MirMarine — Фреоновые холодильные установки
Компрессионные холодильные установки, работающие на фреоне-12 широко распространены в системах охлаждения судовых провизионных камер и кондиционирования воздуха.
На рис. 128, б приведена принципиальная схема фреоновой автоматизированной холодильной установки, обслуживающей две провизионные камеры с различными температурами. Парожидкостная смесь поступает в испарительные батареи, где кипит за счет тепла воздуха камер и хранящихся в них продуктов питания, охлаждая их. Образовавшиеся в батареях испарителя пары хладагента отсасываются компрессором, сжимаются и нагнетаются в конденсатор. В конденсаторе происходит сжижение (конденсация) паров хладагента путем отвода тепла забортной водой, проходящей по трубам.
Компрессор необходим для понижения давления в испарительных батареях, получения низкой температуры кипения хладагента и создания повышенного давления нагнетания, при котором возможен переход фреона из компрессора в конденсатор.
Из конденсатора жидкий фреон, пройдя теплообменник, фильтросушитель и соленоидный вентиль, поступает в терморегулирующий вентиль, который регулирует количество фреона, идущего в батареи испарителя. В ТРВ происходит дросселирование жидкого фреона, давление его снижается от давления конденсации 4—8 ати до давления кипения 0,3—1 ати. Таким образом, терморегулирующий вентиль разделяет систему хладагента на сторону высокого давления (конденсации)—от нагнетательной полости компрессора до ТРВ и сторону низкого давления (давления всасывания или кипения)—от ТРВ до всасывающей полости компрессора.
Компрессоры фреоновых холодильных установок по конструкции могут быть с вертикальным, V- и W-образным расположением цилиндров. Они делятся на прямоточные и непрямоточные по направлению движения паров холодильного агента в цилиндре.
В малых холодильных установках в основном применяются непрямоточные простого действия компрессоры, в которых всасывающие и нагнетательные клапаны расположены в одной плите, помещенной на торце цилиндрического блока.
В прямоточных компрессорах всасывание происходит через поршень и клапан, встроенный в его головке. При этом направление движения пара хладагентов в цилиндре не изменяется, т. е. он совершает прямой ток. Это увеличивает производительность компрессора за счет уменьшения теплообмена между стенками цилиндра и паром хладагента.
Фреоновые компрессоры выполняются без охлаждающей рубашки, так как температура паров фреона в конце сжатия незначительна. Охлаждение цилиндров производится воздухом и для этого на наружной поверхности блока делают ребра.
Компрессор ФВ-4. На рис. 129, а показан отечественный фреоновый компрессор марки ФВ-4, выпускаемый Одесским заводом холодильных машин. Компрессор двухцилиндровый, вертикальный, простого действия, непрямоточный, холодо-производительностью 4000 ккал/ч. Число оборотов вала в минуту 850, диаметр поршня 67,5 мм и ход поршня 50 мм.
Шатуны стальные штампованные, двухтаврового профиля. Поршень алюминиевый с двумя уплотнительными и одним маслосбрасывающим кольцами. Смазка механизма движения и цилиндров производится разбрызгиванием.
Всасывающие и нагнетательные клапаны пластинчатые, полосовые самопружинящие и расположены на общей плите, помещенной на торце цилиндрового блока. На клапанную плиту опирается крышка блока (общая для двух цилиндров), имеющая перегородку для разделения полостей всасывания и нагнетания.
Уплотнение коленчатого вала в месте выхода из картера производится сильфонным сальником. Препятствие для выхода фреона из картера создают сильфон (гофрированная латунная трубка), прокладка и притертые поверхности уплотнительных колец.
Компрессор ФВ-12. Компрессор фреоновый вертикальный двухцилиндровый прямоточный марки ФВ-12, холодопро-изводительностью при наибольшем числе оборотов 12 000 ккал/ч (рис. 130). Он рассчитан на работу при трех различных числах оборотов в минуту — 480, 720 и 960, соответственно которым холодопроизводительность равна 7000, 10000 и 12 000 ккал/ч.
Цилиндры и картер компрессора представляют единую чугунную отливку с запрессованными цилиндровыми втулками. Охлаждение цилиндров воздушное. Для лучшего теплообмена крышка цилиндров и в верхней части цилиндровый блок компрессора имеют ребра.
Вал компрессора стальной, двухопорный, двухколенный (колена под углом 180°) с двумя противовесами, опирается на два шариковых подшипника.
Поршни чугунные с тремя уплотнительными и одним масло-съемным кольцами.
Шатуны стальные, облегченные, двутаврового сечения с разъемной нижней и неразъемной верхней головками. Нижние головки залиты баббитом, в верхние запрессованы биметаллические втулки.
Всасывающие и нагнетательные клапаны самодействующие. Всасывающие ленточного типа установлены на днище поршня, а нагнетательные с пластинками и пружинами смонтированы на клапанной доске, укрепленной на верхней плоскости блока.
Сальник компрессора двухмембранный с масляным затвором и металлическими кольцами трения. Он состоит из подвижных частей (стопорный фланец, подвижное кольцо), вращающихся вместе с коленчатым валом, и неподвижных частей (упругих диафрагм с упорным кольцом и обоймой). Неподвижные части закрепляются с помощью буксы и крышки на переднем фланце блоккартера с уплотнением прокладками. Уплотнение достигается за счет упругости диафрагм и взаимно-притертых неподвижного кольца и обоймы с внешним ободом подвижного кольца.
Масло в сальник при работе компрессора поступает непрерывно и избыток его сливается из бачка в картер.
Смазка компрессора принудительная от шестеренчатого насоса, расположенного в задней крышке и приводимого в движение коленчатым валом через поводок. Масло подается в двух направлениях: в сверление коленчатого вала и полость сальника. В месте забора масла из картера установлен сетчатый фильтр. По сверлениям коленчатого вала масло подается для смазки мотылевых и по трубке вдоль шатуна — головных подшипников.
В случае прекращения подачи масла полость сальника остается наполненной благодаря обратному клапану и этим сохраняется плотность сальника при остановках машины. Для контроля работы масляного насоса на его корпусе установлен манометр.
Похожие статьи
Описание принципа работы холодильной установки
Обычному человеку, как правило, нет необходимости разбираться в принципе действия холодильной машины, для него важен результат. Результатом работы холодильной установки является: охлажденные продукты – от замороженных овощей, до мясо-молочной продукции или например охлажденный воздух, если речь идет о сплит-системах.
Другое же дело, когда холодильные машины выходит из строя и для проведения ремонта холодильных установок требуется вызов специалиста. В данном случае уже было бы не плохо разбираться в принципе работы таких агрегатов. Хотя бы для того, чтобы понимать необходимость замены или ремонта составляющей холодильной машины.
Основное назначение холодильной установки – это забор тепла от охлаждаемого тела и перенос этого тепла или энергии другому объекту или телу. Для понимания процесса требуется уяснить простую вещь – если мы нагреваем или сжимаем тело, то мы сообщаем этому телу энергию (или тепло), охлаждая и расширяя, мы отбираем энергию. Это основной принцип, на основе которого и построен перенос тепла.
