠΎΡΡΡ
ΡΠΎΡΡΠ°Π²Π»ΡΠ΅Ρ 20 ΠΌΠΈΠ»Π»ΠΈΠΌΠ΅ΡΡΠΎΠ². Π§Π°ΡΡΠΈ ΡΠ°Π·ΡΠ΅ΠΌΠ½ΠΎΠΉ ΠΊΠΎΠ½ΡΡΡΡΠΊΡΠΈΠΈ ΡΠΊΡΠ΅ΠΏΠ»ΡΡΡΡΡ ΠΏΡΠΈ ΠΏΠΎΠΌΠΎΡΠΈ ΡΡΠ°Π»ΡΠ½ΡΡ
ΡΡΠ΅ΡΠΆΠ½Π΅ΠΉ Π-ΠΎΠ±ΡΠ°Π·Π½ΠΎΠΉ ΡΠΎΡΠΌΡ, ΠΎΠ±Π»Π°Π΄Π°ΡΡΠΈΡ
ΡΠ΅Π·ΡΠ±ΠΎΠΉ Π8, Π½Π° ΠΊΠΎΡΠΎΡΡΡ Π½Π°ΠΊΡΡΡΠΈΠ²Π°Π΅ΡΡΡ Π±Π°ΡΠ°ΡΠΊΠΎΠ²Π°Ρ Π³Π°ΠΉΠΊΠ°.
Π€ΠΎΡΠΌΡ Π΄Π»Ρ Π½Π΅Π±ΠΎΠ»ΡΡΠΈΡ Π±Π»ΠΎΠΊΠΎΠ² ΠΌΠΎΠΆΠ½ΠΎ ΠΈΠ·Π³ΠΎΡΠΎΠ²ΠΈΡΡ ΡΠΎΡΡΠΎΡΡΠΈΠΌΠΈ ΠΈΠ· Π½Π΅ΡΠΊΠΎΠ»ΡΠΊΠΈΡ ΡΡΠ΅Π΅ΠΊ. Π Π°Π·ΠΌΠ΅Ρ ΡΡΠ΅Π΅ΠΊ ΠΌΠΎΠΆΠ΅Ρ Π±ΡΡΡ Π²ΡΠ±ΡΠ°Π½ Π² ΡΠΎΠΎΡΠ²Π΅ΡΡΡΠ²ΠΈΠΈ Ρ ΡΠΎΠ»ΡΠΈΠ½ΠΎΠΉ ΡΡΠ΅Π½. ΠΠΎΠ»ΠΈΡΠ΅ΡΡΠ²ΠΎ ΡΡΠ΅Π΅ΠΊ ΠΌΠΎΠΆΠ΅Ρ Π²Π°ΡΡΠΈΡΠΎΠ²Π°ΡΡΡΡ. ΠΡΠΈ ΡΠΎΡΠΌΡ ΡΠ²Π»ΡΡΡΡΡ ΠΏΠΎΠ»Π½ΠΎΡΡΡΡ ΡΠ°Π·Π±ΠΎΡΠ½ΡΠΌΠΈ.
Source: u-dachniki.ru
Π§ΠΈΡΠ°ΠΉΡΠ΅ ΡΠ°ΠΊΠΆΠ΅
ΠΠΈΡΠΏΠΈΡ ΠΈΠ· ΠΎΠΏΠΈΠ»ΠΎΠΊ: ΠΈΠ·Π³ΠΎΡΠΎΠ²Π»Π΅Π½ΠΈΠ΅, ΠΏΡΠΈΠΌΠ΅Π½Π΅Π½ΠΈΠ΅, Π²ΠΈΠ΄Ρ
ΠΡΠΈΠ³ΠΎΡΠΎΠ²ΠΈΡΡ ΠΊΠΈΡΠΏΠΈΡ ΠΈΠ· ΠΎΠΏΠΈΠ»ΠΎΠΊ ΠΈ ΡΠ΅ΠΌΠ΅Π½ΡΠ° ΡΠ°ΠΌΠΎΡΡΠΎΡΡΠ΅Π»ΡΠ½ΠΎ Π½Π΅ ΡΠΎΡΡΠ°Π²ΠΈΡ ΡΡΡΠ΄Π° Π΄Π°ΠΆΠ΅ Π½Π΅ΠΎΠΏΡΡΠ½ΡΠΌ ΡΡΡΠΎΠΈΡΠ΅Π»ΡΠΌ. ΠΠ»Ρ ΡΡΠΎΠ³ΠΎ ΠΏΠΎΠ½Π°Π΄ΠΎΠ±ΡΡΡΡ Π½Π΅ΠΎΠ±Ρ ΠΎΠ΄ΠΈΠΌΡΠ΅ ΡΠΎΡΡΠ°Π²Π»ΡΡΡΠΈΠ΅, ΠΎΠΏΠ°Π»ΡΠ±ΠΊΠ° ΠΈ Π²ΡΠ΅ΠΌΡ. Π’Π°ΠΊΠΎΠΉ ΠΌΠ°ΡΠ΅ΡΠΈΠ°Π» ΠΈΠΌΠ΅Π΅Ρ ΡΡΠ΄ ΠΏΡΠ΅ΠΈΠΌΡΡΠ΅ΡΡΠ², ΡΡΠ΅Π΄ΠΈ ΠΊΠΎΡΠΎΡΡΡ ΠΎΡΠ½ΠΎΠ²Π½ΡΠ΅ β ΡΠΊΠΎΠ»ΠΎΠ³ΠΈΡΠ½ΠΎΡΡΡ, Π΄Π΅ΡΠ΅Π²ΠΈΠ·Π½Π° ΠΈ Π½ΠΈΠ·ΠΊΠ°Ρ ΡΠ΅ΠΏΠ»ΠΎΠΏΡΠΎΠ²ΠΎΠ΄Π½ΠΎΡΡΡ. Π Π°Π·ΠΌΠ΅ΡΡ ΠΊΠΈΡΠΏΠΈΡΠΈΠΊΠ° ΡΠ΅Π³ΡΠ»ΠΈΡΡΡΡ ΡΠΎΠΎΡΠ½ΠΎΡΠ΅Π½ΠΈΡ ΠΈΠ½Π³ΡΠ΅Π΄ΠΈΠ΅Π½ΡΠΎΠ², Π·Π° ΡΡΠ΅Ρ ΡΠ΅Π³ΠΎ ΠΌΠΎΠ³ΡΡ ΠΈΠ·ΠΌΠ΅Π½ΡΡΡΡΡ ΠΈ Ρ Π°ΡΠ°ΠΊΡΠ΅ΡΠΈΡΡΠΈΠΊΠΈ. ΠΠΏΠΈΠ»ΠΊΠΎΠ±Π΅ΡΠΎΠ½ Π½Π΅ ΠΏΠΎΠ΄Ρ ΠΎΠ΄ΠΈΡ Π² Π²ΠΎΠ·Π²Π΅Π΄Π΅Π½ΠΈΠΈ ΠΌΠ½ΠΎΠ³ΠΎΡΡΠ°ΠΆΠ½ΡΡ ΡΠΎΠΎΡΡΠΆΠ΅Π½ΠΈΠΉ.
Π‘ΠΎΡΡΠ°Π² ΠΈ ΠΈΠ·Π³ΠΎΡΠΎΠ²Π»Π΅Π½ΠΈΠ΅
ΠΠ½Π³ΡΠ΅Π΄ΠΈΠ΅Π½ΡΡ ΠΈΠ·Π³ΠΎΡΠ°Π²Π»ΠΈΠ²Π°Π΅ΠΌΠΎΠ³ΠΎ ΠΌΠ΅ΡΠ°ΡΠΈΠ°Π»Π°:
- ΠΎΠΏΠΈΠ»ΠΊΠΈ;
- ΠΏΠ΅ΡΠΎΠΊ;
- Π²ΠΎΠ΄Π°;
- Ρ Π»ΠΎΡΠΈΡΡΡΠΉ ΠΊΠ°Π»ΡΡΠΈΠΉ;
- Π΄ΠΎΠ±Π°Π²ΠΊΠΈ;
- ΡΠ΅ΠΌΠ΅Π½Ρ.
ΠΡΠΎΠΏΠΎΡΡΠΈΠΈ ΡΠΊΠ»Π°Π΄ΡΠ²Π°ΡΡΡΡ, ΠΈΡΡ ΠΎΠ΄Ρ ΠΈΠ· ΠΌΠ°ΡΡΡ ΠΊΠΈΡΠΏΠΈΡΠ°. ΠΠ°ΡΡΡΠ΅Π½ΠΈΠ΅ ΡΠΎΠΎΡΠ½ΠΎΡΠ΅Π½ΠΈΡ ΡΠΎΡΡΠ°Π²Π½ΡΡ ΡΡ ΡΠ΄ΡΠ°Π΅Ρ ΡΡΠ½ΠΊΡΠΈΠΎΠ½Π°Π»ΡΠ½ΠΎΡΡΡ.
ΠΠ· ΡΠ΅ΠΌΠ΅Π½ΡΠ° Π»ΡΡΡΠ΅ ΠΏΡΠΈΠΌΠ΅Π½ΡΡΡ ΠΌΠ°ΡΠΊΡ Π-400, ΡΠΎΠ΅Π΄ΠΈΠ½ΡΡ Ρ ΠΏΠ΅ΡΠΊΠΎΠΌ ΡΡΠ΅Π΄Π½Π΅ΠΉ ΠΈΠ»ΠΈ ΠΊΡΡΠΏΠ½ΠΎΠΉ ΡΡΠ°ΠΊΡΠΈΠΈ. ΠΠ»Ρ ΠΈΠ·Π³ΠΎΡΠΎΠ²Π»Π΅Π½ΠΈΡ ΡΠ°ΠΊΠΎΠ³ΠΎ ΠΌΠ°ΡΠ΅ΡΠΈΠ°Π»Π° ΠΏΡΠΈΠΌΠ΅Π½ΠΈΠΌΡ ΠΎΠΏΠΈΠ»ΠΊΠΈ Ρ Π»ΡΠ±ΡΡ ΠΏΠΎΡΠΎΠ΄ Π΄Π΅ΡΠ΅Π²Π°. ΠΠ½ΠΈ Π²ΡΠ΄Π΅ΡΠΆΠΈΠ²Π°ΡΡΡΡ 2β3 ΠΌΠ΅ΡΡΡΠ° Π΄Π»Ρ Π²ΡΡ ΠΎΠ΄Π° ΡΠ°Ρ Π°ΡΠ° ΠΏΠΎΠ΄ Π½Π°Π²Π΅ΡΠΎΠΌ ΠΈΠ»ΠΈ ΠΊΠΎΠΌΠΏΠΎΠ½ΡΡΡΡΡ Ρ Π΄ΠΎΠ±Π°Π²ΠΊΠ°ΠΌΠΈ, ΡΡΠΎΠ±Ρ Π·Π°ΡΠΈΡΠΈΡΡ ΠΎΡ Π³Π½ΠΈΠ΅Π½ΠΈΡ ΠΈ ΠΏΠΎΡΡΠΈ. ΠΠ· Π΄ΠΎΠ±Π°Π²ΠΎΠΊ Π² ΡΠΎΡΡΠ°Π² Π²Ρ ΠΎΠ΄ΠΈΡ ΠΈΠ·Π²Π΅ΡΡΡ, ΡΡΠ»ΡΡΠ°Ρ Π°ΠΌΠΌΠΎΠ½ΠΈΡ ΠΈ ΠΆΠΈΠ΄ΠΊΠΎΠ΅ Π½Π°ΡΡΠΈΠ΅Π²ΠΎΠ΅ ΡΡΠ΅ΠΊΠ»ΠΎ. ΠΠ΅ΡΠ΅ΠΌΠ΅ΡΠΈΠ²Π°ΡΡΡΡ Ρ Π΄ΡΡΠ³ΠΈΠΌΠΈ ΡΠ»Π΅ΠΌΠ΅Π½ΡΠ°ΠΌΠΈ ΠΏΠΎΠ΄ ΠΎΡΠΊΡΡΡΡΠΌ Π½Π΅Π±ΠΎΠΌ 1 ΡΠ°Π· Π² 3 Π΄Π½Ρ. ΠΠ·Π±Π°Π»ΡΡΠ²Π°ΡΡΡΡ ΠΈ ΡΠ°ΡΡΡΡΡΡ Π² ΡΠΎΡΠΌΡ Π΄ΠΎ Π·Π°ΡΡΡΠ²Π°Π½ΠΈΡ. ΠΡ Π»Π΅Π³ΠΊΠΎ ΠΈΠ·Π³ΠΎΡΠΎΠ²ΠΈΡΡ ΡΠ²ΠΎΠΈΠΌΠΈ ΡΡΠΊΠ°ΠΌΠΈ.

ΠΠΏΠΈΠ»ΠΊΠΈ β Π²ΡΠΎΡΡΡΡΡΠ΅ Π΄Π»Ρ Π΄Π΅ΡΠ΅Π²ΠΎΠΎΠ±ΡΠ°Π±Π°ΡΡΠ²Π°ΡΡΠ΅ΠΉ ΠΎΡΡΠ°ΡΠ»ΠΈ. ΠΠ°ΡΠ°ΡΡΡΡ ΠΈΡ ΠΏΡΠΎΡΡΠΎ ΡΠΆΠΈΠ³Π°ΡΡ, Π° ΡΠ°ΠΊΠΎΠΉ ΡΠΏΠΎΡΠΎΠ± ΠΈΠ·Π³ΠΎΡΠΎΠ²Π»Π΅Π½ΠΈΡ ΡΡΡΠΎΠΈΡΠ΅Π»ΡΠ½ΠΎΠ³ΠΎ ΠΌΠ°ΡΠ΅ΡΠΈΠ°Π»Π° Π΄Π°Π΅Ρ ΡΡΡΡΡ Π²ΡΠΎΡΡΡ ΠΆΠΈΠ·Π½Ρ. Π‘ΡΡΠΎΠΈΡΠ΅Π»ΠΈ ΡΠ΅ΠΊΠΎΠΌΠ΅Π½Π΄ΡΡΡ ΠΏΡΠΈΠΌΠ΅Π½ΡΡΡ ΠΎΠΏΠΈΠ»ΠΊΠΈ ΠΈΠ· Π΄Π΅ΡΠ΅Π²ΡΠ΅Π² Ρ Π²ΠΎΠΉΠ½ΡΡ ΠΏΠΎΡΠΎΠ΄, ΡΠ°ΠΊ ΠΊΠ°ΠΊ ΠΎΠ½ΠΈ ΠΎΠ±Π»Π°Π΄Π°ΡΡ Π»ΡΡΡΠΈΠΌΠΈ Ρ Π°ΡΠ°ΠΊΡΠ΅ΡΠΈΡΡΠΈΠΊΠ°ΠΌΠΈ Π΄Π»Ρ Π²ΠΎΠ·Π²Π΅Π΄Π΅Π½ΠΈΡ ΠΆΠΈΠ»ΡΡ ΠΊΠΎΠ½ΡΡΡΡΠΊΡΠΈΠΉ. ΠΠ»Ρ ΠΏΡΠΈΠ³ΠΎΡΠΎΠ²Π»Π΅Π½ΠΈΡ ΡΡΡΠΆΠΊΠΈ ΠΈ Π±Π»ΠΎΠΊΠΎΠ² ΠΈΠ· ΠΎΠΏΠΈΠ»ΠΎΠΊ ΠΏΡΠΈΠΌΠ΅Π½ΡΡΡ ΡΠ°Π·Π»ΠΈΡΠ½ΡΠ΅ ΠΊΠΎΠ½ΡΠ΅Π½ΡΡΠ°ΡΠΈΠΈ ΠΌΠ°ΡΠ΅ΡΠΈΠ°Π»ΠΎΠ².
ΠΠ΅ΡΠ½ΡΡΡΡΡ ΠΊ ΠΎΠ³Π»Π°Π²Π»Π΅Π½ΠΈΡΠΠΈΠ΄Ρ ΠΊΠΈΡΠΏΠΈΡΠ° ΠΈΠ· ΠΎΠΏΠΈΠ»ΠΎΠΊ
ΠΠΎ ΠΏΡΠΈΠΌΠ΅Π½Π΅Π½ΠΈΡ Π²ΡΠ΄Π΅Π»ΡΡΡ ΡΡΠ΅Π½ΠΎΠ²ΡΠ΅ ΠΈ ΠΏΠ΅ΡΠ΅Π³ΠΎΡΠΎΠ΄ΠΎΡΠ½ΡΠ΅ Π±Π»ΠΎΠΊΠΈ. Π‘ ΠΏΠΎΠΌΠΎΡΡΡ ΠΏΠ΅ΡΠ²ΡΡ ΡΡΡΠΎΡΡ Π²Π½ΡΡΡΠ΅Π½Π½ΠΈΠ΅ ΠΈ Π½Π°ΡΡΠΆΠ½ΡΠ΅ ΡΡΠ΅Π½Ρ, Π²ΡΠΎΡΡΠ΅ ΠΏΡΠ΅Π΄Π½Π°Π·Π½Π°ΡΠ΅Π½Ρ Π΄Π»Ρ ΠΏΠ΅ΡΠ΅Π³ΠΎΡΠΎΠ΄ΠΎΠΊ. ΠΠ° ΡΠΎΡΠΌΠΎΠΉ ΠΊΠ»Π°ΡΡΠΈΡΠΈΡΠΈΡΡΡΡ Π½Π° ΠΏΠΎΠ»Π½ΠΎΡΠ΅Π»ΡΠ΅ (Π±Π΅Π· ΠΏΡΡΡΠΎΡ Π²Π½ΡΡΡΠΈ) ΠΈ ΠΏΡΡΡΠΎΡΠ΅Π»ΡΠ΅. Π’Π°ΠΊΠΆΠ΅ ΡΠ°ΠΊΠΎΠΉ ΠΌΠ°ΡΠ΅ΡΠΈΠ°Π» ΠΈΠΌΠ΅Π΅Ρ ΡΠ°Π·Π»ΠΈΡΠ½ΡΠΉ Π²Π΅Ρ ΠΈ ΡΠ°Π·ΠΌΠ΅ΡΠ½ΠΎΡΡΠΈ. ΠΡΡ ΠΎΠ΄Ρ ΠΈΠ· ΡΡΠΎΠ³ΠΎ ΠΌΠ΅Π½ΡΡΡΡΡ Ρ Π°ΡΠ°ΠΊΡΠ΅ΡΠΈΡΡΠΈΠΊΠΈ ΠΏΡΠΎΡΠ½ΠΎΡΡΠΈ, ΡΠ΅ΠΏΠ»ΠΎΠ²ΠΎΠ΄Π½ΠΎΡΡΠΈ, ΠΌΠΎΡΠΎΠ·ΠΎΡΡΠΎΠΉΠΊΠΎΡΡΠΈ, ΡΡΠ°Π΄ΠΊΠΈ, ΠΎΠ³Π½Π΅ΡΡΠΎΠΉΠΊΠΎΡΡΠΈ ΠΈ Π΄ΡΡΠ³ΠΈΡ Π²Π°ΠΆΠ½ΡΡ ΠΏΠ°ΡΠ°ΠΌΠ΅ΡΡΠΎΠ².
ΠΠ΅ΡΠ½ΡΡΡΡΡ ΠΊ ΠΎΠ³Π»Π°Π²Π»Π΅Π½ΠΈΡΠΡΠ΅ΠΈΠΌΡΡΠ΅ΡΡΠ²Π° ΠΈ Π½Π΅Π΄ΠΎΡΡΠ°ΡΠΊΠΈ
ΠΠΎΠ»ΠΎΠΆΠΈΡΠ΅Π»ΡΠ½ΡΠ΅ ΡΡΠΎΡΠΎΠ½Ρ ΡΡΡΠΎΠΈΡΠ΅Π»ΡΠ½ΠΎΠ³ΠΎ ΠΌΠ°ΡΠ΅ΡΠΈΠ°Π»Π°:

- Π½Π°ΡΡΡΠ°Π»ΡΠ½ΠΎΡΡΡ ΠΈ ΡΠΊΠΎΠ»ΠΎΠ³ΠΈΡΠ½ΠΎΡΡΡ;
- ΡΠΎΡ ΡΠ°Π½ΡΡΡ ΡΠ΅ΠΏΠ»ΠΎΡΡ Π΄ΠΎΠΌΠ° Π·Π° ΡΡΠ΅Ρ Π½ΠΈΠ·ΠΊΠΎΠΉ ΡΠ΅ΠΏΠ»ΠΎΠΏΡΠΎΠ²ΠΎΠ΄Π½ΠΎΡΡΠΈ;
- Π»Π΅Π³ΠΊΠΎΡΡΡ ΠΊΠΈΡΠΏΠΈΡΠ° ΠΈΠ· ΠΎΠΏΠΈΠ»ΠΊΠΎΠ±Π΅ΡΠΎΠ½Π° Π΄Π΅Π»Π°Π΅Ρ Π΅Π³ΠΎ ΡΠΊΠΎΠ½ΠΎΠΌΠΈΡΠ½ΡΠΌ Π² ΠΏΠ»Π°Π½Π΅ Π·Π°ΡΡΠ°Ρ Π½Π° ΡΡΡΠΎΠΈΡΠ΅Π»ΡΡΡΠ²ΠΎ ΡΡΠ½Π΄Π°ΠΌΠ΅Π½ΡΠ° ΠΈ Π² ΠΏΠ΅ΡΠ΅Π²ΠΎΠ·ΠΊΠ΅;
- ΠΏΠΎΠΆΠ°ΡΠΎΠ±Π΅Π·ΠΎΠΏΠ°ΡΠ½ΡΠΉ;
- ΡΡΠ°Π²Π½ΠΈΡΠ΅Π»ΡΠ½ΠΎ Π΄Π΅ΡΠ΅Π²ΡΠΉ;
- ΠΏΡΠΎΡΠ½ΡΠΉ;
- ΠΏΡΠΎΡΡ Π² ΠΏΡΠΈΠΌΠ΅Π½Π΅Π½ΠΈΠΈ.
ΠΠ΅Π³Π°ΡΠΈΠ²Π½ΡΠ΅ Ρ Π°ΡΠ°ΠΊΡΠ΅ΡΠΈΡΡΠΈΠΊΠΈ ΠΊΠΈΡΠΏΠΈΡΠ° ΠΈΠ· ΠΎΠΏΠΈΠ»ΠΎΠΊ β Π²ΡΡΠΎΠΊΠ°Ρ ΡΡΠ΅ΠΏΠ΅Π½Ρ ΠΏΠΎΠ³Π»ΠΎΡΠ΅Π½ΠΈΡ Π²Π»Π°Π³ΠΈ. ΠΠ»Ρ Π±ΠΎΡΡΠ±Ρ Ρ ΡΡΠΈΠΌ ΠΌΠΈΠ½ΡΡΠΎΠΌ ΠΌΠ°ΡΠ΅ΡΠΈΠ°Π»Π° ΠΏΡΠΎΠ²ΠΎΠ΄ΡΡ ΡΡΠ΄ Π²Π»Π°Π³ΠΎΠ·Π°ΡΠΈΡΠ½ΡΡ ΠΌΠ΅ΡΠΎΠΏΡΠΈΡΡΠΈΠΉ. ΠΡΠΈ ΠΌΠ½ΠΎΠ³ΠΎΡΡΠ°ΠΆΠ½ΠΎΠΌ ΡΡΡΠΎΠΈΡΠ΅Π»ΡΡΡΠ²Π΅ ΠΏΡΠΈΡ ΠΎΠ΄ΠΈΡΡΡ ΡΠ²Π΅Π»ΠΈΡΠΈΠ²Π°ΡΡ ΠΊΠΎΠ»ΠΈΡΠ΅ΡΡΠ²ΠΎ ΡΠ΅ΠΌΠ΅Π½ΡΠ°, Π²Ρ ΠΎΠ΄ΡΡΠ΅Π³ΠΎ Π² ΡΠΎΡΡΠ°Π², ΡΡΠΎ Π΄Π΅Π»Π°Π΅Ρ Π΅Π³ΠΎ Π±ΠΎΠ»Π΅Π΅ Π΄ΠΎΡΠΎΠ³ΠΈΠΌ ΠΈ ΠΌΠ΅Π½Π΅Π΅ ΡΠ΅ΠΏΠ»ΠΎΠ΅ΠΌΠΊΠΈΠΌ. ΠΠΎ Π²ΡΠ΅ΠΌΡ ΠΏΡΠΎΡΠ΅ΠΌΡ Π΄Π»Ρ ΠΎΠΏΠΈΠ»ΠΊΠΎΠ±Π΅ΡΠΎΠ½Π° Ρ Π°ΡΠ°ΠΊΡΠ΅ΡΠ½Π°Ρ ΡΠΈΠ»ΡΠ½Π°Ρ ΡΡΠ°Π΄ΠΊΠ°, ΠΈΠ·-Π·Π° ΡΡΠΎΠ³ΠΎ ΠΏΡΠΎΠ²ΠΎΠ΄ΠΈΡΡ ΠΎΡΠ΄Π΅Π»ΠΎΡΠ½ΡΠ΅ ΡΠ°Π±ΠΎΡΡ ΡΠ»ΠΎΠΆΠ½Π΅Π΅.
ΠΠ΅ΡΠ½ΡΡΡΡΡ ΠΊ ΠΎΠ³Π»Π°Π²Π»Π΅Π½ΠΈΡΠΠ±Π»Π°ΡΡΠΈ ΠΏΡΠΈΠΌΠ΅Π½Π΅Π½ΠΈΡ
Π‘ ΠΏΠΎΠΌΠΎΡΡΡ ΠΊΠΈΡΠΏΠΈΡΠ° ΠΈΠ· ΠΎΠΏΠΈΠ»ΠΎΠΊ Π²ΠΎΠ·Π²ΠΎΠ΄ΡΡ Π·Π΄Π°Π½ΠΈΡ ΡΠ°Π·Π½ΠΎΠΎΠ±ΡΠ°Π·Π½ΡΡ ΡΠΈΠΏΠΎΠ². Π ΡΠΎΠΌΡ ΠΆΠ΅ ΠΈΡ ΡΠ°ΡΡΠΎ ΠΏΡΠΈΠΌΠ΅Π½ΡΡΡ Π² ΡΡΠ΅ΠΏΠ»Π΅Π½ΠΈΠΈ ΡΠΆΠ΅ ΠΏΠΎΡΡΡΠΎΠ΅Π½Π½ΡΡ Π΄ΠΎΠΌΠΎΠ² Π»ΠΈΠ±ΠΎ Π² Π²ΠΎΠ·Π²Π΅Π΄Π΅Π½ΠΈΠΈ ΠΎΠ³ΡΠ°Π΄, ΡΡΠΎΠ»Π±ΠΎΠ². ΠΠ°ΡΠ°ΡΡΡΡ Ρ Π±Π»ΠΎΠΊΠΎΠ² ΡΡΡΠΎΡΡ ΠΌΠ°Π»ΠΎΡΡΠ°ΠΆΠ½ΡΠ΅ ΡΠΎΠΎΡΡΠΆΠ΅Π½ΠΈΡ ΠΈΠ»ΠΈ ΠΌΠ΅ΠΆΠΊΠΎΠΌΠ½Π°ΡΠ½ΡΠ΅ ΠΏΠ΅ΡΠ΅Π³ΠΎΡΠΎΠ΄ΠΊΠΈ. ΠΠ°ΡΠ΅ΡΠΈΠ°Π» ΠΏΠΎΠ΄Ρ ΠΎΠ΄ΠΈΡ Π΄Π»Ρ ΠΆΠΈΠ»ΡΡ ΠΈ Ρ ΠΎΠ·ΡΠΉΡΡΠ²Π΅Π½Π½ΡΡ ΠΏΠΎΠΌΠ΅ΡΠ΅Π½ΠΈΠΉ, Π΅ΡΠ΅ Ρ Π΅Π³ΠΎ ΠΏΠΎΠΌΠΎΡΡΡ ΡΡΡΠΎΡΡ Π³Π°ΡΠ°ΠΆΠΈ, ΡΠ°ΡΠ°ΠΈ, ΠΆΠΈΠ»ΡΠ΅ Π΄ΠΎΠΌΠ° Π»ΠΈΠ±ΠΎ Π΄ΡΡΠ³ΠΈΠ΅ ΠΏΠΎΠΌΠ΅ΡΠ΅Π½ΠΈΡ.
ΠΈΠ·Π³ΠΎΡΠΎΠ²Π»Π΅Π½ΠΈΠ΅ ΡΡΡΠΎΠΈΡΠ΅Π»ΡΠ½ΠΎΠ³ΠΎ Π±Π»ΠΎΠΊΠ°, ΡΠ°ΡΡΡΡ ΠΏΡΠΎΠΏΠΎΡΡΠΈΠΈ Π² Π΄ΠΎΠΌΠ°ΡΠ½ΠΈΡ ΡΡΠ»ΠΎΠ²ΠΈΡΡ
ΠΠ½ΠΎΠ³ΠΎΡΠΈΡΠ»Π΅Π½Π½ΡΠ΅ ΠΈΡΡΠ»Π΅Π΄ΠΎΠ²Π°Π½ΠΈΡ ΡΠΏΠ΅ΡΠΈΠ°Π»ΠΈΡΡΠΎΠ², ΠΊΠΎΡΠΎΡΡΠ΅ ΡΠ°Π±ΠΎΡΠ°ΡΡ Π² ΡΡΠ΅ΡΠ΅ ΡΡΡΠΎΠΈΡΠ΅Π»ΡΡΡΠ²Π°, Π΄ΠΎΠΊΠ°Π·Π°Π»ΠΈ, ΡΡΠΎ ΠΎΠΏΠΈΠ»ΠΊΠΎΠ±Π΅ΡΠΎΠ½ ΡΠ²Π»ΡΠ΅ΡΡΡ ΠΎΡΠ»ΠΈΡΠ½ΡΠΌ ΠΌΠ°ΡΠ΅ΡΠΈΠ°Π»ΠΎΠΌ Π΄Π»Ρ Π²ΠΎΠ·Π²Π΅Π΄Π΅Π½ΠΈΡ ΠΏΡΠΎΡΠ½ΡΡ
ΠΈ ΡΡΠΏΠ»ΡΡ
ΡΡΠ΅Π½. ΠΠΎΠΌΠΈΠΌΠΎ ΡΡΠΎΠ³ΠΎ, ΠΎΠ½ ΠΎΡΠ»ΠΈΡΠ°Π΅ΡΡΡ Π²ΡΡΠΎΠΊΠΈΠΌΠΈ ΡΠ΅ΠΏΠ»ΠΎΠΈΠ·ΠΎΠ»ΡΡΠΈΠΎΠ½Π½ΡΠΌΠΈ ΡΠ²ΠΎΠΉΡΡΠ²Π°ΠΌΠΈ, Ρ
ΠΎΡΠΎΡΠΈΠΌΠΈ ΡΠ°Π½ΠΈΡΠ°ΡΠ½ΠΎ-Π³ΠΈΠ³ΠΈΠ΅Π½ΠΈΡΠ΅ΡΠΊΠΈΠΌΠΈ ΠΏΠΎΠΊΠ°Π·Π°ΡΠ΅Π»ΡΠΌΠΈ ΠΈ ΠΎΠ³Π½Π΅ΡΡΠΎΠΉΠΊΠΎΡΡΡΡ. ΠΠ·Π³ΠΎΡΠΎΠ²ΠΈΡΡ ΠΊΠ°ΡΠ΅ΡΡΠ²Π΅Π½Π½ΡΠΉ ΠΎΠΏΠΈΠ»ΠΊΠΎΠ±Π΅ΡΠΎΠ½ ΡΠ²ΠΎΠΈΠΌΠΈ ΡΡΠΊΠ°ΠΌΠΈ Π½Π΅ ΡΠ°ΠΊ ΡΠΆ ΠΈ ΡΠ»ΠΎΠΆΠ½ΠΎ, Π³Π»Π°Π²Π½ΠΎΠ΅, ΠΏΡΠΈΠ΄Π΅ΡΠΆΠΈΠ²Π°ΡΡΡΡ ΠΏΡΠ°Π²ΠΈΠ»ΡΠ½ΠΎΠΉ ΠΏΡΠΎΠΏΠΎΡΡΠΈΠΈ ΠΈ ΡΠ΅Ρ
Π½ΠΎΠ»ΠΎΠ³ΠΈΠΈ ΠΏΡΠΎΠΈΠ·Π²ΠΎΠ΄ΡΡΠ²Π°.
ΠΡΠ°ΡΠΊΠΎΠ΅ ΠΎΠΏΠΈΡΠ°Π½ΠΈΠ΅ ΠΌΠ°ΡΠ΅ΡΠΈΠ°Π»Π°
ΠΠΏΠΈΠ»ΠΊΠΎΠ±Π΅ΡΠΎΠ½ ΠΎΡΠ½ΠΎΡΠΈΡΡΡ ΠΊ ΠΊΠ°ΡΠ΅Π³ΠΎΡΠΈΠΈ Π»ΡΠ³ΠΊΠΈΡ
ΠΌΠ°ΡΠ΅ΡΠΈΠ°Π»ΠΎΠ². ΠΡΠΎ ΡΠ²ΡΠ·Π°Π½ΠΎ Ρ ΡΠ΅ΠΌ, ΡΡΠΎ Π΄Π»Ρ Π΅Π³ΠΎ ΠΈΠ·Π³ΠΎΡΠΎΠ²Π»Π΅Π½ΠΈΡ ΠΈΡΠΏΠΎΠ»ΡΠ·ΡΡΡΡΡ ΠΎΠ±ΡΡΠ½ΡΠ΅ Π΄ΡΠ΅Π²Π΅ΡΠ½ΡΠ΅ ΠΎΠΏΠΈΠ»ΠΊΠΈ, ΠΏΠ΅ΡΠΎΠΊ ΠΈ ΡΠ΅ΠΌΠ΅Π½Ρ. ΠΠΏΠ΅ΡΠ²ΡΠ΅ ΡΡΠΎΡ ΠΌΠ°ΡΠ΅ΡΠΈΠ°Π» Π±ΡΠ» ΡΠ°Π·ΡΠ°Π±ΠΎΡΠ°Π½ Π΅ΡΡ Π² 1960 Π³ΠΎΠ΄Ρ, Π½ΠΎ ΡΠ²ΠΎΡ ΠΏΡΠΈΠΌΠ΅Π½Π΅Π½ΠΈΠ΅ ΠΏΠΎΠ»ΡΡΠΈΠ» ΡΠΎΠ»ΡΠΊΠΎ Π²Π½Π°ΡΠ°Π»Π΅ 90-Ρ
. ΠΠ°ΡΡΠ΅Ρ ΡΠΎΠ³ΠΎ, ΡΡΠΎ ΠΎΠΏΠΈΠ»ΠΊΠΎΠ±Π΅ΡΠΎΠ½ ΠΎΠ±Π»Π°Π΄Π°Π΅Ρ Π²ΡΡΠΎΠΊΠΈΠΌΠΈ ΡΠ°Π½ΠΈΡΠ°ΡΠ½ΠΎ-Π³ΠΈΠ³ΠΈΠ΅Π½ΠΈΡΠ΅ΡΠΊΠΈΠΌΠΈ ΠΏΠΎΠΊΠ°Π·Π°ΡΠ΅Π»ΡΠΌΠΈ, ΠΎΠ½ ΡΠΈΡΠΎΠΊΠΎ ΠΈΡΠΏΠΎΠ»ΡΠ·ΡΠ΅ΡΡΡ Π΄Π»Ρ Π²ΠΎΠ·Π²Π΅Π΄Π΅Π½ΠΈΡ ΡΠ°Π·Π»ΠΈΡΠ½ΡΡ
Π·Π΄Π°Π½ΠΈΠΉ ΠΈ ΡΡΡΠ΅ΠΆΠ΄Π΅Π½ΠΈΠΉ. ΠΠ»ΠΎΠΊΠΈ ΠΏΠΎΠ»ΡΡΠ°ΡΡΡΡ ΠΎΡΠ΅Π½Ρ ΠΊΡΠ΅ΠΏΠΊΠΈΠΌΠΈ, Π±Π»Π°Π³ΠΎΠ΄Π°ΡΡ ΡΠ΅ΠΌΡ ΠΈΡ
ΠΌΠΎΠΆΠ½ΠΎ ΡΠΌΠ΅Π»ΠΎ ΠΏΠΎΠ΄Π²Π΅ΡΠ³Π°ΡΡ Π»ΡΠ±ΡΠΌ ΠΌΠ΅Ρ
Π°Π½ΠΈΡΠ΅ΡΠΊΠΈΠΌ ΠΎΠ±ΡΠ°Π±ΠΎΡΠΊΠ°ΠΌ. ΠΠΎΠΆΠ½ΠΎ Π½Π΅ Π±ΠΎΡΡΡΡΡ, ΡΡΠΎ Π½Π° ΠΎΠΏΠΈΠ»ΠΊΠΎΠ±Π΅ΡΠΎΠ½Π΅ ΠΎΠ±ΡΠ°Π·ΡΡΡΡΡ ΡΡΠ΅ΡΠΈΠ½Ρ ΠΈΠ»ΠΈ ΡΠΊΠΎΠ»Ρ.
ΠΠ½ΠΎΠ³ΠΈΠ΅ ΠΏΠΎΡΡΠ΅Π±ΠΈΡΠ΅Π»ΠΈ ΡΠ°ΡΡΠΎ ΠΏΡΡΠ°ΡΡ ΡΡΠΎΡ ΠΌΠ°ΡΠ΅ΡΠΈΠ°Π» ΡΠΎ ΡΠΏΠ΅ΡΠΈΡΠΈΡΠ΅ΡΠΊΠΈΠΌΠΈ Π°ΡΠ±ΠΎΠ»ΠΈΡΠΎΠ²ΡΠΌΠΈ Π±Π»ΠΎΠΊΠ°ΠΌΠΈ. ΠΠΎ ΠΌΠ΅ΠΆΠ΄Ρ Π½ΠΈΠΌΠΈ Π΅ΡΡΡ Π³Π»Π°Π²Π½ΠΎΠ΅ ΠΎΡΠ»ΠΈΡΠΈΠ΅ β Π² Π½ΠΈΡ ΠΈΡΠΏΠΎΠ»ΡΠ·ΡΡΡΡΡ ΡΠΎΠ²Π΅ΡΡΠ΅Π½Π½ΠΎ ΡΠ°Π·Π½ΡΠ΅ Π·Π°ΠΏΠΎΠ»Π½ΠΈΡΠ΅Π»ΠΈ. Π‘ΡΠΎΠΈΡ ΠΎΡΠΌΠ΅ΡΠΈΡΡ, ΡΡΠΎ Π΄Π»Ρ Π°ΡΠ±ΠΎΠ»ΠΈΡΠ° ΠΏΡΠΈΠΌΠ΅Π½ΡΠ΅ΡΡΡ ΡΠΏΠ΅ΡΠΈΠ°Π»ΡΠ½Π°Ρ Π΄ΡΠΎΠ±Π»ΡΠ½Π°Ρ ΡΠ΅ΠΏΠΊΠ°, ΠΊΠΎΡΠΎΡΡΡ ΠΏΠΎΠ»ΡΡΠ°ΡΡ Π² ΡΠ΅Π·ΡΠ»ΡΡΠ°ΡΠ΅ ΡΡΠ°ΡΠ΅Π»ΡΠ½ΠΎΠ³ΠΎ ΠΈΠ·ΠΌΠ΅Π»ΡΡΠ΅Π½ΠΈΡ Π΄ΡΠ΅Π²Π΅ΡΠΈΠ½Ρ. Π ΡΠΎΡΡΠ°Π² ΡΠ°ΠΊΠΆΠ΅ Π²Ρ ΠΎΠ΄ΡΡ Π΄ΡΠΎΠ±Π»ΡΠ½ΡΠ΅ ΡΡΠ΅Π±Π»ΠΈ Ρ Π»ΠΎΠΏΡΠ°ΡΠ½ΠΈΠΊΠ° ΠΈ ΠΊΠ°ΠΌΡΡΠ°. Π Π²ΠΎΡ ΡΡΠΎ ΠΊΠ°ΡΠ°Π΅ΡΡΡ ΠΎΠΏΠΈΠ»ΠΊΠΎΠ±Π΅ΡΠΎΠ½Π°, ΡΠΎ Π΄Π»Ρ Π΅Π³ΠΎ ΠΈΠ·Π³ΠΎΡΠΎΠ²Π»Π΅Π½ΠΈΡ Π½ΡΠΆΠ΅Π½ ΡΠΎΠ»ΡΠΊΠΎ ΠΎΠΏΠΈΠ»ΠΊΠΎΠ²ΡΠΉ Π·Π°ΠΏΠΎΠ»Π½ΠΈΡΠ΅Π»Ρ.
ΠΡΠΎΠ±Π΅Π½Π½ΠΎΡΡΠΈ ΠΈΠ·Π³ΠΎΡΠΎΠ²Π»Π΅Π½ΠΈΡ
Π‘ΠΏΠ΅ΡΠΈΠ°Π»ΠΈΡΡΡ Π²ΡΠ΅Π³Π΄Π° Π°ΠΊΡΠ΅Π½ΡΠΈΡΡΡΡ Π²Π½ΠΈΠΌΠ°Π½ΠΈΠ΅ Π½Π° ΡΠΎΠΌ, ΡΡΠΎ Π΄Π»Ρ ΠΏΡΠΎΠΈΠ·Π²ΠΎΠ΄ΡΡΠ²Π° ΠΎΠΏΠΈΠ»ΠΊΠΎΠ±Π΅ΡΠΎΠ½Π° Π½Π΅ΠΎΠ±Ρ ΠΎΠ΄ΠΈΠΌΠΎ ΠΈΡΠΏΠΎΠ»ΡΠ·ΠΎΠ²Π°ΡΡ ΡΠΎΠ»ΡΠΊΠΎ ΠΊΠ°ΡΠ΅ΡΡΠ²Π΅Π½Π½ΡΠ΅ ΠΎΠΏΠΈΠ»ΠΊΠΈ ΡΠ΅Ρ ΠΏΠΎΡΠΎΠ΄ Π΄Π΅ΡΠ΅Π²Π°, ΠΊΠΎΡΠΎΡΡΠ΅ ΠΎΡΠ»ΠΈΡΠ°ΡΡΡΡ ΠΌΠΈΠ½ΠΈΠΌΠ°Π»ΡΠ½ΡΠΌ ΡΠΎΠ΄Π΅ΡΠΆΠ°Π½ΠΈΠ΅ΠΌ ΡΠ°Ρ Π°ΡΠΎΠ². ΠΠΏΡΠΈΠΌΠ°Π»ΡΠ½ΡΠΌΠΈ Π² ΡΡΠΎΠΌ ΡΠ»ΡΡΠ°Π΅ ΡΡΠΈΡΠ°ΡΡΡΡ:
- Π‘ΠΎΡΠ½Π°.
- ΠΠ»Ρ.
- Π’ΠΎΠΏΠΎΠ»Ρ.
- ΠΠ΅ΡΡΠ·Π°.
ΠΠ΅ΡΠΌΠΎΡΡΡ Π½Π° ΡΠΎ ΡΡΠΎ Π»ΠΈΡΡΠ²Π΅Π½Π½ΠΈΡΠ° ΠΎΡΠ»ΠΈΡΠ°Π΅ΡΡΡ Π²ΡΡΠΎΠΊΠΈΠΌΠΈ ΠΏΡΠΎΡΠ½ΠΎΡΡΠ½ΡΠΌΠΈ Ρ Π°ΡΠ°ΠΊΡΠ΅ΡΠΈΡΡΠΈΠΊΠ°ΠΌΠΈ, ΠΎΠ½Π° Π½Π°Ρ ΠΎΠ΄ΠΈΡΡΡ Π½Π° ΡΠ°ΠΌΠΎΠΌ ΠΏΠΎΡΠ»Π΅Π΄Π½Π΅ΠΌ ΠΌΠ΅ΡΡΠ΅ ΠΏΠΎ ΠΏΠΎΠΏΡΠ»ΡΡΠ½ΠΎΡΡΠΈ, ΡΠ°ΠΊ ΠΊΠ°ΠΊ Π² Π½Π΅ΠΉ ΡΠΎΠ΄Π΅ΡΠΆΠΈΡΡΡ Π²ΡΡΠΎΠΊΠΈΠΉ ΠΏΡΠΎΡΠ΅Π½Ρ ΡΠ°Ρ Π°ΡΠΎΠ². Π ΠΏΡΠΈΠΌΠ΅ΡΡ, Ρ Π΅Π»ΠΈ Π½Π°ΡΠ°Π»ΠΎ Π½Π°Π±ΠΎΡΠ° ΠΏΡΠΎΡΠ½ΠΎΡΡΠΈ Π½Π°ΡΠΈΠ½Π°Π΅ΡΡΡ ΡΠ΅ΡΠ΅Π· 14 Π΄Π½Π΅ΠΉ ΠΏΠΎΡΠ»Π΅ ΠΏΠΎΠ»Π½ΠΎΠ³ΠΎ Π²ΡΡΡΡ Π°Π½ΠΈΡ, Π° Π²ΠΎΡ ΠΎΠΊΠΎΠ½ΡΠ°Π½ΠΈΠ΅ ΡΡΠΎΠΉ ΠΏΡΠΎΡΠ΅Π΄ΡΡΡ ΠΏΡΠΎΠΈΡΡ ΠΎΠ΄ΠΈΡ Π½Π° ΡΠΎΡΠΎΠΊΠΎΠ²ΠΎΠΉ Π΄Π΅Π½Ρ ΠΏΠΎΡΠ»Π΅ ΠΈΠ·Π³ΠΎΡΠΎΠ²Π»Π΅Π½ΠΈΡ. Π§ΡΠΎ ΠΆΠ΅ ΠΊΠ°ΡΠ°Π΅ΡΡΡ Π»ΠΈΡΡΠ²Π΅Π½Π½ΠΈΡΡ, ΡΠΎ ΡΡΠΎΡ ΠΏΠ΅ΡΠΈΠΎΠ΄ Π΄Π»ΠΈΡΡΡ Π³ΠΎΡΠ°Π·Π΄ΠΎ Π΄ΠΎΠ»ΡΡΠ΅ β Π±ΠΎΠ»Π΅Π΅ 30 Π΄Π½Π΅ΠΉ Π΄Π»Ρ Π½Π°Π±ΠΎΡΠ° ΠΏΡΠΎΡΠ½ΠΎΡΡΠΈ ΠΈ 140 Π΄Π½Π΅ΠΉ Π΄Π»Ρ Π΅Π³ΠΎ ΠΎΠΊΠΎΠ½ΡΠ°Π½ΠΈΡ.
Π§ΡΠΎΠ±Ρ Π΄ΠΎΠ±ΠΈΡΡΡΡ ΠΆΠ΅Π»Π°Π΅ΠΌΠΎΠ³ΠΎ ΡΠ΅Π·ΡΠ»ΡΡΠ°ΡΠ°, Π²ΡΠ΅ ΡΠ°Π±ΠΎΡΡ ΠΏΠΎ ΠΎΠΏΠΈΠ»ΠΊΠΎΠ±Π΅ΡΠΎΠ½Ρ Π½ΡΠΆΠ½ΠΎ ΠΏΡΠΎΠ²ΠΎΠ΄ΠΈΡΡ Π² ΡΠ΅ΡΠ΅Π΄ΠΈΠ½Π΅ Π²Π΅ΡΠ½Ρ, ΡΡΠΎΠ±Ρ ΠΊ ΠΏΡΠΈΡ ΠΎΠ΄Ρ ΠΎΡΠ΅Π½ΠΈ Π²ΡΠ΅ Π±ΡΠ»ΠΎ Π³ΠΎΡΠΎΠ²ΠΎ. ΠΠ·-Π·Π° ΡΠΎΠ³ΠΎ, ΡΡΠΎ ΠΈΠ· ΠΎΠΏΠΈΠ»ΠΎΠΊ Π²ΡΠ΄Π΅Π»ΡΠ΅ΡΡΡ ΡΠΏΠ΅ΡΠΈΡΠΈΡΠ΅ΡΠΊΠΈΠΉ ΡΠ°Ρ Π°Ρ, ΡΠ°Π±ΠΎΡΠ°ΡΡ Ρ Π½ΠΈΠΌΠΈ Π½ΡΠΆΠ½ΠΎ ΠΈΡΠΊΠ»ΡΡΠΈΡΠ΅Π»ΡΠ½ΠΎ Π½Π° ΡΠ²Π΅ΠΆΠ΅ΠΌ Π²ΠΎΠ·Π΄ΡΡ Π΅. ΠΠ΅ ΡΡΠΎΠΈΡ Π·Π°Π±ΡΠ²Π°ΡΡ ΠΎ ΡΠΎΠΌ, ΡΡΠΎ ΠΎΠΏΠΈΠ»ΠΊΠΈ ΠΎΠ±ΡΠ·Π°ΡΠ΅Π»ΡΠ½ΠΎ Π½ΡΠΆΠ½ΠΎ ΠΏΠΎΠ»ΠΈΡΡ ΡΠΈΡΡΠΎΠΉ Π²ΠΎΠ΄ΠΎΠΉ, ΡΡΠΎΠ±Ρ ΡΠΌΡΡΡ Π²ΡΠ΅ ΠΈΠΌΠ΅ΡΡΠΈΠ΅ΡΡ ΠΎΡΡΠ°ΡΠΊΠΈ ΡΠ°ΡΠΏΠ°Π΄Π° ΡΠ°Ρ Π°ΡΠ°.
