Приспособление для плазмореза своими руками
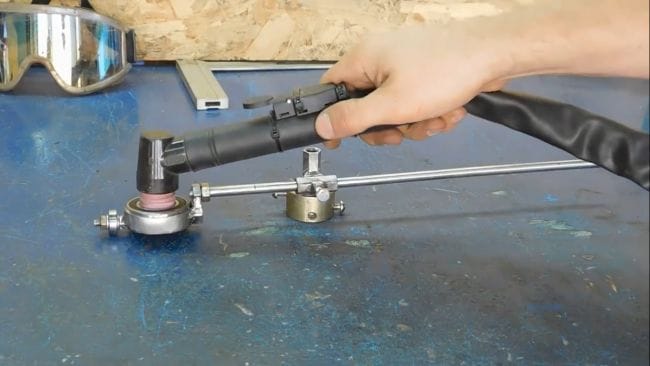
Приветствую, Самоделкины!
Работая непродолжительное время с плазморезом мастер-самодельщик, автор YouTube канала «TeraFox», столкнулся с такой проблемой, как сделать ровный рез. Например, то, что касается прямых линий, тут уж без особых проблем в роли линейки может выступать обычная металлическая полоса.


Рез получается довольно таки неплохим, а вот то, что касается круглых отверстий, как бы мастер ни пробовал, огрехи как ни крути все равно будут.
Автор демонстративно показывает, при этом реально стараясь максимально ровно струей плазмы вырезать круг. Но увы получается то, что получается. Если диаметр будет больше шансы на косяки увеличивается, так как концентрация внимания уменьшается, а напряженность в руках возрастает. И вот сегодня мы будем решать эту проблему. Не самая простая задача подобрать составляющие элементы, но все же автор постарался сделать сегодняшнюю самоделку из максимально доступных вещей.
— отрезок восьмого кругляка;
— резец, который автору попался на барахолке;
— там же он нашел плашкодержатель и по диаметру подобрал несколько подшипников.
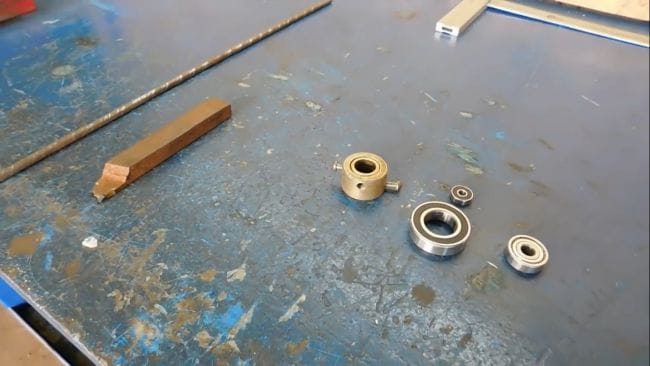
На удивление, но к плашкодержателю удалось подобрать магнит необходимого диаметра и подшипник, который почти плотно садился. По бокам прижимные винты, которые фиксировали магнит и подшипник, так что пока всё складывается.
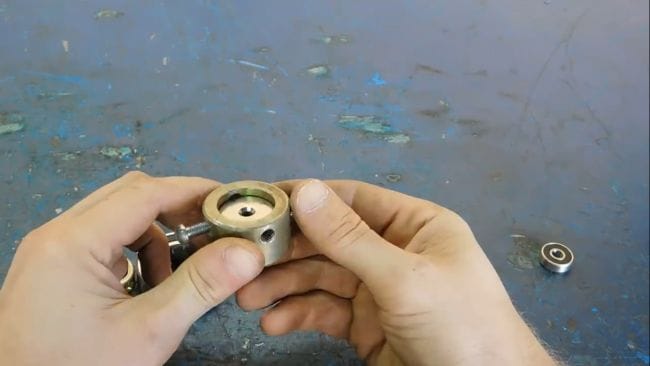
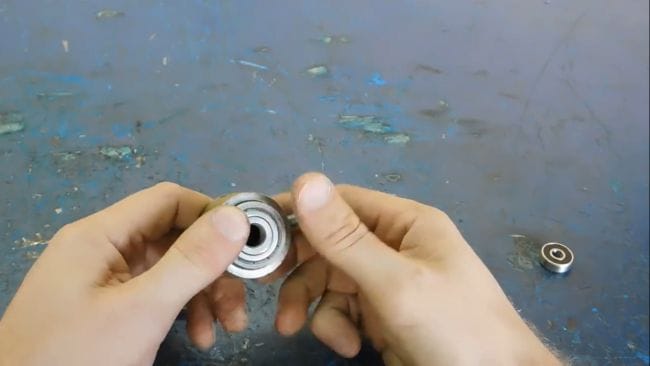
А вот резец как автор его не крутил, не подошел по высоте, поэтому внеплановая замена на удлиненные гайки и болт в придачу, который был найден на полке верстака.

