Пенопласты — характеристики свойства и виды пенопласта | ПластЭксперт
Пенопласт. Основные понятия
Пенопласт – это разновидность композитного материала низкой плотности или пеноматериала, одним из компонентов которого является полимер, вторым компонентом – газ. Другими словами, пенопласт является наполненной газом пластической массой. Как правило, пенопласты, в отличие от поропластов, имеют строение в виде изолированных ячеек или отвердевших пен. Ячейки состоят из замкнутых полостей, которые не соединены между собой и в качестве разделителя имеют стенки полимерной матрицы. Отличие поропластов от пенопластов состоит в том, что первые обладают губчатой структурой (поры не изолированы). Система пор, связанных между собой, является главным признаком поропластов.
Отметим, что определение пенопластов и поропластов, данное выше, достаточно условно, т.к. во многих случаях в пенопласте значительное количество ячеек соединено между собой, а в поропласте может быть изолировано. На сто процентов можно говорить об изоляции лишь в том случае, если материал состоит из отдельных вспененных гранул, например популярный в строительстве пенопласт пенополистирол. Точнее будет называть пенопластом любой наполненный газом пластик, который был произведен вспениванием изначально вязко-текучей или жидкой композиции полимера с дальнейшим отверждением последней.
Производство вспененных пластмасс
Выпуск пенопластов в промышленных условиях заключается в том, что газ распределяется в полимере, который в данном случае является полуфабрикатом. Это может быть расплав, раствор, расплаве, дисперсия, жидкий олигомер и т.д. Либо в процессе производства газ не добавляется, а создаются условия для самостоятельного выделения необходимого объема газа в массе полимерного связующего. Это может происходить непосредственно в ходе синтеза или модификации исходного полимера, яркий пример такого материала – пенопласт ППУ (пенополиуретан).
Технологический процесс получения пенопластов использует разнообразные способы достижения эффекта вспенивания, их можно разделить на следующие виды:
- нагнетание газа под давлением в полимерную систему;
- добавление в полимерную систему химических агентов порофоров или газообразователей, которые при определенных условиях разлагаются с выделением газообразных соединений;
- добавление веществ, которые выделяют газ в ходе химической реакции между собой или с другими компонентами системы;
- перемешивание при помощи механических устройств в присутствии пенообразователей или так называемое «барботирование»;
- введение в полимерную матрицу легкоиспаряющихся жидкостей, создающих газовую фазу при повышении температуры;
- другие реже используемые операции.
Различные способы получения вспененной структуры позволяют варьировать свойства готовой продукции в зависимости от исходного состава системы и условий отверждения композиции. В частности, можно получить пенопласт более открытой или замкнутой структурой, разной плотности, различных размеров ячеек и т.п.
Производство пенопласта
Машины и оборудование для производства пенопластов детится на типы, которые зависят от метода получения конечного материала и технических характеристик начального полимера, предназначенного для вспенивания.
Виды пенопласта по методу производства. Экструдированный пенопласт, чаще всего встречается полиэтилен, производят из полимера вспениванием в цилиндре экструдера, либо в элементах формующей оснастки. Пенополистирол или ПСВ производится в виде бисерных гранул, содержащих легкокипящий пентан, которые затем для вспенивания обрабатываются горячим паром непосредственно в форме.
Уже упомянутый выше пенополиуретан получают и перерабатывают в изделия методом впрыска двухкомпонентной смеси на специальных заливочных машинах под давлением. Причем таким образом получают изделия и из мягкого (поролон) ППУ, и жесткого (изоляция труб, детали интерьера автомобиля), так называемого интегрального пенополиуретана. Компонентами для смеси являются полиол и изоцианат, реагирующие с выделением углекислого газа. Их химические особенности и соотношение при впрыске определяют свойства получаемых изделий. Смешение полиола и изоцианата из-за их высокой реакционной способности обычно происходит в головке высокого давления непосредственно перед впрыском в полость в формы.
Рис. 1 Мягкая мебель – основной рынок для эластичного ППУ (поролон).