Π‘ΠΎΡΡΠ°Π² ΡΠΌΠ΅ΡΠΈ
ΠΠΌΠ΅Π½Π½ΠΎ ΠΎΡ ΡΠΎΠ³ΠΎ, Π½Π°ΡΠΊΠΎΠ»ΡΠΊΠΎ ΠΏΡΠ°Π²ΠΈΠ»ΡΠ½ΠΎ ΠΏΠΎΠ΄ΠΎΠ±ΡΠ°Π½ ΠΊΠ°ΠΆΠ΄ΡΠΉ ΠΊΠΎΠΌΠΏΠΎΠ½Π΅Π½Ρ, Π·Π°Π²ΠΈΡΠΈΡ ΠΊΠ°ΡΠ΅ΡΡΠ²ΠΎ Π±ΡΠ΄ΡΡΠ΅Π³ΠΎ ΠΌΠ°ΡΠ΅ΡΠΈΠ°Π»Π°. ΠΡΠΏΠΎΠ»ΡΠ·ΡΠ΅ΠΌΡΠ΅ Π±Π»ΠΎΠΊΠΈ Π΄ΠΎΠ»ΠΆΠ½Ρ Π±ΡΡΡ ΠΏΡΠΎΡΠ½ΡΠΌΠΈ ΠΈ Π΄ΠΎΠ»Π³ΠΎΠ²Π΅ΡΠ½ΡΠΌΠΈ. ΠΠ½Π΅ Π·Π°Π²ΠΈΡΠΈΠΌΠΎΡΡΠΈ ΠΎΡ ΠΌΠ°ΡΠΊΠΈ ΠΎΠΏΠΈΠ»ΠΊΠΎΠ±Π΅ΡΠΎΠ½Π°, Π² Π΅Π³ΠΎ ΡΠΎΡΡΠ°Π² Π΄ΠΎΠ»ΠΆΠ½Ρ Π²Ρ ΠΎΠ΄ΠΈΡΡ ΡΠ»Π΅Π΄ΡΡΡΠΈΠ΅ ΠΊΠΎΠΌΠΏΠΎΠ½Π΅Π½ΡΡ:
- ΠΠ΅ΡΠΎΠΊ.
- Π¦Π΅ΠΌΠ΅Π½Ρ.
- ΠΠΏΠΈΠ»ΠΊΠΈ.
- ΠΠ°ΡΡΠ½Π°Ρ ΠΈΠ·Π²Π΅ΡΡΡ.
Π Π°Π·Π½ΠΈΡΠ° Π² ΠΏΡΠΎΠΏΠΎΡΡΠΈΠΈ Π·Π°Π²ΠΈΡΠΈΡ ΡΠΎΠ»ΡΠΊΠΎ ΠΎΡ ΡΠΎΠΎΡΠ½ΠΎΡΠ΅Π½ΠΈΡ ΠΊΠΎΠΌΠΏΠΎΠ½Π΅Π½ΡΠΎΠ² ΡΠΌΠ΅ΡΠΈ. Π‘ΡΡΠΎΠΈΡΠ΅Π»ΠΈ ΠΎΡΠΌΠ΅ΡΠ°ΡΡ, ΡΡΠΎ Π±Π»ΠΎΠΊΠΈ Ρ Π±ΠΎΠ»ΡΡΠΈΠΌ ΡΠΎΠ΄Π΅ΡΠΆΠ°Π½ΠΈΠ΅ΠΌ ΡΠ΅ΠΌΠ΅Π½ΡΠ° Π±ΠΎΠ»ΡΡΠ΅ Π²ΡΠ΅Π³ΠΎ ΠΏΠΎΠ΄Ρ
ΠΎΠ΄ΡΡ Π΄Π»Ρ Π²ΠΎΠ·Π²Π΅Π΄Π΅Π½ΠΈΡ ΠΌΠ½ΠΎΠ³ΠΎΡΡΠΎΠ²Π½Π΅Π²ΡΡ
Π½Π΅ΠΆΠΈΠ»ΡΡ
Π·Π΄Π°Π½ΠΈΠΉ. Π’Π°ΠΊΠ°Ρ ΡΠ΅Π½Π΄Π΅Π½ΡΠΈΡ ΠΎΠ±ΡΡΡΠ½ΡΠ΅ΡΡΡ ΡΠ΅ΠΌ, ΡΡΠΎ ΠΌΠ΅Π½ΡΠ΅ΡΡΡ ΠΊΠΎΡΡΡΠΈΡΠΈΠ΅Π½Ρ ΡΠ΅ΠΏΠ»ΠΎΠΏΡΠΎΠ²ΠΎΠ΄Π½ΠΎΡΡΠΈ ΠΌΠ°ΡΠ΅ΡΠΈΠ°Π»Π°, Π° ΡΡΠΎ ΡΡΠ΅Π²Π°ΡΠΎ Π±ΠΎΠ»ΡΡΠΈΠΌΠΈ ΡΠ°ΡΡ
ΠΎΠ΄Π°ΠΌΠΈ Π½Π° ΠΎΡΠΎΠΏΠ»Π΅Π½ΠΈΠ΅. ΠΡΠ»ΠΈ ΠΌΠ°ΡΡΠ΅Ρ ΡΠ΅ΡΠΈΡ ΠΈΡΠΏΠΎΠ»ΡΠ·ΠΎΠ²Π°ΡΡ ΡΠ΅ΠΌΠ΅Π½Ρ Π10, ΡΠΎ ΠΊΠΎΡΡΡΠΈΡΠΈΠ΅Π½Ρ Π±ΡΠ΄Π΅Ρ ΡΠ°Π²Π΅Π½ 0.21, ΡΡΠΎ ΠΎΡΠ΅Π½Ρ Ρ
ΠΎΡΠΎΡΠΎ ΠΏΡΠΈ Π»ΡΠ±ΡΡ
ΡΡΠ»ΠΎΠ²ΠΈΡΡ
.
ΠΠ»Ρ ΠΌΠ°ΡΠΊΠΈ ΡΠ΅ΠΌΠ΅Π½ΡΠ° Π15 ΡΡΠΎΡ ΠΏΠΎΠΊΠ°Π·Π°ΡΠ΅Π»Ρ ΡΠΎΡΡΠ°Π²Π»ΡΠ΅Ρ 0.24, ΡΡΠΎ ΠΎΠ±ΡΡΠ»ΠΎΠ²Π»Π΅Π½ΠΎ Π½Π΅Π·Π½Π°ΡΠΈΡΠ΅Π»ΡΠ½ΡΠΌΠΈ ΠΈΠ·ΠΌΠ΅Π½Π΅Π½ΠΈΡΠΌΠΈ Π² ΡΡΠ΅Π±ΠΎΠ²Π°Π½ΠΈΡΡ ΠΊ ΠΏΡΠΎΡΠ½ΠΎΡΡΠΈ. ΠΠΌΠ΅Π½Π½ΠΎ ΠΏΠΎΡΡΠΎΠΌΡ ΠΌΠ°ΡΡΠ΅ΡΡ ΠΏΠΎΡΡΠ΅Π±ΡΠ΅ΡΡΡ Π³ΠΎΡΠ°Π·Π΄ΠΎ Π±ΠΎΠ»ΡΡΠ΅ ΡΠ΅ΠΌΠ΅Π½ΡΠ°, ΡΡΠΎΠ±Ρ ΠΏΠΎΡΡΡΠΎΠΈΡΡ ΠΊΠ°ΡΠ΅ΡΡΠ²Π΅Π½Π½ΡΠΉ Π΄Π²ΡΡ ΡΡΠ°ΠΆΠ½ΡΠΉ Π΄ΠΎΠΌ. Π§ΡΠΎ ΠΊΠ°ΡΠ°Π΅ΡΡΡ ΠΌΠ°ΡΠΊΠΈ ΡΠ΅ΠΌΠ΅Π½ΡΠ° Π25, ΡΠΎ Π΅Π³ΠΎ ΠΊΠΎΡΡΡΠΈΡΠΈΠ΅Π½Ρ ΡΠ²Π΅Π»ΠΈΡΠΈΠ²Π°Π΅ΡΡΡ Π΄ΠΎ 0.39, Π° ΡΡΠΎ ΡΠΆΠ΅ Π² Π΄Π²Π° ΡΠ°Π·Π° Π±ΠΎΠ»ΡΡΠ΅, Π½Π΅ΠΆΠ΅Π»ΠΈ Ρ Π±Π»ΠΎΠΊΠ° Π10. ΠΠΎΠ½Π΅ΡΠ½ΠΎ, ΡΠ°ΠΊΠΎΠΉ ΠΎΠΏΠΈΠ»ΠΊΠΎΠ±Π΅ΡΠΎΠ½ ΠΏΠΎΠ»ΡΡΠ°Π΅ΡΡΡ Π±ΠΎΠ»Π΅Π΅ Ρ ΠΎΠ»ΠΎΠ΄Π½ΡΠΌ, Π½ΠΎ ΠΎΠ½ ΠΎΡΠ»ΠΈΡΠ½ΠΎ ΠΏΠΎΠ΄Ρ ΠΎΠ΄ΠΈΡ Π΄Π»Ρ Π²ΠΎΠ·Π²Π΅Π΄Π΅Π½ΠΈΡ Π±ΠΎΠ»ΡΡΠΈΡ Π·Π΄Π°Π½ΠΈΠΉ.
ΠΡΠ΅ΠΈΠΌΡΡΠ΅ΡΡΠ²Π° ΠΈ Π½Π΅Π΄ΠΎΡΡΠ°ΡΠΊΠΈ
ΠΠ°ΠΆΠ΄ΡΠΉ ΡΠΏΠ΅ΡΠΈΠ°Π»ΠΈΡΡ Π·Π½Π°Π΅Ρ, ΡΡΠΎ ΠΏΠ΅ΡΠ΅Π΄ ΡΠ΅ΠΌ ΠΈΡΠΏΠΎΠ»ΡΠ·ΠΎΠ²Π°Π½ΠΈΠ΅ΠΌ Π»ΡΠ±ΠΎΠ³ΠΎ ΠΌΠ°ΡΠ΅ΡΠΈΠ°Π»Π° Π½Π΅ΠΎΠ±Ρ ΠΎΠ΄ΠΈΠΌΠΎ ΠΎΠ·Π½Π°ΠΊΠΎΠΌΠΈΡΡΡΡ ΡΠΎ Π²ΡΠ΅ΠΌΠΈ Π΅Π³ΠΎ ΠΏΠ»ΡΡΠ°ΠΌΠΈ ΠΈ ΠΌΠΈΠ½ΡΡΠ°ΠΌΠΈ. ΠΠΎΠΌΠΈΠΌΠΎ ΡΡΠΎΠ³ΠΎ, ΡΡΠΎΠ±Ρ ΠΈΠ·Π³ΠΎΡΠΎΠ²ΠΈΡΡ ΡΡΡΠΎΠΈΡΠ΅Π»ΡΠ½ΡΠ΅ Π±Π»ΠΎΠΊΠΈ ΠΈΠ· ΠΎΠΏΠΈΠ»ΠΎΠΊ ΡΠ²ΠΎΠΈΠΌΠΈ ΡΡΠΊΠ°ΠΌΠΈ, Π½ΡΠΆΠ½ΠΎ ΡΡΠ΅ΡΡΡ ΠΊΠ°ΠΆΠ΄ΡΠΉ Π½ΡΠ°Π½Ρ. ΠΠ°ΡΠΈΠ½Π°ΡΡ Π·Π½Π°ΠΊΠΎΠΌΡΡΠ²ΠΎ Ρ ΠΎΠΏΠΈΠ»ΠΊΠΎΠ±Π΅ΡΠΎΠ½ΠΎΠΌ Π»ΡΡΡΠ΅ Π²ΡΠ΅Π³ΠΎ Ρ Π΅Π³ΠΎ ΡΠΈΠ»ΡΠ½ΡΡ ΡΡΠΎΡΠΎΠ½.
ΠΡΠ΅ΠΈΠΌΡΡΠ΅ΡΡΠ²Π°:
Π ΠΏΠΎΠ»ΠΎΠΆΠΈΡΠ΅Π»ΡΠ½ΡΠΌ Ρ Π°ΡΠ°ΠΊΡΠ΅ΡΠΈΡΡΠΈΠΊΠ°ΠΌ ΠΌΠΎΠΆΠ½ΠΎ ΠΎΡΠ½Π΅ΡΡΠΈ Ρ ΠΎΡΠΎΡΡΡ ΡΡΡΠΎΠΉΡΠΈΠ²ΠΎΡΡΡ ΠΊ Π½ΠΈΠ·ΠΊΠΈΠΌ ΡΠ΅ΠΌΠΏΠ΅ΡΠ°ΡΡΡΠ°ΠΌ. ΠΠΏΠΈΠ»ΠΊΠΎΠ±Π»ΠΎΠΊ ΠΌΠΎΠΆΠ΅Ρ Π²ΡΠ΄Π΅ΡΠΆΠ°ΡΡ Π΄ΠΎ 50 ΡΠΈΠΊΠ»ΠΎΠ² ΡΠΈΠ»ΡΠ½ΠΎΠΉ Π·Π°ΠΌΠΎΡΠΎΠ·ΠΊΠΈ.
- ΠΠ΅Π²ΡΡΠΎΠΊΠ°Ρ ΡΡΠΎΠΈΠΌΠΎΡΡΡ ΡΠ°ΡΡ ΠΎΠ΄Π½ΡΡ ΠΌΠ°ΡΠ΅ΡΠΈΠ°Π»ΠΎΠ².
- ΠΡΡΠΎΠΊΠΈΠΉ ΠΏΡΠΎΡΠ΅Π½Ρ ΡΠ΅ΠΏΠ»ΠΎΡΡΡΠ΅ΠΊΡΠΈΠ²Π½ΠΎΡΡΠΈ. ΠΠ°ΡΠ΅ΡΡΠ²Π΅Π½Π½ΡΠΉ Π±Π»ΠΎΠΊ ΠΈΠ· ΠΎΠΏΠΈΠ»ΠΎΠΊ ΡΡΠΈΡΠ°Π΅ΡΡΡ Π»ΠΈΠ΄Π΅ΡΠΎΠΌ Π½Π° ΡΠΎΠ²ΡΠ΅ΠΌΠ΅Π½Π½ΠΎΠΌ ΡΡΡΠΎΠΈΡΠ΅Π»ΡΠ½ΠΎΠΌ ΡΡΠ½ΠΊΠ΅. ΠΡΠ»ΠΈ ΡΡΠ°Π²Π½ΠΈΠ²Π°ΡΡ ΡΡΠΎΡ ΠΌΠ°ΡΠ΅ΡΠΈΠ°Π» Ρ ΠΏΡΠ΅Π΄ΡΡΠ°Π²ΠΈΡΠ΅Π»ΡΠΌΠΈ Π»ΡΠ³ΠΊΠΈΡ Π±Π΅ΡΠΎΠ½ΠΎΠ², ΡΠΎ ΠΏΡΠ΅Π²Π·ΠΎΠΉΡΠΈ ΠΎΠΏΠΈΠ»ΠΊΠΎΠ±Π΅ΡΠΎΠ½ ΠΌΠΎΠΆΠ΅Ρ ΡΠΎΠ»ΡΠΊΠΎ ΠΏΠΎΠ»ΠΈΡΡΠΈΡΠΎΠ»Π±Π΅ΡΠΎΠ½. Π‘ΡΠΎΠΈΡ ΠΎΡΠΌΠ΅ΡΠΈΡΡ, ΡΡΠΎ ΠΊΠΎΡΡΡΠΈΡΠΈΠ΅Π½Ρ Π±Π»ΠΎΠΊΠ° ΠΈΠ· ΠΎΠΏΠΈΠ»ΠΎΠΊ Π²Π°ΡΡΠΈΡΡΠ΅ΡΡΡ ΠΎΡ 0.07 Π΄ΠΎ 0.20.
- ΠΠ°ΡΠ΅ΡΠΈΠ°Π» Π»Π΅Π³ΠΊΠΎ ΠΏΠΎΠ΄Π΄Π°ΡΡΡΡ ΠΎΠ±ΡΠ°Π±ΠΎΡΠΊΠ΅, Π° Π΅Π³ΠΎ Π³Π°Π±Π°ΡΠΈΡΡ ΡΡΠ°Π²Π½ΠΈΡΠ΅Π»ΡΠ½ΠΎ Π²Π΅Π»ΠΈΠΊΠΈ. ΠΠΌΠ΅Π½Π½ΠΎ ΡΡΠΈ ΡΠ°ΠΊΡΡ ΡΠΊΠ°Π·ΡΠ²Π°ΡΡ Π½Π° ΡΠΎ, ΡΡΠΎ Ρ ΠΏΠΎΠΌΠΎΡΡΡ ΡΡΠΈΡ Π±Π»ΠΎΠΊΠΎΠ² ΠΌΠΎΠΆΠ½ΠΎ Π²ΠΎΠ·Π²Π΅ΡΡΠΈ Π½Π΅ΠΎΠ±Ρ ΠΎΠ΄ΠΈΠΌΡΠ΅ Π·Π΄Π°Π½ΠΈΡ Π·Π° ΠΊΠΎΡΠΎΡΠΊΠΈΠΉ ΡΡΠΎΠΊ.
- Π ΡΠΎΡΡΠ°Π² ΠΎΠΏΠΈΠ»ΠΊΠΎΠ±Π»ΠΎΠΊΠΎΠ² Π²Ρ ΠΎΠ΄ΡΡ ΡΠΎΠ»ΡΠΊΠΎ ΡΠΊΠΎΠ»ΠΎΠ³ΠΈΡΠ΅ΡΠΊΠΈΠ΅ ΠΌΠ°ΡΠ΅ΡΠΈΠ°Π»Ρ, ΠΊΠΎΡΠΎΡΡΠ΅ ΠΏΠΎΠ»Π½ΠΎΡΡΡΡ Π±Π΅Π·ΠΎΠΏΠ°ΡΠ½Ρ ΠΊΠ°ΠΊ Π΄Π»Ρ Π»ΡΠ΄Π΅ΠΉ, ΡΠ°ΠΊ ΠΈ Π΄Π»Ρ ΠΎΠΊΡΡΠΆΠ°ΡΡΠ΅ΠΉ ΡΡΠ΅Π΄Ρ.
- Π₯ΠΎΡΠΎΡΠ°Ρ Π·Π°ΡΠΈΡΠ° ΠΎΡ ΠΏΠΎΡΡΠΎΡΠΎΠ½Π½ΠΈΡ Π·Π²ΡΠΊΠΎΠ².
- ΠΠ°ΡΡΡΡ ΡΠΎΠ³ΠΎ, ΡΡΠΎ Π² Π±Π»ΠΎΠΊΠ΅ ΡΠΎΠ΄Π΅ΡΠΆΠΈΡΡΡ ΡΠ΅ΠΌΠ΅Π½Ρ, ΠΎΠ½ Π½Π΅ ΠΏΠΎΠ΄Π²Π΅ΡΠΆΠ΅Π½ Π²Π½Π΅Π·Π°ΠΏΠ½ΠΎΠΌΡ Π²ΠΎΠ·Π³ΠΎΡΠ°Π½ΠΈΡ.
- ΠΠ½ΠΎΠ³ΠΈΠ΅ ΡΠΏΠ΅ΡΠΈΠ°Π»ΠΈΡΡΡ ΡΡΠ²Π΅ΡΠΆΠ΄Π°ΡΡ, ΡΡΠΎ ΠΈΠ·Π³ΠΎΡΠΎΠ²Π»Π΅Π½ΠΈΠ΅ ΠΎΠΏΠΈΠ»ΠΊΠΎΠ±Π΅ΡΠΎΠ½Π½ΡΡ Π±Π»ΠΎΠΊΠΎΠ² Π² Π΄ΠΎΠΌΠ°ΡΠ½ΠΈΡ ΡΡΠ»ΠΎΠ²ΠΈΡΡ Π½Π΅ ΠΈΠΌΠ΅Π΅Ρ ΠΊΠ°ΠΊΠΈΡ -Π»ΠΈΠ±ΠΎ ΡΠ»ΠΎΠΆΠ½ΠΎΡΡΠ΅ΠΉ, ΠΈ Ρ Π·Π°Π΄Π°ΡΠ΅ΠΉ ΡΠΏΡΠ°Π²ΠΈΡΡΡ Π΄Π°ΠΆΠ΅ Π½ΠΎΠ²ΠΈΡΠΎΠΊ.
Π‘ΡΠ΅Π΄ΠΈ Π½Π΅Π΄ΠΎΡΡΠ°ΡΠΊΠΎΠ² ΠΌΠΎΠΆΠ½ΠΎ Π²ΡΠ΄Π΅Π»ΠΈΡΡ:
ΠΠ»ΠΎΠΊΠΈ ΠΏΠΎΠ΄Π²Π΅ΡΠΆΠ΅Π½Ρ ΡΡΠ°Π΄ΠΊΠ΅.
- ΠΡΠ΅Π½Ρ ΡΠ°ΡΡΠΎ Π³Π΅ΠΎΠΌΠ΅ΡΡΠΈΡ ΠΌΠ°ΡΠ΅ΡΠΈΠ°Π»Π° ΠΎΡΡΠ°Π²Π»ΡΠ΅Ρ ΠΆΠ΅Π»Π°ΡΡ Π»ΡΡΡΠ΅Π³ΠΎ.
- ΠΠΎΡΡΠ°ΡΠΎΡΠ½Π°Ρ Π³ΠΈΠ³ΡΠΎΡΠΊΠΎΠΏΠΈΡΠ½ΠΎΡΡΡ. ΠΠΏΠΈΠ»ΠΊΠΈ Ρ ΠΎΡΠΎΡΠΎ Π²ΠΏΠΈΡΡΠ²Π°ΡΡ Π²Π»Π°Π³Ρ. ΠΠΎ Π²Π°ΠΆΠ½ΠΎ ΠΎΡΠΌΠ΅ΡΠΈΡΡ, ΡΡΠΎ ΡΡΠΎΡ ΠΏΠΎΠΊΠ°Π·Π°ΡΠ΅Π»Ρ Π½Π΅ ΡΡΠΈΡΠ°Π΅ΡΡΡ Π²ΡΡΠΎΠΊΠΈΠΌ ΡΡΠ΅Π΄ΠΈ ΡΡΠ΅Π½ΠΎΠ²ΡΡ Π·Π΄Π°Π½ΠΈΠΉ.
- ΠΡΠΆΠ½ΠΎ ΠΌΠ½ΠΎΠ³ΠΎ Π²ΡΠ΅ΠΌΠ΅Π½ΠΈ, ΡΡΠΎΠ±Ρ ΠΎΠΏΠΈΠ»ΠΊΠΎΠ±Π΅ΡΠΎΠ½ Π΄ΠΎΡΡΠΈΠ³ Π½Π΅ΠΎΠ±Ρ ΠΎΠ΄ΠΈΠΌΠΎΠΉ ΠΌΠ°ΡΠΎΡΠ½ΠΎΠΉ ΠΏΡΠΎΡΠ½ΠΎΡΡΠΈ. Π Π½Π΅ΠΊΠΎΡΠΎΡΡΡ ΡΠ»ΡΡΠ°ΡΡ ΡΡΠΎ ΠΌΠΎΠΆΠ΅Ρ Π·Π°Π½ΡΡΡ Π½Π΅ΡΠΊΠΎΠ»ΡΠΊΠΎ ΠΌΠ΅ΡΡΡΠ΅Π².
- Π ΡΠ²ΡΠ·ΠΈ Ρ ΡΠ΅ΠΌ, ΡΡΠΎ ΡΠ΅Ρ Π½ΠΎΠ»ΠΎΠ³ΠΈΡ ΠΈΠ·Π³ΠΎΡΠΎΠ²Π»Π΅Π½ΠΈΡ Π±Π»ΠΎΠΊΠΎΠ² Π½Π΅ ΡΠ²Π»ΡΠ΅ΡΡΡ ΡΠ»ΠΎΠΆΠ½ΠΎΠΉ, ΠΈΡ ΡΠ°ΡΡΠΎ ΠΈΠ·Π³ΠΎΡΠ°Π²Π»ΠΈΠ²Π°ΡΡ Π² ΠΊΡΡΡΠ°ΡΠ½ΡΡ ΡΡΠ»ΠΎΠ²ΠΈΡΡ . ΠΠΎΠ½Π΅ΡΠ½ΠΎ, ΠΊΠ°ΡΠ΅ΡΡΠ²ΠΎ ΡΠ°ΠΊΠΈΡ ΠΈΠ·Π΄Π΅Π»ΠΈΠΉ Π½Π΅ ΠΊΠΎΠ½ΡΡΠΎΠ»ΠΈΡΡΠ΅ΡΡΡ ΠΈ Π½Π΅ ΡΠ΅ΡΡΠΈΡΡΠ΅ΡΡΡ, ΡΡΠΎ ΠΏΠΎΠ²ΡΡΠ°Π΅Ρ ΡΠΈΡΠΊΠΈ ΠΏΠΎΠΊΡΠΏΠΊΠΈ ΠΌΠ°ΡΠ΅ΡΠΈΠ°Π»Π° ΡΠΎΠΌΠ½ΠΈΡΠ΅Π»ΡΠ½ΠΎΠ³ΠΎ ΠΊΠ°ΡΠ΅ΡΡΠ²Π°.
ΠΡΠ°ΠΏΡ ΡΠ°ΠΌΠΎΡΡΠΎΡΡΠ΅Π»ΡΠ½ΠΎΠ³ΠΎ ΠΏΡΠΎΠΈΠ·Π²ΠΎΠ΄ΡΡΠ²Π°
Π§ΡΠΎΠ±Ρ ΠΈΠ·Π³ΠΎΡΠΎΠ²ΠΈΡΡ ΠΊΠ°ΡΠ΅ΡΡΠ²Π΅Π½Π½ΡΠ΅ ΠΎΠΏΠΈΠ»ΠΊΠΎΠ±Π»ΠΎΠΊΠΈ ΡΠ²ΠΎΠΈΠΌΠΈ ΡΡΠΊΠ°ΠΌΠΈ, Π½ΡΠΆΠ½ΠΎ ΠΏΡΠΈΠ΄Π΅ΡΠΆΠΈΠ²Π°ΡΡΡΡ Π½Π΅ΡΠΊΠΎΠ»ΡΠΊΠΈΡ ΡΠ΅ΠΊΠΎΠΌΠ΅Π½Π΄Π°ΡΠΈΠΉ, ΠΊΠΎΡΠΎΡΡΠ΅ Π±ΡΠ»ΠΈ ΡΠ°Π·ΡΠ°Π±ΠΎΡΠ°Π½Ρ ΠΎΠΏΡΡΠ½ΡΠΌΠΈ ΡΠΏΠ΅ΡΠΈΠ°Π»ΠΈΡΡΠ°ΠΌΠΈ. ΠΡΠΎ ΡΠ²ΡΠ·Π°Π½ΠΎ Ρ ΡΠ΅ΠΌ, ΡΡΠΎ ΡΠΎΠ»ΡΠΊΠΎ ΡΠΎΡΠ½ΠΎΠ΅ Π²ΡΠΏΠΎΠ»Π½Π΅Π½ΠΈΠ΅ Π²ΡΠ΅Ρ Π½ΠΎΡΠΌ ΠΏΠΎΠ·Π²ΠΎΠ»ΠΈΡ ΠΏΠΎΠ»ΡΡΠΈΡΡ ΠΊΠ°ΡΠ΅ΡΡΠ²Π΅Π½Π½ΠΎΠ΅ ΠΈΠ·Π΄Π΅Π»ΠΈΠ΅, ΠΊΠΎΡΠΎΡΠΎΠ΅ Π±ΡΠ΄Π΅Ρ ΠΎΠ±Π»Π°Π΄Π°ΡΡ Π½Π΅ΠΎΠ±Ρ ΠΎΠ΄ΠΈΠΌΡΠΌΠΈ ΠΏΡΠΎΡΠ½ΠΎΡΡΠ½ΡΠΌΠΈ ΠΈ ΡΠΊΡΠΏΠ»ΡΠ°ΡΠ°ΡΠΈΠΎΠ½Π½ΡΠΌΠΈ Ρ Π°ΡΠ°ΠΊΡΠ΅ΡΠΈΡΡΠΈΠΊΠ°ΠΌΠΈ. ΠΡΠ½ΠΎΠ²Π½ΠΎΠΉ Π°Π»Π³ΠΎΡΠΈΡΠΌ ΠΏΡΠΎΠΈΠ·Π²ΠΎΠ΄ΡΡΠ²Π° Π²ΡΠ³Π»ΡΠ΄ΠΈΡ ΡΠ»Π΅Π΄ΡΡΡΠΈΠΌ ΠΎΠ±ΡΠ°Π·ΠΎΠΌ:
ΠΠ° ΠΏΠ΅ΡΠ²ΠΎΠΌ ΡΡΠ°ΠΏΠ΅ ΠΎΡΡΡΠ΅ΡΡΠ²Π»ΡΠ΅ΡΡΡ ΠΏΠΎΠ΄Π³ΠΎΡΠΎΠ²ΠΊΠ° Π²ΡΠ΅Ρ Π½Π΅ΠΎΠ±Ρ ΠΎΠ΄ΠΈΠΌΡΡ ΠΌΠ°ΡΠ΅ΡΠΈΠ°Π»ΠΎΠ². Π‘ΡΠΎΠΈΡ ΠΎΡΠΌΠ΅ΡΠΈΡΡ, ΡΡΠΎ Π½Π΅Ρ Π½Π΅ΠΎΠ±Ρ ΠΎΠ΄ΠΈΠΌΠΎΡΡΠΈ ΠΏΡΠΈΠΎΠ±ΡΠ΅ΡΠ°ΡΡ ΠΎΡΠ½ΠΎΠ²Π½ΡΠ΅ ΡΠΎΡΡΠ°Π²Π»ΡΡΡΠΈΠ΅ ΠΊΠΎΠΌΠΏΠΎΠ½Π΅Π½ΡΡ Π·Π°ΡΠ°Π½Π΅Π΅. ΠΡΠ΅ ΡΡΠΎ ΠΌΠΎΠΆΠ½ΠΎ ΡΠ΄Π΅Π»Π°ΡΡ Π½Π΅ΠΏΠΎΡΡΠ΅Π΄ΡΡΠ²Π΅Π½Π½ΠΎ ΠΏΠ΅ΡΠ΅Π΄ ΠΈΠ·Π³ΠΎΡΠΎΠ²Π»Π΅Π½ΠΈΠ΅ΠΌ Π±Π»ΠΎΠΊΠΎΠ². Π ΡΡΠΎΠΌ ΡΠ»ΡΡΠ°Π΅ ΠΎΡΠ»ΠΈΡΠ½ΠΎ ΠΏΠΎΠ΄ΠΎΠΉΠ΄ΡΡ Π½Π΅ ΡΠΎΠ»ΡΠΊΠΎ ΡΠΏΠ΅ΡΠΈΠ°Π»ΠΈΠ·ΠΈΡΠΎΠ²Π°Π½Π½ΡΠΉ ΡΡΡΠΎΠΈΡΠ΅Π»ΡΠ½ΡΠΉ ΠΌΠ°Π³Π°Π·ΠΈΠ½ ΠΈΠ»ΠΈ ΡΠΊΠ»Π°Π΄, ΠΌΠΎΠΆΠ½ΠΎ Π²ΠΎΡΠΏΠΎΠ»ΡΠ·ΠΎΠ²Π°ΡΡΡΡ ΠΏΡΠΎΠΈΠ·Π²ΠΎΠ΄ΡΡΠ²Π΅Π½Π½ΡΠΌΠΈ ΠΎΡΡ ΠΎΠ΄Π°ΠΌΠΈ Π΄Π΅ΡΠ΅Π²ΠΎΠΎΠ±ΡΠ°Π±Π°ΡΡΠ²Π°ΡΡΠΈΡ ΠΏΡΠ΅Π΄ΠΏΡΠΈΡΡΠΈΠΉ.
- ΠΡΠ΅ ΠΊΠΎΠΌΠΏΠΎΠ½Π΅Π½ΡΡ Π΄ΠΎΠ»ΠΆΠ½Ρ Π±ΡΡΡ ΡΠΌΠ΅ΡΠ°Π½Ρ Π² ΠΎΠ΄Π½ΠΎΠΉ ΡΠΌΠΊΠΎΡΡΠΈ Π² ΡΠΎΠΎΡΠ²Π΅ΡΡΡΠ²ΠΈΠΈ Ρ ΠΏΡΠΎΠΏΠΎΡΡΠΈΠ΅ΠΉ. ΠΠ»Ρ ΠΏΠ΅ΡΠ΅ΠΌΠ΅ΡΠΈΠ²Π°Π½ΠΈΡ ΠΌΠΎΠΆΠ΅Ρ Π±ΡΡΡ Π·Π°Π΄Π΅ΠΉΡΡΠ²ΠΎΠ²Π°Π½ ΠΌΠ΅Ρ Π°Π½ΠΈΡΠ΅ΡΠΊΠΈΠΉ ΡΠΏΠΎΡΠΎΠ± Ρ ΠΏΡΠΈΠΌΠ΅Π½Π΅Π½ΠΈΠ΅ΠΌ ΠΌΠΎΡΠ½ΠΎΠ³ΠΎ Π±Π΅ΡΠΎΠ½ΠΎΡΠΌΠ΅ΡΠΈΡΠ΅Π»Ρ Π»ΠΈΠ±ΠΎ ΡΡΡΠ½ΡΠΌ ΠΏΡΡΡΠΌ ΠΏΡΠΈ ΠΏΠΎΠΌΠΎΡΠΈ ΠΎΠ±ΡΡΠ½ΡΡ Π»ΠΎΠΏΠ°Ρ. ΠΠ°ΠΊ ΠΏΠΎΠΊΠ°Π·ΡΠ²Π°Π΅Ρ ΠΏΡΠ°ΠΊΡΠΈΠΊΠ°, Π°Π²ΡΠΎΠΌΠ°ΡΠΈΠ·Π°ΡΠΈΡ ΡΠ΅Ρ Π½ΠΎΠ»ΠΎΠ³ΠΈΡΠ΅ΡΠΊΠΎΠ³ΠΎ ΠΏΡΠΎΡΠ΅ΡΡΠ° Ρ ΠΏΠΎΠΌΠΎΡΡΡ ΡΡΡΠΎΠΈΡΠ΅Π»ΡΠ½ΠΎΠΉ Π±Π΅ΡΠΎΠ½ΠΎΠΌΠ΅ΡΠ°Π»ΠΊΠΈ ΠΏΠΎΠ·Π²ΠΎΠ»ΡΠ΅Ρ ΡΡΡΠ΅ΡΡΠ²Π΅Π½Π½ΠΎ ΠΏΠΎΠ²ΡΡΠΈΡΡ ΠΈΡΠΎΠ³ΠΎΠ²ΡΡ ΠΏΡΠΎΠΈΠ·Π²ΠΎΠ΄ΠΈΡΠ΅Π»ΡΠ½ΠΎΡΡΡ, Π° ΡΠ°ΠΊΠΆΠ΅ ΡΠ»ΡΡΡΠΈΡΡ ΠΊΠ°ΡΠ΅ΡΡΠ²ΠΎ ΠΏΡΠΎΠ΄ΡΠΊΡΠΈΠΈ. Π ΡΡΠΎΠΌ ΡΠ»ΡΡΠ°Π΅ ΠΎΠ±Π΅ΡΠΏΠ΅ΡΠΈΠ²Π°Π΅ΡΡΡ ΡΡΠ°ΡΠ΅Π»ΡΠ½ΠΎ ΡΠΌΠ΅ΡΠΈΠ²Π°Π½ΠΈΠ΅ Π²ΡΠ΅Ρ ΠΈΠ½Π³ΡΠ΅Π΄ΠΈΠ΅Π½ΡΠΎΠ², ΠΊΠΎΡΠΎΡΠΎΠ΅ ΠΏΠΎΠΌΠΎΠ³Π°Π΅Ρ ΠΈΠ·Π±Π΅ΠΆΠ°ΡΡ ΠΏΠΎΡΠ»Π΅Π΄ΡΡΡΠ΅Π³ΠΎ Π±ΡΠ°ΠΊΠ°.
- ΠΠ° ΡΠ»Π΅Π΄ΡΡΡΠ΅ΠΌ ΡΡΠ°ΠΏΠ΅ ΠΎΡΡΡΠ΅ΡΡΠ²Π»ΡΠ΅ΡΡΡ ΡΠΎΡΠΌΠΈΡΠΎΠ²ΠΊΠ° Π±Π»ΠΎΠΊΠΎΠ². ΠΠ³ΡΠΎΠΌΠ½ΡΠΌ ΠΏΡΠ΅ΠΈΠΌΡΡΠ΅ΡΡΠ²ΠΎΠΌ ΠΎΠ±Π»Π°Π΄Π°Π΅Ρ Π³ΡΡΠΏΠΏΠΎΠ²ΠΎΠΉ ΠΏΡΠΎΡΠ΅ΡΡ ΡΠΎΡΠΌΠΈΡΠΎΠ²ΠΊΠΈ. ΠΡΠ° ΡΠ΅Ρ Π½ΠΎΠ»ΠΎΠ³ΠΈΡ ΠΏΠΎΠ΄ΡΠ°Π·ΡΠΌΠ΅Π²Π°Π΅Ρ ΡΠΎ, ΡΡΠΎ ΡΡΠ°ΡΠ΅Π»ΡΠ½ΠΎ ΠΏΠ΅ΡΠ΅ΠΌΠ΅ΡΠ°Π½Π½ΡΠΉ ΡΠΎΡΡΠ°Π² Π·Π°Π»ΠΈΠ²Π°Π΅ΡΡΡ ΡΡΠ°Π·Ρ Π² Π½Π΅ΡΠΊΠΎΠ»ΡΠΊΠΎ ΡΠΎΡΠΌ. Π Π·Π°Π²ΠΈΡΠΈΠΌΠΎΡΡΠΈ ΠΎΡ ΠΌΠ°ΡΡΡΠ°Π±ΠΎΠ² ΡΡΡΠΎΠΉΠΊΠΈ, ΡΠΏΠ΅ΡΠΈΠ°Π»ΠΈΡΡΡ ΠΌΠΎΠ³ΡΡ ΠΈΡΠΏΠΎΠ»ΡΠ·ΠΎΠ²Π°ΡΡ ΠΊΠ°ΠΊ Π΅Π΄ΠΈΠ½ΠΈΡΠ½ΡΠ΅, ΡΠ°ΠΊ ΠΈ Π³ΡΡΠΏΠΏΠΎΠ²ΡΠ΅ ΡΠΎΡΠΌΡ ΡΠ°Π·Π±ΠΎΡΠ½ΠΎΠΉ ΠΊΠΎΠ½ΡΡΡΡΠΊΡΠΈΠΈ. ΠΠ½ΠΈ ΠΌΠΎΠ³ΡΡ Π±ΡΡΡ ΠΈΠ·Π³ΠΎΡΠΎΠ²Π»Π΅Π½Ρ ΠΈΠ· ΠΊΠ°ΡΠ΅ΡΡΠ²Π΅Π½Π½ΠΎΠΉ Π΄ΡΠ΅Π²Π΅ΡΠΈΠ½Ρ ΡΠΎΠ»ΡΠΈΠ½ΠΎΠΉ 2 ΡΠΌ ΠΈ ΠΎΠ±ΠΈΡΡ ΠΏΠ»Π°ΡΡΠΈΠΊΠΎΠΌ ΠΈΠ»ΠΈ ΠΆΠ΅ ΠΌΠ΅ΡΠ°Π»Π»ΠΎΠΌ. ΠΡΠΏΠΎΠ»ΡΠ·ΠΎΠ²Π°Π½ΠΈΠ΅ ΠΎΠ±ΡΡΠ½ΠΎΠΉ ΠΏΠΎΠ»ΠΈΡΡΠΈΠ»Π΅Π½ΠΎΠ²ΠΎΠΉ ΠΏΠ»ΡΠ½ΠΊΠΈ ΡΠΏΡΠΎΡΠ°Π΅Ρ ΠΈΠ·Π²Π»Π΅ΡΠ΅Π½ΠΈΠ΅ Π³ΠΎΡΠΎΠ²ΡΡ Π±Π»ΠΎΠΊΠΎΠ².
- ΠΠ° ΡΠΈΠ½Π°Π»ΡΠ½ΠΎΠΌ ΡΡΠ°ΠΏΠ΅ ΠΏΡΠΎΠ²ΠΎΠ΄ΠΈΡΡΡ ΡΡΡΠΊΠ° Π³ΠΎΡΠΎΠ²ΠΎΠ³ΠΎ ΠΌΠ°ΡΠ΅ΡΠΈΠ°Π»Π° ΠΏΠΎΠ΄ ΠΎΡΠΊΡΡΡΡΠΌ Π½Π΅Π±ΠΎΠΌ. Π§Π΅ΡΠ΅Π· 5 ΡΡΡΠΎΠΊ ΠΏΠΎΡΠ»Π΅ Π·Π°Π»ΠΈΠ²ΠΊΠΈ ΠΎΡΡΡΠ΅ΡΡΠ²Π»ΡΠ΅ΡΡΡ ΡΠ½ΡΡΠΈΠ΅ ΡΠΎΡΠΌ. Π ΡΡΠΎΠΌ ΡΠ»ΡΡΠ°Π΅ ΠΌΠ°ΡΡΠ΅Ρ Π΄ΠΎΠ»ΠΆΠ΅Π½ ΠΎΡΠ»Π°Π±ΠΈΡΡ Π·Π°ΡΡΠΆΠΊΠΈ Π±Π°ΡΠ°ΡΠΊΠΎΠ²ΡΡ Π³Π°Π΅ΠΊ, ΠΈΠ·Π²Π»Π΅ΡΡ ΡΠ΅Π·ΡΠ±ΠΎΠ²ΡΠ΅ ΡΠΏΠΈΠ»ΡΠΊΠΈ ΠΈ ΠΏΠΎΡΡΠ°ΠΏΠ½ΠΎ ΡΠ°Π·ΠΎΠ±ΡΠ°ΡΡ ΡΠΎΡΠΌΠΈΡΠΎΠ²ΠΎΡΠ½ΡΠΉ ΡΡΠΈΠΊ. ΠΠ»ΠΈΡΠ΅Π»ΡΠ½ΠΎΡΡΡ Π΅ΡΡΠ΅ΡΡΠ²Π΅Π½Π½ΠΎΠΉ ΡΡΡΠΊΠΈ Π·Π°Π²ΠΈΡΠΈΡ ΠΈΡΠΊΠ»ΡΡΠΈΡΠ΅Π»ΡΠ½ΠΎ ΠΎΡ ΠΏΠΎΡΠΎΠ΄Ρ Π΄ΡΠ΅Π²Π΅ΡΠΈΠ½Ρ (Π½Π΅ Π±ΠΎΠ»Π΅Π΅ ΡΡΡΡ ΠΌΠ΅ΡΡΡΠ΅Π²). Π ΡΠ΅ΡΠ΅Π½ΠΈΠ΅ ΡΡΠΎΠ³ΠΎ ΠΏΡΠΎΠΌΠ΅ΠΆΡΡΠΊΠ° Π²ΡΠ΅ΠΌΠ΅Π½ΠΈ ΡΡΡΠ΅ΡΡΠ²Π΅Π½Π½ΠΎ ΡΠ½ΠΈΠΆΠ°Π΅ΡΡΡ ΠΊΠΎΠ»ΠΈΡΠ΅ΡΡΠ²ΠΎ Π²Π»Π°Π³ΠΈ, ΠΈ Π±Π»ΠΎΠΊΠΈ ΠΏΡΠΈΠΎΠ±ΡΠ΅ΡΠ°ΡΡ Π½Π΅ΠΎΠ±Ρ ΠΎΠ΄ΠΈΠΌΡΡ ΡΠΊΡΠΏΠ»ΡΠ°ΡΠ°ΡΠΈΠΎΠ½Π½ΡΡ ΠΏΡΠΎΡΠ½ΠΎΡΡΡ.
ΠΠ΅ΠΎΠ±Ρ ΠΎΠ΄ΠΈΠΌΡΠ΅ ΠΈΠ½ΡΡΡΡΠΌΠ΅Π½ΡΡ ΠΈ ΡΠΎΡΠΌΡ
ΠΠ΅ ΡΠΎΠ»ΡΠΊΠΎ ΠΎΠΏΡΡΠ½ΡΠ΅ ΡΡΡΠΎΠΈΡΠ΅Π»ΠΈ, Π½ΠΎ ΠΈ Π½Π°ΡΠΈΠ½Π°ΡΡΠΈΠ΅ ΠΌΠ°ΡΡΠ΅ΡΠ° Π²ΡΠ΅ ΡΠ°ΡΠ΅ ΡΠ΅ΡΠ°ΡΡ ΡΠ΄Π΅Π»Π°ΡΡ ΠΎΠΏΠΈΠ»ΠΊΠΎΠ±Π΅ΡΠΎΠ½ ΡΠ²ΠΎΠΈΠΌΠΈ ΡΡΠΊΠ°ΠΌΠΈ. Π’Π΅Ρ Π½ΠΎΠ»ΠΎΠ³ΠΈΡ ΠΈΠ·Π³ΠΎΡΠΎΠ²Π»Π΅Π½ΠΈΡ ΠΏΠΎΠ΄ΡΠ°Π·ΡΠΌΠ΅Π²Π°Π΅Ρ Π½Π°Π»ΠΈΡΠΈΠ΅ ΡΠΈΡΠΊΠΎΠ² Π΄Π»Ρ ΠΎΠΏΠ°Π»ΡΠ±ΠΊΠΈ. ΠΠ½ΠΈ Π΄ΠΎΠ»ΠΆΠ½Ρ Π±ΡΡΡ ΠΏΡΠ°Π²ΠΈΠ»ΡΠ½ΠΎ Π²ΡΠΌΠ΅ΡΠ΅Π½Ρ, ΡΡΠΎΠ±Ρ Π±Π»ΠΎΠΊΠΈ ΠΏΠΎΠ»ΡΡΠΈΠ»ΠΈΡΡ ΠΌΠ°ΠΊΡΠΈΠΌΠ°Π»ΡΠ½ΠΎ ΡΠΎΠ²Π½ΡΠΌΠΈ. ΠΠ΅Π»Π°ΡΠ΅Π»ΡΠ½ΠΎ, ΡΡΠΎΠ±Ρ Π΄ΠΎΡΠΊΠΈ Π΄Π»Ρ ΡΠΈΡΠΊΠ° ΠΈΠΌΠ΅Π»ΠΈ ΡΠΎΠ»ΡΠΈΠ½Ρ 38 ΠΌΠΌ. ΠΠΏΠΈΠ»ΠΊΠΈ ΠΎΠ±ΡΠ·Π°ΡΠ΅Π»ΡΠ½ΠΎ ΠΏΡΠΎΡΠ΅ΠΈΠ²Π°ΡΡ ΠΎΡ Π½Π°ΠΊΠΎΠΏΠΈΠ²ΡΠ΅Π³ΠΎΡΡ ΠΌΡΡΠΎΡΠ° ΠΈ ΠΊΠ°ΠΌΠ½Π΅ΠΉ. ΠΠΎΠ³Π΄Π° ΡΠ΅ΠΏΠ° ΠΈ ΠΊΠΎΡΠ° ΠΎΡΡΠΎΡΡΠΈΡΠΎΠ²Π°Π½Ρ, Π½ΡΠΆΠ½ΠΎ Π΄ΠΎΠ±Π°Π²ΠΈΡΡ ΠΊ Π½ΠΈΠΌ ΠΏΠΎΠ΄Π³ΠΎΡΠΎΠ²Π»Π΅Π½Π½ΡΡ Π΄ΡΠ΅Π²Π΅ΡΠ½ΡΡ ΡΡΡΡΠΆΠΊΡ. Π’Π°ΠΊ ΠΌΠΎΠΆΠ½ΠΎ ΡΠ²Π΅Π»ΠΈΡΠΈΡΡ ΠΈΡΠΎΠ³ΠΎΠ²ΡΡ ΠΏΡΠΎΡΠ½ΠΎΡΡΡ ΠΌΠ°ΡΠ΅ΡΠΈΠ°Π»Π° Π² Π½Π΅ΡΠΊΠΎΠ»ΡΠΊΠΎ ΡΠ°Π·.