В холодильной машине для переноса тепла применяются хладагенты – рабочие вещества холодильной машины, которые при кипении и в процессе изотермического расширения отнимают теплоту от охлаждаемого объекта и затем после сжатия передают её охлаждающей среде за счёт конденсации
Холодильный компрессор 1 отсасывает газообразный хладагент – фреон из испарителей 3, сжимает его и нагнетает в конденсатор 2. В конденсаторе 2 фреон конденсируется и переходит в жидкое состояние. Из конденсатора 2 жидкий хладагент попадает в ресивер 4, где происходит его накопление. Ресивер оснащен запорными вентилями 19 на входе и выходе. Из ресивера хладагент поступает в фильтр-осушитель 9, где происходит удаление остатков влаги, примесей и загрязнений, после этого проходит через смотровое стекло с индикатором влажности 12, соленоидный вентиль 7 и дросселируется терморегулирующим вентилем 17 в испаритель 3.
В испарителе хладагент кипит, забирая тепло от объекта охлаждения. Пары хладагента из испарителя через фильтр на всасывающей магистрали 11, где они отчищаются от загрязнений, и отделитель жидкости 5 поступают в компрессор 1. Затем цикл работы холодильной установки повторяется.
Отделитель жидкости 5 предотвращает попадание жидкого хладагента в компрессор. Для обеспечения гарантированного возврата масла в картер компрессора, на выходе из компрессора устанавливаться маслоотделитель 6. При этом масло через запорный вентиль 24, фильтр 10 и смотровое стекло 13 по линии возврата – поступает в компрессор.
Виброизоляторы 25, 26 на всасывающей и нагнетательной магистралях гасят вибрации при работе компрессора и препятствуют их распространению по холодильному контуру.
Компрессор оснащён картерным нагревателем 21 и двумя запорными вентилями 20. Картерный нагреватель 21 выпаривает хладагент из масла, предотвращая конденсацию хладагента в картере компрессора во время его стоянки и поддержания заданной температуры масла.
В холодильных машинах с полугерметичными поршневыми компрессорами, у которых в системе смазки установлен масляный насос, используется реле контроля давления масла 18. Задача этого реле – отключить компрессор в случае снижения давления масла в системе смазки.
В случае установки агрегата на улице он должен быть дополнительно укомплектован гидравлическим регулятором давления конденсации, для обеспечения стабильной работы в зимних условиях и поддержания необходимого давления конденсации в холодное время года.
Реле высокого давления 14 управляют включением/выключением вентиляторов конденсатора, для поддержания необходимого давления. Реле низкого давления 15 управляет включением/выключением компрессора.
Аварийное реле высокого и низкого давлений 16 предназначено для аварийного отключения компрессора в случае пониженного или повышенного давления.
Знакомство c устройством и работой холодильных установок
Сегодня в охлаждении нуждается огромное количество продуктов, а еще без холода невозможно реализовать многие технологические процессы. То есть с необходимостью применения холодильных установок мы сталкиваемся в быту, в торговле, на производстве. Далеко не всегда удается использовать естественное охлаждение, ведь оно сможет понизить температуру лишь до параметров окружающего воздуха.
На выручку приходят холодильные установки. Их действие основано на реализации несложных физических процессов испарения и конденсации. К преимуществам машинного охлаждения относится поддержание в автоматическом порядке постоянных низких температур, оптимальных для определенного вида продукта. Также немаловажными являются незначительные удельные эксплуатационные, ремонтные затраты и расходы на своевременное техническое обслуживание.
Как работает холодильная машина
Для получения холода используется свойство холодильного агента корректировать собственную температуру кипения при изменении давления. Чтобы превратить жидкость в пар, к ней подводится определенное количество теплоты. Аналогично конденсация парообразной среды наблюдается при отборе тепла. На этих простых правилах и основывается принцип работы холодильной установки.
Это оборудование включает в себя четыре узла:- компрессор
- конденсатор
- терморегулирующий вентиль
- испаритель
Между собой все эти узлы соединяются в замкнутый технологический цикл при помощи трубопроводной обвязки. По этому контуру подается холодильный агент. Это вещество, наделенное способностью кипеть при низких отрицательных температурах. Этот параметр зависит от давления парообразного хладагента в трубках испарителя. Более низкое давление соответствует низкой температуре кипения. Процесс парообразования будет сопровождаться отнятием тепла от той окружающей среды, в которую помещено теплообменное оборудование, что сопровождается ее охлаждением.
При кипении образуются пары хладагента. Они поступают на линию всасывания компрессора, сжимаются им и поступают в теплообменник-конденсатор. Степень сжатия зависит от температуры конденсации. В данном технологическом процессе наблюдается повышение температуры и давления рабочего продукта. Компрессором создают такие выходные параметры, при которых становится возможным переход пара в жидкую среду. Существуют специальные таблицы и диаграммы для определения давления, соответствующего определенной температуре. Это относится к процессу кипения и конденсации паров рабочей среды.
Конденсатор – это теплообменник, в котором горячие пары хладагента охлаждаются до температуры конденсации и переходят из пара в жидкость. Это происходит путем отбора от теплообменника тепла окружающим воздухом. Процесс реализуется при помощи естественной или же искусственной вентиляции. Второй вариант зачастую применяется в промышленных холодильных машинах.
После конденсатора жидкая рабочая среда поступает в терморегулирующий вентиль (дроссель). При его срабатывании давление и температура понижается рабочих параметров испарителя. Технологический процесс вновь идет по кругу. Чтобы получить холод необходимо подобрать температуру кипения хладагента, ниже параметров охлаждаемой среды.
На рисунке представлена схема простейшей установки, рассмотрев которую можно наглядно представить принцип работы холодильной машины. Из обозначений:- «И» — испаритель
- «К» -компрессор
- «КС» — конденсатор
- «Д» — дроссельный вентиль
Стрелочками указано направление технологического процесса.
Помимо перечисленных основных узлов, холодильная машина оснащается приборами автоматики, фильтрами, осушителями и иными устройствами. Благодаря им установка максимально автоматизируется, обеспечивая эффективную работу с минимальным контролем со стороны человека.
В качестве холодильного агента сегодня в основном используются различные фреоны. Часть из них постепенно выводится из употребления ввиду негативного воздействия на окружающую среду. Доказано, что некоторые фреоны разрушают озоновый слой. Им на смену пришли новые, безопасные продукты, такие как R134а, R417а и пропан. Аммиак применяется лишь в масштабных промышленных установках.
Теоретический и реальный цикл холодильной установки
На этом рисунке представлен теоретический цикл простейшей холодильной установки. Видно, что в испарителе происходит не только непосредственно испарение, но и перегрев пара. А в конденсаторе пар превращается в жидкость и несколько переохлаждается. Это необходимо в целях повышения энергоэффективности технологического процесса.Левая часть кривой – это жидкость в состоянии насыщения, а правая – насыщенный пар. То, что между ними – паро-жидкостная смесь. На линии D-A` происходит изменение теплосодержания холодильного агента, сопровождающееся выделением тепла. А вот отрезок В-С` наоборот, указывает на выделение холода в процессе кипения рабочей среды в трубках испарителя.
Реальный рабочий цикл отличается от теоретического ввиду наличия потерь давления на трубопроводной обвязке компрессора, а также на его клапанах.
Чтобы компенсировать данные потери работа сжатия должна быть увеличена, что снизит эффективности цикла. Данный параметр определяется отношением холодильной мощности, выделяемой в испарителе к мощности, потребляемой компрессором и электрической сети. Эффективность работы установки – это сравнительный параметр. Он не указывает непосредственно на производительность холодильника. Если данный параметр 3,3, это будет указывать, что на единицу электроэнергии, потребляемой установкой, приходится 3,3 единицы произведенного ею холода. Чем больше этот показатель, тем выше эффективность установки.