Простейшие изделия из вспененных пластмасс можно получать и на стандартных машинах для переработки полимеров, например ТПА или экструзионных линиях. Для этого в состав композиции необходимо добавить специальные концентраты добавок веществ, разлагающихся в ходе техпроцесса, так называемых порофоров. Обычно при этом не достигается значительного вспенивания изделий, соответствующей экономии сырья и улучшения свойств готового продукта, однако на его поверхности могут появиться нежелательные следы выхода газа по полимерной массы – дефект «серебрения». Строго говоря, при этом методе получается слегка подвспененная монолитная деталь, а не пенопласт в классическом понимании.
Полимеры, пригодные для вспенивания, и вспениватели
Большинство известных полимеров вполне можно наполнять газами, получая пенопласт. При этом крупнотоннажные пенопласты промышленность производит в основном на основе полистирола (вспененный полистирол, ПСВ), полиэтилена (вспененный ПЭ), поливинилхлорида (пеноПВХ), полиуретанов (ППУ), полипропилена (вспененный ПП). Реже используются полиреактивные, как и ППУ, материал, например эпоксидные, карбамидные, фенольные смолы, а также кремнийорганические полимеры.
Главным образом, при вспенивании в промышленности применяются следующие газообразователи: имеющие в составе азот (азосоединения, нитросоединения, карбонат аммония и т.п.) и легкокипящие жидкости — изопентан, разновидности фреона, метиленхлорид.
Свойства изделий из пенопластов
Современная индустрия производит эластичные (мягкие) и жесткие (интегральные) пенопласты, имеющие ячейки размером 0,02—2 мм, максимум до 5 мм. Эти материалы обладают очень высокими теплоизоляционными и звукоизоляционными свойствами и очень низкой кажущейся плотностью (от 0,02 до 0,5 г/см2). Другие характеристики пенопластов, такие как механические и электрические свойства, газопроницаемость, водо- и химическая стойкость и т.п. зависят от химического состава и рецептуры изначальной полимерной системы и от метода производства и структуры изделия.
Детали из пенопласта, как правило, не нуждаются в дальнейшей постобработке. То есть количество отходов при производстве и эксплуатации таких изделий низкое. Этот факт вкупе с уже озвученными преимуществами делает пенопласт очень привлекательной для изготовителей изделий из пластиков.
Области применения пенопластовых изделий
Теплопроводность любых вспененных материалов очень низкая, что определяющих широкий спектр их применения в самых различных областях человеческой жизни.
Рис 2. Относительно новое применение пенопласта – одноразовые лотки для пищи.
Описываемые изделия широко применяются как утеплитель и звукоизоляционный материал в строительстве, теплоизоляции трубопроводов, в судостроении и самолётостроении, в машиностроении (изоляция холодильников и химических реакторов), автопроме и во многих других областях. Пенопласт применяют при производстве многослойных конструкций (сэндвич-панели), различных плавучих средств, изоляционных листов, амортизирующих прокладок. Широчайшую популярность завоевал вспененный полистирол в разнообразной таре и упаковки, в том числе для бытовой техники и электроники, а также в виде лотков для пищевых продуктов. Огромный объем производства эластичного пенополиуретана необходим для выпуска мягкой мебели, матрацев и зимней одежды. Срок эксплуатации таких изделий может достигать десятков лет.
Объявления о покупке и продаже оборудования можно посмотреть на
Обсудить достоинства марок полимеров и их свойства можно на
Зарегистрировать свою компанию в Каталоге предприятий
Пенопласты полимерные материалы | ПластЭксперт
Пенопласты — газонаполненные пластические массы ячеистой структуры. Пенопласты имеют строение отвердевших пен. Они содержат преимущественно замкнутые, не сообщающиеся между собой полости, разделённые прослойками полимера. Этим они отличаются от поропластов, пронизанных системой связанных каналов-пор, то есть имеющих губчатую структуру. Также пенопласты могут состоять из отдельных гранул (чаще всего пенополистирол).
Выделение пенопластов среди прочих газонаполненных пластмасс в отдельную классификационную группу по признаку изолированности ячеек-полостей достаточно условно, так как во многих пеноматериалах значительная их часть всё же соединена. Правильнее к пенопластам относить любой газонаполненный полимер, полученный путём вспенивания и последующего отверждения первоначально жидкой или пластично-вязкой композиции. При производстве пенопластов газ диспергируют в полимерном сырье полуфабрикате (растворе, расплаве, жидком олигомере, дисперсии) или создают условия для выделения газовой фазы непосредственно в объёме отверждаемого продукта. Технология производства пенопластов бывает основана на различных технологических приёмах вспенивания: механическое перемешивание или барботирование в присутствии пенообразователей; введение газообразователей (веществ, разлагающихся с выделением газа) или веществ, взаимодействующих с образованием газообразных продуктов; насыщение исходной смеси газом под давлением с последующим снижением давления; введение жидкостей, быстро испаряющихся с повышением температуры. В зависимости от состава композиции и условий её отверждения получают материал с преимущественно открытыми или замкнутыми ячейками.