Π£ΠΊΠ»Π°Π΄ΠΊΠ° ΡΠ°ΡΡΠ²ΠΎΡΠ° ΠΌΠΎΠΆΠ΅Ρ ΠΎΡΡΡΠ΅ΡΡΠ²Π»ΡΡΡΡΡ Π² Π΄Π²Π° ΡΠΈΠΏΠ° ΡΠΎΡΠΌ:
ΠΠ΅Π±ΠΎΠ»ΡΡΠΈΠ΅ Π±Π»ΠΎΠΊΠΈ. Π’Π°ΠΊΠΈΠ΅ ΡΠΎΡΠΌΡ ΠΈΠΌΠ΅ΡΡ ΠΊΠΎΠΌΠΏΠ°ΠΊΡΠ½ΡΠ΅ ΡΠ°Π·ΠΌΠ΅ΡΡ, ΠΈ Π·Π° ΠΎΠ΄ΠΈΠ½ ΡΠ°Π· ΠΌΠΎΠΆΠ½ΠΎ ΠΈΠ·Π³ΠΎΡΠΎΠ²ΠΈΡΡ Π΄ΠΎ 9 ΠΎΠΏΠΈΠ»ΠΊΠΎΠ±Π»ΠΎΠΊΠΎΠ².
- ΠΠ°Π±Π°ΡΠΈΡΠ½ΡΠ΅ Π±Π»ΠΎΠΊΠΈ. ΠΠ»Ρ ΡΠ°ΠΊΠΎΠ³ΠΎ ΠΌΠ°ΡΠ΅ΡΠΈΠ°Π»Π° Π½Π΅ΠΎΠ±Ρ ΠΎΠ΄ΠΈΠΌΠΎ ΠΏΠΎΠ΄Π³ΠΎΡΠΎΠ²ΠΈΡΡ Π²ΠΌΠ΅ΡΡΠΈΡΠ΅Π»ΡΠ½ΡΠ΅ ΡΡΠΈΠΊΠΈ ΠΈΠ· Π΄ΠΎΡΠΎΠΊ. Π‘ΡΠΎΠΈΡ ΠΎΡΠΌΠ΅ΡΠΈΡΡ, ΡΡΠΎ ΡΠ°ΡΠ΅ Π²ΡΠ΅Π³ΠΎ ΠΎΠ½ΠΈ ΡΠ°Π·Π±ΠΎΡΠ½ΡΠ΅, ΡΠ°ΠΊ ΠΊΠ°ΠΊ ΡΡΠΎ ΡΡΠΊΠΎΡΡΠ΅Ρ ΠΏΡΠΎΡΠ΅ΡΡ ΠΈΠ·ΡΡΡΠΈΡ Π³ΠΎΡΠΎΠ²ΠΎΠ³ΠΎ ΠΌΠ°ΡΠ΅ΡΠΈΠ°Π»Π°.
Π‘ΠΏΠ΅ΡΠΈΠ°Π»ΠΈΡΡΡ ΡΡΠ²Π΅ΡΠΆΠ΄Π°ΡΡ, ΡΡΠΎ ΠΊ ΡΠΊΠ»Π°Π΄ΠΊΠ΅ ΠΏΡΠΈΠ³ΠΎΡΠΎΠ²Π»Π΅Π½Π½ΠΎΠ³ΠΎ ΡΠ°ΡΡΠ²ΠΎΡΠ° Π½Π΅ΠΎΠ±Ρ ΠΎΠ΄ΠΈΠΌΠΎ ΠΏΡΠΈΡΡΡΠΏΠ°ΡΡ ΡΡΠ°Π·Ρ, ΡΠ°ΠΊ ΠΊΠ°ΠΊ ΡΠΆΠ΅ ΡΠ΅ΡΠ΅Π· Π½Π΅ΡΠΊΠΎΠ»ΡΠΊΠΎ ΡΠ°ΡΠΎΠ² ΠΎΠ½ Π½Π°ΡΠ½ΡΡ Π·Π°ΡΡΡΠ²Π°ΡΡ. ΠΡΠΆΠ½ΠΎ ΠΏΠΎΠΌΠ½ΠΈΡΡ, ΡΡΠΎ ΠΏΠ΅ΡΠ΅Π΄ ΠΈΡΠΏΠΎΠ»ΡΠ·ΠΎΠ²Π°Π½ΠΈΠ΅ΠΌ Π²Π½ΡΡΡΠ΅Π½Π½ΠΈΠ΅ ΡΠ°ΡΡΠΈ ΠΎΠΏΠ°Π»ΡΠ±ΠΊΠΈ ΠΎΠ±ΡΠ·Π°ΡΠ΅Π»ΡΠ½ΠΎ ΡΠ²Π»Π°ΠΆΠ½ΡΡΡΡΡ ΠΎΠ±ΡΡΠ½ΠΎΠΉ Π²ΠΎΠ΄ΠΎΠΉ.
Π£ΠΊΠ»Π°Π΄ΡΠ²Π°ΡΡ ΡΠ°ΡΡΠ²ΠΎΡ Π½Π΅ΠΎΠ±Ρ ΠΎΠ΄ΠΈΠΌΠΎ Π°ΠΊΠΊΡΡΠ°ΡΠ½ΡΠΌΠΈ ΡΠ»ΠΎΡΠΌΠΈ ΠΏΠΎ 150 ΠΌΠΌ. ΠΡΠΈ ΡΡΠΎΠΌ ΠΊΠ°ΠΆΠ΄Π°Ρ ΡΠ°ΡΡΡ Π΄ΠΎΠ»ΠΆΠ½Π° Π±ΡΡΡ ΡΡΠ°ΡΠ΅Π»ΡΠ½ΠΎ ΡΡΡΠ°ΠΌΠ±ΠΎΠ²Π°Π½Π°, ΡΠ°ΠΊ ΠΊΠ°ΠΊ ΡΡΠΎ ΠΏΡΠ΅Π΄ΠΎΡΠ²ΡΠ°ΡΠ°Π΅Ρ ΠΎΠ±ΡΠ°Π·ΠΎΠ²Π°Π½ΠΈΠ΅ ΠΏΡΡΡΠΎΡ.
Π§Π΅ΡΠ΅Π· ΡΠ΅ΡΡΡΠ΅ Π΄Π½Ρ ΠΎΠΏΠ°Π»ΡΠ±ΠΊΡ Π½Π΅ΠΎΠ±Ρ ΠΎΠ΄ΠΈΠΌΠΎ Π°ΠΊΠΊΡΡΠ°ΡΠ½ΠΎ ΡΠ½ΡΡΡ (Π½ΠΎ ΡΠΎΠ»ΡΠΊΠΎ Π² ΡΠΎΠΌ ΡΠ»ΡΡΠ°Π΅, Π΅ΡΠ»ΠΈ ΡΠ°ΡΡΠ²ΠΎΡ ΠΏΠΎΠ»Π½ΠΎΡΡΡΡ Π·Π°ΡΡΡΠ»). Π Π²ΠΎΡ ΠΎΠΏΠΈΠ»ΠΊΠΎΠ±Π»ΠΎΠΊΠΈ ΠΆΠ΅Π»Π°ΡΠ΅Π»ΡΠ½ΠΎ ΠΎΡΡΠ°Π²ΠΈΡΡ Π΄ΠΎΡΡΡ Π°ΡΡ Π΅ΡΡ Π½Π° ΡΠ΅ΡΡΡΠ΅ Π΄Π½Ρ. ΠΡΠΎ Π΄Π΅Π»Π°Π΅ΡΡΡ Π΄Π»Ρ ΡΠΎΠ³ΠΎ, ΡΡΠΎΠ±Ρ ΠΏΠΎΠ²ΡΡΠΈΡΡ ΠΈΡΠΎΠ³ΠΎΠ²ΡΡ ΠΏΡΠΎΡΠ½ΠΎΡΡΡ ΠΌΠ°ΡΠ΅ΡΠΈΠ°Π»Π°. ΠΡΠ΄Π΅Π»ΡΠ½ΠΎ ΡΡΠΎΠΈΡ ΡΡΠ΅ΡΡΡ, ΡΡΠΎ Π΄Π»Ρ ΡΡΡΠΊΠΈ ΠΈΠ·Π³ΠΎΡΠ°Π²Π»ΠΈΠ²Π°Π΅ΠΌΡΡ Π±Π»ΠΎΠΊΠΎΠ² Π»ΡΡΡΠ΅ Π²ΡΠ΅Π³ΠΎ ΠΈΡΠΏΠΎΠ»ΡΠ·ΠΎΠ²Π°ΡΡ ΡΠΎΡ ΡΡΠ°ΡΡΠΎΠΊ, Π³Π΄Π΅ Π΅ΡΡΡ ΡΠΊΠ²ΠΎΠ·Π½ΡΠΊΠΈ, ΡΡΠΎΠ±Ρ ΡΠ°ΡΡΠ²ΠΎΡ Π·Π°ΡΡΡΠ²Π°Π» ΡΠ°Π²Π½ΠΎΠΌΠ΅ΡΠ½ΠΎ. ΠΠ΅ΠΆΠ΄Ρ ΠΊΠ°ΠΆΠ΄ΡΠΌ ΠΎΠΏΠΈΠ»ΠΊΠΎΠ±Π»ΠΎΠΊΠΎΠΌ Π΄ΠΎΠ»ΠΆΠ΅Π½ ΠΏΡΠΈΡΡΡΡΡΠ²ΠΎΠ²Π°ΡΡ Π·Π°Π·ΠΎΡ. ΠΡΠ»ΠΈ ΡΠΎΠ±ΠΈΡΠ°Π΅ΡΡΡ Π΄ΠΎΠΆΠ΄Ρ, ΡΠΎΠ³Π΄Π° ΠΌΠ°ΡΠ΅ΡΠΈΠ°Π» Π½ΡΠΆΠ½ΠΎ ΡΠΊΡΡΡΡ ΠΏΠ»ΡΠ½ΠΊΠΎΠΉ, ΡΡΠΎΠ±Ρ ΠΏΡΠ΅Π΄ΠΎΡΠ²ΡΠ°ΡΠΈΡΡ Π½Π°ΠΌΠΎΠΊΠ°Π½ΠΈΠ΅.
ΠΠ»Ρ Π³Π°ΡΠ°Π½ΡΠΈΡΠΎΠ²Π°Π½Π½ΠΎΠΉ ΡΡΡΠΊΠΈ Π΄ΠΎΠ»ΠΆΠ½Ρ Π±ΡΡΡ Π·Π°Π΄Π΅ΠΉΡΡΠ²ΠΎΠ²Π°Π½Ρ ΡΡΠΎΠ»Π±Ρ. ΠΠ»ΠΎΠΊΠΈ ΠΌΠΎΠΆΠ½ΠΎ ΡΠ»ΠΎΠΆΠΈΡΡ Π½Π° ΠΊΠΈΡΠΏΠΈΡΠΈ. ΠΠ»Π°Π³ΠΎΠ΄Π°ΡΡ ΡΠ°ΠΊΠΈΠΌ ΠΌΠ°Π½ΠΈΠΏΡΠ»ΡΡΠΈΡΠΌ, ΠΌΠΎΠΆΠ½ΠΎ Π΄ΠΎΠ±ΠΈΡΡΡΡ 90% ΠΏΡΠΎΡΠ½ΠΎΡΡΠΈ ΡΠΆΠ΅ ΠΏΠΎΡΠ»Π΅ ΠΌΠ΅ΡΡΡΠ° ΡΠ°ΠΊΠΎΠΉ ΡΡΡΠΊΠΈ.
ΠΠΏΡΠΈΠΌΠ°Π»ΡΠ½ΡΠ΅ ΠΏΡΠΎΠΏΠΎΡΡΠΈΠΈ
ΠΠ°ΠΊ ΠΏΠΎΠΊΠ°Π·ΡΠ²Π°Π΅Ρ ΠΏΡΠ°ΠΊΡΠΈΠΊΠ°, Π½Π΅ΡΠΎΠ±Π»ΡΠ΄Π΅Π½ΠΈΠ΅ ΠΌΠΈΠ½ΠΈΠΌΠ°Π»ΡΠ½ΡΡ ΡΡΠ΅Π±ΠΎΠ²Π°Π½ΠΈΠΉ ΡΡΠ΅Π²Π°ΡΠΎ Π½Π΅Π³Π°ΡΠΈΠ²Π½ΡΠΌΠΈ ΠΏΠΎΡΠ»Π΅Π΄ΡΡΠ²ΠΈΡΠΌΠΈ, ΠΊΠΎΡΠΎΡΡΠ΅ ΠΌΠΎΠ³ΡΡ ΡΡΡΠ΅ΡΡΠ²Π΅Π½Π½ΠΎ ΡΠ½ΠΈΠ·ΠΈΡΡ ΠΊΠ°ΡΠ΅ΡΡΠ²ΠΎ Π²ΠΎΠ·Π²Π΅Π΄ΡΠ½Π½ΠΎΠ³ΠΎ Π·Π΄Π°Π½ΠΈΡ. ΠΡΠΎΠΏΠΎΡΡΠΈΠΈ Π·Π°Π²ΠΈΡΡΡ ΠΎΡ ΡΠΎΠ³ΠΎ, ΠΊΠ°ΠΊΡΡ ΠΌΠ°ΡΠΊΡ ΡΠ΅ΠΌΠ΅Π½ΡΠ° Π±ΡΠ΄Π΅Ρ ΠΈΡΠΏΠΎΠ»ΡΠ·ΠΎΠ²Π°ΡΡ ΠΌΠ°ΡΡΠ΅Ρ. ΠΠΏΡΠΈΠΌΠ°Π»ΡΠ½ΠΎΠ΅ ΡΠΎΠΎΡΠ½ΠΎΡΠ΅Π½ΠΈΠ΅ ΠΊΠΎΠΌΠΏΠΎΠ½Π΅Π½ΡΠΎΠ² Π²ΡΠ³Π»ΡΠ΄ΠΈΡ ΡΠ»Π΅Π΄ΡΡΡΠΈΠΌ ΠΎΠ±ΡΠ°Π·ΠΎΠΌ:
ΠΠ»Ρ ΡΠ΅ΠΌΠ΅Π½ΡΠ° ΠΌΠ°ΡΠΊΠΈ Π10 Π½ΡΠΆΠ½ΠΎ: ΠΏΠΎΠ»Π½ΠΎΠ΅ Π²Π΅Π΄ΡΠΎ ΡΠΈΡΡΠΎΠ³ΠΎ ΠΏΠ΅ΡΠΊΠ°, 5 ΠΊΠ³ ΡΠ΅ΠΌΠ΅Π½ΡΠ° ΠΈ ΡΡΠΈ ΠΏΠΎΠ»Π½ΡΡ Π²Π΅Π΄ΡΠ° ΠΎΠΏΠΈΠ»ΠΎΠΊ.
- ΠΠΏΠΈΠ»ΠΊΠΎΠ±Π΅ΡΠΎΠ½ Π½Π° ΠΎΡΠ½ΠΎΠ²Π΅ ΡΠ΅ΠΌΠ΅Π½ΡΠ° Π15: 1.5 Π²Π΅Π΄ΡΠ° ΠΏΠ΅ΡΠΊΠ°, ΠΏΠΎΠ»Π²Π΅Π΄ΡΠ° ΡΠ΅ΠΌΠ΅Π½ΡΠ° ΠΈ 4 Π²Π΅Π΄ΡΠ° Π΄ΡΠ΅Π²Π΅ΡΠ½ΡΡ ΠΎΠΏΠΈΠ»ΠΎΠΊ.
- Π¦Π΅ΠΌΠ΅Π½Ρ Π25: 1.5 Π²Π΅Π΄ΡΠ° ΠΏΠ΅ΡΠΊΠ°, 0.5 Π²Π΅Π΄ΡΠ° ΡΠ΅ΠΌΠ΅Π½ΡΠ° ΠΈ ΡΡΠΈ Π²Π΅Π΄ΡΡΠΊΠ° ΠΎΠΏΠΈΠ»ΠΎΠΊ.
Π‘ΡΠΎΠΈΡ ΠΎΡΠΌΠ΅ΡΠΈΡΡ, ΡΡΠΎ ΠΊΠ°ΠΆΠ΄ΡΠΉ ΠΌΠ°ΡΡΠ΅Ρ Π΄ΠΎΠ»ΠΆΠ΅Π½ ΠΏΡΠΈΠ΄Π΅ΡΠΆΠΈΠ²Π°ΡΡΡΡ ΠΈΠΌΠ΅Π½Π½ΠΎ ΡΡΠΎΠΉ ΡΠ΅ΡΠ΅ΠΏΡΡΡΡ, ΡΠ°ΠΊ ΠΊΠ°ΠΊ ΡΡΠΎ Π±ΡΠ»ΠΎ ΠΏΡΠΎΠ²Π΅ΡΠ΅Π½ΠΎ Π² ΡΠ΅ΡΠ΅Π½ΠΈΠ΅ Π½Π΅ΡΠΊΠΎΠ»ΡΠΊΠΈΡ Π΄Π΅ΡΡΡΠΈΠ»Π΅ΡΠΈΠΉ. Π‘ΡΡΠΎΠΈΡΠ΅Π»Π΅ΠΉ Π½Π΅ Π΄ΠΎΠ»ΠΆΠ½ΠΎ ΡΠΌΡΡΠ°ΡΡ ΠΎΡΡΡΡΡΡΠ²ΠΈΠ΅ ΠΏΡΠΎΠ³ΡΠ΅ΡΡΠΈΠΈ Π² ΠΏΡΠΎΠΏΠΎΡΡΠΈΡΡ ΠΈ ΠΊΠΎΠ»ΠΈΡΠ΅ΡΡΠ²Π΅. Π’Π°ΠΊΠ°Ρ ΡΠ΅Π½Π΄Π΅Π½ΡΠΈΡ ΡΠ²ΡΠ·Π°Π½Π° Ρ ΡΠ΅ΠΌ, ΡΡΠΎ Π² ΠΊΠ°ΠΆΠ΄ΠΎΠΌ ΡΠ»ΡΡΠ°Π΅ ΠΊΠΎΠΌΠΏΠΎΠ½Π΅Π½ΡΡ ΡΠ°Π±ΠΎΡΠ°ΡΡ ΡΠΎΠ²Π΅ΡΡΠ΅Π½Π½ΠΎ ΠΏΠΎ-ΡΠ°Π·Π½ΠΎΠΌΡ. Π§ΡΠΎ ΠΊΠ°ΡΠ°Π΅ΡΡΡ Π³Π°ΡΡΠ½ΠΎΠΉ ΠΈΠ·Π²Π΅ΡΡΠΈ, ΡΠΎ ΠΎΠ½Π° Π½ΡΠΆΠ½Π° Π΄Π»Ρ Π½Π°Π΄ΡΠΆΠ½ΠΎΠ³ΠΎ ΠΎΠ±Π΅ΡΡΠ°Ρ Π°ΡΠΈΠ²Π°Π½ΠΈΡ ΠΎΠΏΠΈΠ»ΠΎΠΊ.
ΠΠΏΠΈΠ»ΠΊΠΎΠ±Π΅ΡΠΎΠ½. ΠΠΏΠΈΠ»ΠΊΠΈ ΠΈ ΡΠΎΡΡΠ°Π².ΠΠ»ΡΡΡ ΠΈ ΠΌΠΈΠ½ΡΡΡ.Π Π΄ΠΎΠΌΠ°ΡΠ½ΠΈΡ ΡΡΠ»ΠΎΠ²ΠΈΡΡ
ΠΠΏΠΈΠ»ΠΊΠΎΠ±Π΅ΡΠΎΠ½ β ΡΡΠΎ Π»Π΅Π³ΠΊΠΈΠΉ Π±Π΅ΡΠΎΠ½, ΡΠΎΡΡΠΎΡΡΠΈΠΉ ΠΈΠ· ΡΠΌΠ΅ΡΠΈ Π²ΠΎΠ΄Ρ, ΡΠ΅ΠΌΠ΅Π½ΡΠ°, ΠΈΠ·Π²Π΅ΡΡΠΈ, Π³Π»ΠΈΠ½Ρ, ΠΏΠ΅ΡΠΊΠ° ΠΈ ΠΎΠΏΠΈΠ»ΠΎΠΊ. ΠΠ½ ΠΏΡΠΈΠΌΠ΅Π½ΡΠ΅ΡΡΡ Π΄Π»Ρ ΠΏΡΠΎΠΈΠ·Π²ΠΎΠ΄ΡΡΠ²Π° ΡΡΡΠΎΠΈΡΠ΅Π»ΡΠ½ΡΡ Π±Π»ΠΎΠΊΠΎΠ² ΠΈ Π²ΠΎΠ·Π²Π΅Π΄Π΅Π½ΠΈΡ ΠΌΠΎΠ½ΠΎΠ»ΠΈΡΠ½ΡΡ Π·Π΄Π°Π½ΠΈΠΉ. ΠΠΎ ΡΠ²ΠΎΠ΅ΠΌΡ ΡΠΎΡΡΠ°Π²Ρ ΠΌΠ°ΡΠ΅ΡΠΈΠ°Π» ΠΏΠΎΡ ΠΎΠΆ Π½Π° Π°ΡΠ±ΠΎΠ»ΠΈΡ, Π½ΠΎ ΡΠΎΠ΄Π΅ΡΠΆΠΈΡ Π±ΠΎΠ»Π΅Π΅ ΠΌΠ΅Π»ΠΊΠΈΠΉ Π΄ΡΠ΅Π²Π΅ΡΠ½ΡΠΉ Π½Π°ΠΏΠΎΠ»Π½ΠΈΡΠ΅Π»Ρ. ΠΡΠΈΠΌΠ΅Π½Π΅Π½ΠΈΠ΅ ΠΎΠΏΠΈΠ»ΠΊΠΎΠ±Π΅ΡΠΎΠ½Π° ΡΠΊΠΎΠ»ΠΎΠ³ΠΈΡΠ΅ΡΠΊΠΈ ΡΠ΅Π»Π΅ΡΠΎΠΎΠ±ΡΠ°Π·Π½ΠΎ, ΠΏΠΎΡΠΊΠΎΠ»ΡΠΊΡ ΠΎΠ½ ΡΠ²Π»ΡΠ΅ΡΡΡ ΠΏΠΎΠ»Π½ΠΎΡΡΡΡ Π±Π΅Π·ΠΎΠΏΠ°ΡΠ½ΡΠΌ, ΠΎΡΠ²Π΅ΡΠ°Π΅Ρ ΡΠ°Π½ΠΈΡΠ°ΡΠ½ΠΎ-Π³ΠΈΠ³ΠΈΠ΅Π½ΠΈΡΠ΅ΡΠΊΠΈΠΌ ΡΡΠ΅Π±ΠΎΠ²Π°Π½ΠΈΡΠΌ, ΠΊΡΠΎΠΌΠ΅ ΡΡΠΎΠ³ΠΎ ΠΎΡΠ»ΠΈΡΠ°Π΅ΡΡΡ ΠΏΠΎΠ²ΡΡΠ΅Π½Π½ΠΎΠΉ ΡΠ΅ΠΏΠ»ΠΎΠΈΠ·ΠΎΠ»ΡΡΠΈΠ΅ΠΉ ΠΈ Π·Π²ΡΠΊΠΎΠΈΠ·ΠΎΠ»ΡΡΠΈΠ΅ΠΉ.
ΠΠ΄Π΅ ΠΈΡΠΏΠΎΠ»ΡΠ·ΡΠ΅ΡΡΡ ΠΎΠΏΠΈΠ»ΠΊΠΎΠ±Π΅ΡΠΎΠ½
ΠΠ°ΡΠ΅ΡΠΈΠ°Π» ΡΠΈΡΠΎΠΊΠΎ ΠΏΡΠΈΠΌΠ΅Π½ΡΠ΅ΡΡΡ Π² ΡΡΠ΅ΡΠ΅ ΡΡΡΠΎΠΈΡΠ΅Π»ΡΡΡΠ²Π° ΠΌΠ°Π»ΠΎΡΡΠ°ΠΆΠ½ΡΡ ΠΆΠΈΠ»ΡΡ ΠΈ Π½Π΅ΠΆΠΈΠ»ΡΡ Π·Π΄Π°Π½ΠΈΠΉ. Π§Π°ΡΠ΅ Π²ΡΠ΅Π³ΠΎ Π΅Π³ΠΎ ΠΈΡΠΏΠΎΠ»ΡΠ·ΡΡΡ ΠΏΡΠΈ Π²ΠΎΠ·Π²Π΅Π΄Π΅Π½ΠΈΠΈ Π·Π°Π³ΠΎΡΠΎΠ΄Π½ΡΡ Π΄ΠΎΠΌΠΎΠ², Π³Π°ΡΠ°ΠΆΠ΅ΠΉ, Ρ ΠΎΠ·ΡΠΉΡΡΠ²Π΅Π½Π½ΡΡ ΠΏΠΎΡΡΡΠΎΠ΅ΠΊ, ΡΠ°ΡΠ°Π΄Ρ ΠΊΠΎΡΠΎΡΡΡ ΠΏΠ»Π°Π½ΠΈΡΡΠ΅ΡΡΡ ΡΡΡΠΊΠ°ΡΡΡΠΈΡΡ, Π·Π°ΠΊΡΡΠ²Π°ΡΡ ΡΠ°ΠΉΠ΄ΠΈΠ½Π³ΠΎΠΌ, Π²Π°Π³ΠΎΠ½ΠΊΠΎΠΉ.
ΠΠ΅ΡΡΡΠΈΠ΅ Ρ Π°ΡΠ°ΠΊΡΠ΅ΡΠΈΡΡΠΈΠΊΠΈ ΠΌΠ°ΡΠ΅ΡΠΈΠ°Π»Π° ΠΈΡΠΊΠ»ΡΡΠ°ΡΡ Π²ΠΎΠ·ΠΌΠΎΠΆΠ½ΠΎΡΡΡ Π΅Π³ΠΎ ΠΈΡΠΏΠΎΠ»ΡΠ·ΠΎΠ²Π°Π½ΠΈΡ Π΄Π»Ρ Π²ΠΎΠ·Π²Π΅Π΄Π΅Π½ΠΈΡ ΠΌΠ½ΠΎΠ³ΠΎΡΡΠ°ΠΆΠ½ΡΡ Π·Π΄Π°Π½ΠΈΠΉ. ΠΠ· ΠΎΠΏΠΈΠ»ΠΊΠΎΠ±Π΅ΡΠΎΠ½Π° ΠΌΠΎΠΆΠ½ΠΎ ΡΡΡΠΎΠΈΡΡ ΠΊΠΎΡΠΎΠ±Π° Π²ΡΡΠΎΡΠΎΠΉ Π΄ΠΎ 2-Ρ ΡΡΠ°ΠΆΠ΅ΠΉ. ΠΠ»Ρ Π΅Π³ΠΎ ΠΏΡΠΈΠΌΠ΅Π½Π΅Π½ΠΈΡ ΠΏΡΠΈ ΠΊΠ»Π°Π΄ΠΊΠ΅ Π±ΠΎΠ»Π΅Π΅ Π²ΡΡΠΎΠΊΠΈΡ ΠΏΠΎΡΡΡΠΎΠ΅ΠΊ ΡΡΠ΅Π±ΡΠ΅ΡΡΡ ΠΏΡΠΎΠ²Π΅Π΄Π΅Π½ΠΈΠ΅ ΡΠΎΡΠ½ΡΡ ΠΈΠ½ΠΆΠ΅Π½Π΅ΡΠ½ΡΡ ΡΠ°ΡΡΠ΅ΡΠΎΠ², Π° ΡΠ°ΠΊΠΆΠ΅ Π·Π°Π»ΠΈΠ²ΠΊΠ° ΠΆΠ΅Π»Π΅Π·ΠΎΠ±Π΅ΡΠΎΠ½Π½ΠΎΠ³ΠΎ Π°ΡΠΌΠΎΠΏΠΎΡΡΠ° ΠΏΠΎ Π²ΡΠ΅ΠΌΡ ΠΊΠΎΠ½ΡΡΡΡ.
ΠΠ· ΠΎΠΏΠΈΠ»ΠΊΠΎΠ±Π΅ΡΠΎΠ½Π° Π½Π΅ΡΠ΅Π΄ΠΊΠΎ Π΄Π΅Π»Π°Π΅ΡΡΡ ΡΠ΅ΡΠ½ΠΎΠ²Π°Ρ ΡΡΡΠΆΠΊΠ° ΠΏΠΎΠ»Π°. ΠΠ»Ρ ΡΡΠΎΠ³ΠΎ ΠΈΡΠΏΠΎΠ»ΡΠ·ΡΠ΅ΡΡΡ ΠΌΠ°ΡΠ΅ΡΠΈΠ°Π» ΠΌΠ°Π»ΡΡ ΠΌΠ°ΡΠΎΠΊ Π5 ΠΈ Π10. Π‘Π²Π΅ΡΡ Ρ ΡΡΡΠΆΠΊΠΈ ΠΌΠΎΠ³ΡΡ ΡΠΊΠ»Π°Π΄ΡΠ²Π°ΡΡΡΡ Π»Π°Π³ΠΈ Π΄ΠΎΡΠ°ΡΠΎΠ³ΠΎ ΠΏΠΎΠ»Π°, Π»Π°ΠΌΠΈΠ½Π°Ρ, ΠΏΠ°ΡΠΊΠ΅Ρ ΠΈ Ρ.Π΄. Π‘ΡΡΠΆΠΊΠ° ΡΠΎΠ²ΠΌΠ΅ΡΡΠΈΠΌΠ° Ρ ΡΠΈΡΡΠ΅ΠΌΠΎΠΉ Π²ΠΎΠ΄ΡΠ½ΠΎΠ³ΠΎ ΠΈ ΡΠ»Π΅ΠΊΡΡΠΈΡΠ΅ΡΠΊΠΎΠ³ΠΎ ΡΠ΅ΠΏΠ»ΠΎΠ³ΠΎ ΠΏΠΎΠ»Π°.
ΠΡΠ΅ΠΈΠΌΡΡΠ΅ΡΡΠ²Π° ΠΎΠΏΠΈΠ»ΠΊΠΎΠ±Π΅ΡΠΎΠ½Π°
ΠΠ»Π°Π²Π½ΡΠΌ Π΄ΠΎΡΡΠΎΠΈΠ½ΡΡΠ²ΠΎΠΌ ΠΌΠ°ΡΠ΅ΡΠΈΠ°Π»Π° ΡΠ²Π»ΡΠ΅ΡΡΡ ΠΏΡΠΈΠΌΠ΅Π½Π΅Π½ΠΈΠ΅ ΠΏΡΠΈ Π΅Π³ΠΎ ΠΏΡΠΎΠΈΠ·Π²ΠΎΠ΄ΡΡΠ²Π΅ Π²ΡΠΎΡΡΡΡΡΡ. ΠΡΠΈ ΡΡΠΎΠΌ ΠΎΠΏΠΈΠ»ΠΊΠΈ Π² Π±Π΅ΡΠΎΠ½Π΅ Π½Π΅ ΠΏΠΎΠ΄Π²Π΅ΡΠ³Π°ΡΡΡΡ Π³ΠΎΡΠ΅Π½ΠΈΡ ΠΈ Π³Π½ΠΈΠ΅Π½ΠΈΡ, ΠΏΠΎΡΡΠΎΠΌΡ Π»ΠΈΡΠ΅Π½Ρ ΡΠ²ΠΎΠΈΡ ΠΎΡΠ½ΠΎΠ²Π½ΡΡ Π½Π΅Π΄ΠΎΡΡΠ°ΡΠΊΠΎΠ². ΠΡ ΠΏΡΠΈΠΌΠ΅Π½Π΅Π½ΠΈΠ΅ ΠΏΡΠΈ ΠΏΡΠΎΠΈΠ·Π²ΠΎΠ΄ΡΡΠ²Π΅ ΠΎΠΏΠΈΠ»ΠΊΠΎΠ±Π΅ΡΠΎΠ½Π° Π΄Π΅Π»Π°Π΅Ρ Π΅Π³ΠΎ Π΄Π΅ΡΠ΅Π²ΡΠΌ ΠΈ Π΄ΠΎΡΡΡΠΏΠ½ΡΠΌ.
ΠΡΠΎΠΌΠ΅ ΠΏΠΎΠ»ΡΠ·Ρ ΡΠ°ΡΠΈΠΎΠ½Π°Π»ΡΠ½ΠΎΠ³ΠΎ ΠΏΡΠΈΠΌΠ΅Π½Π΅Π½ΠΈΡ ΠΎΡΡ ΠΎΠ΄ΠΎΠ² Π»Π΅ΡΠΎΠΏΠΈΠ»ΠΎΠΊ, Π²ΡΠ±ΠΎΡ Π΄Π»Ρ ΡΡΡΠΎΠΈΡΠ΅Π»ΡΡΡΠ²Π° ΠΎΠΏΠΈΠ»ΠΊΠΎΠ±Π΅ΡΠΎΠ½Π° ΠΈΠΌΠ΅Π΅Ρ ΠΈ Π΄ΡΡΠ³ΠΈΠ΅ ΠΏΠΎΠ»ΠΎΠΆΠΈΡΠ΅Π»ΡΠ½ΡΠ΅ ΡΡΠΎΡΠΎΠ½Ρ:
- ΠΡΡΠΎΠΊΠΈΠ΅ ΡΠ΅ΠΏΠ»ΠΎΠ·Π°ΡΠΈΡΠ½ΡΠ΅ ΠΊΠ°ΡΠ΅ΡΡΠ²Π°.
- Π₯ΠΎΡΠΎΡΠ°Ρ Π·Π²ΡΠΊΠΎΠΈΠ·ΠΎΠ»ΡΡΠΈΡ.
- ΠΠ°Π»ΡΠΉ Π²Π΅Ρ ΠΏΠΎΡΡΡΠΎΠ΅Π½Π½ΡΡ ΠΊΠΎΠ½ΡΡΡΡΠΊΡΠΈΠΉ.
- ΠΡΡΠΎΠΊΠ°Ρ ΡΡΡΠΎΠΉΡΠΈΠ²ΠΎΡΡΡ ΠΊ ΡΠ°ΡΡΡΠΆΠ΅Π½ΠΈΡ.
- ΠΠ³Π½Π΅ΡΠΏΠΎΡΠ½ΠΎΡΡΡ Π½Π΅ΡΠΊΠΎΠ»ΡΠΊΠΎ ΡΠ°ΡΠΎΠ² ΠΏΡΠΈ ΡΠ΅ΠΌΠΏΠ΅ΡΠ°ΡΡΡΠ΅ ΠΏΠ»Π°ΠΌΠ΅Π½ΠΈ 1200Β°Π‘.
- ΠΡΠΎΡΡΠΎΠΉ ΡΠ°ΡΠΏΠΈΠ».
ΠΡΠΎ ΠΏΡΠ°ΠΊΡΠΈΡΠ΅ΡΠΊΠΈ ΠΈΠ΄Π΅Π°Π»ΡΠ½ΡΠΉ ΡΡΡΠΎΠΈΡΠ΅Π»ΡΠ½ΡΠΉ ΠΌΠ°ΡΠ΅ΡΠΈΠ°Π» ΡΠΎΠΎΡΠ²Π΅ΡΡΡΠ²ΡΡΡΠΈΠΉ ΡΠΎΠ²ΡΠ΅ΠΌΠ΅Π½Π½ΡΠΌ ΡΠ°Π½ΠΈΡΠ°ΡΠ½ΠΎ-Π³ΠΈΠ³ΠΈΠ΅Π½ΠΈΡΠ΅ΡΠΊΠΈΠΌ Π½ΠΎΡΠΌΠ°ΠΌ. Π₯ΠΎΡΡ Π² Π΅Π³ΠΎ ΡΠΎΡΡΠ°Π²Π΅ ΠΈ Π½Π°Ρ ΠΎΠ΄ΡΡΡΡ Π²ΠΎΠ»ΠΎΠΊΠ½Π° Π΄ΡΠ΅Π²Π΅ΡΠΈΠ½Ρ, Π½ΠΎ Π² ΡΠ΅ΠΌΠ΅Π½ΡΠ½ΠΎΠΉ ΡΡΠ΅Π΄Π΅ ΠΎΠ½ΠΈ Π½Π΅ ΠΌΠΎΠ³ΡΡ Π²ΡΡΡΡΠΏΠΈΡΡ ΡΡΠ±ΡΡΡΠ°ΡΠΎΠΌ Π΄Π»Ρ ΡΠ°Π·Π²Π΅Π΄Π΅Π½ΠΈΡ ΠΏΠ»Π΅ΡΠ΅Π½ΠΈ, Π³ΡΠΈΠ±ΠΊΠ°, ΠΊΠΎΠ½Π΅ΡΠ½ΠΎ ΠΏΡΠΈ ΠΎΡΡΡΡΡΡΠ²ΠΈΠΈ ΡΡΠ΅Π·ΠΌΠ΅ΡΠ½ΠΎΠΉ Π²Π»Π°ΠΆΠ½ΠΎΡΡΠΈ. ΠΡΠ΄Π΅Π»ΡΠ½ΠΎΠ³ΠΎ Π²Π½ΠΈΠΌΠ°Π½ΠΈΡ Π·Π°ΡΠ»ΡΠΆΠΈΠ²Π°ΡΡ ΡΠ΅ΠΏΠ»ΠΎΠΈΠ·ΠΎΠ»ΡΡΠΈΠΎΠ½Π½ΡΠ΅ ΠΊΠ°ΡΠ΅ΡΡΠ²Π° ΠΌΠ°ΡΠ΅ΡΠΈΠ°Π»Π°. Π‘ΡΠ΅Π½Π° ΠΈΠ· ΠΎΠΏΠΈΠ»ΠΊΠΎΠ±Π΅ΡΠΎΠ½Π° ΡΠΎΠ»ΡΠΈΠ½ΠΎΠΉ Π²ΡΠ΅Π³ΠΎ 30 ΡΠΌ ΡΠΎΠΏΠΎΡΡΠ°Π²ΠΈΠΌΠ° ΠΏΠΎ ΡΠ΅ΠΏΠ»ΠΎΠ·Π°ΡΠΈΡΠ½ΡΠΌ ΡΠ²ΠΎΠΉΡΡΠ²Π°ΠΌ Ρ ΠΊΠΈΡΠΏΠΈΡΠ½ΠΎΠΉ ΠΊΠ»Π°Π΄ΠΊΠΎΠΉ ΡΠΈΡΠΈΠ½ΠΎΠΉ 1 ΠΌ. ΠΠΎΠΌΠ° ΠΈΠ· ΠΎΠΏΠΈΠ»ΠΊΠΎΠ±Π΅ΡΠΎΠ½Π° ΡΠ΅ΠΏΠ»ΡΠ΅, ΠΈΡ ΡΠΎΠ΄Π΅ΡΠΆΠ°Π½ΠΈΠ΅ Π½Π° ΠΎΡΠΎΠΏΠ»Π΅Π½ΠΈΠ΅ ΠΈ ΠΊΠΎΠ½Π΄ΠΈΡΠΈΠΎΠ½ΠΈΡΠΎΠ²Π°Π½ΠΈΠ΅ ΠΎΠ±Ρ ΠΎΠ΄ΠΈΡΡΡ Π΄Π΅ΡΠ΅Π²Π»Π΅.
Π ΡΡΠ°Π²Π½Π΅Π½ΠΈΠΈ Ρ ΠΊΠ»Π°ΡΡΠΈΡΠ΅ΡΠΊΠΈΠΌ Π±Π΅ΡΠΎΠ½ΠΎΠΌ ΠΎΠΏΠΈΠ»ΠΊΠΎΠ±Π΅ΡΠΎΠ½ Π½Π° ΠΏΠΎΡΡΠ΄ΠΎΠΊ Π»Π΅Π³ΡΠ΅. ΠΠ³ΠΎ ΠΏΡΠΈΠΌΠ΅Π½Π΅Π½ΠΈΠ΅ Π² ΡΡΡΠΎΠΈΡΠ΅Π»ΡΡΡΠ²Π΅ ΠΏΠΎΠ·Π²ΠΎΠ»ΡΠ΅Ρ Π·Π°Π»ΠΈΠ²Π°ΡΡ Π±ΠΎΠ»Π΅Π΅ Π»Π΅Π³ΠΊΠΈΠΉ ΡΡΠ½Π΄Π°ΠΌΠ΅Π½Ρ, ΡΡΠΎ ΡΡΡΠ΅ΡΡΠ²Π΅Π½Π½ΠΎ ΡΠ½ΠΈΠΆΠ°Π΅Ρ ΠΎΠ±ΡΡΡ ΡΠΌΠ΅ΡΡ ΡΡΡΠΎΠΈΡΠ΅Π»ΡΡΡΠ²Π°. ΠΡΠΎΠΌΠ΅ ΡΡΠΎΠ³ΠΎ, ΡΡΠ΅Π½Ρ ΠΈΠ· ΠΎΠΏΠΈΠ»ΠΊΠΎΠ±Π΅ΡΠΎΠ½Π° ΡΠΏΠΎΡΠΎΠ±Π½Ρ ΠΏΠ΅ΡΠ΅Π½ΠΎΡΠΈΡΡ ΡΠ΄Π°ΡΡ, Π²ΠΎΠ·Π΄Π΅ΠΉΡΡΠ²ΠΈΠ΅ Π½Π° ΡΠ°ΡΡΡΠΆΠ΅Π½ΠΈΠ΅ ΠΈ ΠΈΠ·Π³ΠΈΠ±. ΠΠ° Π½ΠΈΡ Π³ΠΎΡΠ°Π·Π΄ΠΎ ΡΠ΅ΠΆΠ΅ ΠΏΠΎΡΠ²Π»ΡΡΡΡΡ ΡΡΠ΅ΡΠΈΠ½Ρ, ΡΠ΅ΠΌ Π½Π° ΠΊΠ»Π°Π΄ΠΊΠ΅ ΠΈΠ· ΠΊΠΈΡΠΏΠΈΡΠ°, ΡΠ»Π°ΠΊΠΎΠ±Π»ΠΎΠΊΠ°, Π³Π°Π·ΠΎΠ±Π»ΠΎΠΊΠ°, ΠΏΠ΅Π½ΠΎΠ±Π΅ΡΠΎΠ½Π°.
Π‘ΡΠ΅Π½Ρ ΠΈΠ· ΠΎΠΏΠΈΠ»ΠΊΠΎΠ±Π΅ΡΠΎΠ½Π° Π½Π΅ Π³ΠΎΡΡΡ. Π₯ΠΎΡΡ ΠΎΠ½ΠΈ ΡΠΎΠ΄Π΅ΡΠΆΠ°Ρ Π² ΡΠ΅Π±Π΅ Π΄ΡΠ΅Π²Π΅ΡΠΈΠ½Ρ, Π½ΠΎ ΡΠΏΠΎΡΠΎΠ±Π½Ρ ΠΊΠ°ΠΊ ΠΌΠΈΠ½ΠΈΠΌΡΠΌ Π½Π΅ΡΠΊΠΎΠ»ΡΠΊΠΎ ΡΠ°ΡΠΎΠ² ΠΏΠ΅ΡΠ΅Π½ΠΎΡΠΈΡΡ ΠΏΡΡΠΌΠΎΠ΅ Π²ΠΎΠ·Π΄Π΅ΠΉΡΡΠ²ΠΈΠ΅ ΠΏΠ»Π°ΠΌΠ΅Π½ΠΈ ΡΠ΅ΠΌΠΏΠ΅ΡΠ°ΡΡΡΠΎΠΉ 1200Β°Π‘. ΠΡΠΈ ΡΡΠΎΠΌ ΠΏΠΎΠ²Π΅ΡΡ Π½ΠΎΡΡΡ ΠΏΡΠΎΡΡΠΎ ΠΎΠ±ΡΠ³Π»ΠΈΠ²Π°Π΅ΡΡΡ, Π²ΡΠ΄Π΅Π»ΡΡ Π½Π΅Π±ΠΎΠ»ΡΡΠΎΠ΅ ΠΊΠΎΠ»ΠΈΡΠ΅ΡΡΠ²ΠΎ Π΄ΡΠΌΠ°. ΠΡΠΈ ΠΎΠ±ΡΠ³Π»ΠΈΠ²Π°Π½ΠΈΠΈ ΡΡΠ΅Π½Π° ΠΏΠΎΡΡΠ΅ΠΏΠ΅Π½Π½ΠΎ ΠΈΡΡΠΎΠ½ΡΠ°Π΅ΡΡΡ, ΡΡΠΎ ΠΏΡΠΎΠΈΡΡ ΠΎΠ΄ΠΈΡ ΠΊΡΠ°ΠΉΠ½Π΅ ΠΌΠ΅Π΄Π»Π΅Π½Π½ΠΎ.
ΠΠΎΠ»ΠΎΠΆΠΈΡΠ΅Π»ΡΠ½ΡΠΌ ΠΌΠΎΠΌΠ΅Π½ΡΠΎΠΌ ΡΠ²Π»ΡΠ΅ΡΡΡ ΠΈ ΡΠ΄ΠΎΠ±ΡΡΠ²ΠΎ ΡΠ°Π±ΠΎΡΡ Ρ ΠΎΠΏΠΈΠ»ΠΊΠΎΠ±Π΅ΡΠΎΠ½Π½ΡΠΌΠΈ Π±Π»ΠΎΠΊΠ°ΠΌΠΈ, ΠΏΠ°Π½Π΅Π»ΡΠΌΠΈ. ΠΡΠΈ Π½Π΅ΠΎΠ±Ρ ΠΎΠ΄ΠΈΠΌΠΎΡΡΠΈ ΠΎΠ½ΠΈ Π΄ΠΎΡΡΠ°ΡΠΎΡΠ½ΠΎ ΠΏΡΠΎΡΡΠΎ ΡΠ°ΡΠΏΠΈΠ»ΠΈΠ²Π°ΡΡΡΡ Π½ΠΎΠΆΠΎΠ²ΠΊΠΎΠΉ, Π±Π΅Π½Π·ΠΎΠΏΠΈΠ»ΠΎΠΉ. ΠΡΠΎ ΠΎΡΠ΅Π½Ρ Π²Π°ΠΆΠ½ΠΎ Π΄Π»Ρ ΡΠΎΠ±Π»ΡΠ΄Π΅Π½ΠΈΡ ΡΠ°Π³Π° ΡΠΊΠ»Π°Π΄ΠΊΠΈ. Π Π΄Π°Π»ΡΠ½Π΅ΠΉΡΠ΅ΠΌ ΡΡΠ΅Π½Π° ΠΈΠ· ΡΠ°ΠΊΠΎΠ³ΠΎ ΠΌΠ°ΡΠ΅ΡΠΈΠ°Π»Π° ΠΎΡΠ»ΠΈΡΠ½ΠΎ ΡΠ΄Π΅ΡΠΆΠΈΠ²Π°Π΅Ρ ΡΠ°ΠΌΠΎΡΠ΅Π·Ρ Π±Π΅Π· Π΄ΡΠ±Π΅Π»Π΅ΠΉ. ΠΠ° Π½ΠΈΡ ΠΌΠΎΠΆΠ½ΠΎ Π±Π΅Π· ΠΎΠΏΠ°ΡΠΊΠΈ Π½Π°Π²Π΅ΡΠΈΠ²Π°ΡΡ ΠΊΠΎΠ½Π΄ΠΈΡΠΈΠΎΠ½Π΅Ρ, ΠΊΡΡ ΠΎΠ½Π½ΡΠ΅ ΡΠΊΠ°ΡΡΠΈΠΊΠΈ, ΠΏΠΎΠ»ΠΊΠΈ.