Устройство холодильной машины | Техническая библиотека ПромВентХолод
Охлаждение различных объектов – продуктов питания, воды, других жидкостей, воздуха, технических газов и др. до температур ниже температуры окружающей среды происходит с помощью холодильных машин различных типов. Холодильная машина по большому счету не производит холод, она является лишь своеобразным насосом, который переносит теплоту от менее нагретых тел к более нагретым. Основан же процесс охлаждения на постоянном повторении т.н. обратного термодинамического или другими словами холодильного цикла. В самом распространенном парокомпрессионном холодильном цикле перенос теплоты происходит при фазовых превращениях хладагента – его испарении (кипении) и конденсации за счет потребления подведенной извне энергии.
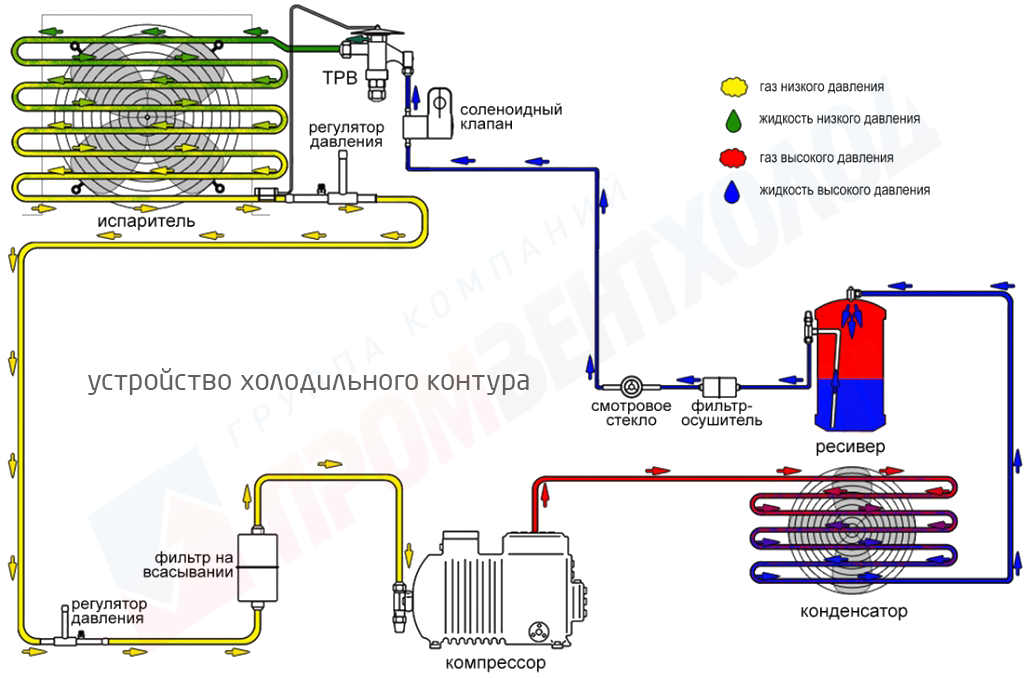
Основными элементами холодильной машины, с помощью которых реализуется ее рабочий цикл, являются:
- компрессор – элемент холодильного цикла, обеспечивающий повышение давления хладагента и его циркуляцию в контуре холодильной машины;
- дросселирующее устройство (капиллярная трубка, терморегулирующий вентиль) служит регулирования количества хладагента, попадающего в испаритель в зависимости от перегрева на испарителе.
- испаритель (охладитель) – теплообменник, в котором происходит кипение хладагента (с поглощением тепла) и непосредственно сам процесс охлаждения;
- конденсатор – теплообменник, в котором в результате фазового перехода хладагента из газообразного состояния в жидкое, отведенная теплота сбрасывается в окружающую среду.

При этом необходимо наличие в холодильной машине других вспомогательных элементов, – электромагнитные (соленоидные) вентили, контрольно-измерительные приборы, смотровые стекла, фильтры-осушители и т.д. Все элементы соединены между собой в герметичный внутренний контур с помощью трубопроводов с теплоизоляцией. Контур холодильной машины заполняется хладагентом в необходимом количестве. Основной энергетической характеристикой холодильной машины является холодильный коэффициент, который определяется отношением количества тепла, отведенного от охлаждаемого источника, к затраченной энергии.
Холодильные машины в зависимости от принципов работы и применяемого хладагента бывают нескольких типов. Наиболее распространенные парокомпрессионные, пароэжекторные, абсорбционные, воздушные и термоэлектрические.
Хладагент
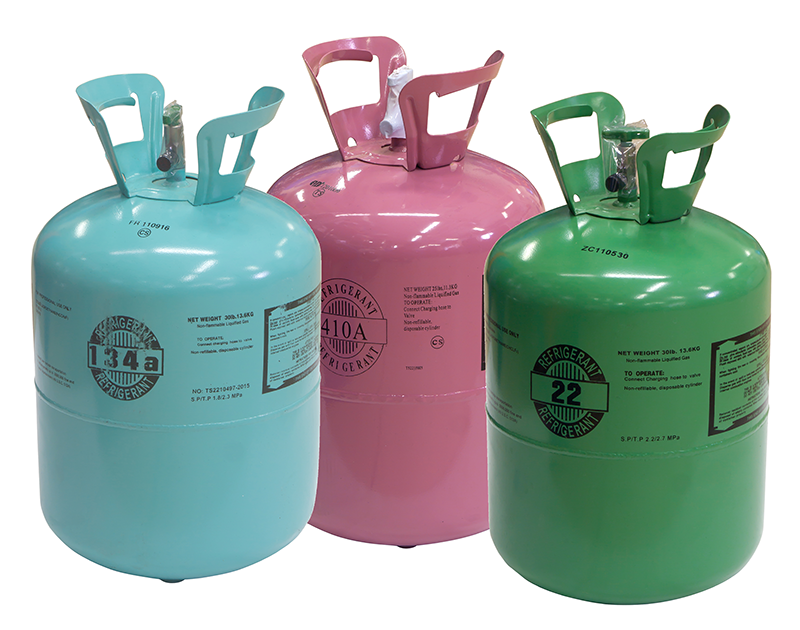
Хладагент – рабочее вещество холодильного цикла, основной характеристикой которого является низкая температура кипения. В качестве хладагентов чаще всего применяют различные углеводородные соединения, которые могут содержать атомы хлора, фтора или брома. Также хладагентом могут быть аммиак, углекислый газ, пропан и т.д. Реже в качестве хладагента применяют воздух. Всего известно около сотни типов хладагентов, но изготавливается промышленным способом и широко применяется в холодильной, криогенной технике, кондиционировании воздуха и других отраслях всего около 40. Это R12, R22, R134A, R407C, R404A, R410A, R717, R507 и другие. Основная область применения хладагентов – это холодильная и химическая промышленность. Кроме того, некоторые фреоны используют в качестве пропеллентов при производстве различной продукции в аэрозольной упаковке; вспенивателей при производстве полиуретановых и теплоизолирующих изделий; растворителей; а также в качестве веществ, тормозящих реакцию горения, для систем пожаротушения различных объектов повышенной опасности – тепловых и атомных электростанций, гражданских морских судов, боевых кораблей и подводных лодок.