Соответственно оборудование для изготовления пенопластов подразделяется на классы в зависимости от характеристик полимерной основы пенопласта и способа получения вспененного материала. Экструзионный (или экструдированный) пенопласт получают путем вспенивания полимера непосредственно в цилиндре и формующем инструменте экструдера. Изделия из пенополиуретана, как мягкого, так и жесткого, производители получают путем заливки в формы под давлением на специальных заливочных машинах ППУ. При литье пенополиуретановых изделий используется технология смешения двух компонентов сырья – полиола и изоцианата. Вспененные материалы можно получать и на обычном оборудовании для переработки пластмасс – экструзионных линиях и термопластавтоматах путем использования специальных добавок к сырью, порофоров.
Изделия из пористых материалы можно изготавливать также вымыванием из монолитной полимерной заготовки растворимого наполнителя, спеканием порошкообразных полимерных материалов, путём конденсационного структурообразования в растворах полимеров. Близки по свойствам к пенопластам газонаполненные пластмассы, полученные с применением полых наполнителей, например заполненных газом сферических микрокапсул.
Пенопласты можно приготовить из большинства синтетических и многих природных полимеров. Однако пенопласты промышленного назначения выпускают главным образом на основе полистирола (ПС), полиэтилена (ПЭ), поливинилхлорида (ПВХ), полиуретанов (ПУ), полипропилена (ПП), фенольных, эпоксидных, карбамидных и кремнийорганических смол. В качестве газообразователей применяют азосоединения, нитросоединения, карбонат аммония и др.; из легкокипящих жидкостей — изопентан, метиленхлорид, фреоны. Промышленность выпускает жёсткие и эластичные пенопласты с размером ячеек 0,02—2 мм (иногда до 3—5 мм). Они обладают чрезвычайно низкой кажущейся плотностью (0,02— 0,5 г/см2) и превосходными тепло- и звукоизоляционными свойствами. Водостойкость, механические и электрические характеристики пенопластов зависят от химической природы и рецептурного состава полимерной композиции, а также от особенностей структуры готового продукта.
Изделия из пенопластов обычно не требуют последующей обработки, из чего следует что и количество отходов пенопласта обычно невысоко. Это говорит об экологичности процесса и делает его еще более привлекательным для производителей.
Пенопласты широко применяют в самолётостроении и судостроении, в транспортном и химическом машиностроении, в строительстве зданий и технических сооружений как листовой тепло- и звукоизоляционный материал. Полистирольный пенопласт используется и как отделочный материал в строительстве, из него делают различные декоративные плитки, панели, молдинги, плинтусы. Постоянно растущие продажи стройматериалов обеспечивают существенный рост выпуска различных пенопластов как в России, так и за рубежом.
Пенопласты используют при изготовлении многослойных конструкций, различных плавучих средств (понтонов, лёгких лодок, бакенов, спасательных поясов и др.). Теплопроводность пенопласта крайне мала – это одно из основных свойств, определяющих его применимость в различных областях науки и техники. Прозрачность пенопластов для радиоволн и достаточно высокие диэлектрические и гидроизоляционные свойства обеспечивают этим материалам применение в радиотехнике и электротехнике. Пенопласты широко используются в технологии получения амортизирующих и демпфирующих прокладок, разнообразной тары и упаковки для оптических и других хрупких приборов и механизмов, электронной аппаратуры и др. изделий. Упаковочный пенопласт, как правило, представляет собой отформованный в соответствии с контурами упаковываемого продукта пенополистирольный материал. Огромный рынок эластичных пенопластов — производство мягкой мебели и тёплой одежды.