ΠΠ΅Π΄ΠΎΡΡΠ°ΡΠΊΠΈ ΠΎΠΏΠΈΠ»ΠΊΠΎΠ±Π΅ΡΠΎΠ½Π°
ΠΠ»Π°Π²Π½ΡΠΌ ΠΈ Π΅Π΄ΠΈΠ½ΡΡΠ²Π΅Π½Π½ΡΠΌ Π½Π΅Π΄ΠΎΡΡΠ°ΡΠΊΠΎΠΌ ΠΎΠΏΠΈΠ»ΠΊΠΎΠ±Π΅ΡΠΎΠ½Π° Π²ΡΡΡΡΠΏΠ°Π΅Ρ ΡΡΠΎΠ²Π΅Π½Ρ Π΅Π³ΠΎ Π²Π»Π°Π³ΠΎΠΏΠΎΠ³Π»ΠΎΡΠ΅Π½ΠΈΡ. Π Π·Π°Π²ΠΈΡΠΈΠΌΠΎΡΡΠΈ ΠΎΡ ΠΏΠ»ΠΎΡΠ½ΠΎΡΡΠΈ ΠΌΠ°ΡΠ΅ΡΠΈΠ°Π»Π°, Π²ΠΏΠΈΡΡΠ²Π°Π΅ΠΌΠΎΡΡΡ ΠΌΠΎΠΆΠ΅Ρ ΡΠΎΡΡΠ°Π²Π»ΡΡΡ ΠΎΡ 8 Π΄ΠΎ 12%.Β ΠΠ°ΠΆΠ΅ ΠΏΡΠΈ Π΄ΠΎΠ±Π°Π²Π»Π΅Π½ΠΈΠΈ Π² ΡΠ°ΡΡΠ²ΠΎΡ ΠΎΠΏΠΈΠ»ΠΊΠΎΠ±Π΅ΡΠΎΠ½Π° ΡΠΏΠ΅ΡΠΈΠ°Π»ΡΠ½ΡΡ Π²ΠΎΠ΄ΠΎΠΎΡΡΠ°Π»ΠΊΠΈΠ²Π°ΡΡΠΈΡ ΡΠΎΡΡΠ°Π²ΠΎΠ², ΡΡΠΎΠ²Π΅Π½Ρ ΠΏΠΎΠ³Π»ΠΎΡΠ΅Π½ΠΈΡ Π²Π»Π°Π³ΠΈ ΠΌΠΎΠΆΠ΅Ρ ΡΠ½ΠΈΠ·ΠΈΡΡΡΡ Π»ΠΈΡΡ Π½Π° 2%. ΠΠΌΠ΅Π½Π½ΠΎ ΠΏΠΎΡΡΠΎΠΌΡ Π·Π΄Π°Π½ΠΈΡ ΠΈΠ· ΡΠ°ΠΊΠΎΠ³ΠΎ Π±Π΅ΡΠΎΠ½Π° Π΄ΠΎΠ»ΠΆΠ½Ρ ΠΈΠΌΠ΅ΡΡ ΠΊΡΠΎΠ²Π»Ρ Ρ ΡΠΈΡΠΎΠΊΠΈΠΌΠΈ ΡΠΊΠ°ΡΠ°ΠΌΠΈ, ΡΡΠΎ ΠΈΡΠΊΠ»ΡΡΠ°Π΅Ρ Π²ΠΎΠ·ΠΌΠΎΠΆΠ½ΠΎΡΡΡ Π½Π°ΠΌΠΎΠΊΠ°Π½ΠΈΡ ΡΠ°ΡΠ°Π΄ΠΎΠ².
Π‘ΠΈΠ»ΡΠ½ΠΎΠ΅ ΠΏΠΎΠ³Π»ΠΎΡΠ΅Π½ΠΈΠ΅ Π²Π»Π°Π³ΠΈ ΡΠ°ΠΊΠΆΠ΅ ΡΠΎΠ·Π΄Π°Π΅Ρ ΠΎΠΏΡΠ΅Π΄Π΅Π»Π΅Π½Π½ΡΠ΅ ΡΡΡΠ΄Π½ΠΎΡΡΠΈ ΠΏΡΠΈ ΡΡΡΠΎΠΈΡΠ΅Π»ΡΡΡΠ²Π΅. ΠΠ»Π°Π΄ΠΊΠ° Π½ΡΠΆΠ΄Π°Π΅ΡΡΡ Π² ΠΊΠ°ΡΠ΅ΡΡΠ²Π΅Π½Π½ΠΎΠΌ ΡΠΊΡΡΠ²Π°Π½ΠΈΠΈ ΠΏΠ»Π΅Π½ΠΊΠΎΠΉ Π½Π° Π²ΡΠ΅ΠΌΡ ΠΎΡΠ°Π΄ΠΊΠΎΠ². Π’Π°ΠΊΠΆΠ΅ Π½Π΅ ΡΠ΅ΠΊΠΎΠΌΠ΅Π½Π΄ΡΠ΅ΡΡΡ ΠΏΡΠΎΠ²ΠΎΠ΄ΠΈΡΡ ΡΡΡΠΎΠΈΡΠ΅Π»ΡΡΡΠ²ΠΎ Ρ ΡΠ°Π½ΠΈΠΌΡΠΌ ΠΏΠΎΠ΄ ΠΎΡΠΊΡΡΡΡΠΌ Π½Π΅Π±ΠΎΠΌ ΠΌΠ°ΡΠ΅ΡΠΈΠ°Π»ΠΎΠΌ, Π½Π΅ Π·Π°ΡΠΈΡΠ΅Π½Π½ΡΠΌ Π΄Π°ΠΆΠ΅ Π½Π°Π²Π΅ΡΠΎΠΌ. ΠΠ½ Π½Π°ΠΌΠ½ΠΎΠ³ΠΎ ΡΡΠΆΠ΅Π»Π΅Π΅, Π½Π΅ ΠΈΠΌΠ΅Π΅Ρ ΠΌΠ°ΠΊΡΠΈΠΌΠ°Π»ΡΠ½ΠΎΠΉ ΠΌΠ°ΡΠΎΡΠ½ΠΎΠΉ ΠΏΡΠΎΡΠ½ΠΎΡΡΠΈ.
Π’ΡΠ΅Π±ΠΎΠ²Π°Π½ΠΈΡ ΠΊ ΠΎΠΏΠΈΠ»ΠΊΠ°ΠΌ Π΄Π»Ρ ΠΏΡΠΎΠΈΠ·Π²ΠΎΠ΄ΡΡΠ²Π° ΠΎΠΏΠΈΠ»ΠΊΠΎΠ±Π΅ΡΠΎΠ½Π°
ΠΠ»Ρ ΠΈΠ·Π³ΠΎΡΠΎΠ²Π»Π΅Π½ΠΈΡ ΠΎΠΏΠΈΠ»ΠΊΠΎΠ±Π΅ΡΠΎΠ½Π° ΠΌΠΎΠ³ΡΡ ΠΈΡΠΏΠΎΠ»ΡΠ·ΠΎΠ²Π°ΡΡΡΡ Π»ΡΠ±ΡΠ΅ ΠΏΡΠΎΡΠ΅ΡΠ½Π½ΡΠ΅ ΠΎΠΏΠΈΠ»ΠΊΠΈ, Π½ΠΎ ΠΎΡ ΠΈΡ ΠΊΠ°ΡΠ΅ΡΡΠ²Π° Π·Π°Π²ΠΈΡΡΡ Π΄Π°Π»ΡΠ½Π΅ΠΉΡΠΈΠ΅ ΡΠΊΡΠΏΠ»ΡΠ°ΡΠ°ΡΠΈΠΎΠ½Π½ΡΠ΅ Ρ Π°ΡΠ°ΠΊΡΠ΅ΡΠΈΡΡΠΈΠΊΠΈ ΡΠ°ΡΡΠ²ΠΎΡΠ°. ΠΠ°ΠΈΠ±ΠΎΠ»Π΅Π΅ ΡΠ΄Π°ΡΠ½ΡΠΌ ΡΠ΅ΡΠ΅Π½ΠΈΠ΅ΠΌ ΡΡΠΈΡΠ°Π΅ΡΡΡ ΠΏΡΠΈΠΌΠ΅Π½Π΅Π½ΠΈΠ΅ ΠΎΠΏΠΈΠ»ΠΎΠΊ Ρ ΡΡΠ°ΠΊΡΠΈΠ΅ΠΉ ΡΠ°ΡΡΠΈΡ 1-5 ΠΌΠΌ ΠΈΠ· Ρ Π²ΠΎΠΉΠ½ΡΡ Π΄Π΅ΡΠ΅Π²ΡΠ΅Π². Π‘Π°ΠΌΡΠΌ Π΄ΠΎΠ»Π³ΠΎΠ²Π΅ΡΠ½ΡΠΌ ΡΠ²Π»ΡΠ΅ΡΡΡ ΠΎΠΏΠΈΠ»ΠΊΠΎΠ±Π΅ΡΠΎΠ½ Π½Π° ΠΎΡΠ½ΠΎΠ²Π΅ Π΅Π»ΠΎΠ²ΡΡ ΠΎΠΏΠΈΠ»ΠΎΠΊ. ΠΡΠΏΠΎΠ»ΡΠ·ΡΠ΅ΠΌΡΠΉ Π½Π°ΠΏΠΎΠ»Π½ΠΈΡΠ΅Π»Ρ Π΄ΠΎΠ»ΠΆΠ΅Π½ Π±ΡΡΡ ΠΏΡΠΎΡΠ΅ΡΠ½Π½ΡΠΌ. ΠΡΠΈΡΡΡΡΡΠ²ΠΈΠ΅ Π΄ΡΠ΅Π²Π΅ΡΠ½ΠΎΠΉ ΠΏΡΠ»ΠΈ ΡΠ½ΠΈΠΆΠ°Π΅Ρ ΡΠ²ΡΠ·ΡΡΡΠΈΠ΅ ΠΊΠ°ΡΠ΅ΡΡΠ²Π°.
Π‘ΠΎΡΡΠ°Π² ΠΈ ΡΡΠ°ΠΊΡΠΈΡ ΠΎΠΏΠΈΠ»ΠΎΠΊ Π²Π»ΠΈΡΠ΅Ρ Π½Π° ΡΠΊΠΎΡΠΎΡΡΡ ΠΎΡΠ²Π΅ΡΠ΄Π΅Π²Π°Π½ΠΈΡ ΠΌΠ°ΡΠ΅ΡΠΈΠ°Π»Π°. ΠΡΠ΅Π²Π΅ΡΠΈΠ½Π° ΡΠΎΠ΄Π΅ΡΠΆΠΈΡ ΡΠ°Ρ Π°Ρ, Π²Π»ΠΈΡΡΡΠΈΠΉ Π½Π° ΡΠ°Π±ΠΎΡΠΈΠ΅ Ρ Π°ΡΠ°ΠΊΡΠ΅ΡΠΈΡΡΠΈΠΊΠΈ ΡΠ΅ΠΌΠ΅Π½ΡΠ°. ΠΡ Π΅Π³ΠΎ ΠΊΠΎΠ½ΡΠ΅Π½ΡΡΠ°ΡΠΈΠΈ Π·Π°Π²ΠΈΡΠΈΡ, ΠΊΠ°ΠΊ Π±ΡΡΡΡΠΎ ΠΈΠ·Π΄Π΅Π»ΠΈΠ΅ ΠΈΠ· ΠΎΠΏΠΈΠ»ΠΊΠΎΠ±Π΅ΡΠΎΠ½Π° ΡΡΠ°Π½Π΅Ρ Π΄ΠΎΡΡΠ°ΡΠΎΡΠ½ΠΎ ΠΏΡΠΎΡΠ½ΡΠΌ Π΄Π»Ρ ΠΏΡΠΈΠΌΠ΅Π½Π΅Π½ΠΈΡ. ΠΡΠΈ ΠΈΡΠΏΠΎΠ»ΡΠ·ΠΎΠ²Π°Π½ΠΈΠΈ ΠΎΠΏΠΈΠ»ΠΎΠΊ ΠΈΠ· Π΅Π»ΠΊΠΈ, ΠΏΠΎΠ²Π΅ΡΡ Π½ΠΎΡΡΡ Π·Π°ΡΠ²Π΅ΡΠ΄Π΅Π΅Ρ Π·Π° 10 ΡΠ°ΡΠΎΠ². ΠΡΠΈ ΠΏΡΠΈΠΌΠ΅Π½Π΅Π½ΠΈΠΈ ΡΠΎΡΠ½ΠΎΠ²ΠΎΠ³ΠΎ Π²ΡΠΎΡΡΡΡΡΡ Π·Π° 15 ΡΠ°ΡΠΎΠ², Π° ΠΏΡΠΈ Π΄ΠΎΠ±Π°Π²Π»Π΅Π½ΠΈΠΈ ΠΎΠΏΠΈΠ»ΠΎΠΊ Π»ΠΈΡΡΠ²Π΅Π½Π½ΡΡ ΠΏΠΎΡΠΎΠ΄ Π±Π΅ΡΠΎΠ½ Π·Π°ΡΡΡΠ²Π°Π΅Ρ Π½Π΅ ΠΌΠ΅Π½Π΅Π΅ ΡΠ΅ΠΌ Π·Π° 4 ΡΡΡΠΎΠΊ.
ΠΠ»Ρ ΡΠ½ΠΈΠΆΠ΅Π½ΠΈΡ Π²Π»ΠΈΡΠ½ΠΈΡ ΠΎΠΏΠΈΠ»ΠΎΠΊ Π½Π° ΡΠ΅ΠΌΠ΅Π½Ρ, ΠΈΡ ΠΌΠΎΠΆΠ½ΠΎ ΠΏΡΠ΅Π΄Π²Π°ΡΠΈΡΠ΅Π»ΡΠ½ΠΎ ΠΎΠ±ΡΠ°Π±ΠΎΡΠ°ΡΡ. ΠΠ»Ρ ΡΡΠΎΠ³ΠΎ ΠΏΡΠΈΠΌΠ΅Π½ΡΡΡΡΡ ΡΠΏΠ΅ΡΠΈΠ°Π»ΠΈΠ·ΠΈΡΠΎΠ²Π°Π½Π½ΡΠ΅ Ρ ΠΈΠΌΠΈΡΠ΅ΡΠΊΠΈΠ΅ ΡΠΎΡΡΠ°Π²Ρ ΠΈΠ»ΠΈ ΠΎΠ±ΡΡΠ½ΠΎΠ΅ Π²ΡΠ΄Π΅ΡΠΆΠΈΠ²Π°Π½ΠΈΠ΅ Π½Π° ΠΎΡΠΊΡΡΡΠΎΠΌ Π²ΠΎΠ·Π΄ΡΡ Π΅. ΠΠΏΠΈΠ»ΠΊΠΈ Ρ Π²ΠΎΠΉΠ½ΡΡ ΠΏΠΎΡΠΎΠ΄ ΠΌΠΎΠ³ΡΡ ΠΎΠΊΠΈΡΠ»ΡΡΡΡΡ Π½Π° ΡΠΎΠ»Π½ΡΠ΅ Π·Π° 3 ΠΌΠ΅ΡΡΡΠ°, ΠΏΠΎΡΠ»Π΅ ΡΠ΅Π³ΠΎ ΠΏΡΠΈΠΎΠ±ΡΠ΅ΡΠ°ΡΡ Π½Π΅ΠΎΠ±Ρ ΠΎΠ΄ΠΈΠΌΡΠ΅ ΠΊΠ°ΡΠ΅ΡΡΠ²Π° Π΄Π»Ρ ΠΏΡΠΎΠΈΠ·Π²ΠΎΠ΄ΡΡΠ²Π° ΡΠ²Π΅ΡΠ΄ΠΎΠ³ΠΎ ΠΏΡΠΎΡΠ½ΠΎΠ³ΠΎ ΠΎΠΏΠΈΠ»ΠΊΠΎΠ±Π΅ΡΠΎΠ½Π°. Π£ΡΠΊΠΎΡΠΈΡΡ Π΄Π°Π½Π½ΡΠΉ ΠΏΡΠΎΡΠ΅ΡΡ ΠΌΠΎΠΆΠ½ΠΎ Π²ΡΠ΄Π΅ΡΠΆΠ°Π² ΠΈΡ Π² Π²ΠΎΠ΄Π΅, Π° ΠΏΠΎΡΠΎΠΌ ΠΏΠΎΠ»Π½ΠΎΡΡΡΡ Π²ΡΡΡΡΠΈΠ² ΠΏΠΎΠ΄ Π΅ΡΡΠ΅ΡΡΠ²Π΅Π½Π½ΡΠΌΠΈ ΡΠΎΠ»Π½Π΅ΡΠ½ΡΠΌΠΈ Π»ΡΡΠ°ΠΌΠΈ.
ΠΠ°ΠΌΠ°ΡΠΈΠ²Π°Π½ΠΈΠ΅ ΠΈ ΡΡΡΠΊΠ° ΠΏΡΠΈΠΌΠ΅Π½ΡΡΡΡΡ ΡΠΎΠ»ΡΠΊΠΎ ΠΏΡΠΈ ΠΊΡΡΡΠ°ΡΠ½ΠΎΠΌ Π΄ΠΎΠΌΠ°ΡΠ½Π΅ΠΌ ΠΏΡΠΎΠΈΠ·Π²ΠΎΠ΄ΡΡΠ²Π΅ ΠΎΠΏΠΈΠ»ΠΊΠΎΠ±Π΅ΡΠΎΠ½Π° Π΄Π»Ρ ΡΠΎΠ±ΡΡΠ²Π΅Π½Π½ΡΡ Π½ΡΠΆΠ΄. ΠΡΠΈ Π΅Π³ΠΎ ΠΈΠ·Π³ΠΎΡΠΎΠ²Π»Π΅Π½ΠΈΠΈ Π² ΠΏΡΠΎΠΌΡΡΠ»Π΅Π½Π½ΡΡ ΠΌΠ°ΡΡΡΠ°Π±Π°Ρ ΠΈΡΠΏΠΎΠ»ΡΠ·ΡΠ΅ΡΡΡ ΠΎΠ±ΡΠ°Π±ΠΎΡΠΊΠ° ΠΆΠΈΠ΄ΠΊΠΈΠΌ ΡΡΠ΅ΠΊΠ»ΠΎΠΌ ΠΈ Ρ Π»ΠΎΡΠΈΡΡΡΠΌ ΠΊΠ°Π»ΡΡΠΈΠ΅ΠΌ. ΠΠΎΠ±Π°Π²Π»Π΅Π½ΠΈΠ΅ ΠΆΠΈΠ΄ΠΊΠΎΠ³ΠΎ ΡΡΠ΅ΠΊΠ»Π° ΡΠΏΠΎΡΠΎΠ±ΡΡΠ²ΡΠ΅Ρ Π·Π°ΡΠ²Π΅ΡΠ΄Π΅Π½ΠΈΡ ΠΎΠΏΠΈΠ»ΠΎΠΊ, Π° Π²ΠΊΠ»ΡΡΠ΅Π½ΠΈΠ΅ Ρ Π»ΠΎΡΠΈΡΡΠΎΠ³ΠΎ ΠΊΠ°Π»ΡΡΠΈΡ ΡΠ²Π΅Π»ΠΈΡΠΈΠ²Π°Π΅Ρ ΠΈΡ ΠΏΡΠΎΡΠ½ΠΎΡΡΡ. ΠΡΠΎΠΌΡΡΠ»Π΅Π½Π½ΡΠ΅ ΠΏΡΠΎΠΈΠ·Π²ΠΎΠ΄ΠΈΡΠ΅Π»ΠΈ ΠΌΠΎΠ³ΡΡ ΡΠ°ΠΊΠΆΠ΅ ΠΈΡΠΏΠΎΠ»ΡΠ·ΠΎΠ²Π°ΡΡ Ρ Π»ΠΎΡΠΈΡΡΡΠΉ Π°Π»ΡΠΌΠΈΠ½ΠΈΠΉ, ΡΠ΅ΡΠ½ΠΎΠΊΠΈΡΠ»ΡΠΉ Π½Π°ΡΡΠΈΠΉ ΠΈΠ»ΠΈ Π°ΠΌΠΌΠΈΠ°ΡΠ½ΡΡ ΡΠ΅Π»ΠΈΡΡΡ. Π’Π°ΠΊΠΈΠ΅ ΡΠ΅ΡΠ΅Π½ΠΈΡ Π΄Π΅Π»Π°ΡΡ ΠΏΡΠΎΠΈΠ·Π²ΠΎΠ΄ΡΡΠ²ΠΎ Π±ΠΎΠ»Π΅Π΅ Π΄ΠΎΡΠΎΠ³ΠΈΠΌ, ΠΏΠΎΡΠΊΠΎΠ»ΡΠΊΡ Ρ ΠΈΠΌΠΈΠΊΠ°ΡΡ ΠΈΡΠΏΠΎΠ»ΡΠ·ΡΡΡΡΡ Π² ΠΏΡΠΎΠΏΠΎΡΡΠΈΠΈ 1 ΠΊ 40 ΡΠ°ΡΡΡΠΌ ΠΎΠΏΠΈΠ»ΠΎΠΊ.
ΠΠΏΠΈΠ»ΠΊΠΎΠ±Π΅ΡΠΎΠ½ Π² Π΄ΠΎΠΌΠ°ΡΠ½ΠΈΡ ΡΡΠ»ΠΎΠ²ΠΈΡΡ
ΠΠΎΠ΄Π°Π²Π»ΡΡΡΠ΅Π΅ Π±ΠΎΠ»ΡΡΠΈΠ½ΡΡΠ²ΠΎ ΠΏΡΠΈΡΡΡΡΡΠ²ΡΡΡΠΈΡ Π² ΠΏΡΠΎΠ΄Π°ΠΆΠ΅ Π±Π»ΠΎΠΊΠΎΠ² ΠΈΠ· ΠΎΠΏΠΈΠ»ΠΊΠΎΠ±Π΅ΠΎΡΠΎΠ½Π° ΡΠ²Π»ΡΡΡΡΡ ΠΏΡΠΎΠ΄ΡΠΊΡΠΎΠΌ ΠΊΡΡΡΠ°ΡΠ½ΠΎΠ³ΠΎ ΠΏΡΠΎΠΈΠ·Π²ΠΎΠ΄ΡΡΠ²Π°. ΠΡΠ°ΠΊΡΠΈΡΠ΅ΡΠΊΠΈ Π½Π΅Ρ ΠΊΡΡΠΏΠ½ΡΡ ΠΏΡΠ΅Π΄ΠΏΡΠΈΡΡΠΈΠΉ ΠΏΡΠΎΠΈΠ·Π²ΠΎΠ΄ΡΡΠΈΡ Π΄Π°Π½Π½ΡΠΉ ΠΌΠ°ΡΠ΅ΡΠΈΠ°Π» Π² ΠΏΠΎΠ»Π½ΠΎΠΌ ΡΠΎΠΎΡΠ²Π΅ΡΡΡΠ²ΠΈΠΈ Ρ Π΄Π΅ΠΉΡΡΠ²ΡΡΡΠΈΠΌΠΈ ΡΡΠ΅Π±ΠΎΠ²Π°Π½ΠΈΡΠΌΠΈ ΠΠΠ‘Π’. ΠΡΠΎΠ΄Π°Π²Π°Π΅ΠΌΡΠΉ Π½Π° ΡΡΠ½ΠΊΠ΅ ΠΌΠ°ΡΠ΅ΡΠΈΠ°Π» Π² ΡΠ²ΠΎΠ΅ΠΌ Π±ΠΎΠ»ΡΡΠΈΠ½ΡΡΠ²Π΅ ΡΠΎΠ²Π΅ΡΡΠ΅Π½Π½ΠΎ Π½Π΅ ΠΎΡΠ²Π΅ΡΠ°Π΅Ρ Π·Π°ΡΠ²Π»Π΅Π½Π½ΡΠΌ Ρ Π°ΡΠ°ΠΊΡΠ΅ΡΠΈΡΡΠΈΠΊΠ°ΠΌ ΠΈ ΠΌΠΈΠ½ΠΈΠΌΠ°Π»ΡΠ½ΡΠΌ ΡΡΠ΅Π±ΠΎΠ²Π°Π½ΠΈΡΠΌ, Π½Π΅ΠΎΠ±Ρ ΠΎΠ΄ΠΈΠΌΡΠΌ Π΄Π»Ρ ΡΡΡΠΎΠΈΡΠ΅Π»ΡΡΡΠ²Π°.
ΠΠ΅ΡΠ΅Π²ΠΈΠ·Π½Π° ΠΏΡΠΎΠΈΠ·Π²ΠΎΠ΄ΡΡΠ²Π° ΠΎΠΏΠΈΠ»ΠΊΠΎΠ±Π΅ΡΠΎΠ½Π° Π΄Π΅Π»Π°ΡΡ Π΅Π³ΠΎ ΠΏΡΠΈΠΌΠ΅Π½Π΅Π½ΠΈΠ΅ Π² ΡΡΡΠΎΠΈΡΠ΅Π»ΡΡΡΠ²Π΅ Π²ΡΠ³ΠΎΠ΄Π½ΡΠΌ, ΠΏΠΎΡΡΠΎΠΌΡ Π½Π΅ΡΠ΅Π΄ΠΊΠΎ Π΅Π³ΠΎ ΠΈΠ·Π³ΠΎΡΠΎΠ²Π»ΡΡΡ Π² Π½ΡΠΆΠ½ΠΎΠΌ ΠΊΠΎΠ»ΠΈΡΠ΅ΡΡΠ²Π΅ ΡΠ°ΠΌΠΈ, Π½Π΅ΠΏΠΎΡΡΠ΅Π΄ΡΡΠ²Π΅Π½Π½ΠΎ Π½Π° ΡΡΡΠΎΠΉΠΏΠ»ΠΎΡΠ°Π΄ΠΊΠ΅. Π ΡΠ°ΠΊΠΎΠΌ ΡΠ»ΡΡΠ°Π΅ ΠΎΠΏΠΈΠ»ΠΊΠΎΠ±Π΅ΡΠΎΠ½ Π·Π°Π»ΠΈΠ²Π°Π΅ΡΡΡ Π² ΠΎΠΏΠ°Π»ΡΠ±ΠΊΡ ΠΏΠΎΡΡΠ°ΠΏΠ½ΠΎ. ΠΠ½ ΡΠ°Π·ΠΌΠ΅ΡΠ°Π΅ΡΡΡ ΡΠ»ΠΎΡΠΌΠΈ. ΠΠΎ ΠΌΠ΅ΡΠ΅ Π²ΡΡΡΡ Π°Π½ΠΈΡ ΠΎΠΏΠ°Π»ΡΠ±ΠΊΠ° ΠΏΠΎΡΡΠ΅ΠΏΠ΅Π½Π½ΠΎ ΠΏΠΎΠ΄Π½ΠΈΠΌΠ°Π΅ΡΡΡ Π²Π²Π΅ΡΡ , Π² ΡΠ΅Π·ΡΠ»ΡΡΠ°ΡΠ΅ ΡΠ΅Π³ΠΎ ΠΏΠΎΠ»ΡΡΠ°ΡΡΡΡ Π½Π΅ΡΡΡΠΈΠ΅ ΡΡΠ΅Π½Ρ ΠΈ ΠΏΠ΅ΡΠ΅Π³ΠΎΡΠΎΠ΄ΠΊΠΈ Π·Π΄Π°Π½ΠΈΡ. ΠΡΠΎ Π΄ΠΎΡΡΠ°ΡΠΎΡΠ½ΠΎ ΠΏΡΠΎΠ΄ΠΎΠ»ΠΆΠΈΡΠ΅Π»ΡΠ½ΡΠΉ ΠΈ ΠΊΡΠΎΠΏΠΎΡΠ»ΠΈΠ²ΡΠΉ ΠΏΡΠΎΡΠ΅ΡΡ. ΠΠ°ΡΠ΅ΡΠΈΠ°Π» Π½Π°Π±ΠΈΡΠ°Π΅Ρ ΠΎΠΊΠΎΠ½ΡΠ°ΡΠ΅Π»ΡΠ½ΡΡ ΠΌΠ°ΡΠΎΡΠ½ΡΡ ΠΏΡΠΎΡΠ½ΠΎΡΡΡ ΡΠΎΠ»ΡΠΊΠΎ ΡΠ΅ΡΠ΅Π· 3 ΠΌΠ΅ΡΡΡΠ°, Π½Π΅ΡΠΌΠΎΡΡΡ Π½Π° ΡΠΎ, ΡΡΠΎ ΡΠ°ΠΌ ΡΠ΅ΠΌΠ΅Π½Ρ Π΄ΠΎΡΡΠΈΠ³Π°Π΅Ρ ΠΌΠ°ΠΊΡΠΈΠΌΠ°Π»ΡΠ½ΡΡ ΡΠ²ΡΠ·ΡΡΡΠΈΡ ΠΊΠ°ΡΠ΅ΡΡΠ² ΡΠΆΠ΅ ΡΠΏΡΡΡΡ 28 Π΄Π½Π΅ΠΉ.
ΠΡΠΎΡΠ½ΠΎΡΡΡ ΠΌΠ°ΡΠ΅ΡΠΈΠ°Π»Π° ΡΠ²Π΅Π»ΠΈΡΠΈΠ²Π°Π΅ΡΡΡ ΠΏΠΎ ΠΌΠ΅ΡΠ΅ Π΅Π³ΠΎ Π²ΡΡΡΡΠΈΠ²Π°Π½ΠΈΡ. Π ΡΠ²ΡΠ·ΠΈ Ρ ΡΡΠΈΠΌ ΠΌΠΎΠ½ΠΎΠ»ΠΈΡΠ½ΠΎΠ΅ ΡΡΡΠΎΠΈΡΠ΅Π»ΡΡΡΠ²ΠΎ ΠΈΠ· ΡΠ°ΠΊΠΎΠ³ΠΎ Π±Π΅ΡΠΎΠ½Π° Π΄ΠΎΠ»ΠΆΠ½ΠΎ ΠΏΡΠΎΠ²ΠΎΠ΄ΠΈΡΡΡΡ ΡΠΎΠ»ΡΠΊΠΎ Π»Π΅ΡΠΎΠΌ Π² ΡΠ°ΠΌΡΠ΅ ΠΆΠ°ΡΠΊΠΈΠ΅ ΠΈ Π·Π°ΡΡΡΠ»ΠΈΠ²ΡΠ΅ ΠΌΠ΅ΡΡΡΡ. ΠΠ΅Π»ΡΠ·Ρ Π·Π°Π»ΠΈΠ²Π°ΡΡ ΠΌΠ°ΡΡΡ Π±ΠΎΠ»ΡΡΠΈΠΌΠΈ ΡΠ»ΠΎΡΠΌΠΈ, ΠΏΠΎΡΠΊΠΎΠ»ΡΠΊΡ Π½ΠΈΠΆΠ½ΠΈΠΉ Π½Π΅Π΄ΠΎΡΡΡΠ΅Π½Π½ΡΠΉ ΡΠ»ΠΎΠΉ ΡΠΊΠ»ΠΎΠ½Π΅Π½ ΠΊ Π΄Π΅ΡΠΎΡΠΌΠ°ΡΠΈΠΈ.
ΠΡΠΈ ΠΈΠ·Π³ΠΎΡΠΎΠ²Π»Π΅Π½ΠΈΠΈ Π±Π»ΠΎΠΊΠΎΠ² ΠΈΠ· ΠΎΠΏΠΈΠ»ΠΊΠΎΠ±Π΅ΡΠΎΠ½Π° Π΅Π³ΠΎ ΠΎΡΡΠ°Π²Π»ΡΡΡ Π² ΡΠΎΡΠΌΠ°Ρ ΠΊΠ°ΠΊ ΠΌΠΈΠ½ΠΈΠΌΡΠΌ 1 ΡΡΡΠΊΠΈ. ΠΡΠ»ΠΈ ΠΈΡ Π²ΡΡΠ°ΡΠΈΡΡ ΡΠ°Π½ΡΡΠ΅, ΡΠΎ Π±Π»ΠΎΠΊ ΠΌΠΎΠΆΠ΅Ρ ΠΏΠ΅ΡΠ΅ΠΊΠΎΡΠΈΡΡΡΡ, ΡΡΠΎ ΠΏΡΠΈΠ²Π΅Π΄Π΅Ρ ΠΊ Π½Π°ΡΡΡΠ΅Π½ΠΈΡ Π³Π΅ΠΎΠΌΠ΅ΡΡΠΈΠΈ.
ΠΡΠΎΠΏΠΎΡΡΠΈΠΈ Π΄Π»Ρ ΠΏΡΠΈΠ³ΠΎΡΠΎΠ²Π»Π΅Π½ΠΈΡ ΠΎΠΏΠΈΠ»ΠΊΠΎΠ±Π΅ΡΠΎΠ½Π°
ΠΠΏΠΈΠ»ΠΊΠΎΠ±Π΅ΡΠΎΠ½ ΠΏΡΠΎΠΈΠ·Π²ΠΎΠ΄ΠΈΡΡΡ ΡΠ°Π·Π»ΠΈΡΠ½ΡΡ ΠΌΠ°ΡΠΎΠΊ ΠΏΡΠΎΡΠ½ΠΎΡΡΠΈ β Π5-Π25. Π‘Π»Π°Π±ΡΠΉ Π±Π΅ΡΠΎΠ½ ΠΌΠ°ΡΠΎΠΊ Π5 ΠΈ Π10 ΠΏΡΠΈΠΌΠ΅Π½ΡΠ΅ΡΡΡ Π² ΠΊΠ°ΡΠ΅ΡΡΠ²Π΅ ΡΡΠ΅ΠΏΠ»ΠΈΡΠ΅Π»Ρ. ΠΠ³ΠΎ Π·Π°Π»ΠΈΠ²Π°ΡΡ Π²ΠΌΠ΅ΡΡΠΎ ΡΠ΅ΠΏΠ»ΠΎΠΈΠ·ΠΎΠ»ΡΡΠΈΠΎΠ½Π½ΠΎΠ³ΠΎ ΠΌΠ°ΡΠ΅ΡΠΈΠ°Π»Π° ΠΌΠ΅ΠΆΠ΄Ρ ΠΊΠΈΡΠΏΠΈΡΠ½ΠΎΠΉ ΠΊΠ»Π°Π΄ΠΊΠΎΠΉ ΡΡΠ΅Π½, ΠΏΡΠΈΠΌΠ΅Π½ΡΡΡ Π΄Π»Ρ ΡΡΠ΅ΠΏΠ»Π΅Π½ΠΈΡ ΡΠ΅ΡΠ΄Π°ΠΊΠΎΠ². ΠΠ°ΡΠΊΠΈ Π15-Π25 ΠΏΠΎΠ΄Ρ ΠΎΠ΄ΡΡ Π΄Π»Ρ ΠΏΡΠΎΠΈΠ·Π²ΠΎΠ΄ΡΡΠ²Π° Π½Π΅ΡΡΡΠΈΡ ΡΡΠ΅Π½, ΠΏΡΠΈ ΡΡΠ»ΠΎΠ²ΠΈΠΈ ΠΎΡΡΡΡΡΡΠ²ΠΈΡ ΡΡΠΆΠ΅Π»ΠΎΠ³ΠΎ Π±Π΅ΡΠΎΠ½Π½ΠΎΠ³ΠΎ ΠΌΠ΅ΠΆΡΡΠ°ΠΆΠ½ΠΎΠ³ΠΎ ΠΏΠ΅ΡΠ΅ΠΊΡΡΡΠΈΡ.
ΠΠ»Ρ ΠΏΡΠΈΠ³ΠΎΡΠΎΠ²Π»Π΅Π½ΠΈΡ 1 Π²Π΅Π΄ΡΠ° ΠΎΠΏΠΈΠ»ΠΊΠΎΠ±Π΅ΡΠΎΠ½Π° ΠΌΠ°ΡΠΊΠΈ Π25 Π½Π΅ΠΎΠ±Ρ ΠΎΠ΄ΠΈΠΌΠΎ:
- Π‘ΡΡΡΠΆΠΊΠ° β 2 ΠΊΠ³.
- Π¦Π΅ΠΌΠ΅Π½Ρ Π500 β 3 ΠΊΠ³.
- ΠΠ΅ΡΠΎΠΊ β 6,7 ΠΊΠ³.
- ΠΠΎΠ΄Π°.
Π’Π°ΠΊΠΆΠ΅ Π²ΠΎΠ·ΠΌΠΎΠΆΠ½ΠΎ ΠΏΡΠΈΠ³ΠΎΡΠΎΠ²Π»Π΅Π½ΠΈΠ΅ ΠΎΠΏΠΈΠ»ΠΊΠΎΠ±Π΅ΡΠΎΠ½Π° ΡΡΠΎΠΉ ΠΆΠ΅ ΠΌΠ°ΡΠΊΠΈ Ρ ΠΈΡΠΏΠΎΠ»ΡΠ·ΠΎΠ²Π°Π½ΠΈΠ΅ΠΌ Π³Π»ΠΈΠ½Ρ ΠΈ ΠΈΠ·Π²Π΅ΡΡΠΈ. Π ΡΠ°ΠΊΠΎΠΌ ΡΠ»ΡΡΠ°Π΅ ΡΠ½ΠΈΠΆΠ°Π΅ΡΡΡ ΠΊΠΎΠ½ΡΠ΅Π½ΡΡΠ°ΡΠΈΡ ΡΠ΅ΠΌΠ΅Π½ΡΠ°, ΡΡΠΎ ΡΠ΄Π΅ΡΠ΅Π²Π»ΡΠ΅Ρ ΠΏΡΠΎΠΈΠ·Π²ΠΎΠ΄ΡΡΠ²ΠΎ.
ΠΠ»Ρ Π·Π°ΠΌΠ΅ΡΠΈΠ²Π°Π½ΠΈΡ Π²Π΅Π΄ΡΠ° ΡΠ°ΡΡΠ²ΠΎΡΠ° ΠΎΠ±ΡΡΠ½ΠΎ ΠΏΡΠΈΠΌΠ΅Π½ΡΠ΅ΡΡΡ ΡΠΎΠΎΡΠ½ΠΎΡΠ΅Π½ΠΈΠ΅ ΠΊΠΎΠΌΠΏΠΎΠ½Π΅Π½ΡΠΎΠ²:
- Π¦Π΅ΠΌΠ΅Π½Ρ Π400-Π500 β 2 ΠΊΠ³.
- ΠΠ΅ΡΠΎΠΊ β 5 ΠΊΠ³.
- ΠΠ·Π²Π΅ΡΡΡ 0,5 ΠΊΠ³.
- ΠΠ»ΠΈΠ½Π° β 1 ΠΊΠ³.
- ΠΠΏΠΈΠ»ΠΊΠΈ β 2 ΠΊΠ³.
ΠΡΠ΅ΡΠ΅Π΄Π½ΠΎΡΡΡ ΡΠΌΠ΅ΡΠΈΠ²Π°Π½ΠΈΡ ΠΊΠΎΠΌΠΏΠΎΠ½Π΅Π½ΡΠΎΠ²
Π§ΡΠΎΠ±Ρ ΠΏΡΠΈΠ³ΠΎΡΠΎΠ²ΠΈΡΡ ΠΎΠΏΠΈΠ»ΠΊΠΎΠ±Π΅ΡΠΎΠ½ Ρ ΠΎΠΏΡΠΈΠΌΠ°Π»ΡΠ½ΠΎΠΉ ΠΎΠ΄Π½ΠΎΡΠΎΠ΄Π½ΠΎΠΉ ΠΊΠΎΠ½ΡΠΈΡΡΠ΅Π½ΡΠΈΠ΅ΠΉ, Π²Π°ΠΆΠ½ΠΎ ΠΏΡΠΎΠ²ΠΎΠ΄ΠΈΡΡ ΡΠΌΠ΅ΡΠΈΠ²Π°Π½ΠΈΠ΅ ΠΊΠΎΠΌΠΏΠΎΠ½Π΅Π½ΡΠΎΠ² ΠΏΡΠ°Π²ΠΈΠ»ΡΠ½ΠΎ. Π ΠΏΠ΅ΡΠ²ΡΡ ΠΎΡΠ΅ΡΠ΅Π΄Ρ ΠΏΠ΅ΡΠ΅ΠΌΠ΅ΡΠΈΠ²Π°ΡΡΡΡ Π²ΡΠΆΡΡΠΈΠ΅ ΡΠΎΡΡΠ°Π²Π»ΡΡΡΠΈΠ΅ ΠΈ ΠΏΠ΅ΡΠΎΠΊ. ΠΠΎΡΠ»Π΅ ΡΡΠΎΠ³ΠΎ Π΄ΠΎΠ±Π°Π²Π»ΡΡΡΡΡ ΠΎΠΏΠΈΠ»ΠΊΠΈ, ΠΈ ΡΠΎΠ»ΡΠΊΠΎ ΠΏΠΎΡΠ»Π΅ ΡΡΠΎΠ³ΠΎ Π²Π²ΠΎΠ΄ΠΈΡΡΡ Π²ΠΎΠ΄Π°. ΠΠ΅ ΠΊΠΎΠ»ΠΈΡΠ΅ΡΡΠ²ΠΎ ΠΎΠΏΡΠ΅Π΄Π΅Π»ΡΠ΅ΡΡΡ Π²ΠΈΠ·ΡΠ°Π»ΡΠ½ΠΎ, ΠΏΠΎΡΠΊΠΎΠ»ΡΠΊΡ Π΄Π°Π½Π½ΡΠΉ ΠΏΠΎΠΊΠ°Π·Π°ΡΠ΅Π»Ρ Π·Π°Π²ΠΈΡΠΈΡ ΠΎΡ Π²Π»Π°ΠΆΠ½ΠΎΡΡΠΈ Π΄ΡΠ΅Π²Π΅ΡΠΈΠ½Ρ ΠΈ ΠΏΠ΅ΡΠΊΠ°. Π Π°ΡΡΠ²ΠΎΡ Π½Π΅ Π΄ΠΎΠ»ΠΆΠ΅Π½ Π±ΡΡΡ ΠΆΠΈΠ΄ΠΊΠΈΠΌ. Π§Π΅ΠΌ Π²ΡΡΠ΅ Π΅Π³ΠΎ Π³ΡΡΡΠΎΡΠ°, ΡΠ΅ΠΌ ΠΌΠ΅Π½ΡΡΠ΅ Π΄Π°Π»ΡΠ½Π΅ΠΉΡΠ°Ρ ΡΡΠ°Π΄ΠΊΠ° ΠΏΡΠΈ Π²ΡΡΡΡ Π°Π½ΠΈΠΈ.
ΠΠΎΡ ΠΎΠΆΠΈΠ΅ ΡΠ΅ΠΌΡ:
ΠΎΡΠ·ΡΠ²Ρ ΡΡΡΠΎΠΈΡΠ΅Π»Π΅ΠΉ, ΡΠ΅Ρ Π½ΠΎΠ»ΠΎΠ³ΠΈΡ ΠΏΡΠΎΠΈΠ·Π²ΠΎΠ΄ΡΡΠ²Π°, ΡΠΎΡΡΠ°Π² ΠΈ ΡΠ²ΠΎΠΉΡΡΠ²Π° :: SYL.ru
ΠΠ΄Π½ΠΎΠΉ ΠΈΠ· ΡΠ°Π·Π½ΠΎΠ²ΠΈΠ΄Π½ΠΎΡΡΠ΅ΠΉ Π»Π΅Π³ΠΊΠΈΡ Π±Π΅ΡΠΎΠ½ΠΎΠ² ΡΠ²Π»ΡΠ΅ΡΡΡ ΠΎΠΏΠΈΠ»ΠΊΠΎΠ±Π΅ΡΠΎΠ½, ΠΊΠΎΡΠΎΡΡΠΉ ΠΏΡΠΎΠΈΠ·Π²ΠΎΠ΄ΠΈΡΡΡ Ρ ΠΈΡΠΏΠΎΠ»ΡΠ·ΠΎΠ²Π°Π½ΠΈΠ΅ΠΌ Π΄ΡΠ΅Π²Π΅ΡΠ½ΡΡ ΠΎΠΏΠΈΠ»ΠΎΠΊ ΠΈ ΠΎΡΠ»ΠΈΡΠ°Π΅ΡΡΡ ΠΏΠΎΠ½ΠΈΠΆΠ΅Π½Π½ΠΎΠΉ ΠΏΠ»ΠΎΡΠ½ΠΎΡΡΡΡ. ΠΠ°ΡΠ΅ΡΠΈΠ°Π» Π±ΡΠ» ΡΠ°Π·ΡΠ°Π±ΠΎΡΠ°Π½ Π² Π‘ΠΎΠ²Π΅ΡΡΠΊΠΎΠΌ Π‘ΠΎΡΠ·Π΅, Π΅ΡΠ΅ Π² 60-Ρ Π³ΠΎΠ΄Π°Ρ ΠΏΡΠΎΡΠ»ΠΎ Π²Π΅ΠΊΠ°. ΠΠΎΠ·ΠΆΠ΅ ΠΎΠ½ ΠΏΡΠΎΡΠ΅Π» Π²ΡΠ΅ ΠΊΠ°ΡΠ΅ΡΡΠ²Π΅Π½Π½ΡΠ΅ ΠΈ ΡΠ΅Ρ Π½ΠΈΡΠ΅ΡΠΊΠΈΠ΅ ΠΈΡΠΏΡΡΠ°Π½ΠΈΡ ΠΈ Π±ΡΠ» ΡΡΠ°Π½Π΄Π°ΡΡΠΈΠ·ΠΈΡΠΎΠ²Π°Π½. ΠΠ°ΡΡΠΎΠ²ΠΎΠ΅ ΠΏΡΠΈΠΌΠ΅Π½Π΅Π½ΠΈΠ΅ ΠΎΠΏΠΈΠ»ΠΊΠΎΠ±Π΅ΡΠΎΠ½Π° Π² Π΄ΠΎΠΌΠΎΡΡΡΠΎΠ΅Π½ΠΈΠΈ Π½Π°ΡΠ°Π»ΠΎΡΡ Π»ΠΈΡΡ Π² ΡΠ΅ΡΠ΅Π΄ΠΈΠ½Π΅ 90-Ρ . Π‘ ΡΠ΅Ρ ΠΏΠΎΡ, Π±Π»Π°Π³ΠΎΠ΄Π°ΡΡ ΡΠ²ΠΎΠΈΠΌ ΡΠ½ΠΈΠΊΠ°Π»ΡΠ½ΡΠΌ ΡΠ²ΠΎΠΉΡΡΠ²Π°ΠΌ, ΠΎΠ½ ΡΡΠ°Π» ΠΏΠΎΠ»ΡΠ·ΠΎΠ²Π°ΡΡΡΡ Π±ΠΎΠ»ΡΡΠΎΠΉ ΠΏΠΎΠΏΡΠ»ΡΡΠ½ΠΎΡΡΡΡ ΡΡΠ΅Π΄ΠΈ ΡΡΡΠΎΠΈΡΠ΅Π»Π΅ΠΉ. Π‘Π΅Π³ΠΎΠ΄Π½Ρ ΠΌΡ Ρ Π²Π°ΠΌΠΈ ΡΠ·Π½Π°Π΅ΠΌ, ΡΡΠΎ ΡΠΎΠ±ΠΎΠΉ ΠΏΡΠ΅Π΄ΡΡΠ°Π²Π»ΡΠ΅Ρ ΠΎΠΏΠΈΠ»ΠΊΠΎΠ±Π΅ΡΠΎΠ½, ΠΊΠ°ΠΊ ΠΎΠ½ ΠΏΡΠΎΠΈΠ·Π²ΠΎΠ΄ΠΈΡΡΡ ΠΈ ΠΊΠ°ΠΊΠΈΠ΅ ΠΎΡΠ·ΡΠ²Ρ ΠΎΡΡΠ°Π²Π»ΡΡΡ ΠΎ Π½Π΅ΠΌ ΡΡΡΠΎΠΈΡΠ΅Π»ΠΈ.