Терморегулирующий вентиль (ТРВ)
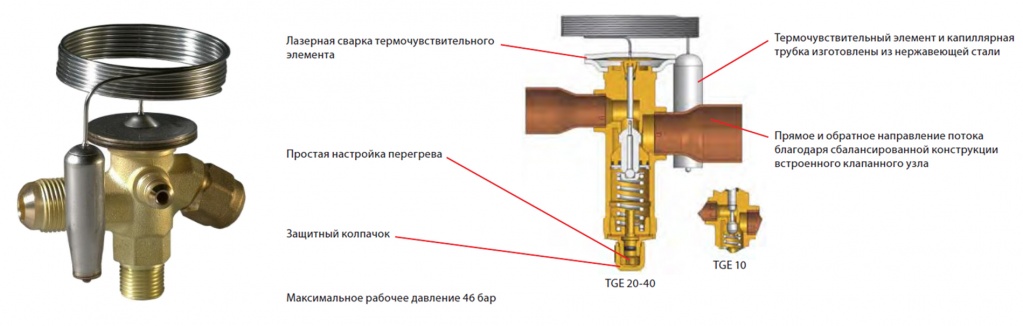
Терморегулирующий вентиль (ТРВ) – один из основных компонентов холодильных машин, известен как наиболее распространенный элемент для дросселирования и точного регулирования подачи хладагента в испаритель. ТРВ использует в качестве регулятора расхода хладагента клапан игольчатого типа, примыкающий к основанию тарельчатой формы. Количество и расход хладагента определяется проходным сечением ТРВ и зависит от температуры на выходе из испарителя. При изменении температуры хладагента на выходе из испарителя, давление внутри этой системы меняется. При изменении давления меняется проходное сечение ТРВ и, соответственно, меняется расход хладагента.
Термосистема заполнена на заводе-изготовителе точно определенным количеством того же хладагента, который является рабочим веществом данной холодильной машины. Задача ТРВ – дросселирование и регулирование расхода хладагента на входе в испаритель таким образом, чтобы в нем наиболее эффективно проходил процесс охлаждения. При этом хладагент должен полностью перейти в парообразное состояние. Это необходимо для надежной работы компрессора и исключения его работы т.н. «влажным» ходом (т.е. сжатие жидкости). Термобаллон крепится на трубопровод между испарителем и компрессором, причем в месте крепления необходимо обеспечить надежный термический контакт и теплоизоляцию от воздействия температуры окружающей среды. Последние 15-20 лет в холодильной технике стали получать широкое распространение электронные ТРВ. Они отличаются тем, что у них отсутствует выносная термосистема, а ее роль играет терморезистор, закрепленный на трубопроводе за испарителем, связанный кабелем с микропроцессорным контролером, который в свою очередь управляет электронным ТРВ и вообще всеми рабочими процессами холодильной машины.
Соленоидный вентиль
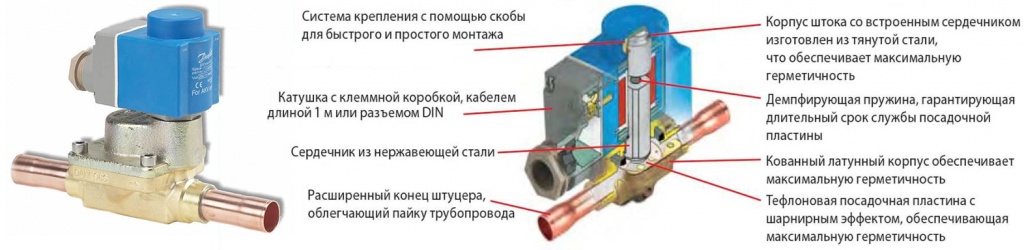
Соленоидный вентиль служит для двухпозиционного регулирования («открыто-закрыто») подачи хладагента в испаритель холодильной машины либо для открытия-закрытия от внешнего сигнала определенных участков трубопроводов. При отсутствии питания на катушке тарелка клапана под воздействием специальной пружины удерживает соленоидный вентиль закрытым. При подаче питания сердечник электромагнита, соединенный штоком с тарелкой, преодолевает усилие пружины, втягивается в катушку, тем самым приподнимая тарелку и открывая проходное сечение вентиля для подачи хладагента.
Смотровое стекло
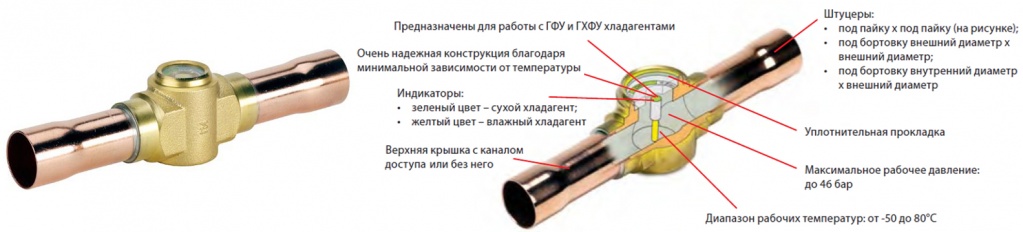
Смотровое стекло в холодильной машине предназначено для определения:
- состояния хладагента;
- наличие влаги в хладагенте, которое определяется цветом индикатора.

Смотровое стекло обычно монтируют в трубопроводе на выходе из накопительного ресивера. Конструктивно смотровое стекло представляет собой металлический герметичный корпус с окном из прозрачного стекла. Если при работе холодильной машины в окне наблюдается поток жидкости с отдельными пузырями парообразного хладагента, то это может свидетельствовать о недостаточной заправке или других неисправностях в ее функционировании. Может устанавливаться и второе смотровое стекло на другом конце указанного выше трубопровода, в непосредственной близости от регулятора расхода, которым может быть соленоидный вентиль, ТРВ или капиллярная трубка. Цвет индикатора показывает наличие или отсутствие влаги в холодильном контуре.
Фильтр-осушитель
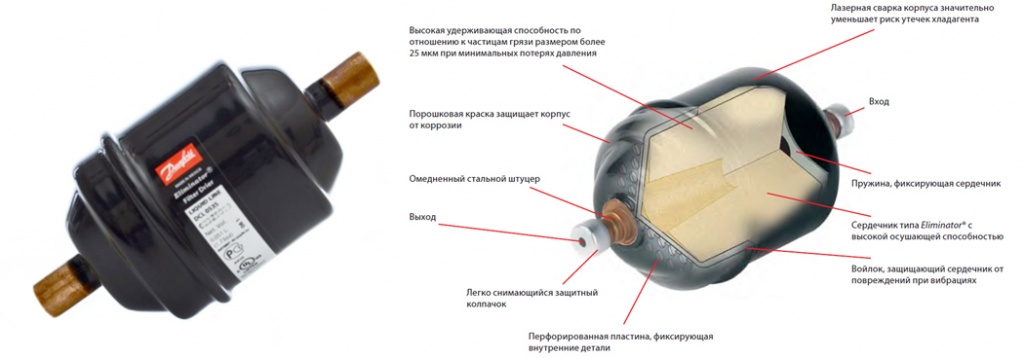
Фильтр-осушитель или цеолитовый патрон еще один важный элемент контура холодильных машин. Он необходим для удаления влаги и механических загрязнений из хладагента, тем самым защищая от засорения ТРВ. Обычно он монтируется с помощью паяных или штуцерных соединений непосредственно в трубопровод между конденсатором и ТРВ (соленоидным вентилем, капиллярной трубкой). Чаще всего конструктивно представляет собой отрезок медной трубы диаметром 16…30 и длиной 90…170 мм, закатанный с обеих сторон и с присоединительными патрубками. Внутри по краям установлены две металлические фильтрующие сетки, между которыми расположен гранулированный (1,5…3,0 мм) адсорбент, обычно это синтетический цеолит. Это т.н. разовый фильтр-осушитель, но существуют многоразовые конструкции фильтров с разборным корпусом и резьбовыми трубопроводными соединениями, требующими только время от времени замены внутреннего цеолитового картриджа. Замена разового фильтра- осушителя или картриджа необходима после каждого вскрытия внутреннего контура холодильной машины. Существуют одно-направленные фильтры, предназначенные для работы в системах «только холод» и дву-направленные, используемые в агрегатах «тепло-холод».