Объявления о покупке и продаже оборудования можно посмотреть на
Обсудить достоинства марок полимеров и их свойства можно на
Зарегистрировать свою компанию в Каталоге предприятий
Пенополистирол | Полимеры | Промышленные материалы
Пенополистирол – отделочный материал. Благодаря своим высоким тепло- и звукоизоляционным характеристикам в сочетании с невысокой ценой, является широко используемым теплоизоляционным материалом. Представляет собой полимер с жёстко вспененной структурой, состоящий из 98% воздуха и 2% полистирола.
В зависимости от способа производства различают следующие виды:
- Безпрессовый, состоит из множества шариков диаметром 5–10 мм, сплавленных друг с другом. Неоднородные, частично открытые поры, высокая степень поглощения влаги;
- Прессовый, имеет замкнуто-ячеистую структуру, обладает высокими диэлектрическими показателями, тепло- и звукоизоляционными свойствами, малым поглощением влаги;
- Экструдированный, характеризуется замкнутыми порами, размеры которых составляют 0.08 – 0,14 мм, минимальным водопоглощением, что позволяет материалу сохранять теплоизоляционные свойства в условиях высокой влажности.
К преимуществам всех видов пенополистирола относятся:
- Значительное снижение теплопотерь в результате использования его в качестве утеплителя;
- Высокие звукоизоляционные характеристики;
- Долговечность, что определяется устойчивостью полимера к воздействию влаги и агрессивных веществ – щёлочи, микроорганизмов;
- Температурный интервал использования от -50°C до +75°C;
- Небольшой вес;
- Невысокая цена.
К недостаткам материала следует отнести его горючесть, с целью её понижения в процессе производства в полимер вводят антипирен, вещество, которое делает конечный продукт трудновоспламеняемым. В маркировке это свойство обозначается буквой «С» – самозатухающий.
Первой технологию производства пенополистирола разработала корпорация BASF в 1951 году, она включает в себя две стадии. Первоначально высушенные гранулы полистирола нагревают до 80°C, содержащийся в размягчённом полистироле изопентан вскипает, гранулы приобретают вид шариков, которые при охлаждении сохраняют свою форму. Затем их снова высушивают и выдерживают при 25°Cпримерно сутки. Изопентан конденсируется, его объём уменьшается, освободившееся место занимает воздух. Пресс-форму на две трети заполняют готовыми гранулами и нагревают до 110°С. Изопентан закипает, гранулы увеличиваются в размере и, слегка расплавляясь, спекаются вместе, занимая всю пресс-форму.
После охлаждения готовый пенополистирол нарезается нагретой нихромовой проволокой на плиты нужного размера. Максимальная длина плиты – 3000 мм, ширина – 1250 мм, толщина – от 20 до 150 мм.
Сегодня выпускаются следующие марки отечественного пенополистирола – ПСБС (полистирол беспрессовый самозатухающий):
- ПСБС-15 плотностью до 15 кг/м³, используют при условии отсутствия механической нагрузки на утеплитель. Подходит для утепления контейнеров, вагонов, строительных бытовок;
- ПСБС-25 от 15 до 25 кг/м³, наиболее универсальный, используется для утепления стен, полов и перекрытий;
- ПСБС-35 от 25 до 35 кг/м³,отличается повышенной прочностью, применяется для изготовления потолочной плитки из пенополистирола, многослойных панелей, теплоизоляции подземных помещений. Служит материалом для устройства спортивных площадок, бассейнов, обогреваемых дорожек, подъездных путей и стоянок для автотранспорта;
- ПСБС-50 от 35 до 50 кг/м³, характеризуется наибольшей устойчивостью к механическим нагрузкам в сочетании с высокой теплопроводностью и низким водопоглощением. Используется для утепления гаражей и стоянок, при строительстве дорог в условиях подвижных грунтов, для обустройства перекрытий многоэтажных холодильников.
Прессовый пенополистирол производится в закрытых пресс-формах при температуре 130°C и давлении 15 МПа с дальнейшим охлаждением. Благодаря своим электроизоляционным свойствам применяется в электро- и радиопромышленности.
Около 50 лет назад американскими специалистами была разработана технология получения экструдированного пенополистирола (ЭППС) из гранулированного полистирола. Перед введением в экструдер исходный полимер можно смешивать с модифицирующими добавками. Например, со стабилизаторами, с целью получения мелких однородных пор. Вспенивающий агент, изопентан или фреон, вводится в расплав полистирола, находящийся в экструдере. В результате получают лёгкий однородный материал, характеризующийся высокими теплоизолирующими свойствами в сочетании с механической прочностью и минимальной степенью водопоглощения.