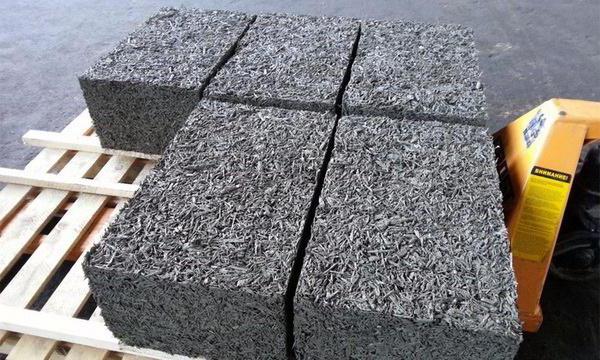
ΠΠ±Π»Π°ΡΡΡ ΠΏΡΠΈΠΌΠ΅Π½Π΅Π½ΠΈΡ
ΠΠ°Π½Π½ΡΠΉ ΠΌΠ°ΡΠ΅ΡΠΈΠ°Π» ΠΎΡΠ»ΠΈΡΠ°Π΅ΡΡΡ ΡΠ°ΠΊΠΈΠΌΠΈ ΠΊΠ°ΡΠ΅ΡΡΠ²Π°ΠΌΠΈ: ΡΠΊΠΎΠ»ΠΎΠ³ΠΈΡΠ½ΠΎΡΡΡ, ΠΎΠ³Π½Π΅ΡΡΠΎΠΉΠΊΠΎΡΡΡ, ΠΏΡΠΎΡΠ½ΠΎΡΡΡ, ΠΏΠ°ΡΠΎΠΏΡΠΎΠ½ΠΈΡΠ°Π΅ΠΌΠΎΡΡΡ, ΠΌΠΎΡΠΎΠ·ΠΎΡΡΠΎΠΉΠΊΠΎΡΡΡ ΠΈ Π΄ΠΎΡΡΡΠΏΠ½ΠΎΡΡΡ. ΠΠ½ ΡΠΈΡΠΎΠΊΠΎ ΠΈΡΠΏΠΎΠ»ΡΠ·ΡΠ΅ΡΡΡ ΠΏΡΠΈ ΡΡΡΠΎΠΈΡΠ΅Π»ΡΡΡΠ²Π΅ Π΄ΠΎΠΌΠΎΠ² ΠΈ Ρ ΠΎΠ·ΡΠΉΡΡΠ²Π΅Π½Π½ΡΡ ΠΏΠΎΡΡΡΠΎΠ΅ΠΊ Π½Π΅Π±ΠΎΠ»ΡΡΠΎΠΉ ΡΡΠ°ΠΆΠ½ΠΎΡΡΠΈ. ΠΡΠΎΠΌΠ΅ ΡΠΎΠ³ΠΎ, ΠΊΠ°ΠΊ ΠΏΠΎΠΊΠ°Π·ΡΠ²Π°ΡΡ ΠΎΡΠ·ΡΠ²Ρ ΡΡΡΠΎΠΈΡΠ΅Π»Π΅ΠΉ, ΠΎΠΏΠΈΠ»ΠΊΠΎΠ±Π΅ΡΠΎΠ½ ΠΎΡΠ»ΠΈΡΠ½ΠΎ ΠΏΠΎΠ΄Ρ ΠΎΠ΄ΠΈΡ Π΄Π»Ρ ΡΠ°Π±ΠΎΡ ΠΏΠΎ ΡΡΠ΅ΠΏΠ»Π΅Π½ΠΈΡ ΠΈ ΡΠ΅ΠΌΠΎΠ½ΡΡ Π·Π΄Π°Π½ΠΈΠΉ. Π Π΅ΠΊΠΎΠ½ΡΡΡΡΠΊΡΠΈΡ Ρ ΠΈΡΠΏΠΎΠ»ΡΠ·ΠΎΠ²Π°Π½ΠΈΠ΅ΠΌ ΡΡΠΎΠ³ΠΎ ΠΌΠ°ΡΠ΅ΡΠΈΠ°Π»Π° ΠΏΠΎΠ·Π²ΠΎΠ»ΡΠ΅Ρ Π½Π΅ ΡΡΠΈΠ»ΠΈΠ²Π°ΡΡ ΡΡΠ½Π΄Π°ΠΌΠ΅Π½Ρ.
ΠΡΠΈ ΡΡΡΠΎΠΈΡΠ΅Π»ΡΡΡΠ²Π΅ Π΄ΠΎΠΌΠ° ΠΈΠ· ΠΎΠΏΠΈΠ»ΠΊΠΎΠ±Π΅ΡΠΎΠ½Π° ΠΌΠΎΠΆΠ½ΠΎ ΠΏΠΎΠ»ΡΠ·ΠΎΠ²Π°ΡΡΡΡ ΠΏΡΠΎΠ΅ΠΊΡΠΎΠΌ, ΡΠ°Π·ΡΠ°Π±ΠΎΡΠ°Π½Π½ΡΠΌ ΠΏΠΎΠ΄ Π»ΡΠ±ΠΎΠΉ Π΄ΡΡΠ³ΠΎΠΉ ΠΌΠ°ΡΠ΅ΡΠΈΠ°Π». ΠΡΠΈ ΡΡΠΎΠΌ Π·Π°ΡΡΠ°ΡΡ Π½Π° ΡΡΡΠΎΠΈΡΠ΅Π»ΡΡΡΠ²ΠΎ Π±ΡΠ΄ΡΡ ΡΡΡΠ΅ΡΡΠ²Π΅Π½Π½ΠΎ Π½ΠΈΠΆΠ΅. Π‘ΡΠ΅Π½Ρ ΠΈΠ· ΠΎΠΏΠΈΠ»ΠΊΠΎΠ±Π΅ΡΠΎΠ½Π° ΠΌΠ°Π»ΠΎ Π²Π΅ΡΡΡ, ΠΏΠΎΡΡΠΎΠΌΡ ΠΈΡΠΏΠΎΠ»ΡΠ·ΡΡ ΡΡΠΎΡ ΠΌΠ°ΡΠ΅ΡΠΈΠ°Π», ΡΠΎΠ²ΡΠ΅ΠΌ Π½Π΅ΠΎΠ±ΡΠ·Π°ΡΠ΅Π»ΡΠ½ΠΎ Π·Π°ΠΊΠ»Π°Π΄ΡΠ²Π°ΡΡ ΡΠ»ΠΈΡΠΊΠΎΠΌ ΡΠ»ΠΎΠΆΠ½ΡΠΉ ΡΡΠ½Π΄Π°ΠΌΠ΅Π½Ρ.
Π‘ΠΎΡΡΠ°Π²
ΠΠ°ΠΊ ΠΌΠΎΠΆΠ½ΠΎ ΠΏΠΎΠ½ΡΡΡ ΠΈΠ· Π½Π°Π·Π²Π°Π½ΠΈΡ, ΠΎΠΏΡΠ΅Π΄Π΅Π»ΡΡΡΠΈΠΌ ΡΠ»Π΅ΠΌΠ΅Π½ΡΠΎΠΌ ΡΡΠΎΠ³ΠΎ ΠΌΠ°ΡΠ΅ΡΠΈΠ°Π»Π° ΡΠ²Π»ΡΡΡΡΡ Π΄ΡΠ΅Π²Π΅ΡΠ½ΡΠ΅ ΠΎΠΏΠΈΠ»ΠΊΠΈ. ΠΡΠΎΠΌΠ΅ ΡΠΎΠ³ΠΎ, Π² ΡΠΎΡΡΠ°Π² ΠΎΠΏΠΈΠ»ΠΊΠΎΠ±Π΅ΡΠΎΠ½Π° Π²Ρ ΠΎΠ΄ΡΡ ΠΏΠ΅ΡΠΎΠΊ, ΡΠ΅ΠΌΠ΅Π½Ρ, Π° ΡΠ°ΠΊΠΆΠ΅ Π³Π»ΠΈΠ½Π° ΠΈΠ»ΠΈ ΠΈΠ·Π²Π΅ΡΡΡ. ΠΠ»Π°Π³ΠΎΠ΄Π°ΡΡ Π±Π»Π°Π³ΠΎΠΏΡΠΈΡΡΠ½ΡΠΌ ΡΠ°Π½ΠΈΡΠ°ΡΠ½ΠΎ-Π³ΠΈΠ³ΠΈΠ΅Π½ΠΈΡΠ΅ΡΠΊΠΈΠΌ ΠΏΠΎΠΊΠ°Π·Π°ΡΠ΅Π»ΡΠΌ ΠΌΠ°ΡΠ΅ΡΠΈΠ°Π» ΠΎΠΏΡΠΈΠΌΠ°Π»Π΅Π½ Π΄Π»Ρ Π²ΠΎΠ·Π²Π΅Π΄Π΅Π½ΠΈΡ ΡΡΠ΅Π½ ΠΆΠΈΠ»ΡΡ ΠΏΠΎΠΌΠ΅ΡΠ΅Π½ΠΈΠΉ.
ΠΠ»ΠΎΡΠ½ΠΎΡΡΡ ΡΡΡΠΎΠΈΡΠ΅Π»ΡΠ½ΠΎΠ³ΠΎ ΠΌΠ°ΡΠ΅ΡΠΈΠ°Π»Π° Π·Π°Π²ΠΈΡΠΈΡ ΠΎΡ ΡΠΎΠΎΡΠ½ΠΎΡΠ΅Π½ΠΈΡ ΠΎΠΏΠΈΠ»ΠΎΠΊ ΠΈ ΠΏΠ΅ΡΠΊΠ°. Π§Π΅ΠΌ Π±ΠΎΠ»ΡΡΠ΅ Π² ΠΎΠΏΠΈΠ»ΠΊΠΎΠ±Π΅ΡΠΎΠ½Π΅ ΠΏΠ΅ΡΠΊΠ° ΠΈ Π²ΡΠΆΡΡΠΈΡ ΠΌΠ°ΡΠ΅ΡΠΈΠ°Π»ΠΎΠ², ΡΠ΅ΠΌ Π±ΠΎΠ»ΡΡΠ΅ Π΅Π³ΠΎ ΠΏΠ»ΠΎΡΠ½ΠΎΡΡΡ. Π ΡΠ°ΠΊΠΎΠΌ ΡΠ»ΡΡΠ°Π΅ ΠΌΠ°ΡΠ΅ΡΠΈΠ°Π» ΠΎΠ±Π»Π°Π΄Π°Π΅Ρ Π²ΡΡΠΎΠΊΠΈΠΌΠΈ ΠΏΡΠΎΡΠ½ΠΎΡΡΠ½ΡΠΌΠΈ, Π½ΠΎ Π½ΠΈΠ·ΠΊΠΈΠΌΠΈ ΡΠ΅ΠΏΠ»ΠΎΡΠ΅Ρ Π½ΠΈΡΠ΅ΡΠΊΠΈΠΌΠΈ Ρ Π°ΡΠ°ΠΊΡΠ΅ΡΠΈΡΡΠΈΠΊΠ°ΠΌΠΈ. Π‘ ΡΠ²Π΅Π»ΠΈΡΠ΅Π½ΠΈΠ΅ΠΌ ΠΊΠΎΠ»ΠΈΡΠ΅ΡΡΠ²Π° ΠΎΠΏΠΈΠ»ΠΎΠΊ ΠΏΡΠΎΡΠ½ΠΎΡΡΡ ΠΏΠΎΠ½ΠΈΠΆΠ°Π΅ΡΡΡ. ΠΠΌΠ΅ΡΡΠ΅ Ρ Π½Π΅ΠΉ ΡΠ½ΠΈΠΆΠ°Π΅ΡΡΡ ΠΌΠΎΡΠΎΠ·ΠΎΡΡΠΎΠΉΠΊΠΎΡΡΡ ΠΌΠ°ΡΠ΅ΡΠΈΠ°Π»Π° ΠΈ Π΅Π³ΠΎ Π²ΠΎΠ΄ΠΎΠ½Π΅ΠΏΡΠΎΠ½ΠΈΡΠ°Π΅ΠΌΠΎΡΡΡ, ΡΡΠΎ, Π² ΡΠ²ΠΎΡ ΠΎΡΠ΅ΡΠ΅Π΄Ρ, Π½Π΅Π³Π°ΡΠΈΠ²Π½ΠΎ ΡΠΊΠ°Π·ΡΠ²Π°Π΅ΡΡΡ Π½Π° ΠΊΠΎΡΡΠΎΠ·ΠΈΠΎΠ½Π½ΠΎΠΉ ΡΡΠΎΠΉΠΊΠΎΡΡΠΈ ΡΡΠ°Π»ΡΠ½ΠΎΠΉ Π°ΡΠΌΠ°ΡΡΡΡ. ΠΡΠΌΠ°ΡΡΡΠ° ΠΈΡΠΏΠΎΠ»ΡΠ·ΡΠ΅ΡΡΡ ΠΏΡΠΈ ΡΠΊΠ»Π°Π΄ΠΊΠ΅ ΡΡΠ΅Π½. ΠΠ· Π²ΡΡΠ΅ΡΠΊΠ°Π·Π°Π½Π½ΠΎΠ³ΠΎ ΠΌΠΎΠΆΠ½ΠΎ ΡΠ΄Π΅Π»Π°ΡΡ Π²ΡΠ²ΠΎΠ΄, ΡΡΠΎ ΠΏΡΠ΅ΠΆΠ΄Π΅ ΡΠ΅ΠΌ Π½Π°ΡΠ°ΡΡ Π²ΠΎΠ·Π²ΠΎΠ΄ΠΈΡΡ Π΄ΠΎΠΌ ΠΈΠ· ΠΎΠΏΠΈΠ»ΠΊΠΎΠ±Π΅ΡΠΎΠ½Π°, Π½Π΅ΠΎΠ±Ρ ΠΎΠ΄ΠΈΠΌΠΎ ΠΈΠ·ΡΡΠΈΡΡ ΠΎΡΠΎΠ±Π΅Π½Π½ΠΎΡΡΠΈ Π²Π»ΠΈΡΠ½ΠΈΡ ΡΠΎΡΡΠ°Π²Π° ΠΌΠ°ΡΠ΅ΡΠΈΠ°Π»Π° Π½Π° Π΅Π³ΠΎ ΡΠ²ΠΎΠΉΡΡΠ²Π°. ΠΡΠ±ΠΈΡΠ°Ρ ΡΠΎΡ ΠΈΠ»ΠΈ ΠΈΠ½ΠΎΠΉ ΡΠΎΡΡΠ°Π², ΡΡΠΎΠΈΡ ΠΏΡΠΈΠ½ΠΈΠΌΠ°ΡΡ Π²ΠΎ Π²Π½ΠΈΠΌΠ°Π½ΠΈΠ΅ ΡΠΎΠ»ΡΠΈΠ½Ρ ΡΡΠ΅Π½, ΡΡΠ°ΠΆΠ½ΠΎΡΡΡ Π·Π΄Π°Π½ΠΈΡ ΠΈ Π½Π°Π·Π½Π°ΡΠ΅Π½ΠΈΠ΅ ΡΡΠ΅Π½ (Π²Π½ΡΡΡΠ΅Π½Π½ΡΡ, Π½Π°ΡΡΠΆΠ½Π°Ρ ΠΈΠ»ΠΈ ΠΆΠ΅ Π½Π΅ΡΡΡΠ°Ρ).
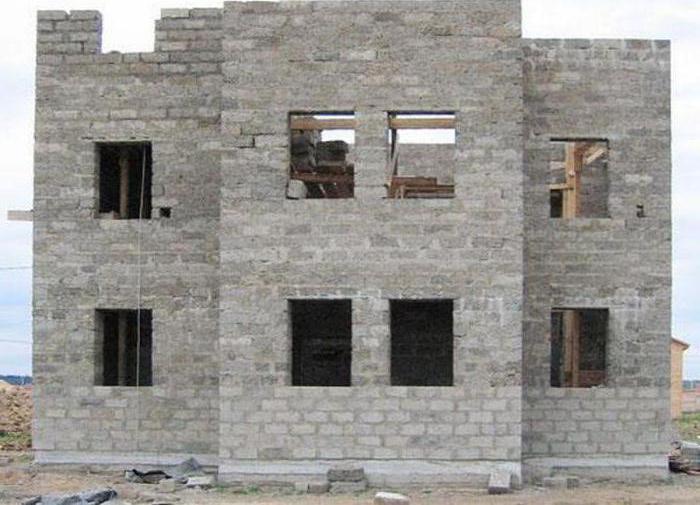
ΠΠ°ΡΠΊΠΈ ΠΎΠΏΠΈΠ»ΠΊΠΎΠ±Π΅ΡΠΎΠ½Π°
ΠΡΠΎΠΏΠΎΡΡΠΈΠΈ, ΠΏΠΎ ΠΊΠΎΡΠΎΡΡΠΌ ΡΠΌΠ΅ΡΠΈΠ²Π°ΡΡ ΠΊΠΎΠΌΠΏΠΎΠ½Π΅Π½ΡΡ, ΠΌΠΎΠ³ΡΡ Π±ΡΡΡ ΡΠ°Π·Π½ΡΠΌΠΈ. ΠΠ±ΡΡΠ½ΠΎ Π²ΡΠ΄Π΅Π»ΡΡΡ ΡΠ΅ΡΡΡΠ΅ ΠΌΠ°ΡΠΊΠΈ ΠΎΠΏΠΈΠ»ΠΊΠΎΠ±Π΅ΡΠΎΠ½Π°:
- Π5. ΠΠ° 100 ΠΊΠ³ ΠΎΠΏΠΈΠ»ΠΎΠΊ ΠΏΡΠΈΡ ΠΎΠ΄ΠΈΡΡΡ 25 ΠΊΠ³ ΡΠ΅ΠΌΠ΅Π½ΡΠ°, 25 ΠΊΠ³ ΠΏΠ΅ΡΠΊΠ°, 100 ΠΊΠ³ ΠΈΠ·Π²Π΅ΡΡΠΈ ΠΈΠ»ΠΈ Π³Π»ΠΈΠ½Ρ. ΠΠ»ΠΎΡΠ½ΠΎΡΡΡ ΡΠ°ΠΊΠΎΠ³ΠΎ ΠΌΠ°ΡΠ΅ΡΠΈΠ°Π»Π° ΡΠ°Π²Π½Π° 500ΠΊΠ³/ΠΌ3.
- Π10. ΠΠ° 100 ΠΊΠ³ ΠΎΠΏΠΈΠ»ΠΎΠΊ ΠΏΡΠΈΡ ΠΎΠ΄ΠΈΡΡΡ 50 ΠΊΠ³ ΡΠ΅ΠΌΠ΅Π½ΡΠ°, 100 ΠΊΠ³ ΠΏΠ΅ΡΠΊΠ° ΠΈ 75 ΠΊΠ³ ΠΈΠ·Π²Π΅ΡΡΠΈ ΠΈΠ»ΠΈ Π³Π»ΠΈΠ½Ρ. ΠΠ»ΠΎΡΠ½ΠΎΡΡΡ ΡΡΠΎΠΉ ΠΌΠ°ΡΠΊΠΈ ΡΠΎΡΡΠ°Π²Π»ΡΠ΅Ρ ΡΠΆΠ΅ 650 ΠΊΠ³/ΠΌ3.
- Π15. ΠΠ° 100 ΠΊΠ³ ΠΎΠΏΠΈΠ»ΠΎΠΊ ΠΏΡΠΈΡ ΠΎΠ΄ΠΈΡΡΡ 75 ΠΊΠ³ ΡΠ΅ΠΌΠ΅Π½ΡΠ°, 175 ΠΊΠ³ ΠΏΠ΅ΡΠΊΠ°, 50 ΠΊΠ³ ΠΈΠ·Π²Π΅ΡΡΠΈ ΠΈΠ»ΠΈ Π³Π»ΠΈΠ½Ρ. ΠΠ»ΠΎΡΠ½ΠΎΡΡΡ ΡΡΠΎΠΉ ΠΌΠ°ΡΠΊΠΈ ΡΠ°Π²Π½Π° 800 ΠΊΠ³/ΠΌ3.
- Π20. ΠΠ° 100 ΠΊΠ³ ΠΎΠΏΠΈΠ»ΠΎΠΊ ΠΏΡΠΈΡ ΠΎΠ΄ΠΈΡΡΡ 100 ΠΊΠ³ ΡΠ΅ΠΌΠ΅Π½ΡΠ°, 250 ΠΊΠ³ ΠΏΠ΅ΡΠΊΠ°, 25 ΠΊΠ³ ΠΈΠ·Π²Π΅ΡΡΠΈ ΠΈΠ»ΠΈ Π³Π»ΠΈΠ½Ρ. ΠΡΠΎ ΡΠ°ΠΌΡΠΉ ΠΏΠ»ΠΎΡΠ½ΡΠΉ ΠΌΠ°ΡΠ΅ΡΠΈΠ°Π» β 950 ΠΊΠ³/ΠΌ3.
Π‘ΡΠ΅Π½ΠΎΠ²ΡΠ΅ Π±Π»ΠΎΠΊΠΈ ΠΏΠ΅ΡΠ²ΡΡ Π΄Π²ΡΡ ΠΌΠ°ΡΠΎΠΊ ΠΏΡΠΈΠΌΠ΅Π½ΡΡΡΡΡ Π΄Π»Ρ Π²ΠΎΠ·Π²Π΅Π΄Π΅Π½ΠΈΡ, ΡΡΠ΅ΠΏΠ»Π΅Π½ΠΈΡ ΠΈ ΡΠ΅ΠΊΠΎΠ½ΡΡΡΡΠΊΡΠΈΠΈ ΠΏΠΎΠ΄Π²Π°Π»ΠΎΠ², ΡΠ°ΠΊ ΠΊΠ°ΠΊ ΠΎΠ½ΠΈ ΠΈΠΌΠ΅ΡΡ ΠΏΡΠ΅ΠΊΡΠ°ΡΠ½ΡΠ΅ ΡΠ΅ΠΏΠ»ΠΎΠΈΠ·ΠΎΠ»ΡΡΠΈΠΎΠ½Π½ΡΠ΅ Ρ Π°ΡΠ°ΠΊΡΠ΅ΡΠΈΡΡΠΈΠΊΠΈ. Π’ΡΠ΅ΡΡΡ ΠΈ ΡΠ΅ΡΠ²Π΅ΡΡΠ°Ρ ΠΌΠ°ΡΠΊΠ° ΠΎΡΠ»ΠΈΡΠ½ΠΎ ΠΏΠΎΠ΄Ρ ΠΎΠ΄ΠΈΡ Π΄Π»Ρ ΡΡΡΠΎΠΈΡΠ΅Π»ΡΡΡΠ²Π° Π²Π½ΡΡΡΠ΅Π½Π½ΠΈΡ ΠΈ Π½Π°ΡΡΠΆΠ½ΡΡ ΡΡΠ΅Π½ Π·Π΄Π°Π½ΠΈΠΉ.
Π’Π΅ΠΏΠ΅ΡΡ ΠΏΠΎΡΡΠ°ΠΏΠ½ΠΎ ΡΠ°ΡΡΠΌΠΎΡΡΠΈΠΌ ΠΏΡΠΎΡΠ΅ΡΡ ΠΈΠ·Π³ΠΎΡΠΎΠ²Π»Π΅Π½ΠΈΡ ΠΎΠΏΠΈΠ»ΠΊΠΎΠ±Π΅ΡΠΎΠ½Π° ΡΠ²ΠΎΠΈΠΌΠΈ ΡΡΠΊΠ°ΠΌΠΈ.
ΠΠ°Π³ΠΎΡΠΎΠ²ΠΊΠ° ΠΌΠ°ΡΠ΅ΡΠΈΠ°Π»ΠΎΠ²
Π’Π΅Ρ Π½ΠΎΠ»ΠΎΠ³ΠΈΡ ΠΏΡΠΎΠΈΠ·Π²ΠΎΠ΄ΡΡΠ²Π° ΠΎΠΏΠΈΠ»ΠΊΠΎΠ±Π΅ΡΠΎΠ½Π° ΠΏΡΠΎΡΡΠ°, ΠΏΠΎΡΡΠΎΠΌΡ ΠΌΠ½ΠΎΠ³ΠΈΠΌ Π½Π΅ ΡΠΎΡΡΠ°Π²ΠΈΡ ΡΡΡΠ΄Π° ΠΎΡΠ²ΠΎΠΈΡΡ Π΅Π΅ Π² Π΄ΠΎΠΌΠ°ΡΠ½ΠΈΡ ΡΡΠ»ΠΎΠ²ΠΈΡΡ . ΠΠΎΠΌΠΏΠΎΠ½Π΅Π½ΡΡ, ΠΈΠ· ΠΊΠΎΡΠΎΡΡΡ ΠΈΠ·Π³ΠΎΡΠ°Π²Π»ΠΈΠ²Π°Π΅ΡΡΡ ΠΌΠ°ΡΠ΅ΡΠΈΠ°Π», Ρ ΠΎΡΠΎΡΠΈ ΡΠ΅ΠΌ, ΡΡΠΎ Π½Π΅Ρ Π½Π΅ΠΎΠ±Ρ ΠΎΠ΄ΠΈΠΌΠΎΡΡΠΈ Π² ΠΈΡ ΠΏΡΠ΅Π΄Π²Π°ΡΠΈΡΠ΅Π»ΡΠ½ΠΎΠΉ Π·Π°Π³ΠΎΡΠΎΠ²ΠΊΠ΅. ΠΡΠ΅ ΡΠΎΡΡΠ°Π²Π»ΡΡΡΠΈΠ΅ Π±Π΅Π· ΠΏΡΠΎΠ±Π»Π΅ΠΌ ΠΌΠΎΠΆΠ½ΠΎ ΠΊΡΠΏΠΈΡΡ Π² ΡΡΡΠΎΠΈΡΠ΅Π»ΡΠ½ΠΎΠΌ ΠΌΠ°Π³Π°Π·ΠΈΠ½Π΅ ΠΈΠ»ΠΈ Π½Π° ΡΡΠ½ΠΊΠ΅, ΠΏΡΡΠΌΠΎ Π² Π΄Π΅Π½Ρ ΠΈΠ·Π³ΠΎΡΠΎΠ²Π»Π΅Π½ΠΈΡ. ΠΡΠ°ΠΊ, Π΄Π»Ρ ΡΠ°ΠΌΠΎΡΡΠΎΡΡΠ΅Π»ΡΠ½ΠΎ ΠΏΡΠΎΠΈΠ·Π²ΠΎΠ΄ΡΡΠ²Π° ΠΎΠΏΠΈΠ»ΠΊΠΎΠ±Π΅ΡΠΎΠ½Π° Π½Π΅ΠΎΠ±Ρ ΠΎΠ΄ΠΈΠΌΠΎ ΠΏΡΠΈΠΎΠ±ΡΠ΅ΡΡΠΈ ΡΠ°ΠΊΠΈΠ΅ ΠΌΠ°ΡΠ΅ΡΠΈΠ°Π»Ρ: ΠΎΠΏΠΈΠ»ΠΊΠΈ, ΠΏΠ΅ΡΠΎΠΊ, ΡΠ΅ΠΌΠ΅Π½Ρ, Π³Π»ΠΈΠ½Π° ΠΈΠ»ΠΈ ΠΈΠ·Π²Π΅ΡΡΡ.
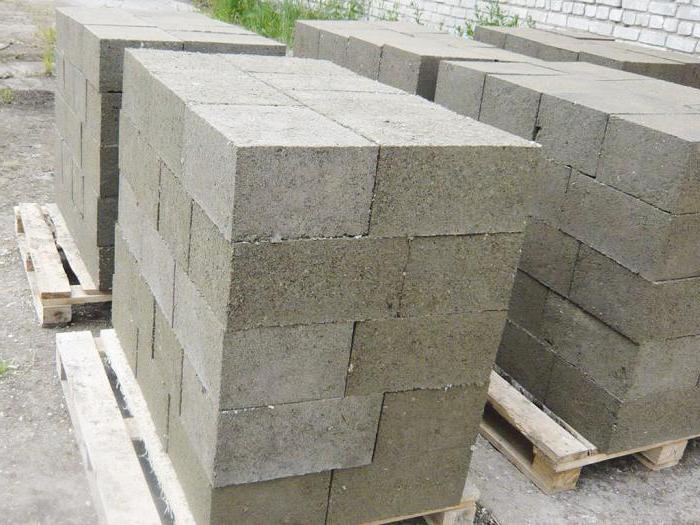
Π‘ΠΌΠ΅ΡΠΈΠ²Π°Π½ΠΈΠ΅
ΠΠ΄Π½ΠΎΠΉ ΠΈΠ· Π½Π°ΠΈΠ±ΠΎΠ»Π΅Π΅ ΡΡΡΠ΄ΠΎΠ΅ΠΌΠΊΠΈΡ ΡΡΠ°Π΄ΠΈΠΉ Π² ΠΏΡΠΎΠΈΠ·Π²ΠΎΠ΄ΡΡΠ²Π΅ ΠΎΠΏΠΈΠ»ΠΊΠΎΠ±Π΅ΡΠΎΠ½Π° (ΡΠ²ΠΎΠΈΠΌΠΈ ΡΡΠΊΠ°ΠΌΠΈ ΠΈΠ·Π³ΠΎΡΠΎΠ²ΠΈΡΡ Π±Π»ΠΎΠΊΠΈ ΠΌΠΎΠΆΠ΅Ρ Π΄Π°ΠΆΠ΅ Π½Π°ΡΠΈΠ½Π°ΡΡΠΈΠΉ ΡΡΡΠΎΠΈΡΠ΅Π»Ρ) ΡΠ²Π»ΡΠ΅ΡΡΡ ΠΏΠ΅ΡΠ΅ΠΌΠ΅ΡΠΈΠ²Π°Π½ΠΈΠ΅, ΠΏΠΎΡΡΠΎΠΌΡ ΡΠ΅ΠΊΠΎΠΌΠ΅Π½Π΄ΡΠ΅ΡΡΡ ΠΈΡΠΏΠΎΠ»ΡΠ·ΠΎΠ²Π°ΡΡ Π±Π΅ΡΠΎΠ½ΠΎΠΌΠ΅ΡΠ°Π»ΠΊΡ ΠΈΠ»ΠΈ Ρ ΠΎΡΡ Π±Ρ ΡΠ°ΡΡΠ²ΠΎΡΠΎΡΠΌΠ΅ΡΠΈΡΠ΅Π»Ρ. ΠΡΠΎ ΠΏΠΎΠ·Π²ΠΎΠ»ΠΈΡ ΡΠ΄Π΅Π»Π°ΡΡ ΠΏΡΠΎΡΠ΅Π΄ΡΡΡ ΡΠΌΠ΅ΡΠΈΠ²Π°Π½ΠΈΡ Π½Π΅ ΡΠΎΠ»ΡΠΊΠΎ Π±ΠΎΠ»Π΅Π΅ ΠΊΠΎΠΌΡΠΎΡΡΠ½ΠΎΠΉ, Π½ΠΎ ΠΈ Π±ΠΎΠ»Π΅Π΅ ΠΊΠ°ΡΠ΅ΡΡΠ²Π΅Π½Π½ΠΎΠΉ. ΠΡΠ΅ΠΆΠ΄Π΅ ΡΠ΅ΠΌ Π·Π°ΡΡΠΏΠ°ΡΡ Π²ΡΡΡΡΠ΅Π½Π½ΡΠ΅ ΠΎΠΏΠΈΠ»ΠΊΠΈ Π² Π±Π΅ΡΠΎΠ½ΠΎΠΌΠ΅ΡΠ°Π»ΠΊΡ, ΠΈΡ Π½ΡΠΆΠ½ΠΎ ΠΏΡΠΎΡΠ΅ΡΡΡ ΡΠ΅ΡΠ΅Π· ΡΠΈΡΠΎ ΡΠΎ ΡΡΠΎΡΠΎΠ½ΠΎΠΉ ΡΡΠ΅ΠΉΠΊΠΈ 1 ΡΠΌ. ΠΠ°ΡΠ΅ΠΌ ΠΌΠΎΠΆΠ½ΠΎ ΡΠΌΠ΅ΡΠ°ΡΡ ΠΎΠΏΠΈΠ»ΠΊΠΈ Ρ ΡΠ΅ΠΌΠ΅Π½ΡΠΎΠΌ. ΠΠΈΡΡ ΠΏΠΎΡΠ»Π΅ ΡΡΠΎΠ³ΠΎ Π² ΡΠΌΠ΅ΡΡ Π΄ΠΎΠ±Π°Π²Π»ΡΡΡ Π³Π»ΠΈΠ½ΡΠ½ΠΎΠ΅ ΠΈΠ»ΠΈ ΠΈΠ·Π²Π΅ΡΡΠΊΠΎΠ²ΠΎΠ΅ ΡΠ΅ΡΡΠΎ, Π·Π°Π³ΠΎΡΠΎΠ²Π»Π΅Π½Π½ΠΎΠ΅ Π·Π°ΡΠ°Π½Π΅Π΅. ΠΡΠ΅ ΠΊΠΎΠΌΠΏΠΎΠ½Π΅Π½ΡΡ Π½ΡΠΆΠ½ΠΎ ΡΡΠ°ΡΠ΅Π»ΡΠ½ΠΎ ΠΏΠ΅ΡΠ΅ΠΌΠ΅ΡΠ°ΡΡ ΠΈ ΡΠ°Π·Π²Π΅ΡΡΠΈ Π²ΠΎΠ΄ΠΎΠΉ. ΠΠΎΠ΄Ρ Π½ΡΠΆΠ½ΠΎ Π΄ΠΎΠ±Π°Π²Π»ΡΡΡ ΠΌΠ°Π»ΡΠΌΠΈ ΠΏΠΎΡΡΠΈΡΠΌΠΈ. ΠΠΎΡΠ»Π΅ ΠΊΠ°ΠΆΠ΄ΠΎΠ³ΠΎ Π΄ΠΎΠ»ΠΈΠ²Π° Π½Π΅ΠΎΠ±Ρ ΠΎΠ΄ΠΈΠΌΠΎ ΠΏΠ΅ΡΠ΅ΠΌΠ΅ΡΠΈΠ²Π°ΡΡ ΡΠΌΠ΅ΡΡ ΠΎΠΏΠΈΠ»ΠΊΠΎΠ±Π΅ΡΠΎΠ½Π°. ΠΡΠΎΠΏΠΎΡΡΠΈΠΈ ΠΊΠΎΠΌΠΏΠΎΠ½Π΅Π½ΡΠΎΠ² ΡΡΡΠ°Π½Π°Π²Π»ΠΈΠ²Π°ΡΡΡΡ ΠΈΠ½Π΄ΠΈΠ²ΠΈΠ΄ΡΠ°Π»ΡΠ½ΠΎ, Π² Π·Π°Π²ΠΈΡΠΈΠΌΠΎΡΡΠΈ ΠΎΡ Π½Π°Π·Π½Π°ΡΠ΅Π½ΠΈΡ ΠΊΠΎΠ½Π΅ΡΠ½ΠΎΠ³ΠΎ ΠΈΠ·Π΄Π΅Π»ΠΈΡ. Π§Π΅ΠΌ Π±ΠΎΠ»ΡΡΠ΅ Π½Π°Π³ΡΡΠ·ΠΊΠΈ Π±ΡΠ΄Π΅Ρ ΠΏΡΠΈΡ ΠΎΠ΄ΠΈΡΡΡΡ Π½Π° Π±Π»ΠΎΠΊΠΈ, ΡΠ΅ΠΌ Π²ΡΡΠ΅ ΠΈΡ ΠΌΠ°ΡΠΊΠ°.
ΠΡΠ»ΠΈ Π·Π°ΠΌΠ΅Ρ ΠΎΠΏΠΈΠ»ΠΊΠΎΠ±Π΅ΡΠΎΠ½Π° ΠΏΡΠΎΠΈΠ·Π²Π΅Π΄Π΅Π½ Π½Π°Π΄Π»Π΅ΠΆΠ°ΡΠΈΠΌ ΠΎΠ±ΡΠ°Π·ΠΎΠΌ, ΡΠΎ ΠΏΡΠΈ ΡΠΆΠ°ΡΠΈΠΈ Π² ΠΊΡΠ»Π°ΠΊΠ΅ ΡΠΌΠ΅ΡΡ Π±ΡΠ΄Π΅Ρ ΠΎΠ±ΡΠ°Π·ΠΎΠ²Π°ΡΡ ΠΏΠ»Π°ΡΡΠΈΡΠ½ΡΠΉ ΠΊΠΎΠΌΠΎΠΊ, Π½Π° ΠΊΠΎΡΠΎΡΠΎΠΌ ΠΏΡΠΈ ΠΎΡΡΡΡΡΡΠ²ΠΈΠΈ ΠΊΠ°ΠΏΠ΅Π»Ρ Π²ΠΎΠ΄Ρ Π±ΡΠ΄ΡΡ ΠΏΡΠΎΡΠΌΠ°ΡΡΠΈΠ²Π°ΡΡΡΡ Π²ΠΌΡΡΠΈΠ½Ρ ΠΎΡ ΠΏΠ°Π»ΡΡΠ΅Π². ΠΡΠΎ ΡΡΠΈΡΠ°Π΅ΡΡΡ ΠΎΡΠ½ΠΎΠ²Π½ΡΠΌ ΠΏΠΎΠΊΠ°Π·Π°ΡΠ΅Π»ΡΠΌ ΠΏΡΠ°Π²ΠΈΠ»ΡΠ½ΠΎ ΠΏΡΠΈΠ³ΠΎΡΠΎΠ²Π»Π΅Π½Π½ΠΎΠΉ ΡΠΌΠ΅ΡΠΈ.
Π€ΠΎΡΠΌΠΈΡΠΎΠ²Π°Π½ΠΈΠ΅ Π±Π»ΠΎΠΊΠΎΠ²
ΠΠΎΠ³Π΄Π° ΡΠΌΠ΅ΡΡ Π³ΠΎΡΠΎΠ²Π°, Π΅Π΅ Π½ΡΠΆΠ½ΠΎ ΡΡΠ°ΡΠ΅Π»ΡΠ½ΠΎ ΡΡΡΠ°ΠΌΠ±ΠΎΠ²Π°ΡΡ Π² Π·Π°Π³ΠΎΡΠΎΠ²Π»Π΅Π½Π½ΡΠ΅ Π·Π°ΡΠ°Π½Π΅Π΅ ΡΠΎΡΠΌΡ. Π ΡΡΠΎΠΌ Π΄Π΅Π»Π΅ Π½ΠΈ Π² ΠΊΠΎΠ΅ΠΌ ΡΠ»ΡΡΠ°Π΅ Π½Π΅Π»ΡΠ·Ρ ΠΌΠ΅Π΄Π»ΠΈΡΡ, ΡΠ°ΠΊ ΠΊΠ°ΠΊ ΡΠ΅ΡΠ΅Π· ΠΏΠΎΠ»ΡΠΎΡΠ°-Π΄Π²Π° ΡΠ°ΡΠ° ΡΠΌΠ΅ΡΡ Π±ΡΡΡΡΠΎ Π½Π°ΡΠΈΠ½Π°Π΅Ρ Π·Π°ΡΠ²Π΅ΡΠ΄Π΅Π²Π°ΡΡ. Π ΡΠΎΡΠΌΠ°Ρ Π±Π»ΠΎΠΊΠΈ ΠΎΡΡΠ°ΡΡΡΡ Π½Π° 3-5 Π΄Π½Π΅ΠΉ. ΠΠ°ΡΠ΅ΠΌ ΠΊΠ°ΡΠΊΠ°Ρ ΡΠ±ΠΈΡΠ°Π΅ΡΡΡ, Π° ΠΈΠ·Π΄Π΅Π»ΠΈΡ ΠΏΡΠΎΠ΄ΠΎΠ»ΠΆΠ°ΡΡ ΡΡΡΠΈΡΡΡΡ Π½Π° ΠΏΡΠΎΡΡΠΆΠ΅Π½ΠΈΠΈ ΠΌΠ΅ΡΡΡΠ°. ΠΠΎ ΠΏΡΠΎΡΠ΅ΡΡΠ²ΠΈΠΈ ΡΡΠΎΠ³ΠΎ Π²ΡΠ΅ΠΌΠ΅Π½ΠΈ Ρ Π±Π»ΠΎΠΊΠ°ΠΌΠΈ ΠΌΠΎΠΆΠ½ΠΎ Π½Π°ΡΠΈΠ½Π°ΡΡ ΡΠ°Π±ΠΎΡΠ°ΡΡ, ΠΎΠ΄Π½Π°ΠΊΠΎ ΠΏΠΎΠ»Π½ΠΎΠ΅ Π²ΡΡΡΡΠΈΠ²Π°Π½ΠΈΠ΅ ΠΏΡΠΎΠΈΡΡ ΠΎΠ΄ΠΈΡ Π»ΠΈΡΡ ΠΏΠΎΡΠ»Π΅ 3 ΠΌΠ΅ΡΡΡΠ΅Π², ΠΏΠΎΡΡΠΎΠΌΡ Ρ ΠΎΠ±Π»ΠΈΡΠΎΠ²ΠΊΠΎΠΉ ΡΠΎΡΠΎΠΏΠΈΡΡΡΡ Π½Π΅ ΡΡΠΎΠΈΡ. ΠΠΎΠ΄ΡΠΎΠ±Π½Π΅Π΅ ΠΎ ΡΠΎΠΌ, ΡΠΊΠΎΠ»ΡΠΊΠΎ ΡΠΎΡ Π½Π΅Ρ ΠΎΠΏΠΈΠ»ΠΊΠΎΠ±Π΅ΡΠΎΠ½, ΠΏΠΎΠ³ΠΎΠ²ΠΎΡΠΈΠΌ Π½Π΅ΠΌΠ½ΠΎΠ³ΠΎ Π½ΠΈΠΆΠ΅.
Π€ΠΎΡΠΌΠ° Π΄Π»Ρ ΠΎΡΠ»ΠΈΠ²ΠΊΠΈ
ΠΠΏΠΈΠ»ΠΊΠΎΠ±Π΅ΡΠΎΠ½ ΠΌΠΎΠΆΠ½ΠΎ ΠΈΡΠΏΠΎΠ»ΡΠ·ΠΎΠ²Π°ΡΡ Π² ΠΌΠΎΠ½ΠΎΠ»ΠΈΡΠ½ΠΎΠΌ ΡΡΡΠΎΠΈΡΠ΅Π»ΡΡΡΠ²Π΅ Ρ ΠΏΡΠΈΠΌΠ΅Π½Π΅Π½ΠΈΠ΅ΠΌ ΠΎΠΏΠ°Π»ΡΠ±ΠΎΠΊ. ΠΠ΄Π½Π°ΠΊΠΎ ΡΠ°ΡΠ΅ Π²ΡΠ΅Π³ΠΎ ΡΡΡΠΎΠΈΡΠ΅Π»ΠΈ ΠΏΡΠ΅Π΄ΠΏΠΎΡΠΈΡΠ°ΡΡ Π½Π΅ ΠΌΠΎΠ½ΠΎΠ»ΠΈΡΠ½ΡΠΉ ΠΎΠΏΠΈΠ»ΠΊΠΎΠ±Π΅ΡΠΎΠ½, Π° Π±Π»ΠΎΡΠ½ΡΠΉ. Π€ΠΎΡΠΌΡ Π΄Π»Ρ ΠΎΡΠ»ΠΈΠ²ΠΊΠΈ Π±Π»ΠΎΠΊΠΎΠ² ΠΈΠ·Π³ΠΎΡΠ°Π²Π»ΠΈΠ²Π°ΡΡΡΡ Π² ΠΏΠ΅ΡΠ²ΡΡ ΠΎΡΠ΅ΡΠ΅Π΄Ρ, Ρ. ΠΊ. ΠΏΠΎΡΠ»Π΅ Π·Π°ΠΌΠ΅ΡΠΈΠ²Π°Π½ΠΈΡ ΡΠΌΠ΅ΡΠΈ ΠΎΠ½ΠΈ Π΄ΠΎΠ»ΠΆΠ½Ρ Π±ΡΡΡ ΠΏΠΎΠ»Π½ΠΎΡΡΡΡ Π³ΠΎΡΠΎΠ²Ρ. ΠΠΎΡΠΊΠΎΠ»ΡΠΊΡ ΠΏΡΠΎΡΠ΅ΡΡ Π²ΡΡΡΡ Π°Π½ΠΈΡ Π±Π»ΠΎΠΊΠΎΠ² Π΄ΠΎΠ²ΠΎΠ»ΡΠ½ΠΎ ΠΏΡΠΎΠ΄ΠΎΠ»ΠΆΠΈΡΠ΅Π»Π΅Π½, ΡΠ΅ΠΊΠΎΠΌΠ΅Π½Π΄ΡΠ΅ΡΡΡ ΡΠ΄Π΅Π»Π°ΡΡ ΡΡΠ°Π·Ρ 10-20 ΡΠΎΡΠΌ.
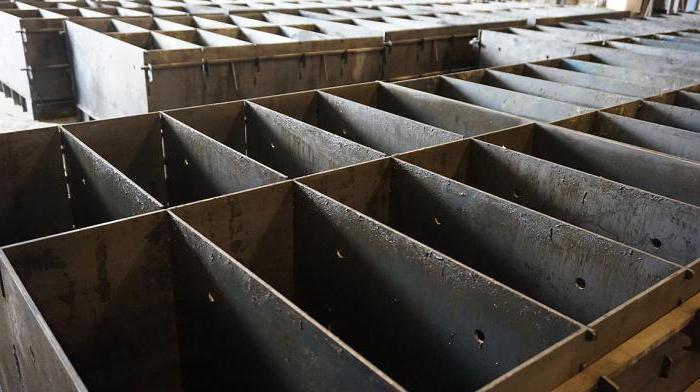
ΠΠ»Ρ ΠΊΡΡΠΏΠ½ΡΡ Π±Π»ΠΎΠΊΠΎΠ² ΠΈΠ·Π³ΠΎΡΠ°Π²Π»ΠΈΠ²Π°ΡΡΡΡ ΡΠ°Π·Π±ΠΎΡΠ½ΡΠ΅ Π΄Π²ΠΎΠΉΠ½ΡΠ΅ ΠΈΠ»ΠΈ Π΄Π°ΠΆΠ΅ ΠΎΠ΄ΠΈΠ½Π°ΡΠ½ΡΠ΅ ΡΠΎΡΠΌΡ. ΠΠΎ ΡΡΡΠΈ, ΠΎΠ½ΠΈ ΠΏΡΠ΅Π΄ΡΡΠ°Π²Π»ΡΡΡ ΡΠΎΠ±ΠΎΠΉ ΡΠ±ΠΈΡΡΠ΅ ΠΈΠ· Π΄ΠΎΡΠΎΠΊ ΡΡΠΈΠΊΠΈ ΡΠ°Π·ΡΠ΅ΠΌΠ½ΠΎΠΉ ΠΊΠΎΠ½ΡΡΡΡΠΊΡΠΈΠΈ. ΠΠ»Ρ ΡΡΠΈΡ ΡΠ΅Π»Π΅ΠΉ ΠΎΠ±ΡΡΠ½ΠΎ ΠΈΡΠΏΠΎΠ»ΡΠ·ΡΡΡ Π΄ΠΎΡΠΊΠΈ ΡΠΎΠ»ΡΠΈΠ½ΠΎΠΉ 2 ΡΠΌ. ΠΡΠ΄Π΅Π»ΡΠ½ΡΠ΅ ΡΠ°ΡΡΠΈ ΠΊΠΎΠ½ΡΡΡΡΠΊΡΠΈΠΈ ΡΠΊΡΠ΅ΠΏΠ»ΡΡΡΡΡ ΠΌΠ΅ΠΆΠ΄Ρ ΡΠΎΠ±ΠΎΠΉ Π-ΠΎΠ±ΡΠ°Π·Π½ΡΠΌΠΈ ΡΡΠ°Π»ΡΠ½ΡΠΌΠΈ ΡΡΠ΅ΡΠΆΠ½ΡΠΌ, Ρ ΡΠ΅Π·ΡΠ±ΠΎΠΉ Π8 ΠΏΠΎΠ΄ Π±Π°ΡΠ°ΡΠΊΠΎΠ²ΡΡ Π³Π°ΠΉΠΊΡ.
ΠΠ»Ρ Π½Π΅Π±ΠΎΠ»ΡΡΠΈΡ Π±Π»ΠΎΠΊΠΎΠ² ΠΈΠ·Π³ΠΎΡΠ°Π²Π»ΠΈΠ²Π°ΡΡ Β«ΠΎΡΡΠΎΠ²ΡΠ΅Β» ΠΊΠ°ΡΠΊΠ°ΡΡ ΠΈΠ· ΡΠ΅Ρ ΠΆΠ΅ 20-ΠΌΠΈΠ»Π»ΠΈΠΌΠ΅ΡΡΠΎΠ²ΡΡ Π΄ΠΎΡΠΎΠΊ. Π ΠΎΡΠ½ΠΎΠ²Π½ΠΎΠΌ ΡΠΎΡΠΌΡ Π΄Π΅Π»Π°ΡΡ ΡΡΠ°Π·Ρ Π½Π° 9 ΡΡΠ΅Π΅ΠΊ. ΠΠΎ ΠΆΠ΅Π»Π°Π½ΠΈΡ ΠΊΠΎΠ»ΠΈΡΠ΅ΡΡΠ²ΠΎ ΡΡΠ΅Π΅ΠΊ ΠΌΠΎΠΆΠ½ΠΎ Π²Π°ΡΡΠΈΡΠΎΠ²Π°ΡΡ ΠΊΠ°ΠΊ Π² Π±ΠΎΠ»ΡΡΡΡ, ΡΠ°ΠΊ ΠΈ Π² ΠΌΠ΅Π½ΡΡΡΡ ΡΡΠΎΡΠΎΠ½Ρ. ΠΠ½ΡΡΡΠ΅Π½Π½ΠΈΠ΅ Π΄ΠΎΡΠΊΠΈ ΠΊΠΎΠ½ΡΡΡΡΠΊΡΠΈΠΈ ΠΊΡΠ΅ΠΏΡΡΡΡ Π΄ΡΡΠ³ ΠΊ Π΄ΡΡΠ³Ρ Ρ ΠΏΠΎΠΌΠΎΡΡΡ Π·Π°Π΄Π²ΠΈΠΆΠ½ΡΡ ΠΏΠ°Π·ΠΎΠ², Π° Π½Π°ΡΡΠΆΠ½ΡΠ΅ β Ρ ΠΏΠΎΠΌΠΎΡΡΡ Π-ΠΎΠ±ΡΠ°Π·Π½ΡΡ ΡΡΠ΅ΡΠΆΠ½Π΅ΠΉ.