Высоту шляпки стачиваем примерно в половину, а то и больше.
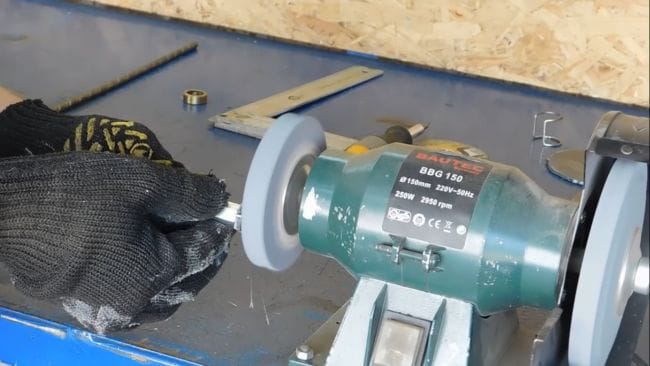
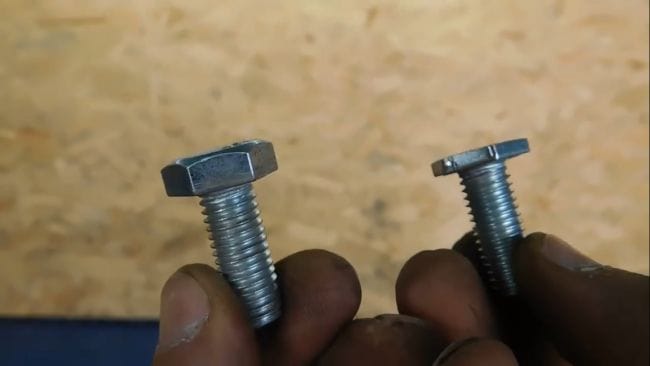
Удлиненную гайку необходимо просверлить посередине и приварить обычную гайку. После свариваем две гайки вместе.
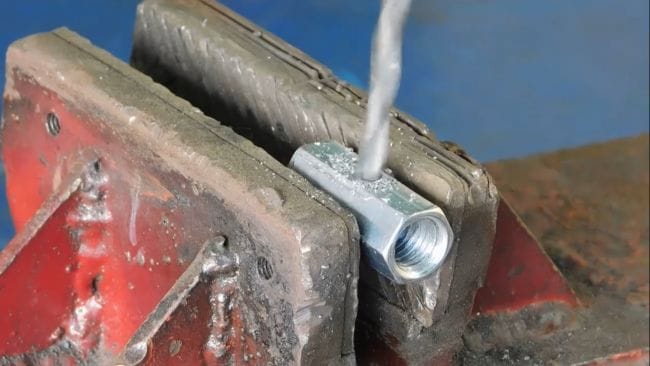

Все детали первого узла сегодняшней самоделки подготовлены, остается собрать и посмотреть всё ли срослось, как и предполагалось.
Все отлично работает, как и хотелось. Можно приступать ко второй части. Подшипник под сопло с внутренним диаметром подходящего размера автор не подобрал, посадка не совсем плотная, поэтому он дремелем снимает немного металла с внутренней части, добиваясь чуть более глубокой посадки.


А дальше начинается сплошная импровизация. Автор нашел завалявшуюся шайбу, которая выступит в роли основания под обойму подшипника.

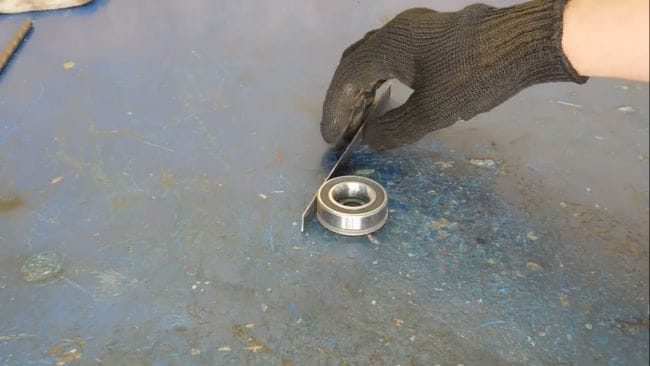
Далее автор обернул металлической полосой шайбу и приварил. Настолько плотно подшипник сел в обойму, что достать оттуда автор его уже не смог.

