Технология изготовления бетонной смеси
Бетон является единственным материалом, без которого трудно представить себе какое-либо строительство. Возведение любого сооружения начинается с вопроса, как приготовить бетон. Уникальность этого материала позволяет применять его при изготовлении фундамента, стен, колонн, различных перекрытий и т.д.
В настоящее время технология серийного производства основных компонентов бетона позволяет ему конкурировать с признанными природными материалами, такими как камень или гранит. Основные его прочностные и технологические свойства во многом зависят от того, как приготовить бетон. В целом такой процесс достаточно прост. Он может быть выполнен собственными силами и требует только аккуратного подхода.
Основные свойства бетона
Бетон представляет собой водную смесь цементного раствора и различных наполнителей и добавок. В свою очередь, цементный раствор (или простейший бетон) состоит из смеси цемента и песка, приготовленного в виде водного раствора. Полный состав конкретного типа бетона определяется рецептурой в зависимости от назначения материала.


Главным параметром бетона при определении его назначения и качества является механическая прочность на сжатие, т.е. стойкость при вертикальной нагрузке. Принятые стандарты регламентируют прочность бетона в пределах от 7,5 до 80 мПа. Соответственно, марки строительного бетона колеблются от В7,5 до В80.
Прочность в основном зависит от прочностных свойств цемента (марки используемого цемента) и в определенной степени от содержания и качества других компонентов. Для повышения прочностных свойств специальных типов бетона, в их состав могут включаться армирующие добавки.
К технологическим параметрам бетона можно отнести эластичность (пластичность), вязкость и однородность раствора. Для облегчения работ по наложению материала и улучшения внешнего вида укладки в состав могут добавляться пластификаторы и другие добавки. Вопросы вязкости решаются изменением объема воды, а однородность массы зависит от качества перемешивания.
Важным свойством бетона является то, что окончательное его высыхание протекает очень медленно, и в течение всего этого процесса материал увеличивает свои прочностные характеристики. Окончательное высыхание бетона наблюдается не ранее, чем через 6 месяцев после укладки, а наивысшей своей прочности он достигает примерно через 12 месяцев. Такое свойство бетона в основном определяется особенностью цемента.
Цемент, песок и заполнитель
Цемент
Цемент является основой бетона и обеспечивает связывание всех компонентов в единое целое. Он во многом определяет прочность и монолитность всего соединения. Самым распространенным типом цемента, используемым для изготовления бетона, стал портлендцемент, который практически на 80% состоит из силиката кальция, что обуславливает его хорошее склеивание (адгезию) с другими веществами.


Маркировка серийно реализуемого цемента указывает его основные характеристики, знание которых необходимо для обеспечения нужной рецептуры бетона. Например, цемент марки М500-Д20. Первые цифры определяют механическую прочность материала на сжатие.
При изготовлении бетона обычно используется цемент М400 или М500; при этом следует помнить, что для особо нагруженных элементов следует использовать наиболее прочный материал. В мало ответственных элементах строительных конструкциях (например, подушка под фундамент) достаточно применение цемента М300.
Вторые цифры в маркировке (совместно с индексом «Д») определяют наличие и процентное содержание примесей (добавок). Для особо важных элементов целесообразно применение цемента с «Д0». В целом, при изготовлении бетона допускается использование цемента до «Д20», т.е. с содержанием примесей не более 20%.
Цемент, предназначенный для изготовления бетона, должен быть сухим, без комков и сыпучим. При неправильном хранении цемент достаточно быстро впитывает воду и теряет свои важнейшие свойства. Во время приобретения цемента необходимо проверить целостность упаковки и срок его изготовления. Приобретать цемент лучше не ранее, чем за 10 дней до начала работ с ним.
Песок
Песок является одним из основных компонентов бетона, обеспечивающим его объем и структуру. В цементных растворах (для штукатурных и укладочных работ) он является основным наполнителем объема. В общем случае строительный песок представляет собой сыпучую смесь твердых силикатных частиц размером 0,15-5 мм. В зависимости от происхождения песок подразделяется на речной, морской, озерный, карьерный, овражный и т.д.

Для приготавливаемого бетона лучше всего подходит песок с размером частиц 1-2 мм. Если бетон предназначен для фундамента наиболее подходящим является речной песок, так как он практически не содержит глины и удовлетворяет требованиям по размеру частиц.
В цементных растворах для кирпичных кладок и штукатурки можно использовать песок с содержанием глины и илистых включений, так как они повышают пластичность смеси. Абсолютно не допускается наличие в песке примесей растительного происхождения или других веществ, способных гнить и распадаться.
Песок в процессе приготовления бетона должен надежно скрепиться цементом, а наилучшая адгезия наблюдается у достаточно крупных частиц. В связи с этим применение песка с большим содержанием очень мелких пылеобразных частиц (менее 0,15 мм) не рекомендуется. Находит применение тяжелый карьерный песок, полученный при дроблении горных пород. Такой песок несколько тяжелей по массе, но имеет необходимые размеры частиц (зерен).
Заполнитель
В качестве объемного заполнителя бетона используются щебень и гравий. Они представляют собой сыпучий материал в виде кусочков горной породы и обеспечивают основную прочность. Размер используемых для бетона кусочков колеблется от 5 до 35 мм.
Лучше всего подходит материал, полученный дроблением породы, так как он обеспечивает наилучшую адгезию цемента за счет неровности (шероховатости) поверхности. Применение речной или морской гальки не желательно, в связи с тем, что ее поверхность отшлифована водой и не гарантирует нужное сцепление.


Наполнитель должен содержать кусочки щебня или гравия разного размера, что необходимо для более плотного их прилегания друг к другу и снижения риска образования пустот. Если приобретенный материал состоит в основном из крупных элементов, рекомендуется добавить щебень размером 8-10 мм; и, наоборот, в мелкий щебень следует добавить кусочки размером 20-30 мм.
Крупные куски размером более 35 мм лучше удалить, так как они затруднят перемешивание массы. Не допускается наличие в наполнителе посторонних примесей в виде грязи, почвы, растительных волокон и т.д.
Вспомогательные компоненты
В состав бетона может входить ряд вспомогательных компонентов. Для увеличения текучести и технологичности смеси обычно добавляются пластификаторы. В бетоне для фундаментов их применение необязательно, а вот для кладок или штукатурки — целесообразно.


Для повышения пластичности массы находит применение добавка в смесь гашеной извести. В то же время следует помнить, что известь может уменьшить адгезию цемента к наполнителю, что требует осторожного подхода к количеству этой добавки.
Находят применение суперпластификаторы, которые повышают технологические свойства бетона, увеличивают его влагостойкость и морозоустойчивость. Для удобства работы с бетоном иногда добавляются ускорители и замедлители высыхания раствора.
Все рекомендуемые вспомогательные компоненты выпускаются серийно и предлагаются торгующими организациями. Следует помнить, что общее количество добавок не должно превышать 2% от массы бетона, для того чтобы они не повлияли на прочностные характеристики материала.
Вода
Не следует халатно относиться к использованию воды, чтобы приготовить бетон. Вода не должна иметь загрязнений и примесей, особенно органического происхождения. Заметное влияние на качество бетона может оказать присутствие в воде кислотных или щелочных веществ, масел и сахаров.
Запрещено применение болотных или неочищенных сточных вод. Осторожно следует использовать воду из рек и других водоемов. Наиболее удовлетворяет всем требованиям водопроводная питьевая вода.
Рецептура бетона своими руками


Чтобы приготовить бетон, прежде всего следует определиться с его рецептурой. Она зависит от назначения бетона и может варьироваться в достаточно широких пределах. Самый простой бетон (так называемый, тощий бетон) марки В7,5 приготавливается в следующем соотношении ингредиентов:
- цемент М400 — 1 часть;
- песок — 10 частей;
- вода — 0,5 части.
Такой бетон используется для подложек (в том числе под фундамент), черновых сглаживающих заливок и т.д. Он не отличается прочностью и пластичностью.
Достаточно распространен бетон марки В15, имеющий следующую рецептуру:
- цемент М400 — 1 часть;
- песок — 2,1 части;
- щебень или гравий — 5 частей;
- вода — 0,6 части.
Большей прочностью обладает бетон марки В25 (цемент М500 — 1 часть, песок — 2 части, щебень — 4 части, вода — 0,5 части). При самостоятельном приготовлении бетона для фундамента часто усредняют рецептуру: цемент М500 — 1 часть, заполнитель — 5 частей, вода — 0,5-1 часть.
Для части фундамента, расположенной ниже поверхности земли содержание наполнителя уменьшают до 3 частей. Следует помнить, что содержание песка во всем объеме наполнителя должно быть не менее 30%. Добавление дополнительных компонентов производится по усмотрению исполнителя работ.
Приготовление бетона: инструкция
Инструмент и приспособления
Понадобится:
- емкость для перемешивания;
- мерное ведро;
- вибратор;
- лопата;
- безмен;
- кувалда;
- сито;
- тачка или носилки;
- совок или мастерок.
Для того чтобы приготовить бетон, необходимо выполнить несколько операций: подготовка компонентов, приготовление смеси компонентов и перемешивание смеси с водой. Подготовка компонентов включает удаление примесей, просеивание и развеску согласно рецептуре. Цемент тщательно разминается во избежание попадания комочков и при необходимости просеивается через мелкое сито.
Песок для удаления примесей и крупных зерен просеивается через сито с размером ячеек до 5 мм. Гравий и щебень целесообразно просеять через это же сито с целью удаления частиц размером менее 5 мм.
Развеску ингредиентов лучше производить с помощью мерного ведра, т.е. по объему (поэтому рецептуру удобнее указывать в частях).
Взвешивание компонентов может привести к заметной погрешности из-за различной степени влажности песка и колебания удельного веса материала наполнителя. Для ориентирования можно привести примерное соответствие объемного и весового измерения. Так, объем стандартного мерного ведра (10 л) соответствует 13 кг цемента М500, 14 кг песка или гравия.

Приготовление смеси компонентов возможно двумя способами. Первый способ основан на сухом перемешивании всего объема цемента и наполнителя с последующим заливом водой. Такой способ при ручном перемешивании не дает гарантии, что весь объем будет полностью перемешан и на дне не останется сухого остатка.
Второй метод предусматривает поочередную загрузку компонентов в воду при одновременном перемешивании. Этот способ грешит тем, что не может обеспечить равномерного распределения ингредиентов по объему. Наиболее частое применение находит все-таки второй способ.
Перемешивание компонентов с водой производится до получения монолитной массы густой сметанообразной консистенции равномерного серого цвета. Не допускается наличия сухих комочков. Дополнительные компоненты предварительно размешиваются в воде и добавляются в раствор бетона при одновременном перемешивании.