Ресивер
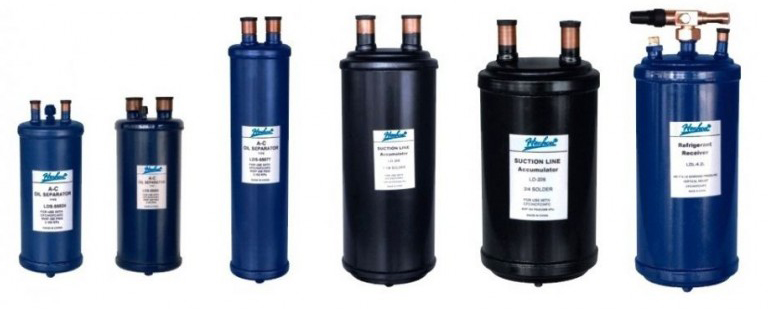
Ресивер – герметичный цилиндрический накопительный бак различной емкости, изготовленный из стального листа, и служащий для сбора жидкого хладагента и его равномерной подачи к регулятору расхода (ТРВ, капиллярная трубка) и в испаритель. Существуют ресиверы как вертикального, так и горизонтального типа. Различают линейные, дренажные, циркуляционные и защитные ресиверы. Линейный ресивер устанавливается с помощью паяных соединений в трубопровод между конденсатором и ТРВ и выполняет следующие функции:
- обеспечивает непрерывную и бесперебойную работу холодильной машины при различных тепловых нагрузках;
- является гидравлическим затвором, препятствующим попаданию пара хладагента в ТРВ;
- выполняет функцию масло- и воздухоотделителя;
- освобождает трубы конденсатора от жидкого хладагента.
Дренажные ресиверы служат для сбора и хранение всего количества заправленного хладагента на время ремонтных и сервисных работ, связанных с разгерметизацией внутреннего контура холодильной машины.
Циркуляционные ресиверы применяют в насосно-циркуляционных схемах подачи жидкого хладагента в испаритель для обеспечения непрерывной работы насоса и монтируют в трубопровод после испарителя в точку с самой низкой отметкой по высоте для свободного слива в него жидкости.
Защитные ресиверы предназначены для безнасосных схем подачи фреона в испаритель, их устанавливают совместно с отделителями жидкости во всасывающий трубопровод между испарителем и компрессором. Они служат для защиты компрессора от возможной работы «влажным» ходом.
Регулятор давления
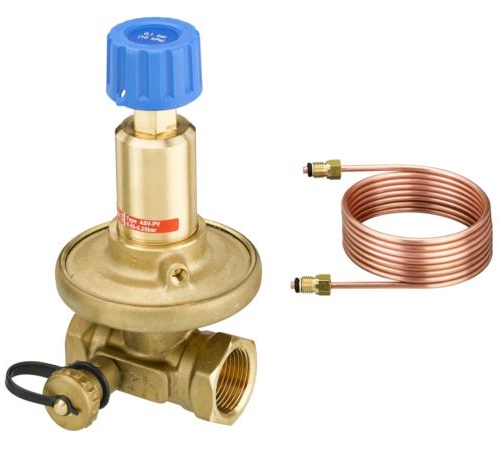
Регулятор давления – автоматически управляемый регулирующий клапан, применяемый для снижения либо поддержания давления хладагента путем изменения гидравлического сопротивления потоку проходящего через него жидкого хладагента. Конструктивно состоит из трех основных элементов: регулирующего клапана, его исполнительного механизма и измерительного элемента. Исполнительный механизм непосредственно воздействует на тарелку клапана, изменяя или закрывая проходное сечение. Измерительный элемент сравнивает текущее и заданное значение давления хладагента и формирует управляющий сигнал для исполнительного механизма регулирующего клапана. В холодильной технике существуют регуляторы низкого давления, чаще называемые прессостатами. Они управляют давлением кипения в испарителе, их устанавливают во всасывающий трубопровод за испарителем. Регуляторы высокого давления называют маноконтроллерами. Их чаще всего применяют в холодильных машинах с воздушным охлаждением конденсатора для поддержания минимально необходимого давления конденсации при понижении температуры наружного воздуха в переходный и холодный период года, обеспечивая тем самым т.н. зимнее регулирование. Маноконтроллер устанавливают в нагнетательный трубопровод между компрессором и конденсатором.

Специалисты рекомендуют
Вернуться
Особенности эксплуатации фреоновых холодильных установок
При эксплуатации установок, работающих на R12 и R22, необходимо учитывать их специфические свойства. Фреоны обладают большой текучестью и способностью проникать через малейшие неплотности. Поэтому обслуживающий персонал должен внимательно следить за герметичностью системы и своевременно выявлять и устранять утечки фреона. Места утечек хладона можно обнаружить галоидными лампами, мыльной пеной, а также по масляным подтекам. Пары фреона хорошо растворяются в смазочном масле, масло циркулирует в системе вместе с холодильным агентом и непрерывно возвращается в картер компрессора.
Особенностью фреоновой холодильной установки является также то, что при малых перегревах всасываемого пара холодопроизводительность компрессора резко понижается, а удельный расход электроэнергии возрастает.
Попадание влаги в систему, заполненную фреоном и смазочным маслом, при действии высоких температур в компрессоре приводит к образованию минеральных и органических кислот, которые разрушающе действуют на детали компрессора, в первую очередь на электрическую изоляцию встроенного электродвигателя. Вода, попавшая в систему, не растворяется во фреоне и при низких температурах замерзает в терморегулирующем вентиле или капиллярной трубке. Кроме того, нарушается нормальная циркуляция масла. Масло скапливается в испарителях и конденсаторе. Компрессор, оставаясь без масла, может выйти из строя.
При эксплуатации фреоновых установок следят за тем, чтобы вода не попала в систему. Наличие влаги в системе можно определить с помощью индикатора влажности. Изменение окраски индикатора зависит от содержания воды во фреоне (табл. ).
Из установки вода удаляется через фильтры-осушители, заполняемые силикагелем марки ШСМ (ГОСТ 3956—54), цеолитом (ВТУ МРТУ 6-01-567—63) или цеолитом марки NaA-2KT.
Таблица
Практикующийся иногда метод использования спирта для устранения замерзания дроссельных устройств во фреоновых установках является нежелательным из-за образования кислот.
Глава 23. Основные отклоненияот оптимального режима в работе холодильных установок и способы их устранения
Отклонения от оптимального режима работы холодильной установки приводят к ухудшению качества продуктов, снижению холодопроизводительности, увеличению эксплуатационных затрат, а при определенных условиях к аварии.