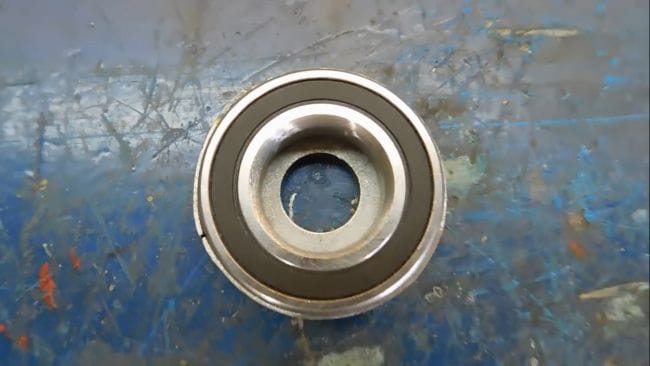
Затем автор подобрал гайки и болтик, выставил будущее расположение, остается только все это приварить.

Во избежание повреждения подшипника окалиной маскируем его скотчем и после пары сварных точек производим охлаждение сжатым воздухом.


Далее сглаживаем сварные швы в труднодоступных местах подходящим инструментом, и второй элемент приспособления готов.
Эхо прошлого, автор взял по случаю набор плашек и метчиков. К радости, такие наборы еще попадаются на рынке.
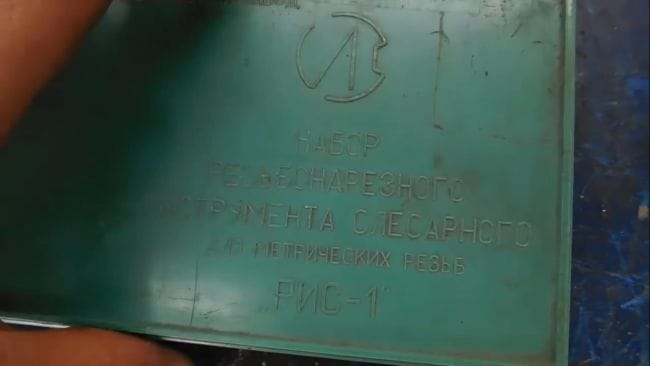
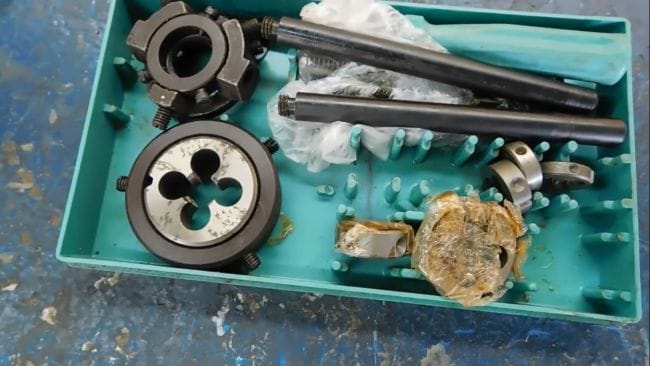
С легкостью нарезаем резьбу на отрезке кругляка под две гайки, остается только собрать все составляющие и приспособление (а точнее циркуль) готово.
Магнит прилипает на отлично, по ощущению на разрыв около 5-ти кг. Итак, теперь давайте попробуем вырезать круг небольшого диаметра. Движение рукой уже более уверенное, так как есть опора. Круги получаются поровнее, но нужно понимать, что без сноровки с ходу, результат будет неудовлетворительным.
Теперь давайте вырежем круг большего диаметра.
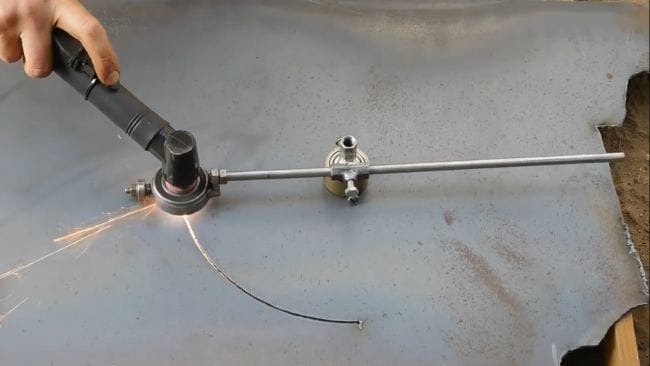
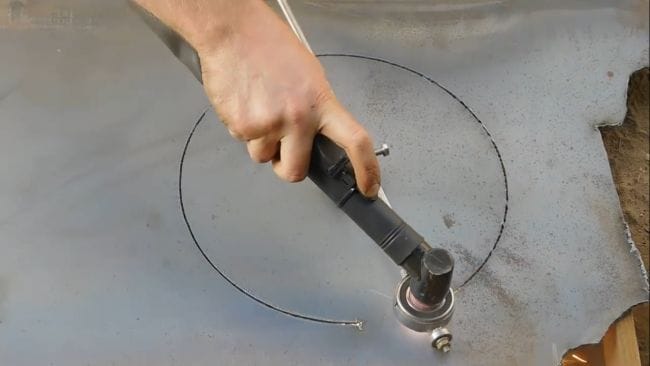
Ещё одно замечание, когда мелкие частицы попадают под подшипник, происходит как бы перескакивания и в последствие не прорезание металла. Вывод: поверхность предварительно хорошо протереть ветошью и удалить весь мусор с поверхности.