Если необходимо приготовить бетон для фундамента в больших количествах, целесообразно арендовать механическую бетономешалку, что намного ускорит и облегчит работы. В этом случае подготовка ингредиентов производится так же. Замешивать смесь следует в следующем порядке: залить в бетономешалку воду и замесить в ней цемент до сметанообразного состояния; загрузить наполнитель и все перемешать в течение не менее 2 минут (до 5 мин) до получения однородной массы.
Бетон должен получиться пластичным, но не очень густым и достаточно текучим, чтобы заполнить опалубку без образования пустот. Время использования раствора не должно превышать 1,5 часа. Укладка бетона должна сопровождаться уплотнением (утрамбовкой). Если нет специальных вибраторов, утрамбовку можно произвести самому методом штыкования стальным прутом. Такое уплотнение целесообразно проводить через каждые 20 см заливки.
При любом строительстве необходим бетон. Приготовить бетон самому не представляет больших сложностей. Главное — необходимо правильно определить требуемые параметры материала, а исходя из них, выбрать нужную рецептуру. Сам процесс приготовления бетона достаточно прост и обеспечит необходимое качество при выполнении элементарных правил.
Смотрите также:22. Технология приготовления бетонной смеси
Технологический процесс бетонирования конструкций, включает приготовление бетонной смеси и транспортирования ее на строящийся объект, подачу, распределение, укладку и уплотнение ее в конструкции, уход за бетоном в процессе твердения.
Бетонную смесь нельзя заготовить заранее и перевозить на большие расстояния. После приготовления она должна быть доставлена и уложена в блоки сооружения до начала схватывания (обычно 1…3 ч). Поэтому бетонную смесь необходимо приготавливать вблизи мест её укладки так, чтобы время нахождения её в пути в летнее время не превышало 1 ч.
Бетонную смесь приготовляют на механизированном или автоматизированном бетонном заводе в готовом виде доставляют на строительство или приготавливают на приобъектных инвентарных (передвижных) бетоносмесительных установках.
Приготовление бетонной смеси состоит из следующих операций: прием и складирование составляющих материалов (цемента, заполнителей), взвешивание (дозирование) и перемешивания их с водой и выдачи готовой бетонной смеси на транспортные средства. В зимних условиях в данный технологический процесс включают дополнительные операции.
Бетонную смесь приготавливают по законченной или расчлененной технологии. При законченной технологии в качестве продукта получают готовую бетонную смесь, при расчлененной – отдозированные составляющие или сухую бетонную смесь. Основными техническими средствами для выпуска бетонной смеси являются расходные бункера с распределительными устройствами, дозаторы, бетоносмесители, системы внутренних транспортных средств и коммуникаций, раздаточный бункер.
Технологическое оборудование стационарного типа для приготовления бетонной смеси может быть решено по одноступенчатой и двухступенчатой схемам.
Одноступенчатая (вертикальная) схема (рис. 6.1, а) характеризуется тем, что составляющие материалы бетонной смеси (вяжущие, заполнители, вода) поднимаются в верхнюю точку технологического процесса один раз и далее перемещаются вниз под действием собственной силы тяжести по ходу технологического процесса. Достоинства: компактны, экономичны, а недостатки — сложность монтажа (из-за значительной высоты, до 35 м).
При двухступенчатой (партерной) схеме (рис. 6.1, б) подъем составляющих материалов бетонной смеси происходит дважды, т.е. составляющие бетонной смеси сначала поднимают в расходные бункера, затем они опускаются самотеком, проходя через собственные дозаторы, попадают в общую приемную воронку и снова поднимаются вверх для загрузки в бетоносмеситель. Достоинством данной схемы является меньшая стоимость монтажа, а недостатком – большая площадь застройки.
При потребности в бетонной смеси не более 20 м3/ч обычно применяют передвижные мобильные бетономешалки со смесителями гравитационного типа.
Рис. 6.1. Схемы компоновки бетоносмесительных заводов и установок: а – одноступенчатая; б – двухступенчатая; 1 – конвейер склада заполнителей
в расходные бункера; 3, 9, 10 – поворотная направляющая и распределительная; 4 – расходные бункера; 5 – трубопровод подачи цемента; 6 – дозатор цемента; 7 – дозатор заполнителей; 8 – дозатор воды; 11 – бетоносмесители; 12 – раздаточный бункер; 13 — автобетоновоз; 14 – автоцементовоз; 15 – скиповый подъемник.
Конструкция бетоносмесительных установок позволяет переводить из рабочего в транспортное положение в течение одной рабочей смены и транспортировать их на прицепе на очередной объект. Использование таких установок целесообразно на крупных рассредоточенных объектах, расположенных от стационарных бетонных заводов на расстояниях, превышающих технологически допустимые.
Бетонные заводы обычно выпускают продукцию двух видов – отдозированные составляющие и готовую бетонную смесь.
В качестве оборудования для приготовления обычной бетонной смеси применяют смесители цикличного и непрерывного действия.
Бетоносмесители цикличного действия различаются по объему готовой смеси, выдаваемой за один замес.
Производительность цикличного бетоносмесителя
П = q·n·kв/1000, м3/ч
где q – объем готовой бетонной смеси за один замес, л; n – число замесов в один час; kв – коэффициент использования бетоносмесителя по времени (0,85…0,93).
Загрузку бетоносмесителя цикличного действия производят в следующей последовательности: сначала в смеситель подают 20…30% требуемого на замес количества воды, затем одновременно начинают загружать цемент и заполнители, не прекращая подачи воды до необходимого количества. Цемент поступает в смеситель между порциями заполнителя, благодаря чему устраняется его распыление. Продолжительность перемешивания бетонной смеси зависит от вместимости барабана смесителя и необходимой подвижности бетонной смеси и составляет от 45 до 240 с.
Бетоносмесители непрерывного действия выпускаются производительностью 5, 15, 30 и 60 м3/ч, а машины гравитационного типа с барабанным смесителем – производительностью 120 м3/ч. Продолжительность перемешивания в этих бетоносмесителях указывают в паспортах машин.
При приготовлении бетонной смеси по раздельной технологии необходимо соблюдать следующий порядок: в смеситель дозируется вода, часть песка, тонкомолотый минеральный наполнитель (в случае его применения) и цемент. Все эти составляющие тщательно перемешиваются, полученную смесь подают в бетоносмеситель, предварительно загруженный оставшейся частью песка и воды, крупным заполнителем и еще раз вся эта смесь перемешивается.
Состав бетонной смеси должен обеспечивать заданные ей свойства, а также свойства затвердевшего бетона.
К бетонной смеси предъявляют определенные требования:
1) она должна сохранять однородность (при транспортировании, перегрузке и укладке в опалубку), которая обеспечивается связностью (нерасслаиваемостью) и водоудерживающей способностью. Все это достигается правильным подбором состава смеси, точностью дозировки составляющих и тщательным перемешиванием всех компонентов;
2) обладать удобоукладываемостью. Удобоукладываемость – это способность бетонной смеси под действием вибрации растекаться и заполнять форму. Она зависит от зернового состава смеси, количества воды, степени армирования, способов транспортирования и уплотнения смеси.
Все большее применение находит сухая строительная смесь (ССС) – смесь вяжущего, заполнителей, добавок, пигментов, отдозированных и перемешанных на заводе, и затворяемых водой перед употреблением. Точное дозирование компонентов позволяет получать более высокие технические характеристики готовой продукции по сравнению со смесями полученными, приготовляемыми на строительной площадке. Важным достоинством сухих смесей является возможность добавления в них химических добавок и микронаполнителей, как улучшающих их структуру, так и подготовленных для применения в холодное время года.
Технология транспортирования бетонных смесей
Транспортирование бетонной смеси включает в себя доставку ее от места приготовления на строительный объект, подачу смеси непосредственно к месту укладки или же перегрузку ее на другие транспортные средства или приспособления, при помощи которых смесь доставляют в блок бетонирования. Блоком бетонирования называют подготовленную к укладке бетонной смеси конструкцию или ее часть с установленной опалубкой и смонтированной арматурой.
На практике процесс доставки бетонной смеси в блоки бетонирования осуществляют по двум схемам:
— от места приготовления до непосредственной разгрузки в блок бетонирования;
— от места приготовления до места разгрузки у бетонируемого объекта, с последующей подачей бетона в блок бетонирования. Эта схема предусматривает промежуточную разгрузку бетонной смеси.
Транспортирование и укладку бетонной смеси необходимо осуществлять специализированными средствами, обеспечивающими сохранение заданных свойств бетонной смеси.
Транспортирование бетонной смеси от места приготовления до места разгрузки или непосредственно в блок бетонирования осуществляют преимущественно автомобильным транспортом, а транспортирование от места разгрузки в блок бетонирования – в бадьях кранами, подъемниками, транспортерами, бетоноукладчиками, вибропитателями, мототележками, бетононасосами и пневмонагнетателями.
Способ транспортирования бетонной смеси к месту ее укладки выбирают в зависимости от характера сооружения, общего объема укладываемой бетонной смеси, суточной потребности, дальности перевозки и высоты подъема. При любом способе транспортирования смесь должна быть защищена от атмосферных осадков, замораживания, высушивания, а также от вытекания цементного молока.
Допустимая продолжительность перевозки зависит от температуры смеси при выходе из смесителя: она не должна превышать 1 ч при температуре 20-30°С; 1,5 ч — 19-10°С; 2 ч — 9-5°С. Длительная перевозка по плохим дорогам приводит к ее расслаиванию. Поэтому в транспортных средствах без побуждения смеси в пути не рекомендуется перевозить на расстояние больше 10 км по хорошим дорогам и больше 3 км — по плохим.
Выбор транспортных средств осуществляют исходя из условий строящегося объекта: объема бетонных работ; срока их производства; расстояния перемещения; размера сооружения в плане и по высоте; ТЭП (производительности, скорости передвижения, удельной стоимости перевозки). Кроме того, необходимо учитывать также требования сохранения свойств бетонной смеси — недопущения распада, изменения однородности и консистенции.
Для перевозки смеси на объект широко применяют автомобильный транспорт – самосвалы общего назначения, бетоновозы и автобетоносмесители (миксеры).
Перевозка смеси самосвалами. Недостатки: возникают трудности по защите смеси от замерзания, высушивания, утечки цементного молока через щели в кузовах, необходимость ручной очистки кузова.
Перевозка бетонной смеси бетоновозами, оборудованными герметичными опрокидывающимися кузовами мульдообразной формы. Достоинства: перевозка смеси возможна на расстояние до 25-30 км, причем без расплескивания ее и вытекания цементного молока.