Сравнивая рабочие параметры работы холодильной установки с их оптимальными, выявляют отклонения от оптимального режима.
Наиболее частыми отклонениями, влияющими на экономичность и безопасность работы холодильной установки, являются пониженная температура кипения холодильного агента в испарительной системе, повышенная температура конденсации пара в конденсаторе, повышенная или чрезмерно высокая температура пара на нагнетательной стороне компрессора, работа компрессора влажным ходом.
Пониженная температура в испарительной системе. Основными причинами низкой температуры кипения являются несоответствие холодопроизводительности включенных компрессоров тепловой нагрузке, снижение коэффициента теплопередачи в теплобменных аппаратах и недостаточное поступление жидкого холодильного агента в испарительную систему.
Работа холодильной установки с пониженной температурой кипения может привести к замерзанию хладоносителя в испарителе при рассольной системе охлаждения, подмораживанию охлаждаемых продуктов при непосредственной системе охлаждения, увеличению усушки продуктов и ухудшению смазки фреоновых компрессоров.
Одной из причин пониженной температуры кипения при эксплуатации рассольных испарителей может быть недостаточное поступление рассола в испаритель из-за неисправности насоса, неправильной регулировки задвижек, наличия воздуха в рассольной системе.
К наиболее распространенным причинам снижения коэффициента теплопередачи относят образование снеговой шубы на наружной поверхности испарителей для охлаждения воздуха или образование льда на трубах в испарителях для охлаждения хладоносителя, загрязнение маслом внутренних поверхностей испарителя и уменьшение скорости движения воздуха в воздухоохладителях или испарителях для охлаждения жидкостей.
При значительном снижении коэффициента теплопередачи практически невозможно поддерживать заданные температуры воздуха в охлаждаемом помещении или температуру рассола на выходе из испарителя. Если применена рассольная система охлаждения, то обращают внимание на плотность рассола. При недостаточной плотности и пониженной температуре кипения лед намораживается в трубках испарителя. При превышении необходимой плотности выпадают кристаллики соли, что также ухудшает работу холодильной установки.
Причинами недостаточного поступления жидкого холодильного агента в испарительную систему являются повышенный перегрев пара на всасывании, низкий уровень холодильного агента в линейном ресивере (или конденсаторе), периодическое оттаивание регулирующего вентиля, засорение жидкостных фильтров и недостаточное количество холодильного агента в системе холодильной установки. Во фреоновых системах может присутствовать влага, которая намораживается в дроссельном отверстии терморегулирующего вентиля и постепенно перекрывает его.
При температуре кипения выше оптимальной невозможно поддерживать заданные параметры работы холодильной установки, так как они зависят от температуры кипения.
Основные причины повышенной температуры кипения — недостаточная холодопроизводительность компрессоров по сравнению с тепловой нагрузкой (для достижения оптимальной температуры кипения включают дополнительные компрессоры или уменьшают тепловую нагрузку), чрезмерная подача жидкого холодильного агента в испарительную систему, особенно в первоначальный период пуска холодильной машины, засорение фильтра-грязеуловителя на всасывающей линии.
Повышенная температура конденсации. Повышенная температура конденсации приводит к снижению холодопроизводительности холодильной машины, увеличению потребляемой мощности и повышению перегрева пара в конце сжатия.
Причины повышенной температуры конденсации следующие:
недостаточное количество воды, подаваемой в конденсатор, повышение ее температуры. При оборотном водоснабжении может наблюдаться неудовлетворительная работа водоохлаждающих устройств;
уменьшение теплопередающей поверхности конденсатора при переполнении его холодильным агентом и вынужденном глушении водяных труб;
снижение коэффициента теплопередачи конденсатора из-за наличия в конденсаторе неконденсирующих примесей (воздух), ухудшение теплообмена в связи с загрязнением поверхности труб водяным камнем, отложением ила, водорослей;
ухудшение распределения охлаждающей воды из-за загрязнения форсунок и распределителей у вертикальных, оросительных и испарительных конденсаторов.
В автоматизированных холодильных установках повышение температуры конденсации вызывается неисправностью водорегуляторов.
Повышенная температура в конце сжатия. Превышение действительной температуры нагнетаемого пара по сравнению с ее оптимальными значениями может явиться следствием .повышенного перегрева всасываемого пара, плохого охлаждения рубашки компрессора и неисправностей компрессора, наличия в системе неконденсирующихся газов.
Работа компрессора с повышенным перегревом пара в конце сжатия приводит к ухудшению смазки всех трущихся частей из-за снижения вязкости масла, повышенному износу трущихся пар.
Повышенный перегрев характеризуется:
значительным износом цилиндров компрессора, неплотностями нагнетательных и всасывающих клапанов;
недостаточной подачей воды в охлаждающую рубашку компрессора или отложением водяного камня на его стенках;
нарушением системы смазки компрессора, что приводит к перегреву трущихся частей компрессора из-за уменьшения количества масла.
У ротационных и винтовых компрессоров температура в конце сжатия зависит от количества и температуры впрыскиваемого масла.
Работа компрессора влажным ходом. Признаками влажного хода компрессоров являются уменьшение перегрева всасываемых паров и понижение их температуры в конце сжатия.
При влажном ходе компрессора обмерзают стенки цилиндров и существенно изменяются характерные для нормальной работы шумы, возможно появление стука в цилиндрах. Сильное охлаждение компрессора приводит к замерзанию воды в охлаждающей рубашке и разрыву блока цилиндров. При резком охлаждении цилиндра происходит так называемый тепловой удар, в результате которого при наличии трещин в металле разрушается нагнетательная полость компрессора. Если количество жидкого холодильного агента превышает объем мертвого пространства компрессора, то возникает опасность гидравлического удара.
Основными причинами влажного хода являются чрезмерная подача жидкого холодильного агента в испарительную систему и вскипание жидкости при резком повышении тепловой нагрузки в испарительной системе.
Одной из причин гидравлических ударов является скопление масла при наличии мешков во всасывающем трубопроводе.
При возникновении влажного хода закрывают всасывающий вентиль компрессора и прекращают подачу жидкого холодильного агента в испарительную систему.
Конструкции фреоновых компрессоров систем холодильных установок
Общие сведения
Парокомпрессорные холодильные установки в зависимости от применяемого типа компрессора разделяют на роторные, поршневые и центробежные.
Первые применяют в холодильных установках малой холодопроизводительности (до 10000 кДж/ч), вторые — при холодопроизводительности до 800000 кДж/ч, третьи — при холодопроизводительности выше 800000 кДж/ч.
Для целей рефрижерации на судах используют автоматизированные парокомпрессорные установки с непосредственным испарением хладагента (фреон-12, фреон-22 или их смеси) в испарительных батареях.
Независимо от типа компрессора состав элементов и принцип действия парокомпрессорных холодильных установок одинаков.
Обзорная и принципиальная схема парокомпрессорной холодильной установки представлена на рис. 6.1 и включает следующие основные элементы: компрессор 1, теплообменник 3, терморегулирующий вентиль 4, вентилятор 5 и испаритель, которые соединены трубопроводами в замкнутую герметичную систему, обеспечивающую циркуляцию хладагента.
Компрессор предназначен для отсасывания паров хладагента из испарителя, что обеспечивает низкое давление, а следовательно, и низкую температуру кипения хладагента, и для сжатия паров до давления, при котором они могут конденсироваться при данной температуре охлаждающей воды.