Π§ΡΠΎΠ±Ρ Π΄ΠΎΡΠΊΠΈ, ΠΈΠ· ΠΊΠΎΡΠΎΡΡΡ ΠΈΠ·Π³ΠΎΡΠΎΠ²Π»Π΅Π½Π° ΡΠΎΡΠΌΠ° Π΄Π»Ρ ΠΎΡΠ»ΠΈΠ²ΠΊΠΈ, Π½Π΅ Π²ΠΏΠΈΡΡΠ²Π°Π»ΠΈ Π²Π»Π°Π³Ρ, Π²Π½ΡΡΡΠ΅Π½Π½ΠΈΠ΅ ΡΡΠ΅Π½ΠΊΠΈ ΠΊΠΎΠ½ΡΡΡΡΠΊΡΠΈΠΈ ΠΎΠ±ΠΈΠ²Π°ΡΡ ΠΏΠ»Π°ΡΡΠΈΠΊΠΎΠΌ ΠΈΠ»ΠΈ ΠΊΡΠΎΠ²Π΅Π»ΡΠ½ΠΎΠΉ ΡΡΠ°Π»ΡΡ, ΠΈΠ»ΠΈ ΠΆΠ΅ ΠΏΠΎΠΏΡΠΎΡΡΡ ΠΏΡΠΎΠΊΠ»Π°Π΄ΡΠ²Π°ΡΡ ΠΏΠΎΠ»ΠΈΡΡΠΈΠ»Π΅Π½ΠΎΠΌ. ΠΡΠΎ Π½Π΅ ΡΠΎΠ»ΡΠΊΠΎ ΠΏΠΎΠ·Π²ΠΎΠ»ΡΠ΅Ρ ΠΎΠ±Π΅Π·ΠΎΠΏΠ°ΡΠΈΡΡ Π΄Π΅ΡΠ΅Π²ΠΎ ΠΎΡ Π²Π»Π°Π³ΠΈ, Π½ΠΎ ΠΈ ΠΎΠ±Π»Π΅Π³ΡΠ°Π΅Ρ ΠΏΡΠΎΡΠ΅Π΄ΡΡΡ Π²ΡΠ½ΠΈΠΌΠ°Π½ΠΈΡ Π·Π°ΡΡΡΠ²ΡΠΈΡ Π±Π»ΠΎΠΊΠΎΠ².
Π Π°Π·ΠΌΠ΅Ρ Π±Π»ΠΎΠΊΠΎΠ²
Π Π°Π·ΠΌΠ΅Ρ ΠΎΠΏΠΈΠ»ΠΊΠΎΠ±Π΅ΡΠΎΠ½ΠΎΠ²ΡΡ Π±Π»ΠΎΠΊΠΎΠ² ΡΡΠ°Π½Π΄Π°ΡΡΠ°ΠΌΠΈ Π½Π΅ ΡΡΡΠ°Π½ΠΎΠ²Π»Π΅Π½. ΠΠ½ ΠΌΠΎΠΆΠ΅Ρ Π·Π°Π²ΠΈΡΠ΅ΡΡ ΠΎΡ ΡΡΠ΄Π° ΠΏΠΎΠΊΠ°Π·Π°ΡΠ΅Π»Π΅ΠΉ: ΡΠΎΠ»ΡΠΈΠ½Π° ΡΡΠ΅Π½, ΡΠΈΡΠΈΠ½Π° ΠΏΡΠΎΠ΅ΠΌΠΎΠ² ΠΈ ΠΏΡΠΎΡΡΠ΅Π½ΠΊΠΎΠ², ΡΠ°ΡΡΡΠΎΡΠ½ΠΈΠ΅ ΠΌΠ΅ΠΆΠ΄Ρ ΠΏΡΠΎΠ΅ΠΌΠ°ΠΌΠΈ ΠΈ ΡΠ³Π»Π°ΠΌΠΈ Π·Π΄Π°Π½ΠΈΡ ΠΈ ΡΠΏΠΎΡΠΎΠ±Π° ΡΠΊΠ»Π°Π΄ΠΊΠΈ. ΠΠ»Ρ Π±ΠΎΠ»Π΅Π΅ ΡΠ΄ΠΎΠ±Π½ΠΎΠ³ΠΎ Π²ΠΎΠ·Π²Π΅Π΄Π΅Π½ΠΈΡ Π·Π΄Π°Π½ΠΈΡ Π΄Π»ΠΈΠ½Ρ ΡΡΠ°ΡΡΠΊΠΎΠ² ΡΡΠ΅Π½ ΡΡΡΠ°Π½Π°Π²Π»ΠΈΠ²Π°ΡΡΡΡ ΡΠ°ΠΊΠΈΠΌ ΠΎΠ±ΡΠ°Π·ΠΎΠΌ, ΡΡΠΎΠ±Ρ ΠΎΠ½ΠΈ Π±ΡΠ»ΠΈ ΠΊΡΠ°ΡΠ½Ρ ΡΠ°Π·ΠΌΠ΅ΡΠ°ΠΌ Π±Π»ΠΎΠΊΠΎΠ².
ΠΠ»Ρ ΠΏΡΠΎΡΡΠΎΡΡ ΠΏΠΎΠ΄ΡΡΠ΅ΡΠΎΠ² ΠΈ ΡΠ½ΠΈΡΠΈΠΊΠ°ΡΠΈΠΈ ΠΏΡΠΎΠ΅ΠΊΡΠ° ΡΠΎΠ»ΡΠΈΠ½Π° Π±Π»ΠΎΠΊΠ° ΠΎΠ±ΡΡΠ½ΠΎ ΡΠ°Π²Π½ΡΠ΅ΡΡΡ 140 ΠΌΠΌ β Π΄Π²Π΅ ΡΠΎΠ»ΡΠΈΠ½Ρ ΠΊΠΈΡΠΏΠΈΡΠ° (ΠΊΡΠ°ΡΠ½ΠΎΠ³ΠΎ), Ρ ΡΡΠ΅ΡΠΎΠΌ ΡΠ»ΠΎΠΆΠ΅Π½Π½ΠΎΠ³ΠΎ ΠΌΠ΅ΠΆΠ΄Ρ Π½ΠΈΠΌΠΈ ΡΠ°ΡΡΠ²ΠΎΡΠ°. Π’Π°ΠΊΠΎΠΉ ΠΏΠΎΠ΄Ρ ΠΎΠ΄ ΠΎΡΠ΅Π½Ρ ΠΏΡΠ°ΠΊΡΠΈΡΠ΅Π½, ΡΡΠΈΡΡΠ²Π°Ρ, ΡΡΠΎ Π² ΠΏΡΠΎΡΠ΅ΡΡΠ΅ ΡΠΊΠ»Π°Π΄ΠΊΠΈ ΡΠ°ΡΡΠΎ Π΄ΠΎΠΏΠΎΠ»Π½ΠΈΡΠ΅Π»ΡΠ½ΠΎ ΠΈΡΠΏΠΎΠ»ΡΠ·ΡΠ΅ΡΡΡ ΠΊΡΠ°ΡΠ½ΡΠΉ ΠΊΠΈΡΠΏΠΈΡ. Π§ΡΠΎΠ±Ρ Π±Π»ΠΎΠΊΠΈ Π±ΡΡΡΡΠ΅Π΅ Π²ΡΡΡΡ Π°Π»ΠΈ ΠΈ ΠΈΠΌΠ΅Π»ΠΈ Π»ΡΡΡΠΈΠ΅ ΡΠ΅ΠΏΠ»ΠΎΠ·Π°ΡΠΈΡΠ½ΡΠ΅ ΡΠ²ΠΎΠΉΡΡΠ²Π°, Π² Π½ΠΈΡ Π΄Π΅Π»Π°Π΅ΡΡΡ 2-3 ΠΎΡΠ²Π΅ΡΡΡΠΈΡ.
Π£ΡΠΈΡΡΠ²Π°Ρ, ΡΡΠΎ ΠΏΡΠΈ Π²ΡΡΡΡ Π°Π½ΠΈΠΈ Π±Π»ΠΎΠΊΠΎΠ² ΠΏΡΠΎΠΈΡΡ ΠΎΠ΄ΠΈΡ ΠΈΡ ΡΡΡΡΠΊΠ°, Π²Π½ΡΡΡΠ΅Π½Π½ΠΈΠ΅ ΡΠ°Π·ΠΌΠ΅ΡΡ ΡΠΎΡΠΌ Π΄Π»Ρ Π»ΠΈΡΡΡ Π΄ΠΎΠ»ΠΆΠ½Ρ Π±ΡΡΡ ΠΏΡΠΈΠΌΠ΅ΡΠ½ΠΎ Π½Π° 10 % Π±ΠΎΠ»ΡΡΠ΅ ΠΏΡΠ΅Π΄ΠΏΠΎΠ»Π°Π³Π°Π΅ΠΌΡΡ ΡΠ°Π·ΠΌΠ΅ΡΠΎΠ² Π±Π»ΠΎΠΊΠΎΠ². Π’Π°ΠΊ, ΠΊ ΠΏΡΠΈΠΌΠ΅ΡΡ, Π΄Π»Ρ Π±Π»ΠΎΠΊΠ° Π³Π°Π±Π°ΡΠΈΡΠ°ΠΌΠΈ 120 Ρ 250 Ρ 140 ΠΌΠΌ Π½Π΅ΠΎΠ±Ρ ΠΎΠ΄ΠΈΠΌΠ° ΡΡΠ΅ΠΉΠΊΠ° ΡΠ°Π·ΠΌΠ΅ΡΠ°ΠΌΠΈ 132 Ρ 275 Ρ 154 ΠΌΠΌ.
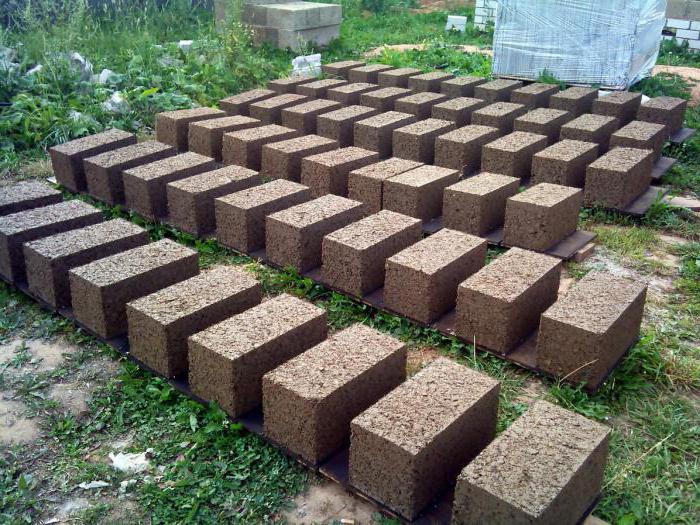
ΠΡΠ°Π½ΡΡ
ΠΡΠ΅ΠΆΠ΄Π΅ ΡΠ΅ΠΌ Π·Π°ΠΏΠΎΠ»Π½ΠΈΡΡ Π΄Π΅ΡΠ΅Π²ΡΠ½Π½ΡΠ΅ ΡΠΎΡΠΌΡ ΠΎΠΏΠΈΠ»ΠΊΠΎΠ±Π΅ΡΠΎΠ½Π½ΠΎΠΉ ΡΠΌΠ΅ΡΡΡ, ΠΈΡ ΡΡΡΠ°Π½Π°Π²Π»ΠΈΠ²Π°ΡΡ Π½Π° ΡΠΎΠ²Π½ΡΠ΅ ΠΏΠ»Π°ΡΡΠΈΠΊΠΎΠ²ΡΠ΅ ΠΈΠ»ΠΈ ΡΡΠ°Π»ΡΠ½ΡΠ΅ ΠΏΠΎΠ΄Π΄ΠΎΠ½Ρ, ΠΏΠΎΡΡΠΏΠ°Π½Π½ΡΠ΅ ΡΠΎΠ½ΠΊΠΈΠΌ ΡΠ»ΠΎΠ΅ΠΌ ΠΎΠΏΠΈΠ»ΠΎΠΊ. ΠΠ°ΡΠ΅ΠΌ Π²Π½ΡΡΡΠΈ ΡΡΠ΅Π΅ΠΊ ΡΡΡΠ°Π½Π°Π²Π»ΠΈΠ²Π°ΡΡ Π΄Π΅ΡΠ΅Π²ΡΠ½Π½ΡΠ΅ ΠΏΡΠΎΠ±ΠΊΠΈ, ΠΎΠ±Π΅ΡΠ½ΡΡΡΠ΅ ΡΠΎΠ»Π΅ΠΌ, ΠΊΠΎΡΠΎΡΡΠ΅ Π½Π΅ΠΎΠ±Ρ ΠΎΠ΄ΠΈΠΌΡ Π΄Π»Ρ ΠΏΠΎΠ»ΡΡΠ΅Π½ΠΈΡ ΠΎΡΠ²Π΅ΡΡΡΠΈΡ Π² Π±Π»ΠΎΠΊΠ°Ρ .
ΠΠΎΠ³Π΄Π° ΡΠΌΠ΅ΡΡ ΡΠ»ΠΎΠΆΠ΅Π½Π° Π² ΡΠΎΡΠΌΡ, Π΅Π΅ ΡΡΠ°ΠΌΠ±ΡΡΡ ΡΠΏΠ΅ΡΠΈΠ°Π»ΡΠ½ΠΎΠΉ ΡΡΠ°ΠΌΠ±ΠΎΠ²ΠΊΠΎΠΉ. ΠΠ° ΠΏΡΠΎΡΡΠΆΠ΅Π½ΠΈΠΈ ΠΏΠΎΡΠ»Π΅Π΄ΡΡΡΠΈΡ 3-5 Π΄Π½Π΅ΠΉ ΠΌΠ°ΡΠ΅ΡΠΈΠ°Π» ΠΏΡΠΈΠΎΠ±ΡΠ΅ΡΠ°Π΅Ρ ΠΎΡ 30 Π΄ΠΎ 40 ΠΏΡΠΎΡΠ΅Π½ΡΠΎΠ² ΠΌΠ°ΡΠΎΡΠ½ΠΎΠΉ ΠΏΡΠΎΡΠ½ΠΎΡΡΠΈ. ΠΠΎ ΠΈΡΡΠ΅ΡΠ΅Π½ΠΈΠΈ ΡΡΠΎΠ³ΠΎ ΡΡΠΎΠΊΠ° ΡΠΎΡΠΌΡ Π΄Π»Ρ Π»ΠΈΡΡΡ ΡΠ°Π·Π±ΠΈΡΠ°ΡΡ, Π° ΠΏΡΠΎΠ±ΠΊΠΈ ΠΈΠ·Π²Π»Π΅ΠΊΠ°ΡΡ ΠΈΠ· Π±Π»ΠΎΠΊΠΎΠ². ΠΠΎΡΠΎΠ²ΡΠ΅, Π½ΠΎ Π΅ΡΠ΅ Π½Π΅ Π²ΡΡΡΡΠ΅Π½Π½ΡΠ΅ ΠΈΠ·Π΄Π΅Π»ΠΈΡ ΠΎΡΡΠ°Π²Π»ΡΡΡ Π½Π° ΡΡΠΎΠΌ ΠΆΠ΅ ΠΌΠ΅ΡΡΠ΅ Π½Π° 3-4 Π΄Π½Ρ. ΠΠ° ΡΡΠΎ Π²ΡΠ΅ΠΌΡ ΠΈΡ ΠΏΡΠΎΡΠ½ΠΎΡΡΡ Π²ΠΎΠ·ΡΠ°ΡΡΠ°Π΅Ρ ΡΠΆΠ΅ Π΄ΠΎ 60-70 ΠΏΡΠΎΡΠ΅Π½ΡΠΎΠ².
ΠΠΊΠΎΠ½ΡΠ°ΡΠ΅Π»ΡΠ½Π°Ρ ΡΡΡΠΊΠ°
ΠΠΎΡΠ»Π΅Π΄Π½Π΅ΠΉ ΡΡΠ°Π΄ΠΈΠ΅ΠΉ ΠΈΠ·Π³ΠΎΡΠΎΠ²Π»Π΅Π½ΠΈΡ ΠΎΠΏΠΈΠ»ΠΊΠΎΠ±Π΅ΡΠΎΠ½Π° ΡΠ²Π»ΡΠ΅ΡΡΡ ΡΡΡΠΊΠ°. ΠΠ»Ρ ΠΎΠΊΠΎΠ½ΡΠ°ΡΠ΅Π»ΡΠ½ΠΎΠΉ ΡΡΡΠΊΠΈ Π±Π»ΠΎΠΊΠΈ Π½Π΅ΠΎΠ±Ρ ΠΎΠ΄ΠΈΠΌΠΎ ΠΏΠ΅ΡΠ΅Π½Π΅ΡΡΠΈ ΠΏΠΎΠ΄ Π½Π°Π²Π΅Ρ ΠΈΠ»ΠΈ Π½Π°ΠΊΡΡΡΡ ΠΏΠΎΠ»ΠΈΡΡΠΈΠ»Π΅Π½ΠΎΠΌ. ΠΠ΅Π»Π°ΡΠ΅Π»ΡΠ½ΠΎ, ΡΡΠΎΠ±Ρ ΠΎΠ½ΠΈ Π½Π°Ρ ΠΎΠ΄ΠΈΠ»ΠΈΡΡ Π½Π° ΡΠΊΠ²ΠΎΠ·Π½ΡΠΊΠ΅. Π£ΠΊΠ»Π°Π΄ΡΠ²Π°Ρ Π±Π»ΠΎΠΊΠΈ, Π½Π΅ΠΎΠ±Ρ ΠΎΠ΄ΠΈΠΌΠΎ ΠΎΡΡΠ°Π²Π»ΡΡΡ ΠΌΠ΅ΠΆΠ΄Ρ Π½ΠΈΠΌΠΈ Π·Π°Π·ΠΎΡΡ Π΄Π»Ρ Π²Π΅Π½ΡΠΈΠ»ΡΡΠΈΠΈ. ΠΠ°ΠΊ ΠΏΡΠ°Π²ΠΈΠ»ΠΎ, ΡΠΊΠ»Π°Π΄ΠΊΡ ΠΏΡΠΎΠΈΠ·Π²ΠΎΠ΄ΡΡ Π² Π²ΠΈΠ΄Π΅ ΡΡΠΎΠ»Π±ΠΎΠ². ΠΠ»Ρ Π½Π°ΡΠ°Π»Π° Π½Π° Π΄Π²Π° ΠΎΠ±ΠΎΠΆΠΆΠ΅Π½Π½ΡΡ ΠΊΠΈΡΠΏΠΈΡΠ° ΠΊΠ»Π°Π΄ΡΡ ΠΏΠ°ΡΡ ΡΡΠ΅Π½ΠΎΠ²ΡΡ Π±Π»ΠΎΠΊΠΎΠ², Π·Π°ΡΠ΅ΠΌ ΠΏΠΎΠΏΠ΅ΡΠ΅ΠΊ Π½ΠΈΡ Π΅ΡΠ΅ ΠΏΠ°ΡΡ ΠΈ ΡΠ°ΠΊ Π΄Π°Π»Π΅Π΅. Π‘ΠΏΡΡΡΡ ΠΌΠ΅ΡΡΡ Π±Π»ΠΎΠΊΠΈ Π·Π°ΡΠ²Π΅ΡΠ΄Π΅ΡΡ, Π²ΡΡΠΎΡ Π½ΡΡ ΠΈ Π΄ΠΎΡΡΠΈΠ³Π½ΡΡ 90 % ΠΏΡΠΎΡΠ½ΠΎΡΡΠΈ. Π§ΡΠΎΠ±Ρ ΠΎΠ½ΠΈ ΠΏΠΎΠ»ΡΡΠΈΠ»ΠΈΡΡ ΠΌΠ°ΠΊΡΠΈΠΌΠ°Π»ΡΠ½ΠΎ ΠΏΡΠΎΡΠ½ΡΠΌΠΈ, ΡΠ΅ΠΊΠΎΠΌΠ΅Π½Π΄ΡΠ΅ΡΡΡ ΠΏΠΎΠ΄ΠΎΠΆΠ΄Π°ΡΡ Π΅ΡΠ΅ ΡΡΠΈ ΠΌΠ΅ΡΡΡΠ°, ΠΏΡΠ΅ΠΆΠ΄Π΅ ΡΠ΅ΠΌ Π½Π°ΡΠ°ΡΡ ΡΡΡΠΎΠΈΡΠ΅Π»ΡΡΡΠ²ΠΎ. ΠΡΠ΅Π½Π΅Π±ΡΠ΅Π³Π°ΡΡ ΡΡΠΈΠΌ ΠΏΡΠ°Π²ΠΈΠ»ΠΎΠΌ ΠΈΠ»ΠΈ Π½Π΅Ρ β ΡΠ΅ΡΠ°ΡΡ Π²Π°ΠΌ, Π²ΡΠ΅ Π·Π°Π²ΠΈΡΠΈΡ ΠΎΡ ΡΠΈΠΏΠ° Π·Π΄Π°Π½ΠΈΡ, Π΄Π»Ρ ΠΊΠΎΡΠΎΡΠΎΠ³ΠΎ Π·Π°Π³ΠΎΡΠ°Π²Π»ΠΈΠ²Π°Π΅ΡΡΡ ΠΌΠ°ΡΠ΅ΡΠΈΠ°Π». Π ΠΏΡΠΈΠΌΠ΅ΡΡ, Π΄Π»Ρ Π²ΠΎΠ·Π²Π΅Π΄Π΅Π½ΠΈΡ Π±Π°Π½ΠΈ ΠΈΠ· ΠΎΠΏΠΈΠ»ΠΊΠΎΠ±Π΅ΡΠΎΠ½Π° Π²ΠΎΠ²ΡΠ΅ Π½Π΅ ΠΎΠ±ΡΠ·Π°ΡΠ΅Π»ΡΠ½ΠΎ ΠΆΠ΄Π°ΡΡ, ΠΏΠΎΠΊΠ° ΠΈΠ·Π΄Π΅Π»ΠΈΡ Π²ΡΡΠΎΡ Π½ΡΡ Π½Π° 100 %. ΠΠΎΠ»Π½ΠΎΡΡΡΡ Π³ΠΎΡΠΎΠ²ΡΠ΅ Π±Π»ΠΎΠΊΠΈ Π΄ΠΎΠ»ΠΆΠ½Ρ Π±ΡΡΡ ΡΠ²Π΅ΡΠ΄ΡΠΌΠΈ, ΠΏΡΠΎΡΠ½ΡΠΌΠΈ ΠΈ Π½Π΅ ΠΈΠΌΠ΅ΡΡ ΡΡΠ΅ΡΠΈΠ½. ΠΡΠΈ ΠΏΠ°Π΄Π΅Π½ΠΈΠΈ Ρ ΠΌΠ΅ΡΡΠΎΠ²ΠΎΠΉ Π²ΡΡΠΎΡΡ ΠΎΠ½ΠΈ Π½Π΅ Π΄ΠΎΠ»ΠΆΠ½Ρ ΡΠ°Π·Π±ΠΈΠ²Π°ΡΡΡΡ.
ΠΠΏΠΈΠ»ΠΊΠΎΠ±Π΅ΡΠΎΠ½: ΠΎΡΠ·ΡΠ²Ρ ΡΡΡΠΎΠΈΡΠ΅Π»Π΅ΠΉ
ΠΠΏΠΈΡΠ°ΡΡΡ Π½Π° ΠΎΡΠ·ΡΠ²Ρ ΠΎΠΏΡΡΠ½ΡΡ ΡΡΡΠΎΠΈΡΠ΅Π»Π΅ΠΉ, ΠΏΠ΅ΡΠ΅ΡΠΈΡΠ»ΠΈΠΌ ΠΎΡΠ½ΠΎΠ²Π½ΡΠ΅ Π΄ΠΎΡΡΠΎΠΈΠ½ΡΡΠ²Π° ΠΈ Π½Π΅Π΄ΠΎΡΡΠ°ΡΠΊΠΈ Π΄Π°Π½Π½ΠΎΠ³ΠΎ ΠΌΠ°ΡΠ΅ΡΠΈΠ°Π»Π°. ΠΠ°ΠΊ Π½Π΅ΡΠ»ΠΎΠΆΠ½ΠΎ Π΄ΠΎΠ³Π°Π΄Π°ΡΡΡΡ, ΠΎΠΏΠΈΠ»ΠΊΠΎΠ±Π΅ΡΠΎΠ½ ΠΏΠΎΠ΄ΠΊΡΠΏΠ°Π΅Ρ ΠΏΡΠ΅ΠΆΠ΄Π΅ Π²ΡΠ΅Π³ΠΎ ΡΠ²ΠΎΠ΅ΠΉ ΡΠΊΠΎΠ»ΠΎΠ³ΠΈΡΠ΅ΡΠΊΠΎΠΉ ΡΠΈΡΡΠΎΡΠΎΠΉ ΠΈ ΡΠ΅ΠΏΠ»ΠΎΠ·Π°ΡΠΈΡΠ½ΡΠΌΠΈ Ρ Π°ΡΠ°ΠΊΡΠ΅ΡΠΈΡΡΠΈΠΊΠ°ΠΌΠΈ. ΠΠ»Π°Π³ΠΎΠ΄Π°ΡΡ ΠΏΠΎΡΠ»Π΅Π΄Π½Π΅ΠΉ ΠΎΡΠΎΠ±Π΅Π½Π½ΠΎΡΡΠΈ Π² ΠΏΡΠΎΡΠ΅ΡΡΠ΅ Π²ΠΎΠ·Π²Π΅Π΄Π΅Π½ΠΈΡ Π·Π΄Π°Π½ΠΈΡ Π½Π΅Ρ Π½Π΅ΠΎΠ±Ρ ΠΎΠ΄ΠΈΠΌΠΎΡΡΠΈ Π² Π΄ΠΎΠΏΠΎΠ»Π½ΠΈΡΠ΅Π»ΡΠ½ΠΎΠΉ ΡΠ΅ΠΏΠ»ΠΎΠΈΠ·ΠΎΠ»ΡΡΠΈΠΈ ΡΡΠ΅Π½, ΡΡΠΎ ΠΏΠΎΠ·Π²ΠΎΠ»ΡΠ΅Ρ ΡΡΡΠ΅ΡΡΠ²Π΅Π½Π½ΠΎ ΡΡΠΊΠΎΠ½ΠΎΠΌΠΈΡΡ. ΠΠ½ΠΎΠ³ΠΎΠ»Π΅ΡΠ½ΠΈΠΉ ΠΎΠΏΡΡ ΠΈΡΠΏΠΎΠ»ΡΠ·ΠΎΠ²Π°Π½ΠΈΡ ΠΎΠΏΠΈΠ»ΠΊΠΎΠ±Π΅ΡΠΎΠ½Π° ΠΏΠΎΠΊΠ°Π·Π°Π», ΡΡΠΎ ΠΎΠ½ Π² ΡΠ°Π·Ρ ΠΏΡΠ΅Π²ΠΎΡΡ ΠΎΠ΄ΠΈΡ Π΄ΡΡΠ³ΠΈΠ΅ ΠΌΠ°ΡΠ΅ΡΠΈΠ°Π»Ρ Ρ ΡΠΎΡΠΊΠΈ Π·ΡΠ΅Π½ΠΈΡ ΠΈΠ·ΠΎΠ»ΡΡΠΈΠΈ ΡΠ΅ΠΏΠ»Π°. Π’Π°ΠΊ, 30-ΡΠ°Π½ΡΠΈΠΌΡΠ΅ΡΠΎΠ²Π°Ρ ΡΡΠ΅Π½Π° ΠΈΠ· ΡΠ°ΠΊΠΈΡ Π±Π»ΠΎΠΊΠΎΠ² ΡΠΎΡ ΡΠ°Π½ΡΠ΅Ρ ΡΠ΅ΠΏΠ»ΠΎ ΡΠ°ΠΊΠΆΠ΅ ΠΆΠ΅, ΠΊΠ°ΠΊ ΠΌΠ΅ΡΡΠΎΠ²Π°Ρ ΡΡΠ΅Π½Π° ΠΈΠ· ΠΊΠΈΡΠΏΠΈΡΠ°.
ΠΡΠΎΠΌΠ΅ ΡΠΎΠ³ΠΎ, ΠΈΠ·-Π·Π° ΠΌΠ°Π»ΠΎΠ³ΠΎ Π²Π΅ΡΠ° ΠΌΠ°ΡΠ΅ΡΠΈΠ°Π»Π° ΡΡΡΠ΅ΡΡΠ²Π΅Π½Π½ΠΎ ΡΠ½ΠΈΠΆΠ°Π΅ΡΡΡ Π½Π°Π³ΡΡΠ·ΠΊΠ° Π½Π° ΡΡΠ½Π΄Π°ΠΌΠ΅Π½Ρ. Π‘Π»Π΅Π΄ΠΎΠ²Π°ΡΠ΅Π»ΡΠ½ΠΎ, Π²ΠΎΠ·Π²Π΅Π΄Π΅Π½ΠΈΠ΅ ΡΡΠ½Π΄Π°ΠΌΠ΅Π½ΡΠ° Π΄Π»Ρ Π΄ΠΎΠΌΠ° ΠΈΠ· ΠΎΠΏΠΈΠ»ΠΊΠΎΠ±Π΅ΡΠΎΠ½Π° ΠΏΠΎΠ»ΡΡΠ°Π΅ΡΡΡ ΠΊΡΠ΄Π° ΠΌΠ΅Π½Π΅Π΅ Π·Π°ΡΡΠ°ΡΠ½ΡΠΌ.
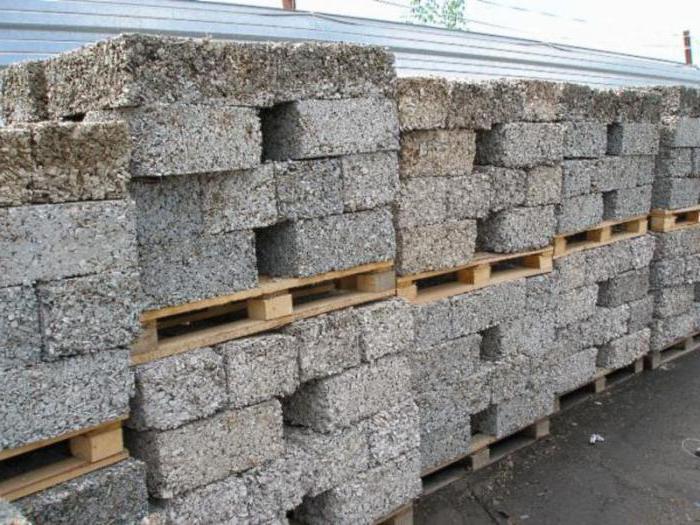
ΠΡΠ΅ ΠΎΠ΄Π½ΠΈΠΌ Π΄ΠΎΡΡΠΎΠΈΠ½ΡΡΠ²ΠΎΠΌ ΠΌΠ°ΡΠ΅ΡΠΈΠ°Π»Π° ΡΠ²Π»ΡΠ΅ΡΡΡ Π΅Π³ΠΎ Π΄ΠΎΠ»Π³ΠΎΠ²Π΅ΡΠ½ΠΎΡΡΡ. ΠΠ°ΠΊ ΠΏΠΎΠΊΠ°Π·ΡΠ²Π°ΡΡ ΠΎΡΠ·ΡΠ²Ρ ΡΡΡΠΎΠΈΡΠ΅Π»Π΅ΠΉ, ΠΎΠΏΠΈΠ»ΠΊΠΎΠ±Π΅ΡΠΎΠ½ ΡΡΠΎΠ΅ΠΊ ΠΊ Π΄Π΅ΡΠΎΡΠΌΠ°ΡΠΈΡΠΌ ΠΈ ΡΠ΄Π°ΡΠ½ΡΠΌ Π½Π°Π³ΡΡΠ·ΠΊΠ°ΠΌ. ΠΠ΅ΡΠΌΠΎΡΡΡ Π½Π° Π½Π°Π»ΠΈΡΠΈΠ΅ Π² ΡΠΎΡΡΠ°Π²Π΅ Π±ΠΎΠ»ΡΡΠΎΠ³ΠΎ ΠΊΠΎΠ»ΠΈΡΠ΅ΡΡΠ²Π° Π΄ΡΠ΅Π²Π΅ΡΠ½ΡΡ ΠΎΠΏΠΈΠ»ΠΎΠΊ, ΠΌΠ°ΡΠ΅ΡΠΈΠ°Π», Π² ΡΠΈΠ»Ρ ΡΠΎΠ΄Π΅ΡΠΆΠ°Π½ΠΈΡ Π² Π½Π΅ΠΌ ΠΏΠ΅ΡΠΊΠ° ΠΈ ΡΠ΅ΠΌΠ΅Π½ΡΠ°, ΡΠ²Π»ΡΠ΅ΡΡΡ Π΄ΠΎΠ²ΠΎΠ»ΡΠ½ΠΎ ΠΎΠ³Π½Π΅ΡΡΠΎΠΉΠΊΠΈΠΌ. ΠΡΠΈ ΡΠ΅ΠΌΠΏΠ΅ΡΠ°ΡΡΡΠ΅ 1200 Β°Π‘ ΠΎΠ½ Π½Π° ΠΏΡΠΎΡΡΠΆΠ΅Π½ΠΈΠΈ Π΄Π²ΡΡ ΡΠ°ΡΠΎΠ² Π½Π΅ Π²ΠΎΡΠΏΠ»Π°ΠΌΠ΅Π½ΡΠ΅ΡΡΡ.
Π ΡΠ°Π±ΠΎΡΠ΅ ΠΎΠΏΠΈΠ»ΠΊΠΎΠ±Π΅ΡΠΎΠ½ Π΄ΠΎΠ²ΠΎΠ»ΡΠ½ΠΎ ΠΏΠΎΠ΄Π°ΡΠ»ΠΈΠ² β Π΅Π³ΠΎ Π±Π΅Π· ΠΏΡΠΎΠ±Π»Π΅ΠΌ ΠΌΠΎΠΆΠ½ΠΎ ΠΏΠΈΠ»ΠΈΡΡ, ΡΠ²Π΅ΡΠ»ΠΈΡΡ ΠΈ ΡΡΠ΅Π·Π΅ΡΠΎΠ²Π°ΡΡ. ΠΠ°ΡΠ΅ΡΠΈΠ°Π» ΡΡΡΠΎΠΉΡΠΈΠ² ΠΊ ΠΌΠΎΡΠΎΠ·Ρ, ΠΏΠ»Π΅ΡΠ΅Π½ΠΈ ΠΈ Π³ΡΠΈΠ±ΠΊΡ, Π° ΡΠ°ΠΊΠΆΠ΅ Π½Π΅ ΠΏΠΎΠ΄Π²Π΅ΡΠΆΠ΅Π½ Π³Π½ΠΈΠ΅Π½ΠΈΡ. Π‘ΠΎ ΡΡΡΠΊΠ°ΡΡΡΠ½ΠΎΠΉ ΠΈ Π±Π΅ΡΠΎΠ½Π½ΡΠΌΠΈ ΡΠΎΡΡΠ°Π²Π°ΠΌΠΈ ΠΎΠ½ ΡΡΠ΅ΠΏΠ»ΡΠ΅ΡΡΡ Ρ ΠΎΡΠΎΡΠΎ, ΡΠΎΠ²Π½ΠΎ, ΠΊΠ°ΠΊ ΠΈ Ρ Π»Π°ΠΊΠΎΠΊΡΠ°ΡΠΎΡΠ½ΡΠΌΠΈ ΠΈ ΠΊΠ»Π΅ΡΡΠΈΠΌΠΈ ΡΡΠ΅Π΄ΡΡΠ²Π°ΠΌΠΈ.
ΠΠΎΠ½Π΅ΡΠ½ΠΎ ΠΆΠ΅, Π±Π΅Π· Π½Π΅Π΄ΠΎΡΡΠ°ΡΠΊΠΎΠ² ΡΠΎΠΆΠ΅ Π½Π΅ Π±ΡΠ²Π°Π΅Ρ. ΠΠ°ΠΊ ΠΏΠΎΠΊΠ°Π·ΡΠ²Π°ΡΡ ΠΎΡΠ·ΡΠ²Ρ ΡΡΡΠΎΠΈΡΠ΅Π»Π΅ΠΉ, ΠΎΠΏΠΈΠ»ΠΊΠΎΠ±Π΅ΡΠΎΠ½ ΠΈΠΌΠ΅Π΅Ρ Π»ΠΈΡΡ ΠΎΠ΄Π½Ρ ΡΠ»Π°Π±ΡΡ ΡΡΠΎΡΠΎΠ½Ρ β Π²ΠΎΠ΄ΠΎΠΏΠΎΠ³Π»ΠΎΡΠ΅Π½ΠΈΠ΅. Π§Π΅ΠΌ Π²ΡΡΠ΅ ΡΡΠΎΡ ΠΏΠΎΠΊΠ°Π·Π°ΡΠ΅Π»Ρ, ΡΠ΅ΠΌ Π½ΠΈΠΆΠ΅ ΠΊΠ°ΡΠ΅ΡΡΠ²ΠΎ ΠΌΠ°ΡΠ΅ΡΠΈΠ°Π»Π°. Π Π·Π°Π²ΠΈΡΠΈΠΌΠΎΡΡΠΈ ΠΎΡ ΠΌΠ°ΡΠΊΠΈ ΠΎΠΏΠΈΠ»ΠΊΠΎΠ±Π΅ΡΠΎΠ½Π° Π΅Π³ΠΎ Π²Π»Π°Π³ΠΎΠΏΠΎΠ³Π»ΠΎΡΠ΅Π½ΠΈΠ΅ ΠΌΠΎΠΆΠ΅Ρ ΡΠΎΡΡΠ°Π²Π»ΡΡΡ ΠΎΡ 8 Π΄ΠΎ 12 %. ΠΠ³ΠΎ ΠΌΠΎΠΆΠ½ΠΎ ΡΠ½ΠΈΠ·ΠΈΡΡ Π½Π° 2-4 % ΠΏΡΡΠ΅ΠΌ ΠΎΠ±ΡΠ°Π±ΠΎΡΠΊΠΈ Π±Π»ΠΎΠΊΠΎΠ² Π²ΠΎΠ΄ΠΎΠΎΡΡΠ°Π»ΠΊΠΈΠ²Π°ΡΡΠΈΠΌΠΈ ΡΠΎΡΡΠ°Π²Π°ΠΌΠΈ.
ΠΠ»Ρ ΡΡΠ°Π²Π½Π΅Π½ΠΈΡ ΠΏΡΠΈΠ²Π΅Π΄Π΅ΠΌ ΠΏΠΎΠΊΠ°Π·Π°ΡΠ΅Π»ΠΈ Π²Π»Π°Π³ΠΎΠΏΠΎΠ³Π»ΠΎΡΠ΅Π½ΠΈΡ Π΄Π»Ρ Π΄ΡΡΠ³ΠΈΡ ΡΠ°ΡΠΏΡΠΎΡΡΡΠ°Π½Π΅Π½Π½ΡΡ ΠΌΠ°ΡΠ΅ΡΠΈΠ°Π»ΠΎΠ²:
- ΠΠ»ΠΈΠ½ΡΠ½ΡΠΉ ΠΊΠΈΡΠΏΠΈΡ β 2-4 %.
- ΠΠ΅ΡΠ°ΠΌΠ·ΠΈΡΠΎΠ±Π΅ΡΠΎΠ½ β 8 %.
- ΠΠ°Π·ΠΎ- ΠΈ ΠΏΠ΅Π½ΠΎΠ±Π΅ΡΠΎΠ½ β 8-10 %.
- ΠΠ΅Π»Π΅Π·ΠΎΠ±Π΅ΡΠΎΠ½ β 3 %.
- ΠΠ°Π·ΠΎ- ΠΈ ΠΏΠ΅Π½ΠΎΡΠΈΠ»ΠΈΠΊΠ°Ρ β 8-10 %.
- ΠΠΎΠ»ΠΈΡΡΠΈΡΠΎΠ»Π±Π΅ΡΠΎΠ½ β 8 %.
Π’Π°ΠΊΠΈΠΌ ΠΎΠ±ΡΠ°Π·ΠΎΠΌ, Π΅ΡΠ»ΠΈ ΠΎΠΏΠΈΠ»ΠΊΠΎΠ±Π΅ΡΠΎΠ½ ΠΈ ΡΡΡΡΠΏΠ°Π΅Ρ ΠΏΠΎ Π²Π»Π°Π³ΠΎΠΏΠΎΠ³Π»ΠΎΡΠ΅Π½ΠΈΡ Π½Π΅ΠΊΠΎΡΠΎΡΡΠΌ ΠΌΠ°ΡΠ΅ΡΠΈΠ°Π»Π°ΠΌ, ΡΠΎ Π½Π΅ ΡΡΠΎΠ»Ρ ΡΡΡΠ΅ΡΡΠ²Π΅Π½Π½ΠΎ, ΡΡΠΎΠ±Ρ ΠΎΡΠΊΠ°Π·ΡΠ²Π°ΡΡΡΡ ΠΎΡ Π΅Π³ΠΎ ΠΏΡΠ΅ΠΈΠΌΡΡΠ΅ΡΡΠ². Π Π΅ΡΠ»ΠΈ ΡΡΠ΅ΡΡΡ, ΡΡΠΎ ΠΏΡΠΈ ΠΈΡΠΏΠΎΠ»ΡΠ·ΠΎΠ²Π°Π½ΠΈΠΈ ΡΠΏΠ΅ΡΠΈΠ°Π»ΡΠ½ΡΡ ΡΠΎΡΡΠ°Π²ΠΎΠ² ΠΌΠΎΠΆΠ½ΠΎ Π΄ΠΎΠ²Π΅ΡΡΠΈ ΡΡΠΎΡ ΠΏΠΎΠΊΠ°Π·Π°ΡΠ΅Π»Ρ Π΄ΠΎ Π²ΠΏΠΎΠ»Π½Π΅ ΠΏΡΠΈΠ΅ΠΌΠ»Π΅ΠΌΡΡ Π·Π½Π°ΡΠ΅Π½ΠΈΠΉ, ΡΠΎ Π΄Π°Π½Π½ΡΠΉ ΠΌΠ°ΡΠ΅ΡΠΈΠ°Π» ΠΈ Π²ΠΎΠ²ΡΠ΅ Π±ΡΠ΄Π΅Ρ Π»ΠΈΠ΄ΠΈΡΠΎΠ²Π°ΡΡ ΠΏΠΎ ΡΡΠ°Π²Π½Π΅Π½ΠΈΡ Ρ Π½Π΅ΠΊΠΎΡΠΎΡΡΠΌΠΈ Π°Π½Π°Π»ΠΎΠ³Π°ΠΌΠΈ.
ΠΡΠ±ΠΎΡ ΠΈ ΠΎΠ±ΡΠ°Π±ΠΎΡΠΊΠ° ΠΎΠΏΠΈΠ»ΠΎΠΊ
ΠΠ»Ρ ΠΈΠ·Π³ΠΎΡΠΎΠ²Π»Π΅Π½ΠΈΡ ΠΊΠ°ΡΠ΅ΡΡΠ²Π΅Π½Π½ΡΡ Π±Π»ΠΎΠΊΠΎΠ² ΡΠ΅ΠΊΠΎΠΌΠ΅Π½Π΄ΡΠ΅ΡΡΡ ΠΈΡΠΏΠΎΠ»ΡΠ·ΠΎΠ²Π°ΡΡ ΠΎΠΏΠΈΠ»ΠΊΠΈ Ρ Π²ΠΎΠΉΠ½ΡΡ ΠΏΠΎΡΠΎΠ΄ Π΄ΡΠ΅Π²Π΅ΡΠΈΠ½Ρ ΡΠ°Π·ΠΌΠ΅ΡΠΎΠΌ Π΄ΠΎ 5 ΠΌΠΌ. ΠΠ»Π°Π³ΠΎΠ΄Π°ΡΡ ΠΎΠ΄Π½ΠΎΡΠΎΠ΄Π½ΠΎΠΌΡ Π³ΡΠ°Π½ΡΠ»ΠΈΡΠΎΠ²Π°Π½Π½ΠΎΠΌΡ ΡΡΡΠΎΠ΅Π½ΠΈΡ ΠΎΠ½ΠΈ ΠΈΠΌΠ΅ΡΡ Ρ ΠΎΡΠΎΡΡΡ ΡΠ΅ΠΊΡΡΠ΅ΡΡΡ, ΠΊΠΎΡΠΎΡΠ°Ρ ΠΊΡΠ°ΠΉΠ½Π΅ Π²Π°ΠΆΠ½Π° Π² ΠΏΡΠΎΡΠ΅ΡΡΠ΅ ΠΏΡΠ΅ΡΡΠΎΠ²Π°Π½ΠΈΡ ΠΎΠΏΠΈΠ»ΠΊΠΎΠ±Π΅ΡΠΎΠ½Π½ΠΎΠΉ ΡΠΌΠ΅ΡΠΈ Π² ΡΠΎΡΠΌΡ. ΠΡΠΎΠΌΠ΅ ΡΠΎΠ³ΠΎ, ΡΡΠΈ ΠΎΠΏΠΈΠ»ΠΊΠΈ ΠΌΠ΅Π½Π΅Π΅ ΠΏΠΎΠ΄Π²Π΅ΡΠΆΠ΅Π½Ρ ΠΏΡΠΎΡΠ΅ΡΡΠ°ΠΌ Π±ΠΈΠΎΠ»ΠΎΠ³ΠΈΡΠ΅ΡΠΊΠΎΠ³ΠΎ ΡΠ°Π·Π»ΠΎΠΆΠ΅Π½ΠΈΡ. Π§Π°ΡΠ΅ Π²ΡΠ΅Π³ΠΎ ΠΏΡΠΈΠΌΠ΅Π½ΡΡΡ Π΅Π»ΠΎΠ²ΡΠ΅ ΠΎΠΏΠΈΠ»ΠΊΠΈ, ΡΠ°ΠΊ ΠΊΠ°ΠΊ ΠΎΠ½ΠΈ ΠΈΠΌΠ΅ΡΡ Π½Π°ΠΈΠ±ΠΎΠ»Π΅Π΅ Π±Π»Π°Π³ΠΎΠΏΡΠΈΡΡΠ½ΡΠ΅ Ρ Π°ΡΠ°ΠΊΡΠ΅ΡΠΈΡΡΠΈΠΊΠΈ, Π²Π°ΠΆΠ½Π΅ΠΉΡΠ΅ΠΉ ΠΈΠ· ΠΊΠΎΡΠΎΡΡΡ ΡΠ²Π»ΡΠ΅ΡΡΡ ΡΠΎΠ΄Π΅ΡΠΆΠ°Π½ΠΈΠ΅ Π²ΠΎΠ΄ΠΎΡΠ°ΡΡΠ²ΠΎΡΠΈΠΌΡΠ΅ Π²Π΅ΡΠ΅ΡΡΠ² β 1,12 %. ΠΠ»Ρ ΡΡΠ°Π²Π½Π΅Π½ΠΈΡ ΠΏΠΎΠ·Π½Π°ΠΊΠΎΠΌΠΈΠΌΡΡ Ρ ΡΠΎΠ΄Π΅ΡΠΆΠ°Π½ΠΈΠ΅ΠΌ Π²ΠΎΠ΄ΠΎΡΠ°ΡΡΠ²ΠΎΡΠΈΠΌΡΡ Π²Π΅ΡΠ΅ΡΡΠ² Π² ΠΎΠΏΠΈΠ»ΠΊΠ°Ρ Π΄ΡΡΠ³ΠΈΡ ΠΏΠΎΡΠΎΠ΄: ΡΠΎΠΏΠΎΠ»ΠΈΠ½ΡΠ΅ β 1,12 %, Π±Π΅ΡΠ΅Π·ΠΎΠ²ΡΠ΅ β 1,3-1,45 %; ΡΠΎΡΠ½ΠΎΠ²ΡΠ΅ β 2,2-6,2 %; Π΄ΡΠ±ΠΎΠ²ΡΠ΅ β 2,5-7,3 %; ΡΡΠ΅Π½Π΅Π²ΡΠ΅ β 2,2-5,8 %; Π»ΠΈΡΡΠ²Π΅Π½Π½ΠΈΡΠ½ΡΠ΅ β ΠΎΡ 10,6 %.