Перевозка смеси автобетоносмесителями (миксерами). Это наиболее эффективное средство транспортирования. Автобетоносмесители загружаются на заводе сухими компонентами и в пути следования или на стройплощадке приготавливают бетонную смесь. Вместимость автобетоносмесителей по готовому замесу от 3 до 10 м3. Перемешивание компонентов с водой обычно начинается за 30 – 40 мин до прибытия на объект. В автобетоносмесителях (миксерах) выгодно перевозить также готовые бетонные смеси вследствие имеющейся возможности их побуждения в пути за счет вращения барабана. Достоинства: дальность перевозки сухих компонентов смеси в автобетоносмесителях технологически не ограничена.
Доставленную на объект бетонную смесь можно выгружать непосредственно в конструкцию (при бетонировании конструкций расположенных на уровне земли или малозаглубленных) или перегружать в промежуточные емкости для последующей подачи на место бетонирования.
В бетонируемые конструкции смесь подают кранами в неповоротных или поворотных бадьях или ленточными конвейерами (транспортерами), бетононасосами и пневмонагнетателями (по трубам), звеньевыми хоботами и виброхоботами, ленточными бетоноукладчиками. Поворотные бадьи вместимостью 0,5 – 8 м3 загружают непосредственно из самосвалов или бетоновозов. Ленточные передвижные конвейеры применяют, когда подать смесь к месту укладки средствами доставки или в бадьях трудно или невозможно. Конвейерами длиной до 15 м подают смесь на высоту до 5,5 м. Для уменьшения высоты свободного падения смеси при выгрузке, применяют направляющие щитки или воронки. Недостаток: конвейеры в процессе бетонирования необходимо часто переставлять.
Поэтому более эффективны в этом отношении самоходные ленточные бетоноукладчики, смонтированные на базе трактора, оборудованные скиповым подъемником и ленточным конвейером длиной до 20 м. Для подачи смеси в конструкции, расположенных в стесненных условиях и в местах, не доступных для других средств транспорта применяют бетононасосы. Они подают смесь по стальному разъемному трубопроводу (бетоноводу) на расстояние по горизонтали до 300 м и по вертикали до 50 м. Также для бесперегрузочной подачи смеси и ее укладки используют пневмонагнетатели. Максимальная дальность транспортирования ими — 200 м по горизонтали или до 35 м по вертикали при подаче до 20 м3/ч. Для подачи и распределения смеси непосредственно на месте укладки при высоте 2 – 10 м применяют хоботы, представляющие собой трубопровод из конусных металлических звеньев и верхней воронки; виброхоботы, представляющие собой звеньевой хобот с вибратором. На загрузочной воронке вместимостью 1,6 м3 и секциях виброхобота диаметром 350 мм через 4-8 м устанавливают вибраторы-побудители, а также гасители.
Подачу и распределение бетонной смеси в конструкции на расстоянии до 20 м с уклоном к горизонту 5-20° обеспечивают виброжелобами в сочетании с вибропитателем вместимостью 1,6 м3. Им можно укладывать смеси до 5 м3/ч при угле наклона 5°, а при угле 15° — до 43 м3/ч.
Приготовление и укладка бетонной смеси
• Приготовление бетонной смеси включает две основные технологические операции: дозировку исходных материалов и их перемешивание.
Важнейшим условием приготовления бетонной смеси с заданными показателями свойств, а также обеспечения постоянства этих показатателей от замеса к замесу является точность дозировки составляющих материалов в соответствии с рабочим составом бетона. Дозирование материалов производят дозаторами (мерниками) периодического или непрырывного действия.
Перемешивание бетонной смеси производят в бетоносмесителях периодического и непрерывного действия. В бетоносмесителях периодического действия рабочие циклы машины протекают с перерывами, т. е. в них периодически загружаются отвешенные порции материалов, которые перемешиваются, а далее бетонная смесь выгружается (рис. 6.9). В бетоносмесителях непрерывного действия все три операции производят
По способу перемешивания материалов бетоносмесители бывают с принудительным и гравитационным перемешиванием (при свободном падении).
Для приготовления жестких и особо жестких бетонных смесей созданы так называемые вибросмесители, в которых перемешивание составляющих материалов осуществляется в сочетании с вибрацией, а в некоторых конструкциях — только вибрацией. При соответствующем режиме вибрации, когда силы трения и сцепления между частицами смеси нарушены, а силам тяжести противодействует значительно превосходящее их давление возбуждения в смеси, последняя переходит во взвешенное состояние с высокой подвижностью, что способствует интенсивному перемешиванию смеси.
Транспортирование бетонной смеси к месту укладки должно обеспечить сохранение ее однородности и степени подвижности. При длительной перевозке бетонная смесь загустевает вследствие гидратации цемента, поглощения воды заполнителями и испарения, однако подвижность смеси к моменту укладки ее должна быть не меньше проектной.
На заводах бетонные смеси транспортируют бетонораздатчиками, самоходными тележками, ленточными транспортерами; в цехах малой и средней мощности — электротельферами и электрокарами. Подвижные смеси можно транспортировать на большие расстояния по трубам с помощью пневматических установок. На строительные площадки, где ведутся бетонные работы, бетонную смесь доставляют в автобетоносмесителях, в которых бетонную смесь перемешивают примерно за 5 мин до прибытия на место.
Завод на каждую партию бетонной смеси выдает паспорт с указанием состава бетона и его класса.
• Укладка бетонной смеси и ее уплотнение являются одними из наиболее трудоемких и энергоемких операций. Эти операции в настоящее время выполняются с помощью бетоноукладчиков или более простых машин — бетонораздатчиков. Бетоноукладчики позволяют в большей степени механизировать процесс распределения бетонной смеси в форме. Бетонная смесь должна быть уложена в форме так, чтобы в ней не оставались свободные места; особенно тщательно нужно заполнять углы и суженные места формы. После укладки бетонной смеси производят уплотнение ее вибрированием, виброштампованием, центрифугированием, вакуумированием, прокатом (см. гл. 11).
Наиболее распространенным видом уплотнения бетонной смеси является вибрирование. Степень уплотнения бетонной смеси с помощью вибраторов зависит в основном от частоты и амплитуды колебаний, а также продолжительности вибрирования.
По роду двигателя различают вибраторы электромеханические, электромагнитные и пневматические; наиболее распространены электромеханические вибраторы. В зависимости от вида, формы и размеров бетонируемой конструкции применяют вибраторы различных типов.
На практике часто используют комбинированные способы уплотнения бетонной смеси.
При центробежном способе формования для уплотнения бетонной смеси используют центробежную силу, возникающую при вращении формы. Частота вращения 400…900 об/мин, при этом бетонная смесь равномерно распределяется по стенкам формы и хорошо уплотняется; часть воды затворения (20…30%) отжимается к внутренней поверхности изделия, это способствует повышению плотности и водонепроницаемости. Такой способ формования применяют при изготовлении труб, полых колонн, опор и т. п.
Повысить качество бетона можно вакуумированием смеси, при этом из бетонной смеси извлекается часть избыточной воды и воздуха, одновременно % под действием атмосферного давления бетонная смесь уплотняется, ускоряется твердение и повышается прочность бетона. Еще лучшие результаты дает повторное вибрирование после вакуумирования, при котором закрываются мелкие поры, образовавшиеся при вакуумировании.
Прочность бетона нарастает в результате физико-химических процессов взаимодействия цемента с водой, которые нормально проходят в теплых и влажных условиях. Бетон при нормальных Условиях постепенно набирает свою прочность и к 28 сут приобретает марочную прочность, причем в первые 3…7 сут прочностьбетона растет более интенсивно и на 7-е сутки составляет 60. 70% марочной (проектной) прочности. Для заводской технологии такие условия твердения бетона неприемлемы.
В заводской технологии применяют ускоренные методы твердения — тепловую обработку при обязательном сохранении влажности изделий. На заводах сборного железобетона чаще всего применяют прогрев изделий при атмосферном давлении в паровоздушной среде с температурой 80…85 °С или выдерживание в среде насыщенного пара при 100 °С. Стремятся применять насыщенный пар, чтобы исключить высыхание бетона и создать хорошие условия для гидратации цемента.
На заводах сборного железобетона применяют также и другие способы тепловой обработки изделий: электропрогрев, контактный обогрев, обогрев в газовоздушной среде и др.
• Твердение бетона и контроль кач-ва
Структура бетона образуется в результате затвердевания бетонной смеси и его превращения в камень.
Уплотненная бетонная смесь в начальный период гидратации цемента сохраняет способность к пластическим деформациям. Со временем количество новообразований цементного камня увеличивается, система уплотняется и твердеет, образуется прочный камень определенной структуры. Время формирования структуры я свойств бетона зависит от состава и применяемых материалов- На формирование структуры оказывают влияние вид цемента, химические добавки, В/Ц, температура бетонной смеси, влажность среды и др.
Введение в бетон пластифицирующих добавок, например СДБ, замедляет схватывание цемента в начальный период; повышение температуры ускоряет процесс схватывания и твердения.
Структура затвердевшего тяжелого бетона представляет собой цементный камень с размещенными в нем зернами заполнителя, с множеством пор и пустот разных размеров и происхождения.
Макроструктура бетона может быть представлена системой щебень — цементно-песчаный раствор.
Макроструктура представляет строение системы песок — цементный камень, микроструктура — тонкое строение цементного камня. Микроструктура цементного камня в бетоне состоит из новообразований, непрореагировавших зерен цемента и микропор. С увеличением возраста бетона микроструктура меняется в результате гидратации цемента и роста новообразований, пористость уменьшается, меняются распределение пор и их размеры, бетон становится плотнее и прочнее. Прочность бетона растет неравномерно, в первые 7 сут после затворе-ния она нарастает быстро, а в дальнейшем замедляется. Скорость нарастания прочности бетона зависит от вида цемента.
В первые дни твердения прочность бетона на быстротвердеющих цементах выше, чем, например, на белитовых цементах.
Для твердения бетона необходима теплая и влажная среда. При повышенной температуре и влажной среде (в горячей воде с температурой 80 °С, во влажном паре с температурой до 100 °С или в автоклаве при температуре 175 °С и среде насыщенного водяного пара высокого давления) твердение протекает значительно быстрее, чем в нормальных условиях.
Твердение бетона при температуре ниже 15 °С замедляется, а при температуре ниже 0°С практически прекращается. Изложенное выше имеет важное значение при изготовлении сборных железобетонных изделий на заводах, а также при бетонировании в зимнее время.
Кроме прогрева бетона паром или электрическим током для ускорения применяют химические добавки, например хлористыйкальций и др.