Пары фреона, засасываемые компрессором из испарительных батарей, сжимаются до давления 0,5-0,8 МПа (5-8 бар), определяемого температурой охлаждающей забортной воды, и подаются в конденсатор.
Конденсаторы кожухотрубного типа служат для охлаждения перегретых после компрессора паров хладагента до температуры конденсации и конденсации их.
В конденсаторе тепло, которое отбирает от охлаждаемых помещений, и тепло, которое сообщается хладагенту при сжатии в компрессоре, передается охлаждающей забортной воде. Из конденсатора жидкий фреон поступает в ресивер и из нижней его части через клапан и фильтр осушитель жидкий фреон поступает в змеевик теплообменника.
В теплообменнике происходит теплообмен между парами, выходящими из испарителя и жидким хладагентом, который выходит из конденсатора. При этом температура жидкости перед терморегулирующим вентилем становится ниже температуры конденсации (хладагент переохлаждается), а влажный пар после испарителя подсушивается до сухого насыщенного пара и несколько перегревается. Терморегулирующий вентиль дросселирует жидкий хладагент от давления конденсации до давления кипения, регулирует количество хладагента, подаваемого в испаритель, таким образом, чтобы он успевал выкипеть, и в виде паров через теплообменник отсасывается компрессором.
Принципиальная схема и теоретический цикл одноступенчатых парокомпрессионных холодильных машин
Основное назначение судовых холодильных машин — поддержание заданных температур в охлаждаемых помещениях (рефрижераторных трюмах, провизионных кладовых, охлаждаемых контейнерах) и в других охлаждаемых объектах. Идеальным холодильным циклом для судовых машин является обратимый обратный цикл Карно, верхняя граница которого определяется температурой окружающей среды, в судовых условиях — это температура забортной воды tw (Tw, а нижняя граница определяется наиболее низкой температурой охлаждаемого объекта tоб. Такой идеальный холодильный цикл теоретически можно получить в одноступенчатой парокомпрессионной холодильной машине.
Действие машины при осуществлении обратимого обратного цикла Карно представляется следующим образом: в испарителе -И- хладагент кипит при температуре tоб и соответствующем ей давлении р за счет теплоты охлаждаемого объекта. В диаграмме S-T этот процесс показан штриховой линией 4’—1’. Влажный пар хладогента непрерывно отсасывается из испарителя компрессором КМ, адиабатно (при s = const), сжимается в нем (штриховая линия 1’-2’) до давления конденсации — р’к, соответствующего температуре t и подается в конденсатор КН. где происходит его конденсация при неизменных давлении и температуре (штриховая линия 2’-3’). Отвод теплоты конденсации осуществляется охлаждающей забортной водой. Жидкий хладагент возвращается в испаритель через расширительный цилиндр-детандер рЦ, в котором происходит адиабатное понижение давления и температуры хладагента (штриховая линия 3’-4’) до исходных значений (р’о и tоб ).
В реальном расширительном цилиндре полезная работа из-за ряда потерь практически оказывается близкой нулю, расширения — близким к процессу дроссселирования, в связи с этим от расширительного цилиндра отказались, заменив его более простым дроссельным устройством — регулирующим клапаном, позволяющим изменить степень заполнения испарителя кипящим хладагентом.
Общие сведения о фреоновых компрессорах
Фреоновые компрессора, работающие на фреоне-12 имеют некоторые конструктивные особенности, обусловленные тепловыми и физико-химическими свойствами фреона. Эти компрессора в большинстве случаев выполняются без водяной рубашки вследствие того, что температура сжатия паров фреона незначительная. Вместо водяной рубашки применяется воздушное охлаждение за счет ребер, устроенных в верхней части цилиндров и в крышках.
Так как компрессоры, работающие на фреоне-12, всасывают перегретые пары значительной повышенной температуры, поэтому они имеют увеличенную площадь сечения каналов и возможность гидравлических ударов в цилиндрах почти исключается. Поршневые холодильные компрессоры по конструкции механизма движения делятся на две группы, имеющие принципиальные различия: крейцкопфные и безккрейцкопфные. В судовых холодильных установках применяются только бескрейцкопфные поршневые компрессоры.
Малые и средние компрессоры выполняются, как правило, со встроенными электродвигателями — герметичными и бессальниковыми.
Современные безкрейцкопфные поршневые холодильные компрессоры, как правило, выполняются блок-картерными, т. е. блок цилиндров и картер у них объединяются в общую конструкцию, которая снабжается сменными рабочими втулками цилиндров. Унификация поршневых холодильных компрессоров, проводимая путем деления их на базы с одинаковыми ходом поршня и диаметром цилиндра, позволила сократить число серий выпускаемых компрессоров.
Ниже рассмотрим поршневой бескрейцкопфный непрямоточный одноступенчатый сальниковый компрессор П220 базы 1V ряда унифицированных поршневых компрессоров новой градации (см. рис. 6.2-6.3).
Корпус компрессора состоит из блок-картера 1 с двумя боковыми 6 и передней 10 крышками и проставок 16 с верхними крышками 17. Все корпусные детали отлиты из чугуна. Число проставок определяется числом пар цилиндров в компрессоре. Проставки крепятся к блок-картеру болтами 18. Разъемы между блок-картером и проставками уплотнены прокладками из паранита. В проставках между верхними крышками и блок-картером образована нагнетательная полость компрессора. Сам блок-картер перегородкой.15 разделен на всасывающую полость и картер. В перегородке предусмотрены уравнительные отверстия 5, позволяющие отсасывать пары хладагента из картера; через эти же отверстия в картер возвращается масло, отделяющееся от хладагента во всасывающей полости.
Цилиндровые втулки чугунные, на наружной поверхности имеют два посадочных пояска. Посадка втулок в блок-картер скользящая.
Коленчатый вал 12 стальной, штампованный, двухколенный, двухопорный. Колена выполнены под углом 180°. На каждой мотылевой шейке расположено четыре шатуна 4, ( в других компрессорах типа П может быть расположено три или два шатуна в зависимости от числа цилиндров в компрессоре). На коренные шейки напрессованы роликовые сферические подшипники 13 и 23. Вал с подшипниками установлен в стаканах 14 и 22, размещенных в расточках в передней и задней стенках блок-картера. Передний подшипник 13 зафиксирован, задний может перемещаться в стакане 22, что необходимо для компенсации линейного расширения вала при изменении температуры.
Шатуны 4 стальные штампованные. В верхнюю головку запрессована втулка, выполненная из бронзы. Нижняя головка шатуна имеет косой разъем, что облегчает сборку. В ней установлены тонкостенные биметаллические вкладыши. Рабочая поверхность вкладышей покрыта слоем антифрикционного алюминиевого сплава АСМ.
Поршни 3 литые из алюминиевого сплава. При сборке с шатуном поршневой палец 21 запрессовывают в поршень и фиксируют от продольных перемещений двумя замковыми шайбами. Верхняя часть поршня имеет специальную форму, повторяющую очертание корпуса всасывающего цилиндра. В верхней части поршня расположены уплотнительные кольца 20, в нижней — маслосъемное кольцо. Поршневые кольца изготовлены из термостабилизированного капрона. Необходимая упругость колец достигается установкой в канавке между кольцом и телом поршня стальных экспандеров. Кольца из капрона обладают высокой износостойкостью. Их применение увеличивает срок службы цилиндровых втулок.