Области применения:
- Утепление пенополистиролом фундаментов, подвалов, перекрытий, полов, стен, кровельного покрытия;
- Производство сэндвич-панелей;
- Защита от температурных перепадов водопроводных и канализационных магистралей;
- Изготовление несъёмной опалубки из пенополистирола при бетонировании фундаментов;
- В качестве теплоизолирующего лёгкого наполнителя;
- Производство одноразовой посуды;
- Строительство спортивных площадок;
- Дорожное строительство.
Приобретая изделия из пенополистирола, стоит обратить внимание на наличие санитарно-гигиенических сертификатов, подтверждающих содержание остаточного стирола не превышающее 0.1%. Долговечность изделий из этого полимера зависит от способа его производства, безпрессовые пенопласты существенно не меняют своих свойств от 10 до 40 лет, в зависимости от марки. Экструзионный пенополистирол хорошего качества может прослужить вам не меньше 80 лет.
Газонаполненные пластмассы — Википедия
Материал из Википедии — свободной энциклопедии
Газонаполненные пластмассы (пенопласт) — сверхлегкие пластические материалы, получаемые на основе различных синтетических полимеров. Напоминают структуру застывшей пены. Наполнитель таких материалов — газ.
Брусок из пенопласта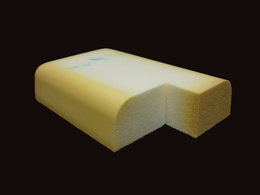
Технология промышленного производства пенопластов впервые разработана в Германии концерном I.G. Farben-Bitterfeld в 1940-х годах. В 1941 году инженеры-химики Вик и Грассл Wick und Grassl концерна I. G. Farben показали возможность получения газонаполненного поливинилхлорида. В эти же годы I. G. Farben-Oppau разработала прессовый метод получения жесткого и эластичного поливинилхлорида с использованием органических газообразователей Porofor N и Porofor PB[1]. Во время войны в Германии при получении пенополистирола и пенополивинилхлорида в качестве газообразователей использовались органические соединения следующих классов: азосоединения (азоизобутиронитрил), сульфонилгидразиды, нитрозосоединения, азиды кислот и производные гуанидина[2].
В 1944 году поливинилхлоридный пенопласт «пористый Игелит» Schaum Igelit производства фирмы Dynamit Nobel A.G. использовался в виде промежуточных слоев диэлектрика в первом радиопоглощающем материале Schornsteinfeger для уменьшения отражающей способности шноркеля (перископа) германских подводных лодок при облучении РЛС союзников, установленных на противолодочных самолётах.
Первый отечественный пенопласт разработан в 1946 году во Всесоюзном институте авиационных материалов (ВИАМ), его серийное производство освоено в 1952 году. Руководил работами учёный-химик А.А. Берлин. Авторы отечественного пенопласта А.А. Моисеев, В.В Павлов, М.Я Бородин и Т.Ф. Дурасова. Специалисты ВИАМ, используя немецкую технологию как основу, установили, что органические газообразователи снижают термостойкость полимерной основы, и в целях повышения последней предложили использовать неорганические газообразователи. Материал предназначался для антенных обтекателей авиационных РЛС[3].
Газонаполненные пластмассы характеризуются высокой тепло-, звуко- и электроизолирующей способностью. Химические и механические свойства газонаполненных пластмасс и их теплостойкость в значительной степени определяются свойствами исходных полимеров, а изоляционные характеристики — особенностями физического строения. Газонаполненные пластмассы могут быть получены из всех известных в настоящее время полимеров.
Подразделение газонаполненных пластмасс[править | править код]
По структуре материала[править | править код]
- C замкнуто-ячеистой структурой (пенопласты (см.пенопласт)).
- C открыто-пористой структурой (поропласты), в которых элементарные ячейки или поры сообщаются между собой и с окружающей атмосферой.
Особый вид газонаполненных пластиков — синтактические пены, вид газонаполненных пластиков, наполнителями в которых служат полые сферические частицы (из синтетических полимеров, стекла и др.), равномерно распределённые в полимерном связующем.