Все вышеизложенное оказывает влияние на твердение бетона, формирование его структуры и, следовательно, свойств бетона.
• Правильно организованный контроль качества бетонных работ на всех стадиях технологического процесса изготовления бетонных конструкций — одно из важнейших условий получения прочного и долговечного бетона и снижения стоимости конструкций. На предприятиях сборного железобетона применяют три вида контроля: входной, пооперационный и выходной. Контроль состоит в испытании и выборе исходных материалов для бетона, в их дозировании и перемешивании, укладке, уплотнении и уходе за ним, а также в определении качества затвердевшего бетона испытанием пробных образцов.
Прочность и качество бетона в конструкции можно ориентировочно определить и без разрушения — с помощью акустических приборов. Сущность их действия основана на скорости распространения ультразвукового импульса или волны удара в материале и зависит от его плотности и прочности. Прочность бетона в конструкции без разрушения можно также определить и механическим способом, например прибором, действие которого основано на характеристике прочности, определяющейся глубиной лунки в бетоне, образованной шариком при его вдавливании, или величины отскока маятника от бетона.
Методы Кошкарова (молотком в стенку), склерометром (прибор со шкалой, по удару определятся Rсж.бет), метод локального разрушения(по динамометру), метод ударного импульса.
Приготовление бетонной смеси
Чтобы из таких разнородных по свойствам веществ, как вода, цемент, песок и щебень или гравий, получить материал с вполне определенными свойствами — бетон, нужно выполнить ряд операций. При этом важно соблюдать указания технических правил и инструкций. Производство бетона хотя и происходит часто непосредственно на строительной площадке, но и в этом случае напоминает нам любое заводское производство.
Из хорошего цемента и каменных материалов можно получить прочный и устойчивый бетон, но можно и испортить его, если нарушить правила приготовления и составления бетона. Прежде всего необходимо определить состав бетонной смеси — соотношение всех материалов для нее. Сколько нужно взять цемента и других материалов и в каком соотношении, определяет лаборатория, существующая на каждом строительстве. До подбора состава бетона должны быть известны требования к этому бетону. В проекте сооружения в зависимости от назначения бетона к нему предъявляются те или иные требования по прочности и другим техническим свойствам.
Прочность бетона указывается в виде марки. Долговечность бетона в большинстве случаев выражается в требовании к его морозостойкости. Для климатических условий нашей страны необходим бетон с очень высокой морозостойкостью. Чтобы бетон удовлетворял этим требованиям, должен применяться портланд-цемент определенного минералогического состава и марки не ниже 500; каменные материалы можно использовать только проверенные на морозостойкость, а водоцементное отношение смеси следует принять не выше 0,50. При соблюдении всех этих требований бетон будет обладать высокой морозостойкостью. Не менее важно при назначении состава бетона предусмотреть, чтобы свойства бетонной смеси соответствавали имеющимся механизмам для ее уплотнения и укладки.
Это соответствие достигается таким подбором состава смеси, который придает ей определенную подвижность. Скорость разжижения бетонной смеси при вибрировании называют еще удобоукладываемостью.
Подвижность бетонной смеси определяют следующим способом. Бетонной смесью наполняют металлическуюформу — конус, не имеющий дна и установленный на ровной подставке. Конус снимают и измеряют оседание (оплывание) бетонной смеси после его снятия. Подвижность бетонной смеси выражают в сантиметрах осадки смеси по сравнению с первоначальной высотой.
Для определения удобоукладываемости конус устанавливают в форму образцов — кубов с размером сторон 20 сантиметров. Форму с конусом закрепляют на лабораторной виброплощадке (рис. 11). Конус заполняют бетонной смесью, так же как и при определении подвижности, снимают форму-конус, включают виброплощадку и определяют время расплывания бетонной смеси в форме. Показателем удобоукладываемости является время в секундах, которое затрачивается на расплывание смеси в форме.
Рис. 11. Определение удобоукладываемости бетонной смеси: слева — форма с конусом, заполненным бетонной смесью, до вибрирования; справа — форма с бетонной смесью после вибрирования
Для обычного дорожного бетона применяется смесь с осадкой конуса 2-3 сантиметра и удобоукладываемостью 20-25 секунд. Для тонкостенных и густоармированных конструкций осадка конуса бетонной смеси должна составлять 5-6 сантиметров при удобоукладываемости 5-10 секунд.
Основное требование, которого обычно придерживаются при подборе состава бетона для дорожных покрытий и для армированных конструкций, — это заполнение всех пустот между частицами более крупного материала мелкими частицами. Кроме этого, необходимо создание смазывающего слоя из цементного теста на поверхности частиц заполнителя для получения подвижной смеси.
Рис. 12. Схема подбора состава бетона
Ha рис. 12 наглядно представлен ход подбора состава бетона. Сначала задаются количеством цемента или по вспомогательным таблицам подсчитывают количество воды, необходимое для данной смеси. Затем определяют водоцементное отношение — В/Ц. Это отношение очень важно для характеристики качества и свойств цементного камня и бетона. Понятно, что чем более разбавлен цементный клей, тем меньше его прочность. В практике подбора состава бетона заданной прочности пользуются построенными на основании опытных данных графиками зависимости прочности бетона от В/Ц. На рис. 13 приведен пример такого графика для бетонов на цементах разных марок и щебня. При большом объеме работ рекомендуется подбирать состав бетона заранее, в лаборатории, определяя зависимость прочности бетона от водоцементного отношения на опыте для данных материалов. Определив расход цемента и воды, рассчитывают количество минеральных материалов — песка и щебня — таким образом, чтобы их объем в сумме с объемом цементного теста составил 1000 литров (1 кубометр). После предварительных расчетов обязательно производят пробное затворение бетонной смеси с проверкой ее удобоукладываемости и с изготовлением контрольных образцов. Если при проверке удобоукладываемость бетонной смеси окажется отличающейся от заданной, производят исправление состава бетона изменением содержания в нем цемента и воды, оставляя неизменным водоцементное отношение.
Рис. 13. График зависимости марки бетона от водоцементного отношения для цементов разных марок (цифры над кривыми обозначают марку цемента).
Когда установлен состав бетона, он передается на бетонный завод. Для точного отвешивания составляющих на современных бетонных заводах применяются автоматические весовые дозаторы, которые устанавливаются для отвешивания заданной порции любого сыпучего материала или воды. На небольших бетоносмесительных установках пользуются более простыми дозаторами, например бункерами или ящиками, смонтированными на обычных сотенных весах.
Точное отмеривание составных частей бетона необходимо для того, чтобы его свойства совпадали с заданными и гарантировалась необходимая однородность смеси. Кроме того, неточность в дозировании ведет к перерасходу цемента — наиболее дорогой составной части бетона. Поэтому современные технические правила требуют обязательного применения несовой дозировки всех материалов.
Следующая операция это перемешивание бетонной смеси. Перемешивание производится в специальных машинах — бетономешалках. Наша промышленность для разных условий работы выпускает передвижные и стационарные бетономешалки разной мощности с объемом смесительного барабана от 100 до 4500 литров. Для приготовления жестких смесей выпускаются бетономешалки с принудительным перемешиванием. Обычные бетономешалки перемешивают бетонную смесь за счет переваливания ее лопастями при вращении барабана. На рис. 14 показаны два вида наиболее распространенных бетономешалок. После перемешивания смесь выгружается путем наклона барабана при его грушевидной форме или через лоток, вдвигаемый внутрь барабана.
Рис. 14. Бетономешалки различной конструкции
Обычные бетономешалки работают по такому периодическому циклу. Но существуют и бетономешалки непрерывного действия, имеющие значительно большую производительность при меньших размерах.
Производительность бетономешалки периодического действия изменяется в зависимости от их емкости. При средней емкости она вмещает при загрузке 1200 литров сухих материалов и выдает около 800 литров готовой бетонной смеси. Ее часовая производительность составляет примерно 15 кубометров смеси. Бетономешалка непрерывного действия более экономична и проектируется на производительность 100-200 кубометров в час.
В дорожном строительстве широко применяются передвижные бетономешалки, так как при поступлении материалов железнодорожным или водным транспортом и больших расстояниях от баз до места укладки перевозка бетонной смеси затрудняется и становится технически недопустимой. При длительной перевозке смеси изменяется ее подвижность и ухудшается качество; поэтому дорожники стремятся перевозить сухие материалы, а смешивать их на месте укладки в передвижной бетономешалке.
Последнее достижение техники в области приготовления бетона — современные автоматизированные заводы для крупных строек. Круглые сутки на таком заводе работают затворы дозаторов, сыплется с грохотом в бункеры щебень и песок, льется вода. Готовая бетонная смесь вываливается в кузова мощных самосвалов, которые везут ее на сооружения, выгружают и снова возвращаются на завод.
Работы по дальнейшему усовершенствованию способов приготовления и укладки бетонной смеси продолжаются.
Чтобы плотно уложить бетонную смесь при наименьшем содержании в ней воды, а следовательно, при наименьшем расходе цемента, в настоящее время широко применяется вибрирование бетонной смеси. В чем же заключается его действие. Каждому известно, что встряхивание зернистого материала, например сухого песка, позволяет поместить и один и тот же ящик гораздо больше материала, чем без такого потряхивания: материал укладывается плотнее. Если встряхивать с большой частотой бетонную смесь, то цементным раствор разжижается, и смесь приобретает свойства жидкости. В таком состоянии бетонная смесь плотно заполняет несь объем опалубки, не оставляя в ней пустот — раковин.
Для придания вибрации бетонной смоги применяются специальные механизмы — вибраторы.
Вибратор совершает несколько тысяч колебаний в минуту, и эти колебания передаются окружающей его бетонной смеси. Смесь, приобретая свойства тяжелой жидкости, растекается по опалубке, заполняя ее и обволакивая арматуру. Щебет, и гравий при этом тонут в цементном растворе и равномерно распределяются по всей массе бетона.
Применяя вибрацию, можно уложить значительно менее подвижные смеси, чем вручную. Уменьшая количество воды для таких смесей, мы улучшаем технические свойства бетона. Поэтому вибрированный бетон обладает более высоким качеством по сравнению с бетоном, уложенным вручную.
Наша промышленность выпускает различные виды вибраторов, предназначенных для укладки бетона в массивные и тонкостенные, неармированные и армированные конструкции. На рис. 15 показан внешний вид внутреннего и поверхностного вибраторов для уплотнения бетонной смеси.