Смазка компрессора осуществляется в расточке передней стенки блок-картера. В картере поддерживают уровень масла выше сетчатого фильтра грубой очистки 8, расположенного на дне картера.
Средний поршневой бескрейцкопфный непрямоточный одноступенчатый бессальниковый холодильный компрессор ПБ
По конструкции основные узлы и детали современных средних компрессоров мало отличаются от используемых узлов в крупных компрессорах.
Новый ряд средних бессальниковых непрямоточных компрессоров выполняется с чугунными или алюминиевыми корпусами, с минимальным количеством разъемов, с числом цилиндров четыре, шесть или восемь. Двух опорные коленчатые валы устанавливают на подшипниках качения или скольжения. При этом, как правило, один подшипник расположен на конце шейки вала, а другой — между шатунно-мотылевым механизмом и электродвигателем. Двухопорная схема вала 11 и блок-картер 1 компрессора обеспечивают равномерность зазора между ротором 3 и статором 4 встроенного электродвигателя. Ротор располагают консольно для облегчения его монтажа и демонтажа. Уровень масла в картере должен быть не менее, чем на 5 мм, ниже зазора между ротором и статором, так как наличие масла в зазоре приводит к росту подводимой мощности и увеличивает унос масла из компрессора. Масло забирается из картера масляным насосом 6 через фильтр 5 и подается через фильтр тонкой очистки в камеру 7, откуда поступает в сверление вала.
По конструкции цилиндровые втулки 2 шатуно-поршневая группа 10 и детали клапанного устройства 8 и 9 аналогичны используемые в компрессоре П220.
Интенсивное охлаждение встроенного электродвигателя всасываемым парами хладагента, поступающим в компрессор через фильтр 12, позволяет увеличить нагрузку двигателя в 1-1,8 раза по сравнению с его номинальной мощностью.В связи с этим бессальниковые компрессоры могут иметь встроенные двигатели значительно меньшей номинальной мощности и массы, чем открытые. Однако пусковой момент у встроенных электродвигателей должен быть повышенным разгружающий запуск.
Для обеспечения нормальной работы в режимах с уменьшенной массой всасываемого пара изоляция обмотки электродвигателя должна длительно выдерживать температуру до 125°С с учетом свойств среды, в которой работает двигатель.
Клапанная группа компрессора П220
Клапанная группа компрессора П220 показана на рис. 6.6. Верхний торец буртика цилиндровой втулки 1 служит седлом кольцевого всасывающего клапана 3. Всасываемый пар-хладогент проходит через отверстия 2, просверленные в буртике цилиндровой втулки.
Корпус всасывающего клапана 4, установленный на буртике цилиндровой втулки, служит седлом нагнетательных клапанов 12. Кольцевые пластины всасывающего 3 и нагнетательных 12 клапанов подпружинены. Специальный фланец 5, устанавливаемый с помощью четырех шпилек 6 на блок-картере 13, прижимает корпус всасывающего клапана к цилиндровой втулке. Этот фланец выполняет также роль направляющей для розетки 7 нагнетательных клапанов, прижатой к корпусу всасывающего клапана буферной пружиной 8. Буферная пружина, направляющие втулки 9 и 11, винт 10 и розетка 7 нагнетательных клапанов образуют ложную крышку. Такое устройство предохраняет механизм движения компрессора от больших перегрузок и гидравлических ударов при попадании жидкого хладагента в цилиндр. Под давлением несжимаемой жидкости розетка нагнетательных клапанов поднимается, сжимая буферную пружину, и жидкость перепускается в нагнетательную полость через каналы в нажимном фланце.
Для обеспечения нормальной работы компрессора при длительной эксплуатации необходимы: качественное уплотнение в соединениях корпус всасывающего клапана — буртик цилиндровой втулки и цилиндровая втулка — блок-картера; строгое соблюдение величины линейного мертвого пространства (зазор между днищем поршня и корпусом всасывающего клапана должен быть 0,8-1,2 мм).
Сальник компрессора П220
Сальник компрессора П220 по принципу действия и конструкции однотипен с сальником компрессора П80. Сальник пружинный, торцового типа, двусторонний, маслозаполненный. Двустороннее уплотнение позволяет удерживать масло в камере сальника. Торцовое уплотнение в сальнике достигается за счет трения между стальными кольцами 1, вращающимися вместе с валом, и неподвижными кольцами 2, выполненными из антифрикционного металлизированного графита. Предварительно сжатыми пружинами 6, расположенными в обойме 3, стальные кольца через нажимные кольца 4 и упругие кольца 5 прижаты к неподвижным. Упругие кольца из хладономаслостойкой резины или фторопласта компенсируют неточности сборки сальника, обеспечивая плотное прилегание трущихся колец, и одновременно служат уплотнением по валу.
Литература
Вспомогательные механизмы и судовые системы. Э. В. КОРНИЛОВ, П. В. БОЙКО, Э. И. ГОЛОФАСТОВ (2009)
Похожие статьи
Схема холодильной установки — Наши статьи ПрофХолодСистемс
Понять, как работает холодильное оборудование разных моделей и типов, помогает схема установки. Она состоит не только из базового комплекта, но и вспомогательных устройств, обеспечивающих бесперебойную и эффективную работу.
Особенности схемы
План установки показывает количество, тип и расположение компрессоров, теплообменников и других компонентов. Все эти детали нужны для полноценного функционирования оборудования. Из-за конструкции и устройства установок, их сервисное обслуживание существенно усложняется.
Основные причины возникающих проблем:
Большое количество охлаждаемых объектов. Они часто расположены на большом расстоянии от диспетчерского пункта.
Разветвленная сеть трубопроводов.
Использование аммиака или других токсичных хладагентов.
Резкие перепады тепловых нагрузок.
Особенности разработки установки
Чтобы создать схему холодильной установки, учитываются определенные требования.
К ним относятся:
Соблюдение стабильного температурного режима с возможностью корректировки для проведения ремонта или изменения параметров работы.
Обеспечение безопасности для обслуживающего персонала и долгой службы оборудования.
Сделать схему наглядно простой и понятной, чтобы можно было быстро внести изменения, не совершая ошибок.
Обеспечение бесперебойного поступления хладагента и теплоотдачи.
Внедрение частичной или полной автоматизации.
Простой монтаж и эксплуатация.
Как автоматизировать холодильную установку?
Большая часть современного оборудования работает автономно. Но важно подготовить его к этому процессу. Точнее, убедиться, что эксплуатация оборудования безопасна для персонала. Для этого улучшают схемы. Они предотвратят возникновения опасных ситуаций из-за резкого изменения тепловых нагрузок. Если оборудование не будет автоматизировано, велика вероятность частичного отключения компрессоров.
Разработка правильной схемы поможет избежать этого.
Холодоснабжение бывает двух типов:
Централизованным. Главными его минусами являются разветвленная сеть и большая протяженность трубопроводов, большое количество хладагента и сложная автоматизация.
Децентрализованным, в котором каждый объект обслуживается отдельным агрегатом.
Создание компаундных схем внесло положительные изменения при обустройстве холодильных машин. Благодаря циркулярным ресиверам, выполняющим функцию промежуточных сосудов и работающих при повышенном давлении, количество компонентов снизилось, а обслуживание и эксплуатация оборудования стало проще.
Любая установка включает набор узлов со специфическими деталями. Их также следует учитывать при создании эффективной схемы.