По виду применяемых смол и полимеров[править | править код]
По реакции на тепловое воздействие[править | править код]
- Термопластичные: размягчаются при нагревании и затвердевают при охлаждении. К термопластичным относятся пенополистиролы, пенопласты на основе поливинилхлорида.
- Термореактивные: однажды затвердев (пройдя полимеризацию), не способны размягчаться при повышении температуры. Термореактивными являются, например, пенополиуретаны и пенопласты на основе фенолоформальдегидных смол.
По своему физическому состоянию[править | править код]
- Жесткие.
- Эластичные.
- Полуэластичные.
Газонаполненные пластмассы применяют в качестве легких уплотнителей и теплоизоляторов в большом спектре производств и в строительстве.
В частности поролон — мягкий упругий поропласт на основе пенополиуретана. Название «поролон» происходит от названия торговой марки «Поролон» В современных спасательных жилетах используют пенопласт (пенополистирол) вместо натуральной пробки.
- ↑ Historical Background of Vinyl Foams. In: Polymer-Plastics Technology and Engineering, Volume 6, Issue 2, 1976, Pages 133 – 135
- ↑ Пенопластмассы. Сборник статей под редакцией А.А. Моисеева, В.В. Павлова и М.Я. Бородина — М.: Оборонгиз, 1960. — 183 с.
- ↑ Берлин А.А. Основы производства газонаполненных пластмасс и эластомеров.М.: Госхимиздат, 1954
Конструкционные пенопласты — СКМ Полимер
Композитные сэндвич-панели, состоящие из низкоплотного наполнителя и двух относительно тонких лицевых слоев (например, стекло- или углеткань), позволяют получить очень жёсткий и прочный и при этом легкий материал. Пропитка пенопластов AIREX смолой происходит только в тонких внешних слоях, непосредственно соприкасающихся с армирующими тканями. Основной объем пенопласта остается пористым, что обеспечивает лёгкость всего изделия.
Процесс формовки сэндвич-панелей мало отличается от традиционных процессов производства композитных деталей. Это может быть ручное формование, вакуумная инфузия, RTM, автоклавное формование препрегов и другие способы. Для каждого из методов формовки разработан отдельный тип финишной обработки листа пенопласта, например, перфорация и каналы для формовки с помощью метода вакуумной инфузии.
Ассортимент пенопластов AIREX делится на 3 большие группы:
— ПЭТ-пенопласты (AIREX Т92, AIREX Т90, AIREX Т10) – самые экономичные и простые в выкладке и термоформовании. Обладают хорошей усталостной прочностью, высокой температурной стойкостью (до 150° С при формовке) и не впитывают влагу.
AIREX Т92 – универсальный пенопласт, обладающим отличным сочетанием механических характеристик и низкой цены.
AIREX Т90 – огнестойкий пенопласт, обладающий рядом европейских сертификатов пожарной безопасности, что позволяет использовать его в конструкциях интерьеров в авиации, железнодорожном и автотранспорте.
AIREX Т10 – промышленный пенопласт, обладающий наивысшими среди ПЭТ-пенопластов механическими свойствами и при этом самый экономичный, благодаря специальной технологии производства.
— ПВХ-пенопласт AIREX С70 – самый прочный. Обладает высоким соотношением прочности и веса, отличной ударной и усталостной прочностью, а также низким впитыванием смолы.
— Специальные пенопласты (AIREX R63, AIREX R82)
AIREX R63 – ударопрочный пенопласт, используемый в основном в конструкциях, требующих хорошей защиты от упругих ударов.
AIREX R82 – высокотехнологичный пенопласт, обладающий отличной стабильностью свойств при температурах от -160° С до +190° С, а также высокой радиопрозрачностью.