Рис. 15. Внешний вид вибраторов: а-внутренний вибратор; б — поверхностный вибратор
Внутренний вибратор при работе погружается в бетонную массу. Для конструкции небольшой толщины и с большой горизонтальной поверхностью, как, например, дорожные покрытия, плиты мостов и перекрытий и т. п., применяются так называемые поверхностные вибраторы (изображен на рис. 15, б), прикрепленные к площадке, которая ставится на поверхность бетона. Колебания площадки передаются бетонной смеси. Они наиболее широко раопространены в дорожном строительстве. Для уплотнения бетона в изделиях форма с изделием устанавливается на специальный вибростол. При включении вибратора колебаниям подвергается вся форма вместе с бетонной смесью; в результате достигается высокая степень уплотнения. Можно передать колебания бетонной смеси и закрепив вибратор на опалубке; такие вибраторы называются наружными или тисковыми, так как крепятся к опалубке при помощи тисков.
Техника уплотнения бетона, особенно при изготовлении сборных бетонных изделий, быстро совершенствуется: увеличиваются мощность и частота колебаний вибраторов, вводится одновременное вибрирование на вибростоле и поверхностным вибратором, вибрирование с пригрузкой бетонной смеси по всей площади изделия. Можно предполагать, что в ближайшие годы технология укладки и уплотнения бетона сделает значительный шаг вперед на пути дальнейшего технического прогресса.
При строительстве дорог применяются сложные комплексные бетоноотделочные машины, производящие разравнивание смеси, уплотнение ее вибрированием и трамбованием, профилирование поверхности и трамбование ее. Современный агрегат для устройства цементобетонного дорожного покрытия (рис. 16) не уступает по сложности выполняемых операций и эффективности работы зерновым и угольным комбайнам.
Рис. 16. Дорожный бетоноукладчик
Весь цикл устройства дорожного покрытия выполняется несколькими машинами. По профилированному и уплотненному основанию устанавливаются рельс-формы; они отграничивают полосу будущего покрытия проезжей части, являются опалубкой для плиты дорожного покрытия и в то же время служат рельсами для движения бетоноукладочных машин. Цепочка автомобилей-самосвалов доставляет бетонную смесь с завода и сбрасывает ее в ковш распределителя. Из ковша смесь перегружается в бункер-распределитель и укладывается п рыхлом состоянии на основание между рельс-формами слоем определенной толщины. Вслед за распределителем движется бетоноотделочная машина, уплотняющая, выравнивающая и профилирующая покрытие; за ней передвигаются устройства для нарезки температурных швов. За сутки такой агрегат может пройти 300 метров, оставив после себя готовое дорожное покрытие. После укладки бетона поверхность его закрывают слоем песка или пленкой какого-либо лака или битума, предохраняя этим от высыхания. В случае когда укрытие сделано песком, его регулярно поливают водой. Через 20 суток разрешается открывать движение по дороге, если стояла теплая погода с температурой воздуха не ниже 15°.
Для средней полосы СССР продолжительность строительного сезона составляет около 200 суток. За это время один комплект машин сможет приготовить 60 километров первоклассной дороги. А какое огромное количество строительных материалов надо перевезти для этого! Только для сооружения покрытия понадобится свыше 3500 тонн материалов на километр дороги, а на все протяжение дороги — свыше 200 000 тонн. Для перевозки всей этой массы песка, щебня, бетонной смеси и т. п. потребуется около 40 000 рейсов мощных самосвалов.
Приготовление бетонных смесей | Технология бетона и изделий из него
Для получения качественного бетона необходимо в процессе приготовления бетонной смеси обеспечить образование сплошного слоя цементного теста на поверхности зерен мелкого и крупного заполнителя, а также равномерное распределение растворной части в массе крупного заполнителя. Получить однородную бетонную смесь можно путем правильного подбора состава и выбора способа приготовления, типа смесительного оборудования, продолжительности перемешивания, степени заполнения емкости смесителя, а также последовательности загрузки и смешивания компонентов бетонной смеси.
Способы приготовления бетонных смесей. Приготовление бетонных смесей можно производить тремя способами: одновременным смешиванием всех компонентов, перемешиванием с одновременной механической обработкой смеси и раздельным приготовлением цементного теста (или раствора) с последующим смешиванием его с заполнителями.
Приготовление бетонной смеси способом одновременного перемешивания всех компонентов в бетоносмесителях различного типа широко используется в строительстве без существующих изменений несколько десятков лет. Основными недостатками этого способа являются неполное использование вяжущего в бетоне и сравнительно большая продолжительность перемешивания, особенно для жестких смесей. Используемое при этом смесительное оборудование, несмотря на простоту конструкции, имеет большие размеры и отличается повышенной металлоемкостью.
Проведенные исследования и практика показали, что при дополнительной механической обработке компонентов в процессе их перемешивания достигается не только большая однородность смесей с различным содержанием воды (в том числе и жестких), но и повышение активности вяжущих, ускорение процесса твердения, а также улучшение сцепления цементного камня с заполнителем. Этот способ приготовления бетонных смесей позволяет улучшить структуру бетона, повысить его прочность и снизить расход вяжущего.
Для приготовления тяжелых бетонных смесей новым способом сконструированы смесительные машины в основном с вибрационной обработкой смеси. Они имеют сравнительно сложную конструкцию и создают в работе трудноустранимые вибрации и шум, вредно действующие на здоровье рабочих и строительные конструкции здания смесительного цеха.
Как показали исследования, одновременное перемешивание всех компонентов не обеспечивает достаточной однородности бетонной смеси и полного использования вяжущих свойств цемента, а прочность и плотность бетона получаются ниже, чем при раздельном способе приготовления с тем же расходом материалов. Сущность раздельного способа приготовления бетонных смесей заключается в том, что сначала готовят цементное тесто (или раствор), добиваясь при этом значительного повышения активности вяжущего, а затем производят смешивание готового теста (или раствора) с заполнителем.
Для приготовления цементного теста (или раствора) с одновременным повышением активности вяжущего можно использовать как известные методы (например,, мокрый домол цемента в вибромельницах), так и сравнительно новые — приготовление смеси с помощью вибровалковых и струйных смесителей и др. Наиболее эффективен мокрый домол в вибромельницах, когда происходит непрерывное измельчение частиц цемента и разрушение оболочек на зернах цемента, образующихся в процессе гидратации, что способствует дальнейшему взаимодействию цемента с водой и ускоряет впоследствии твердение цемента.
В настоящее время ученые работают над созданием новых методов и конструкций машин для приготовления цементного молока одновременно с его активизацией.
- Бетоноведение
- Технология изготовления сборных железобетонных конструкций и деталей
- Бетонные работы в зимних условиях
- Производство сборных конструкций и деталей из легких бетонов
- Производство сборных изделий из плотных силикатных бетонов и бетонов на бесклинкерном вяжущем
- Производство бетонных и железобетонных изделий на полигонах
- Общие правила техники безопасности и противопожарные мероприятия на строительной площадке
методы, оборудование, технологии, материалы, ГОСТ
Бетон — очень распространенный материал в строительстве. Основными его составляющими в большинстве случаев являются цемент и песок. Заливаются из строительного раствора этой разновидности самые разные конструкции зданий и сооружений, в том числе и ответственные. И конечно же, приготовление бетонной смеси должно производиться с точным соблюдением всех положенных технологий.
Требования
Цементный раствор полагается приготавливать таким образом, чтобы бетон в последующем имел заданную прочность. Качественный материал этого типа должен:
сохранять свою однородность при транспортировке и укладке в опалубку;
обладать необходимой для возведения той или иной конструкции консистенцией;
быть удобоукладываемым.
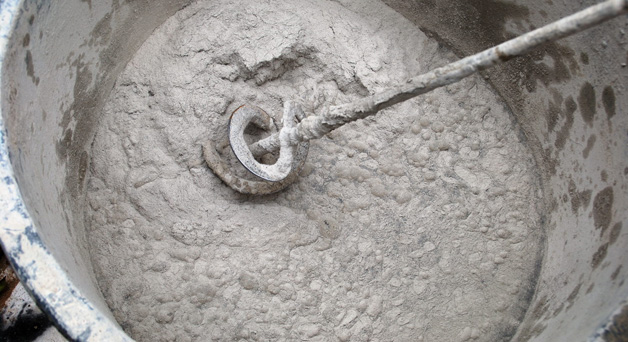
Основные компоненты бетона
При приготовлении бетонной смеси всегда используются следующие три вида ингредиентов:
песок в качестве наполнителя;
цемент как связующее;
вода как затворитель.
Также в некоторых случаях в бетон могут добавляться пластификаторы. Наиболее дешевым и популярным из них является известь. Иногда для повышения эластичности таких растворов могут использоваться и более дорогие полимерные составы.
При приготовлении бетонной смеси также достаточно часто используется щебень. Этот материал делает готовую конструкцию более прочной и позволяет сэкономить на цементе, стоимость которого на рынке сегодня, как известно, довольно-таки высока.
Разновидности
Основных типов бетонов существует всего два — пластичные и жесткие. Первая разновидность растворов хорошо укладывается в опалубку и уплотняется под действием своего веса. Именно такие бетоны в строительстве пользуются наибольшей популярностью. Жесткие смеси содержат в своем составе мало воды. При этом в них добавляют много щебня или гравия. Готовые конструкции из такого бетона получаются более прочными, чем из пластичного. Но при этом в укладке растворы этой разновидности не слишком удобны. При возведении разного рода сооружений такой бетон приходится подвергать вибрированию, виброштампованию, вибропрокату. Помимо этого, такие растворы обычно достаточно сложны в приготовлении. Дозировки при их замешивании приходится соблюдать максимально точно. В противном случае такая смесь может резко изменить свои свойства в худшую сторону.
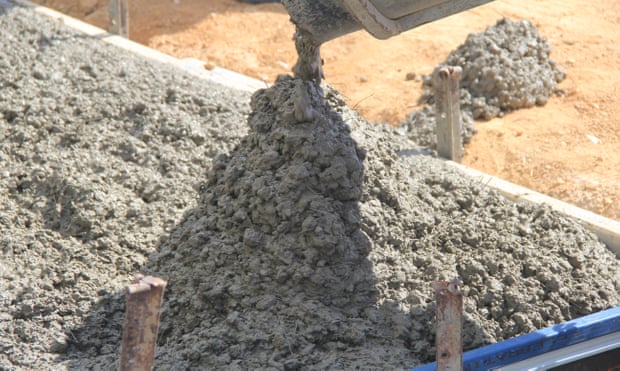
Где может приготавливаться
Чаще всего строительный раствор этой разновидности замешивают на бетонных заводах и доставляют на стройплощадку специальным автотранспортом. Приготовленный таким образом материал характеризуется обычно отличным качеством. В некоторых случаях бетон может приготавливаться и непосредственно на стройплощадке с использованием специального мобильного оборудования. Именно таким образом цементные растворы делают, к примеру, при возведении частных малоэтажных зданий владельцы загородных участков.