Вырезая круг еще большего диаметра, автор прижимает горелку чуть сильнее и старается вести медленно. Все происходит на вытянутую руку, чтобы не попасть в кадр, и в результате этого автор расплачивается очередным проскакиваем подшипника из-за неудобства прижимания. Но тем не менее круг он дорезает и получается довольно-таки прилично.


Далее для удобства мастер перемещается на верстак и попробует еще несколько раз повырезать кружки. Результат его вполне устраивает, это то, чего не хватало в работе с плазморезом при вырезании отверстий большого диаметра.
Циркуль получился полностью разборным, при смене стрелы можно вырезать круги внушительных размеров, но пока что необходимости конечно в этом нет, но мало ли как оно будет. Ну а на сегодня все. Благодарю за внимание. До новых встреч!
Видео:
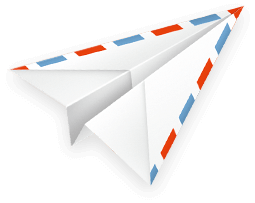
Получайте на почту подборку новых самоделок. Никакого спама, только полезные идеи!
*Заполняя форму вы соглашаетесь на обработку персональных данных
Становитесь автором сайта, публикуйте собственные статьи, описания самоделок с оплатой за текст. Подробнее здесь.Оборудование
Ширина зоны резания (SMM 1\1 mini \ SMM 1,5\1,5 mini) |
1000\1500 мм |
Длина зоны резания (SMM 1\1 mini \ SMM 1,5\1,5 mini) |
1000\1500 мм |
Скорость перемещения |
5000 мм\мин |
Программная точность позиционирования |
0,1 мм |
Разрезаемые материалы при использовании плазменной технологии |
Все виды листовых металлов |
Толщина разрезаемого металла плазмой |
Зависит от источника плазмы |
Рабочая температура окружающей среды |
+5…+40 °С |
Номинальное питающее напряжение |
220В, 50Гц, 400Вт |
Номинальная потребляемая мощность |
1 кВт |
Размещение системы ЧПУ станка |
На удалении не более 1м от станка |
Габаритные размеры блока ЧПУ |
410х325х130мм |
Масса блока ЧПУ |
Не более 8кг |
Габариты станка (ДхШхВ) (SMM 1\1 mini \ SMM 1,5\1,5 mini) |
1264х1308х509 \ 1700х1800х510 мм |
Вес станка (без блока ЧПУ) (SMM 1\1 mini \ SMM 1,5\1,5 mini) |
Не более 25 \ 30 кг |
Станки изготавливаются на основе алюминиевого профиля с приводом по четырехмоторной схеме на шаговых двигателях. По координатам X и Y движение осуществляется посредством гибкого зубчатого ремня и зубчатых барабанчиков. По координате Z – трапецеидальным винтом и гайкой. Вдоль портала уложен лоток с кабель каналом под электрические кабеля питания двигателей. Держатель резака подходит под установку большинства машинных резаков плазменной резки. При необходимости легко может быть заменен на держатель ручного резака.
ЧПУ станка может управлять практически любым плазморезом, оснащенным пилотной дугой с пневмоконтактным или ВЧ (ВВ) поджигом. В комплекте станка есть адаптер подключения любого плазмореза к ЧПУ. Скорость резки определяется конкретным режимом резки и характеристиками примененного плазмореза.
Наши станки оснащены специализированным русскоязычным программным обеспечением, облегчающим освоение оборудования и гарантирующим качественный результат, совместимым практически со всеми CAD и CAM системами.
Процесс резки осуществляется программой с любого (бытового) компьютера, работающего под Windows XP или выше, оснащенного двухъядерным (не менее) процессором и СОМ портом (переходники USB-COM не подходят)
Входная информация для программы резки может быть представлена двухслойным чертежом в формате DXF или УП в G- кодах. Набор управляющих кодов станка может настраиваться. Программа резки на русском языке поставляется на Flаsh карте. Преимущества:
-
Система «Умный прожиг»
-