* — Н-низкая плотность, С-средняя плотность, В-высокая плотность, СВ-сверхвысокая плотность
Сегмент | AIREX R63 | AIREX R82 | AIREX Т90 | AIREX Т92 | AIREX С70 | |||||||||
Плотность* | Н | С | В | Н | С | В | С | В | СВ | С | В | Н | С | В |
Судостроение | ||||||||||||||
Днище | ||||||||||||||
Борта | ||||||||||||||
Стрингеры и шпангоуты | ||||||||||||||
Палуба | ||||||||||||||
Палубная надстройка | ||||||||||||||
Интерьер | ||||||||||||||
Транцы | ||||||||||||||
Рама двигателя | ||||||||||||||
Ветроэнергетика | ||||||||||||||
Лопасти | ||||||||||||||
Гондолы | ||||||||||||||
Железнодорожный транспорт | ||||||||||||||
Бамперы | ||||||||||||||
Корпуса | ||||||||||||||
Боковые обтекатели | ||||||||||||||
Интерьер | ||||||||||||||
Автотранспорт | ||||||||||||||
Полы, корпуса | ||||||||||||||
Локальные усиления | ||||||||||||||
Бамперы | ||||||||||||||
Крыши, спойлеры | ||||||||||||||
Авиастроение | ||||||||||||||
Фюзеляж | ||||||||||||||
Интерьер | ||||||||||||||
Багажные отсеки | ||||||||||||||
Кожухи обтекателей | ||||||||||||||
Промышленность | ||||||||||||||
Радиопрозрачные конструкции | ||||||||||||||
Крышки и кожухи | ||||||||||||||
Медоборудование | ||||||||||||||
Спортивный инвентарь |
Завод по производству пенопласта — ОАО «Полимер»
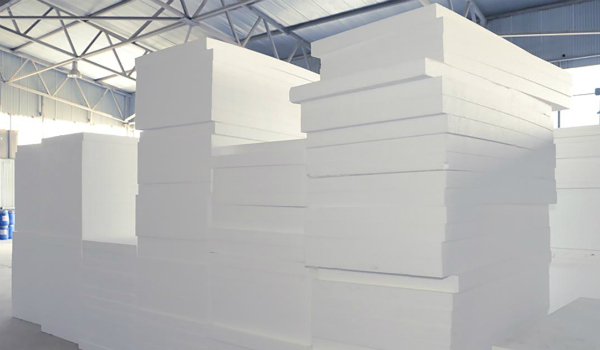
Компания «Полимер» является одним из самых крупных в Черноземье заводов по производству пенопласта. Наша организация предлагает огромный ассортимент высококачественных изделий из резины и пластмассы, пенополистирола и прочих материалов. В этой статье мы подробно изложим вам процесс изготовления пенопласта, благодаря которому вы получаете надёжную и долговечную продукцию.
В первую очередь, мы выбираем сырье, от качества которого зависит очень многое – то как будет вспениваться пенопласт, как долго он будет храниться. Во многом в этом случае имеется зависимость от «возраста» сырья – чем оно старее, тем сложнее будет вспенить гранулы и добиться их необходимой плотности. Сырьё, изготовленное в России, отличается от зарубежного материала широким спектром размеров гранул и их составляющих.
После выбора сырья специалисты завода по производству пенопласта приступают к вспениванию его гранул, используя для этого предвспениватель, в который помещается нужное количество полистирола (его гранул). Подавая горячий пар и наблюдая за процессом через стекло предвспенивателя, мы ожидаем, когда будет достигнут требуемый уровень, после чего извлекаем из него гранулы.
По окончанию предварительного вспенивания гранул их необходимо высушить, для достижения требуемой плотности. Для этой цели они помещаются в специальную сушилку, в которую подаётся горячий воздух. После сушки, гранулы лежат на протяжении двенадцати часов в специальном бункере.
После проведения вышеизложенных работ, мы приступаем к процессу изготовления блоков из пенополистирола. Для этого высушенные и пролежавшие в бункере нужное время гранулы подаются в вакуумную форму для приготовления блока. В этой форме гранулы подаются воздействию пара и давления. Выдержав их в таком состоянии необходимое время, мы убираем давление и пар, и охлаждаем блок-форму. Для того, чтобы снизить влажность и удалить внутренне напряжение у полученных пенополистирольных блоков, они хранятся в специальном помещении.
В дальнейшем, при помощи различных станков и оборудования мы разрезаем эти блоки на листы, торцуем их и получаем готовый материал, из которого в будущем будет изготовлены различные изделия.
Завод по производству пенопласта «Полимер» предлагает только качественно сделанную продукцию по доступным для всех слоёв населения ценам.