ГОСТ
При приготовлении растворов на основе цемента, конечно же, должны в первую очередь соблюдаться требования ГОСТа. Только в этом случае готовые конструкции будут получаться прочными и долговечными. Регулирует процедуру изготовления бетонных смесей в России ГОСТ 7473-2010. В этом документе, помимо всего прочего, указываются допустимые параметры расслаивания растворов, отклонения показателей их удобоукладываемости и пр.
Основные способы приготовления бетона
Чисто технологически операция замеса цементного раствора ничего сложного собой не представляет. Единственное, при выполнении такой работы следует в точности соблюдать дозировки. Согласно требованиям ГОСТ 7473-2010, к примеру, погрешности в этом плане не должны превышать 2 % для воды, цемента и добавок и 3 % для заполнителей. Если это правило соблюдено не будет, слишком прочной и долговечной возводимая из раствора конструкция не получится. А это, в свою очередь, конечно же, негативно скажется на качестве всего здания или сооружения в целом.
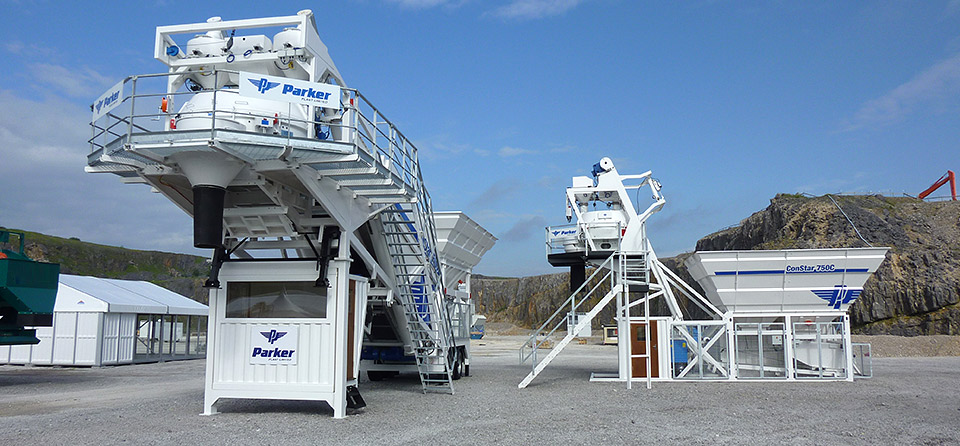
Основных методов приготовления бетонных смесей существует всего два:
Первая технология при этом может использоваться как при замесе раствора на заводе, так и на стройплощадке. Второй способ применяют, конечно же, в основном владельцы загородных участков при возведении каких-либо сооружений своими руками. Оборудования в данном случае не используется никакого. Замес производится с применением чаще всего обычного садового инвентаря.
Механическая технология замеса, в свою очередь, может быть:
В первом случае все операции при изготовлении бетонного раствора производятся с использованием специального оборудования. Именно такой способ замеса применяется на заводах.
Простая технология механического приготовления бетонной смеси предполагает загрузку ингредиентов вручную. При этом собственно само перемешивание компонентов производится с использованием оборудования. Такую методику также достаточно часто используют владельцы загородных участков при самостоятельном возведении бетонных конструкций.
Оборудование
В качестве основного оборудования при замесе цементного раствора используются, конечно же, бетономешалки. Такие машины для приготовления бетонной смеси могут иметь разные размеры и мощность. На рынке сегодня существует недорогое и при этом не слишком габаритное оборудование этого типа, предназначенное специально для владельцев загородных участков и мелких застройщиков.
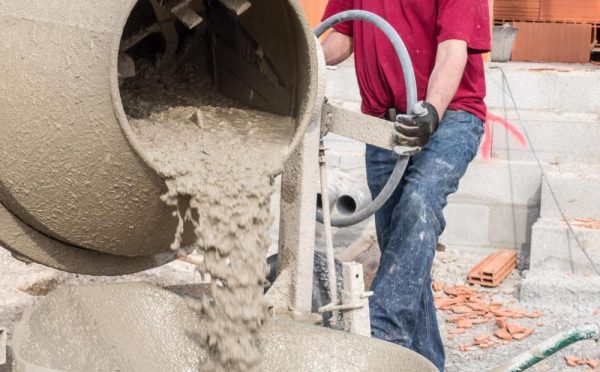
Стандартная методика механического замеса с ручной загрузкой
Технология замеса раствора в бетономешалках разной мощности и габаритов используется обычно одна и та же. При применении такого оборудования для того, чтобы получить качественный материал, важно в первую очередь соблюдать порядок загрузки ингредиентов.
Стандартная технология приготовления бетонной смеси в данном случае выглядит следующим образом:
в чашу бетономешалки загружаются щебень и песок;
производится тщательное перемешивание этих ингредиентов;
в миксер засыпается цемент, после чего бетономешалка включается на несколько минут;
в чашу заливается вода.
Технология автоматического замеса
Порядок подачи ингредиентов при приготовлении бетонных растворов на заводах используется такой же, что и при замесе на стройплощадках с ручной засыпкой компонентов. На первых этапах в данном случае в чашу также закладываются песок и гравий. После перемешивания к ним добавляется цемент. Далее миксер снова включается до получения однородной массы сухих ингредиентов.
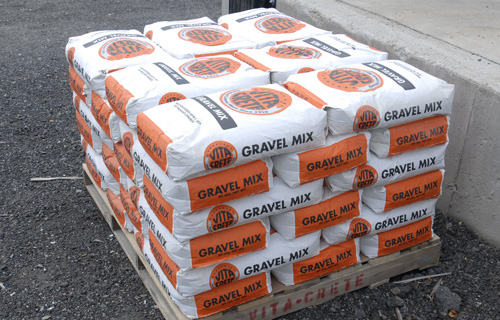
Отличаются методики автоматического и простого приготовления бетонной смеси лишь по способу добавления воды. На заводах в сухую однородную смесь цемента, песка и гравия сначала наливают 70 % положенной доли затворителя. Далее бетономешалка включается на 1 мин. Затем в раствор выливается оставшаяся часть воды.
Можно ли нарушать порядок замеса
Закладывать в миксер бетономешалки ингредиенты желательно именно в той последовательности, которая была указана выше. В противном случае смесь в последующем может, к примеру, содержать комочки. К тому же нарушение порядка действий при приготовлении может привести к тому, что раствор будет иметь не ту консистенцию, которая необходима.
Если по каким-либо причинам бетон на стройплощадке замешивался неправильно и получился не слишком качественным, можно, не теряя времени, попробовать исправить ситуацию. При наличии комочков раствор нужно еще раз хорошенько перемешать в миксере. Если бетон получился жидким, в него следует добавить песка и цемента. Если же смесь вышла слишком густой, ее нужно разбавить небольшим количеством воды. Производить все эти операции следует как можно быстрее. Свои рабочие характеристики цементный раствор сохраняет не более 2-2,5 часа после приготовления.
Технология ручного замеса
Такая методика позволяет получить не настолько качественный, как при использовании бетономешалки, но все же вполне пригодный для возведения не слишком сильно нагруженных конструкций раствор. Инвентарь в данном случае обычно используется такой:
неглубокое корыто;
тяпка и лопата;
ведра;
садовая тачка;
садовый шланг.
Собственно сама методика приготовления бетонной смеси в данном случае выглядит следующим образом:
в корыто засыпают песок и щебень;
тщательно перемешивают эти сухие компоненты;
добавляют в корыто цемент и снова все перемешивают до однородности;
наливают в корыто воды и снова все вымешивают.
Производят замес цементной смеси при использовании такой методики чаще всего с применением мотыжки. Считается, что приготавливать раствор таким инструментом легче, чем лопатой. На заключительном этапе цемент перекладывают в ведра и заливают в опалубку.
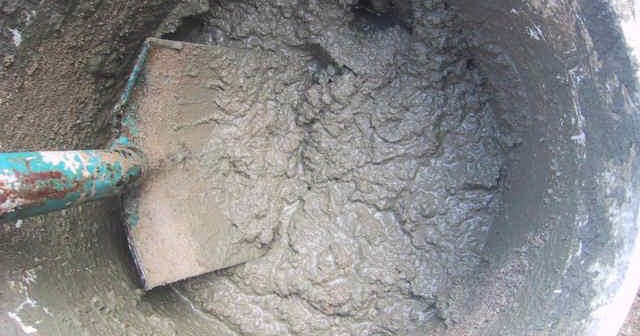
Материалы для изготовления бетонной смеси: требования к качеству
Ингредиенты для приготовления строительных растворов этого типа выбирают в зависимости от конкретного назначения последних. Для заливки нагруженных конструкций обычно используют цемент только высоких марок (к примеру, М400 или даже М500), крупный речной песок и качественный щебень. Для приготовления штукатурного раствора применяют менее дорогое и качественное связующее. Песок при этом используют мелкий карьерный.
В любом случае цемент для приготовления бетонных смесей полагается использовать исключительно свежий. При хранении этот материал обычно вбирает в себя воду и в результате теряет качества связующего. Песок перед приготовлением растворов обязательно просеивают. В таком материале, как в речном, так и в карьерном, могут содержаться грязь, мусор, органические остатки.
Как песок и цемент, щебень перед замесом раствора обычно подготавливают. Такой материал в некоторых случаях предварительно может распределяться по фракциям. Считается, что добавление в смесь таких камней разного, а не одинакового размера, улучшает ее качества.
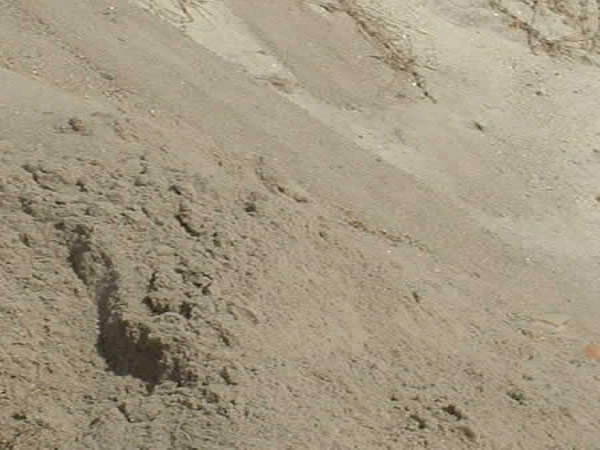
Существуют определенные требования и к предназначенной для приготовления бетонной смеси воде. Она не должна содержать слишком много минералов. И конечно же, воду для раствора следует использовать исключительно чистую без органических примесей и мусора.