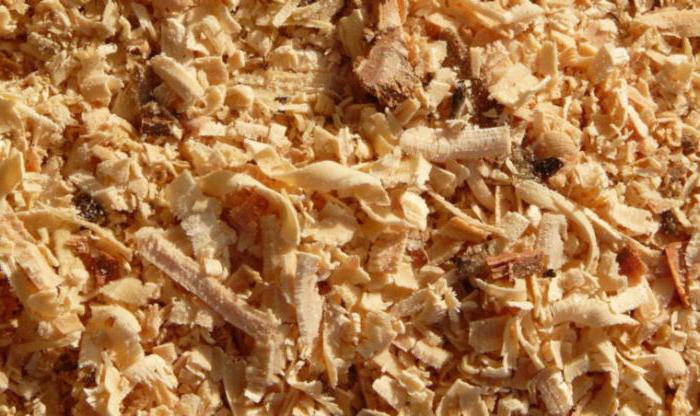
ΠΡΠ΅ΠΌΡ, Π½Π΅ΠΎΠ±Ρ ΠΎΠ΄ΠΈΠΌΠΎΠ΅ Π½Π° ΡΡ Π²Π°ΡΡΠ²Π°Π½ΠΈΠ΅ ΡΠ΅ΠΌΠ΅Π½ΡΠ½ΠΎ-ΠΎΠΏΠΈΠ»ΠΎΡΠ½ΠΎΠΉ ΡΠΌΠ΅ΡΠΈ, ΡΠ°ΠΊΠΆΠ΅ Π·Π°Π²ΠΈΡΠΈΡ ΠΎΡ ΠΏΠΎΡΠΎΠ΄Ρ Π΄Π΅ΡΠ΅Π²Π°. Π’Π°ΠΊ, ΡΠΌΠ΅ΡΡ, ΡΠΎΠ΄Π΅ΡΠΆΠ°ΡΠ°Ρ ΠΎΠΏΠΈΠ»ΠΊΠΈ Π΅Π»ΠΈ, ΠΏΠΎΠ»Π½ΠΎΡΠ΅Π½Π½ΠΎ ΡΡ Π²Π°ΡΡΠ²Π°Π΅ΡΡΡ Π·Π° 10-12 ΡΠ°ΡΠΎΠ². ΠΡΠΈ ΠΈΡΠΏΠΎΠ»ΡΠ·ΠΎΠ²Π°Π½ΠΈΠΈ ΠΎΠΏΠΈΠ»ΠΎΠΊ Π»ΠΈΡΡΠ²Π΅Π½Π½ΠΈΡΠ½ΡΡ ΠΏΠΎΡΠΎΠ΄ ΡΡΠΎΡ ΠΏΠΎΠΊΠ°Π·Π°ΡΠ΅Π»Ρ ΡΠΎΡΡΠ°Π²Π»ΡΠ΅Ρ ΡΠΆΠ΅ 90 ΡΠ°ΡΠΎΠ². Π‘ ΡΠ΅Π»ΡΡ ΡΠΌΠ΅Π½ΡΡΠ΅Π½ΠΈΡ Π²Π»ΠΈΡΠ½ΠΈΡ ΠΎΡΠ³Π°Π½ΠΈΡΠ΅ΡΠΊΠΈΡ Π²ΠΎΠ΄ΠΎΡΠ°ΡΡΠ²ΠΎΡΠΈΠΌΡΡ Π²Π΅ΡΠ΅ΡΡΠ² Π½Π° ΡΠ΅ΠΌΠ΅Π½Ρ, ΠΎΠΏΠΈΠ»ΠΊΠΈ ΠΎΠ±ΡΠ°Π±Π°ΡΡΠ²Π°ΡΡ Ρ ΠΈΠΌΠΈΡΠ΅ΡΠΊΠΈΠΌ ΠΈΠ»ΠΈ ΡΠΈΠ·ΠΈΡΠ΅ΡΠΊΠΈΠΌ ΠΏΡΡΠ΅ΠΌ. Π‘Π°ΠΌΡΠΉ ΠΏΡΠΎΡΡΠΎΠΉ ΡΠΏΠΎΡΠΎΠ± ΠΎΠ±ΡΠ°Π±ΠΎΡΠΊΠΈ β ΠΎΠΊΠΈΡΠ»Π΅Π½ΠΈΠ΅ ΠΎΡΠ³Π°Π½ΠΈΡΠ΅ΡΠΊΠΈΡ ΡΠ»Π΅ΠΌΠ΅Π½ΡΠΎΠ² Π½Π° Π²ΠΎΠ·Π΄ΡΡ Π΅, ΠΆΠ΅Π»Π°ΡΠ΅Π»ΡΠ½ΠΎ ΠΏΠΎΠ΄ ΡΠΎΠ»Π½Π΅ΡΠ½ΡΠΌΠΈ Π»ΡΡΠ°ΠΌΠΈ. ΠΡΠΈ Π½Π°Ρ ΠΎΠΆΠ΄Π΅Π½ΠΈΠΈ ΠΎΠΏΠΈΠ»ΠΎΠΊ Π½Π° ΡΠ΅ΠΏΠ»ΠΎΠΌ Π²ΠΎΠ·Π΄ΡΡ Π΅ ΠΎΠ΄Π½Π° ΡΠ°ΡΡΡ Π²Π΅ΡΠ΅ΡΡΠ² ΠΎΠΊΠΈΡΠ»ΡΠ΅ΡΡΡ ΡΡΠ°Π·Ρ, Π° Π΄ΡΡΠ³Π°Ρ β ΡΠ½Π°ΡΠ°Π»Π° Π±ΡΠΎΠ΄ΠΈΡ, Π·Π°ΡΠ΅ΠΌ ΡΠ°ΡΡΠΈΡΠ½ΠΎ ΠΎΠΊΠΈΡΠ»ΡΠ΅ΡΡΡ, ΠΎΡΡΠ΅ΠΊΠ»ΡΠ΅ΡΡΡ ΠΈΠ»ΠΈ ΠΊΡΠΈΡΡΠ°Π»Π»ΠΈΠ·ΡΠ΅ΡΡΡ, ΠΏΡΠΈΠΎΠ±ΡΠ΅ΡΠ°Ρ Π½Π΅ΡΠ°ΡΡΠ²ΠΎΡΠΈΠΌΡΡ ΡΠΎΡΠΌΡ. ΠΠ΅Π΄ΠΎΡΡΠ°ΡΠΊΠΎΠΌ ΡΡΠΎΠ³ΠΎ ΠΌΠ΅ΡΠΎΠ΄Π° ΠΎΠ±ΡΠ°Π±ΠΎΡΠΊΠΈ ΡΠ²Π»ΡΠ΅ΡΡΡ Π΅Π³ΠΎ Π΄Π»ΠΈΡΠ΅Π»ΡΠ½ΠΎΡΡΡ. Π§ΡΠΎΠ±Ρ Ρ Π²ΠΎΠΉΠ½ΡΠ΅ ΠΎΠΏΠΈΠ»ΠΊΠΈ ΠΎΠΊΠΈΡΠ»ΠΈΡΡ Π½Π° Π²ΠΎΠ·Π΄ΡΡ Π΅, ΠΏΠΎΠ½Π°Π΄ΠΎΠ±ΠΈΡΡΡ 2-3 ΠΌΠ΅ΡΡΡΠ°, Π΄Π»Ρ Π»ΠΈΡΡΠ²Π΅Π½Π½ΡΡ ΡΡΠΎΡ ΠΏΠΎΠΊΠ°Π·Π°ΡΠ΅Π»Ρ Π²ΠΎΠ·ΡΠ°ΡΡΠ°Π΅Ρ Π² Π΄Π²Π° ΡΠ°Π·Π°.
ΠΡΠΎΡΠΎΠΉ ΡΠΏΠΎΡΠΎΠ± ΠΈΠ·Π±Π°Π²Π»Π΅Π½ΠΈΡ ΡΡΡΡΠΆΠΊΠΈ ΠΎΡ Π²ΠΎΠ΄ΠΎΡΠ°ΡΡΠ²ΠΎΡΠΈΠΌΡΡ ΡΠΎΠ΅Π΄ΠΈΠ½Π΅Π½ΠΈΠΉ β ΠΎΠ±ΡΠ°Π±ΠΎΡΠΊΠ° Π²ΠΎΠ΄ΠΎΠΉ. ΠΠ»Ρ ΡΡΠΎΠ³ΠΎ ΠΎΠΏΠΈΠ»ΠΊΠΈ ΠΈΠ»ΠΈ Π²ΡΡΡΠ°Π²Π»ΡΡΡ Π½Π° Π΄Π»ΠΈΡΠ΅Π»ΡΠ½ΠΎΠ΅ Π²ΡΠ΅ΠΌΡ ΠΏΠΎΠ΄ Π΄ΠΎΠΆΠ΄Ρ, ΠΈΠ»ΠΈ Π²ΡΠΌΠ°ΡΠΈΠ²Π°ΡΡ. ΠΠΎ Π²ΡΠ΅ΠΌΠ΅Π½ΠΈ ΡΡΠΎ ΡΠΏΠΎΡΠΎΠ± ΡΠ°ΠΊΠΆΠ΅ ΠΏΡΠΎΠ΄ΠΎΠ»ΠΆΠΈΡΠ΅Π»Π΅Π½, ΡΠ°ΠΊ ΠΊΠ°ΠΊ ΠΌΠ°ΡΠ΅ΡΠΈΠ°Π» Π΄ΠΎΠ»Π³ΠΎ ΡΠΎΡ Π½Π΅Ρ.
Π’ΡΠ΅ΡΠΈΠΉ ΠΈ ΡΠ°ΠΌΡΠΉ ΡΠ°ΡΠΏΡΠΎΡΡΡΠ°Π½Π΅Π½Π½ΡΠΉ ΡΠΏΠΎΡΠΎΠ± β ΠΎΠ±ΡΠ°Π±ΠΎΡΠΊΠ° ΡΠ°ΡΡΠ²ΠΎΡΠΎΠΌ ΠΆΠΈΠ΄ΠΊΠΎΠ³ΠΎ ΡΡΠ΅ΠΊΠ»Π° ΠΈΠ»ΠΈ Ρ Π»ΠΎΡΠΈΡΡΠΎΠ³ΠΎ ΠΊΠ°Π»ΡΡΠΈΡ. ΠΠ΄Π΅ΡΡ Π΅ΡΡΡ Π΄Π²Π° Π½ΡΠ°Π½ΡΠ°. Π‘ ΠΎΠ΄Π½ΠΎΠΉ ΡΡΠΎΡΠΎΠ½Ρ, ΠΏΡΠΈ ΠΎΠ±ΡΠ°Π±ΠΎΡΠΊΠ΅ ΠΆΠΈΠ΄ΠΊΠΈΠΌ ΡΡΠ΅ΠΊΠ»ΠΎΠΌ ΠΌΠ°ΡΠ΅ΡΠΈΠ°Π» ΠΌΠ΅Π½Π΅Π΅ ΠΏΡΠΎΡΠ΅Π½, Π° Ρ Π΄ΡΡΠ³ΠΎΠΉ β Π΄Π»Ρ ΡΡΠΏΠ΅ΡΠ½ΠΎΠΉ ΠΎΠ±ΡΠ°Π±ΠΎΡΠΊΠΈ Ρ Π»ΠΎΡΠΈΡΡΡΠΌ ΠΊΠ°Π»ΡΡΠΈΠ΅ΠΌ ΠΏΠΎΠ½Π°Π΄ΠΎΠ±ΠΈΡΡΡ Ρ ΠΎΡΠΎΡΠΎ Π²ΡΠ΄Π΅ΡΠΆΠ°Π½Π½Π°Ρ Ρ Π²ΠΎΠΉΠ½Π°Ρ Π΄ΡΠ΅Π²Π΅ΡΠΈΠ½Π°.
ΠΡΠ±ΠΎΠ»ΠΈΡ
Π§Π°ΡΡΠΎ ΠΎΠΏΠΈΠ»ΠΊΠΎΠ±Π΅ΡΠΎΠ½ ΠΏΡΡΠ°ΡΡ Ρ Π΄ΡΡΠ³ΠΈΠΌ ΡΡΡΠΎΠΈΡΠ΅Π»ΡΠ½ΡΠΌ ΠΌΠ°ΡΠ΅ΡΠΈΠ°Π»ΠΎΠΌ β Π°ΡΠ±ΠΎΠ»ΠΈΡΠΎΠΌ, ΡΡΠΎ ΡΠΎΠ²Π΅ΡΡΠ΅Π½Π½ΠΎ Π½Π΅Π²Π΅ΡΠ½ΠΎ. Π‘ΠΎΠ³Π»Π°ΡΠ½ΠΎ ΠΠΠ‘Π’Ρ, Π°ΡΠ±ΠΎΠ»ΠΈΡ ΠΎΠΏΡΠ΅Π΄Π΅Π»ΡΠ΅ΡΡΡ ΠΊΠ°ΠΊ Π±Π΅ΡΠΎΠ½ Π½Π° ΡΠ΅ΠΌΠ΅Π½ΡΠ½ΠΎΠΌ Π²ΡΠΆΡΡΠ΅ΠΌ, Ρ ΠΈΠΌΠΈΡΠ΅ΡΠΊΠΈΡ Π΄ΠΎΠ±Π°Π²ΠΊΠ°Ρ ΠΈ ΠΎΡΠ³Π°Π½ΠΈΡΠ΅ΡΠΊΠΈΡ ΡΠ°ΡΡΠ²ΠΎΡΠΈΡΠ΅Π»ΡΡ . ΠΠ΄Π½Π°ΠΊΠΎ Π² ΠΊΠ»Π°ΡΡΠΈΡΠ΅ΡΠΊΠΎΠΌ Π²Π°ΡΠΈΠ°Π½ΡΠ΅ Π°ΡΠ±ΠΎΠ»ΠΈΡΠΎΠ±Π΅ΡΠΎΠ½ ΠΏΡΠ΅Π΄ΠΏΠΎΠ»Π°Π³Π°Π΅Ρ ΠΈΡΠΏΠΎΠ»ΡΠ·ΠΎΠ²Π°Π½ΠΈΠ΅ Π΄ΡΠ΅Π²Π΅ΡΠ½ΠΎΠΉ ΡΠ΅ΠΏΡ. ΠΠΌΠ΅Π½Π½ΠΎ ΠΎΠ½Π° ΠΈ ΠΎΠΏΡΠ΅Π΄Π΅Π»ΡΠ΅Ρ Π΅Π³ΠΎ ΡΠ½ΠΈΠΊΠ°Π»ΡΠ½ΡΠ΅ ΡΠ²ΠΎΠΉΡΡΠ²Π°.
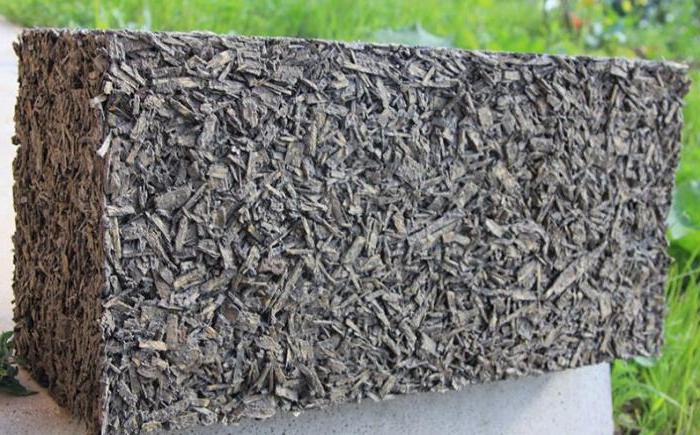
Π ΠΎΠ²Π½ΠΎ, ΠΊΠ°ΠΊ ΠΈ ΠΎΠΏΠΈΠ»ΠΊΠΎΠ±Π΅ΡΠΎΠ½, Π°ΡΠ±ΠΎΠ»ΠΈΡ ΡΠ²Π»ΡΠ΅ΡΡΡ ΡΠΊΠΎΠ»ΠΎΠ³ΠΈΡΠ΅ΡΠΊΠΈ Π±Π»Π°Π³ΠΎΠΏΡΠΈΡΡΠ½ΡΠΌ ΡΡΠ΅Π½ΠΎΠ²ΡΠΌ ΠΌΠ°ΡΠ΅ΡΠΈΠ°Π»ΠΎΠΌ, ΠΎΡΠ»ΠΈΡΠ°ΡΡΠΈΠΌΡΡ Π²ΡΡΠΎΠΊΠΈΠΌΠΈ ΠΏΠΎΠΊΠ°Π·Π°ΡΠ΅Π»ΡΠΌΠΈ ΠΎΠ³Π½Π΅ΡΡΠΎΠΉΠΊΠΎΡΡΠΈ ΠΈ ΡΠ΅ΠΏΠ»ΠΎΠΈΠ·ΠΎΠ»ΡΡΠΈΠΈ. Π’Π΅ΠΌ Π½Π΅ ΠΌΠ΅Π½Π΅Π΅ ΡΡΠΈ Π΄Π²Π° ΠΌΠ°ΡΠ΅ΡΠΈΠ°Π»Π°, Π½Π΅ΡΠΌΠΎΡΡΡ Π½Π° ΡΡ ΠΎΠΆΠ΅ΡΡΡ ΡΡΡΡΠΊΡΡΡΡ, ΠΈΠΌΠ΅ΡΡ ΠΏΡΠΈΠ½ΡΠΈΠΏΠΈΠ°Π»ΡΠ½ΠΎΠ΅ ΠΎΡΠ»ΠΈΡΠΈΠ΅. ΠΠ΅Π»ΠΎ Π² ΡΠΎΠΌ, ΡΡΠΎ Π² ΠΏΡΠΎΠΈΠ·Π²ΠΎΠ΄ΡΡΠ²Π΅ Π°ΡΠ±ΠΎΠ»ΠΈΡΠ° Π²ΠΌΠ΅ΡΡΠΎ ΠΌΠ΅Π»ΠΊΠΈΡ Π΄ΡΠ΅Π²Π΅ΡΠ½ΡΡ ΠΎΠΏΠΈΠ»ΠΎΠΊ, ΠΊΠΎΡΠΎΡΡΠ΅ Π½Π΅ ΠΌΠΎΠ³ΡΡ ΠΎΠ±Π»Π°Π΄Π°ΡΡ Π΄ΠΎΡΡΠ°ΡΠΎΡΠ½ΡΠΌΠΈ ΠΏΡΠΎΡΠ½ΠΎΡΡΠ½ΡΠΌΠΈ ΡΠ²ΠΎΠΉΡΡΠ²Π°ΠΌΠΈ ΡΠ°ΠΌΠΈ ΠΏΠΎ ΡΠ΅Π±Π΅, ΠΈΡΠΏΠΎΠ»ΡΠ·ΡΡΡ ΡΠΏΠ΅ΡΠΈΠ°Π»ΡΠ½ΡΡ Π΄ΡΠ΅Π²Π΅ΡΠ½ΡΡ ΡΠ΅ΠΏΡ, ΡΠ°Π·ΠΌΠ΅Ρ ΠΊΠΎΡΠΎΡΠΎΠΉ ΡΡΡΠΎΠ³ΠΎ Π½ΠΎΡΠΌΠΈΡΡΠ΅ΡΡΡ. ΠΠΏΠΈΠ»ΠΊΠΈ, Π² ΠΎΡΠ»ΠΈΡΠΈΠ΅ ΠΎΡ ΡΠ΅ΠΏΡ, Π½Π΅ ΠΌΠΎΠ³ΡΡ Π² Π΄ΠΎΡΡΠ°ΡΠΎΡΠ½ΠΎΠΉ ΠΌΠ΅ΡΠ΅ Π°ΡΠΌΠΈΡΠΎΠ²Π°ΡΡ (ΡΡΠΈΠ»ΠΈΠ²Π°ΡΡ) ΡΡΠ΅Π½ΠΎΠ²ΠΎΠΉ Π±Π»ΠΎΠΊ ΠΈ Π΄Π°Π²Π°ΡΡ Π΅ΠΌΡ Β«ΠΏΠ»Π°ΡΡΠΈΡΠ½ΠΎΡΡΡΒ». Π’Π°ΠΊΠΈΠΌ ΠΎΠ±ΡΠ°Π·ΠΎΠΌ, Π°ΡΠ±ΠΎΠ»ΠΈΡΠΎΠ±Π΅ΡΠΎΠ½ ΠΏΡΠΎΡΠ½Π΅Π΅ ΠΎΠΏΠΈΠ»ΠΊΠΎΠ±Π΅ΡΠΎΠ½Π° Ρ ΡΠΎΡΠΊΠΈ Π·ΡΠ΅Π½ΠΈΡ ΠΏΡΠΎΡΠ½ΠΎΡΡΠΈ Π½Π° ΠΈΠ·Π³ΠΈΠ± ΠΈ ΡΠΏΠΎΡΠΎΠ±Π½ΠΎΡΡΠΈ ΠΊ Π²ΡΠ΅ΠΌΠ΅Π½Π½ΠΎΠΉ Π΄Π΅ΡΠΎΡΠΌΠ°ΡΠΈΠΈ Π±Π΅Π· ΠΏΠΎΠ»Π½ΠΎΠ³ΠΎ ΡΠ°Π·ΡΡΡΠ΅Π½ΠΈΡ. Π‘ΠΏΡΠ°Π²Π΅Π΄Π»ΠΈΠ²ΠΎΡΡΠΈ ΡΠ°Π΄ΠΈ ΡΡΠΎΠΈΡ ΠΎΡΠΌΠ΅ΡΠΈΡΡ, ΡΡΠΎ ΠΎΠΏΠΈΠ»ΠΊΠΎΠ±Π΅ΡΠΎΠ½ ΠΏΠΎ ΡΡΠΎΠΌΡ ΠΏΠΎΠΊΠ°Π·Π°ΡΠ΅Π»Ρ ΠΏΡΠ΅Π²ΠΎΡΡ ΠΎΠ΄ΠΈΡ ΠΎΡΡΠ°Π»ΡΠ½ΡΠ΅ Π²ΠΈΠ΄Ρ Π»Π΅Π³ΠΊΠΈΡ Π±Π΅ΡΠΎΠ½ΠΎΠ².
ΠΠ»Ρ ΡΠΏΡΠΎΡΠ½Π΅Π½ΠΈΡ Π±Π»ΠΎΠΊΠΎΠ², Π·Π°ΠΏΠΎΠ»Π½Π΅Π½ΠΈΡ ΠΏΡΡΡΠΎΡ ΠΈ ΡΠΌΠ΅Π½ΡΡΠ΅Π½ΠΈΡ ΡΡΠ°Π΄ΠΊΠΈ Π² ΡΠΎΡΡΠ°Π² ΠΎΠΏΠΈΠ»ΠΊΠΎΠ±Π΅ΡΠΎΠ½Π° Π΄ΠΎΠ±Π°Π²Π»ΡΡΡ ΠΌΠ½ΠΎΠ³ΠΎ ΠΏΠ΅ΡΠΊΠ°, Π° Π΄Π»Ρ ΡΠΊΠΎΠ½ΠΎΠΌΠΈΠΈ Π²ΡΠΆΡΡΠ΅Π³ΠΎ ΠΌΠ°ΡΠ΅ΡΠΈΠ°Π»Π° β ΡΠ°ΠΊΠΆΠ΅ Π½Π΅ΠΌΠ°Π»ΠΎ ΠΈΠ·Π²Π΅ΡΡΠΈ ΠΈΠ»ΠΈ Π³Π»ΠΈΠ½Ρ. ΠΡΠΏΠΎΠ»ΡΠ·ΠΎΠ²Π°Π½ΠΈΠ΅ Π±ΠΎΠ»ΡΡΠΎΠ³ΠΎ ΠΊΠΎΠ»ΠΈΡΠ΅ΡΡΠ²Π° ΠΏΠ΅ΡΠΊΠ° Π½Π΅Π³Π°ΡΠΈΠ²Π½ΠΎ ΡΠΊΠ°Π·ΡΠ²Π°Π΅ΡΡΡ Π½Π° ΠΎΠ³Π½Π΅ΡΡΠΎΠΉΠΊΠΎΡΡΠΈ ΡΠ°ΡΡΠΌΠ°ΡΡΠΈΠ²Π°Π΅ΠΌΠΎΠ³ΠΎ Π½Π°ΠΌΠΈ ΠΌΠ°ΡΠ΅ΡΠΈΠ°Π»Π° β ΠΏΡΠΈ ΡΠ΅ΠΌΠΏΠ΅ΡΠ°ΡΡΡΠ΅ +573 Β°Π‘ ΠΎΠΏΠΈΠ»ΠΊΠΎΠ±Π΅ΡΠΎΠ½ ΠΈΠ·ΠΌΠ΅Π½ΡΠ΅ΡΡΡ Π² ΠΎΠ±ΡΠ΅ΠΌΠ΅, ΡΡΠΎ ΠΌΠΎΠΆΠ΅Ρ ΠΏΡΠΈΠ²Π΅ΡΡΠΈ ΠΊ ΡΠ°ΡΡΡΠ΅ΡΠΊΠΈΠ²Π°Π½ΠΈΡ. ΠΡΠΎΠΌΠ΅ ΡΠΎΠ³ΠΎ, ΠΈΠ·-Π·Π° Π²Π΅ΡΠΎΠΌΠΎΠ³ΠΎ ΡΠΎΠ΄Π΅ΡΠΆΠ°Π½ΠΈΡ ΠΏΠ΅ΡΠΊΠ° ΡΠ½ΠΈΠΆΠ°ΡΡΡΡ ΠΊΠΎΠ½ΡΡΡΡΠΊΡΠΈΠΎΠ½Π½ΡΠ΅ Ρ Π°ΡΠ°ΠΊΡΠ΅ΡΠΈΡΡΠΈΠΊΠΈ Π±Π»ΠΎΠΊΠΎΠ². Π’Π°ΠΊ, ΡΡΠΎΠ±Ρ ΠΎΠΏΠΈΠ»ΠΊΠΎΠ±Π΅ΡΠΎΠ½ Π΄ΠΎΡΡΠΈΠ³ ΠΏΡΠΎΡΠ½ΠΎΡΡΠΈ ΠΌΠ°ΡΠΊΠΈ Π25, Π΅Π³ΠΎ ΠΏΠ»ΠΎΡΠ½ΠΎΡΡΡ Π΄ΠΎΠ»ΠΆΠ½Π° ΡΠΎΡΡΠ°Π²Π»ΡΡΡ 950ΠΊΠ³/ΠΌ3. ΠΠ·-Π·Π° Π²ΡΡΠΎΠΊΠΎΠΉ ΠΏΠ»ΠΎΡΠ½ΠΎΡΡΠΈ ΡΡΠΎΠΈΠΌΠΎΡΡΡ ΠΌΠ°ΡΠ΅ΡΠΈΠ°Π»Π° ΠΈ Π΅Π³ΠΎ Π΄ΠΎΡΡΠ°Π²ΠΊΠΈ ΠΏΠΎΠ²ΡΡΠ°Π΅ΡΡΡ, Π° ΠΏΡΠΎΠ²Π΅Π΄Π΅Π½ΠΈΠ΅ ΡΡΡΠΎΠΈΡΠ΅Π»ΡΠ½ΡΡ ΡΠ°Π±ΠΎΡ β ΡΡΠ»ΠΎΠΆΠ½ΡΠ΅ΡΡΡ.
Π£ Π°ΡΠ±ΠΎΠ»ΠΈΡΠ° Π°Π½Π°Π»ΠΎΠ³ΠΈΡΠ½ΠΎΠΉ ΠΌΠ°ΡΠΊΠΈ ΠΏΠ»ΠΎΡΠ½ΠΎΡΡΡ ΡΠΎΡΡΠ°Π²Π»ΡΠ΅Ρ ΠΎΡ 500 Π΄ΠΎ 700 ΠΊΠ³/ΠΌ3. Π£ΡΠΈΡΡΠ²Π°Ρ, ΡΡΠΎ Ρ ΠΏΠΎΠ²ΡΡΠ΅Π½ΠΈΠ΅ΠΌ ΡΠ΄Π΅Π»ΡΠ½ΠΎΠ³ΠΎ Π²Π΅ΡΠ° ΡΠ΅ΠΏΠ»ΠΎΡΠ±Π΅ΡΠ΅Π³Π°ΡΡΠΈΠ΅ ΡΠ²ΠΎΠΉΡΡΠ²Π° ΠΏΠ°Π΄Π°ΡΡ, ΡΠ΅ΠΏΠ»ΠΎΠΏΡΠΎΠ²ΠΎΠ΄Π½ΠΎΡΡΡ ΠΎΠΏΠΈΠ»ΠΊΠΎΠ±Π΅ΡΠΎΠ½Π° ΠΈ Π°ΡΠ±ΠΎΠ»ΠΈΡΠ° ΠΎΡΠ»ΠΈΡΠ°Π΅ΡΡΡ Π±ΠΎΠ»Π΅Π΅ ΡΠ΅ΠΌ Π² Π΄Π²Π° ΡΠ°Π·Π° Π² ΠΏΠΎΠ»ΡΠ·Ρ ΠΏΠΎΡΠ»Π΅Π΄Π½Π΅Π³ΠΎ. Π’Π°ΠΊΠ°Ρ ΡΠ°Π·Π½ΠΈΡΠ° ΠΎΠ±ΡΡΠ»ΠΎΠ²Π»Π΅Π½Π° Π½Π΅Π²ΡΡΠΎΠΊΠΈΠΌ ΠΊΠΎΠ»ΠΈΡΠ΅ΡΡΠ²ΠΎΠΌ Π΄ΡΠ΅Π²Π΅ΡΠΈΠ½Ρ Π² ΠΎΠΏΠΈΠ»ΠΊΠΎΠ±Π΅ΡΠΎΠ½Π΅ ΠΏΠΎ ΡΡΠ°Π²Π½Π΅Π½ΠΈΡ Ρ Π°ΡΠ±ΠΎΠ»ΠΈΡΠΎΠΌ: ΠΏΡΠΈΠΌΠ΅ΡΠ½ΠΎ 50 % ΠΏΡΠΎΡΠΈΠ² 80-90 % ΡΠ΅ΠΏΡ. ΠΡΠΎ Π½Π΅Π³Π°ΡΠΈΠ²Π½ΠΎ ΡΠΊΠ°Π·ΡΠ²Π°Π΅ΡΡΡ Π½Π° ΡΠ°ΠΊΠΎΠΌ ΡΠ²ΠΎΠΉΡΡΠ²Π΅, ΠΊΠ°ΠΊ ΠΎΠ±Π΅ΡΠΏΠ΅ΡΠ΅Π½ΠΈΠ΅ ΠΏΠ°ΡΡΠΈΠ²Π½ΠΎΠΉ Π²Π΅Π½ΡΠΈΠ»ΡΡΠΈΠΈ ΠΏΠΎΠΌΠ΅ΡΠ΅Π½ΠΈΡ. ΠΠ΄Π΅ΡΡ, ΠΎΠΏΡΡΡ ΠΆΠ΅, ΡΡΠΎΠΈΡ ΠΎΡΠΌΠ΅ΡΠΈΡΡ, ΡΡΠΎ ΠΏΠΎ ΡΡΠΎΠΌΡ ΠΏΠ°ΡΠ°ΠΌΠ΅ΡΡΡ ΠΎΠΏΠΈΠ»ΠΊΠΎΠ±Π΅ΡΠΎΠ½ Π·Π½Π°ΡΠΈΡΠ΅Π»ΡΠ½ΠΎ ΠΏΡΠ΅Π²ΠΎΡΡ ΠΎΠ΄ΠΈΡ Π±ΠΎΠ»ΡΡΡΡ ΡΠ°ΡΡΡ ΡΡΠ΅Π½ΠΎΠ²ΡΡ ΠΌΠ°ΡΠ΅ΡΠΈΠ°Π»ΠΎΠ². ΠΠ½ ΠΎΡΠ»ΠΈΡΠ½ΠΎ ΠΏΠΎΠ΄Ρ ΠΎΠ΄ΠΈΡ Π΄Π»Ρ ΡΡΡΠΎΠΈΡΠ΅Π»ΡΡΡΠ²Π° Π·Π΄Π°Π½ΠΈΠΉ ΠΌΠ°Π»ΠΎΠΉ ΡΡΠ°ΠΆΠ½ΠΎΡΡΠΈ ΠΈ ΡΡΡΡΠΏΠ°Π΅Ρ Π»ΠΈΡΡ ΡΠ²ΠΎΠ΅ΠΌΡ «ΡΠΎΠΏΠ΅ΡΠ½ΠΈΠΊΡ».
Π’Π°ΠΊΠΈΠΌ ΠΎΠ±ΡΠ°Π·ΠΎΠΌ, Π½Π°Π·ΡΠ²Π°ΡΡ ΠΎΠΏΠΈΠ»ΠΊΠΎΠ±Π΅ΡΠΎΠ½ Π°ΡΠ±ΠΎΠ»ΠΈΡΠΎΠΌ ΠΊΡΠ°ΠΉΠ½Π΅ Π½Π΅ΠΊΠΎΡΡΠ΅ΠΊΡΠ½ΠΎ, ΡΠ°ΠΊ ΠΊΠ°ΠΊ ΡΡΠΎ ΡΠΎΠ²Π΅ΡΡΠ΅Π½Π½ΠΎ ΡΠ°Π·Π½ΡΠ΅ ΠΌΠ°ΡΠ΅ΡΠΈΠ°Π»Ρ. ΠΠ΄ΠΈΠ½ΡΡΠ²Π΅Π½Π½ΠΎΠ΅ ΡΡ ΠΎΠ΄ΡΡΠ²ΠΎ ΠΌΠ΅ΠΆΠ΄Ρ Π½ΠΈΠΌΠΈ β Π½Π°Π»ΠΈΡΠΈΠ΅ Π΄ΡΠ΅Π²Π΅ΡΠ½ΠΎΠ³ΠΎ ΠΊΠΎΠΌΠΏΠΎΠ½Π΅Π½ΡΠ° Π² ΡΠΎΡΡΠ°Π²Π΅.
ΡΠΎΡΡΠ°Π², ΠΏΡΠΎΠΏΠΎΡΡΠΈΠΈ, ΠΏΡΠΎΠΈΠ·Π²ΠΎΠ΄ΡΡΠ²ΠΎ ΡΠ²ΠΎΠΈΠΌΠΈ ΡΡΠΊΠ°ΠΌΠΈ, ΠΎΡΠ·ΡΠ²Ρ ΠΈ Π²ΠΈΠ΄Π΅ΠΎ
ΠΠΎΠΈΡΠΊ Π±ΠΎΠ»Π΅Π΅ Π½ΠΎΠ²ΡΡ
ΠΌΠ°ΡΠ΅ΡΠΈΠ°Π»ΠΎΠ², ΠΈΠΌΠ΅ΡΡΠΈΡ
Π±ΠΎΠ»ΡΡΠΎΠ΅ ΠΊΠΎΠ»ΠΈΡΠ΅ΡΡΠ²ΠΎ ΠΏΡΠ΅ΠΈΠΌΡΡΠ΅ΡΡΠ² Π²ΠΊΡΠΏΠ΅ Ρ Π΄ΠΎΡΡΡΠΏΠ½ΠΎΡΡΡΡ, ΠΏΡΠΎΠ΄ΠΎΠ»ΠΆΠ°Π΅ΡΡΡ Π΄ΠΎΠ»Π³ΠΎΠ΅ Π²ΡΠ΅ΠΌΡ. Π’Π°ΠΊ, ΠΎΠΏΠΈΠ»ΠΊΠΎΠ±Π΅ΡΠΎΠ½ ΠΌΠΎΠΆΠ½ΠΎ ΡΡΠΈΡΠ°ΡΡ ΠΎΠ΄Π½ΠΈΠΌ ΠΈΠ· Π½ΠΎΠ²Π΅ΠΉΡΠΈΡ
ΡΠΈΠΏΠΎΠ² Π±Π»ΠΎΠΊΠΎΠ², ΠΊΠΎΡΠΎΡΡΠ΅ ΠΈΠΌΠ΅ΡΡ ΠΌΠ½ΠΎΠΆΠ΅ΡΡΠ²ΠΎ ΠΎΡΠΎΠ±Π΅Π½Π½ΠΎΡΡΠ΅ΠΉ. ΠΠΌΠ΅Π½Π½ΠΎ ΠΎ Π½ΠΈΡ
ΡΡΠΎΠΈΡ ΠΏΠΎΠ³ΠΎΠ²ΠΎΡΠΈΡΡ ΠΏΠΎΠ΄ΡΠΎΠ±Π½Π΅Π΅.
ΠΠΏΠΈΡΠ°Π½ΠΈΠ΅ ΠΌΠ°ΡΠ΅ΡΠΈΠ°Π»Π°
ΠΠΏΠΈΠ»ΠΊΠΎΠ±Π΅ΡΠΎΠ½ β ΡΡΠΎ ΠΌΠ°ΡΠ΅ΡΠΈΠ°Π», ΠΊΠΎΡΠΎΡΡΠΉ ΠΌΠΎΠΆΠ½ΠΎ ΠΎΡΠ½Π΅ΡΡΠΈ ΠΊ ΠΊΠ°ΡΠ΅Π³ΠΎΡΠΈΠΈ Π»Π΅Π³ΠΊΠΈΡ . ΠΠ»Ρ Π΅Π³ΠΎ ΡΠΎΠ·Π΄Π°Π½ΠΈΡ ΠΈΡΠΏΠΎΠ»ΡΠ·ΡΡΡΡΡ Π½Π΅ΠΏΠΎΡΡΠ΅Π΄ΡΡΠ²Π΅Π½Π½ΠΎ ΠΎΠΏΠΈΠ»ΠΊΠΈ, ΡΠ΅ΠΌΠ΅Π½Ρ ΠΈ ΠΏΠ΅ΡΠΎΠΊ. Π Π°Π·ΡΠ°Π±ΠΎΡΠ°Π½ ΠΎΠ½ Π±ΡΠ» Π² 60-Ρ Π³ΠΎΠ΄Π°Ρ , Π½ΠΎ ΡΠΈΡΠΎΠΊΠΎ ΠΏΡΠΈΠΌΠ΅Π½ΡΠ΅ΠΌΡΠΌ ΡΡΠ°Π» Π»ΠΈΡΡ Ρ 90-Ρ Π³ΠΎΠ΄ΠΎΠ².
ΠΠ»Π°Π³ΠΎΠ΄Π°ΡΡ Π²ΡΡΠΎΠΊΠΈΠΌ ΡΠ°Π½ΠΈΡΠ°ΡΠ½ΠΎ-Π³ΠΈΠ³ΠΈΠ΅Π½ΠΈΡΠ΅ΡΠΊΠΈΠΌ ΡΠ²ΠΎΠΉΡΡΠ²Π°ΠΌ, Π΅Π³ΠΎ ΠΌΠΎΠΆΠ½ΠΎ ΠΈΡΠΏΠΎΠ»ΡΠ·ΠΎΠ²Π°ΡΡ Π΄Π»Ρ Π²ΠΎΠ·Π²Π΅Π΄Π΅Π½ΠΈΡ Π°Π±ΡΠΎΠ»ΡΡΠ½ΠΎ Π»ΡΠ±ΡΡ Π·Π΄Π°Π½ΠΈΠΉ ΠΈ ΡΡΡΠ΅ΠΆΠ΄Π΅Π½ΠΈΠΉ, Π² ΡΠΎΠΌ ΡΠΈΡΠ»Π΅ ΠΈ ΡΠ΅Ρ , ΠΊΠΎΡΠΎΡΡΠ΅ ΠΏΡΠ΅Π΄Π½Π°Π·Π½Π°ΡΠ°ΡΡΡΡ Π΄Π»Ρ Π΄Π΅ΡΠ΅ΠΉ.
ΠΠ»ΠΎΠΊΠΈ ΠΌΠΎΠΆΠ½ΠΎ ΠΏΠΎΠ΄Π²Π΅ΡΠ³Π°ΡΡ Π°Π±ΡΠΎΠ»ΡΡΠ½ΠΎ Π»ΡΠ±ΠΎΠΉ ΠΌΠ΅Ρ Π°Π½ΠΈΡΠ΅ΡΠΊΠΎΠΉ ΠΎΠ±ΡΠ°Π±ΠΎΡΠΊΠ΅, ΡΠ°ΠΊ ΠΊΠ°ΠΊ ΠΎΠ½ΠΈ ΠΏΡΠ°ΠΊΡΠΈΡΠ΅ΡΠΊΠΈ Π½Π΅ Π΄Π°ΡΡ ΡΡΠ΅ΡΠΈΠ½ ΠΈ ΡΠΊΠΎΠ»ΠΎΠ². ΠΡΠ΅Π½Ρ ΡΠ°ΡΡΠΎ ΠΈΡ ΠΏΡΡΠ°ΡΡ Ρ Π°ΡΠ±ΠΎΠ»ΠΈΡΠΎΠ²ΡΠΌΠΈ Π±Π»ΠΎΠΊΠ°ΠΌΠΈ. ΠΡΠ»ΠΈΡΠ°ΡΡΡΡ ΡΡΠΈ Π΄Π²Π° ΡΡΡΠΎΠΈΡΠ΅Π»ΡΠ½ΡΡ ΠΌΠ°ΡΠ΅ΡΠΈΠ°Π»Π° ΠΏΡΠΈΠΌΠ΅Π½Π΅Π½ΠΈΠ΅ΠΌ Π² Π½ΠΈΡ ΡΠ°Π·Π½ΡΡ Π·Π°ΠΏΠΎΠ»Π½ΠΈΡΠ΅Π»Π΅ΠΉ.
Π§ΡΠΎ ΠΊΠ°ΡΠ°Π΅ΡΡΡ Π°ΡΠ±ΠΎΠ»ΠΈΡΠ°, ΡΠΎ Π΄Π»Ρ Π΅Π³ΠΎ ΠΈΠ·Π³ΠΎΡΠΎΠ²Π»Π΅Π½ΠΈΡ ΠΏΡΠΈΠΌΠ΅Π½ΡΡΡ Π΄ΡΠΎΠ±Π»Π΅Π½Π½ΡΡ ΡΠ΅ΠΏΡ, ΠΊΠΎΡΠΎΡΡΡ ΠΏΠΎΠ»ΡΡΠ°ΡΡ Π·Π° ΡΡΠ΅Ρ ΠΈΠ·ΠΌΠ΅Π»ΡΡΠ΅Π½ΠΈΡ ΠΎΡΡ ΠΎΠ΄ΠΎΠ² Π΄ΡΠ΅Π²Π΅ΡΠΈΠ½Ρ, Π° ΡΠ°ΠΊΠΆΠ΅ Π΄ΡΠΎΠ±Π»Π΅Π½ΠΈΡ ΠΊΠ°ΠΌΡΡΠ° ΠΈ ΡΡΠ΅Π±Π»Π΅ΠΉ Ρ Π»ΠΎΠΏΡΠ°ΡΠ½ΠΈΠΊΠ°, Π° Π΄Π»Ρ ΠΈΠ·Π³ΠΎΡΠΎΠ²Π»Π΅Π½ΠΈΡ ΠΎΠΏΠΈΠ»ΠΊΠΎΠ±Π΅ΡΠΎΠ½Π° ΠΏΡΠΈΠΌΠ΅Π½ΡΡΡΡΡ ΡΠΎΠ»ΡΠΊΠΎ ΠΎΠΏΠΈΠ»ΠΊΠΈ.
Π’Π΅Ρ Π½ΠΈΡΠ΅ΡΠΊΠΈΠ΅ Ρ Π°ΡΠ°ΠΊΡΠ΅ΡΠΈΡΡΠΈΠΊΠΈ
ΠΠ»ΠΎΡΠ½ΠΎΡΡΡ ΠΎΠΏΠΈΠ»ΠΊΠΎΠ±Π΅ΡΠΎΠ½Π½ΡΡ Π±Π»ΠΎΠΊΠΎΠ² ΠΌΠΎΠΆΠ½ΠΎ ΡΠ΅Π³ΡΠ»ΠΈΡΠΎΠ²Π°ΡΡ ΡΠ°ΠΌΠΎΡΡΠΎΡΡΠ΅Π»ΡΠ½ΠΎ, ΡΠ²Π΅Π»ΠΈΡΠΈΠ² Π΄ΠΎΠ»Ρ ΠΎΠΏΠΈΠ»ΠΎΠΊ ΠΈ ΠΏΠ΅ΡΠΊΠ° Π² Π΅Π³ΠΎ ΡΠΎΡΡΠ°Π²Π΅. Π₯Π°ΡΠ°ΠΊΡΠ΅ΡΠΈΡΡΠΈΠΊΠΈ ΠΌΠ°ΡΠ΅ΡΠΈΠ°Π»Π° Π² ΡΡΠ΅ΡΠ΅ ΡΠ΅ΠΏΠ»ΠΎ- ΠΈ Π·Π²ΡΠΊΠΎΠΈΠ·ΠΎΠ»ΡΡΠΈΠΈ Π±ΡΠ΄ΡΡ ΡΠ΅ΠΌ Π²ΡΡΠ΅, ΡΠ΅ΠΌ Π±ΠΎΠ»ΡΡΠ΅ Π±ΡΠ΄Π΅Ρ Π΅Π³ΠΎ ΠΏΠ»ΠΎΡΠ½ΠΎΡΡΡ. ΠΠΎΠ·ΡΠ°ΡΡΠ΅Ρ Π² ΡΠ°ΠΊΠΎΠΌ ΡΠ»ΡΡΠ°Π΅ ΠΈ Π΅Π³ΠΎ ΠΏΡΠΎΡΠ½ΠΎΡΡΡ.
ΠΠΎΠΆΠ½ΠΎ Π²ΡΠ΄Π΅Π»ΠΈΡΡ Π½Π΅ΡΠΊΠΎΠ»ΡΠΊΠΎ Π³ΡΡΠΏΠΏ ΠΎΠΏΠΈΠ»ΠΊΠΎΠ±Π΅ΡΠΎΠ½Π½ΡΡ Π±Π»ΠΎΠΊΠΎΠ², ΠΊΠΎΡΠΎΡΡΠ΅ ΠΏΠΎΠ΄ΡΠ°Π·Π΄Π΅Π»ΡΡΡΡΡ ΠΎΡ Π²ΡΡΠΎΠΊΠΈΡ ΡΠ΅Ρ Π½ΠΈΡΠ΅ΡΠΊΠΈΡ Ρ Π°ΡΠ°ΠΊΡΠ΅ΡΠΈΡΡΠΈΠΊ ΠΊ Π±ΠΎΠ»Π΅Π΅ Π½ΠΈΠ·ΠΊΠΈΠΌ:
- Π5. Π‘Π°ΠΌΡΠΉ ΠΎΠΏΡΠΈΠΌΠ°Π»ΡΠ½ΡΠΉ Π²Π°ΡΠΈΠ°Π½Ρ Π΄Π»Ρ Π²ΠΎΠ·Π²Π΅Π΄Π΅Π½ΠΈΡ ΡΡΠ½Π΄Π°ΠΌΠ΅Π½ΡΠΎΠ² ΠΈ ΡΡΠ΅Π½ ΠΏΠΎΡΡΡΠΎΠ΅ΠΊ, ΡΠ°ΠΊ ΠΊΠ°ΠΊ ΠΎΠ±Π»Π°Π΄Π°Π΅Ρ Π±ΠΎΠ»ΡΡΠ΅ΠΉ ΠΏΠ»ΠΎΡΠ½ΠΎΡΡΡΡ.
- Π10. ΠΠ»ΠΎΠΊΠΈ Ρ ΠΏΠΎΠ΄ΠΎΠ±Π½ΠΎΠΉ ΠΏΡΠΎΡΠ½ΠΎΡΡΡΡ Ρ ΠΎΡΠΎΡΠΈ Π΄Π»Ρ ΡΠ΅ΠΊΠΎΠ½ΡΡΡΡΠΊΡΠΈΠΈ ΡΡΠ΅Π½ ΠΈ ΠΏΠΎΠ΄Π²Π°Π»ΠΎΠ².