Пенопласты на основе фенолоформальдегидных полимеров
admin | ТЕПЛО- И ЗВУКОИЗОЛЯЦИОННЫЕ МАТЕРИАЛЫ ИЗ ПОЛИМЕРОВ | 20.09.2009
Пенопласты на основе фенолоформальдегидных полимеров изготовляют в основном двумя методами:
беспрессовым — вспениванием размягченной полимерной композиции на основе новолачного фенолоформальдегидного полимера газами, выделяющимися при разложении газообразователей, с последующим отверждением во вспененном состоянии при помощи нагревания в присутствии отвердителей;
заливочным — в этом случае жидкая полимерная композиция на основе резольных фенолоформальдегидных полимеров вспенивается газами, выделяющимися при взаимодействии компонентов, или парами легкокипящих жидкостей с последующим отверждением при помощи отвердителей во вспененном состоянии.
Наиболее распространен в строительстве заливочный метод. Для получения пенопластов этим методом используют жидкие резольные фенолоформальдегидные форполимеры марок ФРВ-1, ФРВ-2, ФРВ-1А и «Резецел», представляющие собой полидисперсную смесь продуктов конденсации фенола с формальдегидом в присутствии едкого натра. В форполимер ФРВ-1А вводят алюминиевую пудру. В качестве вспенивающего агента и газообразователя применяют продукты марок ВАГ.
Продукт ВАГ-1 представляет собой гомогенную смесь соляной и ортофосфорной кислот с мочевиной, взятых в весовом соотношении соответственно 2:1:1; продукт ВАГ-2 — диэтиленгликолевый раствор смеси сульфофенола и ортофосфорной кислоты; ВАГ-3 — продукт конденсации сульфофенилмочевины с формальдегидом и ортофосфорной кислотой.|
Технология получения. В процессе получения пенопластов ФРП механическим путем смешивают при нормальной температуре форполимер (100 вес. ч.) и вспенивающий агент (15—25 вес. ч.) и заливают полученную композицию в полость формы или конструкции.
Вспенивание композиции происходит под действием экзотермического тепла реакции окончательной поликонденсации фенолоформальдегидного полимера с кислотным катализатором. При использовании форполимера ФРВ-1А, содержащего алюминиевую пудру, композиция вспенивается водородом, выделяющимся при реакции кислого катализатора с алюминиевой пудрой.
При использовании форполимеров ФРП-1 и ФРП-2, не содержащих алюминиевой пудры, за счет экзотермического тепла от реакции поликонденсации испаряется содержащееся в полимере легкокипящее вещество, например четыреххлористый углерод или фреон 113 (3—8 вес. ч), пары которых и вспенивают композицию. Таким образом, вспенивание и отверждение композиции происходит непосредственно в изделии без подвода тепла извне.
Технологический процесс получения и заливки пенопласта может быть периодическим и непрерывным. При изготовлении пенопластов марок ФРП по периодическому процессу применяют обычные смешивающие устройства (мешалки лопастные, якорные и т. п.) с 800—1400 об/мин.
Продолжительность смешивания компонентов составляет 20—40% от времени живучести данной партии форполимера в зависимости от интенсивности смешивания.|
Для непрерывной заливки смеси применяют машину типа УЗФП, которая состоит из следующих основных частей: двух емкостей (для форполимера и продукта ВАГ), двух насосов и смесительной головки. Последнюю соединяют с машиной при помощи двух шлангов, по которым подаются форполимер и ВАГ в необходимом соотношении. Производительность машины — 6 м³/ч. Машину обслуживают аппаратчик и слесарь средней квалификации.
Свойства и область применения. Пенопласта марки ФРП представляют собой жесткие газонаполненные материалы розового цвета. Основные показатели пенопласта марки ФРП-1, полученного вспениванием газами, и марки ФРП-2, полученного вспениванием в результате испарения легкокипящих жидкостей, приведены в табл. 28.
Таблица 28. Основные показатели пенопластов ФРП-1 и ФРП-2
В процессе вспенивания пенопласт ФРП достаточно хорошо приклеивается к стеклопластику, древесностружечным плитам и несколько хуже к асбестоцементу.
Пенопласты марок ФРП применяют для теплоизоляции трубопроводов, работающих длительное время в диапазоне температур от —50 до +100°, для заполнения различных конструкций, в качестве звукоизоляционного материала и т. д.
Тэгов нет
3667 всего просмотров, 0 просмотров за сегодня