Приготовление бетонной смеси
5.49. Дозирование компонентов бетонных смесей следует производить по массе. Допускается дозирование по объему воды добавок, вводимых в бетонную смесь в виде водных растворов. Соотношение компонентов определяется для каждой партии цемента и заполнителей при приготовлении бетона требуемой прочности и подвижности. Соотношение компонентов следует корректировать в процессе приготовления бетонной смеси с учетом данных контроля показателей свойств цемента, влажности, гранулометрии заполнителей и контроля прочности бетона.
(3.03.01-87, п. 2.3)
5.50. Порядок загрузки компонентов, продолжительность перемешивания бетонной смеси должны быть установлены для конкретных материалов и бетоносмесительного оборудования путем оценки подвижности, однородности и прочности бетона в конкретном замесе.
(3.03.01-87, п. 2.4)
5.51. Транспортирование бетонных смесей следует осуществлять специализированными средствами, обеспечивающими сохранение заданных свойств бетонной смеси. Запрещается добавлять воду на месте укладки бетонной смеси для увеличения ее подвижности.
(3.03.01-87, п. 2.5)
5.52. Состав бетонной смеси, правила приемки, методы контроля и транспортирования должны соответствовать ГОСТ 7473-85.
(3.03.01-87, п. 2.6)
5.53. В соответствии с ГОСТ 7473-85 на каждую партию товарной бетонной смеси завод-изготовитель выдает паспорт, а смесь, отпущенную в транспортное средство сопровождает выпиской из паспорта или накладной (приложение 43), подписанной лицом, ответственным за технический контроль завода-изготовителя смеси.
Потребитель имеет право производить контрольную проверку соответствия бетонной смеси требованиям ГОСТ 7473-85 по согласованному с заводом-изготовителем плану контроля.
Накладная хранится на месте укладки бетона до конца смены, после чего передается в строительную лабораторию.
5.54. Номинальный состав бетона подбирают по утвержденному заданию в соответствии с ГОСТ 27006-86. Состав бетона (раствора) подбирают исходя из условия обеспечения среднего уровня прочности, значение которого следует определять по ГОСТ 18105-86* с учетом однородности бетона (раствора). При отсутствии данных о фактической однородности бетона (раствора) средний уровень прочности необходимо принимать равным требуемой прочности для бетона данного класса при коэффициенте вариации 13,5 %.
Методы подбора составов бетона и раствора приведены в рекомендуемых приложениях 4 и 5 СНиП 3.06.04-91.
(3.06.04-91, приложение 6, п. 1)
При подборе состава бетона следует также руководствоваться ВСН 150-93 и «Техническими указаниями по повышению морозостойкости бетона транспортных сооружений».
5.55. Оптимальную дозировку добавок, вводимых в бетонную смесь следует устанавливать экспериментально при подборе состава бетона с учетом данных, указанных в таблице 14 настоящего «Пособия», дозировку воздухововлекающего компонента необходимо устанавливать при строгом контроле времени перемешивания бетонной смеси и в последующем регулярно корректировать из условия обеспечения на месте укладки заданного содержания в смеси вовлеченного воздуха (с учетом его возможной потери при транспортировании смеси).
(3.06.04-91, приложение 6, п. 3)
5.56. Подбор и назначение состава бетонной смеси должна производить лаборатория (заводская, построечная или центральная ведомственная) перед началом производства изделий, при изменении проектных характеристик бетона, вида или поставщика цемента, заполнителей и технологических режимов производства.
5.57. Рабочий состав бетонной смеси контролируется результатами испытаний образцов, изготовленных из пробных замесов. Бетонную смесь, подобранную расчетно-теоретическим путем без опытной проверки испытанием образцов, применять запрещается. Подбор бетонной смеси следует производить руководствуясь действующими инструкциями и указаниями и оформлять карточкой подбора состава бетона и режима тепловлажностной обработки (приложение 44).
5.58. Корректировку рабочего состава бетона следует производить по данным операционного контроля свойств заполнителей (влажности, зернового состава, насыпной плотности) и бетонной смеси (удобоукладываемости, а для легкого бетона — средней плотности), контроля передаточной прочности для предварительно напряженных конструкций и напряжения для напрягаемого бетона, а также на основе статистической обработки фактических данных по прочности в соответствии с ГОСТ 18105.0-86.
(3.09.01-85, п. 4.3)
5.59. Введение в бетонную смесь добавок — ускорителей твердения бетона для сокращения сроков достижения бетоном требуемой прочности запрещается.
В бетонах с поташом в качестве противоморозного компонента в составе комплексной добавки количество добавки ЛСТ следует устанавливать в зависимости от количества вводимого поташа с обязательной проверкой в лаборатории указанного сочетания с конкретным цементом.
(3.06.04-91, приложение 6, п. 4)
5.60. Нормативные требования, которые следует выполнять при приготовлении бетонов и растворов и проверять при операционном контроле, а также объем и способы контроля приведены в табл. 14
Таблица 14
Технические требования | Контроль | Способ контроля |
1. Минимальный расход цемента, кг/м3 бетона, для конструкций, расположенных ниже глубины промерзания или возможного размыва дна — 230 | Всего объема укладываемого бетона | Измерительный (проверка работы дозаторов цемента и фактического выхода бетона) |
в подводной и надводной (подземной) частях сооружения — 260; в пределах переменного уровня воды или промерзания грунта — 290 | То же | То же |
в мостовом полотне — 290 | То же | То же |
2. Максимальный расход цемента, кг/м3 бетона, класса: до В35 включ. — 450 | Каждого объема укладываемого бетона | То же |
В40 — 500 | То же | То же |
В45 и выше — 550 | » | » |
3. Водоцементное отношение, весовых частей по массе, в бетонах, не более: подземной зоны — 0,65 | Каждого состава | Регистрационный |
подводной —»— — 0,60 | бетона | |
с добавками для повышения их морозостойкости: | ||
Марки по морозостойкости | ||
F100 F200 F300 | ||
В железобетонных — 0,5 0,45 и тонкостенных конструкциях толщиной менее 0,5 м | То же | То же |
В бетонных 0,60 0,55 0,47 массивных конструкциях | То же | То же |
В блоках облицовки — — 0,47 | То же | То же |
4. Объем вовлеченного воздуха в бетонных смесях на месте укладки для бетонов с нормированной морозостойкостью, % в бетонных и железобетонных конструкциях 2 — 4 в мостовом полотне 5 — 6 | Один раз в смену в условиях стабильного производства (при постоянных: составе бетона, качестве материалов, режиме приготовления и уплотнения бетонной смеси) и два раза в смену в других условиях | Проверка по ГОСТ 10181.3-81 |
5. Количество химических добавок, вводимых в бетонную смесь при ее приготовлении, % массы цемента: технических лигносульфонатов ЛСТ (сухого вещества) 0,1 — 0,2 | Не реже одного раза в смену | Операционный (проверка плотности рабочих растворов добавок и дозаторов при приготовлении бетонной смеси |
модифицированных технических лигносульфонатов ЛСТМ — 2 (сухого вещества) 0,10 — 0,25 | То же | То же |
суперпластификаторов С-3 (сухого вещества) 0,3 — 0,7 | То же | То же |
воздухововлекающих компонентов комплексных добавок СНВ, СДО, СВП, КТП, СПД (сухого вещества) 0,003 — 0,05 (уточняется при подборе состава бетона из условия обеспечения требуемого объема повлеченного воздуха) | Не реже одного раза в смену | Операционный (проверка плотности рабочих растворов добавок и дозаторов при приготовлении бетонной смеси |
кремнийорганической эмульсии КЭ-30-04 (50 %-ной концентрации) 0,4 кг/м3 бетона | То же | То же |
щелочного стока производства капролкатама ЩСПК (сухого вещества) до 0,3; | То же | То же |
мылонафта, асидола, асидол-мылонафта (товарного раствора) 0,02 — 0,05; | То же | То же |
ацетоно-формальдегидной смолы АЦФ-3 (сухого вещества) 0,1 — 0,2 | То же | То же |
противоморозных добавок: | ||
Протйвоморозиые добавки при расчетной температуре воздуха, °С | ||
До 5 От 6 От 11 От 16 От 21 до 10 до 15 до 20 до 25 | ||
Нитрита 5 7 9 — натрия | То же | То же |
Поташа 5 7 9 11 14 | ||
суперпластификатор С-3, вводимый совместно с нитритом натрия, 0,3-0,6 | То же | То же |
технические лигносульфонаты ЛСТ (ЛСТМ-2), вводимые в качестве замедлителя схватывания бетона совместно с поташом 0,3-1,2 | То же | То же |
(3.06.04-91, приложение 6, таблица)
5.61. При ожидаемой в период производства бетонных работ среднесуточной температуре наружного воздуха ниже 5°С и минимальной суточный температуре ниже 0°С, приготовление бетонной смеси следует производить в обогреваемых бетоносмесительных установках, применяя подогретую воду, оттаянные или подогретые заполнители, обеспечивающие получение бетонной смеси с температурой не ниже требуемой по расчету. Допускается применение неотогретых сухих заполнителей, не содержащих наледи на зернах и смерзшихся комьев. При этом продолжительность перемешивания бетонной смеси должна быть увеличена не менее, чем на 25 % по сравнению с летними условиями.
(3.03.01-87, п. 2.53 и 2.54)
5.62. Применяемые способы формования и удобоукладываемости бетонной смеси для различных изделий должна соответствовать операционной технологической карте, регламентирующей технологический процесс на всех этапах для конкретных условий производства. Удобоукладываемость бетонной смеси для каждого конкретного вида изделий должна быть уточнена при опытном бетонировании.
5.63. Поданная к месту укладки бетонная смесь должна иметь:
требуемую удобоукладываемость с отклонениями подвижности не более 30 % и жесткости не более 20 %;
температуру в пределах 5-30°С, если принятой технологией не предусмотрена более высокая температура смесей;
требуемый объем вовлеченного воздуха с отклонениями не более ±10 % от заданного для смесей с воздухововлекающими добавками.
(3.09.04-85, п. 4.15)
5.64. Время от выгрузки бетонной смеси из смесителя до формования изделий должно быть не более: для смесей тяжелого бетона — 45 мин.; для бетонных смесей для изготовления преднапряженных конструкций в силовых формах — 30 мин.; для смесей на цементах с малыми сроками схватывания и предварительно разогретых — 15 мин.
(3.09.01-85, п. 4.14)
Данные о бетонировании сборных железобетонных конструкций на полигонах мостостроительных подразделений должны фиксироваться в «Журнале бетонирования изделий или партии изделий» (приложение 45).