- Π15 ΠΈ Π20 ΠΎΠ΄ΠΈΠ½Π°ΠΊΠΎΠ²ΠΎ Ρ ΠΎΡΠΎΡΠΎ ΠΏΠΎΠ΄ΠΎΠΉΠ΄ΡΡ Π΄Π»Ρ Π²ΠΎΠ·Π²Π΅Π΄Π΅Π½ΠΈΡ Π²Π½ΡΡΡΠ΅Π½Π½ΠΈΡ ΡΡΠ΅Π½ ΠΈ ΠΏΠ΅ΡΠ΅Π³ΠΎΡΠΎΠ΄ΠΎΠΊ, Π° ΡΠ°ΠΊ ΠΆΠ΅ Π΄Π»Ρ ΠΎΠ±Π»ΠΈΡΠΎΠ²ΠΊΠΈ.
ΠΡΠ½ΠΎΠ²Π½ΡΠ΅ ΠΏΠΎΠΊΠ°Π·Π°ΡΠ΅Π»ΠΈ Ρ Π°ΡΠ°ΠΊΡΠ΅ΡΠΈΡΡΠΈΠΊ ΠΎΠΏΠΈΠ»ΠΊΠΎΠ±Π΅ΡΠΎΠ½Π½ΡΡ Π±Π»ΠΎΠΊΠΎΠ² ΠΎΡΡΠ°ΠΆΠ΅Π½Ρ Π² ΡΠ°Π±Π»ΠΈΡΠ΅:
Π‘ΡΠ΅Π΄Π½ΡΡ ΠΏΠ»ΠΎΡΠ½ΠΎΡΡΡ, ΠΊΠ³/ΠΌ3 | 500-850 |
ΠΡΠΎΡΠ½ΠΎΡΡΡ ΠΏΡΠΈ ΡΠΆΠ°ΡΠΈΠΈ, ΠΠΠ° | 0,5-3,5 |
Π’Π΅ΠΏΠ»ΠΎΠΏΡΠΎΠ²ΠΎΠ΄Π½ΠΎΡΡΡ, ΠΡ/(ΠΌ2Β·?Π‘) | 0,08-0,17 |
ΠΡΠΎΡΠ½ΠΎΡΡΡ ΠΏΡΠΈ ΠΈΠ·Π³ΠΈΠ±Π΅, ΠΠΠ° | 0,7-1 |
ΠΠΎΠ΄ΡΠ»Ρ ΡΠΏΡΡΠ³ΠΎΡΡΠΈ, ΠΠΠ° | 250-2300 |
ΠΠΎΡΠΎΠ·ΠΎΡΡΠΎΠΉΠΊΠΎΡΡΡ, ΡΠΈΠΊΠ» | 25-50 |
ΠΠΎΠ΄ΠΎΠΏΠΎΠ³Π»ΠΎΡΠ΅Π½ΠΈΠ΅, % | 40-85 |
Π£ΡΠ°Π΄ΠΊΠ°, % | 0,4-0,5 |
ΠΠΈΠΎΡΡΠΎΠΉΠΊΠΎΡΡΡ | V Π³ΡΡΠΏΠΏΠ° |
ΠΠ³Π½Π΅ΡΡΠΎΠΉΠΊΠΎΡΡΡ | 0,75-1,5Ρ |
ΠΠ²ΡΠΊΠΎΠΏΠΎΠ³Π»ΠΎΡΠ΅Π½ΠΈΠ΅, 126-2000ΠΡ | 0,17-0,6 |
Β
ΠΡΠΎΠΈΠ·Π²ΠΎΠ΄ΡΡΠ²ΠΎ ΠΎΠΏΠΈΠ»ΠΊΠΎΠ±Π΅ΡΠΎΠ½Π½ΡΡ Π±Π»ΠΎΠΊΠΎΠ²
ΠΠ·Π³ΠΎΡΠΎΠ²Π»Π΅Π½ΠΈΠ΅ Π΄Π°Π½Π½ΡΡ Π±Π»ΠΎΠΊΠΎΠ² Π½Π΅ ΡΠ²Π»ΡΠ΅ΡΡΡ ΠΎΡΠ΅Π½Ρ ΡΠ»ΠΎΠΆΠ½ΡΠΌ ΠΏΡΠΎΡΠ΅ΡΡΠΎΠΌ, ΠΈΠΌΠ΅Π½Π½ΠΎ ΠΏΠΎΡΡΠΎΠΌΡ ΠΈ Π²ΠΎΠ·ΠΌΠΎΠΆΠ½ΠΎ ΠΎΡΡΡΠ΅ΡΡΠ²ΠΈΡΡ ΡΡΠΎ ΡΠ²ΠΎΠΈΠΌΠΈ ΡΡΠΊΠ°ΠΌΠΈ. ΠΠ»Π°Π²Π½ΠΎΠ΅, ΡΡΡΠΎΠ³ΠΎ ΡΠ»Π΅Π΄ΠΎΠ²Π°ΡΡ ΡΠ΅Ρ Π½ΠΎΠ»ΠΎΠ³ΠΈΡΠ΅ΡΠΊΠΎΠΌΡ ΠΏΡΠΎΡΠ΅ΡΡΡ ΠΈ Π½Π΅ Π½Π°ΡΡΡΠ°ΡΡ Π΅Π³ΠΎ.
ΠΠΎΠ΄Π³ΠΎΡΠΎΠ²ΠΊΠ° ΡΠΌΠ΅ΡΠΈ
Π‘ΠΎΠ·Π΄Π°Π½ΠΈΠ΅ ΠΎΠΏΠΈΠ»ΠΊΠΎΠ±Π΅ΡΠΎΠ½Π½ΡΡ Π±Π»ΠΎΠΊΠΎΠ² ΠΎΠΏΡΠ°Π²Π΄Π°Π½ΠΎ, Π΅ΡΠ»ΠΈ Π½Π΅ΠΏΠΎΠ΄Π°Π»Π΅ΠΊΡ ΠΎΡ ΠΏΡΠΎΠΈΠ·Π²ΠΎΠ΄ΡΡΠ²Π° Π½Π°Ρ ΠΎΠ΄ΠΈΡΡΡ Π»Π΅ΡΠΎΠΏΠΈΠ»ΠΊΠ°. Π ΡΠ°ΠΊΠΎΠΌ ΡΠ»ΡΡΠ°Π΅ ΠΏΡΠΎΠΈΠ·Π²ΠΎΠ΄ΡΡΠ²ΠΎ ΠΈΡ ΡΠ²ΠΎΠΈΠΌΠΈ ΡΡΠΊΠ°ΠΌΠΈ ΡΡΠ°Π½Π΅Ρ Π½Π°ΠΈΠ±ΠΎΠ»Π΅Π΅ Π²ΡΠ³ΠΎΠ΄Π½ΡΠΌ, ΠΏΠΎΡΠΊΠΎΠ»ΡΠΊΡ ΠΌΠ½ΠΎΠ³ΠΎ Π·Π°ΡΡΠ°Ρ Π΄Π»Ρ ΡΡΠΎΠ³ΠΎ Π½Π΅ ΠΏΠΎΡΡΠ΅Π±ΡΠ΅ΡΡΡ.
ΠΠ»Ρ ΠΏΡΠΈΠ³ΠΎΡΠΎΠ²Π»Π΅Π½ΠΈΡ ΠΌΠ°ΡΠ΅ΡΠΈΠ°Π»Π°, ΠΊΠΎΡΠΎΡΡΠΉ Π½Π΅ΠΎΠ±Ρ ΠΎΠ΄ΠΈΠΌ Π΄Π»Ρ ΡΠ°Π·Π½ΡΡ ΡΠ΅Π»Π΅ΠΉ, ΠΏΠΎΠ½Π°Π΄ΠΎΠ±ΠΈΡΡΡ Π²Π·ΡΡΡ ΠΊΠΎΠΌΠΏΠΎΠ½Π΅Π½ΡΡ Π² ΡΠ»Π΅Π΄ΡΡΡΠΈΡ ΠΏΡΠΎΠΏΠΎΡΡΠΈΡΡ :
- ΠΠ»Ρ ΠΏΠΎΠ»ΡΡΠ΅Π½ΠΈΡ Π²ΡΡΠΎΠΊΠΎΠΉ ΠΏΠ»ΠΎΡΠ½ΠΎΡΡΠΈ: ΠΏΠΎ 200 ΠΊΠ³ ΡΠ΅ΠΌΠ΅Π½ΡΠ° ΠΈ ΠΎΠΏΠΈΠ»ΠΎΠΊ, 50 ΠΊΠ³ ΠΈΠ·Π²Π΅ΡΡΠΈ, 500 ΠΊΠ³ ΠΏΠ΅ΡΠΊΠ°.
- ΠΠ»Ρ ΠΏΠΎΠ»ΡΡΠ΅Π½ΠΈΡ ΡΡΠ΅Π΄Π½Π΅ΠΉ ΠΏΠ»ΠΎΡΠ½ΠΎΡΡΠΈ Π½Π° 200 ΠΊΠ³ ΠΎΠΏΠΈΠ»ΠΎΠΊ ΠΏΠΎΠ½Π°Π΄ΠΎΠ±ΠΈΡΡΡ ΡΠΆΠ΅ 150 ΠΊΠ³ ΡΠ΅ΠΌΠ΅Π½ΡΠ°, 100 ΠΊΠ³ ΠΈΠ·Π²Π΅ΡΡΠΈ ΠΈ 350 ΠΊΠ³ ΠΏΠ΅ΡΠΊΠ°.
- ΠΠΈΠ·ΠΊΠ°Ρ ΠΏΠ»ΠΎΡΠ½ΠΎΡΡΡ ΠΏΡΠ΅Π΄ΠΏΠΎΠ»Π°Π³Π°Π΅Ρ ΡΠ½ΠΈΠΆΠ΅Π½ΠΈΠ΅ ΠΊΠΎΠ»ΠΈΡΠ΅ΡΡΠ²Π° Π΄ΠΎΠΏΠΎΠ»Π½ΠΈΡΠ΅Π»ΡΠ½ΡΡ ΠΌΠ°ΡΠ΅ΡΠΈΠ°Π»ΠΎΠ² Π½Π° 200 ΠΊΠ³ ΠΎΠΏΠΈΠ»ΠΎΠΊ Π² Π½Π΅ΡΠΊΠΎΠ»ΡΠΊΠΎ ΡΠ°Π·. Π’Π°ΠΊ, Π½ΡΠΆΠ½ΠΎ Π²ΡΠ΅Π³ΠΎ Π»ΠΈΡΡ ΠΏΠΎ 50 ΠΊΠ³ ΠΏΠ΅ΡΠΊΠ° ΠΈ ΡΠ΅ΠΌΠ΅Π½ΡΠ°, Π° ΠΈΠ·Π²Π΅ΡΡΠΈ β 200 ΠΊΠ³.
ΠΡΡΠ°ΡΠΈ, ΠΈΠ·Π²Π΅ΡΡΡ Π²ΠΎΠ·ΠΌΠΎΠΆΠ½ΠΎ Π·Π°ΠΌΠ΅Π½ΠΈΡΡ Π³Π»ΠΈΠ½ΠΎΠΉ. Π Π΄Π°Π½Π½ΠΎΠΌ ΡΠ»ΡΡΠ°Π΅ Π½Π° ΠΊΠ°ΡΠ΅ΡΡΠ²Π΅ ΠΎΠΏΠΈΠ»ΠΊΠΎΠ±Π΅ΡΠΎΠ½Π° ΡΡΠΎ Π½Π΅ ΡΠΏΠΎΡΠΎΠ±Π½ΠΎ ΡΠΈΠ»ΡΠ½ΠΎ ΡΠΊΠ°Π·Π°ΡΡΡΡ.
ΠΡΠ»ΠΈ ΡΠΊΡΠΏΠ»ΡΠ°ΡΠ°ΡΠΈΡ Π±Π»ΠΎΠΊΠΎΠ² ΠΏΡΠ΅Π΄ΠΏΠΎΠ»Π°Π³Π°Π΅ΡΡΡ Π² ΠΌΠ΅ΡΡΠ½ΠΎΡΡΠΈ Ρ Π±ΠΎΠ»ΡΡΠΎΠΉ Π²Π»Π°ΠΆΠ½ΠΎΡΡΡΡ ΠΈΠ»ΠΈ ΠΆΠ΅ ΠΎΠΏΠΈΠ»ΠΊΠΈ Π»Π΅ΠΆΠ°Π»ΡΠ΅, ΡΠΎ Π·Π°ΠΏΠΎΠ»Π½ΠΈΡΠ΅Π»Ρ ΠΏΠΎΡΡΠ΅Π±ΡΠ΅Ρ Π΄ΠΎΠΏΠΎΠ»Π½ΠΈΡΠ΅Π»ΡΠ½ΠΎΠΉ ΠΎΠ±ΡΠ°Π±ΠΎΡΠΊΠΈ ΠΌΠΈΠ½Π΅ΡΠ°Π»ΠΈΠ·Π°ΡΠΎΡΠ°ΠΌΠΈ. ΠΡΠΎ ΠΏΠΎΠΌΠΎΠΆΠ΅Ρ ΡΠ²Π΅Π»ΠΈΡΠΈΡΡ ΠΎΠ³Π½Π΅ΡΡΠΎΠΉΠΊΠΎΡΡΡ ΠΈ ΡΠ½ΠΈΠ·ΠΈΡ Π²ΠΎΠ·ΠΌΠΎΠΆΠ½ΠΎΡΡΡ ΠΏΠΎΠ³Π»ΠΎΡΠ΅Π½ΠΈΡ Π²ΠΎΠ΄Ρ. ΠΡΠ»ΠΈΡΠ½ΡΠΉ ΡΠΏΠΎΡΠΎΠ± ΠΎΠ±ΡΠ°Π±ΠΎΡΠΊΠΈ β ΡΡΠΎ Π²ΡΠΌΠ°ΡΠΈΠ²Π°Π½ΠΈΠ΅ ΠΈΡ Π² ΠΆΠΈΠ΄ΠΊΠΎΠΌ ΡΡΠ΅ΠΊΠ»Π΅. ΠΡΠ΅Π΄Π²Π°ΡΠΈΡΠ΅Π»ΡΠ½ΠΎ Π½ΡΠΆΠ½ΠΎ Π²ΡΠΌΠΎΡΠΈΡΡ ΠΈΡ Π² ΠΈΠ·Π²Π΅ΡΡΠΊΠΎΠ²ΠΎΠΌ ΠΌΠΎΠ»ΠΎΠΊΠ΅.
Π‘ΠΌΠ΅ΡΡ Π΄ΠΎΠ»ΠΆΠ½Π° Π±ΡΡΡ ΡΡΡ Π°Ρ, ΠΊΠΎΠ³Π΄Π° Π±ΡΠ΄ΡΡ ΠΏΠ΅ΡΠ΅ΠΌΠ΅ΡΠΈΠ²Π°ΡΡΡΡ ΠΎΠΏΠΈΠ»ΠΊΠΈ, ΠΏΠ΅ΡΠΎΠΊ ΠΈ Π±Π΅ΡΠΎΠ½. ΠΠΎΠ΄Π° Π΄ΠΎΠ±Π°Π²Π»ΡΠ΅ΡΡΡ ΡΠΆΠ΅ ΠΏΠΎΡΠ»Π΅, ΠΏΡΠΈ ΠΏΠΎΠΌΠΎΡΠΈ ΡΠ°ΡΠΏΡΡΡΠΊΠΈΠ²Π°ΡΠ΅Π»Ρ.
Π’Π°ΠΊ ΠΊΠ°ΠΊ Π²ΡΡΡΠ½ΡΡ ΠΊΠΎΠΌΠΏΠΎΠ½Π΅Π½ΡΡ ΠΎΡΠ΅Π½Ρ ΡΡΠΆΠ΅Π»ΠΎ ΠΏΠ΅ΡΠ΅ΠΌΠ΅ΡΠΈΠ²Π°ΡΡ, ΠΎΡΠΎΠ±Π΅Π½Π½ΠΎ Π² Π±ΠΎΠ»ΡΡΠΈΡ ΠΊΠΎΠ»ΠΈΡΠ΅ΡΡΠ²Π°Ρ , ΡΠ΅ΠΊΠΎΠΌΠ΅Π½Π΄ΡΠ΅ΡΡΡ ΠΏΠΎΠ·Π°ΠΈΠΌΡΡΠ²ΠΎΠ²Π°ΡΡ ΡΠ°ΡΡΠ²ΠΎΡΠΎΡΠΌΠ΅ΡΠΈΡΠ΅Π»Ρ ΠΈΠ»ΠΈ ΠΆΠ΅ Π±Π΅ΡΠΎΠ½ΠΎΠΌΠ΅ΡΠ°Π»ΠΊΡ.
ΠΡΠΎΠ²Π΅ΡΠΈΡΡ Π³ΠΎΡΠΎΠ²Π½ΠΎΡΡΡ ΡΠ°ΡΡΠ²ΠΎΡΠ° ΠΌΠΎΠΆΠ½ΠΎ, ΡΠΆΠ°Π² Π΅Π΅ Π² ΠΊΡΠ»Π°ΠΊΠ΅. ΠΡΠ»ΠΈ ΠΊΠΎΠΌΠΎΠΊ ΠΏΠ»Π°ΡΡΠΈΡΠ΅Π½ ΠΈ Π½Π° Π½Π΅ΠΌ Ρ
ΠΎΡΠΎΡΠΎ Π²ΠΈΠ΄Π½Ρ ΠΎΡΠΏΠ΅ΡΠ°ΡΠΊΠΈ, Π·Π½Π°ΡΠΈΡ, ΠΌΠ°ΡΠ΅ΡΠΈΠ°Π» Π³ΠΎΡΠΎΠ².
ΠΠΎΠ΄Π³ΠΎΡΠΎΠ²ΠΊΠ° ΡΠΎΡΠΌ ΠΈ ΠΎΠ±ΠΎΡΡΠ΄ΠΎΠ²Π°Π½ΠΈΡ
ΠΠ·Π½Π°ΡΠ°Π»ΡΠ½ΠΎ Π½Π΅ΠΎΠ±Ρ ΠΎΠ΄ΠΈΠΌΠΎ ΠΈΠ·Π³ΠΎΡΠΎΠ²ΠΈΡΡ ΡΠΈΡΠΊΠΈ ΡΠΏΠ΅ΡΠΈΠ°Π»ΡΠ½ΠΎ Π΄Π»Ρ ΠΎΠΏΠ°Π»ΡΠ±ΠΊΠΈ. ΠΠ½ΠΈ Π΄ΠΎΠ»ΠΆΠ½Ρ Π±ΡΡΡ ΡΠ΅ΡΠΊΠΎ Π²ΡΠΌΠ΅ΡΠ΅Π½Ρ, ΡΡΠΎΠ±Ρ ΠΏΠΎΠ»ΡΡΠΈΡΡ ΡΠ°Π²Π½ΡΠ΅ ΠΏΠΎ ΡΠ°Π·ΠΌΠ΅ΡΡ Π±Π»ΠΎΠΊΠΈ. ΠΠΎΡΠΊΠΈ Π΄Π»Ρ ΡΠΈΡΠΊΠ° Π΄ΠΎΠ»ΠΆΠ½Ρ ΠΈΠΌΠ΅ΡΡ ΡΠΎΠ»ΡΠΈΠ½Ρ Π² 38 ΠΌΠΌ. ΠΠΎΡΠ»Π΅ ΡΠ»Π΅Π΄ΡΠ΅Ρ ΠΏΡΠΈΡΡΡΠΏΠΈΡΡ ΠΊ ΠΏΡΠΎΡΠ΅ΠΈΠ²Π°Π½ΠΈΡ ΠΎΠΏΠΈΠ»ΠΎΠΊ. ΠΠ°ΠΊ ΡΠΎΠ»ΡΠΊΠΎ ΡΠ΅ΠΏΠ° ΠΈ ΠΊΠΎΡΠ° Π±ΡΠ΄ΡΡ ΠΎΡΠ΄Π΅Π»Π΅Π½Ρ, ΠΏΠΎΡΡΠ΅Π±ΡΠ΅ΡΡΡ Π΄ΠΎΠ±Π°Π²ΠΈΡΡ ΠΊ Π½ΠΈΠΌ Π΄ΡΠ΅Π²Π΅ΡΠ½ΡΡ ΡΡΡΡΠΆΠΊΡ. ΠΡΠΎ ΠΏΠΎΠ·Π²ΠΎΠ»ΠΈΡ ΡΠ²Π΅Π»ΠΈΡΠΈΡΡ ΠΏΡΠΎΡΠ½ΠΎΡΡΡ ΠΌΠ°ΡΠ΅ΡΠΈΠ°Π»Π° Π² Π½Π΅ΡΠΊΠΎΠ»ΡΠΊΠΎ ΡΠ°Π·.
Π£ΠΊΠ»Π°Π΄ΠΊΡ ΠΌΠΎΠΆΠ½ΠΎ ΠΏΡΠΎΠΈΠ·Π²ΠΎΠ΄ΠΈΡΡ Π² Π΄Π²Π΅ Π³ΡΡΠΏΠΏΡ ΡΠΎΡΠΌ:
- ΠΠ°Π±Π°ΡΠΈΡΠ½ΡΠ΅ Π±Π»ΠΎΠΊΠΈ. ΠΠ»Ρ Π½ΠΈΡ ΠΏΠΎΡΡΠ΅Π±ΡΠ΅ΡΡΡ ΠΎΠ±ΡΡΠ½ΠΎ Π² Π²ΠΈΠ΄Π΅ ΡΡΠΈΠΊΠΎΠ² ΠΈΠ· Π΄ΠΎΡΠΎΠΊ. ΠΠ½ΠΈ ΠΎΠ±ΡΡΠ½ΠΎ ΡΠ°Π·Π±ΠΎΡΠ½ΡΠ΅, ΡΠ°ΠΊ ΠΊΠ°ΠΊ ΡΡΠΎ ΠΏΠΎΠ·Π²ΠΎΠ»ΡΠ΅Ρ Π±ΡΡΡΡΠΎ ΡΠ°Π·Π±ΠΈΡΠ°ΡΡ ΠΈ ΡΠΎΠ±ΠΈΡΠ°ΡΡ Π²Π½ΠΎΠ²Ρ.
- ΠΠ΅Π±ΠΎΠ»ΡΡΠΈΠ΅ Π±Π»ΠΎΠΊΠΈ. ΠΡΠ΅Π΄ΡΡΠ°Π²Π»ΡΡΡ ΡΠΎΠ±ΠΎΠΉ Π½Π΅Π±ΠΎΠ»ΡΡΠΈΠ΅ ΠΏΠΎ ΡΠ°Π·ΠΌΠ΅ΡΡ ΡΠΎΡΠΌΡ, Π±Π»Π°Π³ΠΎΠ΄Π°ΡΡ ΠΊΠΎΡΠΎΡΡΠΌ ΠΎΠ±ΡΡΠ½ΠΎ ΠΌΠΎΠ³ΡΡ ΠΈΠ·Π³ΠΎΡΠ°Π²Π»ΠΈΠ²Π°ΡΡΡΡ Π΄ΠΎ 9 Π±Π»ΠΎΠΊΠΎΠ² ΠΎΠ΄Π½ΠΎΠ²ΡΠ΅ΠΌΠ΅Π½Π½ΠΎ.
Π ΡΠΊΠ»Π°Π΄ΠΊΠ΅ ΡΠ»Π΅Π΄ΡΠ΅Ρ ΠΏΡΠΈΡΡΡΠΏΠ°ΡΡ Π½Π΅ΠΌΠ΅Π΄Π»Π΅Π½Π½ΠΎ, ΡΠ°ΠΊ ΠΊΠ°ΠΊ ΡΠΆΠ΅ ΠΏΠΎΡΠ»Π΅ Π΄Π²ΡΡ ΡΠ°ΡΠΎΠ² ΠΎΠ½Π° Π½Π°ΡΠ½Π΅Ρ Π±ΡΡΡΡΠΎ ΡΠ²Π΅ΡΠ΄Π΅ΡΡ. ΠΡΠ΅Π΄Π²Π°ΡΠΈΡΠ΅Π»ΡΠ½ΠΎ Π΄ΠΎΡΠΊΠΈ ΠΎΠΏΠ°Π»ΡΠ±ΠΊΠΈ Π²Π½ΡΡΡΠΈ ΡΠ²Π»Π°ΠΆΠ½ΡΡΡΡΡ Π²ΠΎΠ΄ΠΎΠΉ. Π£ΠΊΠ»Π°Π΄ΠΊΠ° Π΄ΠΎΠ»ΠΆΠ½Π° ΠΏΡΠΎΠΈΠ·Π²ΠΎΠ΄ΠΈΡΡΡΡ ΡΠ»ΠΎΡΠΌΠΈ ΡΠ°ΡΡΠ²ΠΎΡΠ° Π² 150 ΠΌΠΌ, ΠΏΡΠΈ ΡΡΠΎΠΌ ΠΊΠ°ΠΆΠ΄ΡΡ Π΅Π³ΠΎ ΡΠ°ΡΡΡ Π½ΡΠΆΠ½ΠΎ Ρ ΠΎΡΠΎΡΠΎ ΡΡΡΠ°ΠΌΠ±ΠΎΠ²ΡΠ²Π°ΡΡ, Π΄Π°Π±Ρ ΠΈΠ·Π±Π΅ΠΆΠ°ΡΡ ΠΎΠ±ΡΠ°Π·ΠΎΠ²Π°Π½ΠΈΡ ΠΏΡΡΡΠΎΡ.
ΠΠΏΠ°Π»ΡΠ±ΠΊΡ ΡΠ΅Π»Π΅ΡΠΎΠΎΠ±ΡΠ°Π·Π½ΠΎ ΡΠ½ΠΈΠΌΠ°ΡΡ ΠΏΠΎ ΠΏΡΠΎΡΠ΅ΡΡΠ²ΠΈΠΈ ΡΠ΅ΡΡΡΠ΅Ρ Π΄Π½Π΅ΠΉ, ΠΊΠΎΠ³Π΄Π° ΡΠ°ΡΡΠ²ΠΎΡ ΠΏΠΎΠ»Π½ΠΎΡΡΡΡ Π·Π°ΡΡΡΠ½Π΅Ρ. Π‘Π°ΠΌΠΈ Π±Π»ΠΎΠΊΠΈ Π½ΡΠΆΠ½ΠΎ ΠΎΡΡΠ°Π²ΠΈΡΡ Π΅ΡΠ΅ Π½Π° ΡΡΠΎΠΌ ΠΌΠ΅ΡΡΠ΅ Π½Π° 4 Π΄Π½Ρ, ΡΠ°ΠΊ ΠΊΠ°ΠΊ Π² ΠΏΠΎΠ΄ΠΎΠ±Π½ΠΎΠΌ ΡΠ»ΡΡΠ°Π΅ ΠΏΡΠΎΡΠ½ΠΎΡΡΡ ΠΏΠΎΠ²ΡΡΠ°Π΅ΡΡΡ Π² Π½Π΅ΡΠΊΠΎΠ»ΡΠΊΠΎ ΡΠ°Π·.
Π‘ΡΡΠΊΡ Π±Π»ΠΎΠΊΠΎΠ² Π»ΡΡΡΠ΅ ΠΏΡΠΎΠ²ΠΎΠ΄ΠΈΡΡ Π½Π° ΡΠΊΠ²ΠΎΠ·Π½ΡΠΊΠ΅, ΠΏΠΎΡΠΊΠΎΠ»ΡΠΊΡ ΡΠΎΠ³Π΄Π° ΠΎΠ½Π° Π±ΡΠ΄Π΅Ρ ΠΏΡΠΎΠΈΠ·Π²ΠΎΠ΄ΠΈΡΡΡΡ ΡΠ°Π²Π½ΠΎΠΌΠ΅ΡΠ½ΠΎ. ΠΡΠΈ ΡΡΠΎΠΌ Π²Π°ΠΆΠ½ΠΎ ΠΎΡΡΠ°Π²ΠΈΡΡ ΠΌΠ΅ΠΆΠ΄Ρ Π½ΠΈΠΌΠΈ Π·Π°Π·ΠΎΡΡ. ΠΠ° ΡΠ»ΡΡΠ°ΠΉ Π΄ΠΎΠΆΠ΄Ρ Π»ΡΡΡΠ΅ Π·Π°ΠΊΡΡΡΡ ΠΈΡ ΠΏΠΎΠ»ΠΈΡΡΠΈΠ»Π΅Π½ΠΎΠ²ΠΎΠΉ ΠΏΠ»Π΅Π½ΠΊΠΎΠΉ, Π΄Π°Π±Ρ ΠΏΡΠ΅Π΄ΠΎΡΠ²ΡΠ°ΡΠΈΡΡ Π½Π°ΠΌΠΎΠΊΠ°Π½ΠΈΠ΅ Π±Π»ΠΎΠΊΠΎΠ².
ΠΠΊΠΎΠ½ΡΠ°ΡΠ΅Π»ΡΠ½Π°Ρ ΡΡΡΠΊΠ° ΠΎΡΡΡΠ΅ΡΡΠ²Π»ΡΠ΅ΡΡΡ ΠΏΡΠΈ ΠΏΠΎΠΌΠΎΡΠΈ ΡΡΠΎΠ»Π±ΠΎΠ². ΠΠ»ΠΎΠΊΠΈ Π½Π΅ΠΎΠ±Ρ ΠΎΠ΄ΠΈΠΌΠΎ Π΄Π»Ρ ΡΡΠΎΠ³ΠΎ ΡΠ»ΠΎΠΆΠΈΡΡ Π½Π° ΠΊΠΈΡΠΏΠΈΡΠΈ, Π²ΠΎΠ·Π²ΠΎΠ΄Ρ Π½Π΅Π²ΡΡΠΎΠΊΠΈΠ΅ ΡΡΠΎΠ»Π±Ρ ΠΈΠ· ΠΎΠΏΠΈΠ»ΠΊΠΎΠ±Π΅ΡΠΎΠ½Π½ΡΡ Π±Π»ΠΎΠΊΠΎΠ² ΠΈ ΠΎΠ±ΡΠ·Π°ΡΠ΅Π»ΡΠ½ΠΎ ΠΎΡΡΠ°Π²Π»ΡΡ Π·Π°Π·ΠΎΡΡ ΠΌΠ΅ΠΆΠ΄Ρ Π½ΠΈΠΌΠΈ. Π’Π°ΠΊΠΈΠΌ ΠΎΠ±ΡΠ°Π·ΠΎΠΌ 90% ΠΏΡΠΎΡΠ½ΠΎΡΡΠΈ ΠΌΠΎΠΆΠ½ΠΎ Π΄ΠΎΡΡΠΈΠ³Π½ΡΡΡ ΡΠΆΠ΅ ΠΏΠΎΡΠ»Π΅ ΠΌΠ΅ΡΡΡΠ° ΡΡΡΠΊΠΈ.
ΠΠ° Π²ΠΈΠ΄Π΅ΠΎ β ΡΠ΅Ρ Π½ΠΎΠ»ΠΎΠ³ΠΈΡΒ ΠΏΡΠΎΠΈΠ·Π²ΠΎΠ΄ΡΡΠ²Π° ΠΎΠΏΠΈΠ»ΠΊΠΎΠ±Π΅ΡΠΎΠ½Π½ΡΡ Π±Π»ΠΎΠΊΠΎΠ² ΡΠ²ΠΎΠΈΠΌΠΈ ΡΡΠΊΠ°ΠΌΠΈ ΠΏΡΠΈ ΠΏΠΎΠΌΠΎΡΠΈ ΡΡΠ°Π½ΠΊΠ° Β«ΠΠ»ΠΎΠΊΠΌΠ°ΡΡΠ΅ΡΒ»:
ΠΡΠΈΠΌΠ΅Π½Π΅Π½ΠΈΠ΅ ΠΎΠΏΠΈΠ»ΠΊΠΎΠ±Π΅ΡΠΎΠ½Π½ΡΡ Π±Π»ΠΎΠΊΠΎΠ²
Π ΡΡΡΠΎΠΈΡΠ΅Π»ΡΡΡΠ²Π΅ ΡΠ°ΠΌΡΡ ΡΠ°Π·Π½ΡΡ ΡΡΡΠΎΠ΅Π½ΠΈΠΉ Π½Π°Ρ ΠΎΠ΄ΠΈΡ ΡΠ²ΠΎΠ΅ ΠΏΡΠΈΠΌΠ΅Π½Π΅Π½ΠΈΠ΅ ΠΎΠΏΠΈΠ»ΠΊΠΎΠ±Π΅ΡΠΎΠ½. ΠΠ°ΡΠΈ, Π΄ΠΎΠΌΠ°, Ρ ΠΎΠ·ΡΠΉΡΡΠ²Π΅Π½Π½ΡΠ΅ ΠΏΠΎΡΡΡΠΎΠΉΠΊΠΈ, ΠΊΠΎΡΡΠ΅Π΄ΠΆΠΈ β Π²ΡΠ΅ ΠΎΠ½ΠΈ ΠΏΠΎΠ»ΡΡΠ°ΡΡΡΡ ΠΏΡΠΎΡΠ½ΡΠΌΠΈ ΠΈ ΠΎΠ±Π»Π°Π΄Π°ΡΡ ΠΏΡΠ΅ΠΊΡΠ°ΡΠ½ΡΠΌΠΈ ΠΊΠ°ΡΠ΅ΡΡΠ²Π°ΠΌΠΈ. ΠΠ· ΡΡΠΎΠ³ΠΎ ΠΌΠ°ΡΠ΅ΡΠΈΠ°Π»Π° ΠΌΠΎΠΆΠ½ΠΎ ΡΡΡΠΎΠΈΡΡ ΠΈ Π²ΡΠ΅ΠΌΠ΅Π½Π½ΡΠ΅ ΠΆΠΈΠ»ΠΈΡΠ°, Π²Π΅Π΄Ρ ΠΎΠ±ΠΎΠΉΠ΄ΡΡΡΡ Π±Π»ΠΎΠΊΠΈ Π΄ΠΎΡΡΠ°ΡΠΎΡΠ½ΠΎ Π΄Π΅ΡΠ΅Π²ΠΎ.
ΠΡΠΈΠΌΠ΅Π½ΠΈΠΌ ΠΎΠΏΠΈΠ»ΠΊΠΎΠ±Π΅ΡΠΎΠ½ ΠΈ Π΄Π»Ρ ΠΏΠΎΡΡΡΠΎΠΉΠΊΠΈ ΠΏΡΠΎΡΠ½ΠΎΠ³ΠΎ ΡΡΠ½Π΄Π°ΠΌΠ΅Π½ΡΠ°. ΠΡΠΈ ΡΡΠΎΠΌ Π² ΡΠ΅ΡΡΠ°Π²ΡΠ°ΡΠΈΠΈ ΠΎΠ½ Π½Π΅ Π±ΡΠ΄Π΅Ρ Π½ΡΠΆΠ΄Π°ΡΡΡΡ Π΄Π»ΠΈΡΠ΅Π»ΡΠ½ΠΎΠ΅ Π²ΡΠ΅ΠΌΡ.
ΠΠ»ΡΡΡ ΠΈ ΠΌΠΈΠ½ΡΡΡ
ΠΠ»ΠΎΠΊΠΈ ΠΎΡΠ»ΠΈΡΠ°ΡΡΡΡ ΡΠ»Π΅Π΄ΡΡΡΠΈΠΌΠΈ ΠΏΡΠ΅ΠΈΠΌΡΡΠ΅ΡΡΠ²Π΅Π½Π½ΡΠΌΠΈ Ρ Π°ΡΠ°ΠΊΡΠ΅ΡΠΈΡΡΠΈΠΊΠ°ΠΌΠΈ:
- ΠΡΡΠΎΠΊΠ°Ρ ΡΠ΅ΠΏΠ»ΠΎΠΈΠ·ΠΎΠ»ΡΡΠΈΠΎΠ½Π½ΠΎΡΡΡ;
- ΠΠΊΠΎΠ»ΠΎΠ³ΠΈΡΠ½ΠΎΡΡΡ;
- ΠΠ°ΡΠΎΠΏΡΠΎΠ½ΠΈΡΠ°Π΅ΠΌΠΎΡΡΡ;
- ΠΠ³Π½Π΅ΡΡΡΠΎΠΉΡΠΈΠ²ΠΎΡΡΡ;
- Π£ΡΡΠΎΠΉΡΠΈΠ²ΠΎΡΡΡ ΠΊ Ρ ΠΎΠ»ΠΎΠ΄Π°ΠΌ ΠΈ ΠΌΠΎΡΠΎΠ·Π°ΠΌ.
ΠΡΠΎΠ±ΡΠΌ ΠΏΠ»ΡΡΠΎΠΌ Π±ΡΠ΄Π΅Ρ Π΅Π³ΠΎ Π²Π΅Ρ, ΡΠ°ΠΊ ΠΊΠ°ΠΊ ΠΎΠ½ ΡΠΎΡΡΠ°Π²ΠΈΡ Π²ΡΠ΅Π³ΠΎ 50 ΡΠΎΠ½Π½ ΠΏΡΠΈ ΠΏΠ»ΠΎΡΠ°Π΄ΠΈ Π² 250 ΠΌ2. ΠΠ»Π°Π³ΠΎΠ΄Π°ΡΡ ΡΡΠΎΠΌΡ ΠΊΠ°ΡΠ΅ΡΡΠ²Ρ ΠΌΠ°ΡΠ΅ΡΠΈΠ°Π»Π° ΠΌΠΎΠΆΠ½ΠΎ ΡΡΡΠ΅ΡΡΠ²Π΅Π½Π½ΠΎ ΡΠ½ΠΈΠ·ΠΈΡΡ Π·Π°ΡΡΠ°ΡΡ Π½Π° ΠΏΠΎΡΡΡΠΎΠΉΠΊΡ ΡΡΠ½Π΄Π°ΠΌΠ΅Π½ΡΠ°. ΠΡΠΎΠΌΠ΅ ΡΠΎΠ³ΠΎ, Π½ΠΈΠ·ΠΊΠ°Ρ ΡΡΠΎΠΈΠΌΠΎΡΡΡ ΡΠ°ΠΌΠΈΡ ΠΎΠΏΠΈΠ»ΠΊΠΎΠ±Π΅ΡΠΎΠ½Π½ΡΡ Π±Π»ΠΎΠΊΠΎΠ² ΡΠ°ΠΊΠΆΠ΅ ΠΏΠΎΠ·Π²ΠΎΠ»ΠΈΡ ΡΡΠΊΠΎΠ½ΠΎΠΌΠΈΡΡ.
Π ΠΎΡΠ½ΠΎΠ²Π½ΠΎΠΌΡ ΠΌΠΈΠ½ΡΡΡ, ΠΊΠΎΡΠΎΡΡΠΌ ΠΎΠ±Π»Π°Π΄Π°Π΅Ρ ΠΎΠΏΠΈΠ»ΠΊΠΎΠ±Π΅ΡΠΎΠ½Π½ΡΠΉ Π±Π»ΠΎΠΊ, ΠΌΠΎΠΆΠ½ΠΎ ΠΎΡΠ½Π΅ΡΡΠΈ Π΅Π³ΠΎ Π²ΠΎΠ·ΠΌΠΎΠΆΠ½ΠΎΡΡΡ Π²ΠΏΠΈΡΡΠ²Π°ΡΡ Π²Π»Π°Π³Ρ. ΠΡΠΎ ΠΎΡΠ΅Π½Ρ ΠΏΠ»ΠΎΡ ΠΎ Π΄Π»Ρ ΠΌΠ°ΡΠ΅ΡΠΈΠ°Π»Π°, Π½ΠΎ ΠΏΡΠ΅Π΄ΠΎΡΠ²ΡΠ°ΡΠΈΡΡ Π²ΠΏΠΈΡΡΠ²Π°Π½ΠΈΠ΅ ΠΆΠΈΠ΄ΠΊΠΎΡΡΠΈ Π²ΠΎΠ·ΠΌΠΎΠΆΠ½ΠΎ, Π΅ΡΠ»ΠΈ Π²Π½Π΅ΡΠ½Π΅ ΠΎΠΊΡΠ°ΡΠΈΡΡ ΠΈΡ Π½Π΅ΠΊΠΎΡΠΎΡΡΠΌΠΈ ΡΠΎΡΡΠ°Π²Π°ΠΌΠΈ ΠΈ ΠΊΡΠ°ΡΠΊΠ°ΠΌΠΈ, Π° Π²Π½ΡΡΡΠΈ ΠΏΡΠΎΠ²Π΅ΡΡΠΈ ΠΊΠ°ΡΠ΅ΡΡΠ²Π΅Π½Π½ΡΡ Π³ΠΈΠ΄ΡΠΎΠΈΠ·ΠΎΠ»ΡΡΠΈΡ.
ΠΡΠ·ΡΠ²Ρ
ΠΠ΅ΠΎΡΠ³ΠΈΠΉ, Π³. Π‘Π°ΡΠ°ΡΠΎΠ²:
ΠΠΎΡΡΡΠΎΠΈΠ» ΡΠ΅Π»ΡΠ½ΡΠΉ Π΄ΠΎΠΌ ΠΈΠ· ΠΎΠΏΠΈΠ»ΠΊΠΎΠ±Π΅ΡΠΎΠ½Π°. Π ΡΠ΅Π»ΠΎΠΌ Π΄ΠΎΠ²ΠΎΠ»Π΅Π½, Ρ ΠΎΡΡ, ΠΊΠΎΠ½Π΅ΡΠ½ΠΎ, ΡΡΠΎΠΈΠ»ΠΎ ΡΠ΄Π΅Π»ΠΈΡΡ Π±ΠΎΠ»ΡΡΠ΅ Π²Π½ΠΈΠΌΠ°Π½ΠΈΡ ΠΏΡΠΎΠ²Π΅Π΄Π΅Π½ΠΈΡ ΠΏΠ°ΡΠΎ- ΠΈ Π³ΠΈΠ΄ΡΠΎΠΈΠ·ΠΎΠ»ΡΡΠΈΠΎΠ½Π½ΡΡ ΡΠ»ΠΎΠ΅Π², ΠΏΠΎΡΠΊΠΎΠ»ΡΠΊΡ ΡΠΎΠ²ΡΠ΅ΠΌ Π½Π΅Π΄Π°Π²Π½ΠΎ ΠΎΠ±Π½Π°ΡΡΠΆΠΈΠ» ΠΊΠΎΠ½Π΄Π΅Π½ΡΠ°Ρ. Π‘ΠΎΠ²Π΅ΡΡΡ ΡΡΡΠΎΠΈΡΡ Π΄ΠΎΠΌ ΠΈΠ· ΠΏΠΎΠ΄ΠΎΠ±Π½ΡΡ Π±Π»ΠΎΠΊΠΎΠ² ΡΠΎΠ»ΡΠΊΠΎ Π² ΡΠΎΠΌ ΡΠ»ΡΡΠ°Π΅, Π΅ΡΠ»ΠΈ ΠΡ ΡΠ°ΠΌΠΎΡΡΠΎΡΡΠ΅Π»ΡΠ½ΠΎ ΡΠΏΠΎΡΠΎΠ±Π½Ρ ΠΏΡΠΎΠ²Π΅ΡΡΠΈ ΠΌΠ΅ΡΡ ΠΏΠΎ ΠΈΠ·ΠΎΠ»ΡΡΠΈΠΈ.
ΠΠ»Π°Π΄ΠΈΡΠ»Π°Π², Π³. ΠΠΌΡΠΊ:
ΠΠ°ΡΠ½Π°Ρ ΠΏΠΎΡΡΡΠΎΠΉΠΊΠ° Π²ΡΡΠ»Π° Π² Π½Π΅ΡΠΊΠΎΠ»ΡΠΊΠΎ ΡΠ°Π· Π΄Π΅ΡΠ΅Π²Π»Π΅, ΡΠ΅ΠΌ, Π΅ΡΠ»ΠΈ Π±Ρ Ρ Π·Π°ΠΊΡΠΏΠ°Π» Π΄ΡΡΠ³ΠΎΠΉ ΠΌΠ°ΡΠ΅ΡΠΈΠ°Π». Π Π·Π΄Π΅ΡΡ ΡΠ΄Π΅Π»Π°Π» Π΅Π³ΠΎ ΡΠ°ΠΌ, Π²ΡΠΎΠ΄Π΅ Π±Ρ Π½ΠΈΡΠ΅Π³ΠΎ ΡΠ»ΠΎΠΆΠ½ΠΎΠ³ΠΎ, Π½ΠΎ Π΄ΠΎΡΡΠ°ΡΠΎΡΠ½ΠΎ ΡΡΡΠ΄ΠΎΠ΅ΠΌΠΊΠΈΠΌ ΠΎΠΊΠ°Π·Π°Π»ΡΡ ΠΏΡΠΎΡΠ΅ΡΡ.
ΠΡΠ»ΠΈ ΡΠΎΠ±Π΅ΡΠ΅ΡΠ΅ΡΡ ΡΡΡΠΎΠΈΡΡ Π΄ΠΎΠΌ ΠΈΠ· ΠΎΠΏΠΈΠ»ΠΊΠΎΠ±Π΅ΡΠΎΠ½Π°, ΠΊΠΎΡΠΎΡΡΠΉ Π±ΡΠ΄Π΅Ρ ΠΈΠ·Π³ΠΎΡΠΎΠ²Π»Π΅Π½ ΡΠ°ΠΌΠΎΡΡΠΎΡΡΠ΅Π»ΡΠ½ΠΎ, ΡΠΎ ΠΏΠΎΡΡΠ΅Π±ΡΠ΅ΡΡΡ Π½Π°Π½ΡΡΡ Π±ΡΠΈΠ³Π°Π΄Ρ ΡΠ°Π±ΠΎΡΠΈΡ . ΠΠ½ΠΈ Π±ΡΠ΄ΡΡ ΠΏΠΎΠΌΠΎΠ³Π°ΡΡ Π΅Π³ΠΎ ΠΈΠ·Π³ΠΎΡΠ°Π²Π»ΠΈΠ²Π°ΡΡ, ΠΈΠ½Π°ΡΠ΅ ΠΏΡΠΎΡΠ΅ΡΡ Π±ΡΠ΄Π΅Ρ Π΄ΠΎΡΡΠ°ΡΠΎΡΠ½ΠΎ Π΄Π»ΠΈΡΠ΅Π»Π΅Π½. ΠΠΎ ΠΏΡΠΈ Π·Π°Π΄Π΅ΠΉΡΡΠ²ΠΎΠ²Π°Π½ΠΈΠΈ ΡΠ°Π±ΠΎΡΠΈΡ Π² ΠΈΡΠΎΠ³Π΅ ΡΡΠΌΠΌΠ° Π²ΡΠΉΠ΄Π΅Ρ ΡΠ°ΠΊΠ°Ρ ΠΆΠ΅. ΠΠ΅ Π·Π½Π°Ρ, Π½ΠΎ Π²ΡΠ΅ ΠΆΠ΅ Ρ Π±Ρ ΡΡΡΠΎΠΈΠ» Π΄ΠΎΠΌ ΠΈΠ· Π±ΠΎΠ»Π΅Π΅ ΡΡΠ°Π΄ΠΈΡΠΈΠΎΠ½Π½ΡΡ ΠΌΠ°ΡΠ΅ΡΠΈΠ°Π»ΠΎΠ².
Π ΠΎΠ΄ΠΈΠΎΠ½, Π³. ΠΠΈΠΉΡΠΊ:
Π‘Π΄Π΅Π»Π°Π» Π½Π΅ΡΠΊΠΎΠ»ΡΠΊΠΎ ΠΏΠΎΡΡΡΠΎΠ΅ΠΊ Π½Π° ΠΎΡΠ½ΠΎΠ²Π΅ ΠΎΠΏΠΈΠ»ΠΊΠΎΠ±Π΅ΡΠΎΠ½Π½ΡΡ Π±Π»ΠΎΠΊΠΎΠ². ΠΠΎΠ²ΠΎΠ»Π΅Π½ ΠΎΡΠ΅Π½Ρ, Π½Π° ΡΠ»Π΅Π΄ΡΡΡΠΈΠΉ Π³ΠΎΠ΄ ΠΏΠ»Π°Π½ΠΈΡΡΡ Π·Π°Π½ΡΡΡΡΡ ΠΌΠ°ΡΡΡΠ°Π±Π½ΠΎΠΉ ΡΡΡΠΎΠΉΠΊΠΎΠΉ ΠΈΠ· ΡΡΠΎΠ³ΠΎ ΠΌΠ°ΡΠ΅ΡΠΈΠ°Π»Π°.