Автоматический контроль высоты резака (система ТНС)
-
Автоматический контроль динамики скорости реза и качества обработки углов.
Станок может быть укомплектован точечным индуктивным датчиком поиска металла (автоматической установки высоты врезки).
Так же в комплекте поставки есть описание программы, инструкции подготовки программ и множество примеров, инструкции подключения к ЧПУ основных видов аппаратов плазменной резки.
Станок поставляется в частично разобранном виде под самостоятельную болтовую сборку.
Это оборудование можно приобрести в кредит или рассрочку!
Для процесса плазменной резки требуется чистый воздух без примесей. Производительность компрессора подбирается согласно требованиям на расход воздуха для аппарата плазмы. Коалесцентные фильтры служат для исключения попадания масла и влаги на резак. Эти вещества, попав в камеру плазмотрона, могут привести к его поломке
Запрос коммерческого предложения
Китай Мини- Станки Плазменной, Китай Мини- Станки Плазменной список товаров на ru.Made-in-China.com
Цена FOB для Справки:
2 100,00-9 600,00 $ / set
MOQ:
1 set
- Индивидуальные: Индивидуальные
- Расположение: Горизонтальный
- Резка материала: Медь,Углеродистая сталь,Железо,Алюминий,Сплав металла,Нержавеющая сталь
- Автоматическая ранг: Автоматическая
- Источник питания: Электрический
- Режим «резание»: Плазменная резка
-
Поставщики с проверенными бизнес-лицензиями
Поставщики, проверенные инспекционными службами
Jinan Huaxia Machinery Equipment Co., Ltd. - провинция: Shandong, China
Недорогой плазморез — Оборудование для плазменной и газовой резки
aftaev, какой-ть аппарат конкретно можете порекомендовать?
Я имею китайщину на 50А с пилотным поджигом дуги, но без пилотной дуги, потому плазма аккуратно валяется и не используется.
И есть Hypertherm 1000 (производство США) б/у брал за 1500$ в ваш бюджет не вписывается особенно если брать новую и в Росии. Плазма на 60А и работает от 1-3ф. Имеет пилотный поджиг, и пилотную дугу.
Китайщина у меня приблизительно как на приведенной выше ссылке. Помне нужно брать плазму с пилотной дугой.
Поджиг не сильно важен в вшем случае, я так пологаю. Например в Hypertherm можно поджечь дугу в вздухе и она будет гореть 5-6сек, но если поднести заженный плазматрон к металлу у которого плохой контакт с массой плазма не перейдет на металл.
Пилотная дуга хороша тем что когда выходим за пределы металла плазма не тухнет. Конкретно в моей китайщине, ведешь ведешь плазматрон, чуть выше поднял резак, дуга потухла. Я ставил эту плазму на ЧПУ стол где зазор держится практически одинаковый дуга переодически тухла, например когда резаг переезжал прорезь в 1мм. Сразу дугу зажечь не получается надо ждать пока воздух выйдет из шлангов(так моя устроена).
Пример работы с пилотной и без пилотной дуги. С пилотной дугой без проблем режется сетка когда выходим за пределы металла сетки плазма переходит в пилотную дугу. Если резать без пилотной дуги, дуга будет постоянно тухнуть на конце металла. Вы написали что нужна плазма и для кузовных работ, где металл тонкий. Без пилотной дуги резать тонкий металл сложновато, медленно ведешь резак рез расширяется и плазма тухнет.А каждый прокол (так называется поджиг дуги над металлом) уменьшает ресурс расходников.
SergP что вам рекомендовать, незнаю какой у вас имеется выбор. Я бы брал только с пилотной дугой и не слушал продавцов чтоони говорят, а по возможности пробывал. Зажег плазматрон, довел до конца металл отвел от металла и вернул обратно если не потухнет то есть пилотная дуга.