5.65. Перед бетонированием горизонтальные и наклонные бетонные поверхности рабочих швов должны быть очищены от мусора, грязи, масел, снега, льда, цементной пленки и др. Непосредственно перед укладкой бетонной смеси очищенные поверхности должны быть промыты водой и просушены струей воздуха.
(3.03.01-87, п. 2.8)
5.66. Бетонную смесь необходимо укладывать в соответствии с ППР. При этом бетонную смесь укладывают в форму или опалубку горизонтальными слоями без технологических разрывов, с направлением укладки в одну сторону во всех слоях. При значительных площадях поперечного сечения бетонируемой конструкции допускается укладывать и уплотнять бетонную смесь наклонными слоями, образуя горизонтальный опережающий участок длиной 1,5-2 м в каждом слое. Угол наклона к горизонту поверхности уложенного слоя бетонной смеси перед ее уплотнением не должен превышать 30°. После укладки и распределения бетонной смеси по всей площади укладываемого слоя уплотнение начинают с опережающего участка.
(3.06.04-91, п. 4.21)
5.67. При уплотнении бетонной смеси не допускается опирание вибраторов на арматуру и закладные изделия, тяжи и другие элементы крепления опалубки. Глубина погружения глубинного вибратора в бетонную смесь должна обеспечивать углубление его в ранее уложенный слой на 5-10 см. Шаг перестановки глубинных вибраторов не должен превышать полуторного радиуса их действия, поверхностных вибраторов — должен обеспечивать перекрытия на 100 мм площадкой вибратора границы уже провибрированного участка.
(3.03.01-87, п. 2.11)
5.68. Следующий слой бетонной смеси необходимо укладывать до начала схватывания бетона в предыдущем уложенном слое. Если перерыв в бетонировании превысил время начала схватывания бетона в уложенном слое (бетон потерял способность к тиксотропному разжижению при имеющихся средствах виброуплотнения), необходимо устроить рабочий шов. В этом случае бетон в уложенном слое должен быть выдержан до приобретения прочности, не менее указанной в таблице 15 (в зависимости от способа очистки от цементной пленки). Срок возобновления укладки бетона после перерыва определяется лабораторией.
Положение рабочих швов должно быть, как правило, указано в ППР. При отсутствии специального указания в проекте толщина слоя бетона уложенного после рабочего шва, должна быть не менее 25 см. Рабочие швы не следует располагать на участках переменного горизонта воды и на участках, омываемых агрессивной водой. (табл. 15).
(3.06.04-91, п. 4.25)
Таблица 15
Параметр | Величина параметра | Контроль (метод, объем, вид регистрации) |
1. Прочность поверхностей бетонных оснований при очистке от цементной пленки: | Не менее, МПа | Измерительный по ГОСТ 10180-78, |
водной и воздушной струей | 0,3 | ГОСТ 18105-86, |
Механической металлической щеткой | 1,5 | ГОСТ 22690-88, |
гидропескоструйной или механической фрезой | 5,0 | журнал работ |
(3.03.01-87, табл. 2)
5.69. Рабочие швы не допускается устраивать при бетонировании мостовых конструкций в местах, указанных в проектах в соответствии с требованиями СНиП 3.03.01-87, п. 2.13.
5.70. Бетонную смесь в каждом уложенном слое или на каждой позиции перестановки наконечника вибратора уплотняют до прекращения оседания и появления на поверхности и в местах соприкосновения с опалубкой блеска цементного теста.
(3.06.04-91, п. 4.26)
5.71. Виброрейки, вибробрусья или площадочные вибраторы могут быть использованы для уплотнения только бетонных конструкций; толщина каждого укладываемого и уплотняемого слоя бетонной смеси не должна превышать 25 см.
При бетонировании железобетонных конструкций поверхностное вибрирование может быть применено для уплотнения верхнего слоя бетона и отделки поверхности.
5.72. Бетонирование сборных конструкций на открытых площадках допускается при обеспечении условий, гарантирующих на каждом технологическом этапе приобретение бетоном заданной прочности по всему объему конструкции.
(3.06.04-91, приложение 7, п. 2)
5.73. Допускается укладывать и уплотнять бетонную смесь наклонными слоями на всю высоту поперечного сечения балки, если опалубка не оборудована виброподдоном.
(3.06.04-91, приложение 7, п. 3)
5.74. Блоки составных по длине конструкций коробчатого сечения (К) и плитноребристых конструкций (ПРК) неразрезных пролетных строений, типовых балочных пролетных строений и сборных опор мостов, монтируемых на клееных стыках, следует изготавливать в цельнометаллической или комбинированной опалубке, оборудованной гибкими вибросистемами, и бетонированием «в торец» с использованием в качестве торца опалубки ранее забетонированный блок. Торцевую поверхность бетона, сдвинутого в положение «отпечатка», покрывают перед бетонированием очередного блока специальной разделительной смазкой: раствором коалина, извести и других аналогичных материалов. Не допускается использовать смазки, имеющие в своем составе различные виды масел. Бетонную смесь при бетонировании блоков пролетных строений следует уплотнять виброподдоном и вибролистами боковых щитов и внутренней части опалубки, включая группы вибраторов, соответствующие зоне укладки бетонной смеси.
5.75. Технологические требования, которые следует выполнять при производстве бетонных работ и проверять при операционном контроле, а также объем, методы или способы контроля приведены в табл. 16.
Таблица 16
Технические требования | Контроль | Метод и способ контроля |
1. На месте приготовления и укладки подвижность смеси не должна отличаться от заданной более чем на 15 %, а жесткость более чем на 20 | Не менее, чем 2 раза в смену, а при неустойчивой погоде, нестабильной влажности и колебаниях зернового состава заполнителей — через каждые 2 ч. | Проверка по ГОСТ 10181.1-81 с регистрацией в журнале |
2. Температуры составляющих и бетонной смеси не должны отличаться от расчетной белее, чем на 2°С (воды и заполнителей при загрузке в смеситель бетонной (растворной) смеси — на выходе из смесителя, бетонной (растворной) смеси — на месте укладки. | Через каждые 4 ч в зимнее время, 2 раза в смену — при положительных температурах воздуха — только бетонной смеси | Регистрационный, измерительный |
3. Толщина укладываемого слоя бетонной смеси не должна превышать: 40 см — при уплотнении на виброплощадках, виброподдонах или гибкими вибросистемами | Постоянный в процессе укладки бетона | Измерительный, визуальный |
25 см — то же, при бетонировании конструкции сложной конфигурации и густоармированных | То же | То же |
на 5-10 см длины рабочей части вибратора при уплотнении тяжелыми подвесными вертикально расположенными вибраторами | » | » |
вертикальной проекции длины рабочей части вибратора при уплотнении тяжелыми подвесными вибраторами, располагаемыми под углом 35° к вертикали | » | » |
1,25 длины вибронаконечника и 40 см — при уплотнении ручными глубинными вибраторами | » | » |
25 см — при уплотнении поверхностными вибраторами или вибробрусками в неармированных конструкциях и с одиночной арматурой | » | » |
12 см — в конструкциях с двойной арматурой | » | » |
4. При разделении конструкции на блоки бетонирования следует предусматривать: площадь каждого блока — не менее 50 м2 | Каждой конструкции | Измерительный, регистрационный |
высоту блока не менее 2 м | То же | То же |
расположение рабочих швов блоков в перевязку | » | » |
5. Высоту свободного сбрасывания бетонной смеси следует принимать не более, м: 2 — при бетонировании армированных конструкций | Постоянный | Измерительный, визуальный |
1 — при изготовлении сборных железобетонных конструкций | То же | То же |
6 — при бетонировании неармированных конструкций, устанавливаемых из условия обеспечения и однородности бетона и сохранности опалубки | » | » |
6. Объем вовлеченного воздуха в бетонную смесь, принятый при подборе состава бетона ± 1 % по абсолютной величине | По ГОСТ 7473-85* | Проверка по ГОСТ 10181.3-81 |
7. Прочность бетона в партии (отпускная, передаточная, в промежуточном или в проектном возрасте) — не менее требуемой, определяемой по ГОСТ 18105-86* | Партия бетона по ГОСТ 18105-86* | Проверка по образцам по ГОСТ 10180-90 и неразрушающими методами в соответствии с ГОСТ 18105-86*, за исключением прочности бетона в проектном возрасте |
8. Объем партии бетона для сборных бетонных, железобетонных и монолитных конструкций принимать по п. 2.1 ГОСТ 18105-86*, но не более объема бетона конструкций, отформованных в течение одних суток, если этот объем превышает 10 м3 в одну смену или 40 м3— в одну неделю | То же | Регистрационный |
9. Объем партии бетона для сборных предварительно напряженных конструкций следует принимать по п. 2.1 ГОСТ 18105-86*, но не более объема бетона конструкций, отформованных в течении одних суток | » | То же |
10. Объем партии бетона для омоноличивания следует принимать по п. 2.1 ГОСТ 18105-86* | » | » |
11. Нормы отбора проб бетонной смеси для одной партии бетона необходимо принимать по ГОСТ 18105-86*, но не менее одной пробы: для каждого блока пролетного строения, изготавливаемого в отдельной опалубке и для каждых 25 м3 бетона сборных конструкций | » | » |
для каждых 250 м3 бетона и каждого конструктивного элемента бетонных конструкций | » | » |
для каждых 50 м3 бетона и каждого конструктивного элемента монолитных железобетонных конструкций | » | » |
для каждых 50 м3 подводного бетона и объема бетона, уложенного в одну оболочку под фундамент отдельной опоры | » | » |
12. Нормы контроля конструкций при неразрушающем методе контроля прочности следует принимать по ГОСТ 18105-86*, для сборных конструкций — не менее одной конструкции от каждых 25 м3 объема в партии и каждый блок пролетного строения, изготовленный в отдельной опалубке | Партии конструкций | » |
13. Число серий образцов, изготовленных из одной пробы бетонной смеси, следует принимать по п. 2.3 ГОСТ 18105-86* при обязательном изготовлении серии образцов для определения прочности сборных конструкций в проектном возрасте | Пробы бетонной смеси | » |
14. Число участков сборных и монолитных конструкции, контролируемых неразрушающими методами, следует принимать по п. 2.6 ГОСТ 18105-86* | Каждой конструкции | Регистрационный |
15. Прочность раствора принимать по проектной документации | По ГОСТ 5802-86 | Проверка по ГОСТ 5802-86 |
Водонепроницавморть бетона принимать по проектной документации (п.п. 1-5 СНиП 3.06.04-91 табл. 4, п.п. 6-15 СНиП 3.06.04-91 табл. 9 п.п. 2-11) | По ГОСТ 12730.5-84* | Проверка по ГОСТ 12730.5-84* |